铁路钢桥保护涂装.docx
《铁路钢桥保护涂装.docx》由会员分享,可在线阅读,更多相关《铁路钢桥保护涂装.docx(17页珍藏版)》请在冰豆网上搜索。
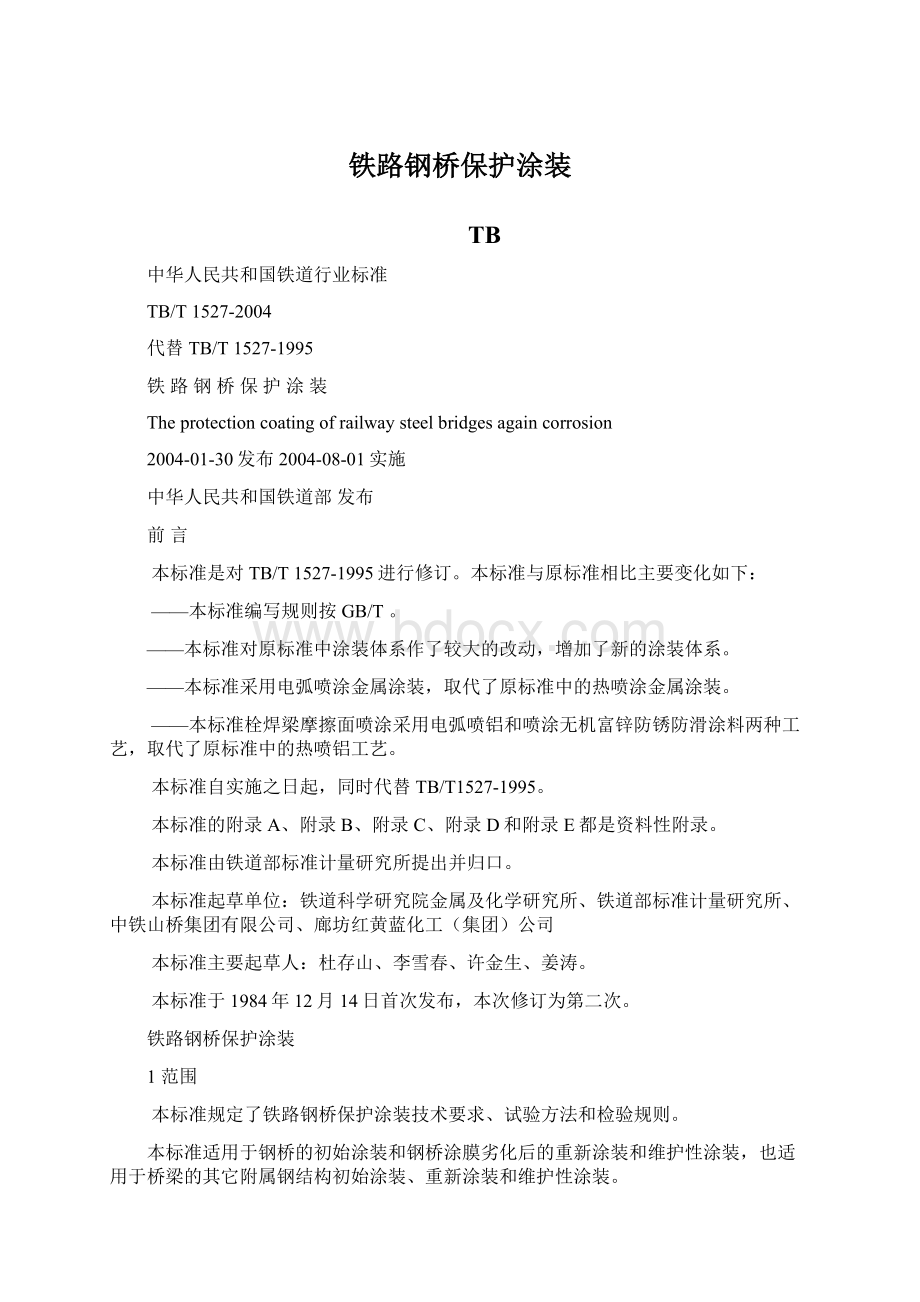
铁路钢桥保护涂装
TB
中华人民共和国铁道行业标准
TB/T1527-2004
代替TB/T1527-1995
铁路钢桥保护涂装
Theprotectioncoatingofrailwaysteelbridgesagaincorrosion
2004-01-30发布2004-08-01实施
中华人民共和国铁道部发布
前言
本标准是对TB/T1527-1995进行修订。
本标准与原标准相比主要变化如下:
——本标准编写规则按GB/T。
——本标准对原标准中涂装体系作了较大的改动,增加了新的涂装体系。
——本标准采用电弧喷涂金属涂装,取代了原标准中的热喷涂金属涂装。
——本标准栓焊梁摩擦面喷涂采用电弧喷铝和喷涂无机富锌防锈防滑涂料两种工艺,取代了原标准中的热喷铝工艺。
本标准自实施之日起,同时代替TB/T1527-1995。
本标准的附录A、附录B、附录C、附录D和附录E都是资料性附录。
本标准由铁道部标准计量研究所提出并归口。
本标准起草单位:
铁道科学研究院金属及化学研究所、铁道部标准计量研究所、中铁山桥集团有限公司、廊坊红黄蓝化工(集团)公司
本标准主要起草人:
杜存山、李雪春、许金生、姜涛。
本标准于1984年12月14日首次发布,本次修订为第二次。
铁路钢桥保护涂装
1范围
本标准规定了铁路钢桥保护涂装技术要求、试验方法和检验规则。
本标准适用于钢桥的初始涂装和钢桥涂膜劣化后的重新涂装和维护性涂装,也适用于桥梁的其它附属钢结构初始涂装、重新涂装和维护性涂装。
2规范性引用文件
下列文件中的条款通过本标准的引用而成为本标准的条款。
凡是注日期的引用文件,其随后所有的修改单(不包括勘误的内容)或修订版均不适用于本标准,然而,鼓励根据本标准达成协议的各方研究是否使用这些文件的最新版本。
凡是不注日期的引用文件,其最新版本适用于本标准。
GB/T470-1997锌锭
GB/T1763-1979漆膜耐化学试剂性测定法
GB/T1765-1979测定耐湿热、耐盐雾、耐侯性(人工加速)的漆膜制备法
GB/T3190-1996变形铝及铝合金化学成分
GB/T4956-1985磁性金属基体上非磁性覆盖层厚度测量磁性方法
GB/T5210-1985涂层附着力的测定法拉开法
GB/T表面粗糙度比较样块抛(喷)丸、喷砂加工表面
GB6514涂装作业安全规程涂漆工艺安全及其通风净化
GB7692涂装作业安全规程涂漆前处理工艺安全及其通风净化
GB/T8923-1988涂装前钢材表面锈蚀等级和除锈等级
GB/T9286-1998色漆和清漆漆膜的划格试验
GB/T9793-1997金属和其他无机覆盖层热喷涂锌、铝及其合金
GB/T11373-1989热喷涂金属件表面预处理通则
GB/T11374-1989热喷涂涂层厚度的无损测量方法
GB11375金属和其他无机覆盖层热喷涂操作安全
