冲压机控制系统.docx
《冲压机控制系统.docx》由会员分享,可在线阅读,更多相关《冲压机控制系统.docx(25页珍藏版)》请在冰豆网上搜索。
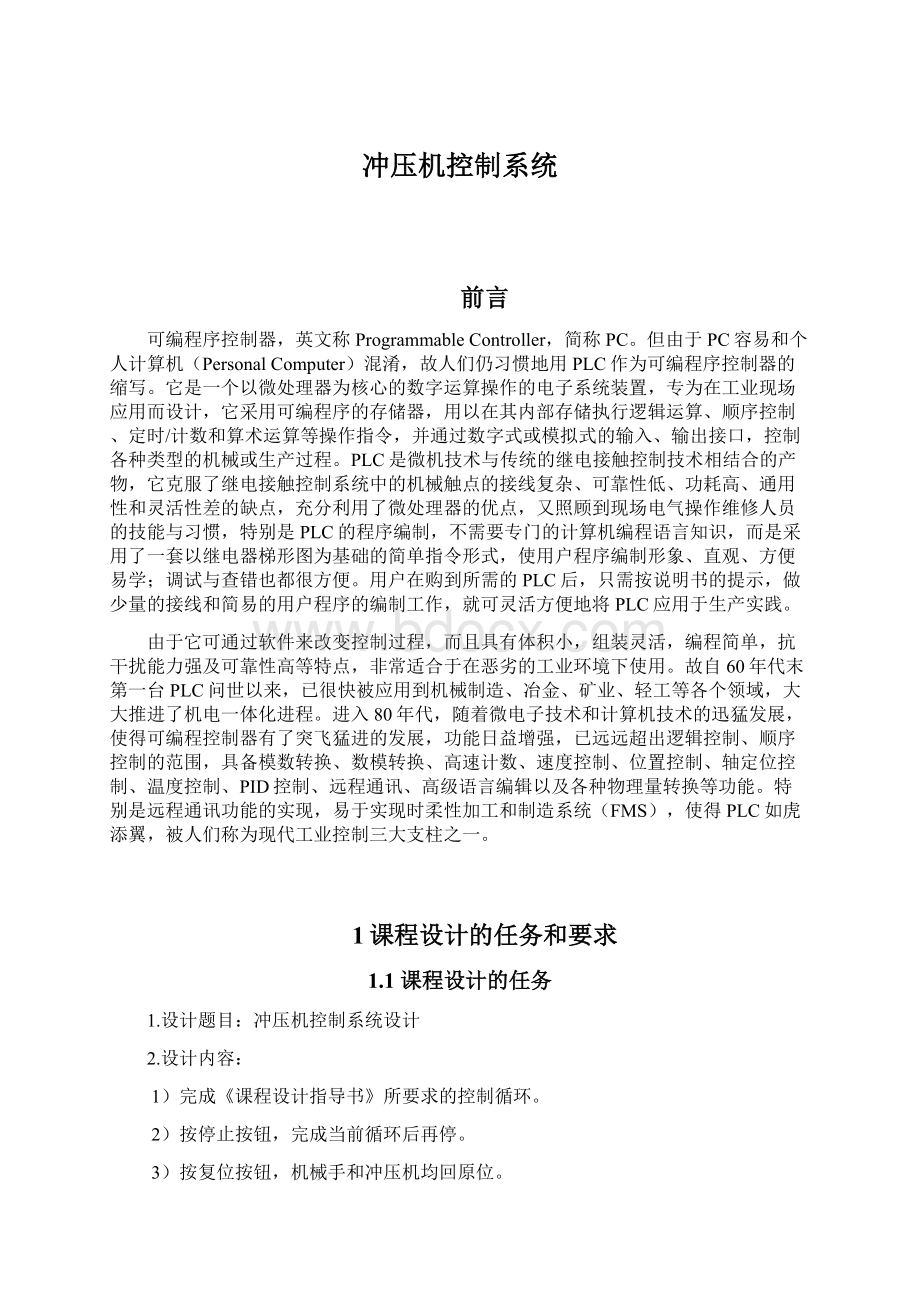
冲压机控制系统
前言
可编程序控制器,英文称ProgrammableController,简称PC。
但由于PC容易和个人计算机(PersonalComputer)混淆,故人们仍习惯地用PLC作为可编程序控制器的缩写。
它是一个以微处理器为核心的数字运算操作的电子系统装置,专为在工业现场应用而设计,它采用可编程序的存储器,用以在其内部存储执行逻辑运算、顺序控制、定时/计数和算术运算等操作指令,并通过数字式或模拟式的输入、输出接口,控制各种类型的机械或生产过程。
PLC是微机技术与传统的继电接触控制技术相结合的产物,它克服了继电接触控制系统中的机械触点的接线复杂、可靠性低、功耗高、通用性和灵活性差的缺点,充分利用了微处理器的优点,又照顾到现场电气操作维修人员的技能与习惯,特别是PLC的程序编制,不需要专门的计算机编程语言知识,而是采用了一套以继电器梯形图为基础的简单指令形式,使用户程序编制形象、直观、方便易学;调试与查错也都很方便。
用户在购到所需的PLC后,只需按说明书的提示,做少量的接线和简易的用户程序的编制工作,就可灵活方便地将PLC应用于生产实践。
由于它可通过软件来改变控制过程,而且具有体积小,组装灵活,编程简单,抗干扰能力强及可靠性高等特点,非常适合于在恶劣的工业环境下使用。
故自60年代末第一台PLC问世以来,已很快被应用到机械制造、冶金、矿业、轻工等各个领域,大大推进了机电一体化进程。
进入80年代,随着微电子技术和计算机技术的迅猛发展,使得可编程控制器有了突飞猛进的发展,功能日益增强,已远远超出逻辑控制、顺序控制的范围,具备模数转换、数模转换、高速计数、速度控制、位置控制、轴定位控制、温度控制、PID控制、远程通讯、高级语言编辑以及各种物理量转换等功能。
特别是远程通讯功能的实现,易于实现时柔性加工和制造系统(FMS),使得PLC如虎添翼,被人们称为现代工业控制三大支柱之一。
1课程设计的任务和要求
1.1课程设计的任务
1.设计题目:
冲压机控制系统设计
2.设计内容:
1)完成《课程设计指导书》所要求的控制循环。
2)按停止按钮,完成当前循环后再停。
3)按复位按钮,机械手和冲压机均回原位。
4)要求可以实现手动、回原点、单周期、连续控制。
5)连续时,循环5次结束,声光间断报警5秒。
1.2课程设计的基本要求
1)画出端子分配图和顺序功能图。
2)设计并调试PLC控制梯形图。
3)设计说明书。
2冲压机的总体设计
2.1PLC选型
PLC主机:
选择S7-200PLC作为冲压机控制系统的控制主机。
