乙醛氧化制醋酸氧化工段.docx
《乙醛氧化制醋酸氧化工段.docx》由会员分享,可在线阅读,更多相关《乙醛氧化制醋酸氧化工段.docx(12页珍藏版)》请在冰豆网上搜索。
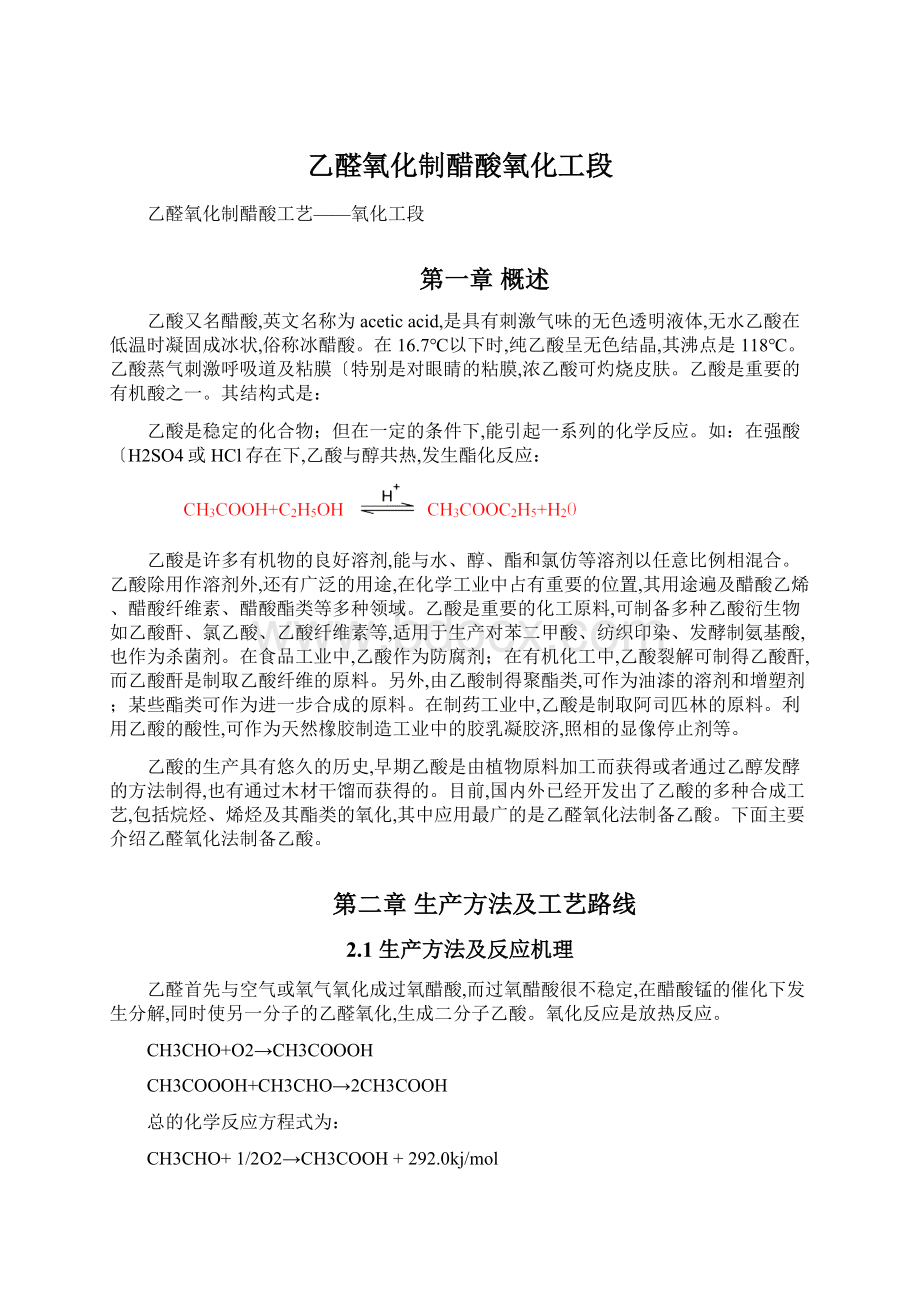
乙醛氧化制醋酸氧化工段
乙醛氧化制醋酸工艺——氧化工段
第一章概述
乙酸又名醋酸,英文名称为aceticacid,是具有刺激气味的无色透明液体,无水乙酸在低温时凝固成冰状,俗称冰醋酸。
在16.7℃以下时,纯乙酸呈无色结晶,其沸点是118℃。
乙酸蒸气刺激呼吸道及粘膜〔特别是对眼睛的粘膜,浓乙酸可灼烧皮肤。
乙酸是重要的有机酸之一。
其结构式是:
乙酸是稳定的化合物;但在一定的条件下,能引起一系列的化学反应。
如:
在强酸〔H2SO4或HCl存在下,乙酸与醇共热,发生酯化反应:
乙酸是许多有机物的良好溶剂,能与水、醇、酯和氯仿等溶剂以任意比例相混合。
乙酸除用作溶剂外,还有广泛的用途,在化学工业中占有重要的位置,其用途遍及醋酸乙烯、醋酸纤维素、醋酸酯类等多种领域。
乙酸是重要的化工原料,可制备多种乙酸衍生物如乙酸酐、氯乙酸、乙酸纤维素等,适用于生产对苯二甲酸、纺织印染、发酵制氨基酸,也作为杀菌剂。
在食品工业中,乙酸作为防腐剂;在有机化工中,乙酸裂解可制得乙酸酐,而乙酸酐是制取乙酸纤维的原料。
另外,由乙酸制得聚酯类,可作为油漆的溶剂和增塑剂;某些酯类可作为进一步合成的原料。
在制药工业中,乙酸是制取阿司匹林的原料。
利用乙酸的酸性,可作为天然橡胶制造工业中的胶乳凝胶济,照相的显像停止剂等。
乙酸的生产具有悠久的历史,早期乙酸是由植物原料加工而获得或者通过乙醇发酵的方法制得,也有通过木材干馏而获得的。
目前,国内外已经开发出了乙酸的多种合成工艺,包括烷烃、烯烃及其酯类的氧化,其中应用最广的是乙醛氧化法制备乙酸。
下面主要介绍乙醛氧化法制备乙酸。
第二章生产方法及工艺路线
2.1生产方法及反应机理
乙醛首先与空气或氧气氧化成过氧醋酸,而过氧醋酸很不稳定,在醋酸锰的催化下发生分解,同时使另一分子的乙醛氧化,生成二分子乙酸。
氧化反应是放热反应。
CH3CHO+O2→CH3COOOH
CH3COOOH+CH3CHO→2CH3COOH
总的化学反应方程式为:
CH3CHO+1/2O2→CH3COOH+292.0kj/mol
在氧化塔内,还有一系列的氧化反应,主要副产物有甲酸、甲酯、二氧化碳、水、醋酸甲酯等。
CH3COOOH→CH3OH+CO2
CH3OH+CO2→HCOOH+H2O
CH3COOOH+CH3COOH→CH3COOCH3+CO2+H2O
CH3OH+CH3COOH→+H2O
CH3OH→CH4+CO
CH3CH2OH+CH3COOH→CH3COOC2H5+H2O
CH3CH2OH+HCOOH→HCOOC2H5+H2O
3CH3CHO+3O2→HCOOH+2CH3COOH+CO2+H2O
4CH3CHO+5O2→4CO2+4H2O
