煤气净化作业指导书.docx
《煤气净化作业指导书.docx》由会员分享,可在线阅读,更多相关《煤气净化作业指导书.docx(13页珍藏版)》请在冰豆网上搜索。
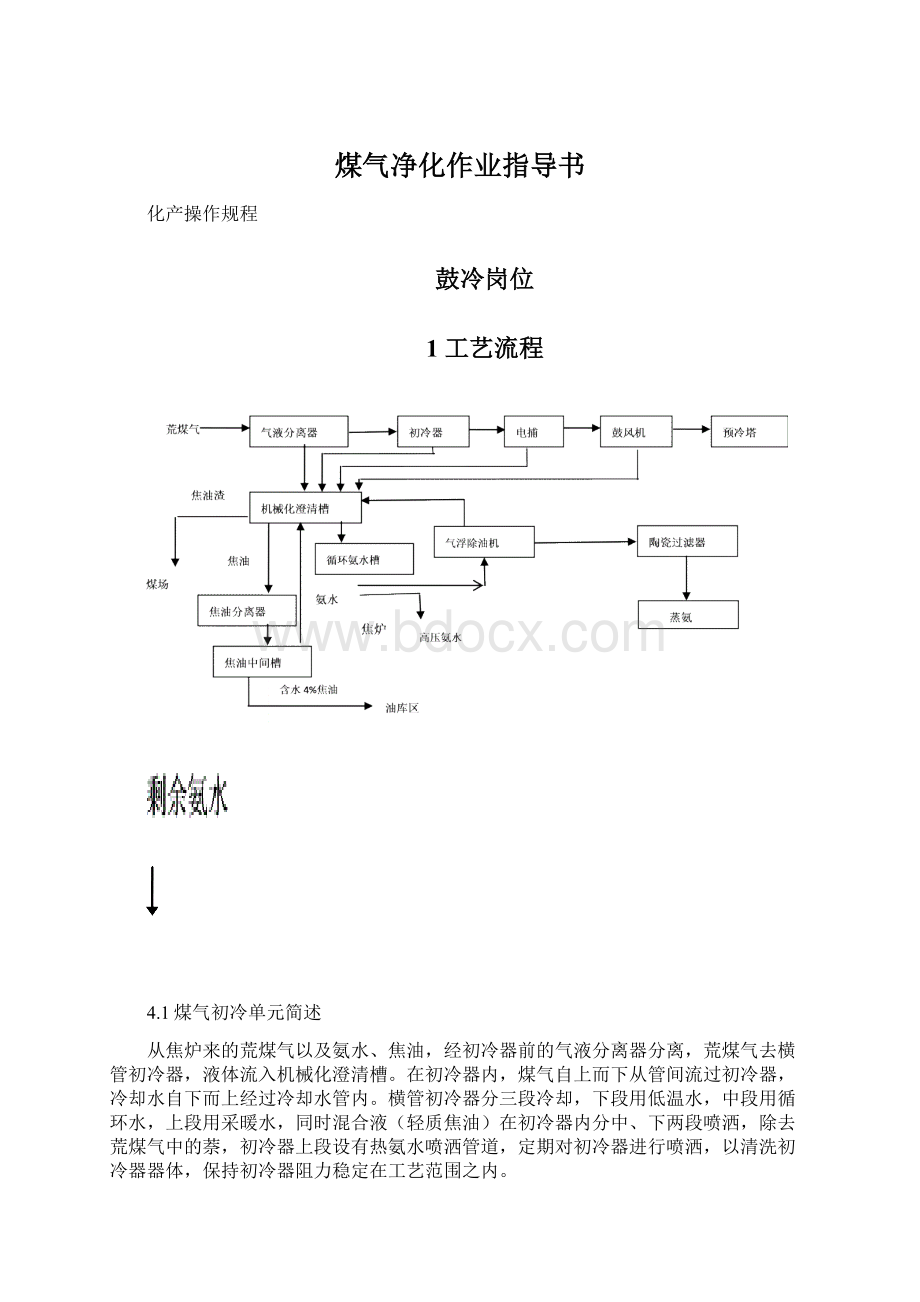
煤气净化作业指导书
化产操作规程
鼓冷岗位
1工艺流程
4.1煤气初冷单元简述
从焦炉来的荒煤气以及氨水、焦油,经初冷器前的气液分离器分离,荒煤气去横管初冷器,液体流入机械化澄清槽。
在初冷器内,煤气自上而下从管间流过初冷器,冷却水自下而上经过冷却水管内。
横管初冷器分三段冷却,下段用低温水,中段用循环水,上段用采暖水,同时混合液(轻质焦油)在初冷器内分中、下两段喷洒,除去荒煤气中的萘,初冷器上段设有热氨水喷洒管道,定期对初冷器进行喷洒,以清洗初冷器器体,保持初冷器阻力稳定在工艺范围之内。
离开焦炉的荒煤气冷凝下来的氨水、焦油等,以及初冷器、电捕等设备的冷凝液均进入机械化焦油氨水澄清槽,它们按密度不同在机械化焦油氨水澄清槽中分为三层;底部为焦油渣,用连续运转的刮板刮出;中间部分为焦油,靠压差自流入焦油分离器中加热,再用泵送到焦油中间槽;最上部为氨水,满流到循环氨水槽后,一部分送焦炉作循环氨水使用,一部分作为高压氨水供装煤除尘或集气道清扫使用,一部分作为剩余氨水经气浮除油机除油后自流入剩余氨水槽,由泵送入陶瓷过滤器处理,分离出的焦油自流入焦油分离器内。
4.3煤气捕雾工艺简述
初冷器冷凝后的煤气进入电捕焦油器下部,捕去焦油雾的煤气从顶部出来进入脱硫工序。
电捕焦油器为蜂窝式,强直流电在电晕极(负极)和沉淀极(正极)之间形成不均匀的高压电场,当煤气通过此高压电场时,夹带于煤气中的焦油雾和灰尘颗粒被荷电化,并沉淀于正极上(沉淀极),棸集成大颗粒焦油雾滴后,靠自身重力沉积于电捕焦油器底部,最终由电捕焦油器底部流出,经水封槽再流到鼓风地下池并送往鼓冷机械化焦油氨水槽。
当电极需要清洗时,可用热氨水或蒸汽清扫。
当安装在煤气管道上的氧分析仪检测出的氧含量超过1.0%(体积)时,电捕焦油器会发出报警,当氧含量超过2.0%(体积)时,电捕焦油器会自动断电,电源恢复手动进行。
4.4鼓风机单元简述
鼓风系统共有三台D1800-1.28/0.96型离心式鼓风机,分别由电机、液力耦合器、变速箱、风机本体组成,鼓风机输送介质为煤气,煤气在风机中为绝热压缩,煤气的压力是在转子的各个叶轮作用下,并经过压头转换被提高的。
转子旋转的速度愈大,煤气的密度愈大,离心力愈大,煤气沿工作叶轮运动的速度也愈大,离开工作叶轮后的静压头就愈高。
在输送过程中,煤气中的部分焦油、水被冷凝下来。
并通过风机排液系统排出,为化产品的回收,风机的安全运行,煤气的正常输送创造良好的条件。
2主要工艺指标控制
5.1温度指标(℃)
初冷器前煤气温度≤78-82
初冷器循环水上水温度≤32
