03蜡油加氢裂化装置.docx
《03蜡油加氢裂化装置.docx》由会员分享,可在线阅读,更多相关《03蜡油加氢裂化装置.docx(56页珍藏版)》请在冰豆网上搜索。
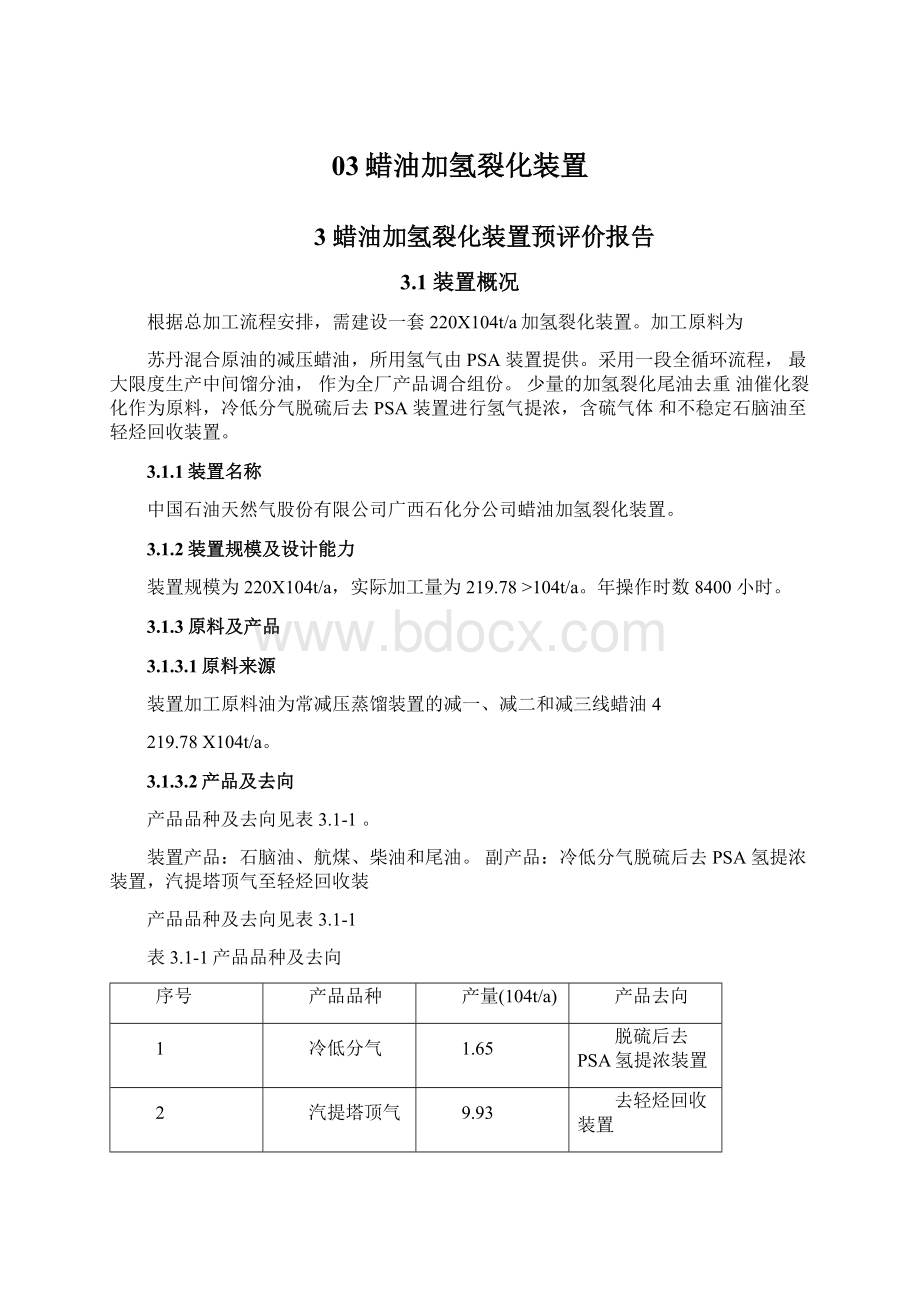
03蜡油加氢裂化装置
3蜡油加氢裂化装置预评价报告
3.1装置概况
根据总加工流程安排,需建设一套220X104t/a加氢裂化装置。
加工原料为
苏丹混合原油的减压蜡油,所用氢气由PSA装置提供。
采用一段全循环流程,最大限度生产中间馏分油,作为全厂产品调合组份。
少量的加氢裂化尾油去重油催化裂化作为原料,冷低分气脱硫后去PSA装置进行氢气提浓,含硫气体和不稳定石脑油至轻烃回收装置。
3.1.1装置名称
中国石油天然气股份有限公司广西石化分公司蜡油加氢裂化装置。
3.1.2装置规模及设计能力
装置规模为220X104t/a,实际加工量为219.78>104t/a。
年操作时数8400小时。
3.1.3原料及产品
3.1.3.1原料来源
装置加工原料油为常减压蒸馏装置的减一、减二和减三线蜡油4
219.78X104t/a。
3.1.3.2产品及去向
产品品种及去向见表3.1-1。
装置产品:
石脑油、航煤、柴油和尾油。
副产品:
冷低分气脱硫后去PSA氢提浓装置,汽提塔顶气至轻烃回收装
产品品种及去向见表3.1-1
表3.1-1产品品种及去向
序号
产品品种
产量(104t/a)
产品去向
1
冷低分气
1.65
脱硫后去PSA氢提浓装置
2
汽提塔顶气
9.93
去轻烃回收装置
3
汽提塔顶液
9.96
去轻烃回收装置
4
分馏塔顶液
54.95
去石脑油加氢分馏部分
5
航煤
31.87
产品出装置
6
柴油
115.38
柴油出装置
7
尾油
1.10
去重油催化裂化装置
3.1.3.3物料平衡
装置物料平衡见表3.1-2。
表3.1-2装置物料平衡
序号
物料名称
数值
W%
kg/h
4
10t/a
-一-
原料
1
减压蜡油
100.00
261643
219.78
2
氢气
2.52
6593
5.54
合计
102.52
268236
225.32
-二二
产品
1
H2S
0.02
52
0.04
2
冷低分气
0.75
1962
1.65
3
汽提塔顶气
4.52
11826
9.93
4
汽提塔顶液
4.53
11852
9.96
5
分馏塔顶液
25.00
65411
54.95
6
航煤
14.50
37938
31.87
7
柴油
52.50
137363
115.38
8
尾油
0.50
1308
1.10
9
损失
0.20
523
0.44
10
合计
102.52
268236
225.32
3.1.4公用工程消耗
3.1.4.1水用量
水用量见表3.1-3
表3.1-3装置给排水用量表
用水地点
给水
t/h
排水
t/h
新鲜水
除氧水
除盐水