3CH3CHO+2O2→CH3CH2+H2O
2CH3COOH→CH3COCH3+CO2+H2O
CH3COOH→CH4+CO2
乙醛氧化制醋酸的反应机理一般认为可以用自由基的链接反应机理来进行解释,常温下乙醛就可以自动地以很慢的速度吸收空气中的氧而被氧化生成过氧醋酸。
CH3CHO+O2→
过氧醋酸以很慢的速度分解生成自由基。
CH3COOOH→+OH
自由基CH3COO引发下列的链锁反应:
+CH3CHO→CH3CO+CH3COOH
CH3CO+O2→
+CH3CHO→+CH3COOOH
+CH3CHO→2CH3COOH
自由基引发一系列的反应生成醋酸。
但过氧醋酸是一个极不安定的化合物,积累到一定程度就会分解而引起爆炸。
因此,该反应必须在催化剂存在下才能顺利进行。
催化剂的作用是将乙醛氧化时生成的过氧醋酸及时分解成醋酸,而防止过氧醋酸的积累、分解和爆炸。
2.2工艺流程简述
2.2.1装置流程简述
本反应装置系统采用双塔串联氧化流程,主要装置有第一氧化塔T101、第二氧化塔T102、尾气洗涤塔T103、氧化液中间贮罐V102、碱液贮罐V105。
其中T101是外冷式反应塔,反应液由循环泵从塔底抽出,进入换热器中以水带走反应热,降温后的反应液再由反应器的中上部返回塔内;T102是内冷式反应塔,它是在反应塔内安装多层冷却盘管,管内以循环水冷却。
乙醛和氧气首先在全返混型的反应器-第一氧化塔T101中反应〔催化剂溶液直
接进入T101内,然后到第二氧化塔T102中,通过向T102中加氧气,进一步进行氧化反应〔不再加催化剂。
第一氧化塔T101的反应热由外冷却器E102A/B移走,第二氧化塔T102的反应热由内冷却器移除,反应系统生成的粗醋酸送往蒸馏回收系统,制取醋酸成品。
蒸馏采用先脱高沸物,后脱低沸物的流程。
粗醋酸经氧化液蒸发器E201脱除催化剂,在脱高沸塔T201中脱除高沸物,然后在脱低沸塔T202中脱除低沸物,再经过成品蒸发器E206脱除铁等金属离子,得到产品醋酸。
从低沸塔T202顶出来的低沸物去脱水塔T203回收醋酸,含量99%的醋酸又返回精馏系统,塔T203中部抽出副产物混酸,T203塔顶出料去甲酯塔T204。
甲酯塔塔顶产出甲酯,塔釜排出废水去中和池处理。
2.2.2氧化系统流程简述
乙醛和氧气按配比流量进入第一氧化塔〔T101,氧气分两个入口入塔,上口和下口通氧量比约为1:
2,氮气通入塔顶气相部分,以稀释气相中氧和乙醛。
乙醛与催化剂全部进入第一氧化塔,第二氧化塔不再补充。
氧化反应的反应热由氧化液冷却器〔E102A/B移去,氧化液从塔下部用循环泵〔P101A/B抽出,经过冷却器〔E102A/B循环回塔中,循环比〔循环量:
出料量约110~140:
1。
冷却器出口氧化液温度为60℃,塔中最高温度为75~78℃,塔顶气相压力0.2Mpa〔表,出第一氧化塔的氧化液中醋酸浓度在92~95%,从塔上部溢流去第二氧化塔〔T102。
