汽车涂料用丙烯酸树脂.docx
《汽车涂料用丙烯酸树脂.docx》由会员分享,可在线阅读,更多相关《汽车涂料用丙烯酸树脂.docx(15页珍藏版)》请在冰豆网上搜索。
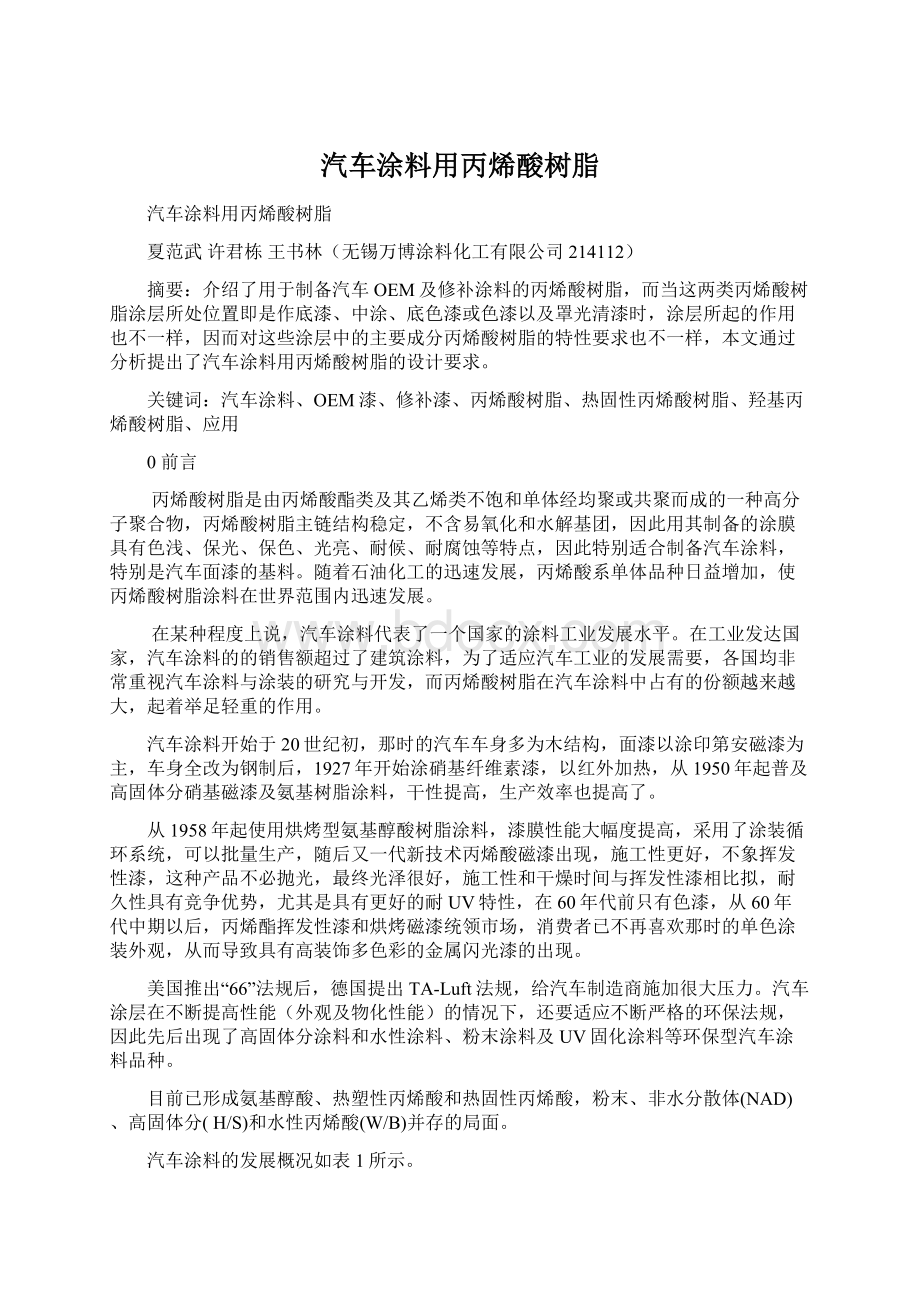
汽车涂料用丙烯酸树脂
汽车涂料用丙烯酸树脂
夏范武许君栋王书林(无锡万博涂料化工有限公司214112)
摘要:
介绍了用于制备汽车OEM及修补涂料的丙烯酸树脂,而当这两类丙烯酸树脂涂层所处位置即是作底漆、中涂、底色漆或色漆以及罩光清漆时,涂层所起的作用也不一样,因而对这些涂层中的主要成分丙烯酸树脂的特性要求也不一样,本文通过分析提出了汽车涂料用丙烯酸树脂的设计要求。
关键词:
汽车涂料、OEM漆、修补漆、丙烯酸树脂、热固性丙烯酸树脂、羟基丙烯酸树脂、应用
0前言
丙烯酸树脂是由丙烯酸酯类及其乙烯类不饱和单体经均聚或共聚而成的一种高分子聚合物,丙烯酸树脂主链结构稳定,不含易氧化和水解基团,因此用其制备的涂膜具有色浅、保光、保色、光亮、耐候、耐腐蚀等特点,因此特别适合制备汽车涂料,特别是汽车面漆的基料。
随着石油化工的迅速发展,丙烯酸系单体品种日益增加,使丙烯酸树脂涂料在世界范围内迅速发展。
在某种程度上说,汽车涂料代表了一个国家的涂料工业发展水平。
在工业发达国家,汽车涂料的的销售额超过了建筑涂料,为了适应汽车工业的发展需要,各国均非常重视汽车涂料与涂装的研究与开发,而丙烯酸树脂在汽车涂料中占有的份额越来越大,起着举足轻重的作用。
汽车涂料开始于20世纪初,那时的汽车车身多为木结构,面漆以涂印第安磁漆为主,车身全改为钢制后,1927年开始涂硝基纤维素漆,以红外加热,从1950年起普及高固体分硝基磁漆及氨基树脂涂料,干性提高,生产效率也提高了。
从1958年起使用烘烤型氨基醇酸树脂涂料,漆膜性能大幅度提高,采用了涂装循环系统,可以批量生产,随后又一代新技术丙烯酸磁漆出现,施工性更好,不象挥发性漆,这种产品不必抛光,最终光泽很好,施工性和干燥时间与挥发性漆相比拟,耐久性具有竞争优势,尤其是具有更好的耐UV特性,在60年代前只有色漆,从60年代中期以后,丙烯酯挥发性漆和烘烤磁漆统领市场,消费者已不再喜欢那时的单色涂装外观,从而导致具有高装饰多色彩的金属闪光漆的出现。
美国推出“66”法规后,德国提出TA-Luft法规,给汽车制造商施加很大压力。
汽车涂层在不断提高性能(外观及物化性能)的情况下,还要适应不断严格的环保法规,因此先后出现了高固体分涂料和水性涂料、粉末涂料及UV固化涂料等环保型汽车涂料品种。
目前已形成氨基醇酸、热塑性丙烯酸和热固性丙烯酸,粉末、非水分散体(NAD)、高固体分(H/S)和水性丙烯酸(W/B)并存的局面。
汽车涂料的发展概况如表1所示。
表1汽车涂料的发展
1924年以前
天然树脂为基料的油性漆(油漆)
1934~1935
硝基磁漆
1935~1945
硝基磁漆和醇酸
1945~1955
