SMT工艺标准.docx
《SMT工艺标准.docx》由会员分享,可在线阅读,更多相关《SMT工艺标准.docx(16页珍藏版)》请在冰豆网上搜索。
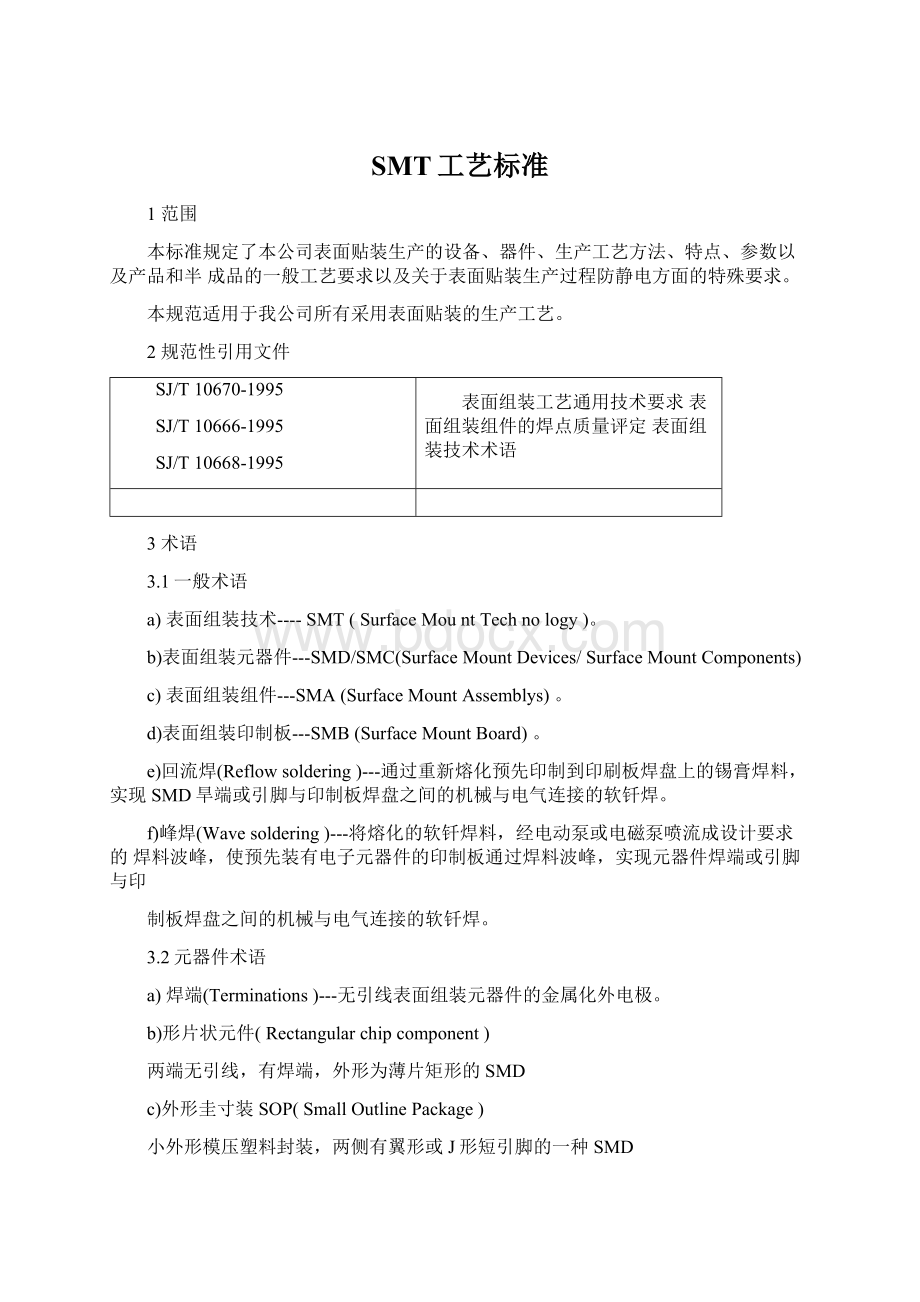
SMT工艺标准
1范围
本标准规定了本公司表面贴装生产的设备、器件、生产工艺方法、特点、参数以及产品和半成品的一般工艺要求以及关于表面贴装生产过程防静电方面的特殊要求。
本规范适用于我公司所有采用表面贴装的生产工艺。
2规范性引用文件
SJ/T10670-1995
SJ/T10666-1995
SJ/T10668-1995
表面组装工艺通用技术要求表面组装组件的焊点质量评定表面组装技术术语
3术语
3.1一般术语
a)表面组装技术----SMT(SurfaceMountTechnology)。
b)表面组装元器件---SMD/SMC(SurfaceMountDevices/SurfaceMountComponents)
c)表面组装组件---SMA(SurfaceMountAssemblys)。
d)表面组装印制板---SMB(SurfaceMountBoard)。
e)回流焊(Reflowsoldering)---通过重新熔化预先印制到印刷板焊盘上的锡膏焊料,实现SMD旱端或引脚与印制板焊盘之间的机械与电气连接的软钎焊。
f)峰焊(Wavesoldering)---将熔化的软钎焊料,经电动泵或电磁泵喷流成设计要求的焊料波峰,使预先装有电子元器件的印制板通过焊料波峰,实现元器件焊端或引脚与印
制板焊盘之间的机械与电气连接的软钎焊。
3.2元器件术语
a)焊端(Terminations)---无引线表面组装元器件的金属化外电极。
b)形片状元件(Rectangularchipcomponent)
两端无引线,有焊端,外形为薄片矩形的SMD
c)外形圭寸装SOP(SmallOutlinePackage)
小外形模压塑料封装,两侧有翼形或J形短引脚的一种SMD
d)小外形晶体管SOT(SmallOutlineTransistor)
采用小外形封装结构的表面组装晶体管。
e)小外形二极管SOD(SmallOutlineDiode)
采用小外形封装结构的表面组装二极管。
f)小外形集成电路SOIC(SmallOutlineIntegratedCircuit)
指外引线数不超过28条的小外形封装集成电路,一般有宽体和窄体两种封装形式;其中有翼形短引线的称为SOL器件,有J型短引线的称为SOJ
g)收缩型小外形圭寸装SSOP(ShrinkSmallOutlinePackage)
近似小外形封装,但宽度更窄,可以节省组装面积的新型封装。
h)芯片载体(Chipcarrier)---表面组装集成电路的一种基本封装形式,它是将集成电路芯片和内弓I线封装于塑料或陶瓷壳体之内,向壳外四边引出相应的焊端或引脚;也泛指采用这种圭寸装形式的表面组装集成电路。
