生产运行过程质量管理细则.docx
《生产运行过程质量管理细则.docx》由会员分享,可在线阅读,更多相关《生产运行过程质量管理细则.docx(29页珍藏版)》请在冰豆网上搜索。
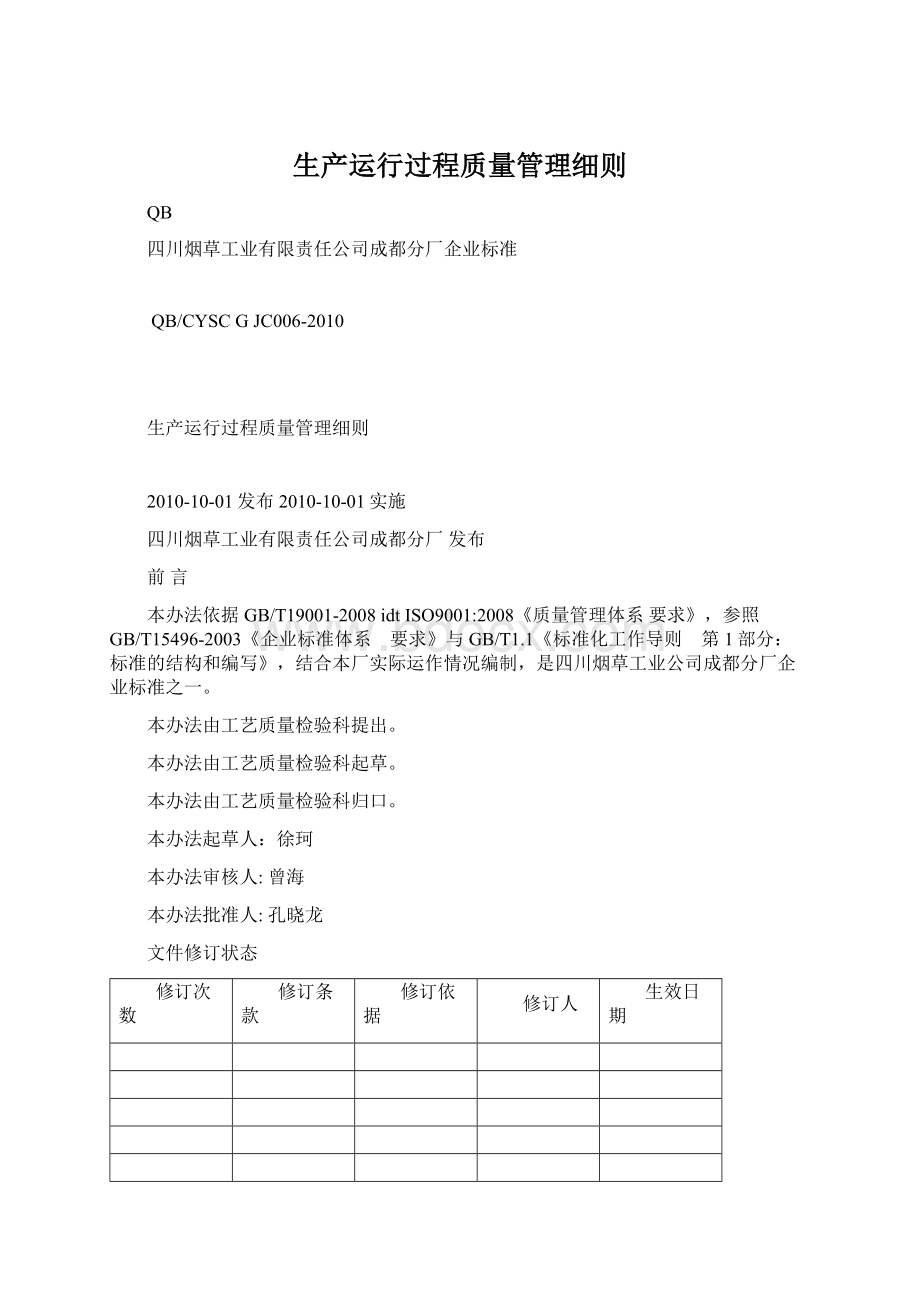
生产运行过程质量管理细则
QB
四川烟草工业有限责任公司成都分厂企业标准
QB/CYSCGJC006-2010
生产运行过程质量管理细则
2010-10-01发布2010-10-01实施
四川烟草工业有限责任公司成都分厂发布
前言
本办法依据GB/T19001-2008idtISO9001:
2008《质量管理体系要求》,参照GB/T15496-2003《企业标准体系 要求》与GB/T1.1《标准化工作导则 第1部分:
标准的结构和编写》,结合本厂实际运作情况编制,是四川烟草工业公司成都分厂企业标准之一。
本办法由工艺质量检验科提出。
本办法由工艺质量检验科起草。
本办法由工艺质量检验科归口。
本办法起草人:
徐珂
本办法审核人:
曾海
本办法批准人:
孔晓龙
文件修订状态
修订次数
修订条款
修订依据
修订人
生效日期
生产运行过程质量管理细则
1范围
本办法规定了四川烟草工业有限责任公司成都分厂对生产过程的工艺管理和人员的工艺行为规范。
本办法适用于四川烟草工业有限责任公司成都分厂生产、设备、材料、原料、环境等与质量相关的所有环节和部门。
2规范性引用文件
四川工业有限责任公司《工艺纪律管理办法》
3术语和定义
卷包落地烟丝:
指设备正常运行时掉落地面的烟丝(不包括设备保养及吹灰后的报废烟丝)。
4职责
4.1工艺质量检验科:
负责本管理要求的制订与修订;负责对卷烟制造部自我监督情况进行抽查;负责对卷烟制造部月度工艺执行率进行考核。
4.2卷烟制造部:
负责对相关人员宣传管理标准;负责实施、内部自我监督检查;可根据本标准要求建立内部管理细则;负责制定内部考核办法。
5工作程序及要求
5.1管理部分
编号
管理细则
扣分
1
生产过程中执行的技术文件、管理文件是无效文件;对于新的或更改后的技术文件、管理文件,未组织宣贯,导致操作人员对工艺质量要求不熟悉、不了解或错误执行。
6
2
擅自更改加工工艺方法、设备工艺参数、工艺技术要求等与产品质量相关的要求。
6
3
违反“工艺指挥生产”的原则;工艺、设备条件未满足工艺要求,就组织实施生产。
6
4
更换品牌、生产结束、节假日停产时,对生产现场的清洁卫生或设备维护保养等未安排。
2
5
设备运行状况不符合工艺要求时,未组织整改。
6
6
发现工艺行为不规范或所加工的在制品不符合技术文件、管理文件的规定时,未及时制止、处理。
6
7
生产过程中出现异常情况(如混牌等严重损害产品质量的情况)未及时按规定处理。
6
8
对设备、工艺、操作已经察觉不足,没有积极主动采取措施,将质量维护到良好状态。
6
9
对质量隐患未及时报告、处理。
2
5.2通用部分
序号
管理细则
扣分
1
工艺指标、参数的设置不符合工艺技术要求。
6
2
在制品不符合工艺技术要求时,未采取纠正措施;出现不合格品未及时联系、处理,导致不合格品流入下道工序。
6
3
更换牌号或其它需要隔离的情况时未清场,出现原材料、在制品、半成品、成品等的混杂、污染、混牌、错牌。
6
4
设备性能、生产条件不能满足工艺要求,未及时纠正、报告有关人员或部门;设备带病强行运转。
6
5
在生产现场吃零食、携带和使用化妆品。
6
6
在操作过程中使用异味、污染物品,对原材料、在制品、半成品、成品造成污染。
6
7
不同品牌、规格物料、合格品与不合格品未严格区分开。
6
8
在原材料、在制品、半成品、成品及生产设备、工(用)具上放置洗涤用品、茶杯、雨伞等与生产无关的异物。
6
9
用于盛装、载送原材料及其制品的用具未保持清洁,设备保养时油污零部件置于材料载送板上。
6
10
伪造工艺、质量数据。
6
11
投入的原材料不符合产品的工艺技术要求和配方规定。
6
12
未掌握相关工序工艺技术要求;工艺文件未妥善保管。
1
13
工序之间衔接不当,造成产品质量受损。
2
14
废料、原材料、在制品、半成品、成品、回收物料、掺兑物等标识不清或标识错误。
应作标识而未标识;或未及时标识。
2
15
生产现场不清洁,有霉变物质产生。
2
16
生产条件(水压、压缩空气压力、蒸汽压力及空调温湿度)未达到工艺要求而进行生产。
2
17
残留烟叶(片)、烟丝、烟梗、梗丝等再处理品未及时处理,造成降级或废弃。
2
18
生产结束(含更换牌号、节假日休息、设备保养等)时,在制品、半成品未排空进行卫生清理;生产现场和设备未打扫干净;烟叶(片)、烟丝、烟梗、梗丝、烟支、烟包、烟末、烟垢、粉尘等残留在生产线上;杂物流入下道工序或混入在制品中;废弃物料未清离现场;废弃物料中有可利用物料。
2
19
原材料、在制品、半成品的发放、使用未遵循先进先出的原则。
2
20
坐、踩、钩、挂、压原材料、在制品、成品、掺兑物。
2
21
野蛮装卸原材料、在制品、成品,导致实物质量受损。
6
22
停产后恢复生产未对设备物料输送带(通道)进行清洁处理。
2
23
对有环境温湿度要求的场所随意开启门窗。
2
24
未按规定填写自互检表、传递卡。
1
5.3制丝工段
序号
工序
管理细则
扣分
1
备料、(开箱、装包)
原料堆放场地不清洁或有异味。
2
2
野蛮装卸和坐、踩、压、钩、挂烟箱、烟包。
2
3
开箱切片(开包喂料)
霉变烟叶、纸板、包装捆扎带等未拣出,混入合格原料中。
6
4
若发现有质量问题的烟叶重量超过10公斤时,未及时报告现场工艺员。
2
5
筛分
振筛未及时清理,使筛孔堵塞。
2
8
除杂工序
除杂设备上的杂物未按规定清理,导致除杂效果差。
2
9
除杂剔除物料未及时按要求挑选回收。
1
10
回潮、松散、干燥工序
生产前未将管路余水、冷凝水排放干净,导致产生水渍烟。
