3万 m3 外浮顶油罐施工方案.docx
《3万 m3 外浮顶油罐施工方案.docx》由会员分享,可在线阅读,更多相关《3万 m3 外浮顶油罐施工方案.docx(25页珍藏版)》请在冰豆网上搜索。
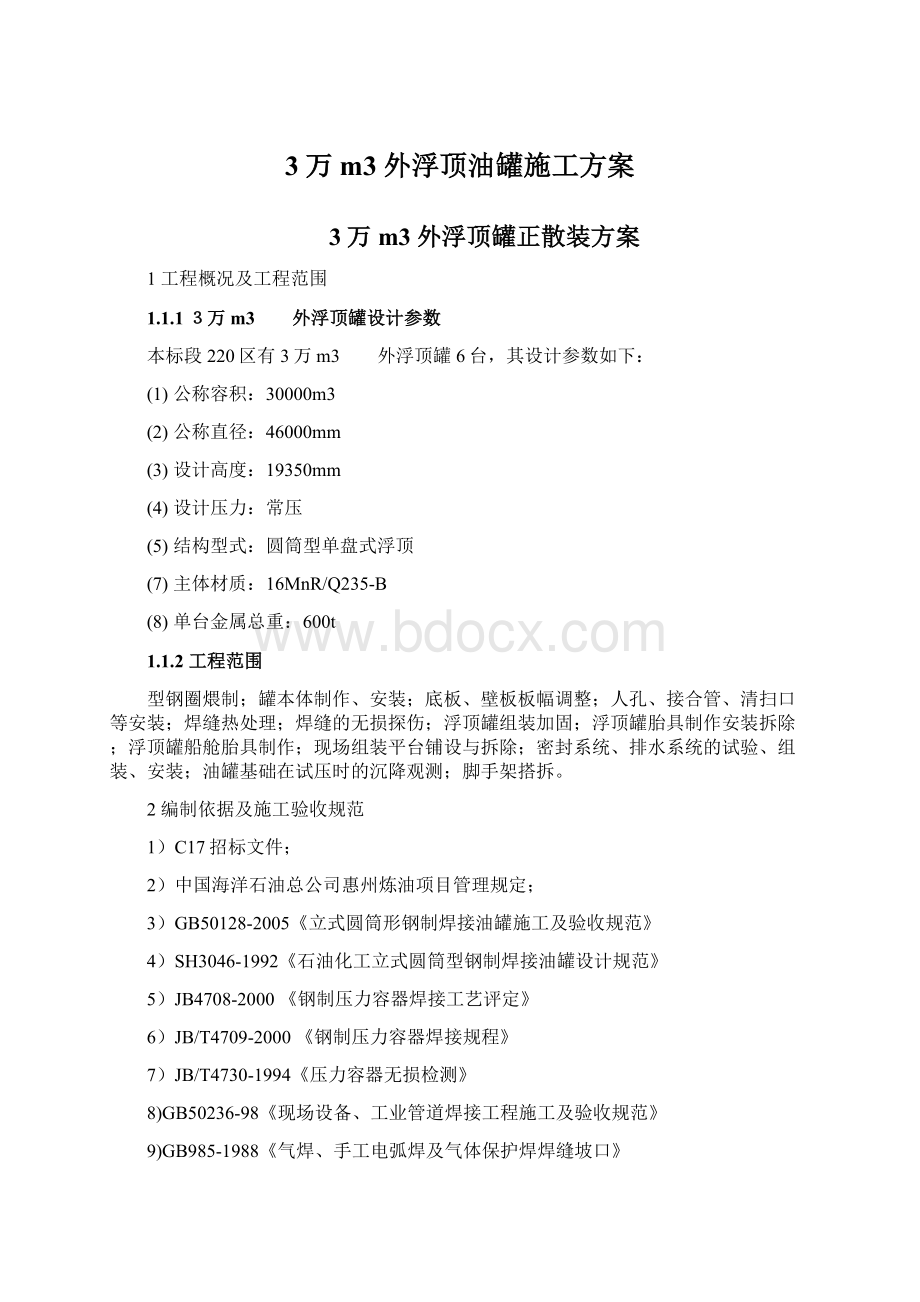
3万m3外浮顶油罐施工方案
3万m3外浮顶罐正散装方案
1工程概况及工程范围
1.1.13万m3 外浮顶罐设计参数
本标段220区有3万m3 外浮顶罐6台,其设计参数如下:
(1)公称容积:
30000m3
(2)公称直径:
46000mm
(3)设计高度:
19350mm
(4)设计压力:
常压
(5)结构型式:
圆筒型单盘式浮顶
(7)主体材质:
16MnR/Q235-B
(8)单台金属总重:
600t
1.1.2工程范围
型钢圈煨制;罐本体制作、安装;底板、壁板板幅调整;人孔、接合管、清扫口等安装;焊缝热处理;焊缝的无损探伤;浮顶罐组装加固;浮顶罐胎具制作安装拆除;浮顶罐船舱胎具制作;现场组装平台铺设与拆除;密封系统、排水系统的试验、组装、安装;油罐基础在试压时的沉降观测;脚手架搭拆。
2编制依据及施工验收规范
1)C17招标文件;
2)中国海洋石油总公司惠州炼油项目管理规定;
3)GB50128-2005《立式圆筒形钢制焊接油罐施工及验收规范》
4)SH3046-1992《石油化工立式圆筒型钢制焊接油罐设计规范》
5)JB4708-2000《钢制压力容器焊接工艺评定》
6)JB/T4709-2000《钢制压力容器焊接规程》
7)JB/T4730-1994《压力容器无损检测》
8)GB50236-98《现场设备、工业管道焊接工程施工及验收规范》
9)GB985-1988《气焊、手工电弧焊及气体保护焊焊缝坡口》
10)GB986-1988《埋弧焊焊缝坡口的基本形式及尺寸》
3施工方法选择
船仓及单盘采用临时架台组对,罐壁安装时采用内悬挂三角架脚手架和行走挂车配合正装法施工,罐本体的焊接纵缝采用药芯焊丝CO2气体保护焊,罐壁环缝和底板焊缝采用埋弧自动焊,为防止焊接变形主要采用刚性固定。
4油罐安装施工准备
4.1技术准备
①认真熟悉储油罐的施工图样和设计文件、标准规范及业主相关的管理规定,结合公司在大型储油罐施工方面的经验,制定切合实际的、先进实用的技术方案和施工工艺。
②做好焊接工艺规范、评定和组装工艺及工装,制定具体详细的施工程序及预制、组焊施工工艺,保证储罐的组装、焊接质量符合设计图样要求。
③施工前,对班组进行详细的技术交底,使所有的施工人员都能清楚的了解储罐的下料、组装、焊接的程序和各项技术数据及质量控制要求。
④按照储罐施工图样编制排版图,并核对管道、人孔、量油孔、附属结构等需在罐壁或罐顶开孔或焊接的部位、开孔补强板的覆盖部位是否开在或盖住焊缝或离焊缝的距离太近,并对排版图进行相应的调整,以满足设计及规范的要求。