4表面组装技术(SMT的组成
表面组装
技术
组装工艺技术
电路印制板(PCB)技术:
单(多层)、材料、电设计、热设计、抗干扰设计、元器件布局设计、电路布局设计、焊盘图形设计等。
5
5.1表面贴装元器件的种类
片式元件
表面贴装元器件
表面贴装兀器件
5.2表面组装兀器件的特点
a)尺寸小、重量轻,节省原料,适合高密度组装,利于电子产品小型化和薄型化。
b)引线或引线很短,有利于减少寄生电感和电容,改善了高频特性。
c)形状简单、结构牢固,组装可靠性好。
d)尺寸和形状标准化,适合自动化组装,效率高、质量好,利于大批量生产,综合成本低。
5.3表面组装元器件的引脚形式
a)翼形:
能适应薄、小间距的发展、适应各种焊接工艺,但在运输和使用中易使引脚受损。
b)J形:
空间利用系数较大,对焊接工艺的适应性比翼形差,但引脚较硬,在运输和使用
中不易损坏。
c)对接引线:
剪切强度低,对贴装和焊接要求更高。
d)球栅阵列:
属于面阵列封装,引脚不会变形,适合于高引脚数的封装;焊接的适应性较差;并且焊后的可检测性较差。
5.4SMT生产条件对贴片元器件(SMD的要求
a)焊端头或引脚应有良好可焊性;
b)应使用引脚为铜的元器件,以保持良好的导热;
c)应有良好的引脚共面性,一般要求不大于0.1mm特殊情况下可放宽至与引脚厚度相同;
e)元器件的外形尺寸和公差要严格按照规格要求;
f)选用的元件必须能承受215C600秒以上的加热;
g)元件规格:
1005〜32mmx32mm(0.3mm以上脚间距);
i)元件包装:
可以使用8mm12mm和16mm带式,各种管式和盘式送料器。
具体要求详见图1和表1。
CHIP插入孔
表1各种包装结构尺寸要求(单位mm
送料器规格
元件类别
A
B
C
D
E
F
G
H
8mm
带式送料器
1005
0.7±0.1
1.2±0.1
8±0.2
1.75±0.1
①1.5±0.1
4±0.1
2±0.1
2±0.05
1608
1.1±0.2
1.9±0.2
8±0.2
1.75±0.1
①1.5±0.1
4±0.1
4±0.1
2±0.05
2012
1.5±0.2
2.3±0.2
8±0.2
1.75±0.1
①1.5±0.1
4±0.1
4±0.1
2±0.05
3216
1.9±0.2
3.5±0.2
8±0.2
1.75±0.1
①1.5±0.1
4±0.1
4±0.1
2±0.05
3225
2.9±0.2
3.6±0.2
8±0.2
1.75±0.1
①1.5±0.1
4±0.1
4±0.1
2±0.05
12mm
带式送料器
4532
3.6±0.2
4.9±0.2
12±0.2
1.75±0.1
①1.5±0.1
4±0.1
8±0.1
2±0.05
