管道对接焊缝的超声波检测.docx
《管道对接焊缝的超声波检测.docx》由会员分享,可在线阅读,更多相关《管道对接焊缝的超声波检测.docx(18页珍藏版)》请在冰豆网上搜索。
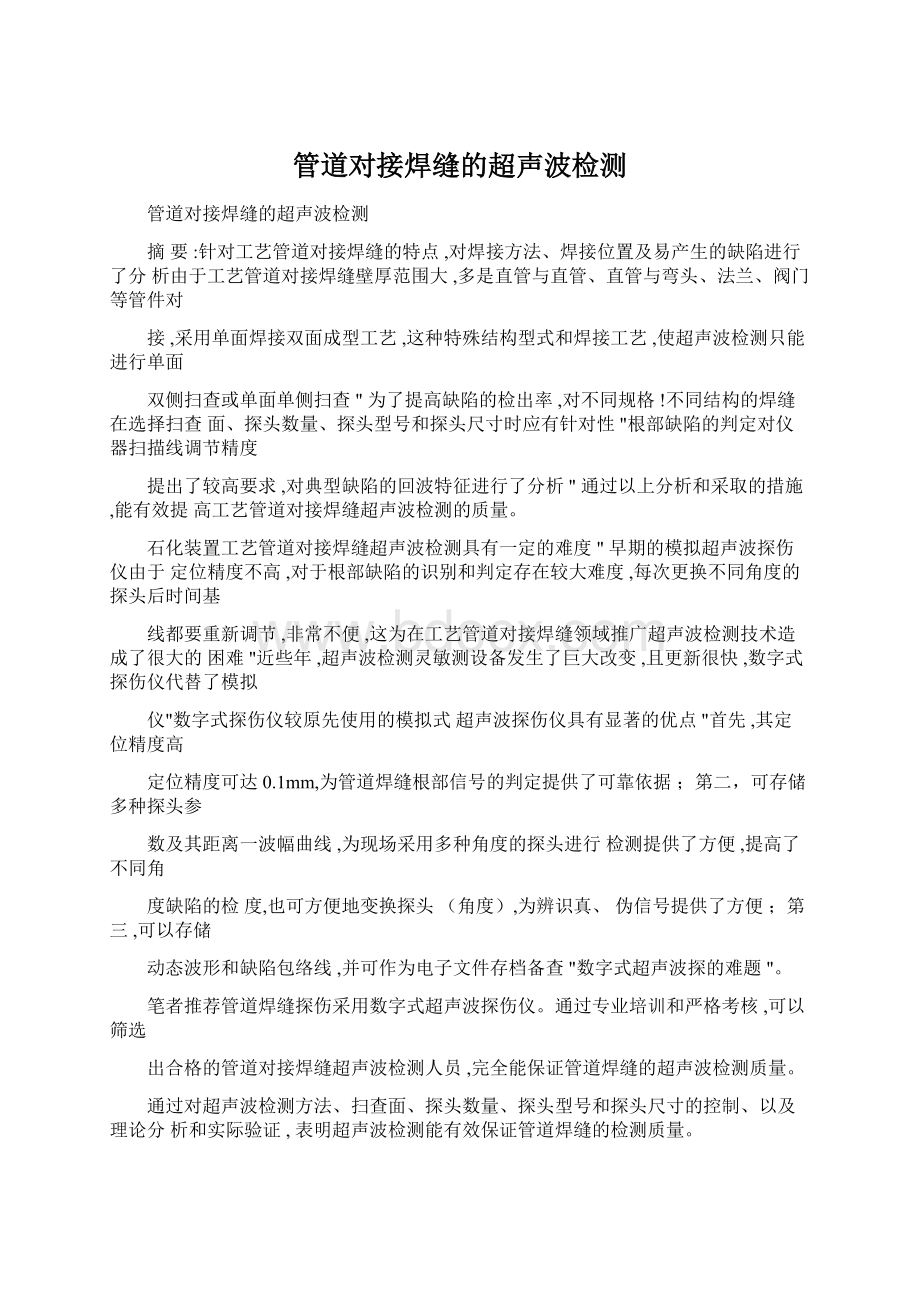
管道对接焊缝的超声波检测
管道对接焊缝的超声波检测
摘要:
针对工艺管道对接焊缝的特点,对焊接方法、焊接位置及易产生的缺陷进行了分析由于工艺管道对接焊缝壁厚范围大,多是直管与直管、直管与弯头、法兰、阀门等管件对
接,采用单面焊接双面成型工艺,这种特殊结构型式和焊接工艺,使超声波检测只能进行单面
双侧扫查或单面单侧扫查"为了提高缺陷的检出率,对不同规格!
不同结构的焊缝在选择扫查面、探头数量、探头型号和探头尺寸时应有针对性"根部缺陷的判定对仪器扫描线调节精度
提出了较高要求,对典型缺陷的回波特征进行了分析"通过以上分析和采取的措施,能有效提高工艺管道对接焊缝超声波检测的质量。
石化装置工艺管道对接焊缝超声波检测具有一定的难度"早期的模拟超声波探伤仪由于定位精度不高,对于根部缺陷的识别和判定存在较大难度,每次更换不同角度的探头后时间基
线都要重新调节,非常不便,这为在工艺管道对接焊缝领域推广超声波检测技术造成了很大的困难"近些年,超声波检测灵敏测设备发生了巨大改变,且更新很快,数字式探伤仪代替了模拟
仪"数字式探伤仪较原先使用的模拟式超声波探伤仪具有显著的优点"首先,其定位精度高
定位精度可达0.1mm,为管道焊缝根部信号的判定提供了可靠依据;第二,可存储多种探头参
数及其距离一波幅曲线,为现场采用多种角度的探头进行检测提供了方便,提高了不同角
度缺陷的检度,也可方便地变换探头(角度),为辨识真、伪信号提供了方便;第三,可以存储
动态波形和缺陷包络线,并可作为电子文件存档备查"数字式超声波探的难题"。
笔者推荐管道焊缝探伤采用数字式超声波探伤仪。
通过专业培训和严格考核,可以筛选
出合格的管道对接焊缝超声波检测人员,完全能保证管道焊缝的超声波检测质量。
通过对超声波检测方法、扫查面、探头数量、探头型号和探头尺寸的控制、以及理论分析和实际验证,表明超声波检测能有效保证管道焊缝的检测质量。
超声波检测操作灵活方便,对厚壁管道检测灵敏度和检测效率均高于射线检测,成本低于射线检测,且对人体无害,是一种科学!
环保的检测方法。
1管道对接焊缝与容器对接焊缝的不同点
管道对接焊缝较容器对接焊缝从焊接工艺、结构型式!
主要缺陷产生的部位、缺陷信号
判别、探头扫查面、探头折射角度的选择以及祸合面曲率等都有较大区别"因此从事管道对
接焊缝超声波检测的人员必须对比有一定的了解"表1是管道对接焊缝与容器对接焊缝超声波检测不同点的比较。
頊和
内雅
黠器就楼焊St
1
wftr艺亲怦
一股为収血胖捲"H欢为自型辉'卑间内FL欖址
2
般艮禮査衬卄衷面吕風检賣.
儀可对專囲査打内鏑表蔺H1«检査*
5
缺陌产蛍的主聲詳位
最眈王菱产也电蝉魅的粮牌{衣悍逸,未堆合,内凹“曲海JSH,吹迫.气扎、壽瓠磁做
块陆圭要产住在如址内部€性札,夹苦.未熔音、林誓〉
4
蜡离谀陪号的判抵
帼器缺陥回迪4月內盘面回谀扣瀝常,不賜刘期区分
乂阳冋泣与却燧覆面回浊位■穷姐不同品于区
井判断
5
1
探罢袒誉fti
•只住莅背西外农除扫査匸
*克背导良青时按畀鑒■巧以甕库鑒两轄扫春
从蓝怦#»扫咼
可以从眸壽内外去面坤蛭网则和査
€
K醐曲曲帝耳肅爵榄矢
褂测血味率才能与工井
小"一魁接近千板-用合駁先恥
7
时18每站宴琅
-对十號希的详址,■煤!
《氏具有粧曲沿和丸KflL埴尢一盛養的列査it"
+血单訓打竟的焊n蔓血赭2秤
不冈葡度的撵盂避廿和査
*对]轮阳陆弊集毒我變论K值不Ijil大■杏
ISili収轉进帝打畫
2焊接工艺及缺陷分析
管道对接焊缝的超声波检测有两个重要环节,一是如何能保证不漏检缺陷,二是如何能正
确识别和判定缺陷”以下对管道的接头型式、焊接方法、焊接位置及易产生的缺陷进行了分析,为设计检测工提高缺陷的检出率和信号判定提供参考。
2.1结构型式与扫查面
石化装置工艺管道对接焊缝一般可分为3种型式:
直管与直管对接、直管与管件对接、
管件与管件对接。
(1)直管与直管对接焊缝探头可以在焊缝两侧进行扫查。
⑵直管与管件对接焊缝由于管件侧表面为不规则曲面(如弯头、法兰、阀门或三通等),探头
不能良好藕合,因此,只能从直管一侧进行扫查,为了提高缺陷检出率,应选择2种不同角度
的探头进行扫查。
(3)管件与管件对接焊缝由于焊缝两侧均为不规则曲面(如弯头!
法兰、阀门或三通等),探头
不能良好祸合,因此,这类焊缝不能进行正常的超声波检测"如客户有措施将焊缝余高磨平(与
母材平齐),则可将探头通过磨平的焊缝进行检测”将焊缝打磨至与母材平齐是一件很困难的事,一般不这样做。
2.2焊接位置
了解焊接位置有助于缺陷性质的分析判断。
管道对接焊缝的焊接位置分为水平转动、水平固定、垂直固定和45度斜固定。
(1)水平转动口焊接时,焊接位置总是处于时钟11点或1点附近的位置,焊接操作最易控制,最
不易产生焊接缺陷(图1)"
(2)水平固定口焊接时,上半部分处于平焊位置,下半部分处于仰焊位置,两侧处于立焊位置(图2)。
图1水平转动口
焊接示恋團
(3)垂直固定口焊接时,其位置为横焊,焊接位置示意见图3。
(4)45度斜固定口焊接时,各部分在水平固定的基础上又增加了倾斜角度,加大了焊接难度
(图4)。
图3垂直呦定图145°颂斜固定
焊接示意图
焊接示愿图
2.3各焊接位置易产生的缺陷类型
(1)焊接程序目前石化装置管道对接焊缝均采用氢弧焊打底,焊工在打底结束前留一
小段用作检查孔,用手电筒观察根部打底情况,若有不良现象则立即将不良部位用磨光机去除重焊,最终检查良好后将根部最后一小段焊好”氢弧焊打底结束后,对于较厚的焊缝一般采用
手工电弧焊或埋弧自动焊填充盖面。
(2)平焊位置铁水熔化后在重力的作用下会向下淌,因此平焊位置焊接时要控制电流不能
过大,焊接电流和焊接速度要适当,否则易形成焊瘤和烧穿。
焊条接头和焊瘤部位易产生气孔。
(3)立焊位置在立焊位置因铁水下淌导致焊缝波纹粗糙及内外表面焊缝成型不良,也容易
产生未焊透、未熔合!
焊瘤及咬边"因此要控制焊接电流不能过大,焊接速度不能过快。
(4)仰焊位置仰焊位置易产生内凹、未焊透、未熔合及焊瘤(余高过高),仰焊位置电流过大
易产生内凹!
烧穿和焊瘤,电流过小易产生未焊透和未熔合,因此仰焊部位的焊接难度最大”焊
工常采用灭弧焊法进行焊接,即引弧!
将焊条熔化一点立即断弧、待片刻熔池凝固、再继续
引弧熔化一点焊条立即断弧…这样循环持续,直至铁水成型达到可控为止,在烧第二层焊缝时电流也不能过大,否则将第一层铁水熔化下坠形成内凹,电流越大形成的内凹越深。
(5)横焊位置管子垂直固定,焊工围绕焊缝进行横向焊接。
横焊位置焊接时,铁水受重力作用,上部易出现咬边,坡口易产生未熔合,焊接每层之间如果清理不好易产生夹渣。
焊缝表
面横排波纹控制不好会比较粗糙。
3探头的选择
探头选择时要考虑的因素有:
(1)检测厚度检测较薄焊缝应选择大K值、短前沿探头,一次波尽可能扫查更多的焊缝截
面;对于大厚度焊缝应选择晶片尺寸较大、K值合适、具有足够灵敏度的探头。
根据实际工作经验,笔者推荐壁厚不小于7mm的焊缝宜采用单斜探头进行检测。
壁厚<
7mm的焊缝检测时杂波干扰严重,目前多选用聚焦探头或双晶探头。
但聚焦探头和双晶探头
一般宽度较大,与小径管藕合时要进行修磨"由于聚焦探头和双晶探头都是在焦点附近灵敏度最高,探测范围受到一定影响,工艺管道壁厚<7mm的管道管径一般均较小,因此,对壁厚<7mm的管道焊缝不推荐采用超声波检测法进行检测。
(2)
检测面曲率半径R较小的管道,要选择接触面小的探头,以保证良好藕合;直径较大的管道可以选择尺寸较大的探头,以提高检测效率。
探头与工件接触面尺寸W应满足下式:
目前市场销售的晶片尺寸为6mmx6mm的短前沿小晶片探头,其探头宽度一般为
12mm。
由式(I)计算可得管道直径应>72mm。
为提高藕合效果,笔者推荐采用探头宽度为12mm的小晶片短前沿探头进行检测时,管道直径下限为100mm。
(3)扫查面直管与直管对接,探头在焊缝两侧扫查时,可以选择1种K值的探头;直管与管件对接,探头只能在焊缝一侧进行扫查时,应选择2种折射角相差不少于10度的探头进行扫查其中较小K值的探头,一次波扫查范围不少于焊缝截面的1/4
(4)探头频率管道探伤宜选择较高频率的探头,以提高指向性和定位精度。
推荐采用频率为5MHz的探头,对于较厚管道(厚度)不小于40mm)可以选择2.5MHz的探头。
对于根部可疑信号,尽可能选择小K值探头复验”经验表明,小K值探头定位精度高,误差小。
综合上述条件,不同厚度的管道推荐选择的探头角度和前沿距离见表2,不同曲率的管道
推荐选择的探头尺寸见表3。
表2不同厚度的管道推荐选择的探头角度和前沿距离
7~.'mni
冕用埶亍弭探头芷炸尊两劇进行扫杳时探头的K值
釆用海冲Kffi探头隹担缝的一割进行扫査时撵头的K值
探头
丽沿
/mni
探头】
探头2
M07S
1(1
XO
久070
2+0
L52.AZt>
L5
2.5
C10
£075
i.n
2.0
—-
L0
2.0
表3不同曲率的管道推荐选择的探头尺寸
管道外轻,mm
W.nrni
£1瓷或纔牌至与工件曲面匹IK
159C/^<21S
^>325
C20
4检测灵敏度分析
检测标准执行JB/T4730.3—2005,外径不小于159mm的管子按标准中表19调节检测灵敏度;外径<159mm的管子按标准中表30调节灵敏度。
管道对接焊缝中存在的主要缺陷有未焊透、未熔合、内凹、焊瘤、错口、气孔、夹渣和
裂纹等。
根部未焊透、未熔合和裂纹属面状缺陷,超声波对其非常敏感。
试验表明,深度为
0.5mm切槽的反射波幅均较高,回波均在判废线上下”因探头的角度不同,回波幅度有所不同,探头折射角度越小,回波幅度越高,因此根部未焊透!
未熔合和根部纵向裂纹类面状缺陷一般不会漏检。
5检测工艺卡编制举例
工艺卡的编制原则:
工艺卡要能够真正指导检测人员能够看懂,按工艺卡要求可以方便实
施"编制检测工艺卡时需重点关注的内容如下:
(1)探头数量和参数能够满足标准和实际检测的需要,能否最大限度地检出危害性缺陷。
⑵检测面要明确”
(3)试块和检测灵敏度符合标准要求。
下文对管道焊缝超声波检测工艺卡的编制进行举例。
已知某石化装置检修改造工程中有一条规格为219*20mm的碳钢工艺管道,坡口型式为
V型,氩弧焊打底,手工电焊填充、盖面,检测比例为100%。
按按JB/T4730.3—2005标
准进行检测,合格级别为一级。
检测工艺卡编制结果见表4。
表4中未对检测技术等级提出要求,这是因为JB/T4730.3
一2005的检测技术等级不适用于直管与管件对接的焊缝检测。
*1
工樟官字
XXXX
X«Hr*4
细h™
曦常
揄射N袪
.219bhi.廉加mm
拒血man
IWH
g
GTA出十SMW
■□■監
V
IlH
TXTW
迎•廉睥
UT舶
瑟IK
4rIH
it呼齡褂
整*|貝■金
ttfllfVl
埠斤
aanl
”nr
1
MAK
•头ME
Mbmm
--
訂|=丄enfn.
ZP9:
':
SK2.G
螺WAmrjTE
3140on
槪悔斥■
M它鼻农
UJ««!
»««VmAHI<41VRBt94MMM9产・耳輒能电加•執慎草的鼻寡暉・,有科FM$«nKM>
(iiKi..-Rift-2.:
的弭冲挥艮更h厲時L
1i)JlWitT^tf;5Onm.Si
I*'晉确曉擱机•負匕板丼買血世叭事代迓计校醤.
:
訂r贅it*施**膻锹#1对妊旅幣片,庄暨昌勺tt^ititfiJi?
1-bt-
H割tXXXXxxxx
•彎JI日軒札權罕丹
6典型缺陷信号的识别
超声波检测前,应对受检焊缝两侧的壁厚靠近焊缝部位用直探头进行测厚,以确认其真实
厚度。
如果测得结果小于标称值的负偏差,则应立即报告委托人;如果测得结果大于或等于标
称值,则认为是可以接受的”所测厚度值应在记录中注明,该值即作为判断回波信号的基准。
对回波信号性质的判定要结合材质、坡口和结构型式、焊接工艺和焊接位置、回波位置
(包括水平位置和深度位置)、指示长度和取向、最大回波高度、静态和动态波形等进行综合分析"对于可疑信号可更换另一种角度的探头进行验证,以助于缺陷定性和伪信号的识别。
管道焊缝正确判别根部信号的关键是时基线标定要准确,要求深度定位误差不超过
0.5mm,否则,根部缺陷信号判断会产生较大误差。
时基线标定完毕后,必须用与所检工件厚度
等深或相近的孔进行校验,该孔的最高回波指示值应与深度标称值相当或略小0.1—
0.5mm(半孔径),则时基线标定是准确的。
时基线的调节还应考虑试块声速与工件声速的差异,当工件厚度较大时,声速的差别会严
重影响定位精度和根部缺陷的判定"如常温测得材质20号钢的横波声速3230m/s,P91的横波声速3301m/s时20号钢的纵波声速5934m/S,P91纵波声速5983m/s。
用KZ探头和20号钢标准试块标定的时基线探测P91钢工件时,由于P91钢的声速较快,其折射角增大,K值变为K
2.25,探测50mm厚P91工件其声程增加至123.297mm,较20号钢的声程111.67mm增加11.62mm,从时基线上观察,与厚度50mm的P91钢工件的实际厚度为54mm。
显然,由此会造成严重的误判,易将焊瘤判为未焊透缺陷。
关于最高峰的确认,许多探伤人员对波峰最高点的判断存在误区,探头总是不敢前后移动
发现了较高的回波就认为是最高波,探头前后移动时最高波的位置又发生变化,从而影响对信
号的正确判断。
在扫查和精探伤时,探头应前后移动,当发现回波信号时,应增加祸合剂并将探头前后往返缓慢移动3一5次,观察动态波形,找出回波最高点的位置,将探头移至出现回波最高点的位置,轻微前后移动或转动探头,找出最高波,用闸门选择该回波,读出回波位置,将探头移至出现回波最高点的位置,轻微前后移动或转动探头,找出最高波,用闸门选择该回波,读出回波位置。
下面对管道焊缝检测中几种典型缺陷信号进行分析和介绍。
6.1质量良好的焊缝
质量良好的焊缝内部没有缺陷,焊缝内外表面成型饱满且均匀过渡,焊缝区段没有缺陷
回波,焊缝根部或焊缝表面不产生或产生较低的回波(视探头角度而异)。
由于根部有一定的凸
出,出现反射波时,反射波峰值的位置略迟后于工件厚度,两侧扫查结果相近。
典型波形见图5。
图5符合査求的焊缝粮部氏时回滥
6.2根部未焊透
一般有一侧可以同时看到底面反射波”而未焊透两
根部未焊透与焊接工艺密切相关”目前中石化范围内的管道工程均要求氨弧焊打底,有
效地减少了未焊透缺陷的产生,同时提高了根部成型质量。
现在发现的未焊透多是由于焊工操作的偶然性所致,未焊透的长度一般不超过20mm,自身高度一般不超过2mm,也可能一侧
钝边略深,另一侧钝边非常浅”从焊缝两侧扫查时,反射波幅有可能相差较大。
在非缺陷侧探测时,信号可能很弱,甚至无信号,改用较小角度探头检测时缺陷信号则易于发现。
因此,从单面单
侧扫查时,应选择2种不同角度的探头进行检测。
如有可能,选择KI斜探头对根部缺
陷进行检测,具有良好的检测灵敏度。
反射波与底波位置的间距与未焊透的深度成正比,未焊透深度大则回波幅度高,反之则回
波幅度低。
探头作摆动或转动时,波形消失很快。
判断是否未焊透的关键是看回波的位置,未焊透的反射波最高峰在底波略前一些的位置
没有底波出现”未焊透回波位置见图6。
深度较大的未焊透一次波和二次波均可以发现,有时
二次波的当量幅值还会高于一次波的当量幅值。
厲】閑翼純边较-Sc
(b>却侧純边不均匀
图G槪部未焊垮
6.3未熔合
管道焊缝的未熔合多为根部钝边未熔合,少部分为坡口未熔合”钝边未熔合在焊缝的根
部,坡口未熔合在焊缝坡口熔合线部位”未熔合反射波的特征是:
在焊缝两侧探测时,反射波幅
不同,大部分未熔合只能从一侧探到”较大尺寸的未熔合,探头平移时波形较稳定。
(I)根部未熔合根部未熔合反射波出现时,一般有一侧可以同时看到底面反射波。
而未焊透两侧均没有底面反射波。
判断是否未熔合,要结合回波深度、水平距离和是否有底波来综合判断。
根部未熔合回波示意见图7。
曲7根部卡烙合冋波小恿虧
(2)坡口未熔合坡口未熔合多在厚壁焊缝和自动焊焊接时产生,具有一定的长度,成连续状
或断续状。
其动态波形为探头平行于焊缝移动时,特征包络线比较平稳(连续状)或有缓慢的起伏(断续);探头前后移动时,特征包络线与气孔差不多;探头作摆动或转动时,波形消失很快其声程特点为如图8,从缺陷侧探测,二次波信号强,一次波信号弱甚至没有;从非缺陷侧探测
情况相反。
£1LKL.
(bjI处{c)口处(d)U1处制找不同探董悅世处的城口未熔合何波
6.4根部内凹
内凹一般产生在固定焊口的仰焊部位。
其在荧光屏上的波形为深度较大且边缘较陡峭的内凹其危害性与回波幅度均与未焊透相似,易于检测,应按未焊透处理。
深度较浅、且平缓过渡的内凹一般回波
较低或不易发现,这类内凹对焊缝强度影响不大。
其动态波形为特征包络线的变化比较平缓无明显的锯齿形,有内凹缺陷时无底波出现。
其声程特点为从两侧探测,声程反射点相隔一定
距离,其距离约等于对口间隙加2一4mm。
6.5裂纹
裂纹多产生于焊缝根部或外表面,一般是由于焊接材料用错!
强行组对或焊接工艺不当所致。
一般裂纹的回波高度较大、波幅宽、有多峰出现。
探头平移时反射波连续出现,波幅有
变动,探头转动时,
波峰有上下错动现象。
表面和近表面微小裂纹反射面小、反射波与表面杂波混杂在一起不易区分,横向裂纹垂直于焊缝,当管径较小时,探头不能平行于焊缝扫查,因此标准要求增加表面检测来补充超声检
测方法的不足。
6.6根部错边
直管、弯头、三通以及大小头等,由于加工精度的原因,其对接端口往往存在一定程度的
椭圆或不等壁厚,组对时局部可能会出现错边,轻微的错边在焊接时易焊至均匀过渡,严重的
错边则会在内表面
形成焊缝错边。
这种错边从一侧探测时,信号较强,而从另一侧探测时,没有信号波,如图9所
示。
等壁厚错边一般从外表可以看出”不等壁厚错边可以在检测前测厚时发现”要注意错边与单侧未焊透的区别。
6.7根部焊瘤
根部焊瘤表面比较光滑,从焊缝两侧扫查,其反射回波相差不大,且均在底波位置之后出现,焊瘤部位一般只有焊瘤反射波,没有底波”焊瘤回波示意见图10(a)所示。
焊瘤回波的判断,焊瘤的反射回波一般都很强,且最高峰在根部之后2一3mm左右的位置,大焊瘤也可能到达根部之后5一6mm的位置。
操作时,前后移动探头,从根部之前就开始
有回波;随着探头缓慢后移,波峰逐渐增高,屏幕指示深度位置增加,超过根部位置2一3mm后出现最高峰;之后,再后移探头前后移动时荧光探头,波峰开始下降,在最高峰之前没有峰值出现,这就是焊瘤回波的典型特征"焊瘤回波包络示意见图10(b)所示。
I
(b)那緇回波但貉示惹图阳IU悼嘩间被示盘国
6.8气孔和点状夹渣等点状缺陷
气孔与夹渣均在焊缝内部,一次波检测时,其反射波位于始波与底波之间,二次波检测时
其反射波位于底波与上表面反射波之间。
(1)单个气孔与点状夹渣回波特征其回波在荧光屏上的波形尖锐、陡峭、清晰、波根较
窄,如图11所示。
(2)密集气孔回波特征密集气孔回波在荧光屏上同时出现数个波,往往有一个较高的波,
旁边簇拥着若干个小波,波形清晰(图12)。
其动态波形为不管探头作怎样的移动,波形总是此
起彼伏。
(A)X光照片回般田形
图12应集气孔回渡
(3)条状夹渣回波牲探头前后移动时荧光屏上的波形与点状夹渣类似,只是左右移动时缺陷
有一定的长度"其动态波形为探头平行于缺陷长度方向移动时,在缺陷长度范围内有缺陷波;
探头作摆动时,波形消失很快。
6.9两种典型的伪缺陷信号
6.9.1扩散声束在根部的反射伪缺陷回波
在实际工作中经常发现在接近下表面之前有强烈的反射波”从反射波出现的位置分析,反射
点应在焊缝内,但长度较长,有时全焊缝连
续,如图13所示。
但是,用射线复测时焊缝质量良好。
产生此伪缺陷回波的原因为:
探头发出波束是扩散的(如图14所示),下扩散波较中心主波束的折射角略小,即K值略小,当探头移动时,下扩散声束在C点与下表面形成接近垂直的角度,反射波强烈”从示波屏上观察,在处有反射波显示,反射点水平位置靠近焊缝对面的熔合线,深度小于工件厚度。
从图14可以看出,由下扩散声束在根部C点产生的反射波相当于主声束在焊缝中B-点
B'产生的反射波,从示波屏上显示的位置如图13所示。
伪信号排除方法:
当出现上述信号时,应选择较高频率!
小角度探头进行复测以排除此类伪信号6.9.2山形伪缺回波
焊缝超声检测时,经常发现在底波之后上表面回波之前出现两个较高回波,如图15所示的山
形回波。
用X射线复验,焊缝质量良好。
山形回波形成原理为:
(1从探头进入工件的横波在焊缝根部(由于根部成型的原因)产生反射回波T1同时产生反
射纵波Bl和反射横波Bs。
(2根部反射回波T1先到达探头并被接收,T1在一次底波(或略迟后一点)的位置。
(3根部反射纵波Bl到达焊缝上表面后又反射回来,在C点又变成横波返回至探头,被探头接收,由于纵波较横波声速快,因此Bl较T1迟到的时间在示波屏上约为tL的时间(大约在距一次底波之后,相当于一次波与二次波时间1/3的位置);tL的计算如下:
tL=T/CL
(2)
式中T----工件厚度;
Cl---纵波声速;
(4根部反射横波Bs到达焊缝上表面后又反射回来,经C点返回至探头,被探头接收,Bs较T1迟到的时间在示波屏上约为ts(大约在距一次波之后,约相当于一次波与二次波时间2/3的位置)。
ts的计算如下:
ts=T/Cs(3)
式中T----工件厚度;
Cs---横波声速;
辨别山形回波的方法为:
用手指沾祸合剂轻轻拍打对应的焊缝表面,如果山形回波在手指接
触焊缝时降低,手指离开焊缝时升高,且跳动明显,则可判定该山形回波为伪信号。
沾有藕合剂的手指在接触焊缝表面时吸收了部分声能,从而使反射声波降低。
从上述管道焊缝缺陷定性的叙述中可以看出,单凭缺陷的某一种特征来判断其性质是
比较困难的,必须对各种特征