2
11
生产前蒸汽管路、水管及其喷嘴未通畅,热风循环系统不正常开始生产。
2
12
当生产出现异常停机超过15分钟,在未停电和筒体能正常运转的情况下,筒体内的物料未转出。
2
13
流化床孔眼未保持通畅。
2
14
热风及排潮管路未保持通畅。
2
15
加料、加香工序
使用的料(香)液与生产牌号不相符。
6
16
香、料系统(流量计、加香、料泵、管路及喷嘴)漏香、料时继续生产。
6
17
加料(香)喷嘴角度、距离不得当、雾化效果差,物料不能正常受料(香)。
6
18
香、料施加与物料不同步(均匀),且加香、加料精度误差不符合工艺要求。
6
19
牌号交换未对加料、加香管道进行运空。
6
20
批次加料完成后未排空加料管道(除同品牌连开)。
2
21
批次烟叶进料前未对空管道进行料液预填充。
2
22
生产过程中更改加料、加香比例的设定值。
2
23
未定期对过滤器进行检查清理;滤网不清洁,有破损。
2
24
加料中未启动糖料搅拌器。
1
25
贮物料工序
擅自改变物料贮存量和贮存高度。
2
26
贮存环境、时间不符合工艺技术要求。
2
27
贮存内物料未使用完进料,或边进边出物料。
2
28
物料进、出柜时流量不稳定,过大过小,物料溢出输送带、堵塞或断料。
1
29
贮柜出料完毕后,未将柜内残留物料清扫干净。
1
30
贮柜内物料与标识不相符合。
1
31
切叶(梗)丝工序
调试切丝机切出的不合格叶、梗丝混入合格叶、梗丝中。
6
32
切叶(梗)丝宽度设定与技术标准的中心值不相符。
2
33
切叶丝间断性跑片,明显粗细丝,没有发现或已经发现但仍然继续运行。
2
34
生产结束后未将叶片、烟梗从设备中全部退出并松散贮存。
2
35
掺配工序
掺兑时错牌;掺兑物与工艺技术文件要求规定不一致。
6
36
掺配物未与叶丝同步且掺配精度误差不符合工艺要求。
6
37
掺兑时未将已变质的掺兑物或杂物选尽。
6
38
生产过程中更改掺配比例的设定值。
2
39
更换不同等级掺配物,未排空。
2
40
叶(梗)丝风选
风选风量调节不合理,风选后梗丝、叶丝纯净度不符合工艺要求。
6
41
风选风量调节不合理剔除梗签、梗块中合格叶(梗)丝比例>3%,或<1%。
6
42
香料发送、使用
发送的料(香)液与生产牌号不相符。
6
43
生产结束后或更换牌号时,未将料(香)液及时回收,未清洁加料(香)系统。
6
44
未按要求设置调制罐及加料工序料液缓冲罐料液温度。
6
45
料(香)液未按先进先用原则使用。
2
46
未定期清洗料液贮存罐和检查滤网是否畅通、有无破损。
2
47
中央控制
各工艺参数和设备参数设定、香辅料牌号与中控下发牌号不一致。
6
48
通过中控摄像观察现场物料生产是否正常,出现异常情况未及时与现场操作人员衔接处理。
6
49
贮丝房柜内烟丝与标识不相符合。
2
50
其他
光电设备表面有灰尘异物影响设备运行。