初冷器循环水下水温度≤45
初冷器低温水上水温度≤18
初冷器低温水下水温度≤30
初冷器煤气出口温度20~25
两台初冷器煤气出口温差≤3~5
电捕绝缘箱温度90~120
鼓风机及主电机机体温度<85
所有轴承温度<85
鼓风机润滑油温度25~40
风机电机定子温度<135
备用风机的润滑油箱温度16-25
偶合器出口油温度≤80
机械化澄清槽工作温度65~80
焦油槽工作温度80~95
各电机温度≯60
轴承温度≯65
循环氨水温度70~80
脱硫岗位
焦炉煤气氨法催化脱硫是根据煤气中同时存在的NH3、H2S、HCN的情况下,三种组分在溶液中相互作用,用NH3吸收煤气中的H2S、HCN,并在催化剂的作用下,使吸收液再生的湿式氧化脱硫法。
脱硫塔内的吸收反应:
NH3+H2O→NH4OH
NH4OH+H2S(气)→NH4HS(液)+H2O(液)+10.94kcal
NH4OH+HCN→NH4CN+H2O
2NH4OH+H2S→(NH4)2S+2H2O
NH4OH+CO2→NH4HCO3
NH4OH+NH4HCO3→(NH4)2CO3+H2O
再生塔内的基本反应如下:
NH4HS+1/2O2→NH4OH+S↓+43kcal
(NH4)2S+1/2O2+H2O→2NH4OH+S
(NH4)2Sx+1/2O2+H2O→2NH4OH+Sx
除上述反应外,还进行以下副反应:
2NH4HS+2O2→(NH4)2S2O3+H2O
2(NH4)2S2O3+O2→2(NH4)2SO4+2S
4.2工艺流程
预冷脱硫工艺简述
从鼓风冷凝岗位送来的煤气首先进入直冷式预冷塔,用循环液冷却到25~30℃分别进入一级、二级、三级串联使用的脱硫塔(两塔并用为一级)脱除硫化氢,然后进入硫铵饱和器,进行脱氨。
预冷塔用剩余氨水作为循环冷却水自成循环系统,从塔底排出的热氨水经泵送至冷却器,用低温水换热冷却后进入预冷塔顶部,循环冷却煤气。
预冷循环液定期排污,送至鼓冷机械化澄清槽,同时为稳定循环冷却水量,需往预冷循环液系统中补充剩余氨水。
从预冷塔来的煤气进入脱硫塔,与塔顶喷淋的脱硫液逆向接触,脱除煤气中的H2S、HCN,然后由塔顶排出进入硫铵工序。
从脱硫塔底排出的脱硫液,经液封槽进入反应槽,再由脱硫液循环泵经预混喷嘴与从再生塔底部鼓入的压缩空气均匀混合,送入再生塔底部,脱硫液在塔内得以再生,再生后的脱硫液于塔上部利用高度差自流回脱硫塔循环使用。
自蒸氨工序浓氨水槽来的约10-15%浓度的氨水送入脱硫反应槽,作为脱硫液的补充碱源。
自再生塔顶部扩大部分来的硫磺泡沫利用位差自流入硫泡沫槽,经搅拌破碎后,用硫泡沫泵送入制酸干燥工段离心机,过滤后的清液送回脱硫液循环系统,过滤后的硫泡沫进入脱硫制酸泡沫槽。
在脱硫制酸系统不运行时,硫泡沫送入备用的板框压滤机进行处理,硫膏通过渣口排出,装槽外运;分离液流入地地下槽,回系统循环使用。