选择CPU226,因为其具有以下特点:
1)24输入/16输出共40个数字量I/O点。
2)可连接7个扩展模版单元,最大可扩展248个数字量I/O点或35路模拟量I/O。
本题所设计的传动需扩展17点输入和7点输出,设计见图2.1。
3)13KB的程序和数据存储区空间。
4)6个独立的30KHz的高速计数器,2路独立的20KHz的高速脉冲输出。
5)具有PID控制器。
6)2个RS-485通信/编程口。
7)具有多点接口MPI通信协议。
8)具有点对点接口PPI通信协议。
9)具有自由通信口。
CPU226
EM221
EM221
EM223
图2.1CPU及其扩展示意图
2.2PLC端子接线
图2.2外部接线图
3PLC程序设计
3.1设计思想
控制过程如下:
1)按下启动键后,把工件放在传送带1上,启动传送带1将工件送到工位1;
2)进料机械手下降到工位1,打开进料机械手吸盘控制阀,使吸盘吸住工件;
3)进料机械手上升,随后右行将工件送入冲压机加工台的工位2,断开吸盘并退回;
4)冲压模具下降,冲压完工件后上升;
5)出料机械手进入冲压机加工台;
6)出料机械手吸盘吸住工件;
7)将工件放到工位3,松开出料吸盘,出料机械手退回原位。
8)启动传送带2将工件从工位3送走。
同时还有三种工作方式:
手动、回原点、单周期、连续。
连续时,循环5次结束,声光报警5次。
设计见图3.1。
图3.1冲压控制系统示意图
为了更加方便快捷的操作冲压机,在工作台上集成一个控制面板,见图3.2。
工作方式选择开关的四个位置分别对应了四种工作方式,操作面板下部的20个按钮手动按钮,通过这些按钮可以手动操作进料机械手、出料机械手、传送带1、传送带2、模具的相关动作。
为了保证在紧急情况下(包括PLC发生故障时)能可靠地切断PLC的负载电源,设置了交流接触器KM。
在PLC开始运行时,按下“负载电源”,使KM线圈得电并自锁,KM的主触点接通,给外部负载提供交流电源,出现紧急情况时“紧急停车”按钮按下可以断开负载电源。
图3.2操作面板示意图
3.2顺序功能图
图3.3顺序功能图
图3.3是处理单周期、连续工作方式的顺序功能图。
在连续工作方式下,I4.2状态为1。
在初始条件M0.5为一时按下启动按钮I0.0,M2.0变为1状态,传送带1开始传送。
同时控制连续工作的M0.7的线圈“得电”并保持。
当出料机械手在M4.1断开吸盘定时时间到时,进入一个并行序列。
传送带2开始传送,与此同时出料机械手上升。
传送带2传送到工位4时,计数器加1,同时出料机械手在步M4.2到达I1.1限位后,加入一个等待步,两个动作都完成后,一起跳出并行序列。
当M0.7为1时且C1计数器未计满时,返回M2.0开始下一个循环,计满了则返回到初始步M0.0。
