重庆大学数控加工实践报告.docx
《重庆大学数控加工实践报告.docx》由会员分享,可在线阅读,更多相关《重庆大学数控加工实践报告.docx(26页珍藏版)》请在冰豆网上搜索。
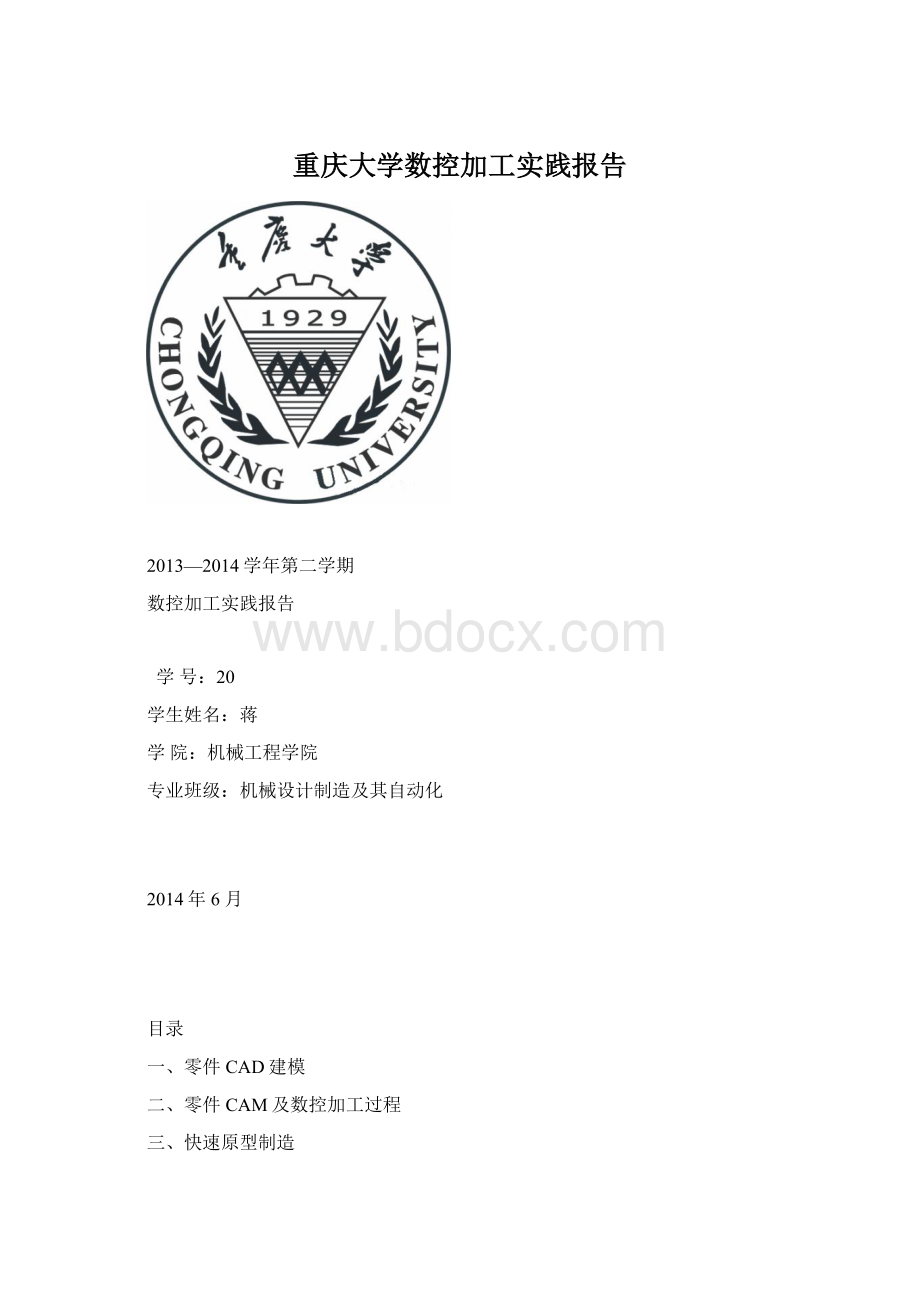
重庆大学数控加工实践报告
2013—2014学年第二学期
数控加工实践报告
学号:
20
学生姓名:
蒋
学院:
机械工程学院
专业班级:
机械设计制造及其自动化
2014年6月
目录
一、零件CAD建模
二、零件CAM及数控加工过程
三、快速原型制造
四、总结
五、科技小论文
一、零件三维CAD建模
1.设定MDT的工作环境
设定其工作环境为“单一零件环境”。
即选择“新零件文件”,就能开始创建一个零件。
2.我创建的零件是压板,三维图如下:
零件分析:
该零件的组成是由一个平板、一个圆孔、一个凸台、一个沟槽组成的。
建模顺序:
第一步采用“拉伸”特征,建立平板:
第二步采用“拉伸”特征,建立平台;
第三步采用“拉伸”特征,建立圆孔;
第四步采用“拉伸”特征,建立凸台;
第五步采用“拉伸”特征,简历沟槽;
第六步倒角;
具体步骤如下:
(1)建立一个三维工作平面
(2)首先建立平板。
故选择一个平面作为草绘平面,进行草绘。
草绘完成后,将草绘图形定义为截面轮廓,进行“添加拉伸”。
(3)在平板的基础上,进行切除。
首先草绘出切除部分图形,并定义为截面轮廓。
然后对该截面轮廓进行“切除拉伸”。
(4)在平板上钻孔。
首先建立孔的截面轮廓图形。
再进行切除拉伸。
(5)创建沟槽特征。
(6)创建凸台特征。
(7)对零件倒圆角。
选择圆角半径为3mm。
以上就是零件的三维实体造型的过程。
二、零件CAM及数控加工过程
1.CAD模型文件输出:
MDT6.0环境下“文件”—>“输出”—>“IGES”—>定义文件名—>保存。
2.用MILL9程序打开IGES文件:
启动MILL9—>MainMenu—>File—>Converters—>IGES—>Readfile—>选择IGES文件—>打开—>进入IGESReadParameters设置界面,确认FileisinMetricunits—>Ok—>按工具栏按钮Screen-Fit—>按工具栏蓝色球按钮(Screen-SurfDisp-Shading)—>出现ShadingSettings页面,选择ShadingActi—>Ok。
删除多余的非Surface构图元素:
MainMenu—>主菜单Delete—>All—>Color—>选择要删除的颜色(通常为绿色)—>Ok—>按工具栏按钮Gview-Isometric—>按工具栏按钮Screen-Fit。
3.根据需要可在MILL9环境下旋转、移动或比例缩放模型。
旋转模型直至零件的主要加工面朝向Z轴的正向,并让零件尺寸最大的方向与X轴一致。
旋转模型步骤如下:
按工具栏按钮Gview-Top或Gview-Front或Gview-side,选择旋转模型的视图平面—>MainMenu—>Xform—>Rotate—>All—>Surfaces—>Done—>Origin—>出现Rotate提示页面,输入旋转角度—>选中Operation的Move,确认NumberofSteps为1—>Ok。