硫铵岗位
4生产原理及工艺流程
4.1硫铵工序生产原理
NH3+H2O→NH4OHNH4OH+H2SO4→NH4HSO4+H2ONH4HSO4+NH3→(NH4)2SO4
NH4OH+H2SO4→(NH4)2SO4
4.2.2蒸氨工艺流程
4.3硫铵工艺简述
煤气流程:
由脱硫工序来的煤气首先进入喷淋式饱和器,分为两路沿饱和器水平方向(环行)流动,每路煤气均由含游离酸的母液喷洒,以吸收煤气中的氨,两路煤气汇合后以切线方向进入饱和器后室,用母液进行二次喷洒以进一步除去煤气中的氨。
然后进入饱和器内旋风除酸器,除去煤气中夹带的酸雾液滴,从上部中心出管离开,再经饱和器煤气出口管上设置的酸雾捕集器进一步除酸后,煤气送至终冷洗苯工序。
母液流程:
饱和器满流出的母液自流入满流槽,再用小母液泵送回饱和器后室喷洒,满流槽上部的酸焦油捞至酸焦油箱。
饱和器反应室内的母液由中心降液管流至饱和器下部结晶室,在此进行晶粒成长和分级。
母液从结晶室上部进入母液循环泵进口管道,经母液加热器根据系统水平衡情况调至适宜温度后,用母液循环泵将其送入饱和器前室进行喷洒,其中有少部分母液在饱和器煤气进口处进行喷洒。
结晶泵从结晶室底部连续抽送含有硫铵的母液至结晶槽沉淀分离,分离后的母液沿回流管道自流至饱和器中段。
产品分离:
料液由结晶槽下来进入离心机进行初步分离脱水,母液进入回流管,晶体落入螺旋输送机后送至振动式流化床干燥器,用热空气对其进行干燥,再经冷风冷却后进入硫铵贮斗。
从硫铵贮斗下来的晶体经自动称量包装码垛机后,成为合格产品贮存。
引风除尘:
由振动流化干燥床排出的尾气,经旋分除尘器分离后,除尘下来的硫铵排入硫铵贮斗。
尾气再经引风机排至洗涤塔进行喷洒,再经雾膜分离器净化后排入大气。
加酸过程:
由酸碱库送来的硫酸至硫酸高置槽,经流量控制加至循环母液泵入口或满流槽内,以维持饱和器内稳定的母液酸度。
4.4剩余氨水蒸氨工艺简述
经除油过滤后的剩余氨水与蒸氨塔底排出的蒸氨废水换热后,与通过计量泵连续打入的液碱在静态混合器中均匀混合进入蒸氨塔蒸氨。
蒸汽进入再沸器对其进行加热,蒸汽走壳程,蒸氨废水走管程,废水被蒸汽加热至沸腾,产生的蒸汽进入蒸氨塔,将剩余氨水中氨气蒸出。
氨汽经蒸氨塔顶分缩器冷凝浓缩后进入氨汽冷凝冷却器,进一步冷却变成浓氨水,存放至浓氨水槽中,经浓氨水泵输送至脱硫工段作为碱源补充液使用(从分缩器顶部出来的氨汽也可直接进入硫铵饱和器中)。
塔底废水一部分自流到塔底废水槽,一部分流入再沸器补充废水。
换热后的蒸氨废水通过废水冷却器冷却后送至污水处理进一步处理。
5主要工艺指标控制
母液加热器后母液温度
48-53℃
饱和器阻力
≤2200Pa
离心机后硫铵含水
≤2﹪
干燥后硫铵含水
≤0.3%
饱和器后含氨
≤0.05g/m³
母液酸度
3.5~5.0%