2
51
加料、加香、掺兑电子称明显偏差,仍然继续运行。
2
52
烘丝、烘梗丝水分仪明显偏差,仍然继续运行。
2
53
不同牌号烟丝批次更换时,批次间无明显间隔。
2
54
其它电子称或水分仪明显偏差,仍然继续运行。
1
55
生产过程中途断料致使车头车尾次数增多(批次更换除外)。
1
56
投料前未对相关设备进行有效预热。
1
57
因人为因素造成批次中途中断。
1
5.4卷包工段
5.4.1卷包工序防差错点及管理要求
防差错点
管理要求
辅料自查
卷包机台、大箱机操作工应在接班、过程加辅料时对辅料正确与否进行自查,并做记录
换烟剩余零散辅料应做好标识,存放于指定地点
生产中发现的不合格辅料应做好标识,存放于指定地点
原料自查
贮丝房操作工应在机台换烟、换柜时对成品烟丝使用是否正确进行自查、并做记录
贮丝房操作工应在每批收丝后,接班时对成品烟丝状态标识进行自查、并做记录
贮丝房操作工应对跑条回收烟丝的使用进行自查、并作记录
贮丝房操作工应对结存烟丝的使用进行自查、并作记录
标识自查
各工序操作工负责责任区域标识牌、卡的使用、更换以及自查
换烟自查
卷烟机操作工应对烟丝使用、通道、美琪、烟盘、烟车及标识、辅料、废烟、整理烟、跑条烟丝、设备调整、钢印、工艺参数调整进行自查
包装机操作工应对通道、辅料、废烟、整理烟、设备调整、钢印进行自查
大箱机操作工应对辅料、一号工程码进行自查
设备自查
卷包机台操作工应按点检记录项目要求对设备在线检测剔除装置进行点检自查、并做记录
整理烟
整理烟在转运过程中不同品牌的烟支,烟包应分开转运
整理烟应按品牌分区域进行整理,或采取其他避免混牌的措施
整理烟应使用与机台生产颜色相同的烟盘
整理烟应进行明确标识,标明整理烟的牌号、质量缺陷、处理意见
产品自查
卷包机台操作工应按产品自检要求进行自检。
(自检详细要求如下)
5.4.2卷、包机台产品首检及自检要求
5.4.2.1首检时间段及要求
5.4.2.1.1卷烟机:
生产出烟支后立即按《产品质量判定规则》检查烟支外观质量,并将前3盘烟支从美琪下盘检查烟支外观和烟支重量、圆周、总通风率指标,确认合格后方能正常生产。
5.4.2.1.2包装机:
a)白班生产出烟包后立即在8号轮后通道处将前20盒烟拿出,按《产品质量判定规则》检查烟支外观质量、烟包包装标识和烟包外观质量;生产出烟条后立即将前5条烟拿出,按《产品质量判定规则》全数检查烟条、烟包包装标识和外观质量,确认合格后方能正常生产。
b)中班、夜班生产出烟包、烟条后立即按《产品质量判定规则》检查烟支外观质量、包装标识和外观质量,并将前5条烟拿出:
前1条全数检查烟支外观质量,后4条全数检查烟条、烟包包装标识和外观质量,确认合格后方能正常生产。
5.4.2.2生产过程中的自检
5.4.2.2.1卷烟机烟支外观自检
根据不同机型产量规定自检频次(下表),自检时在烟支出口通道处同时抽取内外道各10支烟按《产品质量判定规则》进行烟支的外观质量检查判定。
