支撑轴车削数控加工工艺毕业设计.docx
《支撑轴车削数控加工工艺毕业设计.docx》由会员分享,可在线阅读,更多相关《支撑轴车削数控加工工艺毕业设计.docx(17页珍藏版)》请在冰豆网上搜索。
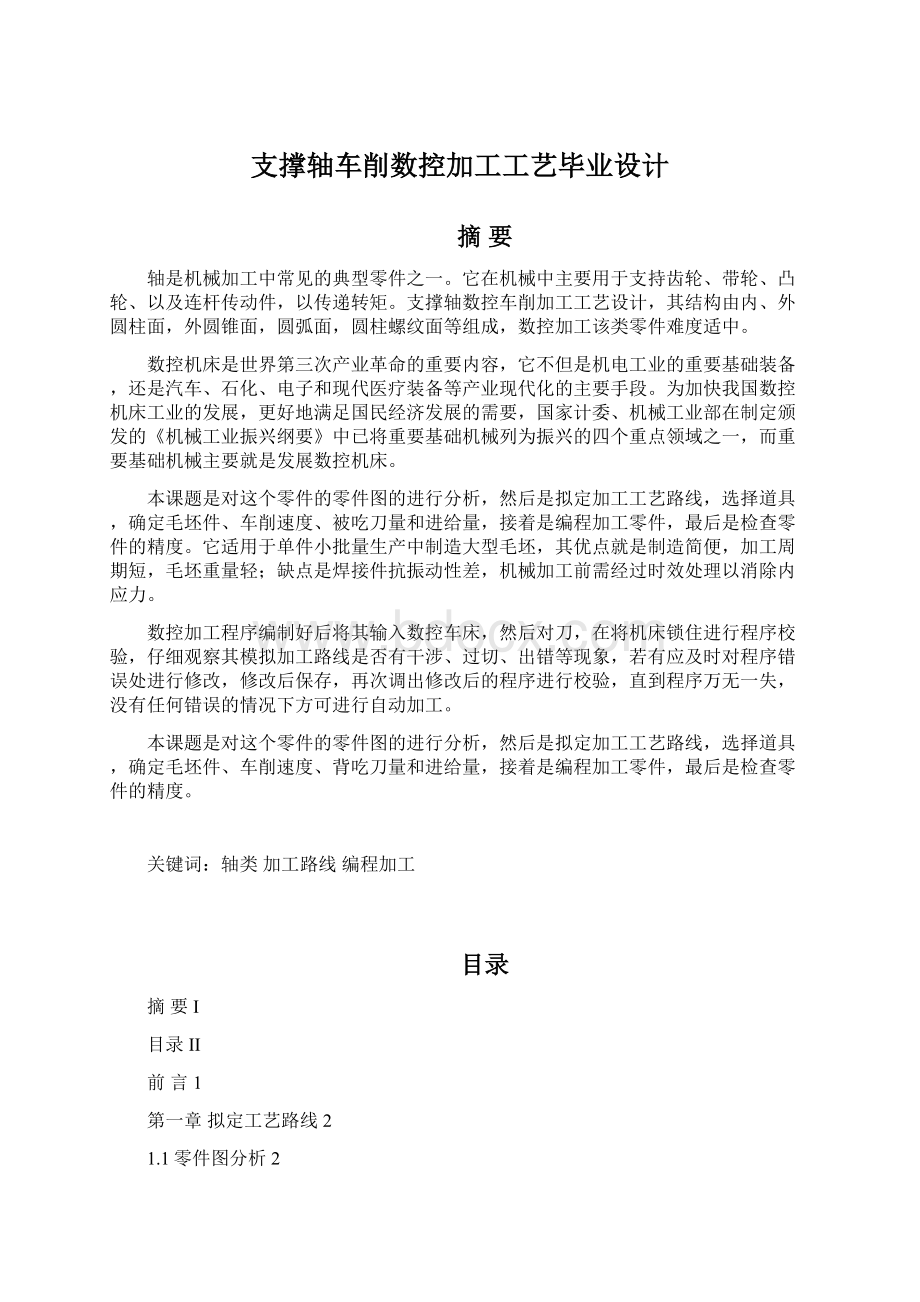
支撑轴车削数控加工工艺毕业设计
摘要
轴是机械加工中常见的典型零件之一。
它在机械中主要用于支持齿轮、带轮、凸轮、以及连杆传动件,以传递转矩。
支撑轴数控车削加工工艺设计,其结构由内、外圆柱面,外圆锥面,圆弧面,圆柱螺纹面等组成,数控加工该类零件难度适中。
数控机床是世界第三次产业革命的重要内容,它不但是机电工业的重要基础装备,还是汽车、石化、电子和现代医疗装备等产业现代化的主要手段。
为加快我国数控机床工业的发展,更好地满足国民经济发展的需要,国家计委、机械工业部在制定颁发的《机械工业振兴纲要》中已将重要基础机械列为振兴的四个重点领域之一,而重要基础机械主要就是发展数控机床。
本课题是对这个零件的零件图的进行分析,然后是拟定加工工艺路线,选择道具,确定毛坯件、车削速度、被吃刀量和进给量,接着是编程加工零件,最后是检查零件的精度。
它适用于单件小批量生产中制造大型毛坯,其优点就是制造简便,加工周期短,毛坯重量轻;缺点是焊接件抗振动性差,机械加工前需经过时效处理以消除内应力。
数控加工程序编制好后将其输入数控车床,然后对刀,在将机床锁住进行程序校验,仔细观察其模拟加工路线是否有干涉、过切、出错等现象,若有应及时对程序错误处进行修改,修改后保存,再次调出修改后的程序进行校验,直到程序万无一失,没有任何错误的情况下方可进行自动加工。
本课题是对这个零件的零件图的进行分析,然后是拟定加工工艺路线,选择道具,确定毛坯件、车削速度、背吃刀量和进给量,接着是编程加工零件,最后是检查零件的精度。
关键词:
轴类加工路线编程加工
目录
摘要I
目录II
前言1
第一章拟定工艺路线2
1.1零件图分析2
1.2加工工艺路线的制订2
第二章毛坯的选择4
2.1正确选择毛坯的意义4
2.2毛坯种类的选择4
第三章刀具的选择5
3.1刀具的选择5
第四章选择切削用量6
4.1背吃刀量的选择6
4.2进给量6
4.3切削速度(Vc)和主轴转速(n)6
4.4进给速度的选择7
4.5螺纹加工切削三要素7
第五章确定零件的定位基准和装夹方式9
5.1粗基准选择原则9
5.2精基准选择原则9
5.3定位基准9
5.4选择车削夹具9
第六章程序编制及模拟运行、零件加工或精度自检11
6.1、程序编制11
6.2、模拟运行13
6.3、零件加工13
6.4、精度自检13
结论14
致 谢15
参考文献16
附录17
前言
数控技术就是指一种采用计算机对机械加工过程中的各种控制信息进行数字化运算、处理、并驱动单元对机械执行构件进行自动化控制的技术。
世界各工业发达国家通过发展数控技术、建立数控机床产业,促使制造业跨入一个新的发展阶段,给国民经济的结构带来了巨大的变化。
数控机床是世界第三次产业革命的重要内容,它不但是机电工业的重要基础装备,还是汽车、石化、电子和现代医疗装备等产业现代化的主要手段。
虽然数控机床产业本身的产值远不如汽车、化工等产业,但高效的数控机床给制造业带来了现代化的生产方式以及高倍率的效益增长,这是促进国民经济发展的巨大源动力。
特别是数控技术在制造业的扩展与延伸所产生的辐射作用和波及效果,足以给机械制造业的产业结构、产品结构、制造方式及管理模式等带来深刻的变化。
近年来,我国数控机床工业发展较快,目前已有数控机床生产厂近百家。
为加快我国数控机床工业的发展,更好地满足国民经济发展的需要,国家计委、机械工业部在制定颁发的《机械工业振兴纲要》中已将重要基础机械列为振兴的四个重点领域之一,而重要基础机械主要就是发展数控机床。
“九五”及2013年前我国数控机床的发展方针是:
重点抓好六类主机(数控车床、加工中心、数控磨床、数控锻压机床、数控重型机床和数控精密电加工机床),集中突破数控系统;发展普及型,提高可靠性;内外结合,以我为主,实现我国数据控机床产业化。
“九五”期间,重点提高可靠性,增加品种,普及型数控系统和数控机床实现经济规模生产。
我国对数控加工和数控设备的应用也呈突飞猛进之势,包括以组合机床为主的大量生产方式现在都向以数控设备为主的生产方式转变,社会上对掌握数控技术的人才需求越来越大,特别是对掌握数控加工技术的人才需求量更大。
此次设计,要求对图示零件进行数控加工工艺分析和手工编写程序指令,这就对对我们关于数控技术的掌握提出了比较高的要求,可以较好地锻炼学生分析问题和解决问题的能力,提高学生的就业竞争力。
并且让我们对数控方面的知识更加了解,是对我们日后的就业能力的初测试。
这份说明书是对整个设计过程的描述,包容了零件图样的分析、刀具夹具的选用、工艺路线的拟定以及手工编程的全部内容。
在零件的加工过程中工艺分析是尤其重要的,而数控加工工艺分析与处理是数控编程的前提和依据,没有符合实际的数控加工工艺,就不可能有真正可行的数控加工程序,所以这次设计的重点就在数控加工工艺上,结合数控加工工艺要求和零件的使用要求对轴的数控加工工艺流程作了较详尽的分析。
第一章拟定工艺路线
制订机械加工工艺是机械制造企业工艺技术人员的一项只要工作内容。
机械加工工艺规程的制订与生产实际有着密切的联系,它要求工艺规程制订者具有一定的生产实践知识和专业基础知识。
在实际生产过程中,由于零件的结构行政、几何精度、技术条件和生产数量等要求不同,一个零件往往要经过一定的加工过程才能将其由图样变成成品零件。
因此机械加工工艺的拟定必须从工厂现有的生
产条件和零件的生产数量出发,根据零件的具体需要,在保证加工质量、提高生产效率和降低生产成本的前提下,对零件的各个表面选择适宜的加工方法,合理地安排加工顺序。
下面就是轴类机械加工工艺路线的确定:
1.1零件图分析
制定零件的机械加工工艺规程前,必须认真分析零件图。
分析此零件图:
其视图能够直观、清晰、准确、充分的表达出零件的形状。
图纸上的尺寸、公差、技术要求合理并且齐全。
本图纸没有错误或遗漏。
1.2加工工艺路线的制订
拟定工艺路线是制订规程的关键一步,它不仅影响零件的加工质量和效率,而且影响设备投资、生产成本、甚至工人的劳动强度。
拟定工艺路线时,在首先选择好定位基准后,紧接着需要考虑这几个问题:
(1)加工方法的选择
加工方法的原则是保证加工质量和生产率与经济性,为了正确选择加工方,应了解各加工方法的特点和掌握经济加工度和粗糙度的概念。