净化水
循环水
含油污水
含盐污水
含硫污水
循环热水
生活污水
水冷却器
900
900
机泵冷却
25
5
20
配制药剂
反应产物注水
11
11
22
I.OMPa蒸汽
48
汽提蒸汽
5
6
生活用水
1*
1
合计
1
48
11
11
925
10
28
920
1
注:
*表示间断用量。
3.1.4.2电用量
电用量见表3.1-4
表3.1-4电用量
序号
电压V
轴功率kW
备注
1
6000V
12750
2
380V
2100
3
220V
150
合计
15000
3.1.4.3蒸汽用量
装置蒸汽用量见表3.1-5
表3.1-5蒸汽用量
蒸汽负荷(t/h)
0.4MPa
1.0MPa
3.5MPa
汽包产
汽
用汽
汽包
产汽
背压
产汽
装置
注汽
加热
用汽
汽包
产汽
汽机
用汽
装置
注汽
加热
用汽
-17
6
-28
-71
5
71
3.1.4.4燃料用量
燃料用量见表3.1-6
表3.1-6燃料用量
序号
使用地点
燃料油kg/h
燃料气kg/h
备注
1
循环氢加热炉
1176
(热值41.868MJ/kg)
2
分馏塔进料加热炉
4023
合计
5199
3.1.4.5压缩空气用量
压缩空气用量见表3.1-7
表3.1-7装置压缩空气用量
3.1.4.6氮气用量
装置氮气用量见表
3.1-8。
序号
项目
压力
MPa(g)
连续Nm3/min
间断Nm3/min
正常
最大
正常
最大
1
净化压缩空气
0.6
6
2
非净化压缩空气
0.6
20
合计
6
20
表3.1-8氮气用量
用气参数
连续,
Nm3/h
间断,Nm3/h
压力MPa
温度C
正常
最大
正常
最大
180
40000开工一次用量
3.1.5装置的平面布置
占地面积:
180X90=16200m2。
压缩机厂房分两层布置,房内设置桥式吊车。
装置的所有管桥及构架均采用钢结构。
装置内留有足够的吊装检修用场地,以满足大型吊车接近与回旋。
反应构架上方设置单轨电动吊车与手动葫芦,大型泵的上方设置有检修用
手动葫芦或检修吊梁,以方便检修与维护。
管桥成组合式布置,仪表电缆、电气电缆拟以槽盒的形式布置在管桥最上
层,便于检修和维护,同时节省地下空间,所有设备与建、构筑物均沿管桥两侧布置;管桥下设置泵房。
重油泵布置在泵房内,其它轻油泵布置在装置的管带下。
3.2工艺流程、设备
3.2.1工艺流程
3.2.1.1工艺方案的选择
(1)工艺技术方案的选择
本项目采用单段全循环工艺流程。
加氢精制催化剂和加氢裂化催化剂分别采用UOP开发的UF-210star和HC-115或其它性能相当的催化剂。
(2)工艺流程方案的选择根据本装置反应器等大型设备的规格尺寸以及设备的制造、运输情况,装置的反应部分可采用单系列。
但由于高压换热器采用单系列设备壳径大,为便于制造和检修,高压换热部分拟采用两路并联。
本装置采用热高压分离流程。
