可转位刀具的基本概念.docx
《可转位刀具的基本概念.docx》由会员分享,可在线阅读,更多相关《可转位刀具的基本概念.docx(22页珍藏版)》请在冰豆网上搜索。
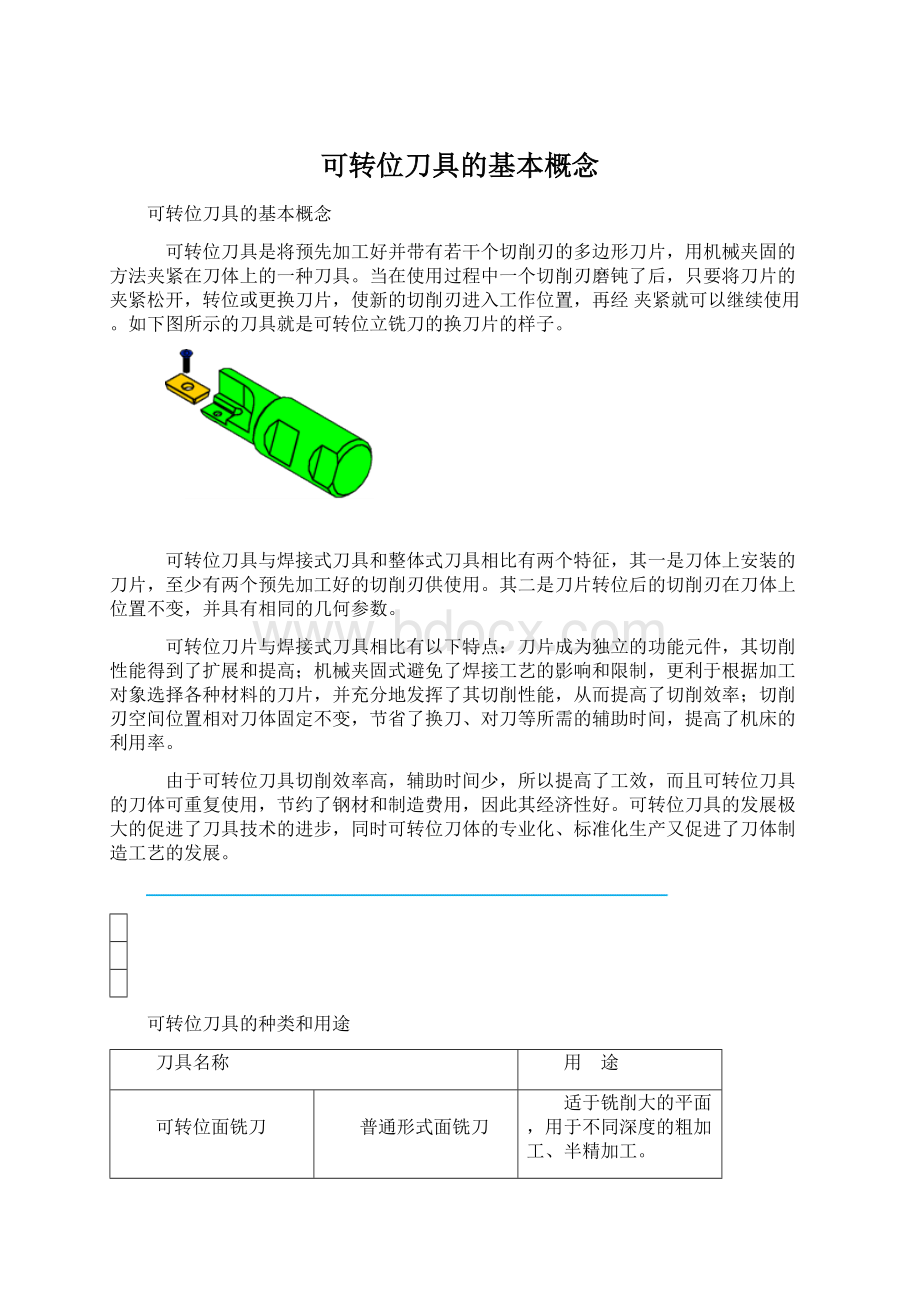
可转位刀具的基本概念
可转位刀具的基本概念
可转位刀具是将预先加工好并带有若干个切削刃的多边形刀片,用机械夹固的方法夹紧在刀体上的一种刀具。
当在使用过程中一个切削刃磨钝了后,只要将刀片的夹紧松开,转位或更换刀片,使新的切削刃进入工作位置,再经夹紧就可以继续使用。
如下图所示的刀具就是可转位立铣刀的换刀片的样子。
可转位刀具与焊接式刀具和整体式刀具相比有两个特征,其一是刀体上安装的刀片,至少有两个预先加工好的切削刃供使用。
其二是刀片转位后的切削刃在刀体上位置不变,并具有相同的几何参数。
可转位刀片与焊接式刀具相比有以下特点:
刀片成为独立的功能元件,其切削性能得到了扩展和提高;机械夹固式避免了焊接工艺的影响和限制,更利于根据加工对象选择各种材料的刀片,并充分地发挥了其切削性能,从而提高了切削效率;切削刃空间位置相对刀体固定不变,节省了换刀、对刀等所需的辅助时间,提高了机床的利用率。
由于可转位刀具切削效率高,辅助时间少,所以提高了工效,而且可转位刀具的刀体可重复使用,节约了钢材和制造费用,因此其经济性好。
可转位刀具的发展极大的促进了刀具技术的进步,同时可转位刀体的专业化、标准化生产又促进了刀体制造工艺的发展。
可转位刀具的种类和用途
刀具名称
用 途
可转位面铣刀
普通形式面铣刀
适于铣削大的平面,用于不同深度的粗加工、半精加工。
可转位精密面铣刀
适用于表面质量要求高的场合,用于精铣。
可转位立装面铣刀
适于钢、铸钢、铸铁的粗加工,能承受较大的切削力,适于重切削。
可转位圆刀片面铣刀
适于加工平面或根部有圆角肩台、筋条以及难加工材料,小规格的还可用于加工曲面。
可转位密齿面铣刀
适于铣削短切屑材料以及较大平面和较小余量的钢件,切削效率高。
可转位三面刃铣刀
可转位三面刃铣刀
适用于铣削较深和较窄的台阶面和沟槽。
可转位两面刃铣刀
可转位两面刃铣刀
适用于铣削深的台阶面,可组合起来用于多组台阶面的铣削。
可转位立铣刀
可转位立铣刀
适于铣削浅槽、台阶面和盲孔的镗孔加工。
可转位螺旋立铣刀(玉米铣刀)
平装形式螺旋立铣刀
适于直槽、台阶、特殊形状及圆弧插补的铣削,适于高效率的粗加工或半精加工。
立装形式螺旋立铣刀
适于重切削,机床钢性要好。
可转位球头立铣刀
普通形球头立铣刀
适于模腔内腔及过渡R的外形面的粗加工,半精加工。
曲线刃球头立铣刀
适于模具工业。
航空工业和汽车工业的仿形加工,用于粗铣、半精铣各种复杂形面,也可以用于精铣。
可转位浅孔钻
可转位浅孔钻
适于高效率的加工铸铁、碳钢、合金钢等,可进行钻孔、铣切等。
可转位成型铣刀
可转位成型铣刀
适于各种型面的高效加工,可用于重切削。
可转位自夹紧切断刀
