化学工程与工艺实习报告.docx
《化学工程与工艺实习报告.docx》由会员分享,可在线阅读,更多相关《化学工程与工艺实习报告.docx(16页珍藏版)》请在冰豆网上搜索。
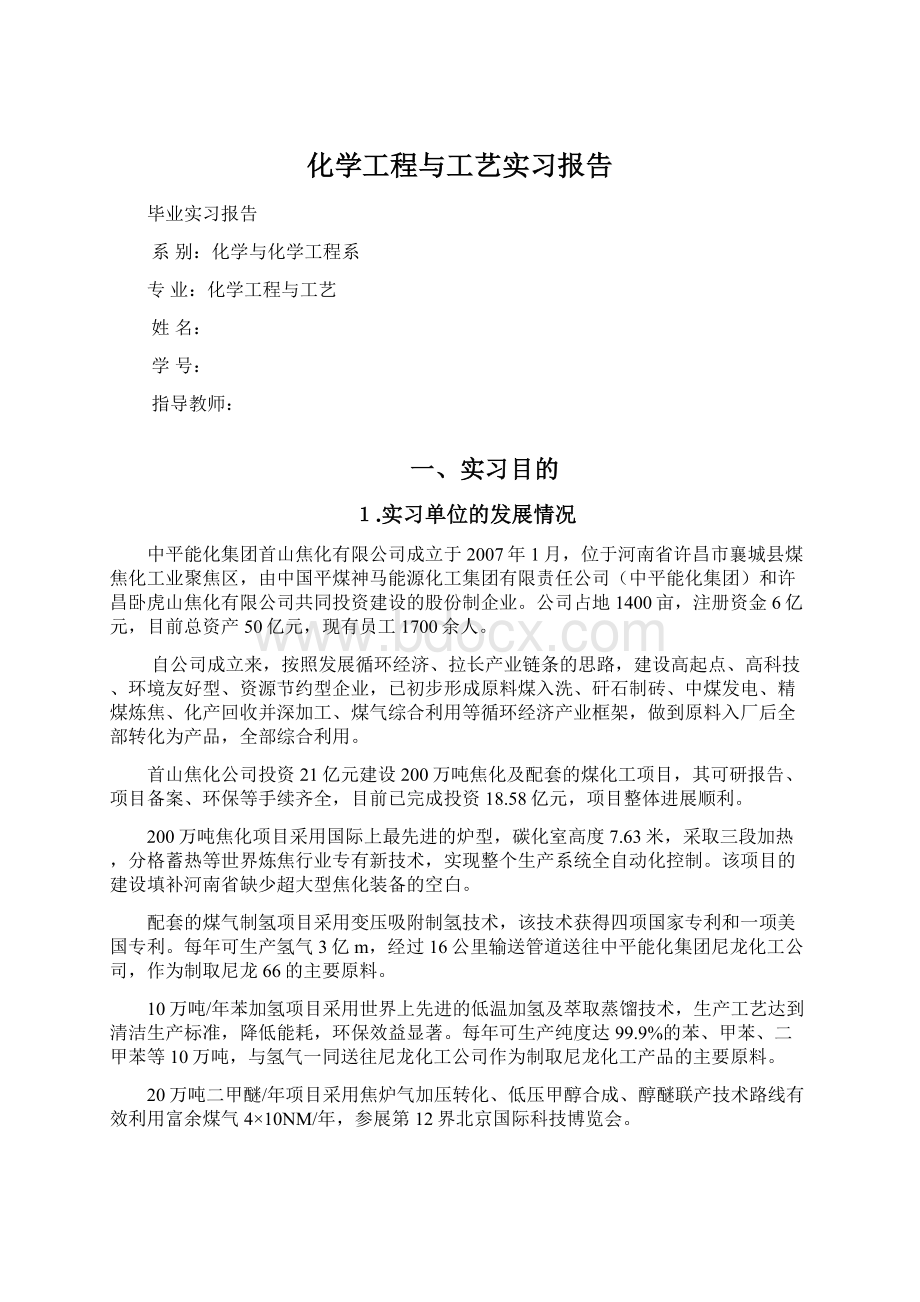
化学工程与工艺实习报告
毕业实习报告
系别:
化学与化学工程系
专业:
化学工程与工艺
姓名:
学号:
指导教师:
一、实习目的
1.实习单位的发展情况
中平能化集团首山焦化有限公司成立于2007年1月,位于河南省许昌市襄城县煤焦化工业聚焦区,由中国平煤神马能源化工集团有限责任公司(中平能化集团)和许昌卧虎山焦化有限公司共同投资建设的股份制企业。
公司占地1400亩,注册资金6亿元,目前总资产50亿元,现有员工1700余人。
自公司成立来,按照发展循环经济、拉长产业链条的思路,建设高起点、高科技、环境友好型、资源节约型企业,已初步形成原料煤入洗、矸石制砖、中煤发电、精煤炼焦、化产回收并深加工、煤气综合利用等循环经济产业框架,做到原料入厂后全部转化为产品,全部综合利用。
首山焦化公司投资21亿元建设200万吨焦化及配套的煤化工项目,其可研报告、项目备案、环保等手续齐全,目前已完成投资18.58亿元,项目整体进展顺利。
200万吨焦化项目采用国际上最先进的炉型,碳化室高度7.63米,采取三段加热,分格蓄热等世界炼焦行业专有新技术,实现整个生产系统全自动化控制。
该项目的建设填补河南省缺少超大型焦化装备的空白。
配套的煤气制氢项目采用变压吸附制氢技术,该技术获得四项国家专利和一项美国专利。
每年可生产氢气3亿m,经过16公里输送管道送往中平能化集团尼龙化工公司,作为制取尼龙66的主要原料。
10万吨/年苯加氢项目采用世界上先进的低温加氢及萃取蒸馏技术,生产工艺达到清洁生产标准,降低能耗,环保效益显著。
每年可生产纯度达99.9%的苯、甲苯、二甲苯等10万吨,与氢气一同送往尼龙化工公司作为制取尼龙化工产品的主要原料。
20万吨二甲醚/年项目采用焦炉气加压转化、低压甲醇合成、醇醚联产技术路线有效利用富余煤气4×10NM/年,参展第12界北京国际科技博览会。
该项目投产后,每年可生产焦炭200万吨、氢气3亿m、精苯10万吨、甲醇10万吨、二甲醚20万吨,实现年销售收入80亿元,利税18亿元。
