物流中心生产力评估指标00诀.docx
《物流中心生产力评估指标00诀.docx》由会员分享,可在线阅读,更多相关《物流中心生产力评估指标00诀.docx(40页珍藏版)》请在冰豆网上搜索。
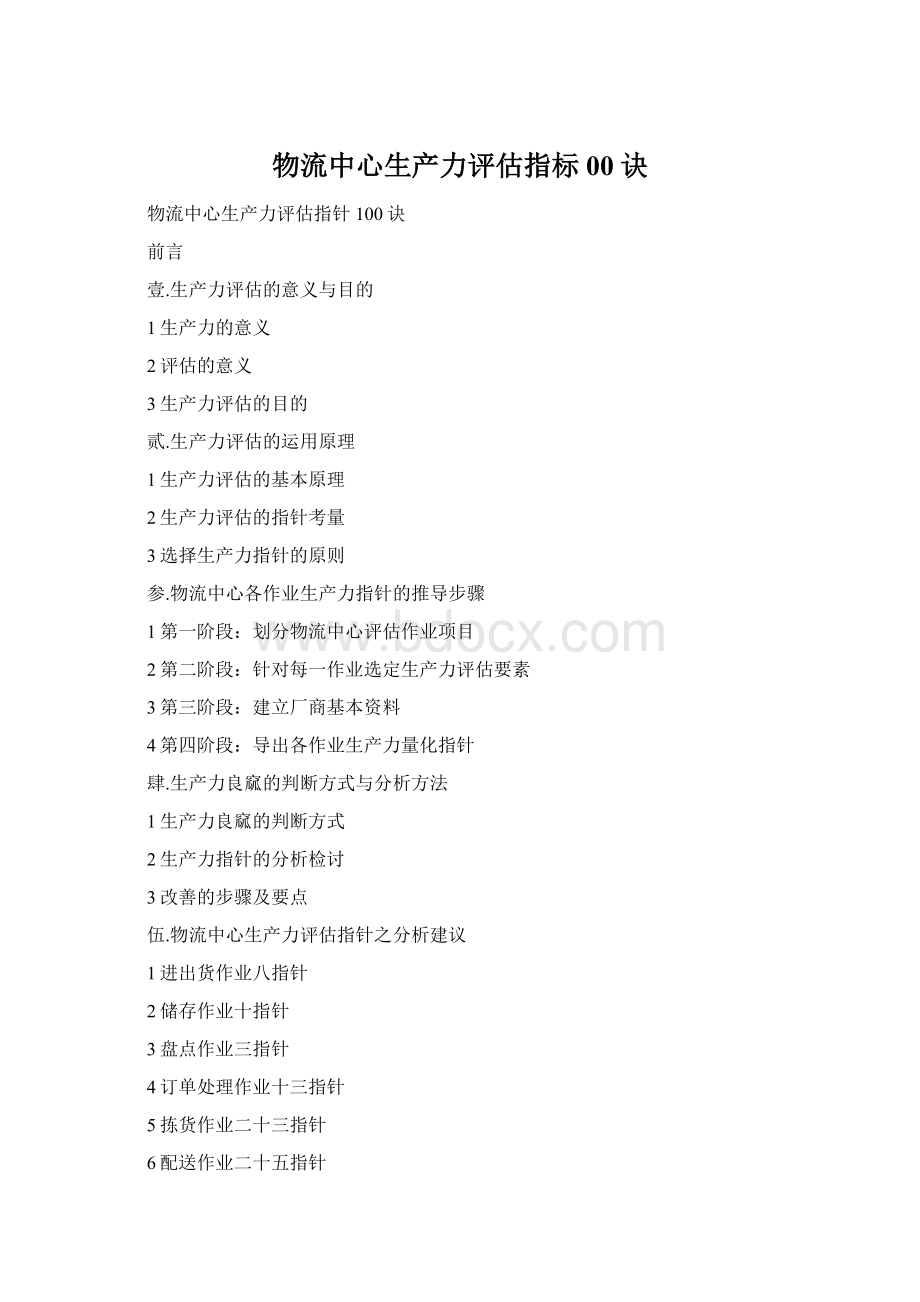
物流中心生产力评估指标00诀
物流中心生产力评估指针100诀
前言
壹.生产力评估的意义与目的
1生产力的意义
2评估的意义
3生产力评估的目的
贰.生产力评估的运用原理
1生产力评估的基本原理
2生产力评估的指针考量
3选择生产力指针的原则
参.物流中心各作业生产力指针的推导步骤
1第一阶段:
划分物流中心评估作业项目
2第二阶段:
针对每一作业选定生产力评估要素
3第三阶段:
建立厂商基本资料
4第四阶段:
导出各作业生产力量化指针
肆.生产力良窳的判断方式与分析方法
1生产力良窳的判断方式
2生产力指针的分析检讨
3改善的步骤及要点
伍.物流中心生产力评估指针之分析建议
1进出货作业八指针
2储存作业十指针
3盘点作业三指针
4订单处理作业十三指针
5拣货作业二十三指针
6配送作业二十五指针
7采购作业五指针
8非作业面评量十三指针
陆.物流中心作业面整合指针的推导
1各作业要素之指针推导
2各作业指针之推导
3物流中心作业面总指针之推导
4整合指针推导例
★下一页
前 言
企业经营绩效管理制度,大多侧重于计画与实绩,或前后期实绩的比较,其目的不外乎让可运用之资源(即人、设备、设施、时间、资金、材料等)发挥最有效的功能,这也就是生产力评估的目标。
一般企业评估生产力方式可分为量化与非量化两种,以非量化而言,无非是采取一些较主观的手法来对企业内的活动做评估,如此将容易产生认同上的问题,且往往无法适用于各个业者。
因此,配合一般业者的需要,我们先将生产力评估的研究重点摆在客观的量化分析上,划分了物流中心的作业及欲探讨的要素,综合研拟了近100个细部评估指针,希望能涵括物流中心营运的每个角落,以极细部的量化指针来对整个物流中心及其它物流厂家之营运作业进行深入的评估诊断,并将这些指针大小做为分析检讨的依据,提供业者未来改善方向的建议。
除此之外,唯恐业者无法由这些细部基本指针看出物流中心整体的营运状况,我们亦运用权重评点法及层级分析法的理论做基础来推导出几个代表性的整体指针,让业者可由此些指针评断企业目前的运作成效。
最后,我们也自行发展了一套生产力评估应用软件,将这套技术的使用变得更效率化。
本书共分为六个章节,第一章节主要探讨生产力评估的重要性,将生产力评估的意义、目的做一介绍。
第二章节点出生产力评估的运用原理并归纳原则要项。
第三章节将整个评估技术的规划、推导步骤作详细交待,让读者知道我们遵循这套做法的考量、原因。
第四章节则介绍指针好坏良窳的判断方式及经由指针发掘现状原因的分析方法,让业者能确实掌握量化评估的结果。
而第五章节是本书的重点,一一针对各个量化指针分析其代表意义、应用目的、可能状况及相对的改善方向,以供业者进行评估改善的参考。
最后一章节即进一步将已整理出的100项细部基本指针,整合推导出可反映各作业要素、各作业、整个物流中心绩效的代表性指针,让公司主管清楚了解整体作业面的运作绩效。
★上一页 ★下一页
壹、生产力评估的意义与目的
1生产力的意义
各种生产因素之有效利用度及对整体之贡献度。
2评估的意义
所谓评估是以科学的方法,对于一件事物或整个组织,依照事前设定的基准,评估其可行性或绩效,进而列举其优劣并提出改善建议。
一般对于评估结果的要求不外乎希望达到「可靠性」与「有效性」两目标。
3生产力评估的目的
生产力评估的主要目的即是要确定生产系统目前的生产力趋势,找出病因或突显出企业较弱环层,以便进一步达到「经营合理化」的目标。
★上一页 ★下一页
贰.生产力评估的运用原理
1生产力评估的基本原理
生产力的基本原理,简单地说,就是投入与产出之比。
此定义可适用于各种企业、工业或任何经济行为。
投入部份即各项资源,产出部份则包括产品、半成品及各种服务行为。
2生产力评估的指针考量
我们在进行物流中心生产力评估时,所考量的指针形式包括:
产出/投入、投入/产出、投入/投入、产出/产出四项。
3选择生产力指针的原则
1.选出的指针能反映组织整体或个别作业单位之生产力。
2.选出的指针能确实反映负责人或经理人之努力程度,对于非其所能控制之因素亦应能适当显示。
3.选出的指针要有助于问题点的分析,才能协助企业找到加强改善的方向。
因此,在本文中,我们所推导的指针将包含物流中心整体及个别作业部份,因若一味追求个别作业的细节可能会忽略个别作业绩效高但整体利益反而有害的情况;同样的,若只集中于整体企业的探讨,则可能无法找出个别作业的潜在问题,而使得企业逐渐走下坡。
另外,对于人员努力度的掌握,我们将由各个作业切入,来观察各部门作业员的生产力。
★上一页 ★下一页
参.物流中心各作业生产力指针的推导步骤
1第一阶段:
划分物流中心评估作业项目
将物流中心的活动划分为进出货、储存、盘点、订单处理、拣货、配送、采购作业及整体评量等八部份来进行诊断,才能真正掌握企业的生产力及发掘问题所在。
图6 物流中心基本作业流程
2第二阶段:
针对每一作业选定生产力评估要素
(1)以大多数物流中心的营运作业而言,生产力评估要素不外乎以下几点:
∙设施空间生产力:
衡量整个厂房空间设施是否已充份利用?
∙人员生产力:
衡量每一人员有无尽到自已最大能力?
∙设备生产力:
衡量资产设备有无发挥最大产能?
∙货品、订单效益:
衡量货品销售贡献是否达到预定目标?
∙作业规划管理力:
衡量目前管理阶层所做的决策规划是否适合?
∙时间生产力:
衡量每一作业有无掌握最佳时间?
∙成本力:
衡量此项作业的成本费用是否耗费不赀?
∙品质力:
衡量产品及服务品质有无达到客户满意的水准?
(2)选定各作业生产力评估要素
﹝进出货作业生产力评估要素:
空间利用(设施空间生产力)
人员负担(人员生产力)
设备稼动(设备生产力)
时间耗费(时间生产力)]
[储存作业生产力评估要素:
设施空间利用度(设施空间生产力)
存货效益(货品、订单效益)
成本(成本力)
呆废料情况(品质力)]
[盘点作业生产力评估要素:
盘点品质(品质力)]
[订单处理作业生产力评估要素:
订单效益(货品、订单效益)
客户服务品质(品质力)]
[拣货作业生产力评估要素:
人员效率(人员生产力)
设备稼动(设备生产力)
拣货策略(作业规划管理力)
时间效率(时间生产力)
成本耗费(成本力)
拣货品质(品质力)]
[配送作业生产力评估要素:
人员负担(人员生产力)
车辆负荷(设备生产力)
配送规划(作业规划管理力)
时间效益(时间生产力)
配送成本(成本力)
配送品质(品质力)]
[采购作业生产力评估要素:
采购成本(成本力)
进货采购品质(品质力)]
[非作业面评量生产力评估要项:
空间效益(设施空间生产力)
全体人员情况(人员生产力)
资产装备投资效益(设备生产力)
货品效益(订单、货品效益)
时间效益(时间生产力)
营运收支状况(成本力)]
3第三阶段:
建立厂商基本资料
4第四阶段:
导出各作业生产力量化指针
★上一页 ★下一页
肆.生产力良寙的判断方式与分析方法
1生产力良窳的判断方式
这些指针,我们如何判断其数据是好是坏,需不需要从事改善,就必须有判断良窳的基准。
好坏系来自比较,而比较的基准有三:
(1)同业其它公司的状况或同业之平均值
(2)企业过去的状况
(3)目标或预算
2生产力指针的分析检讨
其分析检讨步骤如:
1.发掘问题点
2.确认问题点
3.探求原因
4.寻求解决方式
3改善的步骤及要点
步骤一由问题点中决定亟待解决的问题。
步骤二收集有关事实,决定改善目标。
步骤三分析事实,检讨改善方法。
步骤四拟定改善计画。
步骤五试行改善。
步骤六检讨试行实施结果,并使之标准化。
步骤七设定管制标准,励行管理。
★上一页 ★下一页
伍.物流中心生产力评估指针之分析建议
1.进出货作业八指针
□码头使用率
□码头尖峰率
应用目的
观察码头的使用情况,是否因数量不足或规划不佳造成拥塞无效率的问题。
计算说明
码头使用率=
进出货车次装卸货停留总时间
码头月台数×工作天数×每日工作时数
(进出货车次装卸货停留总时间可由表1与表2记录中加总求得)
码头尖峰率=
尖峰车数
码头月台数
□每人时处理进货量
□每人时处理出货量
□进货时间率
□出货时间率
应用目的
评估进出货人员的工作分摊及作业速率,以及目前的进出货时间是否合理。
计算说明
每人时处理进货量=
进货量
进货人员数×每日进货时间×工作天数
每人时处理出货量=
出货量
出货人员数×每日出货时间×工作天数
进货时间率=
每日进货时间
每日工作时数
出货时间率=
每日出货时间
每日工作时数
若进出货人员共享,则以上指针应将进出货量、时间合并加总:
每人时处理进出货量=
进货量+出货量
进出货人员数×每日进出货时间×工作天数
进出货时间率=
每日进货时间+每日出货时间
每日工作时数
每台进出货设备每天的装卸货量
应用目的
评估每台进出货设备的工作分摊
计算说明
每台进出货设备每天的装卸货量=
出货量+进货量
装卸设备数×工作天数
每台进出货设备每小时的装卸货量
应用目的
评估每台进出货设备的工作效率。
计算说明
每台进出货设备每小时的装卸货量=
出货量+进货量
装卸设备数×工作天数×每日进出货时数
2储存作业十指针
储区面积率
应用目的
衡量厂房空间的利用率是否恰当。
计算说明
储区面积率=
储区面积
物流中心建物面积
指针意义
储区是物流中心不可或缺的部份,因而掌握储区占整个物流中心厂区的比 率,可使整体作业更顺畅。
可供保管面积率
应用目的
判断储区内信道规划是否合理。
计算说明
可供保管面积率=
可保管面积
储区面积
指针意义
可供保管面积率为扣除信道后货品的可保管面积占整个储区的比例,因而此指针大小主要在于评估信道空间的安排。
一般好的信道设计应注意以下几点;
(1)流量经济性
(2)空间经济性(3)设计顺序(4)分支信道、内部信道、工作空间信道及安全设施信道的存在(5)信道宽度的决定。
而根据这五点,图29为信道空间相对整厂空间的较佳比率关系图。
□储位容积使用率
□单位面积保管量
应用目的
用以判断储位规划及使用的料架是否适当,以有效利用储位空间。
计算说明
储位容积使用率=
存货总体积
储位总容积
单位面积保管量=
平均库存量
可保管面积
平均每品项所占储位数
应用目的
由每储位保管品项数的多寡来判断储位管理策略是否应用得当。
计算说明
平均每品项所占储位数=
料架储位数
总品项数
指针意义
平均每品项所占储位数若能规划在0.5~2之间,即使无明确的储位编号,也较能迅速存取货品,不至于造成储存、拣货作业人员找寻的困难,也较不会产生同一品项库存过多的问题。
库存周转率
应用目的
库存周转率可用来检讨公司营运绩效,以及做为衡量现今货品存量是否适 当的指针。
计算说明
库存周转率=
出货量
平均库存量
或
营业额
平均库存金额
指针意义
周转率愈高,库存周转期间愈短,表示用较少之库存完成同样的工作,使积压在存货上的资金减少。
换句话说,即表示资金的使用率高,利润也会因货品的周转率提高而增加。
库存掌握程度
应用目的
做为设定产品标准库存的比率依据,以供存货管制参考。
计算说明
库存掌握程度=
实际库存量
标准库存量
库存管理费率
应用目的
衡量公司每单位存货的库存管理费用。
计算说明
库存管理费率=
库存管理费用
平均库存量
呆废料率(数量、金额)
应用目的
用来测定物料耗损影响资金积压状况。
计算说明
呆废料率=
呆废料件数
平均库存量
或
呆废料金额
平均库存金额
指针意义
一般来说,若物料停滞仓库时间超出其周转期间,则可视为
呆料处理。
3.盘点作业三指针
盘点数量误差率
应用目的
衡量库存管理优劣,作为是否加强盘点或改变管理方式的依据,以减低公司 的损失机会。
计算说明
盘点数量误差率=
盘点误差量
盘点总量
指针意义
若公司甚少实施盘点,则损失率将无法确实掌握,而损失率不知道则实际毛利便无法知道,实际毛利无法知到则实际损益也将无法知晓;然一旦连损益都不清楚的事业,则其经营也就变得无意义了。
状况陈述若盘点误差数量过高(在计算机记忆中有库存,但仓库中却无现品,或在计算机中记录无库存,但仓库中却有现品),显示公司对于库存品的管理仍有很大缺失。
□盘点数量误差率
□盘点品项误差率
应用目的
由盘点误差数量及误差品项两者间指针数据的大小关系,来
检讨盘点误差主要的发生原因。
计算说明
盘点数量误差率=
盘点误差量
盘点总量
盘点品项误差率=
盘点误差品项数
盘点实施品项数
平均盘差品金额
应用目的
判断是否需采行ABC分类,或现今已采行之ABC存货重点分类是否发生作 用?
计算说明
平均每件盘差货品之金额=
盘点误差金额
盘点误差量
□平均每日来单数
□平均客单数
□平均每订单包含货品个数
□平均客单价
应用目的
观察每天订单变化情形,据以研拟客户管理策略及业务发展状况。
计算说明
平均每日来单数=
订单数量
工作天数
平均客单数=
订单数量
下游客户数
平均每订单包含货品个数=
出货量
订单数量
平均客单价=
营业额
订单数量
订单延迟率
应用目的
反映交货的延迟状况。
计算说明
订单延迟率=
延迟交货订单数
订单数量
指针意义
公司营运的最终目的是要有能力继续吸收更多的客户与订单,而影响订单多寡的两个主要因素不外乎价格与交运能力。
而交运能力即指交货期管理力,若能确实掌握交货的准确度,则能加以提升公司的信誉以吸收更多的客户。
□订单延迟率
□订单货件延迟率
应用目的
评量公司是否应实施客户重点管理。
计算说明
订单延迟率=
延迟交货订单数
订单数量
订单货件延迟率=
延迟交货量
出货量
指针意义
客户之服务水准是存货管理决策之重要考虑因素。
但若客户众多时,公司为了使有限之人力、物力做最有效之运用,则不得不做重点管理。
未采重点管理之企业,在订单多时,订单处理人员为了使订单积压减少,常会先处理比较简单的订单,而对订单数量多处理手续较繁杂的大客户反而容易忽略,此种「小户驱逐大户」的现象,对企业绩效影响甚大。
立即缴交率
应用目的
观察公司接单至交货的处理时间,及紧急插单的需求情况。
计算说明
立即缴交率=
未超过12小时出货订单
订单数量
□顾客退货率
□顾客折让率
应用目的
检测公司货品销货退货情况,以便尽早谋求改善。
计算说明
顾客退货率=
顾客退货数
出货量
或
客户退货金额
营业额
顾客折让率=
销货折让数
出货量
或
销货折让金额
营业额
□客户取消订单率
□客户抱怨率
应用目的
检测客户满意度。
计算说明
客户取消订单率=
客户取消订单数
订单数量
客户抱怨率=
客户抱怨次数
订单数量
指针意义
「客户」是每一家公司之所以存在的门户,而「客户订单」更是每一公司能够继续营运的基本要件,因此设法降低客户取消订单率及抱怨次数的确是刻不容缓的工作。
缺货率
应用目的
反映存货控制决策是否得宜?
应否调整订购点与订购量的基准。
计算说明
缺货率=
接单缺货数
出货量
指针意义
指客户订货时,查寻库存缺货以至无法接单或无法按时出货的比率。
短缺率
应用目的
反映出货作业的精确度。
计算说明
短缺率=
出货品短缺数
出货量
指针意义
短缺率为在出货前或交货后才发现货品短少的比率。
5.拣货作业二十三指针
拣货时间率
应用目的
衡量拣货耗费时间是否合理。
计算说明
拣货时间率=
每日拣货时数
每天工作时数
指针意义
拣货时间花费过高或过低,其影响因素不外乎:
(1)出货量多寡
(2)拣货员数量多寡
(3)人员、设备、作业方式配合所导致的效率高低
每人时平均拣取能力
(每人时拣取品项数
每人时扱取次数
每人时拣取材积数)
应用目的
衡量拣货的拣取效率,来找出隐藏在作业方法与管理方式中的问题所在。
计算说明
每人时拣取品项数=
订单总笔数
拣取人员数×每日拣货时数×工作天数
每人时扱取次数=
拣货单位累计总件数
拣取人员数×每日拣货时数×工作天数
每人时拣取材积数=
出货品材积数
拣取人员数×每日拣货时数×工作天数
指针意义
每人时平均拣取能力需同时考量「每人时平均拣取品项数」、「每人时平均拣取量」、「每人时拣取材积数」三指针。
在物流中心中,一般拣货都是以品项为单位,一个品项拣完再寻找下一品项,因此,对较人工、机械化物流中心,或是出货多属于少量多样的物流中心而言,其走行寻找时间可能较动手拿取货品的时间来得长,所以「每人时拣取品项数」之指针较能代表拣货效率,其数值高即表示在单位时间内每位人员的拣货效率不错。
反之,对已采行自动化拣货系统之物流中心,或出货多属于多量少样的物流中心而言,并不需花费太多时间在走行寻找品项上(有自动指示系统的帮助,拣货员将能快速找到欲拣取品项),反倒是动手拿取的时间相对较长,其中有可能是要动手拿取的次数较多,也有可能是对象材积大不容易快速拿取或与设备配合不良,因而以「每人时扱取次数」及「每人时拣取材积数」将较能反映出公司的拣货效率,其数值高表示单位时间内每位人员的拣货效率佳。
此外,若公司觉得不论走行寻找或动手拿取之时间对公司影响皆大,则可以「每人时拣取品项数」、「每人时扱取次数」及「每人时拣取材积数」三指针之乘积做为判断拣货效率的指针。
□拣货时间率
□每人时平均拣取能力
应用目的
同时观察此二指针,由如今所花费的拣货时间及运作的拣货效率来决定目前公司应着手改善的方向。
计算说明
拣货时间率=
每日拣货时数
每天工作时数
每人时平均拣取能力:
?
每人时拣取品项数=
订单总笔数
拣取人员数×每日拣货时数×工作天数
?
每人时扱取次数=
拣货单位累计总件数
拣取人员数×每日拣货时数×工作天数
?
每人时拣取材积数=
出货品材积数
拣取人员数×每日拣货时数×工作天数
拣取能量使用率
应用目的
检测拣货能量及其使用率,以判断如今的业绩是否与投入资源相配合。
计算说明
拣取能量使用率=
订单数量
一天目标拣取订单数×工作天数
(「一天预期的标准拣货量」为在现有的人员、设备下,公司预期一天的标准拣货量。
)
指针意义
「拣取能量使用率」是实际拣货量与预期标准拣拣货量的比率,也就是计画与实绩的比较,可反映出公司业绩能再扩张及目前现有拣货人力、设备能量的运用程度。
□拣取能量使用率
□每人时平均拣取能力
应用目的
检查公司目前设定之标准拣货量合不合理?
亦即公司对于拣货人员、设备产能的预估需不需要做调整?
计算说明
拣取能量使用率=
订单数
一天目标拣取订单数×工作天数
每人时平均拣取能力:
?
每人时拣取品项数=
订单总笔数
拣取人员数×每日拣货时数×工作天数
?
每人时扱取次数=
拣货单位累计总件数
拣取人员数×每日拣货时数×工作天数
?
每人时拣取材积数=
出货品材积数
拣取人员数×每日拣货时数×工作天数
拣货责任品项数
应用目的
衡量拣货员的工作负荷与效率是否得当?
计算说明
每位拣货员负责品项数=
总品项数
分区拣取区域数
指针意义
一般在面积过大,同一拣货单货品可能分散颇远的情况下,我们可考虑采行「分区拣取」或「接力拣取」的拣货策略。
所谓
?
分区拣取:
将拣取作业场地做区域划分,每一作业员负责拣取固定区域内的商品。
?
接力拣取:
先决定出数字拣货员各自分担的产品项目或料架责任范围后,各个拣货员只拣取理货单中自己所负责的部份,然后以接力的方式将拣货单交给下一位拣货员。
使用此种分工合作一张理货单的方式,将可能缩短整体的拣货动线,减少人员及设备移动的距离,更可提升拣货效率。
拣取品项移动距离
应用目的
检讨拣货的走行规划是否符合动线效率,且目前储区(拣货区)的布置是否得当。
计算说明
拣取品项移动距离=
拣货行走移动距离