可转位自夹紧切断刀
适于对工件的切断、切槽。
可转位车刀
可转位车刀
适于各种材料的粗车、半精车及精车。
可转位铣刀体常用的结构形式
结 构 简 图
说 明
柄部为锥柄(莫氏锥柄和7:
24锥柄等),用于直径小于或等于Ø80mm的立铣刀和面铣刀。
柄部为削平型直柄,用于小规格的立铣刀。
用一个螺钉,通过铣刀内孔将铣刀固定在端键传动刀杆上的结构,适用于直径小于或等于Ø160mm的面铣刀和Ø63mm~Ø125mm直径的套式立铣刀。
以铣刀内孔及7:
24锥柄心轴定位,适用于直径Ø160mm~Ø500mm的面铣刀和三面刃铣刀。
用刀体止口与机床主轴端面相配合来定位,常用于直径大于或等于Ø250mm的面铣刀和三面刃铣刀,止口直径为Ø128.57mm或Ø221.44mm。
可转位铣刀主要几何角度的符号及意义
名 称
符 号
(度)
定 义
作 用
前角
γ0
前面与基面间的夹角,在正交平面中测量。
决定切削刃的锋利程度和强度。
增大前角可减小切屑变形,减小切削力和切削功率。
刃倾角
λs
主切削刃与基面间的夹角,在基面中测量。
控制切屑流向,影响切削刃强度和切削分力的大小。
背前角
(轴向前角)
γp
前面与基面间的夹角,在背平面中测量 。
决定切削刃的强度和切屑的流向,影响切削分力的大小和表面质量。
侧前角
(径向前角)
γf
前面与基面间的夹角,在假定工作平面中测量。
决定刀齿的强度和切削力的大小。
主偏角
Kr
主切削平面与假定工作平面间的夹角,在基面中测量。
影响刀尖部分的强度、切削分力之间的比例、工件表面的形状和切削刃参加切削的长度。
副偏角
Kr'
副切削平面与假定工作平面间的夹角,在基面中测量 。
减小副切削刃、副后面与工件已加工表面的摩擦,影响表面粗糙度。
后角
α0
后面与切削平面间的夹角,在正交平面中测量。
减小后面与工作表面间的摩擦,并与前角决定切削刃的锋利和强度。
可转位浅孔钻切削用量的选择
被加工材料
布氏硬度
HBS
切削速度
(m/mm)
钻孔直径(mm)
18.5~20.9
21.0~25.9
26.0~30.9
31.0~41.9
42.0~56.0
进给量(mm/r)
易切削钢和碳钢
180~275
100
0.06~0.15
0.09~0.15
0.09~0.16
0.09~0.17
0.10~0.20
200
0.09~0.16
0.10~0.18
0.09~0.25
0.09~0.30
0.10~0.30
300
0.10~0.18
0.11~0.18
0.10~0.25
0.10~0.32
0.10~0.32
碳钢淬火
220~450
100
0.09~0.14
0.09~0.14
0.08~0.14
0.08~0.14
0.10~0.20
200
0.10~0.16
0.10~0.16
0.09~0.17
0.10~0.20
0.10~0.28
300
0.11~0.17
0.11~0.17
0.10~0.18
0.10~0.22