移动模型,直至工件的顶面中心点的坐标为(X0,Y0,Z0)。
移动模型步骤如下:
按工具栏按钮Gview-Top或Gview-Front或Gview-side,改变视图平面—>MainMenu—>Xform—>Translate—>All—>Surfaces—>Done—>Polar—>输入移动距离—>输入移动方向的角度—>出现Translate提示页面,选中Operation的Move,确认NumberofSteps为1—>Ok。
比例缩放模型的目的是让工件尽可能大,但又符合下述注意点④⑤⑥⑦。
比例缩放模型步骤如下:
MainMenu—>Xform—>Scale—>All—>Surfaces—>Done—>Origin—>出现Scale提示页面,选中Operation的Move,选中Scaling的XYZ,确认NumberofSteps为1,输入X、Y、Z三个方向的缩放比例—>Ok。
4.工艺规划。
通常为粗加工、清根、精加工。
因毛坯材料为纤维性材料——木材,要经过两次交叉精加工,才能把木头纤维割断;加工余量不大且木材好加工,不需要清根,因此本次实验安排粗加工、精加工1和精加工2。
5.画粗加工边界
用鼠标点击工具栏上的Cplane-Top和Gview-Top按钮—>MainMenu—>Create—>Rectangle—>1Points—>输入矩形框尺寸为120mm×90mm—>OK—>Origin—>MainMenu—>点击工具栏上的Cplane-3D和Gview-Isometric。
6.设定毛坯
MainMenu—>ToolPaths—>Jobsetup—>输入毛坯长X=120、宽Y=80、高Z=40—>输入毛坯参考点坐标StockOrigin,若设计的的工件顶面中心点为X0Y0XZ0,则可设StockOrigin为X0Y0Z2。
7.MainMenu—>用鼠标点击工具栏上的Cplane-Top—>ToolPaths—>surface—>Rough—>Pocket(挖槽加工方法)—>All—>Surfaces—>Done,出现粗加工参数界面—>在ToolParameters页面中的大空白区点击鼠标右键—>CreateNewTool—>在ToolType页面中选刀具类型为EndMill(立铣刀)—>在Tool–FlatEndMill页面中修改Diameter=10.0、Flute=22.0、Shoulder=22.0和Overall=40。
点击OK按钮,返回ToolParameters页面—>修改Tool#(刀具号)=15、Dia.(刀具半径补偿号)=15、Len.(刀长补偿号)=15、FeedRate=1500、Plunge=150、Retract=5000、Program#(程序号)=1、Spindle=1500、Coolant=OFF