本装置规模较大,加热炉需按多路并联设计,且由于加氢裂化反应所需氢油比较大,采用炉后混油流程,反应加热炉只加热氢气,可避免反应加热炉加热二相介质分配不均匀等问题,因此,本装置选用炉后混油流程,加热炉只加热氢气。
本装置采用热高分流程,热高分温度较高,导致溶解氢损失较大,根据工艺计算结果,装置中冷低分气体氢纯度较高,数量较大,应加以利用,以提高氢气利用率。
结合全厂用氢系统的实际情况推荐采用变压吸附对冷低压分离器的富氢气体进行提浓,然后送入氢气管网。
原料油进装置后,首先经自动反冲洗过滤处理,除去大于25微米的颗粒状杂质,防止其沉积在催化剂表面,以减缓反应器压力降的增加,延长装置开工周期。
装置内原料油缓冲罐采用惰性气体保护,避免原料油与空气接触,以减轻原料油在换热器、加热炉管及反应器中的结焦程度。
分馏部分采用先汽提后分馏的四塔流程。
装置内设有冷低分气脱硫设施。
原料油换热系统采用注阻垢剂设施。
航煤出装置线均匀加入抗氧剂。
采用循环氢聚结除液设施。
催化剂采用器外再生。
为确保催化剂、高压设备及操作人员的安全,设置两个压力等级的紧急泄压系统。
3.2.1.2工艺流程
(1)反应部分
原料油与柴油换热后通过原料油自动反冲洗过滤器除去大于25ym的固体
颗粒,进入原料油缓冲罐,经反应进料泵升压后与反应流出物换热,再与经过换热和加热的循环氢混合,然后进入加氢反应器进行加氢精制、加氢裂化反应。
反应流出物与原料油、循环氢换热至适宜温度进入热高压分离器。
反应流出物在热高压分离器进行气、液分离,热高分气体与冷低分油换热、冷却后进入冷高压分离器进行油、水、气三相分离。
冷高分气经循环氢压缩机入口分液罐去循环氢压缩机升压;冷高分水至酸性水汽提装置统一处理;冷高分油至冷低压分离器进一步闪蒸,冷低分气去脱硫塔;冷低分水与冷高分水一起至酸性水汽提装置统一处理。
冷低分油与热高分气换热后至分馏部分。
热高分油至热低压分离器进一步闪蒸,热低压分离器气相与热水换热,并冷却后至冷低压分离器。
热低压分离器液体直接至分馏部分。
新氢经新氢压缩机升压后与循环氢压缩机来的循环氢混合,一路用作混合
氢气,另一路用作反应器的急冷氢。
参见附图3-1。
(2)分馏部分
来自反应部分的低分油进汽提塔,塔底通入水蒸汽汽提,脱除H2S。
塔顶
气相经空冷器、后冷器冷凝冷却后进汽提塔顶回流罐进行油、气、水三相分离,气体去轻烃回收装置进一步回收液化气;含硫污水去酸性水汽提装置统一处
理;塔顶油相一部分送回塔顶作为回流,另一部分送至石脑油加氢精制装置。
汽提塔底油作为主分馏塔进料
汽提塔底油经与工艺物流换热、分馏塔进料加热炉加热后进入主分馏塔。
主分馏塔塔顶气相经冷凝冷却后进入回流罐,液相经塔顶回流泵升压后一部分
作为塔顶回流,另一部分去轻烃回收装置;主分馏塔设侧线航煤汽提塔和侧线
柴油汽提塔生产航煤及柴油产品;塔底油循环回反应部分,一部分经换热、冷却后出装置,另一部分约0.5%(对原料)的未转化油去重油催化裂化装置。