0.10~0.30
低合金钢淬火
220~450
100
0.09~0.15
0.10~0.17
0.09~0.17
0.09~0.20
0.11~0.21
200
0.11~0.18
0.12~0.20
0.10~0.24
0.10~0.20
0.11~0.28
不锈钢(奥氏体
150~275
300
0.11~0.19
0.12~0.20
0.11~0.25
0.13~0.27
0.12~0.30
高合金钢、退火
150~250
100
0.12~0.17
0.12~0.18
0.10~0.20
0.09~0.25
0.10~0.20
200
0.12~0.20
0.13~0.22
0.10~0.25
0.12~0.30
0.10~0.30
300
0.12~0.22
0.12~0.23
0.11~0.26
0.12~0.31
0.12~0.32
高合金钢、工具钢
>=360
100
0.08~0.14
0.06~0.14
0.09~0.16
0.09~0.17
0.09~0.18
200
0.09~0.16
0.09~0.16
0.10~0.20
0.10~0.20
0.10~0.20
低拉力强度灰铸铁
<=230
100
0.07~0.25
0.07~0.25
0.07~0.30
0.07~0.35
0.07~0.35
200
0.07~0.30
0.07~0.30
0.07~0.35
0.07~0.40
0.07~0.40
300
0.07~0.30
0.07~0.30
0.07~0.35
0.07~0.40
0.07~0.40
高拉力强度灰铸铁
>=230
100
0.07~0.25
0.07~0.30
0.07~0.30
0.07~0.35
0.07~0.35
200
0.07~0.30
0.07~0.30
0.07~0.35
0.07~0.40
0.07~0.40
电子邮件:
xiaohe91@
数控车床对可转位车刀的要求
数控车床与普通车床用的可转位车刀,一般无本质的区别,其基本结构、功能特点是相同的。
但数控车床工序是自动化的,因此对用于其上的可转位车刀的要求侧重点又有别于普通车床的刀具,具体要求和特点如下表所示。
要求
特 点
目 的
精度高
刀片采用M级或更高精度等级的;
刀杆多采用精密级的;
用带微调装置的刀杆在机外预调好。
保证刀片重复定位精度,方便坐标设定,保证刀尖位置精度。
可靠性高
采用断屑可靠性高的断屑槽型或有断屑台和断屑器的车刀;
采用结构可靠的车刀,采用复合式夹紧结构和夹紧可靠的其他结构。
断屑稳定,不能有紊乱和带状切屑;
适应刀架快速移动和换位以及整个自动切削过程中夹紧不得有松动的要求。
换刀迅速
采用车削工具系统;
采用快换小刀夹。
迅速更换不同形式的切削部件,完成多种切削加工,提高生产效率。
刀片材料
刀片较多采用涂层刀片。
满足生产节拍要求,提高加工效率。
刀杆截形
刀杆较多采用正方形刀杆,但因刀架系统结构差异大,有的需采用专用刀杆。