煤化工产业园实现资源的节约、集约最大化利用,进一步拉长煤化工循环经济产业链条,实现经济效益和社会效益的双赢。
2.实习要求
1、注意安全。
实习期间不允许单独行动,严格遵守实习单位的安全条例和各项
规章制度,遇到突发事件要及时向带队老师报告。
实习期间要作到一切行动
听指挥,尊重工人师傅,虚心向工人师傅请教。
2、不迟到,不早退,有事须向老师请假。
3、学生在掌握化工理论和确定设计(论文)题目的基础上,深入生产一线直接
参与设计(论文)相关的化工生产过程,进一步掌握与设计(论文)内容相
关化工生产的规律,熟悉其流程、参数、设备及生产过程及配套设施。
4、了解设计过程,查阅设计文件(图纸)并收集有关数据、资料。
5、保证毕业实习时间,实习结束后,提交实习报告。
3.实习目的和意义
在掌握化工理论和确定设计题目的基础上,深入生产一线直接参与与设计相关的化工生产过程,进一步掌握与设计内容相关化工生产的规律,熟悉其流程、参数、设备及生产过程及配套设施。
了解设计过程,查阅设计文件(图纸)并收集有关数据、资料。
理解和掌握化工生产开、停车、正常操作、事故处理等操作步骤。
掌握化工生产过程中,重要的监测和控制生产过程的仪表的工作过程,了解其工作原理,理解化工仪表及自动化在化工生产过程中的作用。
进一步掌握与设计相关的化工生产装置工艺流程、主要设备的结构、原理及主要工艺操作参数。
了解化工装置及化工厂的设计过程(设计阶段及设计内容),初步熟悉与毕业设计内容相关的设计文件及设计图纸。
在进行毕业设计之前,通过毕业实习有针对性的以比较长的时间参与化工生产过程及化工单元操作,使我们对设计方向的化工生产单元操作的理论计算的理解和掌握更加深刻和熟练,为毕业设计奠定坚实的基础。
二.实习内容
1.甲醇合成工艺的发展历史和技术水平现状
国外甲醇工艺技术,多以天然气为原料生产的甲醇,因此国外公司的甲醇技术均集中于天然气制甲醇。
国际上广泛采用的先进的甲醇生产工艺技术主要有:
DAVY(原I.C.I)、OPSOE、Uhde、Lurgi公司甲醇技术等,不同甲醇技术的消耗及能耗差异不大,其主要的差异在于所采用的主要设备甲醇合成塔的类型不同。