并根据排版图及钢板的规格、尺寸编制下料方案,确定最佳的下料尺寸。
4.2施工准备
①根据施工平面布置图要求平整场地,搭设放样、下料及部件组装钢平台,安装卷板、平板、刨边、剪板等加工机械,并进行调试,确保运转良好,规划布置好储罐预制场地。
②制作储罐组装及焊接的工装、卡具,准备壁板、顶板预制的胎具,布置好焊接材料的存放库房和焊接材料烘干室。
③准备好组装、焊接机具,用于储罐焊接的自动焊机、半自动焊机应按要求准备充分,焊机应性能良好。
对施工用手段用料、技术措施用料进行调遣或就地购买,确保在施工前所需的这部分物资到位。
④搞好储罐组装现场的场地布置,现场的吊车行走道路应提前进行处理,预制件、组焊机具及水电线路应按平面布置图进行摆放和安装。
⑤组织所有参加施工的人员学习甲方的有关规章、制度,并进行罐区内施工方面安全教育,使所有参战职工均能严格遵守甲方的各项规定。
4.3材料检验及存放
①制造储油罐用的材料、配件和其它材料,应具有相应质量合格证明书,当无质量合格证明书或对质量合格证明书有疑问时,应对材料和附件进行复验,合格后方可使用。
②钢板、配件及焊接材料(焊条、焊丝、焊剂),应具有相应质量合格证明书。
③焊接材料(焊条、焊丝及焊剂)应具有质量合格证明书。
焊条质量合格证明书应包括熔敷金属的化学成份和机械性能;低氢型焊条还应包括熔敷金属的扩散氢含量。
当无质量合格证明书或对质量合格证明书有疑问时,应对焊接材料进行复验。
④建造储油罐选用的钢板,必须逐张进行外观检查,其表面质量应符合现行的相应钢板标准的规定。
⑤钢板表面锈蚀减薄量、划痕深度与钢板实际负偏差之和,应符合制造标准要求,并应符合下表规定:
序号
钢板厚度(mm)
允许偏差(mm)
1
4
-0.3
2
4.5~5.5
-0.5
3
6~7
-0.6
4
8~25
-0.8
5
26~30
-0.9
⑥对储罐壁板和罐底边缘板须进行超声波抽查,抽查数量为总量的20%,符合JB4730-94的Ⅱ级。
当发现有不合格的钢板时,应逐张检查。
⑦检验合格的材料应按规格材质摆放好,钢板应做标记,并按材质、规格、厚度等分类存放,存放过程中应防止钢板产生变形,严禁用带棱角的物体垫底。
型材应按规格存放,存放过程中防止型材产生变形,并应做标记。
⑧焊接材料应存放于专用库房中,焊材入库应严格验收,并做好标记。
焊接材料库房应按管理要求设置:
Ⅰ.焊材库必须干燥通风,库房内不得放置有毒气体和腐蚀性介质;
Ⅱ.焊材库房内温度不得低于5℃,空气相对湿度不应高于60%,并做好记录;
Ⅲ.焊材存放,应离开地面和墙壁的距离均不得少于300mm,并应严防焊材受潮;
Ⅳ.焊材应按种类、牌号、批号、规格和入库时间分类存放。
Ⅴ.建立焊材领用台帐,对每次焊材领用的数量、规格、牌号、批号、时间、焊接部位、由领用人签字后发放,以保证领用的焊材的可追溯性。
5油罐的预制工程