GB/T色漆和清漆漆膜厚度的测定
GB/T14522-1993机械工业产品用塑料、涂料、橡胶材料人工气候加速试验方法
TB/T2137-1990铁路钢桥栓接板面抗滑移系数试验方法
TB/T2486-1994铁路钢梁涂膜劣化评定
TB/T2772-1997铁路钢桥用防锈底漆供货技术条件
TB/T2773-1997铁路钢桥用面漆、中间漆供货技术条件
YB/T5149-1993铸钢丸
YB/T5150-1993铸钢砂
3技术要求
钢梁的初始涂装和重新涂装
3.1.1涂装前表面清理
3.1.1.1涂装前钢表面除锈等级要求
3.1.1.电弧喷涂锌、铝或涂装富锌防锈底漆时,钢表面清理应达到GB/T8923-1988规定的Sa3级,外观相当GB/T8923-1988规定的ASa3、BSa3、CSa3。
3.1.1.涂装红丹醇酸、红丹酚醛或聚氨酯底漆,钢表面清理应达到GB/T8923-1988规定的级,外观相当该标准规定的、、、。
3.1.1.桥栏杆、扶手、人行道托架、墩台吊篮等桥梁附属钢结构涂装红丹防锈底漆,箱形梁内表面涂装环氧沥青涂料时,钢表面清理应达到GB/T8923-1988规定的Sa2级,外观相当该标准规定的BSa2、CSa2、DSa2。
附属钢结构的光圆钢涂装红丹防锈底漆时,钢表面清理应达到GB/T8923-1988规定的St3级,外观相当该标准规定的BSt3、CSt3、DSt3。
3.1.1.2涂装前钢表面粗糙度要求
3.1.1.涂装涂料涂层时,钢表面粗糙度规定为Rz25
m~60
m,即符合GB/T规定的粗糙度样块为Ra6.3
m和Ra12.5
m之间的粗糙度要求。
3.1.1.电弧喷涂锌或铝金属时,钢表面粗糙度规定为Rz50
m~100
m,即符合GB/T规定的粗糙度样块为Ra12.5
m和Ra25.0
m之间的粗糙度要求。
3.1.1.磨料粒度和表面粗糙度的关系,可参照附录A(资料性附录)。
3.1.1.涂装涂料涂层时,选用最大粗糙度不超过涂装体系干膜厚度的1/3,表面粗糙度超过规定时需加涂一道底漆;喷涂锌铝涂层时,如果粗糙度超过Rz100
m时,涂层应超过轮廓峰125
m。
3.1.1.3钢表面清理用磨料
钢表面清理用磨料应使用符合YB/T5149-1993和YB/T5150-1993标准规定的钢丸、钢砂,或应使用无盐份和无沾污的石英砂。
3.1.2钢梁的涂料涂装
3.1.2.1钢梁涂装体系见表1。
表1钢梁涂装体系
涂装体系
涂料(涂层)名称
每道干膜最小厚度(
m)
至少涂装道数
总干膜最小厚度(
m)
适用部位
1
特制红丹酚醛(醇酸)防锈底漆
灰铝粉石墨或灰云铁醇酸面漆
35
35
2
2
70
70
桥栏杆、扶手、人行道托架、墩台吊篮、围栏和桥梁检查车等桥梁附属钢结构
2
电弧喷铝层
环氧类封孔剂
棕黄聚氨酯盖板底漆
灰聚氨酯盖板面漆
---
20
50
40
---
1
2
4
200
20
100
160
钢桥明桥面的纵梁、上承板梁、箱型梁上盖板
3
无机富锌防锈防滑涂料
或电弧喷铝层
80
---
1
---
80
100
栓焊梁连接部分摩擦面
4
环氧沥青涂料