切换到SurfaceParameters页面,根据模型确定Clearance(安全平面高度、Absolute)=20.0、Retract(退刀平面高度、Absolute)=10.0、FeedPlane(进给平面高度、Absolute)=5.0,—>确定精加工余量StocktoLeave=0.2—>切换到RoughPocketParameters页面,修改Totaltolerance=0.1、MaxStepDown=2、Stepover=75、复选Promptforentrypoint和Rough(zigzag)—>按Cutdepths按钮、选择Absolute、修改MinimumDepth(毛坯加工最高点坐标)和MaxmumDepth(工件加工最低点坐标)—>点击OK按钮—>按Gapsettings按钮,复选Optimizecutorder—>点击OK按钮—>确定—>选择第5步画的画粗加工边界—>Done—>选入刀点EndPoint(通常为粗加工边界右侧靠近人的一角)。
8.精加工1
MainMenu—>用鼠标点击工具栏上的Cplane-Top—>ToolPaths—>surface—>Finish—>Parallel—>All—>Surfaces—>Done—>进入精加工参数界面—>在ToolParameters页面中的大空白区点击鼠标右键—>CreateNewTool—>在ToolType页面中选刀具类型为SpherMill(球头铣刀)—>在Tool–SphericalEndMill页面中修改Diameter=6.0、Flute=13.0、Shoulder=13.0和Overall=40.0—>点击OK按钮,返回ToolParameters页面—>修改Tool#(刀具号)=16、Dia.(刀具半径补偿号)=16、Len.(刀长补偿号)=16、FeedRate=2000、Plunge=150、Retract=5000、Program#(程序号)=2、Spindle=2000、Coolant=OFF—>切换到SurfaceParameters页面,根据模型确定Clearance(安全平面高度、Absolute)=20.0、Retract(退刀平面高度、Absolute)=10.0、FeedPlane(进给平面高度、Absolute)=5.0,—>确定精加工余量StocktoLeave=0—>切换到FinishParallelParameter页面,修改StepOver值=0.3、MachineAngle=45—>确定。
9.精加工2
MainMenu—>Toolpaths—>Operations,出现OperationsManager界面,鼠标光标指向第二步SurfaceFinishParallel,右击鼠标—>Copy—>在加工步骤下面空白区右击鼠标—>Paste—>点击刚复制的精加工步骤3中的Parameters—>切换到FinishParallelParameter页面,修改MachineAngle=135—>确定—>RegenPath。
10.仿真
MainMenu—>Toolpaths—>Operations,出现OperationsManager界面,点击SelectAll按钮,点击Verify按钮—>出现仿真界面—>按仿真界面的播放键开始仿真,仿真完成后关闭仿真界面,回到OperationsManager界面。
如果仿真不正确,重新修改参数,重新仿真(要求仿真结果不允许出现过切、欠切、飞刀等异常现象)。
11.生成NC程序