5750
5.4±0.2
6.1±0.2
12±0.2
1.75±0.1
①1.5±0.1
4±0.1
8±0.1
2±0.05
16mm
带式送料器
小型
SOP
16±0.2
1.75±0.1
①1.5±0.1
4±0.1
5.5片状元件称呼方法见表2(我公司应统一使用公制的标称方法)表2元件称呼方法
外形尺寸(单位mn)
公制
英制
日本的习惯称呼方法
长
宽
厚
1.0
0.5
0.35
1005
0402
1.6
0.8
<1.0
1608
0603
1型
2.0
1.25
<1.25
2012
0805
2型
3.2
1.6
<1.45
3216
1206
3型
3.2
2.5
<1.5
3225
1210
4型
4.5
3.2
<2.0
4532
1812
5型
5.7
5.0
<2.0
5750
2220
6型
注:
因部品编号目前已经使用了英制的标称方法,改动比较烦琐,所以部品编号暂时仍采用
英制标称。
6生产工艺流程分类(不包含过程检验)
a)单面贴装工艺
印刷锡膏t贴装t回流焊
b)双面贴装工艺
A面印刷锡膏tA面贴装t回流焊tb面印刷低温锡膏tB面贴装t回流焊
c)面混装工艺(在同一PCB面既有表面贴装元器件又有通孔插装元器件)
印刷锡膏T贴装T回流焊T自动插件T人工插件T波峰焊接
d)面混装工艺
A面自动插件tB面点胶TB面贴装t高温固化TA面人工插件tB面双波峰焊接
e)面贴装+单面插件工艺
A面印刷锡膏tA面贴装t回流焊tA面自动插件tB面点胶tB面贴装t高温固化t
A面人工插件tB面双波峰焊接
注:
如果自插元件较少或有高密度贴片元件,可将自插并入手插并将点胶改为印锡膏工艺。
7锡膏印刷工艺
4
>38
20〜38
<20
注:
优先推荐使用焊料粉末颗粒直径为45卩mi—75卩m和20卩mi-45卩m的锡膏。
725合金含量的重量百分比:
印刷锡膏时,推荐使用金属含量在85%-92%的锡膏。
7.2.6工作寿命:
指锡膏印刷后到进行回流焊接的时间,要求使用工作寿命在4小时以上的锡
膏。
7.2.7储存条件:
以密封形态在4C〜10C的温度下冷藏,存储期限一般为3〜6个月(具体参考锡膏的规格要求)。
注:
如储存温度过高,锡膏中的合金粉末和焊剂产生化学反应,使锡膏的粘度升高,影响其印刷质量;如存储温度过低(低于0C),锡膏中的松香成分会发生结晶现象,在焊接中易岀现焊料球或虚焊等问题。
7.2.8使用要求
a)锡膏从冰箱中取出后必须在室温下回温5小时以上才能开盖使用,以免空气中的水气凝
结混入其中,造成锡膏性能劣化。
注意:
不能使用加热的方法来回温,以防锡膏性能劣
化。
b)锡膏回温后,必须用刮刀等工具充分搅拌30分钟以上(以使锡膏内部颗粒均匀一致并保持良好的粘度)才可以使用。
7.3生产工艺标准
a)锡膏印刷的环境温度应为22C〜26C,湿度要在65%以下。
