搭板级进模设计说明书DOC.docx
《搭板级进模设计说明书DOC.docx》由会员分享,可在线阅读,更多相关《搭板级进模设计说明书DOC.docx(14页珍藏版)》请在冰豆网上搜索。
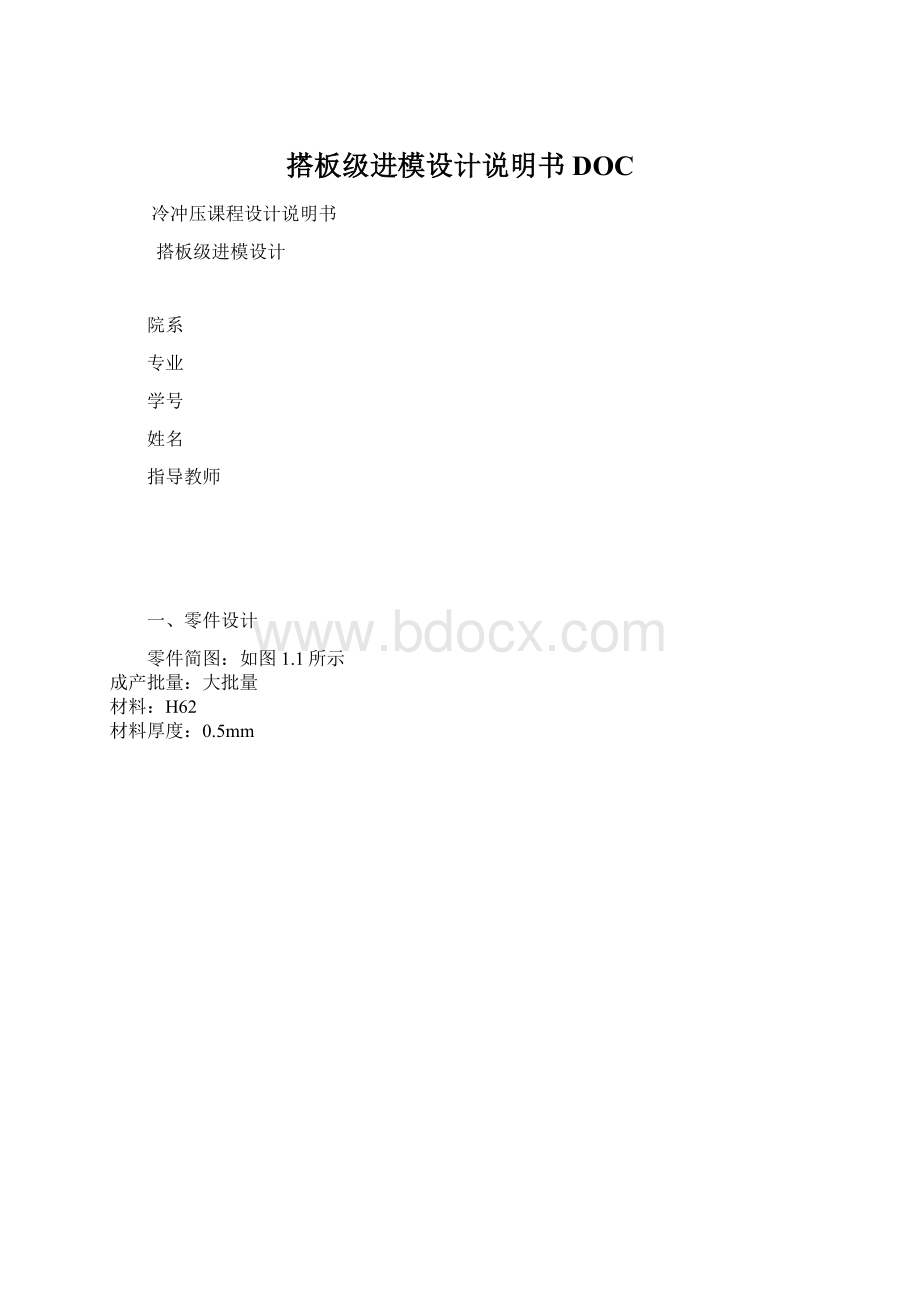
搭板级进模设计说明书DOC
冷冲压课程设计说明书
搭板级进模设计
院系
专业
学号
姓名
指导教师
一、零件设计
零件简图:
如图1.1所示
成产批量:
大批量
材料:
H62
材料厚度:
0.5mm
图1.1零件简图
二、冲压件的工艺分析
2.1、结构分析
该零件形状简单,只有冲孔和落料工序,孔径中等偏小。
2.2、材料分析
材料为H62,其主要性能为:
σs=196Mpa,σb=373Mpa,延伸率δ=20%,塑性良好,因此,此零件用冲裁模生产,采用普通冲裁工艺完全可以。
三、确定冲裁工艺方案
零件为一落料冲孔件,可提出的加工方案如下:
方案一:
先落料,后冲孔。
采用两套单工序模生产。
方案二:
落料—冲孔复合冲压,采用复合模生产。
方案三:
冲孔—落料连续冲压,采用级进模生产。
方案一模具结构简单,但需两道工序、两副模具,生产效率低,零件精度较差,在生产批量较大的情况下不适用。
方案二结构太复杂,尤其一模两件的方案二,制造成本高。
同时生产时模具上的废料和产品的清理也麻烦,再者,零件的位置精度并不高,没必要采用方案二。
方案三也只需一副模具,模具也不复杂。
生产效率高且宜实现自动化生产。
所以,比较三个方案欲采用方案三生产。
四、模具结构形式的选择
4.1模具的类型的选择
根据零件的冲裁工艺方案,采用级进模。
4.2送料与定位方式
零件属于大批量生产,采用自动送料方式。
采用导料板和固定挡料销
五、冲压工艺计算:
2.1.2排样及工艺计算
2.1.2.1排样
零件形状简单、对称,可以采用单排、交叉双排或对称双排;
如图:
考虑到材料利用率,模具大小、复杂程度、造价,以及零件为大批量生产,所以本设计决定采用双排结构。
如图所示:
图2.1排样图
2.1.2.2搭边
查参课本75页表3-25,确定搭边值
,
。
当t=0.5mm时,a=1.8,b=1.5
但由于此表中数值只用于低碳钢,对于其他材料,应将表中数值乘以下列系数:
1.2所以a=1.8x1.2=2.16,b=1.5x1.2=1.8。
但经调整后,取a=2.2,b=2.2。
2.1.2.3条料宽度
B=L+2a=72.2+2*2.2=76.6mm
2.1.2.4材料利用率η
式中
—一个歩距内冲裁件数目;A——冲裁件面积(包括内形结构废料);
S——歩距长度;B——板料宽度;
取:
n=2;A=524;S=22.2;B=76.6
η=2*524/22.2*76.6=61.63%
2.2冲压力及压力中心的计算(课本64页)
2.2.1计算冲压力
2.2.1.1冲裁力
冲裁力公式为F=F孔+F落
式中F—冲裁力;
F孔—冲孔冲裁力;
F落—落料冲裁力。
2.2.1.2冲孔冲裁力F孔
F孔=nKL孔tτ
式中K—系数(取K=1.3);
—孔的个数,n=6。
—冲孔周长,L孔=πx4.2+47.82+44.4+πx1.5=110.12mm
—材料厚度,t=0.5mm
—材料抗剪强度,查参考资料,得τ=294MPa。
F孔=nKL孔tτ=6x1.3x110.12x0.5x294=126.26KN
2.2.1.3落料冲裁力F落。
F落=KL落tτ
L落=πL周长=πx184.4mm=579mm
F落=KL落tτ=1.3x579x0.5x294=110.65KN
所以冲裁力F=F孔+F落=126.26KN+110.65KN=236.91KN
2.2.1.4卸料力F卸
F卸=K卸F
K卸—卸料系数,查课本表3-17知K卸=0.045~0.055,
取K卸==0.05
所以F卸=0.05X110.65=5.53KN
2.2.1.5推料力F推
F推=nK推F
式中K推—推料系数,查课本表3-17取,K推==0.063。
—同时卡在凹模洞孔内的件数,n=10。
所以F推=10X0.063X126.26=79.54KN
2.2.1.6顶件力F顶
F顶=K顶(F孔+F落)
式中K顶—顶件系数,查课本表3-17取K顶=0.08。
所以F顶=0.08x236.91=18.95KN
2.2.1.7总冲压力F总
冲裁时,压力机的压力值必须大于或等于冲裁各工艺力的总和,即大于总的冲压力。
总的冲压力根据模具结构不同计算公式不同,当采用弹压卸料装置和下出件的模具时,总的冲压力为
F总=F+F卸+F推=236.91+5.53+79.54=321.98KN