本零件以Q号轴的加工面有外圆、内孔、端面、槽、球面、螺纹等。
(参考[1]表27-29)
端面:
+0.1本零件的端面为柱体端面,尺寸精度要求不高。
表面粗糙度为Ra6.3um要求Ra6.3um的端面经粗车即可(参考《机械制造工艺设计简明手册》P20表1.4-6)。
ø32
外圆面,公差等级为IT9,表面粗糙度为Ra3.2um需粗车,半粗车、(参考《机械制造工艺设计简明手册》P20表1.4-6)。
ø24
外圆面,公差等级为IT9,表粗糙度为Ra1.6um需粗车、半精车、精车(参考《机械制造工艺设计简明手册》P20表1.4-6)。
球面R10,公差等级为IT9,粗糙度为Ra3.2um,需粗车,半精车,(参考《机械制造工艺设计简明手册》P20表1.4-6)。
两个槽,未注公差尺寸,公差等级为IT9,表面粗糙度为Ra6.3um,需粗车即可(参考《机械制造工艺设计简明手册》P20表1.4-6)。
螺纹,表面粗糙度为Ra3.2um,公差等级为ZT10,需粗车,半精车,(参考《机械制造工艺设计简明手册》P20表1.4-6)。
(2)加工顺序的安排:
工序集中的原则;先粗后精的原则;先近后远的原则;内外交叉的原则;刀具集中的原则;基面先行的原则。
根据上述原则,此加工工艺路线如下:
棒料伸出卡盘75mm车削端面,并采用G71对外圆车削,外圆ø40,长64mm
采用G71粗车外圆表面
采用G70精车外圆表面
采用G75切槽循环加工4Xø17的槽
采用G75切槽循环加工8.5Xø22的槽
采用G92车螺纹循环加工
钻ø12底孔
粗镗ø14内孔
精镗内孔达到精度要求
并切断工件
第二章毛坯的选择
2.1正确选择毛坯的意义
在制订机械加工工艺规程时,正确选择合适的毛坯,对零件的加工质量、材料消耗和加工工时都有很大的影响。
为了正确选择地选择毛坯,需要毛坯制造和机械加工两方面的工艺人员紧密配合。
2.2毛坯种类的选择
在机械加工中常见的毛坯有铸件、锻件、型材、焊接件等种类。
铸件适用形状比较复杂的零件毛坯。
锻件锻件适用于强度要求高、形状比较简单的零件毛坯,锻件有自由锻和模锻件两种。
自由锻造锻件是在锻锤或压力机上用手工操作而成的锻件。
它的精度低,加工余量大,生产率也低,适用于单件小批量生产及大型锻件。
模锻件是在锻锤或压力机上,通过专用模锻制成形的锻件。
它的精度和表面粗糙度均比自由锻造的好,可以使毛坯形状更接近工件形状,加工余量小。
同时,本课题是对这个零件的零件图的进行分析,然后是拟定加工工艺路线,选择道具,确定毛坯件、车削速度、被吃刀量和进给量,接着是编程加工零件,最后是检查零件的精度。
模锻主要适用于批量较大的中小型零件。
型材主要通过热轧或冷拉而成。
热轧的精度低,价格较冷拉的便宜,用于一般零件的毛坯。
冷拉的尺寸小,精度高,易于实现自动送料,但价格贵,多用于批量较大且自动机床上进行加工的情形。
焊接件是根据需要将型材或钢板焊接而得到的零件,它制作方便、简单,但需要经过热处理才能进行机械加工。
它适用于单件小批量生产中制造大型毛坯,其优点就是制造简便,加工周期短,毛坯重量轻;缺点是焊接件抗振动性差,机械加工前需经过时效处理以消除内应力。
根据图纸得知这个零件是个不复杂的轴类零件,且是小批量生产,确定热轧型材。