第二氧化塔为内冷式,塔底部补充氧气,塔顶也加入保安氮气,塔顶压力0.1Mpa〔表,塔中最高温度约85℃,出第二氧化塔的氧化液中醋酸含量为97~98%。
第一氧化塔和第二氧化塔的液位显示设在塔上部,显示塔上部的部分液位〔全塔高90%以上的液位。
出氧化塔的氧化液一般直接去蒸馏系统,也可以放到氧化液中间贮罐〔V102暂存。
中间贮罐的作用是:
正常操作情况下做氧化液缓冲罐,停车或事故时存氧化液,醋酸成品不合格需要重新蒸馏时,由成品泵〔P402送来中间贮存,然后用泵〔P102送蒸馏系统回炼。
两台氧化塔的尾气分别经循环水冷却的冷却器〔E101中冷却,凝液主要是醋
酸,带少量乙醛,回到塔顶,尾气最后经过尾气洗涤塔〔T103吸收残余乙醛和醋酸后放空,洗涤塔采用下部为新鲜工艺水,上部为碱液,分别用泵〔P103、P104循环。
洗涤液温度常温,洗涤液含醋酸达到一定浓度后〔70~80%,送往精馏系统回收醋酸,碱洗段定期排放至中和池。
第三章工艺技术指标
3.1控制指标
序号
名称
仪表信号
单位
控制指标
备注
1
T101压力
PIC109A/B
MPa
0.19±0.01
2
T102压力
PIC112A/B
Mpa
0.1±0.02
3
T101底温度
TI103A
℃
77±1
4
T101中温度
TI103B
℃
73±2
5
T101上部液相温度
TI103C
℃
68±3
6
T101气相温度
TI103E
℃
与上部液相温差大于13℃
7
E102出口温度
TIC104A/B
℃
60±2
8
T102底温度
TI106A
℃
83±2
9
T102温度
TI106B
℃
85~70
10
T102温度
TI106C
℃
85~70
11
T102温度
TI106D
℃
85~70
12
T102温度
TI106E
℃
85~70
13
T102温度
TI106F
℃
85~70
14
T102温度
TI106G
℃
85~70
15
T102气相温度
TI106H
℃
与上部液相温差大于15℃
16
T101液位
LIC101
%
35±15
17
T102液位
LIC102
%
35±15
18
T101加氮量
FIC101
M3/H
150±50
19
T102加氮量
FIC105
M3/H
75±25
3.2分析项目
序号
名称
位号
单位
控制指标
备注
1
T101出料含醋酸
AIAS102
%
92~95
2
T101出料含醛
AIAS103
%
<4
3
T102出料含醋酸
AIAS104
%
>97
4
T102出料含醛
AIAS107
%
<0.3
5
T101尾气含氧
AIAS101A、B、C
%
<5
6
T102尾气含氧
AIAS105
%
<5
7
T103中含醋酸
AIAS106
%
<80
第四章岗位操作法
4.1冷态开车/装置开工
说明:
斜体字部分是在仿真范围外或必须和其它工段配合的操作。
4.1.1开工应具备的条件
〔1检修过的设备和新增的管线,必须经过吹扫、气密、试压、置换合格〔若是氧气系统,还要脱酯处理