国内现有甲醇生产厂家100多家,但其中大多数是因为生产成本高、设备效益能力低等原因,部份技术落后、设备老旧、产能小的生产设备已经显现出将被淘汰的趋势较大的有上海焦化有限公司以煤为原料的生产装置;中石化四川维尼纶厂以乙炔尾气和天然气为原料的生产设备;以天然气为原料的甲醇生产企业还有陕西榆林天然气化工公司、大庆油田甲醇厂、陕西长庆油田、四川江油甲醇厂等,生产规模多在10万公吨/年左右,其它生产设备大多数采用联醇技术,生产规模多在1~5万公吨/年。
1995年以来,国内甲醇工业发展迅速,生产所用原料由联醇法的合成气为主,向天然气和煤为主的方向发展,其主要发展因素是新天然气田的开发,如新疆、四川、内蒙等。
另外由于国内甲醇下游产品的开发生产,如甲醛、烯烃、醋酸、甲酯系列、民用/汽车燃料等,以及西南化工研究院和南化公司研究甲醇催化剂的开发生产。
有多家以煤或天然气为原料的甲醇计画在申报和筹备之中,其中有6个设备规模在10万公吨/年以上,最大的为60万公吨/年。
拟建装置总产能为213万公吨/年。
我国是煤丰富的国家,甲醇原料采用天然气和煤的较多。
产量几乎各占一半。
生产工艺有单产甲醇和联产甲醇两种。
联产甲醇除在合成氨装置联产甲醇外,还可利用化工厂尾气或结合城市煤气联产甲醇。
煤与焦炭是制造甲醇粗原料气的主要固体燃料.用煤和焦炭制甲醇的工艺路线包括燃料的气化、气体的脱硫、变换、脱碳及甲醇合成与精制.
用蒸汽与氧气(或空气、富氧空气)对煤、焦炭进行热加工称为固体燃料气化,气化所得可燃性气体通称煤气是制造甲醇的初始原料气,气化的主要设备是煤气发生炉,按煤在炉中的运动方式,气化方法可分为固定床(移动床)气化法、流化床气化法和气流床气化法.国内用煤与焦炭制甲醇的煤气化——般都沿用固定床间歇气化法,煤气炉沿用UCJ炉.在国外对于煤的气化,已工业化的煤气化炉有柯柏斯-托切克(Koppers-Totzek)、鲁奇(Lurge)及温克勒(Winkler)三种.还有第二、第三代煤气化炉的炉型主要有德士古(Texaco)及谢尔-柯柏斯(Shell--Koppers)等.
用煤和焦炭制得的粗原料气组分中氢碳比太低,故在气体脱硫后要经过变换工序.使过量的一氧化碳变换为氢气和二氧化碳,再经脱碳工序将过量的二氧化碳除去.原料气经过压缩、甲醇合成与精馏精制后制得甲醇.