刀杆与刀架系统匹配。
可转位车孔刀切削用量的选择
车孔刀的切削用量三要素及选用原则与外圆、端面车刀相同。
因内孔切削条件较差,故选用切削用量时应小于外圆切削。
加工Ø25mm以下的孔通常不采用大背吃刀量加工。
粗车的切削用量与长径比(刀杆伸出刀架长度与被加工孔径的比值)有关,这里只介绍当孔壁有足够刚性时粗车切削用量的推荐值。
半精车、精车常按图样要求选取用量。
1、背吃刀量的选用如下表所示
长径比
加工内孔时的背吃刀量为加工外圆时的百分比(%)
<2
80
2~3
65
3~4
50
4~5
30
2、进给量的选用如下表所示
长径比
加工内孔时的进给量为加工外圆时的百分比(%)
<2
75
2~3
60
3~4
45
4~5
30
3、切削速度的选用 在被加工直径相同的条件下,加工内孔的切削速度应是加工外圆的切削速度的70%~80%。
可转位车孔刀的选用要点
车孔刀与外圆车刀相比有如下特点:
1、由于尺寸受到孔径的限制,装夹部分结构要求简单、紧凑,夹紧件最好不外露,夹紧可靠。
2、刀杆悬臂使用,刚性差,为增强刀具刚性尽量选用大断面尺寸刀杆,减少刀杆长度。
3、内孔加工的断屑、排屑可靠性比外圆车刀更为重要,因而刀具头部要留有足够的排屑空间。
品种规格的选用 常用的车刀有三种不同截面形状的刀柄,即圆柄、矩形柄和正方形柄。
普通型和模块式的圆柄车刀多用于车削加工中心和数控车床上。
矩形和方形柄多用于普通车床。
还有一些特殊用途的车孔刀,如柄部有切削液输送孔的,柄部装有减振机构的和用于重金属做刀柄的等,但是不常用。
1、刀柄截面形状的选用。
优先选用圆柄车刀。
由于圆柄车刀的刀尖高度是刀柄高度的二分之一,且柄部为圆形,有利于排屑,故在加工相同直径的孔时圆柄车刀的刚性明显高于方柄车刀,所以在条件许可时应尽量采用圆柄车刀。
在卧式车床上因受四方刀架限制,一般多采用正方形或矩形柄车刀。
如用圆柄车刀,为使刀尖处于主轴中心线高度,当圆柄车刀顶部超过四方刀架的使用范围时,可增加辅具后再使用。
2、刀柄截面尺寸的选用。
标准内孔车刀已给定了最小加工孔径。
对于加工最大孔径范围,一般不超过比它大一个规格的车孔刀所定的最小加工孔径,如特殊需要,也应小于再大一个规格的使用范围。
3、刀柄形式的选用。
通常大量使用的是整体钢制刀柄,这时刀杆的伸出量应在刀杆直径的4倍以内。
当伸出量大于4倍或加工刚性差的工件时,应选用带有减振机构的刀柄。
如加工很高精度的孔,应选用重金属(如硬质合金)制造的刀柄,如在加工过程中刀尖部需要充分冷却,则应选用有切削液送孔的刀柄。
可转位车刀的头部形式及代号
代号
头部形式
代号
头部形式
A
90°直头侧切
F
90°偏头端切
B
75°直头侧切
G
90°偏头侧切
C
90°直头端切
H
107.5°偏头侧切
D
45°直头侧切
J
93°偏头侧切
E
60°直头侧切
K
75°偏头端切
L
95°偏头侧切及端切
T
60°偏头侧切
M
50°直头侧切