醇酸和氨基
1955~1965
氨基醇酸、热塑性丙烯酸和热固性丙烯酸,出现了色漆、金属闪光漆(金属漆)
1965~现在
氨基醇酸、热塑性丙烯酸和热固性丙烯酸,粉末、非水分散体(NAD)、高固体分(H/S)和水性丙烯酸(W/B)
本文将主要讨论丙烯酸树脂在汽车涂料中的应用。
1汽车原设备制造(OEM)涂料用丙烯酸树脂
热固性丙烯酸树脂涂料是利用丙烯酸树脂的侧链官能团与交联(或自交联)树脂反应成膜,这类涂层坚硬光亮,耐溶剂、耐候,保光保色,抗粉化,是综合性能突出的一类高装饰性涂料品种,适用于汽车、家电、医疗器械仪器仪表等高档产品的涂装。
因此,20世纪70年代以后,热固性丙烯酸涂料发展较快,特别是丙烯酸氨基烘漆普遍投产,在许多领域替代了醇酸氨基烘漆,从而使工业产品的装饰档次明显提高。
热固性树脂的一个优点是可以避免热塑性树脂相对分子质量的提高而增加了树脂的粘度,另一优点是它们具有更高的耐溶剂和表面活性剂的能力,以及更大的混溶范围。
热固性丙烯酸树脂,相对分子质量较小,10000~25000,高分子侧链有活性基团,如-OH、COOH、环氧基,可与其它树脂交联固化,一般需较高温度。
1.1汽车OEM底漆用丙烯酸树脂
汽车底漆自20世纪60年代开发了阳极电泳漆(AED),70年代又开发了防锈性能更高的阴极电泳漆(CED),目前CED技术已是一项成熟的技术,但仍在向环保方向发展。
丙烯酸树脂较少用于制备底漆,因为底漆要求有好的附着力和耐腐蚀性。
但是丙烯酸树脂在汽车底漆中曾经甚至目前仍有部分应用。
比如,丙烯酸树脂用来改性环氧醚树脂以改进阳极电泳涂料的槽液稳定性。
以环氧酯为基础的AED基料,槽液稳定性因皂化而有限。
如果结构中无酯键而只有非皂化的醚键及C-C键,则可以改善槽液稳定性。
方法是环氧树脂用不饱和醇醚化,最后用硬或软的丙烯酸单体如苯乙烯、丙烯腈、丙烯酸丁酯以及含-COOH的丙烯酸接枝加成聚合物。
另一项应用是制备单层浅色电泳,主要用于铝制品铝合金的电泳,目前已有超过PB的市场。
一种可以自由调节结构的阴离子电泳基料的方法是α,β-不饱和单体及含-COOH的α,β-不饱和羧酸的共聚物,通过部分或完全中和水溶,通常丙烯酸含量在5~20%。
这种树脂具有平衡的亲水-疏水单体比如BA/AA比(86/14),用二乙胺中和,兑至10%水溶液,远高于临界胶束浓度,所以可以拼入水不溶的基料如氨基交联剂。
固化时官能性单体会引起固化时的交联,如-OH、环氧基或酰胺基的单体可以很易通过共聚引入,因此可获得自交联及外交联热固性树脂。
自交联体系、槽液稳定性最好,但外交联体系,可以将两种树脂几乎以同样比例沉积,而且比例是可变的。
由于AED防腐性能远不如CED逐渐被CED所取代。
CED基料主体树脂包括环氧树脂、聚酰胺树脂、聚氨酯树脂、丙烯酸乙烯共聚物等,其中,环氧树脂由于附着性、防蚀性优,电阻高,可望获高附着力,引入聚酰胺易于水溶,可引入聚氨酯改性提高防蚀性,成本低,因而在CED中环氧树脂是目前普遍采用的基料之一。