工业上几乎都是采用一氧化碳、二氧化碳加压催化氢化法合成甲醇.典型的流程包括原料气制造、原料气净化、甲醇合成、粗甲醇精馏等工序.天然气、石脑油、重油、煤及其加工产品(焦炭、焦炉煤气)、乙炔尾气等均可作为生产甲醇合成气的原料.天然气与石脑油的蒸气转化需在结构复杂造价很高的转化炉中进行.转化炉设置有辐射室与对流室,在高温,催化剂存在下进行烃类蒸气转化反应.重油部分氧化需在高温气化炉中进行.以固体燃料为原料时,可用间歇气化或连续气化制水煤气.间歇气化法以空气、蒸汽为气化剂,将吹风、制气阶段分开进行,连续气化以氧气、蒸汽为气化剂,过程连续进行.
甲醇生产中所使用的多种催化剂,如天然气与石脑油蒸气转化催化剂、甲醇合成催化剂都易受硫化物毒害而失去活性,必须将硫化物除净.气体脱硫方法可分为两类,一类是干法脱硫,一类是湿法脱硫.干法脱硫设备简单,但由于反应速率较慢,设备比较庞大,湿法脱硫可分为物理吸收法、化学吸收法与直接氧化法三类,也有将干法与湿法两者结合起来的方法。
甲醇的合成是在高温、高压、催化剂存在下进行的,是典型的复合气-固相催化反应过程.随着甲醇合成催化剂技术的不断发展,总的趋势是由高压向低、中压发展.
我们所在的甲醇厂就是以焦炉煤气为原料气用低压合成法合成的甲醇,大致分为五个工段:
空气分离、粗脱硫、精脱硫、合成气转化、甲醇的合成。
2.甲醇合成工艺流程概述
2.1空气分离流程
由空压机来的高温空气经空冷塔温度降至15.5℃,脱去其中的游离水后进入分子筛纯化系统。
在纯化系统采用变温吸附法连续分离空气中的水分和CO2,干燥空气分三路:
一路入增压机,增压后的空气入增压机冷却器,冷却到所需温度进入主换热器,换热后入透平膨胀机,膨胀后进入上塔参与精馏。
一路供仪表气源,绝大部分气体经主换热器,换热后去下塔,在下塔顶部获得氮气,经冷凝器蒸发器,冷凝的液体部分作为下塔的回流液,一部分经过冷凝过热后,再节流作为上塔的回流液送至上塔,在下塔底部获得富氧液空,经过冷凝过冷后,节流送至上塔中部参与精馏。
经上塔精馏顶部得到产品N2,在上塔中上部得到产品污氮气。
氮气及污氮气经过冷器、主换热器、组复热,复热后,N2除一部分送往用户管网,其余均入水冷塔制冷,而污氮气除一部分作再生气外,其余均入水冷塔制冷,在上塔底部得到O2后,经主换热器复热后,入氧气缓冲罐平衡筒,经氧压机吸入加压到2.5Mpa后,进入输气管网,液氧以冷凝蒸发器底部抽出,进量筒入储槽。
空分流程简要表述:
空气→自洁式空气过滤器→空气压缩机组→遇冷系统→纯化系统→分馏塔系统→氧气、液氧、氮气
2.2空分车间“3停”紧急预案
1.停水
循环水停止供水,空压机连锁停机,预冷系统连锁停机,紧急措施:
1 倒换仪表气源。
2 停止产品压缩机运转(氧、氮压缩机),打开放空关送出。
3 停膨胀机,全开增压机回流阀,关闭紧急切断阀,关闭出口阀。
4 关闭液体排放阀。
5 封闭分馏塔系统,根据塔内情况开产品放空阀。
6 停止纯化器再生,关闭所有阀门,并使吸附器内保压。
7 进一步将空压机送出阀关闭,全开放空及防喘振阀。
8 预冷系统所有阀门关闭,注意空冷塔液位情况。
9 查明停水原因后,根据各设备温度变化再停开车,并视停车时间长短,
决定系统是否加温吹除。