参见附图3-2〜3-3。
(3)低分气脱硫部分
装置设置冷低分气(富氢气体)脱硫塔,自冷低压分离器来的富氢气体与柴油加氢精制装置来的低分气一起经脱硫后,送至PSA装置进行氢提浓,提浓
氢送入全厂氢气管网,供其它装置使用。
参见附图3-4。
3.2.1.3主要操作条件
加氢裂化部分的主要操作条件见表3.2-10
分馏部分及低分气脱硫部分的主要操作条件见表3.2-2o
表3.2-1主要操作条件
项目
操作条件
精制段
裂化段
后精制段
催化剂
UF-210stars
HC-115
UF-310
体积空速,h-1(对新鲜进料)
1.61
0.72
15
工艺流程
单段全循环
工艺条件
混合进料比
1.7
高压分离器压力,MPa
15.2
反应器入口氢油比
713:
1
反应温度,C
精制段:
初期375,末期420;裂化段:
初期397,末期428;
表3.2-2主要操作条件
名称
塔顶温度,C
塔顶压力,MPa(G)
汽提塔
159
1.05
分馏塔
131
0.115
航煤汽提塔
204
0.13
柴油汽提塔
320
0.136
低分气脱硫塔
40
0.8
3・2・2工艺设备
3.2.2.1主要工艺设备选择
(1)容器
热高压分离器为热壁锻焊结构,主体材料选用SA336F22(2.25Cr-1Mo),内
壁堆焊TP.309L+TP.347,按应力分析法进行设计。
冷高压分离器等高压容器均为锻焊结构,采用常规设计。
主体材料选用16Mn(R-HIC)纯净钢。
(2)反应器
本装置反应器采用单系列,分别设有加氢精制反应器、加氢裂化反应器各
一台,采用热壁锻焊结构。
主体材质根据操作条件和Nelson曲线,确定为
2.25Cr-1Mo-0.25V(SA336F22V),内壁堆焊TP.309L+TP.347,以防止高温H2S-H2腐蚀。
反应器按应力分析法进行设计,反应器采用国产或进口,应根据项目工期要求及当时国内外市场的供货情况来确定。
(3)加热炉
循环氢加热炉循环氢加热炉管内介质为富氢气体,操作出口温度470°C,
操作出口压力为16.4MPa,在炉管内介质为富氢气体,出口操作温度、操作压力较高条件下,炉管材质采用TP347H。
当管壁设计温度超过550C时,考虑
采用Incoloy800。
循环氢加热炉设计负荷15200kW,考虑采用单排双面辐射管结构型式。
采用立管型结构,优点:
排管灵活,管系合金钢支撑部件用量少。
根据炉子的工艺特点,初步选用①152管径8管程,最小壁厚16mm
由于受循环氢压缩机出口压力的限制,要求尽量减少炉管压降,加氢反应进料加热炉均设计为纯辐射立式炉型,其排出的高温烟气进入分馏塔进料加热炉对流室,回收烟气余热。
炉膛用一个单排双面辐射辐射室或两个单排双面辐射室。
(4)分馏塔进料加热炉
分馏塔进料加热炉管内介质为含氢量较低,操作出口温度377C,操作出