6台3万m3罐,全部在现场进行加工预制。
预制场由龙门自动切割机,30×3000滚板机,19mm剪板机,组成一条预制生产流水线,预制场材料倒运及配合由一台履带吊完成。
预制的半成品排放在预制场一侧,根据安装工程进度由汽车或10t托车运送安装现场。
(1)罐底预制:
中幅板用龙门自动切割机加工,切割前要对切割机进行检修、调整,并进行试切割。
弓形边缘板用半自动切割机下料,内侧直边过渡带坡口用自动切割机加工。
(2)罐壁预制全部采用龙门自动切割机加工坡口,加工后的壁板要在打磨胎具上打磨,MT抽检后,进行滚园,滚园后的壁板放在弧形胎具上存放和运输,以防变形,同时壁板预制进度,根据安装进度来安排。
(3)船仓预制:
全部采用19mm剪板机下料,分组单个整体组对其预制深度按要领书执行。
(4)单盘预制:
采用剪板机下料,人字排板,搭接接头。
(5)其他配件预制:
它主要包括中央排水管,导向量油管,滚动扶梯,抗风圈、加强圈等的预制加工按施工措施及要领书执行。
6底板安装
6.1底板的施工程序
6.2预制、下料
罐底板预制根据底板排板图进行下料。
排板图应符合下列规定:
1)罐底的排板直径,应按设计直径放大l%~2%。
2)边缘板的对接接头,采用不等边间隙,外侧间隙为6mm,内侧间隙为12mm。
3)中幅板的宽度不得小于1000mm;长度不得小于2000mm。
4)底板任意相邻焊缝之间的距离,不得小于200mm。
5)中幅板与边缘板相搭接的各小板,按计算尺寸放大100mm后进行直边切割下料。
罐底中幅板的预制在切割平台上进行,采用半自动切割机进行坡口加工。
弓形边缘板用半自动切割机进行切割、加工坡口,削边用数控切割机加工。
预制后的底板尺寸允许偏差,应符合下表的规定。
弓形边缘板应在(AC、BD)两侧100mm范围内按JB4730-94进行100%超声波检测,以达到Ⅱ级标准为合格;弓形边缘板加工后坡口表面进行磁粉检测,Ⅰ级合格。
底板尺寸允许偏差
序号
检查项目
允许偏差
示意图
1
弓
形
边
缘
板
AB、CD
±2.0mm
AC、BD、EF
±2mm
对角线之差|AD-BC|
≤3.0mm
坡口角度
±2.5°
2
中
幅
板
板宽AC、BD、EF
±1.5mm
6.3罐底铺设
基础验收合格后,确定方位,按排板图进行放样划线,然后进行垫板铺设→焊接→中幅板铺设焊接→边缘板铺设组焊中幅板第1层为手工焊封底,第二层为填充金属埋弧自动焊。
由于3万m2罐底直径46m,采用机械法吊装铺设,即汽车吊停在基础圈梁外侧。
基础沥青沙上铺设16~18mm钢板,履带吊开到基础上,在临时铺设的钢板上行走,采用两台吊车接力的方法进行铺板,顺序是由中心条板开始,然后铺两侧中幅板。
见下图:
由于板大,吊板时用12m平衡梁4对吊点吊装防止吊弯底板。
为防止焊接变形,要严格按焊接工艺要领书进行。
技术人员要随时观察,根据情况决定是否要采用刚性固定法来防止变形。