剩余氨水处理量
≤90m3/h
蒸氨塔底温度
103-110℃
蒸氨塔顶温度
98-105℃
蒸氨塔顶分缩器后温度
96-100℃
冷凝冷却器氨水出口温度
≤45℃
废水冷却器出口温度
≤70℃
蒸氨塔底压力
40-55Kpa
蒸氨塔顶压力
≤25Kpa
硫铵操作室→硫铵一楼(热风机运行、下料及打包情况)→硫铵二楼(干燥系统运行情况)→硫铵三楼(离心机及除尘设备运行情况)→硫铵四楼(结晶槽提料及加酸情况)→硫铵五楼(硫酸高置槽液位情况)→硫铵除尘设备排风
硫铵操作室→泵区→母液加热器→饱和器→满流槽→母液贮槽→母液放空槽→硫铵操作室
蒸氨区域:
剩余氨水槽、碱槽、浓氨水槽、地下放空槽、各泵类设备、蒸氨塔及附属、各塔槽、管道阀门无泄漏、现场及远传的压力表、温度表液位计无异常,各泵类设备轴承温度液位振动无异常,罩壳完好,密封无泄漏,备用泵盘车正常。
硫铵一楼:
打包机、冷热风机、值班室、打包机轴承温度正常,各皮带无跑偏,机械手运行正常,各链条润滑正常,冷热风机轴承、温度、油位、振动无异响,车体内无异声,密封无泄漏,皮带无松动、磨损、护网完好、蒸汽管道及阀门无泄漏。
硫铵二楼:
输送机、干燥床、成品储斗输送机减速机轴承温度油位正常,联轴器螺栓无松动,轴叶片无磨损,压盖螺栓无松动异响,箱体无杂物无异声,干燥床筛网无泄漏,振动布无泄漏,床体焊接部位无磨损,成品储斗无积料。
硫铵三楼:
离心机、洗涤泵、洗涤塔及附属。
离心机轴承温度、油位振动无异响、泵体内无异声,罩壳完好密封无泄漏,冷却水正常,舱内无积料,转股螺丝无松动滤网无腐蚀,洗涤泵车轴温度、液位、振动无异响泵体内无异声,罩壳冷却水正常,密封无泄漏,洗涤塔管道阀门无泄漏,液位计灵活。
10安全与环保
10.1有毒、有害成份及安全防护措施
生产过程中产生的焦化废水全部送焦化装置酚氰废水处理站处理;酸液等介质集中收集回用。
10.3.3固体废弃物治理
固体废弃物主要为生活垃圾、酸焦油等,全部由厂内回收处理,不排入外环境。
因此对周围环境无影响。
粗苯岗位
4工艺流程
4.1.2终冷洗苯工艺流程
4.1.2终冷洗苯工艺简介
来自硫铵工序的煤气首先从底部进入直冷式终冷塔,与自上而下喷洒的循环液直接接触并得以冷却。
终冷塔用冷却液分上、下两段,从塔底排出的热水经泵送至冷却器,用低温水换热后进入终冷塔中部,作为下段煤气冷却液;从塔中部排出的热水经泵送冷却器,用低温水换热后进入终冷塔顶部,作为上段煤气冷却液。
终冷循环液连续排污,送至机械化澄清槽。
从终冷塔顶部出来的煤气从底部进入洗苯塔,自下而上与塔顶喷入的贫油逆向接触,洗去煤气中的苯类物质,塔底富油用富油泵送至粗苯蒸馏工序进行脱苯操作,煤气从洗苯塔顶出来大部分送至后续后续用户。
洗苯后的富油用富油泵送至粗苯进行脱苯,新洗油直接通过贫油泵前管道补入循环油系统。
4.2负压脱苯工艺流程