而以单周期工作方式时M0.7的状态为0,出并行序列后也返回到初始步M0.0。
按下停止按钮I0.1后,M0.7变为0状态,当冲压机不会停止工作,在当前工作周期的全部操作后,出料机械手、进料机械手、模具均回到原位后,系统返回并停留在初始步。
图3.4回原点和复位程序的顺序功能图。
回原点工作方式下,I4.0为ON。
按下启动按钮I0.0,M5.0为ON,复位模具下降,再模具上升,在连续、单周期的自动程序中,按下复位按钮也能达到这个效果。
升到上限位,I0.6为ON。
进入到一个并行序列,复位进料机械手下降,再进料机械手上升。
同时也复位出料机械手下降,在上升。
随后复位进机械手右行,再左行到限位;复位出料机械手左行后右行,右行到右限位,在M5.2和M5.5后面分别加入M5.3和M5.6,都完成后跳出并行序列。
这时原点条件M0.5条件满足,M0.5为ON,在公用程序中,初始步M0.0被置位,为进入单周期、连续工作方式做好准备,因此认为M0.0是并行序列的后续步。
图3.4回原点和复位的顺序功能图
3.3PLC梯形图
1.主程序
EN手动
回原点
EN自动
EN公用
2.公用程序
原点条件
初始条件
自复位
复位非初始步
复位连续标志
3.自动程序
连续
初始
传送带1传送
进料机械手吸盘打开
进料机械手右行
进料机械手吸盘断开
进料机械手左行
模具下降
模具上升
出料机械手吸盘打开
出料机械手左行
出料机械手右行
传送带2传送
等待
出料机械手吸盘断开
计数器C1计数
声
光
进料机械手下降
出料机械手上升
出料机械手下降
进料机械手上升
复位
复位模具下降
模具上升
复位进料机械手下降
进料机械手上升
复位进料机械手右行
进料机械手左行
出料机械手右行
复位出料机械手左行
出料机械手上升
复位出料机械手下降
等待步
等待步
进出机械手吸盘断开
4.手动程序
传送带1传送
进料机械手吸盘打开
进料机械手右行
进料机械手吸盘断开
进料机械手左行
模具下降
模具上升
出料机械手吸盘打开
出料机械手右行
进料机械手下降
传送带2传送
出料机械手吸盘断开
进料机械手上升
出料机械手下降
出料机械手上升
5.回原点程序
4程序调试说明
程序调试是在S7-200仿真软件上完成的,将梯形图导入后,选择CPU226,再增加2个(8I)和1个(8I/O)。
运行仿真软件运行前,先将原点条件的限位都打开。
运行软件,SM0.1的上升沿激活初始步M0.0。
打开连续I4.2,复位非初始步,启动I0.0后,冲压机系统开始动作,一直到传送带2达到工位4时,计数器加1,并开始下一次循环,直到计数器计满5次,停止循环并返回到初始步M0.0。
与连续不同的是,单周期循环一次后就直接返回到M0.0。
打开手动I3.7,主程序中手动成程序接通,通过相应按钮即可完成动作。