1)底板铺设前,应先会同有关部门对罐基础表面平整情况和整体几何尺寸、罐基表面标高、坡度进行验收,检查基础表面无裂缝,光泽度、局部凹凸度符合标准要求,基础强度、沉降观测点是否符合要求,检查基础的几何尺寸是否符合图纸要求。
基础验收的技术要求如下:
①中心坐标的允许偏差为±20mm。
②中心标高的允许偏差为±10mm。
③基础表面应光滑平整,在任意方向不应有突起的棱角。
从罐中心向周边拉线测量,基础表面局部凹凸度不大于25mm。
④沥青砂垫层表面应平整、密实、无突起、凹陷及贯穿裂纹。
同一圆周上各个测点必须满足下列要求:
相邻测点的标高差值不得大于5mm,任意点间的标高差不大于10mm。
⑤基础环墙顶面,在10m弧长度内,水平偏差不得大于6mm,整个圆周长度内,任意两点的高差不大于12mm。
2)底板的铺设按先垫板,再铺边缘板,最后中幅板的顺序进行,中幅板铺设按从中心向外铺设的顺序,先铺条形板。
3)垫板铺设时,丁字接头处不焊接,其它焊缝打磨平。
4)底板铺设用吊车吊板铺设,吊车在基础上时应垫钢板,以防压坏基础。
底板铺设时应及时调整组对间隙,同垫板焊接。
6.4底板铺设技术要求:
①罐底板全部采取对接,对口间隙为6±2mm,边缘板可采用不等间隙内侧12mm,外侧8mm。
对接口下部的垫板应紧贴底板,间隙不得大于1mm,边缘板对接口下部的垫板与基础环墙接触处,应将环墙开设深6mm,宽120mm的槽,用于安放垫板。
②底板垫板接口应增设δ=4mm的辅助垫板,垫板的对接焊缝应完全焊透,焊缝表面应打磨平整,应在中幅板垫板适当位置预留活口。
③底板铺设对口错边量不得大于1.5mm。
6.5焊接
1)底板选用的焊材:
母材钢号16MnR,手工焊E5015,埋弧自动焊H10Mn2,HJ431
2)弓形边缘板的对焊接采用手工焊。
先焊其外侧300mm焊缝,打底焊后进行渗透检查,以第二层开始每层错开50~70mm,焊接完成,上部磨平,进行磁粉和真空试检查,边缘板对接焊缝的其余部分在大角焊缝焊完后进行,为控制焊接引起的角变形和控制外部的成形,须安装防变形龙门板,并在边缘板外部焊缝处焊接引弧块。
3)中幅板的焊接采用手工焊打底、埋弧自动焊盖面成型,焊接顺序如下图,为防止焊接时引起钢板端部凸起,将T字缝与向上提起6~8mm,卡具型式及位置如下图示:
①距边缘板2m范围内焊缝暂留不焊接,在与边缘板组对后再焊接。
②边缘板剩余部分对接焊缝焊接,在焊第二层前将卡具拆下,进行焊接。
③焊完后,切割出边缘板与底板中幅板的接缝坡口,切割方法见下图。
④防变形夹具的安装方式见上图。
⑤中幅板焊缝及龟甲缝打底焊时,分成均匀8等份,同时对称进行焊接。
⑥通常长焊缝焊接时,为防止变形应在焊缝一侧加通长背杠。
7壁板安装
7.1预制
1)壁板预制前应按设计图样绘制排版图,所绘制的排版图应符合下列要求:
①各圈壁板的纵向焊缝宜向同一方向逐圈错开,错开距离以板长的1/3为宜,其距离最小不得小于500mm;
②底圈壁板的纵向焊缝与罐底边缘板对接焊缝之间的距离,不得小于300mm;
③罐壁开孔接管或开孔接管补强板外缘与罐壁纵向焊缝之间的距离,不得小于200mm;与环向焊缝之间的距离,不得小于100mm;
④包边角钢对接接头与壁板纵向焊缝之间的距离,不得小于200mm。
2)罐壁板预制在龙门切割机平台上进行放线切割下料,壁板预制不留调整板,一次下净料,预制一圈壁板的累计误差等于零,这样预制有利于保证罐体整体几何尺寸,采用这种方法,要求预制精度高。
3)壁板吊到数控龙门切割机平台上进行划线,核对尺寸,用龙门切割机进行切割,先割横焊缝的坡口一侧,后切割立焊缝坡口的一侧。
割时先按安装尺寸下料,后按图纸的坡口尺寸切割。
4)壁板下料后,根据质量检查标准进行检查,并检查其各尺寸偏差和坡口形式是否符合要求。
各尺寸偏差如下:
壁板下料的尺寸允许偏差
检查项目
允许偏差
示意图
壁
板
板宽AC、BD、EF
±1.5mm
板长AB、CD
±1.5mm
对角线之差│AD-BC│
≤3.0mm
直线度
AC、BD
≤1.0mm
AB、CD
≤2.0mm
卷制后
垂直方向
≤1.0mm(1m直线样板)
水平方向
≤4.0mm(2m弧形样板)
坡口角度
±2.5mm
5)壁板预制合格后,吊运到指定地点存放,存放地点距滚板机较近,存放时要按安装先后,分门别类存放,板边错开150mm。
6)壁板下完料检查合格后,在滚板机上滚弧,滚弧时应用前后拖架,所有壁板的内侧曲率半径均为R=40000mm。
壁板卷制后,应立置在平台上,水平方向用弦长不小于2m的弧形样板检查,其间隙不大于3mm。
垂直方向上用长度不小于lm的直线样板检查,其间隙不得大于1mm。
滚板示意图如下:
7.2底圈壁板开口接管壁板预制及热处理(如要求)
1)底圈壁板滚弧完毕后,按图纸及排板图要求,号线、开孔、组装开口接管(人孔、清扫孔、进出油管等)及开孔补强板。
开口接管的中心位置偏差不大于3mm,接管外伸长度允许偏差为±5mm,法兰密封面倾斜不大于法兰外径的l%且不大于3mm。
补强板安装前进行滚弧,弧度与壁板相同。
2)为防止焊接接管补强板焊接变形,焊接前应在罐内壁开孔处点焊一定数量的防变形板,待热处理完毕后再拆除,并应在焊接时注意采取合理的焊接顺序。
3)补强板及接管焊缝的打底焊采用手弧焊,打底焊道完成后进行着色检查,无缺陷后进行其余各焊道的焊接。
其余焊道采用药芯焊丝CO2气体保护焊。
4)接管及补强板焊接完毕后,在消除应力热处理之前对补强板进行气密性试验。
试验压力为0.1Mpa。
5)开孔接管及补强板组焊完毕并检验合格后,对开孔壁板进行整体热处理。
随炉处理试板两块。
热处理温度为580±15℃,保温时间为180分钟。
热处理曲线如下:
6).壁板入炉热处理必须置于专用的胎架之上(如下图)