〔2电气、仪表、计算机、联锁、报警系统全部调试完毕,调校合格、准确好用。
〔3机电、仪表、计算机、化验分析具备开工条件,值班人员在岗。
〔4备有足够的开工用原料和催化剂。
4.1.2引公用工程
4.1.3N2吹扫、置换气密
4.1.4系统水运试车
4.1.5酸洗反应系统
〔1首先将尾气吸收塔T103的放空阀V45打开;从罐区V402〔开阀V57将酸送入V102中,而后由泵P102向第一氧化塔T101进酸,T101见液位<约为2%>后停泵P102,停止进酸。
"快速灌液"说明,向T101灌乙酸时,选择"快速灌液"按钮,在LIC101有液位显示之前,灌液速度加速10倍,有液位显示之后,速度变为正常;对T102灌酸时类似。
使用"快速灌液"只是为了节省操作时间,但并不符合工艺操作原则,由于是局部加速,有可能会造成液体总量不守衡,为保证正常操作,将"快速灌液"按钮设为一次有效性,即:
只能对该按钮进行一次操作,操作后,按钮消失;如果一直不对该按钮操作,则在循环建立后,该按钮也消失。
该加速过程只对"酸洗"和"建立循环"有效。
〔2开氧化液循环泵P101,循环清洗T101;
〔3用N2将T101中的酸经塔底压送至第二氧化塔T102,T102见液位后关来料阀停止进酸;
〔4将T101和T102中的酸全部退料到V102中,供精馏开车;
〔5重新由V102向T101进酸,T101液位达30%后向T102进料,精馏系统正常出料,建立全系统酸运大循环。
4.1.6全系统大循环和精馏系统闭路循环
〔1氧化系统酸洗合格后,要进行全系统大循环:
V402T101T102E201T201
T202T203V209
E206V204V402
〔2在氧化塔配制氧化液和开车时,精馏系统需闭路循环。
脱水塔T203全回流操作,成品醋酸泵P204向成品醋酸储罐V402出料,P402将V402中的酸送到氧化液中间罐V102,由氧化液输送泵P102送往氧化液蒸发器E201构成下列循环:
〔属另一工段
顶顶全回流
T201T202T203
底E206P204V402P402
E201P102V102
等待氧化开车正常后逐渐向外出料。
4.1.7第一氧化塔配制氧化液
向T101中加醋酸,见液位后〔LIC101约为30%,停止向T101进酸。
向其中加入少量醛和催化剂,同时打开泵P101A/B打循环,开E102A通蒸汽为氧化液循环液通蒸汽加热,循环流量保持在700000KG/H〔通氧前,氧化液温度保持在70~76℃,直到使浓度符合要求〔醛含量约为7.5%。
4.1.8第一氧化塔投氧开车
<1>开车前联锁投入自动;
<2>投氧前氧化液温度保持在70~76︒C,氧化液循环量FIC104控制在700000KG/H。
<3>控制FIC101N2流量为120M3/H
<4>按如下方式通氧:
a>用FIC110小投氧阀进行初始投氧,氧量小于100M3/H开始投。
首先特别注意两个参数的变化:
LIC101液位上涨情况;
尾气含氧量AIAS101三块表是否上升。
