乙炔干燥项目实施建议书.docx
《乙炔干燥项目实施建议书.docx》由会员分享,可在线阅读,更多相关《乙炔干燥项目实施建议书.docx(10页珍藏版)》请在冰豆网上搜索。
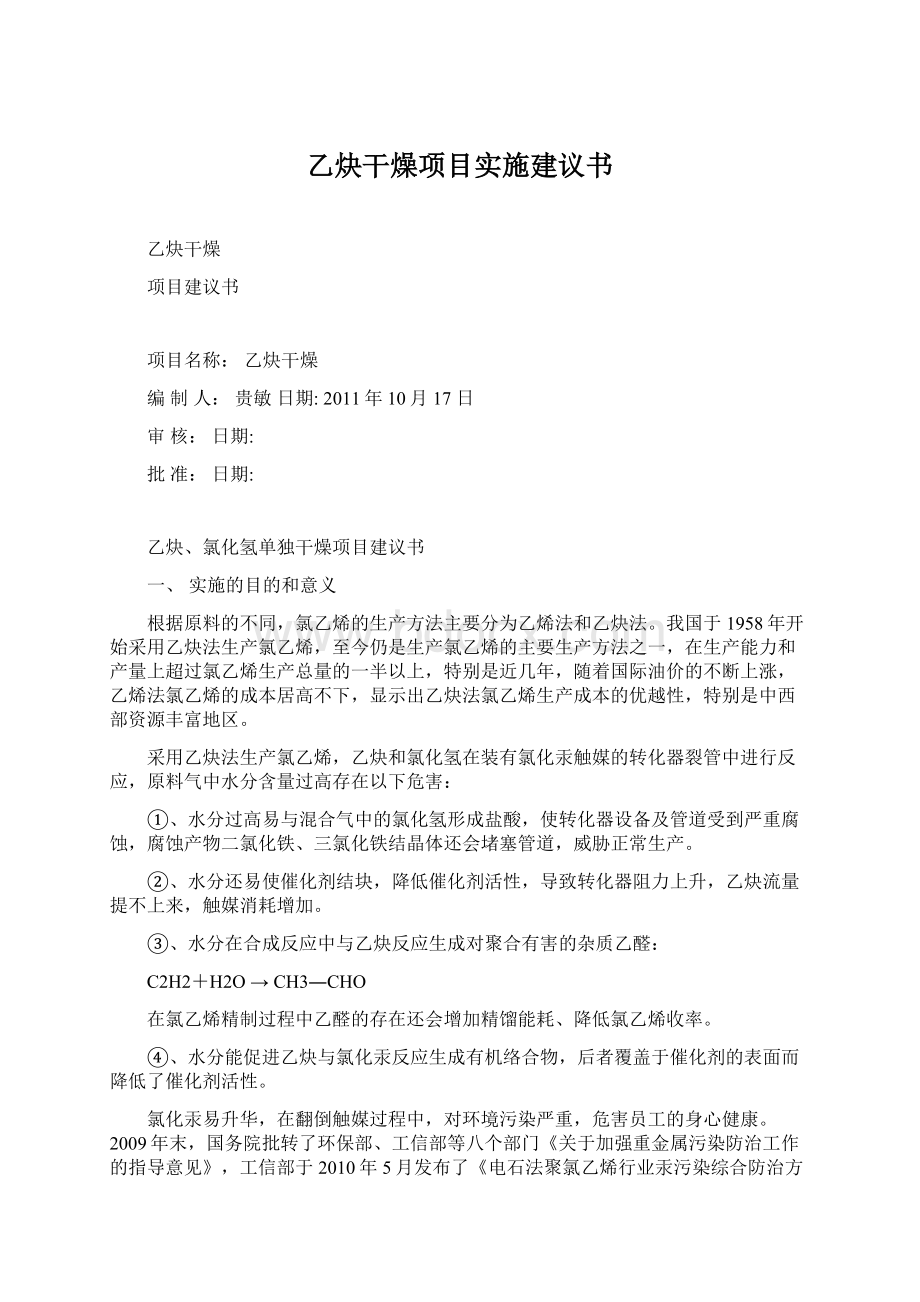
乙炔干燥项目实施建议书
乙炔干燥
项目建议书
项目名称:
乙炔干燥
编制人:
贵敏日期:
2011年10月17日
审核:
日期:
批准:
日期:
乙炔、氯化氢单独干燥项目建议书
一、实施的目的和意义
根据原料的不同,氯乙烯的生产方法主要分为乙烯法和乙炔法。
我国于1958年开始采用乙炔法生产氯乙烯,至今仍是生产氯乙烯的主要生产方法之一,在生产能力和产量上超过氯乙烯生产总量的一半以上,特别是近几年,随着国际油价的不断上涨,乙烯法氯乙烯的成本居高不下,显示出乙炔法氯乙烯生产成本的优越性,特别是中西部资源丰富地区。
采用乙炔法生产氯乙烯,乙炔和氯化氢在装有氯化汞触媒的转化器裂管中进行反应,原料气中水分含量过高存在以下危害:
①、水分过高易与混合气中的氯化氢形成盐酸,使转化器设备及管道受到严重腐蚀,腐蚀产物二氯化铁、三氯化铁结晶体还会堵塞管道,威胁正常生产。
②、水分还易使催化剂结块,降低催化剂活性,导致转化器阻力上升,乙炔流量提不上来,触媒消耗增加。
③、水分在合成反应中与乙炔反应生成对聚合有害的杂质乙醛:
C2H2+H2O→CH3―CHO
在氯乙烯精制过程中乙醛的存在还会增加精馏能耗、降低氯乙烯收率。
④、水分能促进乙炔与氯化汞反应生成有机络合物,后者覆盖于催化剂的表面而降低了催化剂活性。
氯化汞易升华,在翻倒触媒过程中,对环境污染严重,危害员工的身心健康。
2009年末,国务院批转了环保部、工信部等八个部门《关于加强重金属污染防治工作的指导意见》,工信部于2010年5月发布了《电石法聚氯乙烯行业汞污染综合防治方案》,汞污染问题已被列为乙炔法PVC行业重金属污染防治的重点问题,由于我国可开采的汞资源已接近枯竭,进口汞受制于国际汞公约,氯化汞触媒价格已从开车时的2.4万元/吨上升到目前的6万/吨左右。
由于我公司目前采用的混合脱水工艺,乙炔和氯化氢混合后用冷冻盐水冷冻脱水,脱水效果不好,从2007年底聚氯乙烯工程一期开车后,转化器一直在频繁泄漏,频繁维修,频繁翻倒更换触媒,造成转化器维修成本居高不下,触媒消耗过高,员工劳动强度增大。
二、工艺方案选择
1、国氯乙烯生产中原料气脱水方法
①、乙炔气固碱干燥
乙炔单独采用固碱进行干燥,气体水分含量高,碱消耗量大,目前已经被淘汰。
②、混合脱水
混合脱水即烧碱装置送来的氯化氢与乙炔装置来的湿乙炔气直接进行混合,然后通过二级石墨换热器,用-35℃冷冻盐水深冷到-14±2℃,原料气中的水分被氯化氢吸收,呈40%的盐酸雾析出,再通过除雾器进行分离。