b)对刮刀的要求:
如刮刀太软会使锡膏凹陷,所以要求使用硬度较高的金属刮刀。
c)舌切的压力:
要同刮刀的压力、倾角和印刷速度以及锡膏的粘度相配合,压力太小会使
印刷板上的锡膏量不足,太大的压力会使锡膏印刷的太薄。
一般应使刮刀的压力正好把钢
网上的锡膏刮干净。
IC引脚间距、钢网开口的尺寸、钢网的厚度以及印刷后锡膏的厚度关系应满足表4的要求。
表4IC引脚间距、钢网开口的尺寸、钢网的厚度以及印刷后锡膏的厚度关系
IC引脚间距(mn)
0.8
0.65
0.5
0.4
开口尺寸(mm
长
2.0〜2.5
2.0〜2.2
1.7〜2.0
1.7
宽
0.4±0.04
0.31±0.02
0.25±0.015
0.2±0.015
钢网厚度(mm
0.2
0.2
0.15
0.15
锡膏厚度(mr)
0.17〜0.2
0.17〜0.2
0.13〜0.15
0.12〜0.15
d)刮刀倾角:
一般为45°〜70°。
e)印刷速度:
一般为15mm/s〜25mm/s,进行高精度印刷时(引脚间距w0.5mm)印刷速度
为20mm/s〜30mm/s。
f)印刷间隙:
印刷钢网与印制板表面的间隙应控制在0〜1.0mm。
g)脱离速度:
钢网与印制板的脱离速度也会对印刷效果产生较大的影响,推荐脱离速度见表5。
'表5推荐脱离速度
引脚间距(mr)
w0.3
0.4〜0.5
0.5〜0.65
>0.65
推荐速度(mm/s)
0.1〜0.5
0.3〜1.0
0.5〜1.0
0.8〜2.0
f)钢网清洗:
在锡膏印刷过程中每印刷5〜10块板,需要对钢网底部清洗一次,以消除钢
网底部的附着物(残留的锡膏),要求使用无水酒精或专用的清洗剂作为清洗液。
7.4工艺检查标准
7.4.1理想的印刷效果
a)锡膏与焊盘对齐;
b)锡膏与焊盘尺寸及形状相符;
c)锡膏表面光滑且不带有受扰区域或空穴。
742检查标准
a)焊盘上单位面积上的锡膏量应为0.8mg/mm2左右,对细间距元器件应为0.5mg/mm2左右;
b)过量的锡膏延伸出焊盘,但锡膏覆盖面积小于焊盘面积的2倍,并且未与相邻焊盘接触;
C)锡膏覆盖每个焊盘的面积要大于75%
d)错位不能大于0.2mm(对于细间距焊盘,错位不得大于0.1mm),且不能与相邻焊盘接触;
e)印刷后应无严重塌陷、拉尖,边缘整齐,基板不许被锡膏污染。
8点胶工艺
8.1设备:
全自动双头高速点胶机
8.1.1对PCB的要求:
厚度0.5mm〜2mm尺寸50mnK50mnrr330mnX360mm
8.1.2对动力的要求:
电源AC100X〜240V、50Hz,压缩空气5kgf/cm。
8.1.3对注射管的要求:
30ml标准注射管。
8.2胶水
8.2.1有合适的粘度,胶水粘度太大时会出现“拉丝”现象,粘度太小时涂覆后不能保持轮廓并形成足够的高度,且会漫流到有待焊接的部位而造成虚焊。