或环氧沥青厚浆涂料
60
120
4
2
240
240
非密封的箱形梁和箱形杆件内表面
5
特制环氧富锌防锈底漆
或水性无机富锌防锈底漆
棕红云铁环氧中间漆
灰铝粉石墨醇酸面漆
40
40
35
2
1
2
80
40
70
钢梁主体,用于气候干燥、腐蚀环境较轻的地区
6
特制环氧富锌防锈底漆
或水性无机富锌防锈底漆
棕红云铁环氧中间漆
灰色丙烯酸脂肪族聚氨酯面漆
40
40
35
2
1
2
80
40
70
钢梁主体,用于腐蚀环境较严重的地区
7
特制环氧富锌防锈底漆
或水性无机富锌防锈底漆
棕红云铁环氧中间漆
氟碳面漆
40
40
30
2
1
2
80
40
60
钢梁主体,用于酸雨、沿海等腐蚀环境严重、紫外线辐射强、有景观要求的地区
3.1.2.2初始涂装时,钢梁制造厂应完成全部底漆(中间漆)和第一道面漆涂装。
3.1.2.3对于距离水面较近的钢梁底面(包括桁梁下弦杆、纵横梁底面,下承板梁主梁和上承板、箱梁底
面)、跨越受污染的河流的钢梁底部应增加涂装底漆一道、中间漆一道。
3.1.3钢梁的电弧喷涂金属涂装
3.1.3.1电弧喷铝用铝丝材质应采用GB/T3190-1996中LF2,含铝量为%以上;
3.1.3.2电弧喷锌用锌丝材质应符合GB/T470-1997的规定,含锌量不低于%;
3.1.3.3金属涂层采用环氧类封孔剂进行封孔时,封孔层厚度无要求,涂覆的封孔剂至不被吸收为止;封孔后应加涂相应的配套涂料。
3.1.4栓焊梁螺栓连接部分摩擦面涂装
3.1.4.1采用电弧喷涂铝,涂层厚度为150
m±50
m或采用无机富锌防锈防滑涂料,涂层厚度为120
m±40
m。
涂层的抗滑移系数不小于。
3.1.4.2杆件栓接点外露的铝表面、无机富锌防锈防滑涂料表面与涂料涂层搭接处应涂装特制环氧富锌防锈底漆。
钢梁组装后,栓接点外露的铝涂层应按条规定进行涂装。
栓接点螺栓、螺栓头处涂装特制环氧富锌防锈底漆,涂装前螺栓应除油,螺母和垫片应水洗清除皂化膜。
钢梁维护性涂装
3.2.1铁路钢梁涂膜劣化类型按TB/T2486-1994判定。
3.2.2劣化类型为3级粉化时,应清除涂层表面污渍,用细砂纸除去粉化物,然后覆盖2道相应面漆。
3.2.3当旧涂层未锈蚀,劣化类型为2~3级起泡、裂纹或脱落时,用手动工具或动力工具清理损坏的区域周围疏松的涂层,并延伸至未损坏的涂层区域50mm~80mm坡口,局部涂相应底漆和面漆。
如要保持涂层表面一致,可在局部涂面漆后,全部再覆盖面漆。
3.2.4当旧涂层锈蚀,劣化类型为2~3级生锈时,应清除松散的涂层,直到良好结合的涂层区域为止,旧涂层表面清理应达到PSt31)级,未损坏的涂层区域边缘按条要求处理,然后局部涂装相应防锈底漆和相应中间漆、面漆。
如要保持涂层表面一致,可在局部涂面漆后,全部再覆盖面漆。
3.2.5当旧喷锌或铝涂层发生锈蚀劣化类型为2~3级生锈时,应除去松动的锌或铝涂层和涂料涂层直到良好结合的锌或铝涂层区域为止,钢表面锈蚀清理应达到级。
对于未损坏的涂料和锌或铝涂层区域边缘按条要求处理。
对于电弧喷锌或铝涂层清理部位,也可改涂特制环氧富锌防锈底漆2道,然后涂装相应中间漆和面漆。
