塑料模具课程设计说明书.docx
《塑料模具课程设计说明书.docx》由会员分享,可在线阅读,更多相关《塑料模具课程设计说明书.docx(36页珍藏版)》请在冰豆网上搜索。
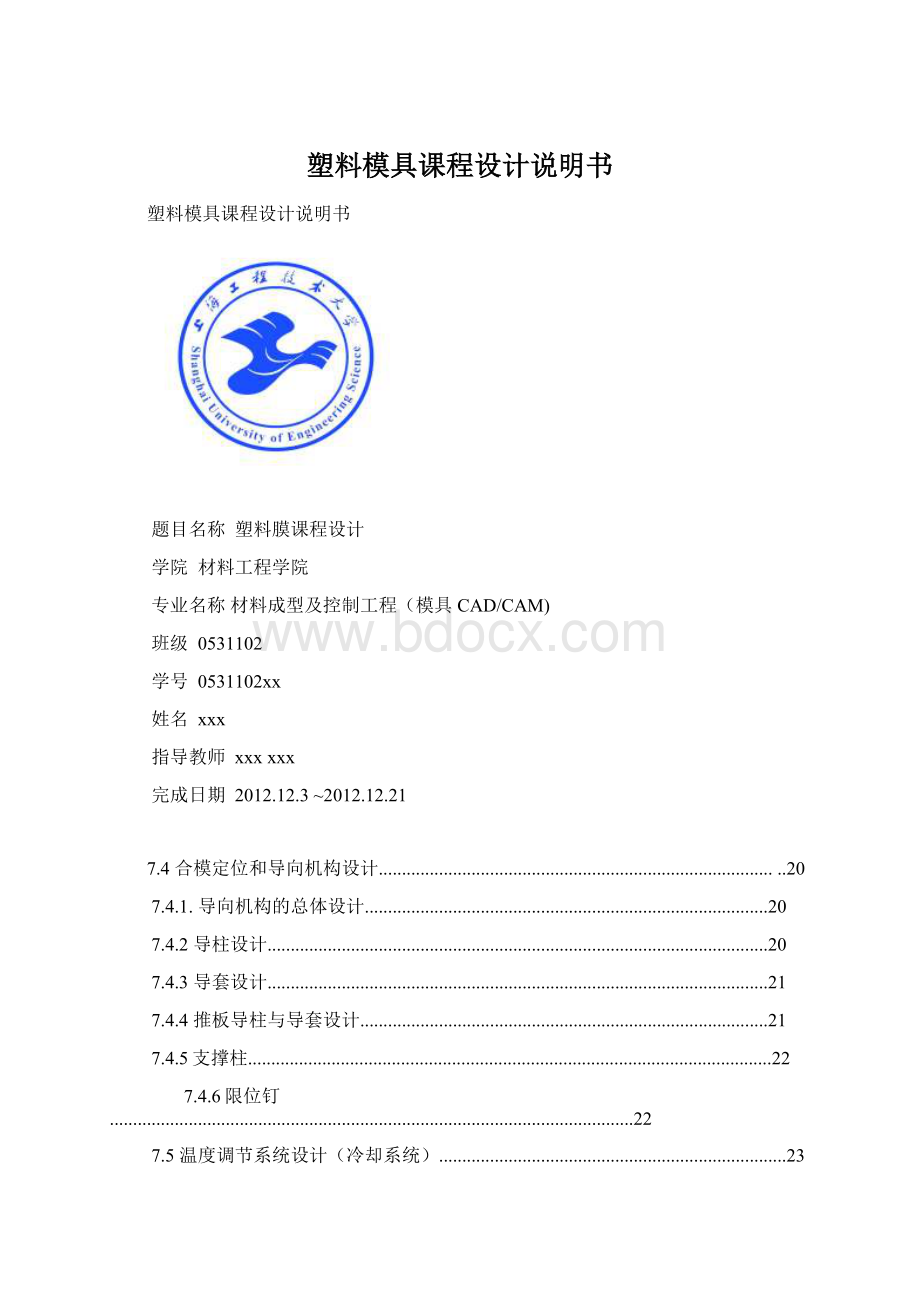
塑料模具课程设计说明书
塑料模具课程设计说明书
题目名称塑料膜课程设计
学院材料工程学院
专业名称材料成型及控制工程(模具CAD/CAM)
班级0531102
学号0531102xx
姓名xxx
指导教师xxxxxx
完成日期2012.12.3~2012.12.21
7.4合模定位和导向机构设计.......................................................................................20
7.4.1.导向机构的总体设计.......................................................................................20
7.4.2导柱设计............................................................................................................20
7.4.3导套设计............................................................................................................21
7.4.4推板导柱与导套设计........................................................................................21
7.4.5支撑柱.................................................................................................................22
7.4.6限位钉.................................................................................................................22
7.5温度调节系统设计(冷却系统)...........................................................................23
7.6排气系统的设计.......................................................................................................23
第一章设计任务书
1.1课程设计目的
本课程设计的目的是使我们在学完《塑料模具设计》课程之后,巩固和加深对塑料模有关理论的认识,提高设计计算、制图和查阅参考资料的能力。
使得我们能正确运用专业知识,初步掌握制定注塑工艺规程及进行注塑模具设计的原则和方法。
在课程设计中应本着技术上先进、经济上合理的原则,制定注塑工艺规程和设计有关的注塑模具。
1.2课程设计任务书
塑料制品名称:
轴套固定销(如下图)
成型方法与设备:
在适当的塑料注射机上注射成型;