胎架制作使用型钢制,其顶面弧度与壁板弧度相同,壁板热处理时,使用卡具将壁板固定于胎架之上,防止变形。
热处理完毕后,拆除防变形卡具并打磨光滑。
所有热处理完毕的焊缝均进行磁粉检查,符合JB4730-94Ⅰ级合格。
信号孔中涂抹润滑油。
壁板热处理完毕后再对其内弧用进行样板进行检查。
7.3弧形板的存运
壁板滚弧完毕后,保存和运输必须使用弧形托架。
存运前必须在板两侧标明油罐编号和壁板编号。
7.4组对、安装
1)在壁板组立前,应在存运胎架上安装好方帽,龙门板及蝴蝶板,如下图:
壁板的吊装用汽车吊进行,并使用吊梁,壁板吊装用9m长平衡梁4吊点吊装,对12mm的薄板为防止吊装变形用12#槽钢背杠加固(见下图)。
2)第一带壁板组立前,按下图示划线安装组对档板。
壁板逐张组对,每张安装二个加减丝以调节壁板垂直度。
安装纵缝组对卡具及方楔子,用以将壁板固定。
罐壁组装为对接组装,应保证罐壁内侧表面齐平。
整圈壁板全部组立后调整壁板立纵缝组对错边量,上口水平度及壁板的垂直度应符合以下要求:
①相邻两壁板上口水平的允许偏差,不应大于2mm,在整个圆周上任意两点水平的允许偏差,不应大于6mm。
②第一圈壁板的垂直度允许偏差,不大于3mm;其它各圈壁板的垂直度允许偏差不应大于该圈壁板高度的0.2%。
③罐壁总高度的垂直度允许偏差,不大于50mm。
④纵向焊缝的错边量为板厚的10%,且不大于1.5mm。
环向焊缝的错边量(任意点),不大于上圈壁板厚的10%,且不大于2mm。
⑤第一圈壁板检查lm高处任意点的半径允许偏差不得超过±20mm;其它各圈壁板的半径允许偏差不得超过±25mm(将圆周至少等分为30等分测定),每圈罐壁至少测量2个罐截面。
⑥罐壁局部凸凹变形,第一、第二圈不得大于8mm;第三以上不得大于10mm。
⑦第一圈壁板的纵焊缝与罐底边缘板对接焊缝之间的距离不得小于300mm,每圈壁板长度累计总偏差应为±10m。
3)第二至以上圈壁板的组装方法参照第一带壁板的组装。
环缝应安装组对用龙门板、槽钢。
4)组装第二带板前在第一带板上搭设简易脚手架,如下图示,以后组对上一带板时在下带板上搭设同样的脚手架,在罐人孔处搭设斜梯,以供上下脚手架,如下图示。
在浮顶施工时将浮顶下面的斜梯拆除,浮顶上面的斜梯逐层搭设,每台罐两层脚手架循环使用。
7.5壁板焊接
1)壁板焊接应检查坡口对口尺寸,纵缝对口间隙公差±1mm,环缝对口间隙为0~1mm。
罐壁板坡口的表面无损探伤(PT或MT)应合格。
2)壁板纵缝焊接
①壁板焊接应先焊纵缝,再焊环缝,纵缝焊接前,先焊上定位及防变形用龙门板,如下图示,然后拆下纵缝组对卡具,方可进行焊接。
②纵缝焊接时,应先焊外侧,焊接完毕进行清根、打磨、磁粉探伤,检查合格后焊内侧,纵缝焊接上端加熄弧板(如上图),纵焊、横焊起弧处加引弧棉。