其次,随时注意塔底液相温度、尾气温度和塔顶压力等工艺参数的变化。
如果液位上涨停止然后下降,同时尾气含氧稳定,说明初始引发较理想,逐渐提高投氧量。
b>当FIC-110小调节阀投氧量达到320M3/H时,启动FIC-114调节阀,在FIC-114增大投氧量的同时减小FIC-110小调节阀投氧量直到关闭。
c>FIC-114投氧量达到1000M3/H后,可开启FIC-113上部通氧,FIC-113与FIC-114的投氧比为1:
2。
原则要求:
投氧在0~400M3/H之内,投氧要慢。
如果吸收状态好,要多次小量增加氧量。
400~1000M3/H之内,如果反应状态好要加大投氧幅度,特别注意尾气的变化及时加大N2量。
d>T101塔液位过高时要及时向T102塔出一下料。
当投氧到400M3/H时,将循环量逐渐加大到850000KG/H;当投氧到1000M3/H时,将循环量加大到
1000M3/H。
循环量要根据投氧量和反应状态的好坏逐渐加大。
同时根据投氧量和酸的浓度适当调节醛和催化剂的投料量。
<5>调节方式:
a>将T101塔顶保安N2开到120M3/H,氧化液循环量FIC104调节为500000~700000KG/H,塔顶PIC109A/B控制为正常值0.2Mpa。
将氧化液冷却器〔E102A/B中的一台E102A改为投用状态,调节阀TIC104B备用。
关闭E102A的冷却水,通入蒸汽给氧化液加热,使氧化液温度稳定在70~76︒C。
调节T101塔液位为25±5%,关闭出料调节阀LIC101,按投氧方式以最小量投氧,同时观察液位、气液相温度及塔顶、尾气中含氧量变化情况。
当液位升高至60%以上时需向T102塔出料降低一下液位。
当尾气含氧量上升时要加大FIC101氮气量,若继续上升氧含量达到5%〔v打开FIC103旁路氮气,并停止提氧。
若液位下降一定量后处于稳定,尾气含氧量下降为正常值后,氮气调回120m3/H,含氧仍小于5%并有回降趋势,液相温度上升快,气相温度上升慢,有稳定趋势,此时小量增加通氧量,同时观察各项指标。
若正常,继续适当增加通氧量,直至正常。
待液相温度上升至84︒C时,关闭E102A加热蒸汽。
当投氧量达到1000M3/H以上时,且反应状态稳定或液相温度达到90︒C时,关闭蒸汽,开始投冷却水。
开TIC104A,注意开水速度应缓慢,注意观察气液相温度的变化趋势,当温度稳定后再提投氧量。
投水要根据塔内温度勤调,不可忽大忽小。
在投氧量增加的同时,要对氧化液循环量做适当调节。
b>投氧正常后,取T101氧化液进行分析,调整各项参数,稳定一段时间后,根据投氧量按比例投醛,投催化剂。
液位控制为35±5%向T102出料。
c>在投氧后,来不及反应或吸收不好,液位升高不下降或尾气含氧增高到5%时,关小氧气,增大氮气量后,液位继续上升至80%或含氧继续上升至8%,联锁停车,继续加大氮气量,关闭氧气调节阀。
取样分析氧化液成分,确认无问题时,再次投氧开车。
4.1.9第二氧化塔投氧