但是丙烯酸树脂和乙烯基共聚物也可用于CED基料,用于制备彩色电泳或低温固化电泳。
丙烯酸酯和乙烯基化合物可通过自由基反应共聚,通常这种含胺基的单体含叔胺基甲基丙烯酸的二甲基乙醇胺,(甲基)丙烯酸的乙烯基咪唑。
低温固化CED目前有引入丙烯酸基氨基甲酸酯到分子中,保留其在固化体系中的高活性,就可以实现无催化剂的一种低温固化体系。
1.2汽车OME中涂用丙烯酸树脂
汽车车身所用中涂基料,二战后多使用酚醛树脂,1958年以后则从自干型转向烘干型,涂膜质量得到飞跃提高,这时使用的主基料是醇酸树脂,以环氧树脂改性提高附着力以氨基树脂作固化剂的固化体系直到目前仍是中涂的一大体系,这也是现代中涂的前身。
20世纪80年代曾使用聚酯树脂为主的粉末涂料,由于成本等原因等停止使用,开始从溶剂型液体中涂向水性中涂转变,水性中涂的应用始于20世纪80年代后期,现已发展为三大体系即醇酸氨基,醇酸聚氨酯以及醇酸-氨基聚氨酯杂混体系,目前醇酸-聚氨酯体系在欧洲在高级轿车应用占主导地位。
中涂的功能有两个方面比较重要,首先是抗石击,其次是受到损伤时抵达底材的剥离面积要最小化,因此,而丙烯酸树脂在机械性能方面难以调节,特别是硬度和柔韧性的平衡,因此丙烯酸树脂比较少见于汽车中涂,尤其是国外。
但是,也不是绝对不可以采用,比如丙烯酸树脂与聚酯比,内聚力不如聚酯大,所以不容易产生缩孔等漆膜弊病,可以采用丙烯酸通过接枝来改性聚酯或反过来用聚酯改性丙烯酸来增加柔韧性也未尝不可。
通过接枝使丙烯酸脂侧链可以通过接枝共聚引入到聚酯分子中,从而达到改性的目的。
如WF-S6035即是这种类型。
丙烯酸树脂在中涂中的另一个方面的应用是改性水性自干醇酸树脂。
醇酸树脂最突出优点是原料易得、价廉,调节油度及用不同的油(从干性到不干性)可获得从自干到烘干的醇酸树脂,但是自干醇酸的干性总是不尽人意,尤其初期干性,由于氧化干燥速度太慢而不理想,改性后水性醇酸树脂可改进颜色、干率、早期耐水性及长期柔韧性。
最常用的方法是丙烯酸改性,此法还可以增大酯键周围立体障碍,获抗水解稳定性,其方法为:
第一步先制得相对分子质量非常低的含-OH、-COOH的丙烯酸酯预聚物;第二步将此预聚物取代一部分脂肪酸,按等质量取代,然后与醇酸树脂或与醇酸树脂原料一起酯化。
中涂层所用涂料体系发展方向是高固体化、水性化和粉末化。
1.3汽车OEM面漆用丙烯酸树脂
汽车面漆是汽车多层涂层中最后涂层用的涂料,它直接影响汽车的装饰性,耐候性和外观等。
因此采用何种树脂类型是汽车制造商及涂料商非常重视的一个方面。
汽车面漆分为两类:
本色(实色)面漆和金属闪光漆,大体上各占一半。
由于丙烯酸树脂的突出的保光保色性,而且与醇酸树脂或聚酯比,有以下不同点:
干燥性良好;涂料的粘度低;涂膜外观平滑性高;树脂的透明度(作为罩光漆)高;涂料的网状结构致密(官能团分布在侧链,而非如聚酯一样只分布在两头)。