2.停电
所有电机驱动设备停止运转,精馏系统阻力下降,紧急措施:
1 倒换仪表气源。
2 停止产品压缩机运转(氧、氮压缩机),打开放空关送出。
3 全开增压机回流阀,关闭紧急切断阀,关闭进出口阀。
4 封闭分馏塔系统,根据塔内情况开产品放空阀。
5 关闭液体排放阀。
6 停止纯化器再生,关闭所有阀门,并使吸附器内保压。
7 进一步将空压机送出阀关闭,全开放空及防喘振阀。
8 预冷系统所有阀门关闭,注意空冷塔液位情况。
9 将全部电机启动按钮,确定车停车位置。
10 电源故障排除后,视停电时间长短,决定是否对系统加温吹除。
3.停气
空气压缩机停气,无法往后工序提供加压空气,若产品气压缩机继续运转,会造成管道负压,另外排气压力低会造成预冷系统水泵、冷水机连锁停机,膨胀机转速下降进而停车,紧急措施:
1 倒换仪表气源。
2 停膨胀机油泵。
3 停止产品压缩机运转(氧、氮压缩机)。
4 进一步停膨胀机,全开增压机回流阀,关闭紧急切断阀,关闭进出口阀。
5 关闭液体排放阀。
6 封闭分馏塔系统,根据塔内情况开产品放空阀。
7 停止纯化器再生,关闭所有阀门,并使吸附器内保压。
8 进一步将空压机送出阀关闭,全开放空及防喘振阀。
9 预冷系统所有阀门关闭,注意空冷塔液位情况。
空压机停气原因处理后,停开车视停车时间长短,决定是否对系统加温吹除。
2.3粗脱硫工艺流程
采用PDS+栲胶碳酸钠湿法脱硫技术,将来自焦炉的粗煤气依次串连进入脱硫塔下部
与塔顶喷淋下来的脱硫液逆流接触洗涤,吸收煤气中的H2S、HCN等物质,脱除硫化氢的
煤气送至后续工段。
粗脱硫工艺流程:
来自洗脱苯工段的粗煤气依次串连进入脱硫塔下部与塔顶喷淋下来的脱硫液逆流接触洗涤,吸收煤气中的H2S、HCN等物质,脱除硫化氢的煤气送至后续工段。
从脱硫塔流出的脱硫液经脱硫塔液封槽后送入溶液循环槽,加入Na2CO3溶液与由催化剂贮槽补充滴加的催化剂溶液后,冬季用溶液循环泵抽送到溶液换热器进行加热,使溶液保持在30~35℃左右进入再生塔再生。
自空压站来的压缩空气与脱硫富液由再生塔下部并流入再生塔对脱硫液氧化再生,再生后的脱硫贫液返回脱硫塔塔顶喷淋。
非冬季时,溶液循环泵抽送的脱硫富液直接送至再生塔再生。
从再生塔顶浮选出的硫泡沫自流入硫泡沫槽,在此经搅拌、加热、沉降、分离,硫泡沫自流入三足刮刀自动下卸料离心机,生产硫膏,人工包装外售。
离心机排出的清液进入低位槽,定期分析,根据结果由低位槽液下泵送至溶液循环泵循环使用,或送至锅炉房煤场喷洒用水。
粗脱硫岗位开车流程:
①用脱硫液注满脱硫塔塔底及水封槽。
②关闭煤气交通阀,打开煤气出入口阀门。
③全开溶液循环槽A,B出入口阀门,脱硫塔出口阀全开,溶液循环泵入口阀全开。
④稍开脱硫液入口阀,全开脱硫液自调阀截止阀。
⑤按正常开泵启动循环泵,稍开泵出口阀。
注意泵的出口压力≧0.5Mpa,流量稳定,
电流<18.7A。
⑥打开脱硫塔脱硫液入口阀调节入脱硫塔流量(流量根据化验室的结果进行调节)。
⑦待脱硫塔塔液位正常后,打开压缩空气前后截止阀及入再生塔空气自调阀,缓慢
加入空气(空气量根据硫泡沫产生情况及再生塔液位进行调节)。
⑧脱硫塔的开塔与停塔步骤
开塔操作:
①检查塔人孔是否封好,水封槽及塔底是否已灌满水,能否封住煤气,打开塔顶放
散阀。
②打开氮气清扫阀,用氮气赶净塔内的空气,通知化验室从放散管取样口取出做含
氧分析直至合格。
③稍开煤气进出口阀,用煤气置换塔内的氮气,待塔顶放散管冒出大量煤气,通知
化验室取样,做煤气爆炸试验合格后,关闭放散管,全开出入口阀门,关闭交通
管阀门,注意风机后压力变化及脱硫塔阻力。
④待塔内煤气正常后,启动脱硫液循环泵,并调节循环量,使之符合技术规定。
停塔操作:
①先停止循环泵运转并关闭泵的出入口阀门。
②启动脱硫塔煤气交通管阀门。
③关闭脱硫塔煤气出入口阀门。
④若要长期停塔或进塔内施工检修,用蒸汽或氮气进行扫除。
直至放散管有蒸汽或
氮气冒出,关闭蒸汽或氮气阀,再打开塔下部人孔通风,待化验室化验合格后,
方可入塔内施工。
遇到突然停电的紧急操作:
①某泵电机设备电路发生故障,则开启备用泵,然后通知电工维修。
②短期停电,先切断电源,关闭泵出口阀门。
③当脱硫塔堵塔,可将再生塔来的脱硫液通过交通管引入脱硫塔维持生产。
④当脱硫塔堵塔时,可通过贫、富液槽的吸入管倒用,维持生产。
⑤当脱硫塔堵塔时,可用热贫液冲塔,联系PDS厂家,用清塔剂洗塔。
粗脱硫岗位正常生产时控制要点:
①控制各项工艺指标达到要求
②控制再生塔液位及溢流情况
③控制压缩空气流量与压力
④根据煤气量的多少,而增大喷淋密度
⑤根据进工段H2S含量多少,适量加碱加药,加大脱硫液循环量
2.3精脱硫工艺流程
精脱硫原理:
铁钼触媒对有机硫及烯烃的加氢转化反应:
RSH+H2=RH+H2S+Q
RSR’+2H2=RH+R’H+H2S+Q
C4H4S+4H2=C4H10+H2S+Q
CS2+4H2=CH4+2H2S+Q
COS+H2=CO+H2S+Q
C2H4+H2=C2H6+Q
以上反应平衡常数都很大,在操作温度为350~430℃的条件下,有机硫的转化是很完全的。
有机硫加氢转化反应速度随硫化物种类不同而有很大差异,其中噻吩的加氢反应速度很慢,因此有机硫加氢反应速度取决于噻吩加氢反应速度。
氧化铁对H2S的吸收反应:
3Fe2O3+H2=2Fe3O4+H2O
Fe3O4+H2+3H2S=3FeS+4H2O
氧化锌对H2S的吸收反应:
氧化锌除对H2S的吸收作用外,还对有机硫有吸收作用,其可与硫化物反应生成十分稳定的ZnS。
ZnO+H2S=ZnS+H2O+Q
ZnO+COS=ZnS+CO2+Q
ZnO+C2H5SH=ZnS+C2H4+H2O+Q
2ZnO+CS2=2ZnS+CO2+Q
精脱硫工艺流程:
由焦炉气压缩机送来的焦炉气含有H2S≦20mg/m3和CS2、COS、RSH、C4H4S等有机硫≦250mg/m3,其压力为2.5Mpa,温度40℃,首先经过过滤器过滤气体中残余的焦油雾滴,再经预脱硫槽脱出无机硫之后送至转化装置焦炉气初预热器提温到300℃左右,经转化装置焦炉气初预热器提温的气体返回精脱硫装置经一级加氢预转化器和一级加氢转化器,气体中的有机硫大部分在此转化为无机硫。
另外,气体中的氧也在此与氢反应生成水,不饱和烃加氢饱和。
加氢转化后的气体进入中温脱硫槽,除去绝大部分的无机硫,此时气体中的总硫含量约35mg/m3,之后经过二级加氢转化器进一步加氢转化。