塑料原料:
聚丙烯(PP);
收缩率:
1.20--2.0%;
塑件图:
如图所示为制品的图样。
第二章塑件成形工艺分析
2.1塑料的成型性能
1.无定形料,吸湿性小,流动性差,为了提高流动性,防止发生气泡,塑料可预先干燥。
模具浇注系统宜粗短,浇口截面宜大,不得有死角。
模具须冷却,表面镀铬。
2.极易分解,特别在高温下与钢、铜接触更易分解(分解温度为200℃),分解时逸出腐蚀、刺激性气体。
成型温度范围小。
3.采用螺杆式注射机及直通式喷嘴时,孔径宜大,以防死角滞料,滞料时必须及时清除。
2.2塑件的尺寸精度分析
该塑件无尺寸精度特殊要求,所有尺寸按MT6查取公差。
其主要尺寸公差要求如下表所示:
受模具活动部分影响的尺寸公差,取表中公差值与附加值之和。
6~8级附加值为0.2mm。
所以1.0±0.24修正为1.0±0.34,15±0.40修正为15±0.50
为便于加工所有圆角统一为R0.5
塑件标注尺寸
塑件尺寸公差
(按MT6级精度)
塑件标注尺寸
塑件尺寸公差
(按MT6级精度)
外形尺寸
Φ16
Φ16-0.40
内形尺寸
Φ14
Φ14+0.36
Φ12
Φ12-0.36
Φ10
10+0.32
1.0
1.0±0.34
3
3+0.24
15
15±0.50
2.3塑件表面质量分析
该塑件表面没有提出特殊要求,一般情况下外表面要求光洁,表面粗糙度可以取到
。
没有特殊要求时,塑件内部表面粗糙度可取
。
2.4塑件结构工艺性分析
(1)壁厚分析:
设计合理,壁厚相对均匀,且符合最小壁厚的要求。
(2)圆角过渡:
要从分型面位置、型芯、型腔结构来分析过渡圆角的设置。
根据本塑件的壁厚,采用圆角半径R0.5mm。
(3)脱模斜度:
为便于塑件从模腔中取出,塑件的内外壁需要足够的脱模斜度。
外形尺寸以大端为基准,根据PP的性能和《模具设计与制造简明手册(第二版)》P357—表2-19:
型芯脱模斜度为:
1°,型腔脱模斜度为1.2°
2.5生产实际考虑
该塑件的生产类型应该是大批量生产,因此在设计模具时,要提要塑件的生产效率,倾向于采用多型腔、高寿命、自动脱模的模具,以降低生产成本。
第三章成型设备的选择及校核
3.1注射机的初选
3.1.1计算塑件的体积
根据制件的三维模型,利用三维软件直接求得塑件的体积为:
V1=1221mm3。
3.1.2计算所需的体积
浇注系统凝料按1:
1取,故:
V2=V1=1221mm3
塑件和浇注系统凝料总体积为(按一模两腔算):
V=2(V1+V2)=4884mm3=4.9cm3
3.1.3选用注射机
根据总体积V=4884mm3,初步选取XS-ZY-125型螺杆式注射成型机。
XS-ZY-125型螺杆式注射成型机主要参数如下表所示
项目
参数
项目
参数
理论注射量
125cm3
移模行程
115mm
注射压力
119MPa
定位孔的直径
Φ100+0.054
锁模力
900kN
喷嘴球半径
SR12mm
最大模具厚度
300mm
喷嘴口孔径
Φ4
最小模具厚度
200mm
3.2注射机的终选
3.2.1注射量的校核公式
(0.8~0.85)
式中
——注射机的公称注射量,cm3
——每模的塑料体积量,cm3
如前所述,塑件及浇注系统的总体积为4.9cm3,远小于注射剂的理论注射量125cm3,故满足要求。
3.2.2模具闭合高度的校核
模具闭合高度的校核公式为:
由装配图可知模具的闭合高度
=206mm,而注射机的最大模具厚度
=300mm,最小模具厚度
=200mm,满足安装要求。
