泵体毕业设计.docx
《泵体毕业设计.docx》由会员分享,可在线阅读,更多相关《泵体毕业设计.docx(37页珍藏版)》请在冰豆网上搜索。
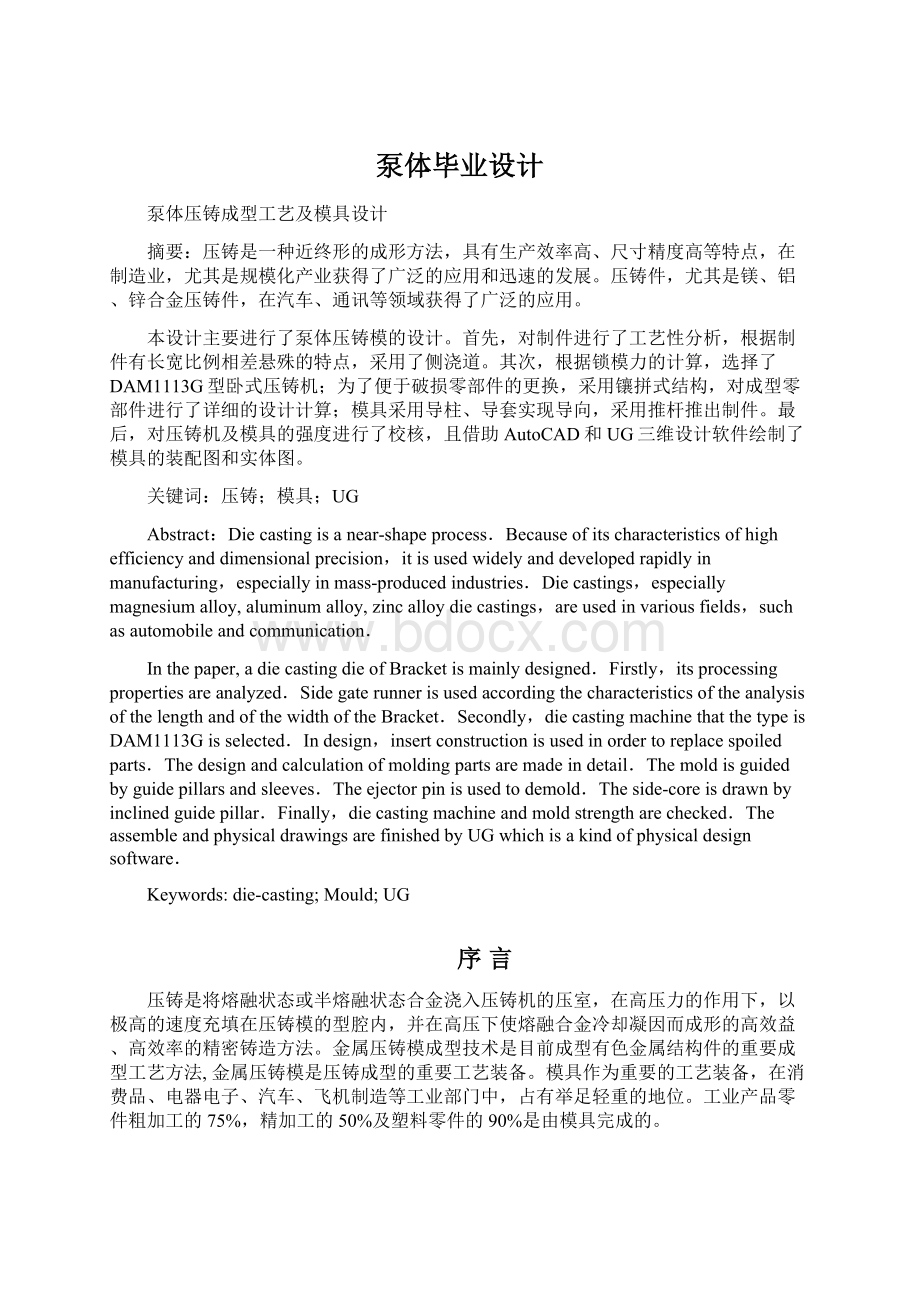
泵体毕业设计
泵体压铸成型工艺及模具设计
摘要:
压铸是一种近终形的成形方法,具有生产效率高、尺寸精度高等特点,在制造业,尤其是规模化产业获得了广泛的应用和迅速的发展。
压铸件,尤其是镁、铝、锌合金压铸件,在汽车、通讯等领域获得了广泛的应用。
本设计主要进行了泵体压铸模的设计。
首先,对制件进行了工艺性分析,根据制件有长宽比例相差悬殊的特点,采用了侧浇道。
其次,根据锁模力的计算,选择了DAM1113G型卧式压铸机;为了便于破损零部件的更换,采用镶拼式结构,对成型零部件进行了详细的设计计算;模具采用导柱、导套实现导向,采用推杆推出制件。
最后,对压铸机及模具的强度进行了校核,且借助AutoCAD和UG三维设计软件绘制了模具的装配图和实体图。
关键词:
压铸;模具;UG
Abstract:
Diecastingisanear-shapeprocess.Becauseofitscharacteristicsofhighefficiencyanddimensionalprecision,itisusedwidelyanddevelopedrapidlyinmanufacturing,especiallyinmass-producedindustries.Diecastings,especiallymagnesiumalloy,aluminumalloy,zincalloydiecastings,areusedinvariousfields,suchasautomobileandcommunication.
Inthepaper,adiecastingdieofBracketismainlydesigned.Firstly,itsprocessingpropertiesareanalyzed.SidegaterunnerisusedaccordingthecharacteristicsoftheanalysisofthelengthandofthewidthoftheBracket.Secondly,diecastingmachinethatthetypeisDAM1113Gisselected.Indesign,insertconstructionisusedinordertoreplacespoiledparts.Thedesignandcalculationofmoldingpartsaremadeindetail.Themoldisguidedbyguidepillarsandsleeves.