中温氧化锌脱硫剂把关,使气体中的总硫<0.1ppm。
出氧化锌脱硫槽的气体压力约2.3Mpa,温度约为380℃送至转化岗位。
精脱硫岗位的生产过程:
①用过滤器分离焦炉气油水。
②用预脱硫槽吸收H2S。
③利用铁钼触媒进行有机硫一级加氢转化生产H2S。
④利用氧化铁吸收H2S。
⑤利用铁钼触媒进行有机硫二级加氢转化生产H2S。
⑥利用氧化锌吸收H2S,进行最终把关,使精脱硫焦炉气中总硫含量<0.1ppm。
2.4转化工艺流程
转化原理:
采用加压催化部分氧化法,一定温度和压力条件下的焦炉煤气和蒸汽混合气体进入转化炉后,与适量的氧气混合在转化炉燃烧室内(催化剂层上部空间),部分可燃气体与氧气进行剧烈燃烧反应。
反应如下:
2H2+O2=2H2O+115.48kcal
2CH4+O2=2CO+4H2+17.0kcal
放出的热量使气体温度骤然升高,氧气几乎全部反应掉,在此高温下甲烷与蒸汽发生转化反应:
CH4+H2O(g)=CO+3H2-49.3kcal
CH4+2H2O(g)=CO2+4H2-39.5kcal
CH4+CO2=2CO+2H2-59.1kcal
CO+H2O=CO2+H2+9.8kcal
转化工艺流程简述:
焦炉气
来自压缩岗位的焦炉气,温度40℃,压力为2.5Mpa,流量31000m3/h,甲烷含量23%~26%,经过滤器再去预脱硫槽后去焦炉气初预热器加热至300℃后,送往精脱硫岗位脱出有机硫和无机硫。
脱硫后的焦炉气,压力约2.3Mpa,温度380℃返回转化岗位。
为使甲烷转化反应的需要,同时为防止焦炉气在高温下析碳,在焦炉气中加入3.0Mpa的饱和蒸汽,蒸汽流量根据焦炉气的流量来调节。
加入蒸汽后的焦炉气经焦炉气预热器加热至500℃后,再经预热炉预热至520℃~660℃左右进入转化炉上部。
氧气
来自空分岗位的氧气,温度100℃,压力约2.5Mpa,流量5197m3/h,加入预热炉预热后的过热蒸汽,进入转化炉上部,氧气流量根据转化炉出口温度来调节。
燃料气
来自甲醇合成的驰放气(或来自气柜前的燃料煤气)经燃料气混合器后,进入预热炉底部,与空气鼓风机来的空气混合后燃烧,为焦炉气和水蒸汽预热提供热量。
经燃料气混合器后的燃料气一部分送精脱硫升温炉做燃料。
脱盐水
来自脱盐水站的脱盐水主要分三条管线。
第一条管线经过脱盐水预热器去除氧站;第二条管线去往冷凝液冷却器;第三条管线一部分作为废热锅炉的冷却水,另一部分作为转化炉的夹套水冷却。
除此之外,事故水槽和烧嘴保护泵的用水水管也是连接在脱盐水的第一条管线上。
锅炉给水
来自脱氧站给水,温度104℃,压力约4.2Mpa,经锅炉给水预热器预热至190℃,一部分去往甲醇合成;另一部分经废锅的汽包进入废锅生产中压蒸汽。
废锅所生产的234℃、3.0Mpa的饱和蒸汽除提供给本工段用气外,富余的蒸汽经减温减压装置后送往蒸汽管网。
冷凝液
经锅炉给水预热器降温的转化气经采暖水加热器,再经转化气冷却器后进入分离器分离出一部分冷凝液,转化气再经过脱盐水预热器后进入气液分离器分离出另外一部分冷凝液。
两部分冷凝液进入汽提塔,再经冷凝液泵送往冷凝液冷却器之后,冷凝液送往合成。
采暖水
采暖水来自外管经采暖水加热器加热后去外管。