3.2.3模具安装部分的校核
模具定位圈的直径Φ100mm与注射机定位孔的直径Φ100mm相等,满足安装要求。
浇口套的球面半径SR1=SR+(1~2)mm=14mm,满足要求。
浇口套小端直径R1=R+(1~2)mm=5mm,满足要求。
3.2.4模具开模行程的校核
模具开模行程的校核公式为:
式中
——模具的开模行程,mm
——注射机的移模行程,mm
——制件的推出距离,mm
——包括流道凝料在内的制品的高度,mm
——取出凝料所需分开的距离,mm
代入数据得:
H1+H2+5~10=15+66+10=81<300,满足要求。
3.2.5锁模力的校核
锁模力的校核公式为:
式中F——注射机的额定锁模力,kN
A——制件和流道在分型面上的投影面积之和,mm2
——型腔的平均压力,MPa
K——安全系数,通常取1.1~1.2
代入数据得:
KAPm=1.2×2592×40=124.5KN<900KN。
满足要求。
3.2.6注射压力的校核
注射压力的校核公式为:
式中
——注射机的额定注射压力,MPa
——注射成型时的所需用的注射压力,MPa
——安全系数
代入数据得:
K′p0=1.2×80=96MPa<
=119MPa。
满足要求。
综上所述:
选取XS-ZY-125型螺杆式注射成型机完全符合本模具的使用要求。
第四章分型面的选择
4.1分型面的选择原则
如何确定分型面,需要考虑的因素比较复杂。
由于分型面受到塑件在模具中的成型位置、浇注系统设计、塑件的结构工艺性及精度、嵌件位置形状以及推出方法、模具的制造、排气、操作工艺等多种因素的影响,因此在选择分型面时应综合分析比较,从几种方案中优选出较。
为合理的方案。
选择分型面时一般应遵循以下几项原则:
(1)分型面应选择在制品的最大截面处,无论塑件以何形式布置,都应将此作为首要原则;
(2)便于塑件顺利脱模,尽量使塑件开模时留在动模一边。
(3)有利于保证塑件的精度要求。
(4)尽可能满足塑件的外观质量要求。
分型面上型腔壁面稍有间隙,就会产生飞边。
(5)便于模具加工制造,在选择非平面分型面时,应有利于型腔加工和制品的脱模方便。
(6)对成型面积的影响,尽量减少制品在合模方向上的投影面积,以减小所需锁模力。
(7)对排气效果的影响,尽可能有利于排气。
(8)对侧向抽芯的影响(本塑件没有抽芯)。
其中最重要的是第
(2)和第(5)、第(8)点。
为了便于模具加工制造,应尽是选择平直分型面工易于加工的分型面。
4.2方案分析
该塑件为电器用塑料,要求表面光滑平整;无毛刺无毛边;不允许缩水、凹坑;无划伤;无污物。
在选择分型面时,根据分型面的选择原则,考虑不影响塑件的外观以及成型后能够顺利取出制件,有以下几种方案:
分型面选择的首要原则是必须选择塑件断面轮廓最大的地方作为分型面,这是确保塑件能够脱出模具而必须遵循的基本原则。
(1)分型面的方案一:
该塑件采用垂直分型,用活动镶块垂直分型后,留在包紧在下模的型芯上,在有动模端的推杆将塑件从型芯上脱出,虽然这样使模具型腔由内型变成了外型,可以降低模具型腔的加工难度,但是会在塑件的垂直分型面上产生熔接痕,不能达到塑件的外观要求,并且模具的结构复杂,所以此分型面方案不是好。
(2)分型面的方案二:
该塑件采用水平分型,定模部分成型塑件的内部结构,将型芯装在动模上,型腔做在定模,当开模后塑件包紧在型芯,随型芯留在动模,然后由动模上的推板将塑件脱出型芯,这样就可以达到塑件的外观的使用要求。
结论:
综合上述的两种方案,从塑件的外观要求,模具的成型性能,以及模具的加工经济性考虑出发,还是方案二的分型方案是两者当中最好的一种方案,所以采用方案二的分型面。
第五章成型工艺参数的确定
成型工艺卡片:
(具体见附录一)
产品
参数
产品名称及图号
轴套固定销
模腔数
2
产品单重
1.722g
总重
3.4g
单件体积
1.221cm3
总体积
2.442cm3
投影面积
497mm2
总投影面积
994mm2
外形尺寸(H-V-W)
Φ15.5×50×20
最大壁厚
3mm
最小壁厚
1mm
抽芯数
0
嵌件数
0
注塑工艺参数
料筒温度(前、中、后)
前180~190℃中170~180℃后160~170℃
喷嘴温度
170~180℃
模具温度
90~120℃
注射压力
80~130MPa
注射时间
20~90s
保压温度
100~120℃
保压压力
40~60MPa
保压时间
0~5s
冷却时间
20~60s
锁模压力
124.5kN
螺杆转速
28r/min
成型周期
50~160s
原料
参数
名称
聚丙烯(PP)
预备干燥温度、时间
70~80℃3~4h
密度
1.41g/cm3
比容
0.71cm3/g
吸水率
0.12%~0.15%
收缩率
1.5%~3.0%
熔点
180~200℃
抗拉屈服强度
69MPa
弯曲强度
104MPa
硬度
11.2HB
击穿电压
18.6KV/mm
注射机参数
最大注塑容量
125cm3
最大注射压力
119MPa
最大锁模力
900kN
最大开模行程
300mm
最大装模尺寸
300mm
最大封闭高度
300mm
最小封闭高度
200mm
喷嘴球径
12mm
喷嘴口径
Φ4
定位孔径
Φ100+0.054
顶杆直径
两侧Φ22
最大注射面积
1000mm2
模板行程
300mm
第六章浇注系统的设计
6.1浇注系统设计原则
(1)浇注系统与塑件一起在分型面上,应有压降,流量和温度的分布的均衡布置;
(2)结合型腔布置考虑,尽可能采用平衡式分流道布置;
(3)尽量缩短熔体的流程,以便降低压力损失、缩短充模时间;
(4)浇口尺寸、位置和数量的选择十分关键,应有利于熔体流动、避免产生湍流、涡流、喷射和蛇形流动,有利于排气和补缩,且应设在塑件较厚的部位,以使熔料从后断面移入薄断面,以利于补料;
(5)避免高压熔体对模具型芯和嵌件产生冲击,防止变形和位移的产生;
(6)浇注系统凝料脱出应方便可靠,凝料应易于和制品分离或者易于切除和整修;
(7)熔接痕部位与浇口尺寸、数量及位置有直接关系,设计浇注系统时要预先考虑到熔接痕的部位、形态,以及对制品质量的影响;
(8)尽量减少因开设浇注系统而造成的塑料凝料用量;
(9)浇注系统的模具工作表面应达到所需的硬度、精度和表面粗糙度,其中浇口应有IT8以上的精度要求;
(10)设计浇注系统时应考虑储存冷料的措施;
(11)尽可能使主流道中心与模板中心重合,若无法重合应使两者的偏离距离尽可能小。
6.2主流道设计
主流道通常位于模具中心塑料熔体的入口处,它将注射机喷射出的熔体导入分流道或型腔中。
主流道的形状为圆锥形,以便于熔体的流动和开模时主流道凝料的顺利拔出。
6.2.1主流道尺寸
(1)主流道小端直径d
主流道小端直径d=注射机喷嘴直径+0.5~1
=4+0.5~1
取d=5(mm)这样便于喷嘴和主流道能同轴对准,也能使的主流道凝料能顺利脱出
(2)主流道球面半径
主流道入口的凹坑球面半径R,应该大于注射机喷嘴球头半径的2~3mm。
反之,两者不能很好的贴合,会让塑件熔体反喷,出现溢边致使脱模困难.