涂层质量要求
3.3.1涂料涂层表面平整均匀,不允许有剥落、起泡、裂纹、气孔,允许有不影响防护性能的轻微桔皮、流挂、刷痕和少量杂质。
3.3.2金属涂层表面均匀一致,不允许有起皮、鼓泡、大熔滴、松散粒子、裂纹、掉块,允许有不影响防护性能的轻微结疤、起皱。
3.3.3整个涂装体系涂层间附着力按GB/T9286-1998规定作划格试验,附着力不低于一级。
3.3.4锌、铝涂层对钢基材附着力按GB/T9793-1997规定,采用切格试验法时,试验结束后,方格内的涂层不得与基体剥离;采用拉力试验法时,附着力不低于。
涂装作业环境和涂装间隔时间要求
3.4.1电弧喷涂锌、铝涂层时作业环境要求与电弧喷涂作业的间隔时间要求,按GB/T11373-1989规定。
3.4.2钢结构表面清理后应在4h内完成涂装锌、铝涂层,电弧喷涂锌或铝完成后应立即覆盖封孔剂。
既有线利用列车运行间隔施工时,覆盖封孔剂或涂层前,应对锌或铝涂层表面作清洁处理。
1)PSt3:
被清理的表面油漆涂层部分应粘附牢固完好无损,其它部分应无可见的油脂和污物,无粘附不牢的氧化皮、铁锈、油漆涂层和异物,金属基底要有金属光泽。
3.4.3涂装涂料时作业环境要求:
水性无机富锌防锈底漆、酚醛漆、醇酸漆、聚氨酯漆、氟碳面漆不允许在气温5℃以下施工,环氧类漆不允许在10℃以下施工;
不允许在相对湿度80%以上,雨天、雾天或风沙场合施工。
3.4.4涂装涂料涂层需在上一道涂层实干后,方可涂装下一道漆,底漆、中间漆最长暴露时间不超过7天,两道面漆间隔若超过7天时需用细砂纸打磨成细微毛面。
3.4.5水性无机富锌防锈底漆和氟碳面漆的施工参照附录B的规定进行。
涂装施工安全
3.5.1手工和动力工具除锈、喷射除锈和清除旧涂层等涂装前处理工艺安全,按GB7692规定进行。
3.5.2涂漆工艺中如贮存、涂料调制、涂装、干燥等劳动安全卫生技术要求按GB6514规定进行,按该标准规定划出涂漆区、火灾危险区、电气防爆区。
3.5.3锌、铝喷涂设备的安全操作、操作人员的安全保证和通风保健要求,按GB11375规定。
4试验方法
表面清理等级检验按GB/T8923-1988规定除锈等级目视评定方法进行,注意磨料不同造成的外观上差别。
表面粗糙度检验
4.2.1表面粗糙度可采用GB/T规定的比较样块进行粗糙度目视和触觉评定。
4.2.2表面粗糙度可用触针式表面轮廓仪测量。
4.2.3测量峰谷深度可用指针式千分尺。
涂层表面质量检查方法采用目视法
涂层厚度的检测方法
4.4.1涂料涂层干膜厚度和湿膜厚度测量,按GB/T规定进行。
4.4.2涂料涂层厚度测量时,以钢梁杆件为一测量单元,在特大杆件表面上以10m2为一测量单元,每个测量单元至少应选取三处基准表面,每一基准表面测量五点,其测量分布如图1,取其算术平均值。
100mm
100mm
图1
4.4.3锌、铝涂层厚度测量方法按GB/T4956-1985规定,测点位置按GB/T11374-1989规定进行。
涂层附着力检测方法
4.5.1涂料涂层附着力检验按GB/T9286-1998做划格试验或GB/T5210-1985做拉开试验。