4.2.负压脱苯工序
从终冷洗苯工段送来的富油进入富油槽,用富油泵抽出经过粗苯冷凝冷却器与塔顶油气换热、然后分别进一、二段贫富油换热器换热到160~175C进入管式炉,经过管式炉对流段加热到185~195C,进入负压脱苯塔进行蒸馏脱苯。
塔顶出来的粗苯蒸汽经粗苯冷凝冷却器冷却后进入粗苯回流罐油水分离,分离出的粗苯一部分经回流泵打回脱苯塔顶回流,另一部分送到粗苯中间槽。
用粗苯产品泵送至粗苯贮槽;分离水经分离水泵送至分离水放空槽经分离水泵送至冷凝鼓风工段的机械化氨水澄清槽。
在精馏段侧线采出萘油,送至相应的萘油贮罐,定期用萘油泵送往油库工段焦油槽。
现场无法采出萘油。
脱苯塔底的热贫油经热贫油泵抽出经一、二段贫富油换热器换热和一段贫油冷却器冷却后进贫油槽,经冷贫油泵加压送二段贫油冷却器冷却至25C后送至终冷洗苯工段。
塔釜另设贫油循环泵,将热贫油抽出加压送至管式加热炉加热至230~245C后返回脱苯塔釜,作为负压脱苯热源。
为了保证循环油质量,从脱苯塔底引出1~1.5%热贫油送入再生系统。
再生系统,主要由真空罐、再生真空泵、再生冷凝冷却器,再生洗油罐、再生洗油泵等组成。
再生真空罐温度和压力控制在195~210℃、10~15kPa(绝压),再生热源由高温循环贫油提供。
再生贫油经闪蒸后油气经过冷凝冷却后送去冷贫油槽,。
再生残渣(稀渣)由渣油泵送油库焦油槽。
系统消耗的洗油定期送入新洗油槽通过新洗油泵补入油循环系统。
脱苯塔的真空排气经粗苯冷凝冷却器、粗苯回流罐抽出经不凝气冷却器冷却后进入真空机组,真空机组出口排出的不凝性气体经管道排入脱硫后的煤气系统。
真空机组采用苯环式,用苯做循环液。
5主要工艺指标控制
5.1终冷塔后煤气温度25~30℃
洗苯塔后煤气含苯≤3g/m3
富油含苯1.5~3%
入洗苯塔煤气温度25~28℃
入洗苯塔贫油温度28~30℃
夏季比入洗苯塔煤气温度高2~3℃
冬季比入洗苯塔煤气温度高3~5℃
终冷塔阻力≤1.0Kpa
洗苯塔阻力≤1.5Kpa
5.2进塔富油温度185~195℃
再生器顶部温度190-210℃
脱苯塔顶温度60~78℃
回流比4~6
二段贫油冷却器后贫油温度28~35℃
脱苯塔底部压力40-60kpa(绝压)
脱苯塔底贫油温度210~225℃
进脱苯塔底循环贫油温度230~235℃
冷凝冷却器后粗苯温度18~25℃
粗苯冷凝冷却器后富油温度50~70℃
一段贫油冷却器后贫油温度40~60℃
再生器顶部压力10~15kPa(绝压)
脱苯塔顶部压力35-45kpa(绝压)
油库岗位
4主要工艺指标控制
4.1各油槽(碱槽)上空高度≥300mm
4.2使用油槽最低液位≥1000mm
4.3装车时槽车上空高度≥300mm
4.4卸车后槽车内残留液位<100mm
4.5轴承温度<65℃
4.6电机温升<名牌规定或60℃.