8.2.2应具有一定的绝缘性能,要求在任何的环境条件(主要指长期的潮湿环境)下,其绝缘电阻》10Q/cm。
8.2.3固化后有一定的粘接强度,以确保在波峰焊接时被粘贴的元件不会掉出。
一般要求在室温下,以及经受3次极限焊接周期(260C每次10秒)后均能达到》200gf.cm/mm2。
8.2.4在常温下的存储期限要小于5天,在低温(4C〜10C)下的存储期限不得大于3个月。
8.2.5要具有抗潮和抗腐蚀的能力,应与后续工艺的化学制品相容,不产生化学反应。
8.2.6应有颜色(一般为红色)。
8.2.7使用要求
a)应在低温下储存(4C〜10C);
b)在常温或低温下储存的时间必须在存储期限以内(具体参见胶水的使用说明书);
c)从低温下取出后必须在室温下回温4小时以上才可以上机使用。
8.3生产工艺标准
a)粘贴不同的元件要使用不同的点胶嘴,具体要求见表6。
表6
元件规格
1608
2012
3216
大型晶体管
小型IC
中型IC
胶嘴型号
NEEDLE(1608)
NEEDLE(2012)
NEEDLE(3216)
NEEDLE(TYPED
NEEDLE(TYPE2>
胶嘴内径
0.45mm(双嘴)
0.5mm(双嘴)
0.55mm(双嘴)
0.65mm(单嘴)
0.75mm(单嘴)
确定胶点数量的原则:
大型晶体管和IC常因体积较大而采用一个元件点多个胶点的做法,一
般情况下“TYPE1'两个点的距离为6mm-10mm左右,“TYPE2两个点的距离为10mm-15mm左右。
注1:
密切控制胶滴的高度(点胶量),太高(点胶量太大)容易将胶水压出污染焊盘而造成虚焊,太低(点胶量太小)容易使胶水未能与元件接触或接触面积太小而造成掉件。
注2:
对一些贴装后元件较高的位置要适当的增加点胶量来确保元件上的胶滴的直径符合要求。
b)为了确保涂覆的稳定性,在开始正式地涂覆之前要在两点以上的地方进行预涂。
c)喷嘴的清洁
――每周末要进行定期的清洁;
――一天以上不使用时,要进行清洁;
――当出现吐出状态不稳时,进行检查清洁。
d)从涂覆到贴装的时间不得超过1小时。
e)从涂覆到高温固化的时间不得超过24小时。
8.4工艺检查标准
841理想的点胶效果
a)胶滴居中,不与焊盘和元件电极接触;
b)粘接强度(高温固化后)大于标准30%以上。
8.4.2检验标准
a)焊盘或电极处的胶水均应小于有效焊接面积的1/5;
b)胶水朝向贴片电极的渗漏必须小于电极宽度的1/3;
c)使用双嘴点胶头时,每个单侧胶点必须与贴片部品全部或部分接触,不得完全脱离(不接触);
d)于SOPQFP等封装壳体较大的元件,元件上的胶滴直径应大于基板上的胶滴直径的1/2,同时要求胶水不得粘污引脚或焊盘。
9贴片工艺
9.1设备:
中速贴片机和多功能全视觉激光贴片机
9.1.1对PCB的要求:
厚度0.4mm〜4.2mm,尺寸50mnX30mmr460mnX400mm
9.1.2对动力的要求:
电源AC100X〜240V、50Hz,压缩空气5kgf/cm2。
9.1.3贴片元件及其包装的要求:
参见本文5.4之e、f的要求。
9.2生产工艺标准
9.2.1贴装压力:
对有引线的贴片部品,一般每根引线所承受的压力为10Pa〜40Pa,弓I线应压
入锡膏中的深度至少为引脚厚度的一半;对矩形片状元件,一般压力为450Pa〜1000Pa。
9.2.2贴装时要防止锡膏被挤出,可以通过调整贴装压力和控制印刷锡膏的厚度等方法预防。
对
于普通元件,要求焊盘之外的挤出量(长度)应小于0.2mm,对于细小间距(小于0.8mm)的元器
件,挤出量(长度)应小于0.1mm=
9.2.3视像对中系统(vision)的使用条件:
大于23mnK23mn或脚间距小于0.65mm的IC等圭寸装
壳体较大的元器件的贴装应该使用视像对中系统。
9.2.4各台机的作业时间应尽可能相同(工艺平衡),以保证高的生产效率。
9.2.5吸嘴的规格是根据贴片部品的大小和形态而选择,所以吸嘴选择合适与否将直接影响贴装
质量的好坏,具体要求参见表7。
表7贴片部品与吸嘴对应关系表
吸嘴名
外径
内径
最小部品宽度
适用部件以及主要形式
N045
1.0mm
0.45mm
0.5mm〜2.5mm
1005、1608、2012、SOT(0.8X1.6)等
N08
1.5mm
0.8mm
0.8mm〜3.2mm
1608、2012、3216、MEL(圆柱形贴片元件1.2X2.0)、SOT等
N14
2.7mm
1.4mm
1.6mm〜4.5mm
小型铝电解电容、钽电容、微型电位器等
N24
4.0mm
2.4mm
4.0mm〜7.0mm
中型铝电解电容、SOP(窄的)、SOJ连接器
N40
6.2mm
4.0mm
7.0mm〜10.0mm
大型铝电解电容、SOP(宽的)、QFPPLCCSOJ连
接器等
N75
9.0mm
7.5mm
10mn〜
中型QFP中型PLCC等
N110
12.7mm
11.0mm
20mm-
大型QFP大型PLCC等
9.3工艺检查标准
9.3.1理想贴装效果
a)矩形元件:
元件电极全部位于焊盘上、居中;
b)小外形晶体管:
引脚全部位于焊盘上、对称居中;
c)小外形集成电路及网络电阻:
引脚趾部和跟部全部位于焊盘上,所有引脚对称居中;
d)四边扁平封装器件和超小型封装器件:
引脚与焊盘重叠无偏移。
9.3.2检验标准(见表8)
表8贴装检验标准
元件类型
图示
检验标准
矩形贴片元件
贴片电极与相邻焊盘和相邻贴片电极的距离必须大于0.5mm;
贴片电极与相邻图形的距离应大于0.2mm(包含元件下面的图形)
A
元件电极宽度的一半或一半以上应处于焊盘上
dl
元件电极要有0.3mm以上在焊盘间上;
?