SR=注射机喷嘴球头半径+2~3
SR=12+2~3
取SR=14(mm)
(3)主流道长度L
一般按模板厚度确定,但为了减小充模时压力降和减少物料损耗,以短为好,小模具控制在50之内。
在出现过长流道时,可以将主流道衬套挖出深凹坑,让喷嘴伸入模具。
本设计中结合该模具的结构,取L=60(mm)
(4)主流道大端直径
D=d+2Ltgα(半锥角α:
为1°~2°,取α=1.2°)≈7.4mm
6.2.2主流道衬套形式及其固定
主流道小端入口处与注射机喷嘴反复接触,属易损件,对材料要求较严,因而模具主流道部分常设计成可拆卸更换的主流道衬套形式,即浇口套。
在定模座板上开设阶梯孔,将浇口套放入。
浇口套自行设计。
在定模座板上在安装定位圈定位。
定位圈及浇口套装配图:
6.3分流道的设计
本模具的流道布置形式采用平衡式,如下图:
分流道的形状及尺寸与塑件的体积、壁厚、形状的复杂程度、注射速率等因素有关。
该塑件的体积不大而且形状不复杂,且壁厚均匀,可以考虑采用侧浇口进料的方式,有利于塑件的成型和外观质量的保证。
从便于加工的方面考虑,采用截面形状为半圆形的分流道.查有关的手册,选择d=5mm。
此外该模具是一模2件,型腔的数量较少,模具的结构简单而紧凑,所以采用平衡式,各个型腔的分流道的断面形状及大小、分流道长度都取作一致。
这样,熔体就能以相同的成型压力和温度同时充满各个型腔,使一模内成型出的各个塑件的尺寸及性能容易保持一致。
6.4浇口的设计
浇口可分为限制性和非限制性浇口两种。
我们将采用限制性浇口。
限制性浇口一方面通过截面积的突然变化,使分流道输送来的塑料熔体的流速产生加速度,提高剪切速率,使其成为理想的流动状态,迅速面均衡地充满型腔,另一方面改善塑料熔体进入型腔时的流动特性,调节浇口尺寸,可使多型腔同时充满,可控制填充时间、冷却时间及塑件表面质量,同时还起着封闭型腔防止塑料熔体倒流,并便于浇口凝料与塑件分离的作用。
模具设计时,浇口的位置及尺寸要求比较严格,初步试模后还需进一步修改浇口尺寸,无论采用何种浇口,其开设位置对塑件成型性能及质量影响很大,因此合理选择浇口的开设位置是提高质量的重要环节,同时浇口位置的不同还影响模具结构。
总
之要使塑件具有良好的性能与外表,一定要认真考虑浇口位置的选择。
通常要考虑以下几项原则:
a.尽量缩短流动距离。
b.浇口应开设在塑件壁厚最大处。
c.必须尽量减少熔接痕。
d.应有利于型腔中气体排出。
e.考虑分子定向影响。
f.避免产生喷射和蠕动。
g.浇口处避免弯曲和受冲击载荷。
h.注意对外观质量的影响。
6.4.1浇口形式的选择
由于该塑件外观质量要求高,浇口的位置和大小还是要不能太影响塑件的外观,同时,也应该尽量使模具结构简单。
根据对塑件结构的分析及已确定的分型面的位置,可选的浇口形式有几种方案,如下:
(1)方案一:
侧浇口一般开设在分型面上,有塑件侧面进料,侧浇口断面易取矩形形状(必要时用圆形),它能方便地调节剪切速率,充模流量速率,流动状态和浇口封闭时间,并可以灵活地选择塑件进浇位置,广泛使用于多腔模中。
(2)方案二
点浇口是一种断面尺寸很小的浇口,当物料通过时产生很高的剪切速率,这对于表观粘度随剪切速率变化而明显变化的塑料熔体和粘度较低的塑料熔体是适合用的.点浇口在开模时容易自行切断,并且在塑件上留下的残痕极小,不容易觉察,故无需修剪浇口的工序.点浇口的另一个优点是,它很容易向模腔多点进料,浇口位置选择灵活,对于单腔模和多腔模均适用。
但由于次塑件为圆环状,且材料为PVC,采用点浇口不合适。
综上所述,对塑件成型性能、浇口和模具结构的分析比较,由于塑件的尺寸及表面精度要求不高,从模具的制造及结构考虑,确定成型该塑件的模具采用侧浇口的形式。
(采用方案一)
6.5冷料穴和拉料杆的设计
在完成一次注射循环的间隔,考虑到注射机喷嘴和主流道入口这一段熔体因辐射散热而低于所要求的塑料熔体的温度,从喷嘴端部到注射机料筒以内约10~25mm的深度有个温度逐渐升高的区域,这时才达到正常的塑料熔体温度。
位于这一区域内的塑料的流动性能及成形性能不佳,如果这里相对较低的冷料进入型腔,便会产生次品。