这种方法理论上可以将原料气中的水分降低到0.0165%(wt),实际上冷凝过程中形成的盐酸雾不可能全部分离下来,生产中测到的水分含量远大于理论值。
③、混合脱水+硫酸干燥
近年企业新建的装置中有采用混合脱水后再加硫酸干燥的工艺,在混合脱水后再用98%的浓硫酸进行深度干燥,进一步降低了原料气中的水分含量。
只是在对混合气进行硫酸干燥的同时部分乙炔气被硫酸碳化,当温度高时,此种情况更加严重,导致吸收水后95%的硫酸杂质含量增加。
被污染的硫酸无法回收利用,销售困难。
④、变压吸附脱水
此技术利用活性吸附物质吸附水分,通过气体压力变化脱除乙炔气水分,由于乙炔具有不饱和三键,性质不稳定,在压力较高时易发生自聚分解,进而发生爆炸,在实际操作中,使用压力不得超过150kpa(g),压力变化围较小,不宜采用此方法脱水。
且脱水深度不够,产品气仍含有较多水分,不能满足生产需要。
⑤、变温吸附脱水
此技术是引进国外先进氯乙烯生产技术的一部分,乙炔气采用变温吸附进行干燥,乙炔气中的水分含量最低可以达到3ppm(v/v)。
原料氯化氢采用98%浓硫酸进行干燥,可将氯化氢气体中的水分含量控制到50ppm(v/v)以下。
2、原料气脱水工艺选择
根据我厂现有的混合脱水工艺,综合考虑投资、运行及满足生产要求,可采用原料气单独脱水工艺,将现有混合脱水的系统单独用于脱除氯化氢气体中的水分,乙炔采用变温吸附工艺,将水分控制在50ppm(v/v)以下,即可满足生产要求,降低投资及运行费用;又可避免因原料气含水高而带来的对生产的不利影响。
三、工艺方案及流程说明
1、工艺方案
本方案采用变温吸附技术,分为两条独立的生产线,每条线配套20万吨氯乙烯装置。
1、原料及产品气规格
序号
项目
原料气
产品气
1
组成
%v/v
C2H2
95.865
98.25
N2
1.245
1.75
H2O
2.89
50ppm
2
温度℃
33
15
3
压力kPa(g)
80~100
60~80
4
气体流量Nm3/h
10000
2、工艺流程说明
乙炔气经过阻火器进入本装置,冷却到2℃,进入乙炔气聚结器,除去冷凝水雾,送入乙炔干燥塔进行干燥,干燥合格的乙炔气供氯乙烯合成用。
每条生产线使用三台并联的干燥塔,其中两台吸附,一台进行再生。
再生过程中先通入一定量的氮气吹扫干燥塔;经过加热的氮气进入干燥塔,带出水分后进入冷却器,冷凝分离出水分;加热过程结束后,用冷氮气将干燥塔冷却。
整个加热、冷却过程中,氮气由鼓风机进行循环利用,只有极少量的补充。
3、工艺流程简图:
乙炔干燥工艺简图
合成
去乙炔
乙炔干燥塔再生工艺简图
氮气
四、主要设备技术参数及关键阀门
序号
设备名称
规格
数量
备注
1
干燥塔
φ2000×10000LL
6
2
乙炔冷却器
φ1200×6000LL
2
3
乙炔气聚结器
φ2000×6000LL
2
4
再生气鼓风机