在OperationsManager界面中点击粗加工工步,出现“√”标记—>按Post按钮,选SaveNCFile—>OK—>出现提示回答“否”—>保存NC文件。
复选两个精加工工步,—>按Post按钮,选SaveNCFile—>OK—>出现提示回答“否”—>保存NC文件。
生成NC代码如下:
%
O0001
(PROGRAMNAME-压板)
(DATE=DD-MM-YY-18-06-14TIME=HH:
MM-15:
01)
N100G21
N102G0G17G40G49G80G90
(TOOL-15DIA.OFF.-15LEN.-15DIA.-10.)
N104T15M6
N106G0G90X-60.Y-45.A0.S1500M3
N108G43H15Z20.
N110Z5.
N112G1Z2.F100.
N114X-59.Y-44.F1500.
N116X59.
N118Y-36.667
N120X-59.
N122Y-29.333
N124X59.
N126Y-22.
三、
快速原型制造
1.打开快速成型零件数据准备系统,装入模型。
但是装入我自己生成的STL文件是出现这样的提示。
因此,我只有使用软件本身的一些模型。
如下所示
2.原型零件制作的缩放
3.原型零件制作的定向
该零件的放置方向是比较适合分层处理和加工的,因此不需要对制作模型的方向进行调整。
4.原型零件的校验
通常由CAD系统构造的三维模型转换成STL格式文件,由于CAD软件和STL文件格式本身的问题,以及转换过程中造成的错误,有时难免有少量的缺陷。
故需“模型校验”。
校验结果如下:
再对模型进行修正,选择“模型修补功能”。
5.分层处理
(1)参数设置
我们在进行分层处理时,需要确定分层的厚度,一般将分层厚度确定为0.1mm。
分层时,若分层厚度值越大,则制作的原型零件越粗糙。
(2)模型分层
模型分层是在Z向对原型零件模型进行分层助理,将原型零件分层为众多的水平面。
(3)轮廓编辑
由于各种不同CAD设计系统产生的STL模型文件会有各自的缺陷,STL文件可能会有缺少面片、缝隙等实体不封闭因素,这样可能导致生产的分层文件、二维资料不封闭,使加工的模型出现问题。
为了防止上述问题的产生,数据准备Rppptogram软件还提供了分层后轮廓资料的编辑功能。
点击数据准备Rpprogram软件“轮廓状态检查信息”,如下
发现病态或开口轮廓线,要跳到病态或开口轮廓线所在层,进行轮廓编辑。
将开口轮廓线闭合。
对于病态轮廓线,一般对其梳理。
当开口轮廓中开口较大时,需要扩大允许连接的端点间距才能修复轮廓。
经过轮廓编辑后对罗阔状态检查如下
6.支撑设计
基础支撑是许多十字状支撑呈网络状排列,连接托板与制作的原型零件不封,主要目的是便于制作的原型零件从托板上取下。
人工支撑设计如下:
7.打开快速成型工艺系统控制系统,载入模型。
进入仿真模式,仿真。
四、总结
在用MDT三维建模当中,我认为虽然MDT和PREO是两种不同的三维建模软件,但是最基本的东西都是一样的,首先是建立草绘平面,然后画出封闭图元(PREO是自动识别是否封闭,而MDT是需要认为的去定义截面轮廓),再然后就是在封闭图元的基础上创建各种特征。
在零件的CAM中,基准特征包括基准平面、基准轴、基准点、基准曲线、基准坐标系五种类型,其中每一种类型都是独立的个体,单相互之间具有紧密的联系。