U
93°偏头端切
N
63°直头侧切
V
72.5°直头侧切
R
75°偏头侧切
W
60°偏头端切
S
45°偏头侧切
Y
85°偏头端切
可转位车刀的夹紧方式及代号
代号
刀片夹紧方式
C
装无孔刀片,从刀片上方将刀片夹紧,如压板式。
M
装圆孔刀片,从刀片上方并利用刀片孔将刀片夹紧,如楔沟式。
P
装圆孔刀片,利用刀片孔将刀片夹紧,如杠杆式、偏心式、拉垫式等。
S
装沉孔刀片,螺钉直接穿过刀片孔将刀片夹紧。
如压孔式。
用球面三角函数计算可转位刀具的空间角度
贺战涛 (发表于《工具技术》1998年10期)
在五坐标数控机床用普通刀具加工可转位刀具时常会遇到平面计算问题,常规解法是用换平面法和相量法,在此介绍一种用球面三角函数计算平面空间角度的方法。
1.建立数学模型
图1中,要加工出①、②、③、④面,仅需用立铣刀端齿加工出②、③面,①、④面便可由周齿同时加工出来。
根据刀体简图建立①、②、③面的数学模型如图2所示,ΔPQJ为①面,∠OQJ=α,∠PQJ=β,ΔPQK与ΔPQJ夹角为90°,ΔPQG与ΔPQJ夹角为(90°-λ),所以ΔPQK为②面,ΔPQG为③面。
2.用球面三角函数解ΔPQG如图3所示,以P点为中心做一任意半径的球面,球面与PQ、PJ、PG分别交于Q`,J`,G`点,所以可得出如下各角度值:
A=90°-λ,B=90°-α,C=γ,α=90°-θ,b=90°-ψ,c=90°-β,根据球面三角的余弦定理:
cosC=-cosAcosB-sinAsinBcosc,可解出γ值,根据正弦定理:
,可以解出θ、ψ值。
加工③、④面时,只需将工件绕Y轴旋转θ,绕X轴旋转(90°-γ),再沿角度ψ方向走刀即可。
在可转位刀具角度的计算中,只要是关于平面旋转的问题,均可用球面三角函数计算。
一种可转位型面铣刀的CAD/CAM方法
贺战涛 韩春钰(发表于《工具技术》2000年11期)
1、引言
铁道工业的发展,引起了大尺寸、大余量铸钢件加工和修理业的发展。
在道岔、钢轨、车轮毂、挂钩、心盘等零件的加工中使用了许许多多的可转位型面铣刀,这些铣刀的引入极大地提高了加工效率、降低了加工成本。
我单位近几年承接了多项铁道专用可转位型面铣刀的加工任务,在设计和加工过程中我们摸索出了一套适和自己的CAD/CAM方法,在此作以介绍。
2、型面铣刀的CAD/CAM
如图1所示,早先的型面铣刀的三维造型要在图形工作站上才能完成,近几年由于PC中CPU及显卡的性能的极大提高,在普通586机(基本配置PII266/64MRAM/4M显存以上的机型)上使用具有三维造型功能的软件如AutoCADR14就可实现型面铣刀的三维造型设计。
在设计中先根据被加工型面排出如图2所示的刀片排列图,再在空间展开成刀片组的三维立体图,最后生成每组刀片的空间状态图并标出各组刀片的参数来。
具体的设计流程如图4所示:
按以上的流程所设计出的刀具就可以满足加工的需要了。