Q=10000Nm3/h△P=50kPa
4
两开两备
5
再生气鼓风机冷却器
φ900×3000LL
2
6
再生气加热器
φ800×3000LL
2
7
再生气电加热器
4
8
再生气冷却器
φ900×4500LL
2
9
再生气二级冷却器
φ1100×3000LL
2
10
再生气聚结器
φ2000×6000LL
2
11
自控阀门
DN50
2
12
自控阀门
DN80
6
13
自控阀门
DN100
4
14
自控阀门
DN150
2
15
自控阀门
DN200
2
16
自控阀门
DN250
2
17
自控阀门
DN400
12
18
自控阀门
DN450
12
19
手动阀门
DN400
12
20
手动阀门
DN450
21
21
液压站
成套设备
1
自控阀用
五、公用工程消耗
1、氮气(再生干燥塔用)
压力:
100kPa(G)
温度:
环境温度
最大流量:
1450Nm3/h(间歇使用)
单耗:
19.3Nm3/t·VCM
2、循环水(再生气冷却器用)
压力:
500kPa(G)
上水温度:
32℃
回水温度:
≤40℃
流量:
220t/h
3、电(电加热器、鼓风机用)
380/10000V380Hz
单耗:
14KWh/t·VCM
4、蒸汽
压力:
700kPa(G)
温度:
饱和温度
最大流量:
1.6t/h(间歇使用)
单耗:
0.024t/t·VCM
5、冷量
规格:
0℃
最大量:
5275440KJ/h
单耗:
120495KJ/t·VCM
六、项目投资估算
序号
工程项名称
费用
备注
一
设计费估算
80
二
专利费和专有技术费
100
三
工程建设费
1428.5
1
设备购置费
957.75
2
安装工程费
360.75
3
建筑工程费
110
四
开车费及人员培训费
28
五
分子筛
190
总费用
1826.5
上述费用不包括配套公用工程,公用工程可利用现有公用工程系统的余量。
所需占地面积约1200m2左右(不包括冷冻及公用工程装置)。
七、实施计划、
计划实施进展情况:
2012年1月项目立项、初步设计、完成相关审批手续
2012年2月审批手续完成后,进行设计、设备制造等工作。
2012年4月土建施工
2012年7月设备、管道安装
2012年9月管道吹扫打压、设备调试,电气仪表调试
2012年10月假物料试车
2012年11月调试及验收。
八、资金来源:
项目资金来自集团自筹。
九、经济效益分析
目前转化器泄漏维修成本
项目
上下封头、管道拆装
转化器修理
触媒翻倒
税费
合计
费用(万元)
0.25
0.5
0.2
0.05
1
转化器泄漏统计表
2010年
8月
9月
10月
11月
12月
泄漏台数
5
5
9
12
4
2011年
1月
2月
3月
4月
5月
6月
7月
8月
9月
泄漏台数
2
7
8
17