选用压力机(书本324页)
初选压力机:
J23-16。
根据总冲压力为321.98KN,采用开式双柱可倾压力机,
公称压力:
350KN
滑块行程:
80mm
最大闭合高度:
280mm
闭合高度调节量:
60mm
滑块行程次数/(次/min):
50
滑块中心线到床身距离:
205mm
工作台尺寸:
380mmx610mm
垫板厚度:
60mmx150mm
模柄孔尺寸:
Φ50mmx70mm
床身最大可倾角:
20°
2.2.2计算模具压力中心(课本67页)
压力中心计算如下:
编号
冲载线长度
压力中心到Y轴距离x
压力中心到X轴距离x
1
46.2
0
0
2
8.2
2.05
0
3
26
4.1
0
4
23.6
10
0
5
26
15.9
0
6
8.2
17.95
0
7
46.2
20
0
8
26.376
32.2
0
9
8.2
27.2
0
10
31.4
32.2
0
11
8.2
37.2
0
12
2.2
44.4
0
13
20
54.4
0
14
2.2
64.4
0
15
9.42
63.65
0
汇总
Yc=0
Xc=21.065
2.3凸模凹模凸凹模刃口及结构尺寸计算(课本57页)
2.3.1计算模具刃口尺寸及公差
(1)将零件图尺寸全部按入体原则标注,未注公差按IT12查取,查表3-2,得间隙Zmin=0.025mm,Zmax=0.035mm.Zmax-Zmin=0.01mm.
(2)φ4.2mm冲孔。
查表3-7,得凸、凹模制造公差为δp=0.020mm,δd=0.020mm.δp+δd=0.040mm,不满足δp+δd≤Zmax—Zmin的凸、凹模分别制造条件,但由于相差不大,故采用分别制造方式,制造公差作如下调整:
δd=0.6(Zmax—Zmin)=0.6X0.01=0.006mm
δp=0.4(Zmax—Zmin)=0.4X0.01=0.004mm
查表3-6得磨损系数X=0.75,则凸、凹模刃口尺寸计算如下:
dp=(dmin+X△)0-δp=(4.2+0.75x0.08)0-0.004=4.260-0.004mm.
dd=(dp+Zmin)+δd=(4.26+0.025)+0.0060=4.285+0.0060mm.