划格试验时涂层厚度不大于80
m时,划线间隔为1mm;涂层厚度为80
m~120
m时,划线间隔为2mm;涂层厚度大于120
m时,划线间隔为3mm。
4.5.2锌、铝涂层附着力检验按GB/T9793-1997规定做切格试验或拉力试验。
5检验规则
水性无机富锌防锈底漆、无机富锌防锈防滑涂料、灰色丙烯酸脂肪族聚氨酯面漆、氟碳面漆技术指标分别参见附录C、附录D、附录E,其它涂料的技术指标应符合TB/T2772-1997、TB/T2773-1997的规定。
在涂装过程中对温度、湿度和周围环境等涂装作业环境进行检验。
在钢梁涂装前对钢表面除锈等级和粗糙度大小进行检验。
在涂装过程中对涂装间隔时间和涂膜外观进行检验。
涂装过程中对底漆涂层、锌铝涂层以及完整的涂装体系的涂层厚度分别进行检验。
涂料涂层涂装过程中,可以测量湿膜厚度以控制干膜厚度。
不允许单独制备试片代替钢梁杆件作涂层厚度检验。
涂装过程可用抽样方法对涂层附着力进行检验,附着力检验可以是钢基体和涂层间附着力,也可以是完整涂装体系涂层间附着力。
附录A
(资料性附录)
磨料粒度与粗糙度的关系
磨料粒度与粗糙度的关系见表。
表磨料粒度与粗糙度的关系
序号
表面处理
磨料
表面粗糙度RY(
m)
方法
条件
品种
颗粒度
组成%
1
2
3
4
平均
1
2
3
4
5
6
7
抛丸
单面、50周
钢砂
钢丝段
1mm
~2.3mm
20
80
67
82
73
66
72
钢砂
钢砂
钢丸
钢丝段
钢丝段
钢砂
1mm
0.7mm
0.7mm
0.8mm
~2.3mm
0.4mm
100
100
100
100
100
100
57
35
37
45
90
27
53
35
38
42
91
28
50
38
39
44
96
26
54
37
36
43
94
26
53
37
38
43
93
27
8
压缩空
气喷射
喷嘴直径9mm,压力,距离300mm
钢砂
70目
100目
--
62
54
54
51
56
9
压缩空
气喷射
喷嘴直径8.5mm,
压力<,距离300mm
50目
70目
100目
20
60
20
53
56
55
57
55
10
11
12
压缩空
气喷射
同上
细丸
细砂
粗砂
--
--
--
--
--
--
45
26
61
49
29
63
42
26
68
39
28
65
44
27
64
附录B
(资料性附录)
水性无机富锌防锈底漆、氟碳面漆施工要求
水性无机富锌防锈底漆施工要求
环境要求如下:
a)气温:
环境温度不低于5℃,室外施工时应避免底材被太阳直晒。
b)相对湿度:
≤80%,不允许在相对湿度80%以上的天气、雨天、雾天或风沙场合施工。
c)风力:
≤3级。
施工注意事项如下:
a)所有工具使用前应用清水冲洗,不能被油污污染。
b)用强力搅拌机搅拌液体物料。
c)逐步将锌粉搅入液体物料中。
继续搅拌直到粉剂完全分散,直至混合料中无团块。
不要一次混合过多的物料,以便在适用期内用完。
切勿倒转次序,也不得改变混合比率。
d)一般情况下,都不得进行稀释。