(1)待T-102塔见液位后,向塔底冷却器内通蒸汽保持氧化液温度在80︒C,控
制液位35±5%,并向蒸馏系统出料。
取T-102塔氧化液分析。
〔2T-102塔顶压力PIC112控制在0.1Mpa,塔顶氮气FIC-105保持在90M3/H。
由T102塔底部进氧口,以最小的通氧量投氧,注意尾气含氧量。
在各项指标不超标的情况下,通氧量逐渐加大到正常值。
当氧化液温度升高时,表示反应在进行。
停蒸汽开冷却水TIC-105,TIC-106,TIC-108,TIC-109使操作逐步稳定。
4.1.10吸收塔投用
〔1打开V49,向塔中加工艺水湿塔。
〔2开阀V50,向V105中备工艺水
〔3开阀V48,向V103中备料〔碱液
〔4在氧化塔投氧前开P103A/B向T103中投用工艺水
〔5投氧后开P104A/B向T103中投用吸收碱液
〔5如工艺水中醋酸含量达到80%时,开阀V51向精馏系统排放工艺水。
4.1.11氧化塔出料
〔1当氧化液符合要求时,开LIC102和阀V44向氧化液蒸发器E201出料。
用LIC102控制出料量。
4.2正常停车
4.2.1氧化系统停车
〔1将FIC102切至手动,关闭FIC-102,停醛。
〔2将FIC114逐步将进氧量下调至1000m3/H。
注意观察反应状况,当第一氧化塔T101中醛的含量降至0.1以下时,立即关闭FIC114、FICSQ106,关闭T101、T102进氧阀。
〔3开启T101、T102塔底排,逐步退料到V-102罐中,送精馏处理。
停P101泵,将氧化系统退空。
4.3紧急停车
4.3.1事故停车
主要是指装置在运行过程中出现的仪表和设备上的故障而引起的被迫停车。
采取的措施如下:
〔1首先关掉FICSQ102、FIC112、FIC301三个进物料阀。
然后关闭进氧进醛线上的塔壁阀。
〔2根据事故的起因控制进氮量的多少,以保证尾气中含氧小于5%〔V。
〔3逐步关小冷却水直到塔内温度降为60︒C,关闭冷却水TIC104A/B。
〔4第二氧化塔关冷却水由下而上逐个关掉并保温60︒C。
4.3.2紧急停车
生产过程中,如遇突发的停电、停仪表风、停循环水、停蒸汽等而不能正常生产时,应做紧急停车处理。
〔1紧急停电
仪表供电可通过蓄电池逆变获得,供电时间30分钟;所有机泵不能自动供电。
1.氧化系统
正常来说,紧急停电P101泵自动联锁停车。
a>马上关闭进氧进醛塔壁阀。
b>及时检查尾气含氧及进氧进醛阀门是否自动连锁关闭。
2.精馏系统
此时所有机泵停运。
a>首先减小各塔的加热蒸汽量。
b>关闭各机泵出口阀,关闭各塔进出物料阀。
c>视情况对物料做具体处理。
3.罐区系统
a>氧化系统紧急停车后,应首先关闭乙醛球罐底出料阀及时将两球罐保压。
b>成品进料及时切换至不合格成品罐V403。
〔2紧急停循环水
停水后立即做紧急停车处理。
停循环水时PI508压力在0.25Mpa连锁动作〔目前未投用。
FICSQ102、FIC112、FIC301三电磁阀自动关闭。
1.氧化系统停车步骤同事故停车。
