集成电路工艺复习资料.docx
《集成电路工艺复习资料.docx》由会员分享,可在线阅读,更多相关《集成电路工艺复习资料.docx(10页珍藏版)》请在冰豆网上搜索。
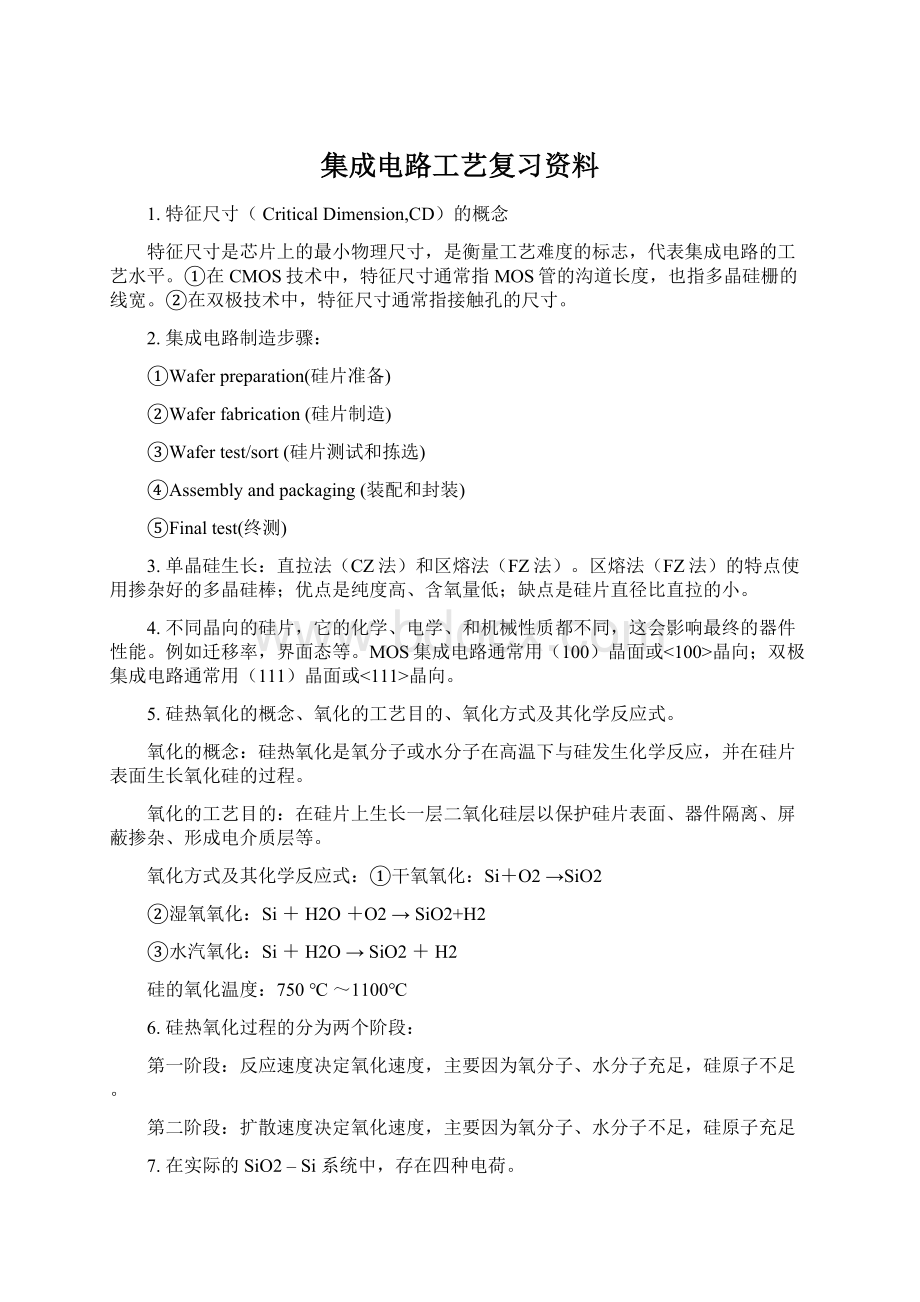
集成电路工艺复习资料
1.特征尺寸(CriticalDimension,CD)的概念
特征尺寸是芯片上的最小物理尺寸,是衡量工艺难度的标志,代表集成电路的工艺水平。
①在CMOS技术中,特征尺寸通常指MOS管的沟道长度,也指多晶硅栅的线宽。
②在双极技术中,特征尺寸通常指接触孔的尺寸。
2.集成电路制造步骤:
①Waferpreparation(硅片准备)
②Waferfabrication(硅片制造)
③Wafertest/sort(硅片测试和拣选)
④Assemblyandpackaging(装配和封装)
⑤Finaltest(终测)
3.单晶硅生长:
直拉法(CZ法)和区熔法(FZ法)。
区熔法(FZ法)的特点使用掺杂好的多晶硅棒;优点是纯度高、含氧量低;缺点是硅片直径比直拉的小。
4.不同晶向的硅片,它的化学、电学、和机械性质都不同,这会影响最终的器件性能。
例如迁移率,界面态等。
MOS集成电路通常用(100)晶面或<100>晶向;双极集成电路通常用(111)晶面或<111>晶向。
5.硅热氧化的概念、氧化的工艺目的、氧化方式及其化学反应式。
氧化的概念:
硅热氧化是氧分子或水分子在高温下与硅发生化学反应,并在硅片表面生长氧化硅的过程。
氧化的工艺目的:
在硅片上生长一层二氧化硅层以保护硅片表面、器件隔离、屏蔽掺杂、形成电介质层等。
氧化方式及其化学反应式:
①干氧氧化:
Si+O2→SiO2
②湿氧氧化:
Si+H2O+O2→SiO2+H2
③水汽氧化:
Si+H2O→SiO2+H2
硅的氧化温度:
750℃~1100℃
6.硅热氧化过程的分为两个阶段:
第一阶段:
反应速度决定氧化速度,主要因为氧分子、水分子充足,硅原子不足。
第二阶段:
扩散速度决定氧化速度,主要因为氧分子、水分子不足,硅原子充足
7.在实际的SiO2–Si系统中,存在四种电荷。
①.可动电荷:
指Na+、K+离子,来源于工艺中的化学试剂、器皿和各种沾污等。
②.固定电荷:
指位于SiO2–Si界面2nm以内的过剩硅离子,可采用掺氯氧化降低。
③.界面态:
指界面陷阱电荷(缺陷、悬挂键),可以采用氢气退火降低。
④.陷阱电荷:
由辐射产生。
8.(硅热氧化)掺氯氧化工艺
在氧化工艺中,通常在氧化系统中通入少量的HCl气体(浓度在3%以下)以改善SiO2–Si的界面特性。
其优点:
①.氯离子进入SiO2-Si界面与正电荷中和以减少界面处的电荷积累。
②.氧化前通入氯气处理氧化系统以减少可动离子沾污。
9.SiO2-Si界面的杂质分凝(DopantSegregation):
高温过程中,杂质在两种材料中重新分布,氧化硅吸引受主杂质(B)、排斥施主杂质(P、As)。
10.SiO2在集成电路中的用途
①栅氧层:
做MOS结构的电介质层(热生长)
②场氧层:
限制带电载流子的场区隔离(热生长或沉积)
③保护层:
保护器件以免划伤和离子沾污(热生长)
④注入阻挡层:
局部离子注入掺杂时,阻挡注入掺杂(热生长)
⑤垫氧层:
减小氮化硅与硅之间应力(热生长)
⑥注入缓冲层:
减小离子注入损伤及沟道效应(热生长)
⑦层间介质:
用于导电金属之间的绝缘(沉积)
11.硅热氧化工艺中影响二氧化硅生长的因素
①氧化温度;
②氧化时间;
③掺杂效应:
重掺杂的硅要比轻掺杂的氧化速率快
④硅片晶向:
<111>硅单晶的氧化速率比<100>稍快
⑤反应室的压力:
压力越高氧化速率越快
⑥氧化方式:
湿氧氧化比干氧氧化速度快
12.热生长氧化层与沉积氧化层的区别
①结构及质量:
热生长的比沉积的结构致密,质量好。
②成膜温度:
热生长的比沉积的温度高。
可在400℃获得沉积氧化层,在第一层金属布线形成完进行,做为金属之间的层间介质和顶层钝化层。
③硅消耗:
热生长的消耗硅,沉积的不消耗硅。
13.杂质在硅中的扩散机制
①间隙式扩散;②替位式扩散。
14.扩散杂质的余误差函数分布特点(恒定表面源扩散属于此分布)
①杂质表面浓度由该种杂质在扩散温度下的固溶度所决定。
当扩散温度不变时,表面杂质浓度维持不变;
②扩散时间越长,扩散温度越高,则扩散进入硅片内的杂质总量就越多;
③扩散时间越长,扩散温度越高,杂质扩散得越深。
15.扩散杂质的高斯分布特点(有限源扩散属于此分布)
①在整个扩散过程中,杂质总量保持不变;
②扩散时间越长,扩散温度越高,则杂质扩散得越深,表面浓度越低;
③表面杂质浓度可控。
16.结深的定义
杂质扩散浓度分布曲线与衬底掺杂浓度曲线交点的位置称为结深。
17.离子注入的概念:
离子注入是在高真空的复杂系统中,产生电离杂质并形成高能量的离子束,入射到硅片靶中进行掺杂的过程。
18.离子注入工艺相对于热扩散工艺的优缺点:
优点:
①精确地控制掺杂浓度和掺杂深度;②可以获得任意的杂质浓度分布;③杂质浓度均匀性、重复性好;④掺杂温度低;⑤沾污少;⑥无固溶度极限。
缺点:
①高能杂质离子轰击硅原子将产生晶格损伤;②注入设备复杂昂贵。
19.离子注入效应
沟道效应:
当注入离子未与硅原子碰撞减速,而是穿透了晶格间隙时就发生了沟道效应。
控制沟道效应的方法:
①倾斜硅片;②缓冲氧化层;③硅预非晶化(低能量(1KEV)浅注入应用非常有效);④使用质量较大的原子。
注入损伤:
高能杂质离子轰击硅原子将产生晶格损伤。
消除晶格损伤的方法:
①注入缓冲层;②离子注入退火工艺。
20.离子注入退火
工艺目的:
消除晶格损伤,并且使注入的杂质转入替位位置从而实现电激活。
①高温热退火
通常的退火温度:
>950℃,时间:
30分钟左右
缺点:
高温会导致杂质的再分布。
②快速热退火
采用RTP,在较短的时间(10-3~10-2秒)内完成退火。
优点:
杂质浓度分布基本不发生变化
21.在先进的CMOS工艺中,离子注入的应用
①深埋层注入;②倒掺杂阱注入;③穿通阻挡层注入;④阈值电压调整注入;⑤轻掺杂漏区(LDD)注入;⑥源漏注入;⑦多晶硅栅掺杂注入;⑧沟槽电容器注入;⑨超浅结注入;⑩绝缘体上的硅(SOI)中的氧注入。
22.部分离子注入工艺的作用
①深埋层注入:
高能(大于200KEV)离子注入,深埋层的作用:
减小衬底横向寄生电阻,控制CMOS的闩锁效应。
②倒掺杂阱注入:
高能量离子注入使阱中较深处杂质浓度较大,倒掺杂阱改进CMOS器件的抗闩锁和穿通能力。
③穿通阻挡层注入:
作用:
防止亚微米及以下的短沟道器件源漏穿通,保证源漏耐压。
④轻掺杂漏区(LDD)注入:
减小最大电场,增强抗击穿和热载流子能力。
⑤超浅结注入:
大束流低能注入。
作用:
抑制短沟道效应
23.光刻的概念
光刻是把掩膜版上的电路图形精确地转移到硅片表面光刻胶膜上的过程。
光刻是集成电路制造的关键工艺。
24.光刻工艺的8个基本步骤:
①气相成底膜;②旋转涂胶;③软烘;④对准和曝光;⑤曝光后烘培(PEB);⑥显影;⑦坚膜烘培;⑧显影检查。
25.什么是光刻胶、光刻胶的用途、光刻对光刻胶的要求
光刻胶是一种有机化合物,它受紫外线曝光后在显影液中的溶解度发生显着变化,而未曝光的部分在显影液中几乎不溶解。
光刻胶的用途:
①做硅片上的图形模版(从掩膜版转移到硅片上的图形);②在后续工艺中,保护下面的材料(例如刻蚀或离子注入)。
光刻对光刻胶的要求:
①分辨率高;②对比度好;③敏感度好;④粘滞性好⑤粘附性好;⑥抗蚀性好;⑦颗粒少。
26.正胶和负胶区别
正胶:
曝光的部分易溶解,占主导地位;负胶:
曝光的部分不易溶解。
负胶的粘附性和抗刻蚀性能好,但分辨率低。
27.数值孔径(NA)
28.分辨率(R)
分辨率是将硅片上两个相邻的关键尺寸图形区分开的能力。
分辨率是光刻中一个重要的性能指标。
k为工艺因子,范围是~;λ为光源的波长;NA为曝光系统的数值孔径。
提高分辨率的方法:
①减小工艺因子k:
先进曝光技术
②减小光源的波长:
汞灯?
准分子激光(?
等离子体)
③增大介质折射率:
浸入式曝光
④增大θm:
增大透镜半径、减小焦距
29.焦深(DOF)
焦深是焦点上下的一个范围,在这个范围内图像连续保持清晰。
焦深类似照相的景深,集成电路光刻中的景深很小,一般在μm左右。
焦深限制光刻胶厚度,并要求表面平坦化
30.刻蚀的概念、工艺目的、分类、应用
概念:
用化学或物理的方法,有选择地去除硅片表面层材料的过程称为刻蚀。
工艺目的:
把光刻胶图形精确地转移到硅片上,最后达到复制掩膜版图形的目的。
刻蚀是在硅片上复制图形的最后图形转移工艺,是集成电路制造的重要工艺之一。
刻蚀的分类:
①按工艺目的分类:
有图形刻蚀、无图形刻蚀。
无图形刻蚀:
材料去除和回蚀。
②按工艺手段分类:
干法刻蚀和湿法刻蚀。
③按刻蚀材料分类:
金属刻蚀、介质刻蚀、硅刻蚀。
应用:
在硅片上制作不同的特征图形,包括选择性氧化的氮化硅掩蔽层、沟槽隔离和硅槽电容的沟槽、多晶硅栅、金属互联线、接触孔和通孔。
31.干法刻蚀与湿法刻蚀
把硅片置于气态产生的等离子体,等离子体中的带正电离子物理轰击硅片表面,等离子体中的反应粒子与硅片表面发生化学反应,从而去除暴露的表面材料。
干法刻蚀用物理和化学方法,可实现各向异性刻蚀,能实现图形的精确转移。
干法刻蚀是集成电路刻蚀工艺的主流技术,广泛用于有图形刻蚀、回蚀和部分材料去除工艺。
把硅片置于液体化学试剂,化学腐蚀液与硅片表面发生化学反应,从而去除暴露的表面材料。
湿法刻蚀用化学方法,一般是各向同性刻蚀,不能实现图形的精确转移。
湿法刻蚀基本只用于部分材料去除工艺。
32.干法刻蚀的优缺点(与湿法刻蚀比)
优点:
①刻蚀剖面各向异性,非常好的侧壁剖面控制;②好的CD控制;③最小的光刻胶脱落或粘附问题;④好的片内、片间、批间的刻蚀均匀性;⑤化学品使用费用低。
(为什么现代集成电路工艺多采用干法刻蚀?
)
缺点:
①对下层材料的刻蚀选择比较差;②等离子体诱导损伤;③设备昂贵。
33.刻蚀参数
①刻蚀速率;②刻蚀偏差;③选择比;④均匀性;⑤刻蚀剖面。
34.ULSI对刻蚀的要求
①对不需要刻蚀的材料(主要是光刻胶和下层材料)的高选择比;②可接受产能的刻蚀速率;③好的侧壁剖面控制;④好的片内均匀性;⑤低的器件损伤;⑥宽的工艺窗口。
35.为什么微米以下工艺的干法刻蚀需要高密度等离子体?
传统的RIE系统等离子体离化率最大%,因而需要较多的气体以产生足够的粒子。
较高的气压使得粒子碰撞频繁,反应粒子很难进入小尺寸高深宽比图形,反应产物也很难排出。
高密度等离子体的离化率达到10%,用于微米以下的工艺。
36.为什么多晶硅的干法刻蚀要采用氯基气体而不是氟基气体?
不用SF6等F基气体是因为Cl基气体刻蚀多晶硅对下层的栅氧化层有较高的选择比。
37.化学气相沉积CVD的概念
(ChemicalVaporDeposition)化学气相沉积是利用电阻加热、等离子体、光辐射等能源使某些气态物质发生化学反应,生成固态物质并沉积在衬底表面形成薄膜的过程。
38.集成电路对薄膜的要求
①好的台阶覆盖能力;②填充高深宽比间隙的能力;③好的厚度均匀性;④高纯度和高密度;⑤受控制的化学剂量;⑥高度的结构完整性和低的应力;⑦好的电学特性;⑧对衬底材料或下层膜有好的粘附性。
39.描述CVD生长的简化过程。
写出影响CVD生长速率的因素
自己整理
影响CVD生长速率的因素:
①质量传输限制(常压CVD);②表面反应限制(低压CVD);③CVD气流动力学;④CVD反应中的压力。
40.异类反应和同类反应
异类反应:
反应发生在硅片表面或非常接近表面。
同类反应:
反应发生在离硅片很远的高空。
必须避免同类反应生成薄膜束状物,同类反应产生的薄膜粘附性差、质量差、均匀性差。
41.常压CVD系统(APCVD)
质量输运限制为主、气流控制要求高。
优点:
沉积速度高。
缺点:
膜致密性差、颗粒多,气体消耗大、硅片不可密集摆放,台阶覆盖差(主要决定于反应气体)。
42.低压CVD系统(LPCVD)
反应速度限制为主、温度控制要求高。
优点:
膜致密、颗粒少,硅片可密集摆放,台阶覆盖较好(主要决定于反应气体)。
缺点:
速度较慢。
43.在APCVDSiO2时掺杂PH3,形成磷硅玻璃(PSG)。
优点:
吸附可动离子电荷改善器件界面,降低玻璃的软化点温度易于平坦化。
缺点:
易吸潮,一般控制P2O5的含量在4%以下。
44.沉积多晶硅采用什么CVD工具?
掺杂的Poly-Si的主要用途。
写出掺杂的Poly-Si做栅电极的6个原因。
沉积多晶硅采用LPCVD。
用途:
①掺杂的Poly-Si在MOS器件中用做栅电极;②掺杂的Poly-Si做多晶电阻及桥联;③PIP电容的上下电极。
掺杂的Poly-Si做栅电极的原因:
①通过掺杂可得到特定的电阻;②与SiO2有优良的界面特性;③和后续高温工艺的兼容性;④比金属电极(如Al)更高的可靠性;⑤在陡峭的结构上沉积的均匀性;⑥实现栅的自对准工艺。
45.蒸发的优缺点
优点:
①成膜速率高(能蒸发5微米厚的铝膜);②金属膜纯度高
缺点:
①台阶覆盖能力差;②不能沉积金属合金
46.溅射的优缺点
优点:
①台阶覆盖能力好;②能沉积金属合金;③能进行原位溅射刻蚀
缺点:
溅射速率低,金属膜含氩
47.电镀的优缺点
优点:
非常好的间隙填充能力,成本低、温度低
缺点:
需要导电种子层,控制复杂
48.高能离子轰击
①离子反射(能量很小);②离子吸附(<10eV),能量转化热能;③离子注入(>10keV),能量改变结构;④溅射(~5keV),溅射原子能量10~50eV。
49.铝互连的优缺点
优点:
①电阻率低;②铝的成本低;③与硅和二氧化硅的粘附性好;④易于沉积成膜(蒸发、溅射);⑤易于刻蚀;⑥抗腐蚀性能好,因为铝表面总是有一层抗腐蚀性好的氧化层(Al2O3);⑦接触电阻低(欧姆接触)。
缺点:
①结穿刺现象;②电迁移现象。
50.铝的结穿刺现象
在纯铝和硅的界面加热合金化过程中(450~500℃),硅开始溶解在铝中直到在铝中的浓度达到%,该过程消耗硅并在硅中形成空洞,可穿透浅结,引起短路。
解决方法:
①使用含硅(1~2%)的铝合金,铝中硅已饱和,抑制硅向铝中扩散;②引入阻挡层金属(例如TiN)以抑制硅扩散。
51.电迁移现象
当金属线流过大密度的电流时,电子和金属原子的碰撞引起金属原子的移动导致金属原子的消耗和堆积。
电迁移现象会造成金属线开路、两条邻近的金属线短路。
纯铝的电迁移现象非常严重。
解决方法:
使用含%铜的铝合金
52.铜互连的优点及采取的工艺措施
优点:
①电阻率更低;②电流密度高:
抗电迁徙能力好于铝,铜合金中加入Al或Ti进一步增强抗电迁移;③更少的工艺步骤:
采用大马士革方法,减少20%~30%;④易于沉积(铜CVD、电镀铜);⑤铜的成本低。
缺点:
①不能干法刻蚀铜;②铜在硅和二氧化硅中扩散很快,芯片中的铜杂质沾污使电路性能变坏;③抗腐蚀性能差;④粘附性差。
工艺措施:
①采用大马士革工艺回避干法刻蚀铜;②采用电镀来满足大马士革工艺对间隙填充的要求;③用阻挡层金属(例如Ta)增强粘附阻挡扩散;④用金属钨做底层金属解决了器件的铜沾污。
53.硅化物及其作用
硅化物是在高温下难熔金属(通常是钛Ti、钴Co)与硅反应形成的金属化合物(如TiSi2、CoSi2)。
其作用:
①降低器件寄生电阻;②降低接触电阻;③作为金属与硅之间的粘合剂。
54.化学机械平坦化CMP
(ChemicalMechanicalPlanarization)也称为化学机械抛光CMP(ChemicalMechanicalPolish)是通过化学反应和机械研磨相结合的方法对表面起伏的硅片进行平坦化的过程。
55.CMP技术的优点
①全局平坦化,台阶高度可控制到50?
左右;②平坦化不同的材料;③平坦化多层材料;④减小严重表面起伏;⑤能配合制作金属图形(大马士革工艺);⑥改善金属台阶覆盖;⑦减少缺陷;⑧不使用危险气体。
56.μmCMOS集成电路工艺技术工艺流程
①双阱工艺:
备片→初氧氧化→光刻N阱区→N阱磷注入→刻蚀初氧层→光刻P阱区→P阱硼注入→阱推进
②LOCOS隔离工艺:
垫氧氧化→氮化硅沉积→光刻有源区→光刻NMOS管场区→NMOS管场区硼注入→场区选择氧化
③多晶硅栅结构工艺:
去除氮化硅→栅氧化→多晶硅沉积→多晶掺磷→光刻多晶硅
④源/漏(S/D)注入工艺:
光刻NMOS管源漏区→NMOS管源漏区磷注入→光刻PMOS管源漏区→PMOS管源漏硼注入
⑤金属互连的形成:
BPSG沉积→回流/增密→光刻接触孔→溅射Si-Al-Cu→光刻金属互连
⑥制作压点及合金:
钝化→光刻压焊窗口→合金
⑦参数测试
57.先进的μmCMOS集成电路工艺技术1~7大工艺步骤
①双阱工艺;②浅槽隔离工艺;③多晶硅栅结构工艺;④轻掺杂漏(LDD)工艺;⑤侧墙形成工艺;⑥源/漏(S/D)注入工艺;⑦接触形成工艺;
58.倒掺杂阱技术:
连续三次离子注入
①第一次高能量(>200KEV)、深结(~μm)倒掺杂注入,以减小CMOS器件的闭锁效应;
②第二次中能量注入,以保证源漏击穿电压;
③第三次小剂量注入,以调整阈值电压。
59.LOCOS隔离原理:
通过NMOS场区的硼注入及场区选择氧化,增加场区的表面掺杂浓度及场区氧化层厚度,从而提高寄生NMOS管的阈值电压,使该阈值电压大于Vcc,实现了NMOS管之间的隔离。
LOCOS隔离的缺点:
①鸟嘴浪费有源区面积影响集成度;②横向尺寸不能精确控制。
60.浅槽隔离STI(ShallowTrenchIsolation)
浅槽隔离是在衬底上通过刻蚀槽、氧化物填充及氧化物平坦化等步骤,制作晶体管有源区之间的隔离区的一种工艺。
它取代了LOCOS隔离工艺。
优点:
提高电路的集成度,改善电路的抗闩锁性能。
61.轻掺杂漏(LDD)工艺目的
减小源漏间的穿通和沟道漏电,提高源漏击穿电压。
62.侧墙工艺目的
侧墙用来环绕多晶硅栅侧壁阻挡大剂量的S/D注入以免其接近沟道导致源漏穿通。