因此很适合用作汽车面漆(包括金属底色漆、实色漆和罩光清漆)的主要基料。
1.3.1汽车OEM金属闪光漆用丙烯酸树脂
在金属闪光色已流行于美国市场时,欧洲仍然喜欢单色的传统施工,但由于欧洲在美国的汽车厂引入了金属闪光漆,所以闪光涂料涂装的汽车在欧洲市场逐渐受到欢迎。
金属闪光涂料获得高装饰性即具有良好金属闪光效果的关键在于使铝片在湿膜中能够平行定向排列,而在干燥过程中,这种排列不再紊乱。
最大限度地利用涂层体积收缩以影响金属闪光粉的排列,因此应尽可能地采用具有溅涂效果的涂装方法,使涂膜垒加,低固体分化就具有大的收缩体积。
金属闪光底色漆涂装后不象以前那样直接烘烤,而是直接外加罩光清漆,然后一起烘烤固化即所谓两涂一烘(2C1B)方法,清漆的作用是可使漆膜表面平整光亮,而且保持效应颜料不受风雨、酸雾、鸟粪的腐蚀,并提供保光性和抗老化性。
经排列好的金属片在涂膜中不再因本身或受罩光清漆的影响而移动,即具有运动抑制效果。
归纳起来为四种效果:
溅涂效果、多层效果、体积收缩效果和运动抑制效果。
丙烯酸树脂是丙烯酸酯、甲基丙烯酸酯单体为主要成分的聚合树脂,在140℃下烘烤30min左右(保持)就能固化干燥。
丙烯酸树脂涂料黏度低,涂装后涂膜收缩,色泽鲜艳且透明感好;因体积收缩大,有利于金属闪光色涂装时平行排列铝粉的作用。
而且平滑性良好,鲜映性(外观装饰性)良好,耐候性优良,因而很适用于金属闪光色涂装。
1965年前后开发成功的热固型丙烯酸酯,使汽车金属闪光色面漆涂装得到积极发展,涂装工艺由一涂一烘(1C1B)进步为底色加罩光工艺(2C1B),面漆涂膜质量(外观、耐候性、耐划伤性等)有了大幅度提高。
因此可以说丙烯酸树脂在推动汽车面漆涂装(金属闪光色)的技术进步起到重要作用。
无论新车的闪光色面漆涂装,还是汽车修补用金属色面漆,都是采用丙烯酸树脂系列涂料,前者采用热固型丙烯树脂制的烘烤型涂料,汽车修补用闪光色面漆为低温干燥型(单组分的底色漆加双组分罩光清漆)。
在美日西欧,汽车闪光漆主要用丙烯酸树脂来生产,其中有选用丙烯酸非水分散体为基料的。
底色漆用丙烯酸树脂的粘度及相对分子质量比用作实色漆的树脂粘度及相对分子质量要高,以保证底色漆的干燥速率,虽然树脂的粘度提高了,但是底色漆采用的是低固体分施工,所以没有多大影响。
有时还需要借助添加醋酸丁酸纤维素(CAB)来提高干性。
CAB树脂液主要是用来提高底色漆的干燥速率、提高体系低固体分下的粘度、阻止铝粉和珠光颜料在湿漆膜中杂乱无章的运动和防止回溶现象。
因此,要求丙烯酸树脂与CAB具有良好的混容性,才不致于影响涂膜的鲜映性和光泽甚至耐候性。
无锡万博涂料化工有限公司推出了三个品种:
WF-S5024(固体分50%)、WF-S6030(固体分60%)和WF-S6027(60%)。
WF-S5024为经济型,WF-S6030特别适合于汽车铝材轮毂的喷涂。
后两个品种还可用于制备实色漆。