13
22
12
5
11
合计泄漏
132台
2010年10月-2011年9月一年泄漏
122台
修理费用
132万
2010年10月-2011年9月修理费用
122万
2010年10月到2011年9月,转化器更换33台算,转化器大修费用为30万/台,转化器大修费用为33台×30万/台=990万。
我厂2011年触媒消耗为1.73Kg/吨PVC,设计为1.2Kg/吨PVC,比设计值偏高0.53Kg/吨PVC,触媒消耗成本比设计增加40万吨×0.53Kg/吨PVC=212吨,目前触媒价格为6.5万/吨,触媒消耗成本比设计增加212×6.5=1378万,若与采用乙炔分子筛干燥的厂家相比,如茌平信发触媒消耗为:
0.8Kg/吨PVC,每年我们触媒消耗成本比茌平信发高:
(1.73-0.8)Kg/吨×40万吨×6.5万/吨=2418万。
每年因混合脱水效果不好,原料气含水过高,转化器泄漏造成的生产成本为990+1378=2368万,此成本不含因原料气含水过高副反应增多导致的乙炔损失和氯乙烯精制过程中乙醛的存在增加精馏能耗、降低氯乙烯收率造成的生产成本增加。
乙炔干燥装置生产运行成本:
序号
消耗项
单耗
部核算单价
40万吨/年成本
备注
1
氮气
19.3Nm3/t·VCM
0.32元/m³
247万
2
循环水
220t/h
0.12元/t
21.12万
每年按8000小时
3
电
14KWh/t•VCM
0.32元/KWh
179.2万
4
蒸汽
0.024t/t•VCM
98元/t
94万
5
冷量
120495KJ/t•VCM
0.67元/t
153万
单耗为0度水
合计
694.32万
投资回收期限:
投资回收期=装置投资成本÷(节省成本—装置运行成本)=1826.5÷(2368—694.32)=1.09年,投资回收期为1年零两个月。
十、结论、
综上所述,新增乙炔变温吸附脱水干燥装置,将现有的乙炔、氯化氢混合气干燥装置改为氯化氢脱水装置,乙炔、氯化氢先单独脱水,然后混合,相比现有混合脱水工艺,脱水混合工艺原料气含水量较低,转化器不易泄漏,维修成本低,触媒使用寿命较长,触媒消耗成本低,翻倒次数少,有利于减少职业危害,副反应少,氯乙烯质量好。
由于我国汞资源已经接近枯竭,国际间汞贸易受制于国际汞公约,在新型无汞催化剂研发没有取得突破的情况下,随着新建PVC项目的增加,触媒需求量增加,价格会进一步上涨,随着新建产能的投产,未来我国PVC产能会过剩,PVC利润微薄,行业竞争激烈,如何降低成本提高效益是每一个企业所面临的问题,新建乙炔干燥装置可以降低氯乙烯生产成本,能提高企业的竞争力量。
氯碱生产部
2011年10月17日
十二、审核部门专业人员评审会签、
序号
专业
会签
1
工艺、总图
2
设备
3
电气
4
仪表
5
土建
6
防腐保温
7
给排水
8
安全技术