旋转偏差,距离P应大于元件宽度的1/2;
小外形晶体管
允许有偏差和旋转偏差,但各引脚的含趾部和跟部应处于焊盘上,并且确保
引脚的1/2以上在焊盘上
小外形集成电路和网络
电阻
允许有偏差和旋转偏差,但各引脚的跟部和趾部应处于焊盘上,并且确保引
脚宽度的1/2和0.2mm以上在焊盘上。
四边扁平封装和超小型封装器件
r
1
S£
旦eEj
豈蚩
允许有偏差和旋转偏差,但各引脚的跟部和趾部应处于焊盘上,并且确保引
脚宽度的1/2和0.2mm以上在焊盘上。
10回流焊接工艺
10.1设备:
5温区热风回流焊
10.1.1对动力的要求:
电源:
3相380V动力电,27kW压缩空气:
4kgf/cm〜6kgf/cm。
10.1.2对PCB的要求:
宽度50mm-300mm(采用导轨运输方式)。
10.1.3设备主要参数:
温度控制范围:
室温〜350C,升温时间35分钟,各温区温度独立控制,传送网带宽度390mm长度3.8米,内配UPS电源,内配三点温度曲线测试系统和测试导线。
10.2生产工艺标准
10.2.1预热温度控制在120C〜150C,预热时间应大于60秒,温升的速率要小于3C/s(仅供参考,具体参见锡膏的规格书的规定)。
10.2.2焊接温度控制在230C〜240C,时间应为5〜10秒,同样温升的速率要小于3C/s(仅
供参考,具体参见锡膏的规格书的规定)。
10.2.3转产和每天上班前,读取温度曲线,确认满足要求后才可以开始生产。
10.2.4PCB上同一条直线(该直线应与过炉方向垂直)上的各个焊盘温度的差异应小于5C。
10.2.5注意进炉的方向,否则会因为元件的两端焊脚因焊锡溶化和凝结时间的差异而容易形成吊桥(或称曼哈顿现象),即元器件的一端离开焊盘而向上方斜立或直立的现象。
10.3工艺检验标准
10.3.1浸润:
焊料应在被焊金属表面铺展,其接触角必须小于90°;
10.3.2焊料量:
焊料量要适中,避免过多或过少;
10.3.3焊点表面:
应完整、连续和圆滑;
10.3.4不允许有虚焊、脱焊、孔洞、桥接、拉尖、焊料球或吊桥的现象。
11高温固化工艺
11.1设备:
5温区热风回流焊。
11.2生产工艺标准
11.2.1当PCB上有通孔电解电容时,固化温度为120C〜135C(为防止电解电容的爆裂,电解
电容体上的温度不得高于110C),固化时间应大于120秒,温升的速率要小于3C/s(仅供参考,
具体参见胶水的规格书的规定)。
11.2.2当PCB上无通孔电解电容时,固化温度为150C〜170C,固化时间应大于90秒,温升
的速率要小于3C/s(仅供参考,具体参见胶水的规格书的规定)。
11.2.3转产和每天上班前,读取温度曲线,确认满足上述要求后才可以开始生产。
11.2.4同一条直线(该直线应与过炉方向垂直)上的各个焊盘温度的差异应小于5°Co
11.3工艺检验标准
11.3.1粘接强度应满足表9的要求,每次转产时应进行测定并记录。
表9粘接强度力矩要求
元件规格
1005
1608
2012、晶体管
3216、电位器
钽电解、其他大型贴片
力矩要求
>80gf•cm
>120gf•cm
>150gf•cm
>200gf•cm
>250gf•cm
11.3.2外观应呈暗红色。
12清洗
对在维修后有明显助焊剂痕迹的PCB应进行清洗。
方法:
使用植物纤维毛刷(可防止产生静
电)沾无水乙醇进行刷洗,凉干即可。
13防静电要求
因SMT器件属微型元件,对静电更加敏感,在生产过程中要特别注意静电防护。
13.1IC、晶体管必须使用防静电料盒盛放;
13.2在收发材料、贴装、检验、修理等工序凡是可能接触到贴片IC的员工必须佩带防静电手带;
13.3应使用防静电周转架、车或防静电周转箱对已贴装IC的PCB进行存放和运输;
13.4对已贴装IC的PCB进行检验、修理的工作台必须铺防静电垫,并良好接地;
13.5技术、管理等非固定工位人员接触贴片IC或已贴装IC的PCB时,必须戴防静电手套。
13.6检验、修理人员使用的电烙铁必须是恒温烙铁,并