采用聚酯改性丙烯酸树脂如WF-S6035,可以提高涂膜的柔韧性和丰满度,但是干性会稍有下降,可以通过添加CAB来解决。
由于丰满度提高,该品种还可以用作实色漆树脂。
目前国内汽车涂装线一般采用溶剂型闪光底色漆,而在一些西方发达国家已经大量使用水性底色漆。
一方面,是环保法规的压力;另一方面,是水性金属闪光漆的效果比溶剂型更优异。
近年来金属闪光漆系列发展迅速,以往欧美常用的涂装体系CED、中固体分中涂、中固体分金属闪光漆、双组分高固体分清漆,每m2VOC排放量120g,其中近一半(55g)为金属闪光漆所释放,是主要的VOC释放源,如果金属闪光漆水性化则可大大降低VOC排放。
图1溶剂型与水性型金属闪光底色漆VOC比较
水性金属闪光漆有特殊流变性,利于效应颜料定向,比溶剂型涂料有更好的金属闪光效应,所以水性金属闪光漆比水性中涂更早被汽车制造厂所接受,欧美已广泛使用。
到20世纪70年代,由于涂料无公害化、省资源、省能的要求,丙烯酸树脂也发生了质的转变,开始向高固体分、水性型和无溶剂化转变。
金属闪光涂料所用主基料若为丙烯酸树脂,最好是可以交联成膜,自交联或外加交联剂通过热固化(2K体系)可交联丙烯酸树脂,可以通过前述溶液聚合或乳液聚合。
溶液聚合时,用醇溶剂作为分散介质,直接转入水相,也可以用芳香族溶剂或酮类溶剂等水不溶性溶剂,通过真空脱去溶剂,再转入水相,转入水相时,引入胺中和主链中的羧基溶解或分散聚合物于水中,这些阴离子稳定体系的pH值最好在7.5~8.0之间;乳液聚合时可直接分散,也可以胺调节pH在上述范围。
金属闪光底色漆体系的流变由树脂组分及由特殊流变剂或增稠剂如聚丙烯酸盐或硅酸盐来决定。
目前所有的水性金属闪光底色漆体系显示剪切稀化特性,它们是假塑性或触变性的。
高剪切速率下(典型的是喷涂施工)粘度低,导致涂料极好雾化,施工后立即处于低剪速率下粘度非常高或恢复很快,湿漆膜的流变是极复杂的,水性金属闪光漆的开发过程中许多工作集中在金属粉取向及涂膜的流平及抗流挂性。
HiromiHarakawa等人提出了喷涂过程粘度理想变化的模型,如图所示。
图2喷涂过程水性金属闪光涂料粘度的变化理想区域
理想的情况是图示曲线2的情况。
通过混合微凝胶(MG)与水分散丙烯酯树脂,可以在A区和B区控制粘度。
在A区通过添加亲水溶剂可以增大A区粘度到某一程度,在B区粘度却降低,这是因为此区有机溶剂比水挥发更多,尽管A区粘度增长,但仍不够,MG的引入增加了漆雾的弹性,对降低B区的涂膜流平起作用,对A区的增粘不起作用。
无锡万博涂料化工有限公司开发了一种丙烯酸分散体树脂WF-S2410AQ,树脂通过中和后具有假塑性,该树脂是核壳聚合的交联微粒子树脂,用于制备水性金属闪光漆可以产生优异的效果而不需加入铝粉定向剂改进定向或加入CAB来改进干性。
水性金属闪光漆与溶剂型金属闪光漆的很大不同在于,它所采用的铝粉必须是经包覆的,能够经受水性涂料的碱性环境。
1.3.2汽车OEM罩光清漆用丙烯酸树脂
罩光清漆是汽车涂料的最后一个涂层,特别是金属闪光漆必须罩清漆。