例如,可以利用基准点构建基准曲线、基准轴以及基准平面等特征,而反过来,也可以利用基准曲线、基准平面等特征确定基准点。
基准特征主要用来辅助建立三维模型,在实际设计中合理巧妙的应用基准特征可以使一些复杂的三维零件的建模工作变得直观而简单。
在Mastercam里,对零件的坐标系的更改一定要注意移动的方向问题,也就是控制移动的角度来改变方向,例如90度则是向右移动。
在建立一把刀具的同时就设定刀具的直径、r角、转数,进给率等参数一次性设定好。
以后调用此刀时,就不需要每次都设定转数,进给率了。
在快速原型制造当中,我了解到了它的基本原理——综合利用CAD技术、数控技术、激光加工技术和材料技术实现从零件设计到三维实体原型制造一体化的系统技术。
同时认识到了应用快速原型制造可以从设计和工程的角度出发,可以设计更加复杂的零件。
从制造角度出发,减少设计、加工、检查的工具。
从市场和用户角度出发,减少风险,可实时地根据市场需求低成本地改变产品。
快速原型制造技术的应用及发展趋势
蒋
专业班级:
机自学号:
[摘要]本文主要介绍了快速原型制造技术的应用,并且简要的分析讨论它的发展趋势。
关键词快速原型制造技术应用趋势
1.快速原型制造技术简介
快速原型制造技术,又叫快速成形技术,(简称RP技术)。
RP技术是在现代CAD/CAM技术、激光技术、计算机数控技术、精密伺服驱动技术以及新材料技术的基础上集成发展起来的。
不同种类的快速成型系统因所用成[2] 形材料不同,成形原理和系统特点也各有不同。
但是,其基本原理都是一样的,那就是"分层制造,逐层叠加",类似于数学上的积分过程。
形象地讲,快速成形系统就像是一台"立体打印机"。
2.应用
快速原型制造系统的发展为模具制造、机械加工开辟了一条高效率、低成本的崭新道路。
快速原型制造还可以获得一般切削加工所不能获得的复杂形状。
发达国家正在汽车、航空、电子仪表与家电等领域大力推广该项技术,以取代传统的注塑模、铸模、木模等的设计制造,并取得了明显效果。
这项技术也在向医用机械、人造关节和人造血管,制造、建筑美工设计、工艺品设计制造等行业扩展。
因此,推广这项技术有着广阔的市场。
下面给出了日本行业利用情况:
电子电气62%;航空航天14%;汽车13%;其它11%。
用途统计:
设计检查用43%;短期实用19%;真空注射母模13.5%;仿形加工母模1%;其它13.5%。
2.1设计检查
工业设计越来越多地使用三维CAD模型取代传统的方式,但是,目前设计者只能在显示屏幕上进行检查。
快速原型制造提供了一个理想的方法,帮助验证不能完全用计算机仿真的设计方面。
能够很快地生成设计的原型,并能对其观察、触摸、测量、评估,及设计美学方面或设计配合与装配的检验,使设计人员能够很快修改原设计中存在的错误。
2.2工装模具的制造
对于一些类型的模具,如注塑模具的设计和制造工作周期通常长达数月,这是由于模具加工相当复杂。
要求人们有相当丰富的经验,并在细节上花费大量注意力。
快速原型制造提供了另一种CAD模型与制造间沟通的捷径。
减少了设计反复的次数,使产品性能达到优化要求,使因设计问题变更工装模具在时间和资金上所带来的损失降低到最低限度。
2.3代替传统铸造的木模