口压力为0.2MPa,在此工艺条件下,炉管材质采用T9。
分馏塔进料加热炉设计负荷52000kW,考虑采用立管单排单面辐射管结构型式。
根据炉子的工艺特点,初步选用①168管径4管程。
分馏塔进料加热炉采用立管立式炉,循环氢加热炉排出的高温烟气进入分馏塔进料加热炉对流室,回收烟气余热。
(5)冷换设备
本装置高压换热器的管程、壳程均属高压的有10台,管程高压、壳程低压
的有4台。
根据操作条件,管、壳程壳体的主体材料分别选用2.25Cr-1Mo,换
热管材料选用oCr18Ni10Ti。
管程采用螺纹锁紧环式结构。
本装置高压空冷器管箱为板焊丝堵式结构。
根据操作条件,管箱材料采用
碳钢,换热管材料为碳钢。
为防止NH3(H2S)的腐蚀,在每根换热管的入口端设置一段不小于600mm长的不锈钢衬管。
(6)压缩机压缩机是装置中关键机械设备。
新氢压缩机选用往复式,开二备一,为保证装置长周期稳定运行,考虑新氢压缩机由国外引进;循环氢压缩机选用背压式蒸汽透平驱动离心式压缩机一台,由国内生产。
(7)机泵
原料油泵由于介质包括新鲜进料和循环油,且温度较高、流量大、扬程高,所以应选用双壳体多级离心泵。
鉴于国内大泵的制造技术与国外相比还存在一定差距,为保证装置长周期运转,本可研推荐引进反应进料泵。
(8)设备防腐措施
加氢裂化装置中,通常见到的腐蚀现象有氢腐蚀和硫化氢腐蚀,在许多设
备及管道中则存在着这两种介质的同时腐蚀。
在高温高压下,氢对钢有强烈的
脆化作用,腐蚀的程度取决于操作温度、氢分压及合金元素的添加情况;硫化氢的腐蚀程度主要取决于硫化氢的浓度和操作温度。
浓度越大腐蚀越厉害。
对
于温度来说,200〜250C以下不含水的硫化氢气体,对钢铁不产生腐蚀或腐蚀
甚微。
当温度大于260C时,腐蚀加快。
装置设备设计按API941《临氢作业用
钢防止脱碳和开裂的操作极限》曲线(Nelson曲线)选用相应的材料;凡有高温
H2S+H2腐蚀的部位,材料的腐蚀率按照柯珀(Couper)曲线进行估算,采用内
壁堆焊309L+347L等相应的防腐措施;在湿硫化氢应力腐蚀和氢致开裂环境下工作的设备,其主体材质采用16MnR(R-HIC)或16Mn(R-HIC)纯净钢。
3・2・2・2重要工艺设备
(1)主要静设备
主要静设备汇总见表3.2-3。
表3.2-3主要静设备汇总表
序号
名称
规格
数量
重量⑴
材质
-一-
反应器类
1
加氢反应器
04800X34500
(内经X切线长)
1
1321
2.25Cr-1Mo-0.25V内壁堆焊
TP.309L+TP.347
-二二
塔类
4座
1
汽提塔
1座
93
16Mn+OCr13
2
分馏塔
1座
135
16Mn+OCr13
三
加热炉类
1
循环氢加热炉
立式炉,15200kW
1座
炉管材质为TP347H
2
分馏塔进料加热炉
立式炉,52000kW
1座
炉管材质为T9
四
冷换类
1