第一圈壁板纵缝下端约300mm,用手工焊接;第二圈及纵缝下端150~200mm焊缝采用手工焊,其余为自动焊(气电立焊)。
③焊缝引弧处,在焊接完毕后应清除掉,经磁粉探伤检查合格后,用手工焊接,焊后应按规定进行射线探伤检查。
3)大角焊缝焊接
①大角焊缝焊接前安装防变形卡具,将第一圈壁板与底板边缘板垂直固定,如左图示。
焊缝内外侧手工打底,用角焊自动焊机(LT~7)焊接内盖面焊缝,外侧焊缝使用手弧焊填充、盖面。
②大角焊缝的焊接顺序为:
内外侧第一道手工打底→拆除外侧固定块及方楔子→磁粉探伤检查→外侧手弧焊填充、盖面→拆内侧固定块及方楔子→磁粉探伤检查→内侧自动焊盖面。
③第一圈壁板与底板边缘板的大角焊缝,必须满足图样要求,其圆弧需在焊满图样规定的焊接尺寸后,再焊接形成圆弧过渡,该焊缝的最终尺寸不得小于规定值。
4)壁板环缝焊接
①壁板环缝焊接采用埋弧自动焊方法进行。
各圈壁板的环缝均需要双面焊接成型。
环缝第一遍焊完后,对未焊透或成形不良的部位要打磨、修补,其每遍焊接的起弧和收弧部位应错开100mm以上。
②环缝焊接顺序为:
先焊外侧焊缝,外侧焊接完成后,罐内侧卡具拆除,然后使用砂轮进行清根,如果清根深度达到焊缝厚度的2/3,要用手工焊方法进行补焊,清理完后,经着色检验合格后,再进行内侧环缝焊接。
③壁板环缝焊接时使用横焊机进行焊接。
8浮顶安装
8.1浮顶的预制
1)浮顶预制材料数量多而繁杂,因而应按排版图及时做好标记,分类存放。
2)浮顶的边缘板、桁架、径向隔板、加强筋、连接板、船舱底板、船舱顶板及其附件的预制在罐外进行。
其切割下料要做好防变形措施,如用夹具固定拘束后再切割或采用小的切割规范,高速切割的同时,割咀后加水冷却。
切割后要用直尺进行检查,发现有较大变形时进行矫正。
3)型钢的下料用砂轮切断机,加强筋及桁架在平台上组焊成半成品,型材焊接时,掌握好焊接顺序,对接焊接,防止变形。
组焊后的加强筋用样板进行检查合格,若发现弯曲或翘曲变形,要进行校正合格。
8.2浮顶组装
1)浮顶组装工艺:
组装在浮顶临时胎架上进行(如下图),浮顶分为船仓和单盘两部分,采用满堂江临时架台组装工艺施工。
当罐底中幅板焊接和第二节壁板焊完,开始组对临时架台。
然后组对船仓和单盘。
浮顶安装前要把内部大型配件如中央排水管、搅拌器,导向管支座等吊装就位。
船仓吊装就位后要进行调整然后再焊接。
单盘按排板图铺放,从中心开始向四周铺设,全部采用于手工电焊弧,先焊短缝后焊长缝。
浮顶临时胎架组立时的坡度与图纸要求的浮顶坡度一致,同时浮顶临时胎架立柱与罐底加斜支撑,外侧部分横梁胎架同罐壁联接定位。
2)浮船组装顺序如下:
3)浮顶底板安装
①浮顶底板的安装使用条形排板方式,板与板之间进行搭接,一般搭接宽度≥30mm。
用线坠对准罐底板,在板的中心板上划中心线,确定浮顶板的中心;铺板时,从中心开始顺次向外铺设,为保证浮顶的几何尺寸,板安装直径放大60mm。