打开回原点I4.0,在主程序中选择回原点程序,系统进入回原点程序,最后进料,出料,模具回到原位后,返回到M0.0。
在调试程序过程中遇到了很多的困难,开始时因为自己的疏忽大意将程序的梯形图输入错误,导致不能导出或者在调试过程中定时器不接通,在经过软件本身的找错方法找出错误并加以改正,但在仿真程序中系统中不执行相应的程序,如连续开始时循环一次后计数器不加1,并且直接回到M0.0,后来经过反复的检查发现是程序出错,经过多次调解后程序才可以运行。
结束语
这一次课设让我收获了不少。
我学到了很多在书本上所没有学到过的知识。
而且通过这次课程设计使我懂得了理论与实际相结合是很重要的,只有理论知识是远远不够的,只有把所学的理论知识与实践相结合起来,从理论中得出结论,才能真正的学到知识。
通过这次设计实践,我学会了PLC的基本编程方法,对PLC的工作原理和使用方法也有了更深刻的理解。
在对理论的运用中,提高了我们的工程素质,在没有做实践设计以前,我们对知道的撑握都是思想上的,对一些细节不加重视,当我们把自己想出来的程序与到PLC中的时候,问题出现了,不是不能运行,就是运行的结果和要求的结果不相符合。
能过解决一个个在调试中出现的问题,我们对PLC的理解得到加强,看到了实践与理论的差距。
通过合作,我们的合作意识得到加强。
合作能力得到提高。
上大学后,很多同学都没有过深入的交流,在设计的过程中,我们用了分工与合作的方式,每个人互责一定的部分,同时在一定的阶段共同讨论,以解决分工中个人不能解决的问题,在交流中大家积极发言,和提出意见,同时我们还向别的同学请教。
在此过程中,每个人都想自己的方案得到实现,积极向同学说明自己的想法。
能比较选出最好的方案。
在这过程也提高了我们的表过能力。
此次课设,让我了解了plc梯形图、指令表、顺序功能图有了更好的了解,也让我了解了关于PLC设计原理。
有很多设计理念来源于实际,从中找出最适合的设计方法。
虽然本次课程设计是自己独立完成,但是,彼此还是脱离不了集体的力量,遇到问题和同学互相讨论交流,多和同学讨论。
还有就是老师的帮助,当我困惑不解时,老师的帮助给我指引了方向,同时老师给我也指出了不少的错误,让我少走了不少弯路。
经过这次设计我学到很多很多的的东西,既让我们懂得了怎样把理论应用于实际,又让我们懂得了在实践中遇到的问题怎样用理论去解决。
使我进一步提高了自己的实际动手能力和独立思考的能力。
为我以后的学习和工作打下了坚实的基础,使我受益匪浅
参考文献
[1]陈白宁,段智敏,刘文波.机械传动基础.沈阳:
东北大学出版社,2008.
[2]夏田,陈婵娟,祁广利.PLC电气控制技术.北京:
化学工业出版社,2009.
[3]张凤珊,祖龙起.电气控制及可编程程序控制器.北京:
中国轻工业出版社,2003.