管壳式冷换设备
39台
2
空冷器
33片
五
容器类
30台
六
其它
10台
(2)主要动设备
主要动设备汇总见表3.2-4
表3.2-4主要动设备汇总
序号
设备名称
规格
数量
介质名称
流量
3
Nm/h
操作压力
MPa(G)
轴功率
电机功率
备
注
入口
出口
kW
kW
1
压缩机
1)
新氢压缩机
电动往复式
3
新氢
55470
2.1
17.0
4900
二开-
-备
2)
循环氢压缩机
离心式
1
循环氢
518500
15.2
17.0
4000
2
泵
50
1)
反应进料泵
双壳体多级离心式
2
蜡油
627
4051
⑶引进设备
引进设备见表3.2-5
表3.2-5进口设备表
序号
名称
规格
材料
台数
备注
1
反应器
1
台
2
新氢压缩机组
2
套
3
反应进料泵
2
台
4
反应加热炉炉管
V
5
部分高压临氢阀门、管道及配件
V
6
高压多点柔性热电偶
6
台
7
调节阀/气缸式切断阀
90
套
8
氧化锆氧含量分析仪
2
套
9
在线氢浓度分析仪
4
套
10
在线微量氧分析仪
2
套
11
便携式露点分析仪
1
套
12
在线闪点分析仪
1
套
13
在线密度分析仪
1
套
3.2.3主要自控方案
1)工艺装置对自动控制的要求
要求主要工艺参数在控制室内集中指示、记录、调节,参数越限时声光报警;不需要经常观察的参数,只设就地检测仪表。
为防止恶性事故发生,避免人身伤害、重要设备损坏或环境污染,根据要求设置安全联锁保护系统。
在可能泄漏可燃或有毒气体的场所,分别设置可燃、有毒气体浓度检测器。
浓度超限时在控制室和现场声光报警。
2)主要控制方案原料罐压力分程控制:
分别控制补气阀门和排气阀门。
加热炉出口温度控制:
出口温度与炉膛温度串级控制燃料量。
高压分离器液位控制非常重要,因此设置多重液位检测手段。
分别设置不同原理的仪表,如差压变送器、浮筒液位变送器、浮筒液位开关,在液位低限时联锁切断液位控制阀,防止向低分串压。
所有机泵状态均通过通讯接口接入DCS显示。
工艺过程及压缩机组设联锁保护,由SIS完成。
3.3预评价单元划分及安全预评价方法
本次预评价根据本项目评价范围和重点,按照便于评价、有利于提高评价准确性的原则,以本项目生产工艺、工艺装置、物料的特点和特征与危险、有害因素的类别、分布有机结合,在对各装置主要危险、有害因素的分析的基础上,同时考虑到装置的工艺特征、工艺设备布局来进行本项目各装置预评价单元的划分。
3.3.1评价单元划分
本次评价依据各装置的工艺特征、设备平面布局及装置主要危险、有害因素,参照单元划分原则,将本装置划分为以下预评价单元,结果见表3.3-1。
表3.3-1装置预评价单元划分
装置名称
序号
预评价单元
主要设备
蜡油加氢裂化装置
P1
反应单元
加氢反应器、热咼压分离器等
P2
分离单元
高压分离器和低压分离器等
P3
分馏单元
汽提塔、主分馏塔等