卷烟机型
Passim
Protos
MK-95机
产量(箱)
2.0
2.0
1.0
5.4.2.2.2卷烟机烟支物理指标自检
每生产9件烟自检一次,自检时在烟支出口通道处,同时抽取内外道各15支烟按《产品质量判定规则》用在线综合测试台进行烟支的重量、圆周指标检查,并留存测试打印记录以备检查。
5.4.2.2.3包装机自检
根据不同机型产量规定自检频次(下表),自检时在提升机处随机连续抽取5条成品按《产品质量判定规则》进行烟条质量检查判定;任取其中1条进行烟条、烟包的质量检查判定;其中4盒按《产品质量判定规则》进行烟支外观质量检查判定,另外6盒拆掉小盒透明纸按《产品质量判定规则》进行烟包的质量检查判定。
包装机型
GDx2
ALFA
BE机
YB43
产量(箱)
3.0
3.0
2.0
1.5
5.4.2.3包装机和卷烟机每次自检后的烟支放在自检箱内,接受检验工的抽查。
5.4.2.4自检过程中不合格的烟支倒放、不合格的烟盒放在自检箱中。
5.4.3卷包过程防差错及工艺质量行为扣分标准
序号
工序
管理细则
扣分
1
烟丝输送
所送烟丝及标识牌与机台实际生产牌号不一致。
6
2
更换牌号时未及时与相关机台、工序衔接造成牌号混淆。
6
3
对喂丝机、输送带两侧、底盘、地面的烟丝、烟末未清理;将清扫卫生未经整理的烟丝、烟末、尘土混入合格烟丝中。
2
4
风力送丝管道粗糙,或风速过高过低,没有及时处理。
1
5
材料保管、发送
材料暂存库不清洁、有异味。
6
6
所送材料与机台生产品种不一致。
6
7
因保管、发放不当造成材料物理性质发生变化(如水分、纸张平整度等)或受污染。
6
8
装卸材料时未遵循轻拿轻放的原则,使材料质量受损。
2
9
滤棒输送
变形、弯曲等有明显质量缺陷的滤棒未挑选。
2
10
发送的滤棒与机台生产品种不一致。
6
11
停产期间滤棒未封存。
2
12
卷接包装
返工烟中的不合格烟支、烟包、烟条未选出。
6
13
符合翻箱要求而未主动翻箱,或需要翻箱检查而未检查。
6
14
装盘或卷接机烟支输出时的散乱、倒装烟支等未经整理转入包装工序。
1
15
梗签排管阻塞,或退梗含丝率>4%。
1
16
装箱及成品输送
散条、破损等不合格条包未挡下;不合格条包未及时反馈机台操作工。
6
17
装箱后纸箱出现封口不严;提升、输送过程中封箱带脱落;纸箱破损未及时处理。
2
18
生产过程中封箱机不进烟的通道挡块未放下。
0.5
19
自检
首检不合格。
2
20
未在自检时间段内进行自检(含物测),并按要求填写记录。
1
21
自检产品数量不符合自检数量要求。
1
22
自检实物不符合质量判定规则要求。
1
23
过程检验出现不合格进行翻箱,翻箱时间段>1个自检周期。
2
24
过程检验出现不合格进行翻箱,翻箱时间段>2个自检周期。
3
25
过程检验出现不合格进行翻箱,翻箱时间段>3个自检周期。