Theejectorpinisusedtodemold.Theside-coreisdrawnbyinclinedguidepillar.Finally,diecastingmachineandmoldstrengtharechecked.TheassembleandphysicaldrawingsarefinishedbyUGwhichisakindofphysicaldesignsoftware.
Keywords:
die-casting;Mould;UG
序言
压铸是将熔融状态或半熔融状态合金浇入压铸机的压室,在高压力的作用下,以极高的速度充填在压铸模的型腔内,并在高压下使熔融合金冷却凝因而成形的高效益、高效率的精密铸造方法。
金属压铸模成型技术是目前成型有色金属结构件的重要成型工艺方法,金属压铸模是压铸成型的重要工艺装备。
模具作为重要的工艺装备,在消费品、电器电子、汽车、飞机制造等工业部门中,占有举足轻重的地位。
工业产品零件粗加工的75%,精加工的50%及塑料零件的90%是由模具完成的。
本次泵体模具设计基于UG平台进行三维造型与仿真加工。
UG是一套集CAD、CAM于一身的大型软件,其功能强大,造型过程简单而且方便快捷,同时还可以对三维零件进行仿真加工,动画演示,相应可生成数控加工程序,直接传输到数控铣机床即可对零件进行加工。
使用该软件进行设计,能直观、准确地反映零、组件的形状、装配关系,可以使产品开发完全实现设计、工艺、制造的无纸化生产,并可使产品设计、工装设计、工装制造等工作并行开展,大大缩短了生产周期。
模具制造的工艺方法可以分为锻造、热处理、切削加工、表面处理和装配等,其中以切削加工为主要的加工方法。
切削加工大体可以分为切削机床加工、钳加工和特殊加工等,通常模具零件的加工工艺路线一般应遵循普通机械加工工艺的基本原则。
压铸模零件的加工大体可以分为模板加工、孔及孔系加工、成型零件加工等,对不同的模体应根据其自身的实际情况选择合适的加工方法。
随着世界科技进步和机床工业的发展,数控机床作为机床工业的主流产品,已成为实现装备制造业现代化的关键设备,是国防军工装备发展的战略物资。
数控机床的拥有量及其性能水平的高低,是衡量一个国家综合实力的重要标志。
加快发展数控机床产业也是我国装备制造业发展的现实要求。
数控加工是现代制造技术的典型代表,数控技术是机械加工自动化的基础,是数控机床的核心技术,其水平高低关系到国家战略地位和体现国家综合国力的水平。
第1章压铸件结构及工艺分析
1.1任务介绍
主要内容及基本要求:
1.完成泵体的模具设计
2.在UG或其他三维软件平台上完成模具零件的三维建模
3.完成模具的装配
4.设计说明书一份,字数不少于10000字。
1.2压铸零件的分析
本次设计的零件为泵体的模具设计,如下图1-1所示:
图1-1泵体产品图
泵体是某种型号电机上的零件,生产批量100,000件,铸件要求无欠铸、气孔、疏松、裂纹等缺陷。
产品原始信息
产品大小:
65.57*78.49*18.38单位:
MM
产品平均壁厚:
7.6MM
材质:
锌合金(ZZnAlD4)
重量:
199g
缩水率:
1.005
其物理和力学性能为:
密度6.6g/mm³,固相线与液相线温度分别为381ºC和387ºC,抗拉强度283MPa,屈服强度414MPa,硬度82HB,剪切强度214MPa,疲劳强度476MPa。
压铸锌合金的使用性能和工艺性能都优于其他压铸合金,而且来源丰富,所以在各国的压铸生产中都占据极重要的地位,其用量远远超过其他压铸合金。
锌合金的特点是:
比重小、强度高;铸造性能和切削性能好;耐蚀性、耐磨性、导热性和导电性好。
锌和氧的亲和力很强,表面生成一层与锌结合得很牢固的氧化膜,致密而坚固,保护下面的锌不被继续氧化。
锌硅系合金在杂质铁含量较低的情况下,粘模倾向严重。
锌合金体收缩值大,易在最后凝固处形成大的集中缩孔。
用于压铸生产的锌合金主要是铝硅合金、铝镁合金和铝锌合金三种。
纯锌铸造性能差,压铸过程易粘模,但因它的导电性好,所以在生产泵体时使用。
锌合金中主要合金元素及杂质对其性能影响如下:
硅:
硅是大多数锌合金的主要元素。
它能改善合金在高温时的流动性,
提高合金抗拉强度,但使塑性下降。
硅与锌能生成固熔体,它在锌中的溶解度随温度升高而增加,温度577℃时溶解度为1.65%,而室温时仅为0.2%。
在硅含量增加到11.6%时,硅与其在锌中的固溶体形成共晶体,提高了合金高温流动性,收缩率减小,无热裂倾向。
二元系铝硅合金耐蚀性高、导电性和导热性良好、比重和膨胀系数小。
硅能提高铝锌系合金的抗蚀性能。
当合金中硅含量超过共晶成分,而铜、铁等杂质又较多时,就会产生游离硅,硅含量越高,产生的游离硅就越多。
游离硅的硬度很高,由它们所组成的质点的硬度也很高,加工时刀具磨损厉害,给切削加工带来很大的困难。
此外,高硅锌合金对铸铁坩锅熔蚀严重。
硅在锌合金中通常以粗针状组织存在,降低合金的力学性能,为此需要进行变质处理。
铜:
铜和锌组成固溶体,当温度为548℃时,铜在锌中的溶解度为
5.65%,室温时降至0.1%左右。
铜含量的增加可提高合金的流动性、抗拉强度和硬度,但降低了耐蚀性和塑性,热裂倾向增大。
压铸通常不用锌铜合金,而用锌硅铜合金。
该产品的成型材料是锌合金,该材料密度小,熔点为381~387度,强度较高,耐磨性能较好,导热、导电性能好,机械切削性能良好,但由于锌与铁有很强的亲和力,容易粘模,加入Mg以后可得到改善。
锌压铸,其锌很容易就粘在模具表面上,造成铆接柱拉伤、拉断,浇注口堵塞现象.