注意氧化塔温度不能超得太高,加大氧化液循环量。
1.精馏系统
a>先停各塔加热蒸汽,同时向塔内充氮,保持塔内正压。
b>待各塔温度下降时,停回流泵,关闭各进出物料阀。
〔1紧急停蒸汽
同事故停车。
〔2紧急停仪表风
所有气动薄膜调节阀将无法正常启动,应做紧急停车处理。
1.氧化系统
应按紧急停车按钮,手动电磁阀关闭FIC102、FIC103、FIC106三个进醛进氧阀。
然后关闭醛氧线塔壁阀,塔压力及流量等的控制要通过现场手动副线进行调整控制。
其他步骤同事故停车。
2.精馏系统
所有蒸汽流量及塔罐液位的控制要通过现场手动进行操作。
停车步骤同二。
4.4岗位操作法
4.4.1第一氧化塔
塔顶压力0.18~0.2Mpa〔表,由PIC109A/B控制。
循环比〔循环量与出料量之比为110~140之间,由循环泵进出口跨线截止阀控制,由FIC104控制,液位35±15%,由LIC101控制。
进醛量满负荷为9.86吨乙醛/小时,由FICSQ102控制,根据经验最低投料负荷为66%,一般不许低于60%负荷,投氧不许低于1500M3/H。
满负荷进氧量设计为2871M3/H由FI108来计量。
进氧,进醛配比为氧:
醛=0.35~0.4,根据分析氧化液中含醛量,对氧配比进行调节。
氧化液中含醛量一般控制为3~4×10-2〔WT。
上下进氧口进氧的配比约为1:
2。
塔顶气相温度控制与上部液相温差大于13℃,主要由充氮量控制。
塔顶气相中的含氧量<5×10-2〔<5%,主要由充氮量控制。
塔顶充氮量根据经验一般不小于80M3/H,由FIC101调节阀控制。
循环液〔氧化液出口温度TI103F为60±2℃,由TIC104控制E102的冷却水量来控制。
塔底液相温度TI103A为77±1℃,由氧化液循环量和循环液温度来控制。
4.4.2第二氧化塔〔T102
塔顶压力为0.1±0.02MPa,由PIC112A/B控制
液位35±15%,由LIC102控制
进氧量:
0~160M3/H,由FICSQ106控制。
根据氧化液含醛来调节。
氧化液含醛为0.3×10-2以下
塔顶尾气含氧量<5%,主要由充氮量来控制。
塔顶气相温度TI106H控制与上部液相温差大于15℃,主要由氮气量来控制。
塔中液相温度主要由各节换热器的冷却水量来控制。
塔顶N2流量根据经验一般不小于60M3/H为好,由FIC105控制。
4.4.3洗涤液罐
V103液位控制0~80%,含酸大于70~80×10-2就送往蒸馏系统处理。
送完后,加盐水至液位35%。
4.5联锁停车
开启INTERLOCK,当T101、T102的氧含量高于8%或液位高于80%,V6、V7关闭,联锁停车。
取消联锁的方法:
若联锁条件没消除〔T101、T102的氧含量高于8%或液位高于80%,点击"INTERLOCK"按钮,使之处于弹起状态,然后点击"RESET"按钮即可;
若联锁条件已消除〔T101、T102的氧含量低于8%且液位低于80%,直接点击"RESET"按钮即可。