4
26
成品检验出现不合格进行翻箱,翻箱时间段>1个自检周期。
4
27
成品检验出现不合格进行翻箱,翻箱时间段>2个自检周期。
6
28
成品检验出现不合格进行翻箱,翻箱时间段>3个自检周期。
8
29
自检记录其他内容不完整、规范、准确。
0.5
30
检测点检
在线检测设备故障或效果不好,未及时通知电工维修。
0.5
31
在线检测设备故障或效果不好,未经工艺质量检验科工艺检验工确认直接暂停使用。
1
32
在线检测设备未按点检要求进行自查,或不能提供实物。
1
33
在线检测设备点检记录不真实。
0.5
34
各检测头表面未及时清洁,光电设备表面有灰尘异物影响检测器的运行。
0.5
35
电子秤人为损坏。
1
36
整理烟
不合格品进入整理房未明确存在的质量问题及处理意见。
1
37
不同品牌的烟支、烟包未分开转运、整理,存在混牌可能。
4
38
不同品牌的整理烟未用不同颜色的烟盘,未使用与机台颜色相同的烟盘。
1
39
整理桌上两种颜色的烟盘未背靠背放。
0.5
40
整好的半成品需通知检验工,未经检验合格就进入生产线。
2
41
因换牌不能及时消化的整选烟支、结存烟支未使用布罩放存放区点。
1
42
整理换牌后未及时更换品牌标识。
1
43
生产现场
烟盘未按要求使用,不同品牌的烟支未用不同颜色的烟盘。
1
44
空烟盘未倒置,每车烟支未使用完就用下一车烟支。
1
45
不同品牌的烟支未分开装烟车,烟盘上的烟支不整齐。
1
46
机台上的废烟箱装有其它物品或出现杂物。
1
47
夜班下班时,不轮保的设备上裸露在外的半成品未遮盖。
1
48
现场手工捡条封的空烟箱超过20个(吃饭时间除外)。
0.5
49
行手工捡条未拣满下层后就拣上层。
1
50
生产现场有与生产品牌无关的其他物料。
2
51
废胚处理
回收烟丝未按工艺要求、生产计划、牌号及时处理;烟丝纯净度不符合要求;标识不清楚,计量不准确。
2
52
废胚处理超过规定时间;节假日遗留的废胚、回收丝未采取防尘、防潮、防异味等防护措施。
2
53
跑条烟丝和废烟支未分班、分品牌回收。
0.5
54
跑条、废烟支内混有烟包、烟条、烟沫、废品及杂物。
1
55
跑条烟丝未经工艺质量检验科检验合格直接掺加。
非特殊情况下,不得放于剥烟机。
1
56
跑条未在整理车上整理,整理出的跑条未折断成20—30cm长。
0.5
57
装跑条、烟丝烟支的容器有杂物、胶水、油渍和水渍。
1
58
整理好的跑条烟丝中有短支烟、纸屑和杂物。
1
59
符合废弃条件物料(油烟、油跑条)未做相应处理,继续运行混入正常产品,无法分离。
5
60
其他
因设备调整、参数调整、部件安装等问题造成设备运行不好,或产生缺陷产品。
2
61
非本岗位造成的问题,已经知道可能对后续岗位造成的影响情况,对后续岗位人员没有提示。
1
62
本岗位造成的质量问题,可能影响到下一岗位的应提醒下一岗位人员,但未提醒。