(3)外轮廓落料。
虽然落料形状不规则,但并不十分复杂,尺寸中等,凸、凹模刃口均可采用线切割加工(凸、凹模可为直通式)。
落料刃口尺寸计算
制件尺寸
制件公差△
刃口磨损凹模尺寸变化
刃口磨损系数X
刃口尺寸公差
刃口尺寸计算
11.90-0.2
0.2
变大
凹模:
A1d=(11.9-X△)+δd0=11.75+0.0060
凸模:
A1p=(11.75-Zmin)0-δp=11.7250-0.004
200-0.26
0.26
变大
0.75
凹模:
A2d=(20-X△)+δd0=19.805+0.0060
凸模:
A2p=(19.805-Zmin)0-δp=19.780-0.004
350-0.03
0.03
变大
δp=0.004
凹模:
A3d=(35-X△)+δd0=34.97+0.0060
凸模:
A3p=(34.97-Zmin)0-δp=34.9450-0.004
R5+0.120
0.12
变小
δd=0.006
凹模:
A4d=R(5-X△)+1/2δd0=R4.88+0.0030
凸模:
A4p=R(4.88-1/2Zmin)0-1/2δp=R4.8680-0.002
10+0.160
0.16
变小
1
凹模:
A5d=(10-X△)+δd0=9.84+0.0060
凸模:
A5p=(9.84-Zmin)0-δp=9.8150-0.004
8+0.150
0.15
变小
凹模:
A6d=(8-X△)+δd0=7.85+0.0060
凸模:
A6p=(7.85-Zmin)0-δp=7.8250-0.004
13.070-0.14
0.14
不变
凹模:
A7d=(13.07-X△)+δd0=12.93+0.0060
凸模:
A7p=(12.93-Zmin)0-δp=12.9050-0.004
中心距
26+0.12
0.24
不变
0.75
δc=0.006
CA=CT=C+1/2δc=26+0.003
六、主要零部件设计
6.1、落料凹模(课本99页)
由表3-33查得凹模厚度系数k=0.3
凹模高度H=KS2=0.3x72.2=21.66mm≈22mm(≥15mm)
凹模壁厚C=(1.5~2)H=32.49mm~43.32mm取C=35mm
凹模总长L=64.4+2x35=134.4mm
凹模宽度B=72.2+2x35=142.2mm
按冲压模标准模架,选用滑动导向中间导柱模架
由参考资料取凹模周界尺寸
LxBxH=160mmx160mmx22mm
凹模周界|L:
160
凹模周界|B:
160
外形尺寸|L1:
315
外形尺寸|B1:
160
闭合高度H|min:
165
闭合高度H|max:
200
凹模零件简图如图7.1
图6.1凹模简图
6.2、卸料装置的设计
根据要求采用弹性卸料板
6.2.1、卸料板设计
由资料查得卸料板厚度为15mm
取外形尺寸为160mmx160mmx15mm
6.2.2、弹性元件设计
弹性元件采用弹簧,相关选择(简明冲模设计手册)和计算(121页)如下:
1)、初定弹簧数为4,每个弹簧所分担的卸料力为:
Fx/4=5530/4=1382.5(N)。
2)、根据预压力和模具结构尺寸,选外形为弹簧中径:
D=10mm;材料直径:
d=1mm;自由高度:
H0=30mm;的圆柱螺旋压缩弹簧,最大压缩量△H2=17.2mm。
6.3、凸模固定板的设计(课本126页)
厚度h=(60%~80%)H凹=(60%~80%)x22=13.2mm~17.6mm
取h=15mm外形尺寸为160mmx160mmx15mm
凸模与凸模固定板的配合为H7/n6
6.4、垫板设计(课本126页)
厚度h一般为5~10mm,取9mm
外形尺寸为160mmx160mmx9mm
6.5、凸模设计(课本95页)
凸模长度L=凸模固定板厚度+卸料板厚度+卸料元件被压缩后的高度
L=15+15+20=50mm
凸模结构简图如图6.2
图6.2凸模简图
七、模架以及其他零部件的选用
7.1、模架选择
前面已选用中间导柱模架
由参考资料取
1上模座数量1规格:
160×160×32
2下模座数量1规格:
160×160×40
3导柱数量1规格:
24×160
4导柱数量1规格:
25×160
5导套数量1规格:
24×80×30
6导套数量1规格:
25×80×30
7.2、模柄选用
采用凸缘模柄,根据压力机模柄孔尺寸:
Φ50mmx70mm由参考资料查得,
选用模柄A50×100GB2862.3-81Q235
模柄夹持长度比模柄孔深度小5~10mm
7.3、挡料销
挡料销A6×4×3GB2866.11-81
7.4、螺钉选用
卸料螺钉:
由冲模手册查得卸料螺钉M8×80GB2867.6
凹模锁紧螺钉:
由冲模手册查得螺钉M10×55GB70-85
模柄锁紧螺钉:
由冲模手册查得螺钉M8×12GB70-85
7.5、销钉选用
根据参考资料查得:
凹模定位销采用销8×40GB199-85
八、设计并绘制模具总装图