部分高级轿车也在实色漆上再罩一层清漆,使漆膜外观得到改善,如美国克莱斯勒公司的所有轿车、通用汽车公司的部分轿车就罩了清漆。
罩清漆后,漆膜外观、耐久性均会有所提高。
目前,欧洲和北美以及我国均有采用双组分或单组分高固体分丙烯酸清漆,但由于环境保护方面的原因,人们极力减少使用溶剂,促使人们这样做的另一动力是近年来溶剂价格的上涨。
最早用水性清漆的是Opel用的丙烯酸氨基水性清漆。
但水性罩光清漆的推广并不广泛,这是因为2KPUR罩光清漆VOC排放已满足欧洲VOC标准,所以尽管目前涂装线已使用水性中涂和水性闪光底色漆,但罩光清漆仍为典型的溶剂型,水性清漆和粉末清漆不能采用现有设备,所以发展高固体分清漆是目前罩光清漆的主流。
金属闪光漆的罩光漆基本上全是热固性丙烯酸清漆,不管其底涂层是丙烯酸树脂(以美国为主)还是聚酯氨基或醇酸氨基(日本和西欧)。
用丙烯酸清漆罩光,它可以使漆膜表面平整光滑,保护金属鳞片不受风雨,酸雾等腐蚀。
现在人们发现较厚的罩光膜,金属闪光立体感强,丰满度好,因此可以采取两次罩光或采用高固体分清漆罩光,以使罩光漆膜38μm以上,也可在罩光漆中加入紫外线吸收剂,增加其保光性和抗老化性。
涂料中挥发性有机化合物(VOC)对大气污染越来越受到关注。
降低溶剂量,发展高固体分涂料,是涂料研究的重要方向,高固体分涂料很难有确切定义,现在一般的溶剂型热固性涂料,在喷涂要求的粘度下,其固含量(重量)一般在40%~60%,而所谓的高固体分涂料的固含量则在60%~80%。
因成膜物不同,颜料量不同,高固体含量指标差距很大。
例如,对于PVC值高的底漆,高固体分意味着固含量(体积)为50%,而对于PVC值低的高光泽面漆或清漆则为75%以上。
高固体分涂料不仅要保证漆膜性能和涂料应用性能能达到一般溶剂热固性涂料的水平或更高,而且同时要解决粘度高低问题。
影响丙烯酸树脂粘度的主要参数有相对分子质量、相对分子质量分布、基料官能度及其浓度、溶剂等因素。
1.3.2.1高固体分涂料用丙烯酸树脂粘度的控制
(1)相对分子质量
可以通过提高溶剂型丙烯酸树脂在聚合过程中产生的游离基浓度来制备低相对分子质量的丙烯酸树脂。
可以通过下列方法得到:
• 提高聚合温度
在一定的单体组成下提高丙烯酸树脂制备时的温度可以降低平均相对分子质量、相对分子质量分布及粘度。
然而,应注意不要在太高的温度下聚合,因为这可能会导致树脂的黄变,这在用作清漆是不能接受的。
高的加工温度的优点不仅加快了引发剂的分解速度,而且也提高了溶剂的链转移作用。
• 提高引发剂用量(4%或更高)
提高引发剂浓度是经典的降低相对分子质量的方法,但用量太多会导致大量的分解产物,会影响耐久性及产生气味并使价格提高。
• 选择具有更低的半衰温度的引发剂
通常,丙烯酸单体在溶剂中的聚合使用有机过氧化物作为自由基引发剂。
一般,自由基根据其存在时间可以分为长寿、稳定(反应性略差)的及短寿、不稳定(有活性)的自由基。