刀体二维生产图从设计室传到生产分厂后即进入了生产阶段,在生产中我们使用了自己开发的《可转位型面铣刀的空间角度计算及加工建议》软件,程序员将生产图中的各刀片的参数主偏角、刃倾角、法后角、空间点位等信息输入计算机,计算机自动计算并打印出经过修正了的各刀片的空间角度、加工位置,加工建议(包括立卧铣选择、加工方向、合理的加工组合)等信息。
这些加工建议充分考虑到了机床的性能和加工范围,所以只须将这些值传入到加工型面铣刀的程序模块中即可生成加工程序了。
这些程序模块包括:
立铣加工计算模块、卧铣加工计算模块、加工中心空间点位换算模块等。
该软件的流程如图5所示:
以上的几个部分都可在PC中完成的,程序经串形通讯电缆传输到MAHO800C的工控机上就可以投入生产了。
3、此种方法的优点
无须高性能的图形工作站,普通的PC即可胜任;有固定模块,程序员的工作量很小,且无须专用数控编程软件的支持,手工编程即可完成复杂程序的编制;经济实用,使用方便,设计员和编程员很容易掌握;可方便地扩展到其他类型可转刀具的设计和加工中去。
加工刀具用数控机床的选择要点
贺战涛 张绍军 (发表于《工具技术》2000年10期)
[摘要]本文通过对几种典型刀具加工特点的分析,总结出加工刀具用数控机床的选择要点,使用户能够合理经济地从众多数控机床中作出选择。
[关键词]加工刀具,数控机床金属切削刀具的种类繁多,加工方法也多种多样,本文不可能对每种刀具的CNC加工设备都进行讨论,仅从以下三个方面进行论述:
1.需要几个数控轴;2.需要几个数控轴联动;3.需要什么数控系统。
一.需要几个数控轴
刀具一般可根据其外形分为回转刀具(如铣刀,钻头)和方形轮廓刀具(如车刀,镗刀),因而一般都需要X,Y,Z三个数控直线轴对其进行加工以保证其外形尺寸,有所区别的是对数控回转轴的要求。
加工复杂的可转位刀具体现得较为明显。
以加工可转位立铣刀工序中的数控铣削为例(参见图1):
绝大多数可转位立铣刀都有数个(条)均布的切削齿,在每个齿加工完毕后都应对其进行分度旋转(如图1所示B轴)进行下一个(条)齿的加工。
如果CNC铣床没有数控分度头或数控回转工作台,则应在程序中加入无条件停止指令,机床运动停止后通过人工旋转精密手动分度头实现分度旋转(应注意机床外罩锁的影响),然后继续执行NC程序。
精度一般能够满足要求。
但这样会增加工人劳动强度,同时影响工作效率。
如果CNC铣床有数控分度头或数控回转工作台,则分度旋转运动可通过程序中的数控指令实现,精度和效率都较高,但增加一个CNC回转轴也会使CNC铣床的结构复杂化,CNC系统功能增加,大为增加CNC铣床的价格。
需要指出的是,精密手动分度头的分度能力是有限的,特别是对于非整数的角度往往无法满足要求(可转位成形铣刀此类情况较多),此时只能用CNC回转轴实现。
此类CNC回转轴一般用交流伺服电机驱动精密蜗杆副,液压或气动夹紧,高精度编码器作为角度检测元件,因而具备在行程范围内任意角度的旋转功能。