P4
脱硫单元
低分气脱硫塔等
P5
加热炉单元
循环氢加热炉等
P6
压缩机单元
新氢压缩机、循环氢压缩机等
P7
辅助设施
油泵,管线等
3・3・2预评价方法
(1)首先采用危险度评价法”初步定性分析,确定单元危险等级。
(2)对蜡油加氢裂化装置中经危险度分析方法评价出的危险等级高的单
元(指危险度为I、U级的单元)采用道化学公司(DOW)火灾、爆炸危险指数评
价法”。
(3)对不便进行定量评价的单元采用预先危险性分析法”(PHA)。
3.4危险、有害因素分析
本装置包括反应、分馏、低分气脱硫等三部分和与之配套的公用工程设施。
为便于分析,下面首先进行本项目的危险化学品识别和物质危险、危害性分析,
然后进行各部分的工艺、设备危险因素分析,最后对其它方面的危险、有害因素进行分析。
3.4.1火灾爆炸危险因素分析
3.4.1.1危险化学品识别
根据《危险化学品名录》(2002年版),本部分工艺过程涉及的属于危险化学品的物质包括:
石脑油、氢气、煤油、轻烃(其成分主要为液化气)、燃料气
(主要成分为甲烷)、硫化氢、氮气等。
以上危险化学品的火灾危险性类别及危险货物编号列于表3.4-1中。
表3.4-1危险化学品名称及类别
物质名称
危险化学品类别
危险货物编号
UN号
石脑油
第3.2类中闪点易燃液体
32004
1256,2553
氢气(压缩的)
第2.1类压缩易燃气体
21001
1049
轻烃(液化气)
第2.1类压缩易燃气体
21052
1071
燃料气
第2.1类压缩易燃气体
21007
1971
硫化氢[压缩的]
第2.1类压缩易燃气体
21006
1053
氮气
第2.2类不燃气体
22005
1066
3・4・1・2物质的危险性分析
由工艺流程可知,本装置原料为蜡油,辅助材料有氢气、燃料气等,产品有轻石脑油、重石脑油、煤油、柴油、烃类气体和硫化氢等,都具有不同的火灾、爆炸危险性或腐蚀有毒等特性,此类物质一旦发生泄漏,就可能酿成火灾或爆炸事故。
主要物料的易燃、易爆危险特性分述如下:
⑴蜡油
根据《石油化工企业设计防火规范》(GB50160-92,1999年版)的规定,
蜡油的火灾危险类别为丙b类,遇明火、高热或与氧化剂接触,有引起燃烧爆
炸的危险。
灭火方法:
雾状水、二氧化碳、干粉、泡沫、砂土。
(2)氢气
根据《石油化工企业设计防火规范》(GB50160-92,1999年版)的规定,
氢气的火灾危险类别为甲类。
氢气与空气混合物的爆炸极限为4.1%-74.1%(体
积比),爆炸浓度范围较宽,而且当其浓度达到18.3%〜59%时还会发生爆轰。
故生产过程中,一旦发生泄漏,遇火星或静电火花极易发生燃爆事故。
氢气最小引燃能量为0.02mJ,弓I燃能量相对较低。
另外,氢气比空气轻,在室内使用和储存时,若发生泄漏不能及时排出,会滞留在屋顶,遇火星、电火花等点火源会引起爆炸。
灭火方法:
切断气源。
若不能立即切断气源,