5
63
在生产过程中有抵触情绪或弄虚作假的现象。
6
64
空压、真空有异常情况未发现,并继续开机对质量造成影响。
2
65
生产前未对各工序关键参数设置进行检查或有效监控,未对各设备的关键部位进行检查。
1
66
设备保养力度明显不够,或不周全。
1
67
各检测头表面不清洁,光电设备表面有灰尘异物影响设备运行。
1
5.4.3.1考核
5.4.3.1.1卷包过程防差错及工艺质量行为扣分采用一次性扣分的形式予以处罚;
5.4.3.1.2每月对卷包过程防差错及工艺质量行为扣分进行汇总,对卷烟制造部工艺纪律完成情况进行考核;
5.4.3.1.3若后果严重造成质量事故的,则按《质量事故处理办法》的相关条款进行处理。
5.5与生产条件有关的工序
序号
管理细则
扣分
1
当本供应点因设备故障或其他原因需要停止供应时,未及时向部门领导或使用部门、职能部门报告,使产品质量受损。
6
2
空调组未按规定检查、校对各温、湿度测定仪和自动测试探头,使生产环境温湿度不符合工艺要求。
2
5.6原材料储存、搬运及配送
序号
管理细则
扣分
1
原材料仓库不清洁、有异味、油污等,工艺条件不符合要求。
6
2
因保管、搬运、发放不当造成原材料物理性质发生变化或受污染。
6
3
按配方比例、数量送到制造部的原料计量不准确。
6
4
原材料保管、送料、堆码不符合工艺要求,标识不正确,牌号、品种、等级、批次等混淆。
6
5
错配、误配、混牌。
6
6
原材料包装破损,物料外漏。
1
5.7其它
序号
管理细则
扣分
1
设备不能满足工艺要求时,设备归口管理部门相关人员在接收到生产部门的报告后未及时作出处理,使设备相关性能及时恢复。
6
2
服从现场工艺、检验人员的检测、判定和处理,有异议的需按正常程序逐级进行反映和申诉,以任何不良方式、语言、态度干扰妨碍工艺质检人员的正常工作。
6
3
各环节发现的质量问题必须如实反映;出现质量事故,必须及时报告工艺质量检验科和相关职能部门,不得谎报、瞒报。
6
4
指使、怂恿、放任他人违反工艺纪律。
6
5
质量检测数据必须如实记录,擅自修改、损坏;以任何方式伪造、修改仪器的传输数据。
6
6相关记录
序号
记录名称
编号
保存地点
保存期限
1
申诉表
JL/CYSCGJC006-01
工艺质量检验科
2年
2
信息传递单
JL/CYSCGJC006-02
工艺质量检验科
2年
7附录
附录清单:
附录A:
申诉表
附录B:
信息传递单
附录A
(规范性附录)
申诉表编号:
JL/CYSCGJC006-01
申诉部门
申诉理由描述(如有实物请附实物粘贴栏):
部门领导日期
涉及相关部门
对申诉的意见:
部门领导日期
对申诉的意见:
部门领导日期
工艺检验科质量科
对申诉的意见:
部门领导日期
分管厂领导
对申诉的意见:
签名日期
实物粘贴栏:
附录B
(规范性附录)编号:
JL/CYSCGJC006-01