e)用30目滤筛过滤混合物料以防止工具的堵塞。
f)在施工过程中继续缓慢搅拌物料,以保持混合料的均匀状态。
g)采用均匀、同向的湿喷涂,每次覆盖前一次的1/3~1/2,以避免空隙、漏涂和针眼。
h)在焊点、断面、尖锐边缘、铆接点、栓接处及转角处的涂层厚度应适当,涂层过厚会出现裂纹。
i)使压力罐和喷枪保持在同一高度,以便物料能顺利地流入喷枪。
j)当涂层完全干燥后,用无损伤干膜层的厚度检测仪测量膜层厚度。
如需要增加膜厚时,须待膜层干燥至可以操作时再喷涂。
膜层厚度为80μm,允许范围为70μm~100μm。
k)当膜层干燥至可以进行操作时,用刷涂添补针眼、空隙、较小面积的破损和漏涂。
面积较大时则采用喷涂。
l)在施工期间和在最后涂层的固化期间应保持清洁净空气的流通。
m)使用后立即用清水清洗工具。
n)在水性无机富锌防锈底漆涂层上进行棕红云铁环氧中间漆涂装时应分为两步:
1)将棕红云铁环氧中间漆稀释一倍,然后涂装;2)干燥后再正常涂装棕红云铁环氧中间漆到规定的干膜厚度。
氟碳面漆施工要求
环境要求如下:
a)气温:
环境温度不低于5℃,室外施工时应避免底材被太阳直晒。
b)相对湿度:
≤80%,不允许在相对湿度80%以上的天气、雨天、雾天或风沙场合施工。
c)风力:
≤3级。
施工注意事项如下:
a)喷涂的空气要干净,无油无水。
b)涂装时涂料粘度要合适。
c)熟化期:
30min(即两组分混合均匀后,30min后使用)。
d)氟碳涂料为双组分涂料,配漆时应严格按照要求的比例进行调漆。
1)按照当天涂料的用量及涂料的使用期,计划配制涂料,现用现配,用多少配多少;
2)配漆前后必须充分搅匀,配漆用品要分开使用;
3)使用前要将调配好的涂料用40目~100目的筛网过滤。
e)涂漆间隔时间:
中间漆与第一道面漆涂装间隔时间为24h~168h,超过168h时,表面应清理,必要时在涂装面漆前表面应用细砂纸轻轻打磨,再行涂装。
应严格控制每道漆的干膜厚度。
f)涂装
1)试喷:
正式涂装前应试喷涂料,掌握温度、粘度、走枪速度等对涂装质量的影响,取得经验。
2)喷漆前准备:
准备喷枪,调整漆雾,搅拌油漆,除去被涂表面的灰尘和异物。
3)喷涂方式:
行枪速度均匀,枪距物面适当。
先喷上面后喷下面,先难后易。
压盖1/3~1/2,压盖要均匀。
4)防止流挂、超薄和干喷,允许少量流挂,超薄可以补喷,干喷必须返工。
5)自检喷涂质量:
喷涂一个区段后,用眼观察湿膜,如湿膜湿润、丰满、有光泽,喷涂质量好;如湿膜光泽差、有粗糙感,则喷涂不均匀并且偏薄。
可用湿膜测厚计帮助掌握厚度。
6)补偿喷涂:
在光泽差、有粗糙感的地方,可补喷加厚。
干膜超薄的地方,在喷涂下一道漆时可加厚补偿。
7)清洗用具:
用少量相应稀料清洗喷具,至少清洗三次,用过的稀料可重复使用。
附录C
(资料性附录)
铁路钢桥用水性无机富锌防锈底漆技术条件
产品的组成
水性无机富锌防锈底漆由硅酸钾水溶液、锌粉等组成。
锌粉应满足:
总锌含量大于98%,金属锌含量大于94%,细度不低于325目。
水性无机富锌防锈底漆属自固型涂料,为双组分。