转化气
焦炉气和氧气分别进入转化炉后发生转化反应,生成的转化气温度985℃,压力约2.2Mpa,残余甲烷含量<0.6%,由转化炉底部进入废热锅炉回收热量副产蒸汽。
转化气温度降为540℃,然后经焦炉气预热器加热焦炉气,温度降至300℃,再进入焦炉气初预热器加热原料焦炉气,温度降至280℃后,经锅炉给水预热器加热锅炉给水,温度降为161℃,经过采暖水加热器加热采暖水,温度降为100℃或经转化器冷却器温度降为100℃,进入分离器分离冷凝液,再进入脱盐水预热器进一步回收反应热后,转化气温度降为40℃,经气液分离器进一步分离工艺冷凝液后进入常温氧化锌脱硫槽,出脱硫槽的转化气温度为40℃,压力2.0Mpa,送往合成气压缩机岗位。
紧急停车步骤:
①接通知,切除氧化锌脱硫槽,气体在气液分离器放空。
②转化炉依次切氧气工艺气,精脱硫保温保压,焦炉气在入精脱硫前放空。
③利用自产蒸汽、外来蒸汽,按降温要求进行降温。
如停车时间很短则可将转化炉
出口温度降至600~650℃之后保温保压,如停车时间较长则将温度降至500℃以
下或按停车要求进行。
预热炉可维持火咀或灭火。
④水系统要及时调节供水量,转化炉停止降温或温度较低,汽包液位较难控制时可
将自产蒸汽就地放空,关死汽包出口阀门。
⑤各自动自调仪表打至手动位置。
2.5甲醇合成工艺流程
甲醇生产原理:
甲醇合成工艺气体中的CO、CO2分别与H2在铜基催化剂的作用下主要生成甲醇,同时还伴有多种副反应。
主反应:
CO+2H2=CH3OH+Q
CO2+3H2=CH3OH+H2O+Q
主要副反应:
2CO+4H2=CH3OCH3+H2O
4CO+8H2=C4H9OH+3H2O
CO+3H2=CH4+H2O
2CO+2H2=CH4+CO2
从合成反应来看,其主要的反应特点为:
①体积缩小的反应
②放热反应
③可逆反应
④气固相催化反应
⑤伴有多种副反应的发生
⑥合成工艺流程简述:
来自合成气压缩的合成气,经气气换热器预热到225℃左右,进入甲醇合成塔,在催化剂的作用下进行甲醇合成反应。
甲醇合成塔为管壳式反应器,管内填装触媒,反应管外为沸腾热水,利用反应热副产中压饱和蒸汽。
合成塔出口气体进气气换热器与合成塔入口气体换热,把入口气体加热到活性温度上,同时合成塔出口气体温度降至99℃,经蒸发式冷却器冷却到40℃后,进入甲醇分离器进行气液分离。
出甲醇分离器气体大部分作为循环气去合成气压缩增压并补充新鲜气,一小部分作为驰放气,进入洗醇塔底部,与塔顶喷淋下来的水逆流接触,气体中的甲醇溶解在水中,形成烯醇水从塔底排出。
从洗醇塔顶出来的气体,压力约5.4Mpa,经两级减压至0.2Mpa后,一部分送往转化装置作燃料气,其余送往焦炉燃烧。
洗醇塔底出来的烯醇水送往下一工段。
甲醇分离器底部出来的粗甲醇经一级过滤器和二级过滤器滤除其中的固体杂质后,通过分离器液位调节阀减压至0.7Mpa送往下一工段。
甲醇合成塔壳侧出来的气液混合物经上升管进入汽包进行气液分离,分离下来的水循环返回合成塔,蒸汽经减温减压后进入低压蒸汽管网。
合成塔内温度高的原因及处理方法:
温度高原因:
(1)循环量太小
(2)系统加量(3)CO上升(4)汽包压力上涨(5)锅炉水泵异常锅炉水量