查《机械制造加工手册》选择热轧型钢规格为φ40。
表2-1毛坯尺寸参数
加工工步
IT
加工余量
尺寸标注
精加工
IT8
0.2
φ32
半精加工
IT11
1.4
φ32.2
粗加工
IT13
2.0
φ33.6
毛坯
IT13
——
φ35.6±1.0
第三章刀具的选择
3.1刀具的选择
刀具的选择是数控加工中重要的工艺内容之一,它不仅影响机床的加工效率,而且直接影响加工质量。
编程时,选刀具通常要考虑机床的加工能力、工序内容、工件材料等因素。
与传统的加工方法相经,数控加工对刀具的要求更高。
不仅要求精度高、刚度高、红硬性好、耐用度高,而且要求尺寸稳定、安装调整方便,能适应高速和大切削用量切削。
选刀具时,要使刀具的尺寸与被加工工件的表面尺寸和形状相适应。
接合零件轮廓相对还是较复杂,所以具体选刀如下:
外圆车刀的选择平端面可选用90°WC-Co的硬质合金外圆车刀,粗车、精车及在这里我选择一把硬质合金右端面外圆车刀,为防止在进行圆弧切削时刀具的副后刀面与工件轮廓表面发生干涉(可用作图法检验),副偏角应选择Kr′大一点的,取Kr′=40°右端面外圆车刀的材料选择及Kr′值这里分别参照《金属切削与刀具实用技术》一书表1-1,表1-17。
因此外圆车刀应选:
副偏角为40°的90°WC-Co的硬质合金外圆车刀。
精加工和粗加工为同一把刀。
切槽到的选择切槽时由于零件中槽宽4mm,一般都选刀宽为4mm,刀杆25×25mm材料为高速钢W18CrV4R的切断刀,切槽时选用4mm刀宽即可。
切槽刀的选择及型号这里分别参照《金属切削与刀具实用技术》一书表1-3,表2-2。
因此切槽刀应选:
槽宽为4的材料为高速钢W18CrV4R的切槽刀。
螺纹刀的选择切螺纹时为了保证其螺纹刀的强度这里选用W18CrV4R高速金60°外螺纹车刀,为了保证螺纹牙深,刀尖应小于轮廓最小圆弧半径Rε,Rε=0.15~0.2mm。
刀具选材料参照《金属切削与刀具实用技术》一书表1-3即可
分析得应选:
刀尖应小于轮廓最小圆弧半径Rε,Rε=0.15~0.2mm的60°高速钢W18CrV4R的螺纹刀。
钻孔零件中的孔表面粗糙度是1.6
因此加工时要用高速钢制造的Φ3电钻,Φ12麻花钻和镗刀。
第四章选择切削用量
切削用量包括主轴转速(切削速度)、切削深度或宽度、进给速度(进给量)等。
对于不同的加工方法,需选择不同的切削用量,并应编入程序单内。
合理选择切削用量的原则是:
粗加工时,一般以提高生产率为主,但也考虑经济性和加工成本;精加工进,应在保证加工质量的前提下,兼顾切削效率、经济性加工成本。
具体数值应根据机床说明书、切削用量手册,并结合经验而定。
4.1背吃刀量的选择
ap=(dw-dm)/2
零件轮廓粗车循环时选ap=1mm,精加工时选ap=0.2mm,,螺纹粗车时选ap=0.4mm,逐刀减少粗车4次后,精车时选ap=0.1mm。
这里粗车ap值、精车ap值都是《金属切削与刀具实用技术》一书。
4.2进给量
进给量(f)是指工件每转一周,车刀沿进给方向移动的距离(mm/r),它与背吃刀量有着较密切的关第,粗车一为0.3-0.8mm/r,精车时常取0.1-0.3mm/r,切削时宜取0.05-0.2mm/r,具体选择时,可参考[1]表6.3进行(P147)。
棒料伸出卡盘75mm车削端面,并采用G71对外圆车削,外圆ø40,长75mm,其进给量(mm/r),f为0.4(mm/r)[1]表6.5(P149)
采用G71粗车外圆表面,其进给量(mm/r),f为0.4(mm/r)[1]表6.5(P149)
采用G70精车外圆表面,其进给量(mm/r),f为0.2(mm/r)[1]表6.5(P149)
采用G75切槽循环加工4Xø17的槽,其进给量(mm/r),f为0.1(mm/r)[1]表6.5(P149)
采用G75切槽循环加工8.5Xø22的槽,其进给量(mm/r),f为0.1(mm/r)[1]表6.5(P149)
采用G92车螺纹循环加工,其进给量(mm/r),f为0.3(mm/r)[1]表6.5(P149)
粗镗ø14内孔,其进给量(mm/r),f为0.2(mm/r)[1]表6.5(P149)
精镗内孔达到精度要求,其进给量(mm/r),f为0.3(mm/r)[1]表6.5(P149)
倒角并切断工件,其进给量(mm/r),f为0.1(mm/r)[1]表6.5(P149)
4.3切削速度(Vc)和主轴转速(n)
粗车右端外圆时V=160×0.8×0.65×0.81×1.15=77.5m/min
n=1000×V/Πd=1000×77.5/(3.14×40)=617r/min
查《机械制造工艺设计简明手册》n=560r/min;V=70.336mm/min。
精车右端外圆时V=220×0.8×0.65×0.81×1.15=106.6m/min
n=1000×V/Πd=1000×106.6/(3.14×38)=893r/min
查《机械制造工艺设计简明手册》n=900r/min;V=107.388mm/min。
切槽时V=160×0.8×0.65×0.81×1.15=77.5m/min
n=1000×V/Πd=1000×77.5/(3.14×22)=1211r/min
查《机械制造工艺设计简明手册》n=1120r/min;V=53.537mm/min。
钻孔时V=160×0.8×0.65×0.81×1.15=77.5m/min
n=1000×V/Πd=1000×77.5/(3.14×12)=2056r/min
查《机械制造工艺设计简明手册》n=1400r/min;V=52.752mm/min。
镗内孔时V=160×0.8×0.65×0.81×1.15=77.5m/min
n=1000×V/Πd=1000×77.5/(3.14×14)=1762r/min
查《机械制造工艺设计简明手册》n=1400r/min;V=61.54mm/min。
切断工件时V=160×0.8×0.65×0.81×1.15=77.5m/min
n=1000×V/Πd=1000×77.5/(3.14×40)=617.038r/min
查《机械制造工艺设计简明手册》n=560r/min;V=70.336mm/min。
4.4进给速度的选择
进给量(进给速度)f(mm/min或mm/r)是数控机床切削用量中的重要参数,主要根据零件的加工精度和表面粗糙度要求以及刀具、工件材料兴致选取。
最大进给量则受机床刚度和进给系统的性能限制并与脉冲相当有关。
当加工精度、表面粗糙度要求高时。
进给速度(进给量)应选小些,一般在20—50mm/min范围内选取。
粗加工时,为缩短切削时间,一般进给量就选取得大些。
工件材料较软时,可选用较大的进给量;反之,应选较小的进给量。
进给速度是指在单位时间里,刀具沿进给方向移动的距离,有些数控车床规定可以选用以进给量表示的进给速度。
进给速度的大小直接影响表面粗糙度的值和车削效率,因此进给速度的确定应在保证表面质量的前提下,选择较高的进给速度。
一般应根据零件的表面粗糙度、刀具及工件材料等因素,查阅切削用量手册选取。
需要说明的定切削用量手册给出的是每转进给量,因此要根据Vf=fn计算进给速度
粗车端面:
Vf=f.n=560×0.4=224mm/min
采用G71粗车外圆表面,其进给速度为:
Vf=f.n=560×0.4=224mm/min。
采用G70精车外圆表面,其进给速度为:
Vf=f.n=900×0.2=299.6mm/min。
采用G75切槽循环加工4Xø17的槽,其进给速度为:
Vf=f.n=1200×0.1=120mm/min。
采用G75切槽循环加工8.5Xø22的槽,其进给速度为:
Vf=f.n=1200×0.1=120mm/min。
采用G92车螺纹循环加工,其进给速度为:
Vf=f.n=300×0.4=120mm/min。
粗镗ø14内孔,其进给速度为:
Vf=f.n=1400×0.2=280mm/min。
精镗内孔达到精度要求,其进给速度为:
Vf=f.n=1400×0.3=420mm/min。
切断工件,其进给速度为:
Vf=f.n=560×0.1=56mm/min。
4.5螺纹加工切削三要素
车螺纹时,如大多经济型车床数控系统推存车螺纹时的主轴转速如下:
n≤(1200/P)-k,式中:
P是工件螺纹的导程(㎜),英制螺纹为相应换算衙的毫米值;K是保险系数,一般取为80。
取n=300,则V=18.84mm/min。
ap=0.4mm。
根据上述计算,把切削的三要素计算结果填入有关表格。
(见附录)
第五章确定零件的定位基准和装夹方式
5.1粗基准选择原则
为了保证不加工表面与加工表面之间的位置要求,应选不加工表面作粗基准。
合理分配各加工表面的余量,应选择毛坯外圆作粗基准。
粗基准应避免重复使用。
选择粗基准的表面应平整,没有浇口、冒口或飞边等缺陷。
以便定位可靠。
5.2精基准选择原则
基准重合原则;
基准统一原则;
自为基准原则;
互为基准原则。
5.3定位基准
综合上述,粗、精基准选择原则,由于是轴类零件,在车床上只需用三抓卡盘装夹定位,定位基准应选在零件的轴线上,以毛坯ф40mm的棒料的轴线和右端面作为定位基准。
5.4选择车削夹具
机床夹具是在机械制造过程中,用来固定加工对象,使之占有正确位置,以接受加工或检测并保证加工要求的机床附加装置,简称为夹具。
机床夹具的主要功能:
机床上加工工件时,必须用夹具装好夹牢工件。
将工件装好,就是在机床上确定工件相对于刀具的正确位置,这一过程称为定位。
将工件夹牢,就是对工件施加作用力,使之在已经定好的位置上将工件可靠地夹紧,这一过程称为夹紧。
从定位到夹紧的全过程,称为装夹。
机床夹具的主要功能就是完成工件的装夹工作。
工件装夹情况的好坏,将直接影响工件的加工精度。
车床夹具和数控车削夹具要求:
在车床上用于装夹工件的装置称为车床夹具。
夹具是用来定位,夹紧被加工工件并带动工件一起随主轴旋转。
车床夹具可分为通用夹具和专用夹具两大类。
车床通用夹具有三爪卡盘,四爪卡盘,弹簧套和通用心轴等。
在车削加工中较短轴类零件的定位方式通常采用一端圆柱面固定,即用三爪卡盘。
确定装夹方法:
三爪卡盘是最常用的车床通用夹具。
三爪卡盘是由一个大锥齿轮,三个小锥齿轮,三个卡爪组成。
三个小锥齿和大锥齿轮齿合,大锥齿轮的背面有平面螺纹结构三个卡爪等分安装在平面螺纹上。
当用扳手扳动小锥齿轮时,大锥齿轮便转动,它背面的平面螺纹就使三个卡爪同时向中心靠近或退出。
因为平面矩形螺纹的螺距相等,所以三爪运动距离相等,有自动定心的作用。
三爪卡盘最大的优点是可以自动定心,夹持范围大,装夹速度快,但定心精度存在误差,不适于同轴度要求高的工件二次装夹。
为了防止车削是因工件变形和振动而影响加工质量,工件在三爪自定心卡盘中装夹时,其悬伸长度不宜过长。
如:
工件直径小于等于30mm,其悬伸长度不应大于直径的3倍;若工件直径>30mm,其悬伸长度不应大于直径的4倍。
数控机床与普通机床一样也要全里选择定位基准和夹紧应力求设计、工艺与编程计算的基准统一,减少装夹次数,尽可能在一次定位装夹后,加工出全部待加工表面,避免采用占机人工调整式加工方案,以充分发挥数控机床的效能。
装夹应尽可能一次装夹加工出全部或最多的加工表面。
由零件图可分析,可以用三爪自定心卡盘,夹住棒料,棒料伸出卡盘75mm,再从工件右端到左端一次性加工,加工完工件后,再切断。
第六章程序编制及模拟运行、零件加工或精度自检
6.1、程序编制
用φ12的麻花钻,钻一个深度为22的孔
O0001;
G54;
M03S1400;
T0404;(镗刀)
G00X100.0Z100.0;
G00X12.0Z2.0;
G71U0.5R0.3;
G71P10Q2OU0.3W0.1F0.5;
N10G00X14.0;
N20G01Z-22.0F0.2;
G70P10Q20S1400;
G00X100.0Z100.0;
T0101;(60°外圆端面车刀)
S560;
G01X13.0Z2.0;
G71U0.5R0.8;
G71P10Q20U0.2W0.1F50;
N10G01X17.0Z0.0F30;
X21.0Z-2.0;
Z-18.0;
X24.0Z-23.0;
Z-26.0;
G02X24.0Z-38.0R10.0;
G01X24.0Z-42.0;
X32.0Z-46.0;
N20Z-65.0;
G70P10Q20s900;
G28U0W0;
T0202;(槽宽为4的切槽刀)
M03S1211;
G01X28.0Z-18.0;
X17.0;
X50.0;
G00X44.44Z-51.38;
G01X22.0Z-50.36;
X44.44Z-51.38;
X62.0Z-64.0;
X20.0
X20.0Z-58.80;
X62.0Z-64.0;
X40.0Z-51.5
X22.0;
G00X50.0;
G01X34.0Z-64.0;
X32.0Z-62.0;
X28.0Z-60.0;
X50.0;
G00X100.0Z100.0;
T0303;(60度螺纹刀)
G