1.3拟定模具结构形式
根据压铸件的产品信息,产品生产所需的数量,产品的强度和精度有较高要求,综合实际考虑,该产品采用一模二穴的成型方法。
1.4压铸工艺分析及计算
根据压铸件的产品信息,产品生产所需的数量,产品的强度和精度有较高要求,综合实际考虑,该产品采用一模二穴的成型方法。
(1)锁模力计算
根据压铸产品选择压铸机,锁模力通常的计算方式为用模具分型面上承受金属压力的投影面积乘以铸造比压乘以安全系数。
锁模力的计算如下:
T=K*A*P
其中:
T为锁模力,单位为N;
K为安全系数,热室压铸机一般取1.3
A为铸造投影面积,单位mm²(包括铸件、料、头、流道、溢流井等,约相当于铸件的1.8倍)
P为压射比压,单位Mpa。
单位换算1T=10KN=100000N
该产品的铸件投影面积为2843*1.8=5117.4mm²
由于该产品为压铸件,压射比压取值为30Mpa。
故该产品的锁模力为:
T=K*A*P=2*1.3*5117.4*30/10*100=400KN
1.5压铸机的选用
根据以上数据选择锁模力大于400(KN)的机台(如图)即可,结合锌合金机台设备考虑,本次模具设计采用的是热压室压铸机,其型号与主要技术规格如下:
压铸机型号:
DAM1113G
锁模力/KN:
1250
压射力/KN:
85-150
第2章压铸模结构设计
2.1确定模具分型面
分型面的定义:
压铸模的定模与动模接合表面通常称为分型面,分型面是由压铸件的分型线所决定的,而模具上垂直于锁模力方向的接合面,即为基本分型面。
分开模具取出压铸制品的界面称为分型面,也可称为合模面。
分型面的类型选择是否恰当,设计是否合理,在模具设计中非常重要。
它不仅直接关系到模具结构的复杂程度,而且对制品的成型质量和生产操作等都有影响。
选择分型面即是决定型腔空间在模内应占有的位置。
选择分型面时应遵循以下原则:
(1)符合压铸件脱模:
为使压铸件能从模具内取出,分型面的位置应设在压铸件断面尺寸最大的部位。
(2)分型面的数目及形状:
通常只采用一个与压铸机开模运动方向相垂直的分型面,特殊情况下才采用一个以上的分型面或其他形状的分型面。
(3)型腔方位的确定:
在决定型腔在模具内的方位时,分型面的选择应尽量防止形成侧孔或侧凹,以避免采用较复杂的模具结构。
(4)确保压铸件质量:
分型面不要选择在压铸件光滑的外表面,避免影响外观质量;将压铸件要求同轴度的部分全部放在分型面的同一侧,以确保压铸件的同轴度;要考虑减小脱模斜度造成压铸件大,小端的尺寸差异要求等。
(5)有利于压铸件的脱模:
由于模具脱模机构通常设在动模一侧,故选择分型面时应尽可能使开模后压铸件留在动模一侧。
(6)有利于排气:
当分型面作为主要排气渠道时,应将分型面设计在压铸熔体的流动末端,以利于排气。
(7)模具零件易于加工:
选择分型面时,应使模具分割成易于加工的零件,以减小机械加工的困难。
分型面的选择
图2-1分型面方案
型腔图片
型芯图片
2.2浇注系统的设计
浇注系统对熔融金属流动方向、压力传递、模具温度分布、充填时间长短起到重要的调节和控制作用,浇注系统设计直接影响铸件的机械性能和模具寿命。
浇注系统设计一般步骤:
内浇口设计→浇道设计→过水设计→渣包设计
内浇口宽度的选取及内浇口设计的原则:
1.金属液从铸件壁厚处向壁薄处填充
2.金属液进入型腔后不宜立即封闭分型面,溢流面和排气槽
3.内浇口的位置要使进入型腔的金属液先流向远离浇口的部位
4.从内浇口进入的金属液,不宜正面冲击型芯
5.浇口的位置应便于切除
6.避免在浇口部位产生热节