②浮顶底板安装时,先用吊车把板分若干堆,均匀的存放到浮顶胎架的不同部位,绝不允许集中堆放。
每堆存放不得超过2t,吊车落板时要轻稳。
在浮顶胎架上安装橡胶垫板,用卷扬机和滑车配合拖板到位进行安装。
③拖板时要人监护,防止卡滞和刮在架台上。
④排板时,把三张板重叠处,最上面的板割成一斜角。
这种做法防止边缘翘起,便于安装和焊接。
⑤浮顶底板安装后,只进行定位点焊,点焊注意使各板长边压实靠紧,焊接前再进行压缝点焊。
然后进行浮顶构件(环向、径向隔板、加强筋)所在部位焊缝的焊接,焊缝长度300mm左右为宜,焊后真空试漏合格。
4)浮顶边缘环板,隔板和加强筋的安装
在浮顶船舱底板上,按照其隔板和加强筋安装基准线分别划出边缘环板、隔板、加强筋、浮顶支柱、集水坑、呼吸阀、透气阀、浮顶人孔等的位置线,划线后用油漆作出明显的标记。
5)浮顶船舱顶板的安装
船舱顶板一般为一字形排板,板与板之间进行搭接,一般搭接宽度≥30m。
铺设方法与浮船底板相同,搭接缝点焊完毕后,点焊顶板与浮船隔板、析架。
6)浮顶组装技术要求
①浮顶板搭接宽度允许偏差为±5mm
②船舱的外边缘板与罐壁板之间的距离为300mm,允许偏差为±15mm。
③船舱内外边缘板的对接接头的错边量不应大于1.0mm。
④船舱内外边缘板的对口间隙为2±1mm。
⑤船舱外边缘板的铅垂度允许偏差不应大于3mm。
⑥用弧形样板检查,船舱内外边缘板的凹凸变形,其间隙不得大于5mm。
⑦船舱的底板、顶板的局部凹凸变形,用1m直尺检查,其间隙不得大于5mm。
⑧但盘板的局部凹凸变形,不得大于变形长度的4/1000,且不大于50mm。
8.3浮顶的焊接
1)浮顶的焊接采用手工焊接方法。
焊接时应采取防变形措施,采用小焊接规范,掌握好焊接顺序,以确保整个浮顶的几何形状和尺寸。
2)浮船板焊接
①浮船板的焊接从罐中心开始,均布焊工,对称进行焊接。
焊接顺序为:
先焊短焊缝,后焊长焊缝,先焊中部焊缝,后焊两边焊缝。
②浮顶边缘板的焊接我们采用多名焊工分段、对称朝一个方向同时进行施焊的方法进行。
③浮顶底板的搭接焊缝的上表面为连续焊,下表面为断续焊,焊100mm,隔200mm,其它要求见图样中规定。
④焊接内边缘板和外边缘板的对接焊缝时,要用弧形背杠进行防变形,隔板与中幅板间的角焊缝可用钢板块进行防变形。
⑤所有浮顶焊接均采用一根焊条焊接长度的跳焊法或分短退焊法。
并在焊接过程中专人监护,发现有异常变形,要随时修整或采取槽钢拘束限制变形。
⑥所有浮顶中幅板焊缝,隔板焊缝,边缘环板焊缝焊后,应按要求进行外观检查,真空、煤油试漏检查合格。
⑦浮顶船舱的焊接
浮顶船舱的焊接在浮顶组装后进行,其焊接顺序如下:
首先焊浮顶船舱顶板与隔板、加强筋间的角焊缝,此焊缝在船舱人孔开孔后进行焊接,焊接时保证顶板与隔板、加强筋压紧靠实。
然后焊接浮顶船舱顶板弓形边缘板焊缝,多名焊工均布,朝同