而采用端面齿盘定位的CNC回转轴却只能进行等分转度,不适用于此类情况。
某些可转位立铣刀有刃倾角λs,在铣削刀片槽或容屑槽时都应将槽底面转刃倾角λs,使其与CNC铣刀轴线垂直,此时需要一个回转轴(如图1所示A轴)旋转刃倾角λs。
受精密手动分度头的装夹结构和刚性的限制,将其作为A轴效果不佳。
因此应选择具有较高刚性的CNC回转轴作为A轴。
可见如果某CNC铣床加工的可转位刀具品种单一且无刃倾角,可以选择3轴CNC(X,Y,Z)铣床加精密手动分度头,可降低加工成本。
否则应选择5轴CNC铣床(X,Y,Z,A,B)。
二.需要几个数控轴联动
CNC系统的若干轴联动插补功能最能体现CNC系统的性能和其档次高低,也往往决定着CNC系统的价格,因此应根据加工刀具产品的具体情况来仔细选择。
对于加工一般可转位刀具的CNC铣床而言,具有2个直线轴的直线和圆弧插补功能就可以加工几乎所有的ISO标准刀片槽形式,其它运动都可单轴插补完成。
如果也选择多达5-6轴联动的CNC系统则没有必要。
要求比较高的是一些螺旋类精加工刀具。
以下以加工"等螺旋角等前角锥度立铣刀"为例(参见图2):
从图2中可以看出,若要加工(含铣削及磨削)这种立铣刀,CNC机床应具备:
X轴和A轴联动插补切削螺旋槽;Z轴:
X-A插补时也参加插补保证每个截面螺旋角相等;Y轴:
由于前角γ0>0且轴向每个截面半径都不相等从而使偏移量e也处处不相等,为保证每个截面前角都相等,X-A-Z联动时Y轴也要参加插补运动。
因此CNC机床应具备"X-Y-Z-A"4轴联动的插补功能。
同理可知:
"X-Y-Z-A-B"5轴联动插补可完成同上的球头立铣刀的加工。
三.需要什么数控系统
加工一般精度的可转位刀具,选择具有间隙补偿和螺距误差补偿的半闭环CNC系统的数控机床就可以满足要求,而对较高精度刀具(如整体材质的精加工刀具)的精加工可以选择闭环CNC系统。
需要注意的是:
为编程方便,CNC编程软件系统都应具有工件坐标系的平移和旋转功能,并支持几何线性的多种表达方式。
现代CNC系统的编程方法较多,相对而言,以ISO标准G,M代码编程的CNC系统具有较大的灵活性,能满足多品种中小批量的生产要求,但初期编程速度较慢,机床准备工作时间较长。
而具有针对某类刀具产品开发的专业化软件包的CNC系统则可以满足某些复杂刀具的大批量加工,生产效率高,对人员素质要求较低,但价格昂贵且需要不断升级软件包以满足出现的新产品。
选择CNC系统时还应注意:
现代CNC系统的功能较多,可以根据实际情况去掉一些基本不用或近期很少用到的功能(例如某些用于FMS的接口和软件)以降低购买成本。
以上通过几个例子讨论了针对加工刀具产品的CNC机床选择方法和大概原则,实际情况远不止这些。
总之应根据产品具体情况灵活地作出选择,以满足市场对精度和成本的双重要求。
中国工具信息网
英格索尔(Ingersoll)
陕西省刀具协会
伊斯卡(Iscarmill)
成都工具研究所
威迪亚(Widia)
陕硬公