7.金属液进入型腔后的流向要沿着铸件上的肋和散热片
8.选择内浇口位置时,应使金属液流程尽可能短
2.2.1内浇口的设计
根据其各自应用范围和特点,针对本次设计零件的形状,选择端面侧浇口,使金属液首先填充可能存留气体的型腔底侧,将底部的气体排出后,再逐步充满型腔,避免压铸件中气孔缺陷的产生。
内浇口面积的计算
铸件设计完成后,测量浇铸体积(产品+溢料)的体积,在压铸件的填充时间及填充数度选定后,内浇口面积可采用下式计算:
Ag=V/Vg*t
其中:
Ag—内浇口截面积(mm²)
V—铸件的体积(mm³)(包括渣包和产品)
Vg—充填速度(m/s)
t—充填时间(s)
图2-2内浇口示意图
对应参数的计算:
充填时间的计算
充填时间是指熔融金属自到达浇口(gate)起算,至模穴(cavity)及溢流井完全充填完毕为止,所经过的时间。
理论上,充填时间是越短越好;但实际上,充填时间受以下限制:
(a)逃气
(b)模具冲蚀
(c)机器性能
以下列公式(NADCA)计算出填充时间:
t=k[(Ti-Tf+SZ)/(Tf-Td)]×T
其中k=0.0346秒/mm
Ti=熔汤进入模具温度,取650ºC
Tf=合金最低流动温度,取595ºC
S=容许凝固百分率,取0%
Z=转换系数2.5ºC/%
Td=模具温度,取240ºC
T铸件厚度,取7.6m
t=0.0346×[(650-595+0.0×2.5)/(595-240)]×7.6
=0.04(秒)
铸件体积的计算
V=30068*1.2=36000mm³(包括渣包和产品)
内浇口充填速度的计算
对于不同壁厚的镁、铝、锌压铸合金的充填速度不同:
本产品平均壁厚为7.6MM,材质为锌合金,内浇口填充速度为50m/s
本产品的内浇口面积为:
Ag=V/Vg*t=36000/50000*0.04=18mm²
考虑到产品的结构问题,内浇口宽度L取值为18mm,所以内浇口厚度H=H=Ag/L=18/18=1mm
2.2.2直浇道设计
直浇道是金属液从压室进入型腔前首先经过的通道。
卧室热压室压铸模直浇道的由浇口套、浇道镶块和浇道推杆组成。
浇口套与压铸机的压室端面密封对接。
浇口套在压铸模的浇注系统中起着承前启后的作用,直浇道就是在浇口套中形成的。
1.浇口套与压室的连接方式
浇口套与压室的连接方式,根据浇口套结构形式的不同,可分为连接式和整体式。
本次设计采用整体式结构即将压室与浇口套制成整体,这样易于内孔的精度容易保证。
2.浇口套参数的确定
直浇道由压铸模上浇口套构成,能保证压射冲头动作顺畅,有利于压力传递。
直径D:
根据压铸件重量、所需比压、在压室的充满度(一般占2/3)来选择冲头直径,也就是直浇道的直径D。
厚度H:
称为余料,取直径的1/2~1/3,为了易脱模,设1°30’~2º斜度。
3.浇口套的配合精度
浇口套的配合精度有:
浇口套与模板孔的配合精度、浇口套内孔与压射冲头的配合精度和定位孔与压铸机压室法兰的配合精度。
(1)浇口套与模板孔的配合精度为
(H7/h6)
(2)浇口套内孔与压射冲头的配合精度:
由压铸模具设计手册[2]表5-6查得浇口套内孔与压射冲头的配合精度如下表2-1所示:
表2-1浇口套内孔与压射冲头的配合精度
压室基
本尺寸
尺寸偏差
浇口套D(F8)
压室Do(H7)
压射冲头d(e8)
>30~50
+0.064
+0.025
+0.025
0
-0.050
-0.089
(3)定模座板或浇口套的定位孔与压铸机压室法兰的配合精度为
(E8)
图2-3浇口套图片
4.分流系统的设计
(!