为克服这一现象的影响,用一个井穴将主流道延长以接收冷料,防止冷料进入浇注系统的流道和型腔,把这一用来容纳注射间隔所产生的冷料的井穴称为冷料穴(冷料井)。
冷料穴的作用是储存因两次注射间隔而产生的冷料头及熔体流动的前锋冷料,以防止冷料进入型腔而影响制件质量。
由于本塑件是聚丙烯PP,它的特点是无定形,流动性差,因此采用反锥形形拉料杆的冷料穴。
整个浇注系统如下图所示:
第七章模具的结构分析与设计
7.1确定模架
7.1.1确定型腔布局
模具采用一模两腔,布局如下图所示,需要确定图中尺寸。
(1)确定S1和S2
查《模具设计与制造简明手册(第二版)》P498表2-99和P497图2-68可得:
S1=10S2=18
(2)确定模仁L0和B0
L0=4S1+2S2+2d=200mmB0=200mm
7.1.2确定模板尺寸
根据上面的B0和L0,考虑注塑机的大小、导柱、导套和螺钉等布置,根据GB/T12555-2006《塑料注射模模架》,模架型号为:
A3型,200mm×200mm。
7.1.3确定模架尺寸
模具上所有的螺钉尽量采用内六角螺钉;模具外表面尽量不要有突出部分;模具外表面应光洁,加涂防锈油。
两模板之间应有分模间隙,即在装配、调试、维修过程中,可以方便地分开两块模板。
1.定模座板(250mm×200mm、厚25mm)
定模座板上的注射机定位孔为Φ100mm,定模座板是模具与注射机连接固定的板,定模座板上固定定位圈,材料为45钢。
定位圈通过4个M5的内六角圆柱螺钉与其连接。
2.定模板(200mm×200mm、厚30mm)
用于固定定模模仁(型腔镶块)和导套。
应该有一定的厚度,并有足够的强度。
一般用45钢。
其上的导套孔与导套一端采用H7/k6配合,定模与定模模仁(型腔镶块)采用H7/m6配合。
3.推件板(200mm×200mm、厚20mm)
用于推出塑件。
应该有一定的厚度,并有足够的强度。
一般用45钢。
其上的导柱孔与导柱孔一端采用H7/k6配合。
4.动模板(200mm×200mm、厚25mm)
用于固定动模模仁(型芯镶块)和导套。
一般用45钢。
动模板应具有较高的平行度和硬度。
动模模仁(型芯镶块)通过4个沉头螺钉M5固定在动模板上面。
其上的导柱与动模板一端采用H7/k6配合,动模与动模模仁(型芯镶块)采用H7/m6配合。
5.垫块(38mm×200mm、厚70mm)
主要作用:
在动模座板与支承板之间形成推出机构的动作空间,或是调节模具的总厚度,以适应注射机的模具安装厚度要求。
结构形式:
可以是平行垫块或拐角垫块,该模具采用平行垫块。
垫块材料:
垫块材料为45
垫块的高度h校核:
h=h1+h2+h3+s+δ=65<700mm
式中h1——顶出板限位钉的厚度,该模具限位钉厚度,为5mm;
h2——推板厚度,为20mm;
h3——推杆固定板厚度,为15mm;
s——推出行程,为20mm;
δ——推出行程富余量,取5mm。
6.动模座板(250mm×200mm、厚25mm)
动模座板上有四个个挡钉孔,挡钉与挡钉孔采用H7/n6配合,材料为45钢。
7.推板(200mm×120mm、厚20mm)
用4个M8的内六角圆柱螺钉与推杆固定板固定。
材料为45钢。
8.推杆固定板(200mm×120mm、厚15mm)
材料为45钢。
7.2成型零件的设计
7.2.1成型零件的结构分析
1.型腔的设计
(1)定模模仁(型腔镶块)
型腔采用整体嵌入式结构。
整体式型腔有较高的强度和刚度,在使用中不易发生变形。
本模具是一模两腔,两个型腔均做在一个模仁内,而不是分别做两个嵌入定模板。
(2)定模模仁(型腔镶块)的固定
由于定模模仁(型腔镶块)比较大,而且厚度较厚,故采用螺钉连接,这样做能够达到很好的紧固作用。
螺钉连接
(3)定模板
定模模仁(型腔镶块)固定在定模板上。
2.型芯的设计
(1)型芯
(2)动模模仁(型芯镶块)
(3)动模板
动模模仁(型芯镶块)固定在定模板上。
3.成型零件的装配图如下:
7.2.2成型零件的尺寸计算
塑件的平均收缩率
尺寸偏差取MT6级
型腔和型芯成形尺寸:
型腔内径:
型腔深度: