左支座铣槽保证5 夹具课程设计说明书.docx
《左支座铣槽保证5 夹具课程设计说明书.docx》由会员分享,可在线阅读,更多相关《左支座铣槽保证5 夹具课程设计说明书.docx(11页珍藏版)》请在冰豆网上搜索。
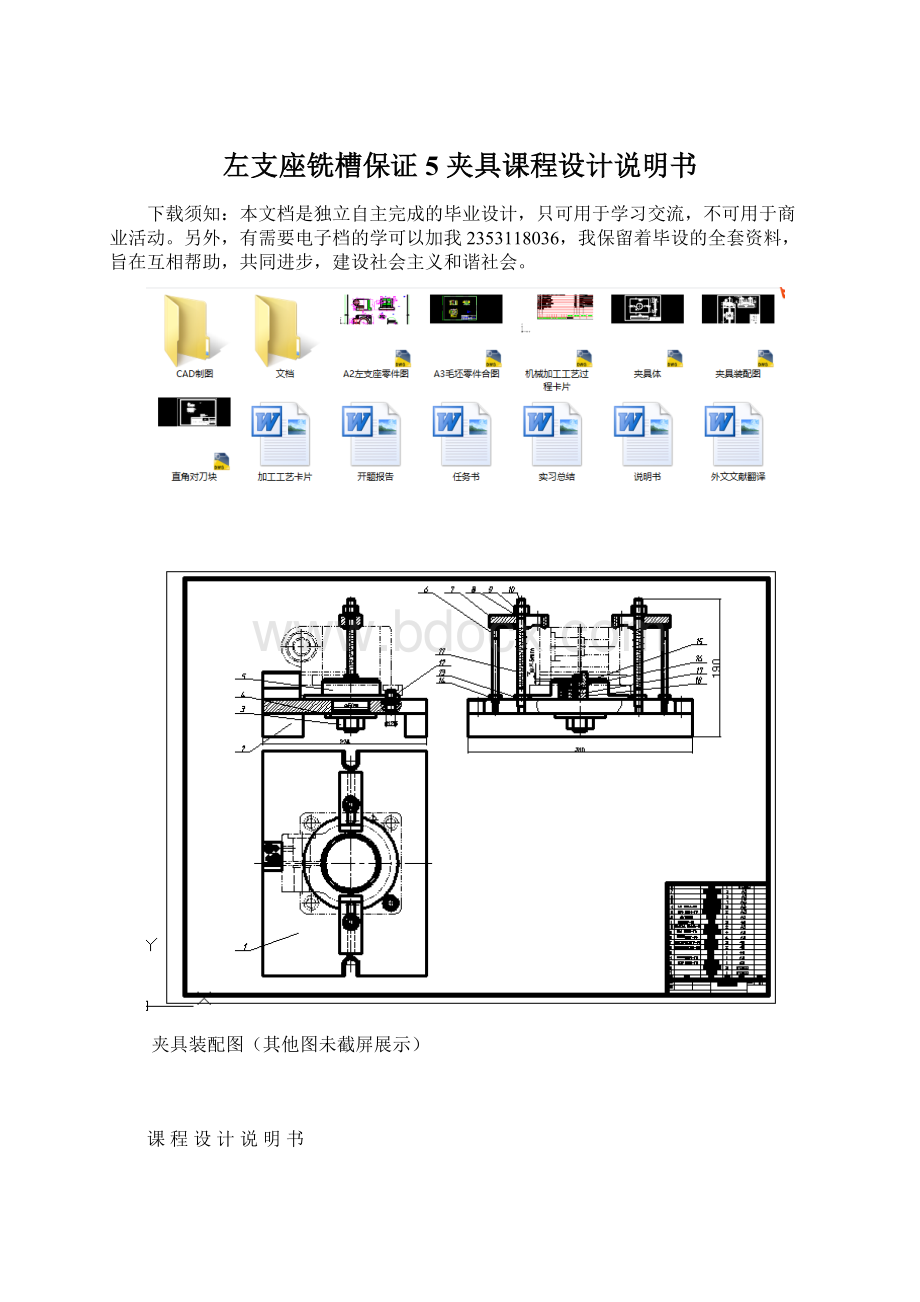
左支座铣槽保证5夹具课程设计说明书
下载须知:
本文档是独立自主完成的毕业设计,只可用于学习交流,不可用于商业活动。
另外,有需要电子档的学可以加我2353118036,我保留着毕设的全套资料,旨在互相帮助,共同进步,建设社会主义和谐社会。
夹具装配图(其他图未截屏展示)
课程设计说明书
设计:
xxx
班级:
xx机制xx班
学号:
xxxxxxxxx
一.零件的工艺分析及生产类型的确定
1.零件的作用
左支座的作用是将穿过支座中心孔
的轴或者杆,通过侧面的耳孔中安装螺栓进行夹紧,使轴杆固定。
松开螺栓后轴杆可转动或者滑动。
底板4X
大孔是固定支座的螺钉孔,2X
是定位销孔,M8-7H为放松螺钉孔,固定侧耳螺栓。
2.零件的工艺分析
通过对该零件图的重新绘制,知原图样的视图正确,完整,尺寸,公差及技术要求齐全。
所以这个零件的工艺性较好。
3.零件的生产类型
零件的生产纲领
N=5000件/年
二.选择毛坯,确定毛坯尺寸,设计毛坯图
1.选择毛坯
该零件材料为HT200,由于零件属批量生产,而且零件的轮廓尺寸不大,故可以采取金属型铸造成型有助于提高生产率,保证加工质量.估计加工质量为0.8kg
2.确定机械加工余量,毛坯尺寸和公差
①根据零件图计算轮廓尺寸,长165.5mm,宽140mm,高100mm,故最大轮廓尺寸为165.5mm
②选取公差等级CT由P119表5-1,铸造方法按机器造型,铸件材料按HT,得公差等级范围8-10级,取为9级。
③根据加工表面的基本尺寸和铸件公差等级CT,由P120表5-3得,公差带相对于基本尺寸对称分布
④由P121表5-5得,铸造方法按机器造型,铸件材料按QT,得机械加工余量等级范围D-F级,取为E级
⑤对所有加工表面取同一个数值,由P120表5-4得最大轮廓尺寸为165.5mm,机械加工余量等级为E级,得RMA(机械加工余量)为1.4mm
⑥毛坯基本尺寸
上下端面属单侧加工,应由P118式5-2得R=F+2RMA+CT/2=100+2*1.4+2.2/2=103.9
孔ф80H9属内腔加工,应由P1185-3式得R=F-2RMA-CT/2=80-2*1.4-2.2/2=76.1
其余尺寸由铸造获得估计质量为2.0kg
三.选择加工方法,制定工艺路线
1.定位基准的选择
(1).粗基准的选择原则:
按照有关粗基准的选择原则,当零件有不加工表面的时候,应该选取这些不加工的表面为粗基准;若零件有若干个不加工表面时,则应该选择加工表面要求相对相对位置精度较高的不加工表面作为粗基准.现取上表面作为定位基准
(2).精基准的选择原则:
精基准的选择主要应该考虑基准重合的问题,当设计基准与工序基准不重合的时候,应该进行尺寸换算。
现选下表面做精基准,估符合基准重合原则。
2.零件表面加工方法的选择
该零件毛坯包括下平面及一个大孔六个阶梯孔两个小孔两个螺纹孔以及两个缝槽,一个内孔倒角,材料为HT200。
以公差等级和表面粗糙度要求,参考《机械制造技术基础课程设计指南》有关资料,其加工方法选择如下。
(1)端面尺寸精度要求不高,表面粗糙度为Ra3.2。
要求Ra3.2的端面粗铣及半精铣即可(P129表5-16)
(2)孔ф80H9公差等级为9级,表面粗糙度为Ra1.6,粗镗,半精镗及精镗即可(P128表5-15)
(3)孔4*ф20为未注公差,公差等级按IT14,表面粗糙度为Ra6.3,粗铣即可(P128表5-16)
(4)孔4*ф13为未注公差,公差等级按IT14,表面粗糙度为Ra12.5,粗铣即可(P128表5-16)
(5)孔2*ф10为未注公差,公差等级按IT14,表面粗糙度为Ra1.6,钻削及铰孔即可(P128表5-15)
(6)内螺纹M8-7H公差等级为7级,表面粗糙度为Ra6.3,钻孔及车内螺纹即可(P128表5-15,P130表5-21)
(7)内螺纹M10-7H深18,表面粗糙度为Ra6.3,钻孔及车内螺纹即可(P128表5-15,P130表5-21)
(8)孔ф38为未注公差,公差等级按IT14,表面粗糙度为Ra3.2,粗铣,半精铣即可(P128表5-16)
(9)孔ф25H7(
)公差等级为7级,表面粗糙度为Ra3.2,粗铣及精铣即可(P128表5-16)
(10)为未注公差,公差等级按IT14,表面粗糙度为Ra12.5,粗铣(P128表5-16)
(11)孔ф43为未注公差,公差等级按IT14,表面粗糙度为Ra12.5,粗铣(P128表5-16)
(12)垂直缝槽5
为未注公差,公差等级按IT14,表面粗糙度为Ra12.5,粗铣即可(P128表5-16)
(13)水平缝槽5
为未注公差,公差等级按IT14,表面粗糙度为Ra12.5,粗铣即可(P128表5-16)
(14)ф80H9内孔边缘2*45°倒角,粗车即可。
3.制定工艺路线
该零件毛坯包括下平面及一个大孔六个阶梯孔两个小孔两个螺纹孔以及两个缝槽,一个内孔倒角。
按照先加工基准面及先粗后精先面后孔的原则,该零家加工可按下述工艺路线进行。
工序一:
以上端面粗铣半精铣下端面。
工序二:
以下端面粗镗,半精镗及精镗孔ф80H9
工序三:
以下端面和孔ф80H9以及孔ф13粗铣孔ф43、孔ф21粗铣,半精铣孔ф38,粗铣及精铣孔ф25H7(
)
工序四:
以下端面和孔ф80H9钻孔4*ф20铣孔4*ф13
工序五:
以下端面和孔ф80H9以及孔ф13粗铣垂直缝槽5
、水平缝槽5
、内孔ф80H9边缘2*45°倒角
工序六:
以下端面和孔ф80H9以及孔ф13钻及铰孔2*ф10,钻M10-7H深18和M8-7H的孔
工序七:
钳工台去毛刺,攻丝,加工倒角R15、R10、R3
工序八:
终检。
四.工序设计
1.选择加工设备与工艺装备
(1)选择机床
工序五用粗铣半精铣缝槽,应选卧式铣床,成批生产不要求很高的生产率,所选机床使用范围较广为宜,故选常用的X61型铣床能满足加工要求。
(P152表5-74)
(2)选择夹具
本零件钻削小孔时用专用的分度夹具外,镗削孔ф80H9用弹簧心轴,其他各工序使用通用夹具即可。
(3)选择刀具
①铣刀按P170表5-103选镶齿套式面铣刀(JB/T7954.1-1999)。
锯片铣刀按P171表5-106选粗齿锯片铣刀(GB/T6120-1996)
直柄立铣刀按P167表5-99选用D=21mm铣刀(GB/T6117.1-1996)
②镗刀选用镶焊硬质合金的双刃镗刀
③钻头按P156表5-84选用莫氏锥柄麻花钻(GB/T1438.1-1996)
P160表5-90带导柱直柄平底锪孔(GB/T4260-1984)
④丝锥按P166表5-97选用细柄机用和手用丝锥(GB/T3464.1-1994)
(4)选择量具
本零件属成批生产,一般情况下尽量采用通用量具。
根据零件表面的粗糙度要求,尺寸和形状特点,参考本书P173表5-108,选择如下
①加工平面经过粗铣及半精铣,粗铣时均为IT11,半精铣时为IT9,可选用读数值为0.02,测量范围为125*0.02的三用游标卡尺进行测量
②孔加工分别经过粗镗,半精镗及精镗和粗铣、半精铣和精铣或钻削。
ф80H9粗镗时为IT11,选读数值为0.01mm,测量范围为50-125mm的内径千分尺。
半精镗时为IT9,选读数值为0.01mm,测量范围为50-100mm的内径百分表。
孔2*ф10钻削时为IT10,选读数值为0.01mm,测量范围为10-18mm的内径百分表。
孔4*ф20、4*ф13和孔ф43、ф21粗铣是为IT12选读数值为0.01mm,测量范围为18-35mm的内径百分表和选读数值为0.01mm,测量范围为35-50mm的内径百分表,
孔ф38粗铣是为IT12选读数值为0.01mm,测量范围为25-50mm的内径千分尺,半精铣为IT11选读数值为0.01mm,测量范围为25-50mm的内径千分尺,
孔ф25H7(
)粗铣是为IT9选读数值为0.01mm,测量范围为18-35mm的内径百分表,精铣时为IT7选读数值为0.01mm,测量范围为18-35mm的内径百分表。
2.确定工序尺寸
由P138表5-43得
毛坯粗镗半精镗零件公差
ф80H976.178.079.580+0.19
由p137表5-42得2*ф10第一次钻为9.8粗铰9.96精铰10
由P141表5-52得M10-7H第一次钻为8.5,攻丝得M10
由P141表5-52得M8-7H第一次钻为6.7,攻丝得M8
由p140表5-49得粗铣下表面铣削加工余量为2.1,公差为+0.5.半精铣下表面铣削加工余量为1.0,公差为+0.3.
由p137表5-41得垂直缝槽5
粗铣宽度余量2.5,宽度偏差+0.12-+0.18
由p137表5-41得水平缝槽5
粗铣宽度余量2.5,宽度偏差+0.12-+0.18
五.确定切削用量及基本时间
1.工序五切削用量及基本时间的确定
(1)切削用量
以下端面和孔ф80H9粗铣垂直缝槽5
、水平缝槽5
、内孔ф80H9边缘2*45°倒角
1确定进给量
机床不变,采用锯片铣刀d=160mm,L=6,D=32,齿数=32
由p152表5-74得X61型铣床的功率为4kw,工艺系统刚性为中等,锯齿铣刀加工铸铁,由p198表5-145得,每齿进给量
=0.03-0.02mm/z,取为0.03mm/z
②选择刀具磨顿标准及耐用度
由p199表5-148得,用锯齿铣刀加工铸铁,铣刀刀齿后刀面最大磨损量为0.2mm,铣刀直径D=160mm,由p200表5-149得耐用度T=150min
③确定切削速度和工作台每分钟的进给量
由p32表2-17公式v=
Cv=24.4,qv=0.25,Xv=0.2,Yv=0.2,Uv=0.3,Pv=0.1,m=0.2,T=160min,ap=55.5,fz=0.03mm/z,
=70mm,D=160mm,z=32,kv=1.0,代入求得v=2.37mm/min
n=
=4.7r/min
由p153表5-75X61型卧式铣床主轴转速表,选择n=65r/min,则实际切削速度v=0.54mm/s,工作台每分钟进给量为
=0.03*32*65=62.4mm/min,由由p153表5-76X61型卧式铣床工作台进给量表,选择
=65mm/min,则实际每齿进给量
=0.03mm/z
④校验机床效率
由p34表2-18公式铣削时的功率为Pc=
,Fc=
Cf=30,Xf=1.0,Yf=0.65,Uf=0.83,Wf=0,qf=0.83,ap=55.5,fz=0.03m/z,
=70mm,D=160mm,z=32,n=65r/min,kfc=1,代入求得Fc=1278.2N,Pc=0.69kw
X61型铣床的功率为4kw,故所选切削用量可以采用。
所确定的切削用量为
=0.03mm/z
,
=65mm/min,n=65r/min,v=0.54mm/s。
(2)基本时间
由p40表2-28得基本时间为t
=
,l=70mm,D=160mm,l
=
=10,l2=2,
=65mm/min,代入求得Tj=1.26min=76s
同上查表读图,将数据代入相关公式得到粗铣水平缝槽5
切削用量为
=0.03mm/z
,
=65mm/min,n=65r/min,v=0.56mm/s。
Tj=1.37min=82s
六.铣削尺寸为5
mm的纵向槽夹具设计
1.选择定位方案,确定要限制的自由度
按照加工要求,钻通孔时应限制六个自由度,即应该实现完全定位。
设计的夹具为工序--铣竖槽。
该夹具适用于XA6132卧式铣床,选择A面与加工的为定位基准。
按照基准重合原则并考虑到目前有A面与孔加工,为避免重复使用粗机组基准,应以A面与孔定位.
从对工件的结构形状分析,若工件以A面朝右放置在支撑板上,定位夹紧都比较可靠,也容易实现,待夹紧后就能满足加工要求。
方案一:
以孔为主要定位基面,用长销限制工件四个自由度,用支撑钉相知一个自由度,但由于x转由长销限制,定位基准与工序基本相同,有利于保证槽侧面与空轴线的垂直度。
但是这种定位方式不利于工件的夹紧,因为辅助支撑钉不能起定位作用,当对辅助支撑钉施加夹紧力时,由于端面的面积太小,工件极易歪斜变形,夹紧也不可靠。
方案二:
在4-Φ20的孔内斜插入一削边销限制一个移动自由度,再Φ80H9的孔内插入一圆柱销,限制2个转动自由度,通过旋转压板压住工件,限制3个自由度
2.夹紧方案
根据工件夹紧的原则,如图3所示,用移动式压板将工件压在支撑钻台上
图3
3.对刀方案
将夹具体平稳放置在车床上,采用侧装直角对刀块(图4).铣刀的距离则由铣刀间的轴套长度确定.因此,只需设置一个对刀块即能满足铣槽的加工要求.
图4
4.夹具体与定位键
为保证夹具在工作台上安装稳定,应按照夹具体的高宽比不大于1.25的原则,确定其宽度,并在底座下开台阶,方便加工且提高精度,方便固定。
夹具在机床工作台的位置灵活,夹具体底面平整,并不需要定位键。
5.夹具总图上的尺寸,公差和技术要求
夹具图上的尺寸,公差和技术要求
1)夹具最大轮廓尺寸为270mm.226mm,190mm.
2)影响夹具在机床上安装精度的尺寸和公差为定位键与铣床工作台T形的配合尺寸18h8(T形槽为18H8)
3)对刀块的位置尺寸10.82,24.955对刀块的位置尺寸h为限位基准到对刀块表面的距离.计算时应考虑定位基准在加工尺寸方向上的最小位移量,在本图中,由于工件定位基准面长度为140mm,槽宽为5mm,槽深控制尺寸66.8js12,所以对刀块水平反向的位置尺寸为
H1=21/2mm
对刀块垂直方向的位置尺寸为
H2=(66.8-100.19/2)mm=15mm
取工件的相应尺寸公差的1/2~1/5
4)影响对刀精度的尺寸和公差Sr:
塞尺的厚度尺寸为5h8
5)加工精度分析铣槽时对槽两侧面对轴线的对称度和平行度要求较高,应进行精度分析,其他加工要求未注公差或者公差很大,可不进行精度分析.
a)、铣槽侧面对轴线的对称度的加工精度
定位误差△D由于对称度的工序基准是轴线,定位基准也是此轴线,故⊿B=0,因此对称度的定位误差为零.
安装误差△A定位键在T形槽中有两种位置,因此在两定位键之间
△A=Xmax=(0.027+0.027)mm=0.054mm
若加工尺寸在两定位键之外,则
△A=Xmax+2Ltg△a
tg△a=Xmax/Lo
对刀误差△T对称度的对刀误差等于尺塞厚度的公差,既△T=0.018mm
夹具误差△J影响对称度的误差有:
对刀块的水平位置尺寸的公差,所以△j=0.06m.
b)、铣槽时对轴线平行度的加工误差
定位误差△D定位误差△D=0
安装误差△A工件的轴线相对于工作台导轨平行时,△A=0
工件的轴线相对于工作台导轨有转角误差,使得槽的侧面对轴线产生平行度误差,所以
△A=tg△aL=(0.054/400*282)mm=0.038mm
对刀误差△T由于平行度不受尺塞厚度的影响,所以△T=0
夹具误差△J影响平行度的制造误差是设计心轴轴线与定位键侧面B的平行度0.03mm,所以△J=0.03mm.
七.总结
机械制造工艺学课程设计是在我们学完了大学的大部分基础课、技术基础课、专业课以及参加了生产实习之后进行的。
这是我们在进行毕业设计之前对所学各课程的一次深入的综合性的总复习,也是一次理论联系实际的训练,它在我们四年的大学生活中占有重要的地位。
通过本次课程设计,我们得到下述各方面的锻炼:
1能熟练运用机械制造工艺学课程中的基本理论以及在生产实习中学到的实践知识,正确解决一个零件在加工中的定位、夹紧以及工艺路线安排、工艺尺寸确定等问题,保证零件的加工质量。
2提高结构设计的能力。
了解设计夹具的训练,获得根据被加工零件的加工要求,设计出高效、省力、经济合理而且能保证加工质量的夹具的能力。
就我个人而言,通过本次课程设计对自己未来将从事的工作进行一次适应性训练,从中锻炼自己分析问题、解决问题的能力,为今后参加生产实践打下一个良好的基础。