因此过氧化物的化学结构对自由基产生速度有很大影响。
自由基本身的性能会影响聚合物的线性及相对分子质量分布。
那些只需更少的分解能量的过氧化物在同样的温度可以产生更多的自由基从而得到更低的相对分子质量。
发现对制备丙烯酸涂料用树脂,2,2-偶氮二(异丁酸甲酯)是有效的引发剂,得到的聚合物溶液柔韧性更好、相对分子质量低、分布窄并能减少挥发物。
与传统的有机过氧化物及偶氮类引发剂相比,使用叔戊基过氧化物及引发剂混合物得到了具有高质量的丙烯酸树脂。
过氧化苯甲酰(BPO)在分解时生成苯基自由基,苯基自由基特别活泼,可以提取聚合物链上的氢原子,从而使聚合物形成分支。
偶氮二异丁腈(AIBN)分解时生成的丁腈自由基,比较稳定,不易进行夺H反应,因此用AIBN为引发剂时,可得相对分子质量分布窄的聚合物。
有报道说,用叔戊基过氧化物,如3,3-二(过氧叔戊基)丁酸乙酯为引发剂时可得相对分子质量分布非常窄的聚合物,但用相应的叔丁基过氧化物则得到相对分子质量分布宽的聚合物,其原因也和生成自由基的活性有关。
叔戊基过氧化物分解所得的叔戊基氧自由基可很快转化为较稳定的乙基自由基和丙酮,而叔丁基过氧化物分解所得的叔丁氧基和进一步分解所得的甲基自由基都是很活泼的自由基,很容易进行夺H反应。
叔戊基氧自由基和丁氧基自由基的分解反应表示如下:
另外,引发剂的半衰期需和聚合反应温度相配合,温度太高,低半衰期的引发剂分解很快,生成的自由基易重新结合,形成无引发作用的物质,只有很少的自由基可用于有效的链引发过程,这就会导致相对分子质量升高。
引发剂的价格也是较现实的问题,叔戊基过氧化物的价格要比其它过氧化物的价格高许多。
可以说,引发剂的选择取决于价格、在加工温度时的分解速度及夺氢的能力。
夺氢越少,树脂支链化程度越低、粘度越小。
因此引发剂的性能可以影响最终树脂的相对分子质量、粘度及分散性。
• 减少单体的滴加时间
通过降低单体滴加入反应器的时间可以控制齐聚物的相对分子质量。
但是太短的滴加时间来不及移去反应热也会导致相对分子质量的分布加宽,树脂的粘度猛增。
•引入链转移剂
链转剂移不仅可调节相对分子质量,通过链转移剂引入反应性官能团也是一个有意义的方法。
以前用(叔)十二烷基硫醇来控制相对分子质量,但得到低相对分子质量时需高用量,高用量的硫醇会导致气味问题、转化率低及涂层在室外曝晒时的耐久性差。
但是使用2-巯基乙醇和2-巯基丙酸,前者可以直接引入羟基,后者则是引入羧基,羧基可进一步和加在体系中的羧酸缩水甘油酯反应得到羟基。
加羧酸缩水甘油酯的另一个作用是它可以和未参与反应的硫醇作用以消除臭味。
目前也有硫醇链转移剂的替代品,这种替代品没有气味或者气味很小,但是用量要比硫醇用量高。
• 其它方法
其它的方法包括目前正在学术界及工业领域进行实际研究的控制自由基聚合:
氮氧化物介质聚合、原子转移自由基聚合、可逆加成裂解转移及催化链转移,目的是为了控制聚合物结构、相对分子质量及分散度。
然而,降低相对分子质量的程度有限,因为太低的相对分子质量会导致干性差、最终涂膜的硬度及耐化学性差。
所以,相对分子质量分布必须保持尽可能窄(高相对分子质量部分会提高粘度)。
(2)相对分子质量分布
对丙烯酸树脂,相对分子质量分与相对分子质量本身有很大关系。
如果相对分子质量提高,相对分子质量分布也提高,因此,很难研究相对分子质量分布对粘度的真实的影响。
相同平均相对分子质量的聚合物,由于相对分子质量分布不同,它们的粘度也很不同,为了说明这种关系可首先将重均相对分子质量通过下式和粘度联系起来:
粘度固定
浓度
相对分子质量
图3粘度固定时相对分子质量与溶液固含量(浓度)的关系
式中k和x定义为和体系有关的常数。
对于聚合物熔体的粘度,当M超过一定值时,由于聚合物分子间的缠绕,x值较高,约为3~4,而对于高固体分的低聚物,一般不发生缠绕问题,x值一般在1~2之间。
然后可借用此式进行下列计算:
两种数均相对分子质量(Mn)均为1000的低聚物,第一种的相对分子质量分布为单分散即Mw/Mn=1,其粘度为η=1Pa·s。
如果x=1,代入上式可求得lgk=-3;第二种低聚物为多分散低聚物,若Mw/Mn=3,则其Mw=3000,按上式计算,η=3Pa·s,若x=2.0,则第二种聚合物的η=9Pa·s。
由此不难看出,相对分子质量分布变宽,可使粘度明显增加。
在此顺便提及,相对分子质量不同的聚合物分子对Mw和Mn的贡献所占比重是不同的,Mn对相对分子质量小的分子敏感,而Mw对相对分子质量高的敏感。
另外,相对分子质量过低的聚合物,在高温固化时便有可能挥发,实际是降低了固含量。
(3)基料官能度及浓度
基料的粘度随官能团浓度增加而提高。
官能团的特性在很大程度上决定这种粘度增长。
众所周知羧基及羟基会提高基料粘度。
这种现象毫无疑问是由于氢键提高了分子间作用力及基料的溶解性。
但羟基又不能太低,因为会降低交联密度,从而影响涂膜性能。
• 在聚合物中引入环状单体如甲基丙烯酸异冰片酯、甲基丙烯酸环己酯、甲基丙烯酸叔丁酯、甲基丙烯酸叔丁基环己酯等,在一定的Tg、Mw、官能度、固含量时粘度都降低。
因此,基于高Tg的大单体的新的丙烯酸多元醇类型确实提供了性能和低VOC的更好的平衡。
• 引入单环氧基的大位阻的单体“CarduraE10”
“CarduraE10”可以通过其环氧基与任何含亲核基团的单体反应而引入丙烯酸树脂,提供低粘度、好的反应活性、具有吸引力的涂膜机械性能、高的涂膜光泽及极好的耐候性。
(4)引入活性稀释剂降低树脂的粘度
活性稀释剂是特别设计以降低涂料体系的VOC的有非常低的粘度的共反应物。
它们通常能提供与溶剂相似的降低聚合组成物粘度的能力,同时也必须能与聚合物母体反应以有效减少VOC。
(5)工艺条件
为了保证低聚物中有2个以上的官能团,除了增加官能团的含量外,很显然要求相对分子质量分布尽量窄,但窄相对分子质量分布的低聚物并不是使每个分子具有2