人工制造木模不仅效率低,而且精度差,很难适应当前CAD技术的发展。
快速原型制造技术能自动生成精度相当高的铸造模型
2.4.熔模铸造
直接制造金属铸造的陶瓷型芯和壳体,可省掉用于制作石蜡模样的金属模具,此外,由于在烤焙模型的同时树脂型芯也消失了,传统的失蜡工艺也可省略,从而可大大简化熔模铸造工艺,缩短生产周期,降低成本。
据报道,全世界每年传统的熔模铸造大约为50亿美元,如果用快速原型制造技术取代了这项低效、劳动密集型工艺的话,其社会效益和经济效益是相当可观的。
2.5直接制造复合材料零件
直接制造多孔陶瓷预成型件,当用液态金属渗透后,就形成了金属陶瓷复合材料零件。
2.6医学上的应用
医学研究人员使用快速原型制造技术和计算机层析X射线摄影法(CT),比以往更快、更精确地生产假肢及弥补性的手术移植物及人体手术前的手术计划模型。
3.存在的问题
快速原型制造技术是一项崭新的技术,它在许多方面还有待于改进。
3.1系统的价格较高
目前,RP系统的价格均在数10万美元以上,限制了其广泛使用,因此,完善RP系统的工艺,降低成本是普及快速原型制造技术的当务之急。
3.2与CAD系统的接口标准问题
随着快速原型制造系统的激增,很多软件公司都已开发了接口界面,使其三维实体或曲面CAD系统能把模型魄几何数据传输到RP系统中。
通常,大多数遵守3DSystems首创的(sterolithography)STL文件格式,STL文件已成为事实上的工业标准,但传输并不总是顺利的,用户常常依赖于专家的技巧来完成STL文件的转换.STL接口界面一般是与建模的CAD软件一起提供的,各CAD系统提供的STL接口界面在性能上可能有所差别,象STEP标准那样的通用格式仍在研制中。
3.3速度与精度
当前,RP系统制造商的竞争主要集中在生产率和零件精度方面,但这两项指标随着不同的零件几何形状、制造方法以及其他因素的变化而出现很大变化,没有规范化的性能标准。
目前生产的原型精度还达不到某些高精度零件和模型的要求。
3.4建模材料
制约RP技术发展的另一个因素是建模材料。
用于快速原型制造系统的材料是昂贵的,有时是有毒的;而且,还由于其易碎和翘曲的倾向。
未来的材料应具有更好的强度和韧性,较小的收缩率,以及其它所希望的特性。
4.发展趋势
虽然快速原型制造工业仍处在初期阶段,但其前途是非常光明的。
据统计,1991年RP系统的世界市场仅为320万美元。
随着人们对其益处的理解,将会迅速增长。
首先,具有工程特性零件的生产是工业界首要的、长期的目标。
大多数用户不仅仅是希望得到一个塑胶模型,而是希望得到具有他们原来指定材料的真实零件,这需要实现材料的多样化。
对硬度较高的材料进行预热处理,增加激光的功率;增大制造零件的尺寸等;在软件方面寻求能够一致地集成CAD和RP的系统。
总之,在CAD接口界面,建模材料,以及由模型产生工装和模具的生产工艺的改进都将受到欢迎。
参考文献
[1]赵志文,程昌折,韩秀坤,快速原型制造技术及应用,北京理工大学出版社,1994
[2]聂信天,史立新,快速原型技术在机械制造中的发展及应用,南京工业大学出版社,2006
[3]崔焕勇,王守仁,高琦山.快速原型制造技术的发展现状与前景[J].东轻工业学院学报,2003