技术要求
水性无机富锌防锈底漆应符合表中的技术要求。
表水性无机富锌防锈底漆技术要求
项目
单位
技术指标
涂层颜色及外观
/
锌灰色,涂层平整
不挥发物
%
≥75
粘度(6号杯)
s
≥6
干膜中锌粉含量
%
≥90
干燥
时间
表干
min
≤30
实干
h
≤2
自固化时间
h
≤6
硬度
H
≥4
附着力
划格法
级
≤2
拉开法
MPa
≥4
耐盐雾性
h
经过1000h盐雾实验,涂层不出现红锈,划痕处120h不出现红锈
适用期
h
≥8
贮存期
月
≥6
耐盐雾性、贮存期作为供应商保证项目,不作为用户必检项目。
试验方法
样板制备:
底材采用普通低碳钢板,表面喷砂处理,达到Sa3级,不能有任何油污,粗糙度不小于20μm。
按GB/T1765-1979规定进行样板制备,漆膜厚度不小于75μm。
自固化时间测定:
将样板的2/3放入盛有蒸馏水或去离子水的烧杯中,调节水温为23±2℃,并在整个实验过程中保持该温度。
样板浸泡后,将试样取出,立即用手指擦拭已浸泡过的涂层,以目视检查手指上是否有涂层溶解物,试样上的涂层是否有起泡、脱落等现象。
6h后涂层应无溶解、无起泡、无脱落现象。
其它项目试验方法按照TB/T2772-1997的规定进行。
附录D
(资料性附录)
铁路钢桥用灰色丙烯酸脂肪族聚氨酯面漆和氟碳面漆技术条件
产品的组成
灰色丙烯酸脂肪族聚氨酯面漆由脂肪族异氰酸酯和含羟基丙烯酸树脂、颜料、助剂及溶剂等组成。
灰色丙烯酸脂肪族聚氨酯面漆为双组份。
氟碳面漆由氟碳树脂和脂肪族异氰酸酯为基料、金红石型钛白粉和助剂等组成。
氟碳面漆为双组份。
技术要求
灰色丙烯酸脂肪族聚氨酯面漆和氟碳面漆应符合表中的技术要求。
表灰色丙烯酸脂肪族聚氨酯面漆和氟碳面漆的技术要求
项目
单位
技术指标
灰色丙烯酸脂肪族聚氨酯面漆
氟碳面漆
氟含量
%
/
≥15
涂层颜色及外观
灰色,半光,表面色调均匀一致,涂层平整
表面色调均匀一致,漆膜平整
不挥发物
%
≥60
≥55
流出时间
s
≥50
≥30
细度
μm
≤50
30
干燥时间
表干
h
≤2
≤2
实干
h
≤24
≤24
弯曲性能
mm
≤2
≤2
耐冲击性
cm
≥50
≥50
附着力(拉开法)
MPa
≥5
≥6
耐碱性(5%NaOH)
h
240h涂层无异常
240h涂层无异常
耐酸性(5%H2SO4)
h
240h涂层无异常
240h涂层无异常
耐水性
h
≥12
≥12
耐人工加速老化性能
h
经过1000h,涂层无明显变色和粉化,无泡,无裂纹
3000h试验漆膜无明显变色,无粉化,无泡,无裂纹,保光率≥80%
适用期
h
≥5
≥5
施工性能
可复涂,每道干膜厚度不小于35μm
可复涂,每道干膜厚度不小于30μm
注:
1)耐人工气候加速试验为型式检验项目;
2)氟含量是指生产氟碳涂料所用原料含氟树脂中的含氟量。
试验方法
试验方法(除耐人工气候加速试验)按照TB/T2773-1997的规定进行;耐酸、碱性按照GB/T1763-1979的规定进行;耐人工气候加速试验按照GB/T14522-1993中a试验方法进行,试验温度为光