)汤料经过浇口套进入型腔前,,需由分流锥的引流,分流锥与浇口套配合使用,组成铸件的浇注系统,精度与浇口套相当
图2-4分流锥图片
2.2.3横浇道设计
图2-5扁梯形
横浇道的尺寸参数如下:
D=(5~8)T
=(3~4)
W=D
+
/D
其中
---横浇道截面积mm2
---脱模斜度
=
D----横浇道深度(mm)
T----内浇口厚度
W----横浇道宽度(mm)
取D=5T=12.5mm
=3
=3
28=84mm2
W=D
+
/D=12.5
+84/5=18mm
至此,整个浇注系统设计完毕,各部位参数均已选定,进而绘制出模具浇注系统结构图如下图2-6所示:
图2-6浇注系统
2.3排溢系统的设计
2.3.1溢流槽的设计
设置溢流槽可作为接纳型腔中的气体、气体夹杂物及冷污金属,还可以作调节型腔局部温度、改善充填条件以及必要时作为工艺搭子顶出铸件之用。
渣包的作用:
1.排除型腔中的气体、涂料、残渣等冷污金属液,与排气槽配合,迅速将型腔内的气体引出;
2.控制金属液充填的流动状态,防止局部产生涡流;
3.转移缩孔、酥松、气孔和冷隔的部位;
4.调节模具各部位的温度,改善模具热平衡状态,减少铸件表面流痕、冷隔和浇不足的现象;
5.帮助铸件脱模顶出,防止铸件变形或在铸件表面有顶针痕迹;
6.溢流槽的总体积占合金量的10%~30%,根据型腔体积,铸件壁厚来考虑,溢口面积为水口面积的60%~75%;溢口厚度:
0.2~0.5mm,溢口厚度不应大于内浇口厚度以保证增压效果。
溢流槽与排气槽连接,减小型腔内压力,排出气体。
数量根据需要位置的多少来决定。
过水设计原则:
1.改善汤流阻力
2.增加产品强度便于后
3.加工不影响产品外观
溢流槽设计及参数的确定
在分型面上设置溢流槽是一种简单适用的常用方式。
为了后序工艺的需要,而保持溢流包与压铸件的整体连接,将溢流槽开设在动模一侧。
溢流槽的截面形状一般有三种,椭圆形、方形和梯形,本次设计采用椭圆形溢流槽,如下图2-7所示:
图2-7溢流槽
根据压铸模具设计手册确定溢流槽的相关尺寸:
溢流口厚度h=0.3~0.8mm,取0.4mm;
溢流口长度l=2~3mm,取2mm;
溢流口宽度S=8~12mm,取8mm;
溢流槽半径r=5~10mm,取5.5mm;
溢流槽长度中心距b>(1.5~2)S,取b>1.5S=12mm。
为了便于脱模,溢口脱模斜度做成
,溢口与铸件连接处应有(0.3~1)mm
的倒角,以便清除。
2.3.2排气道的设计
排气道是在填充过程中让型腔和浇注系统内的气体得以逸出的通道。
为使型腔内的气体尽可能地被金属液有序有效地排出,应将排气道设置在金属液最后填充的部位。
结合实际情况,选用在分型面上开设排气道,这种布局易于加工和修正而且排气效果也很理想。
本次设计在分型面上开设的排气道的截面形状是扁平状的,由压铸模具设计手册[2]表5-8可查得推荐的尺寸如下:
排气槽深度:
0.2~0.5mm
排气槽宽度:
8~25mm
为了便于溢流和余料的脱模,扁平槽的周边也应有
~
的斜角或过渡圆角。
A(排气)=0.2~0.5A(内浇口)
A(排气)=5mm2
图2-8溢流槽与排气示意图
2.4模具温度及冷却系统的设计
模具温度对压铸制件的质量及生产效率有极大的影响。
每一种压铸件都有其适宜的成形模温,在生产过程中若能始终维持想适宜的模温,则其成形性能得到改善。
若模温过低,会降低压铸熔体流动性,使压铸件轮廓不清,甚至充模不满;模温过高,会使压铸件脱模时和脱模后发生变形,使其形状和尺寸精度降低。
利用模温调节系统保持模温恒定,能有效减少压铸件成型收缩的波动,提高压铸件的合格率。
模具型芯与型腔温差过大,会使压铸件收缩不均匀,导致压铸件翘曲变形。
适当提高模具温度能有效地改善压铸件外观质量。
过低的模温会使压铸件轮廓不清,产生明显的银丝,云纹等缺陷,表面无光泽或粗糙度增加等。
就压铸成形过程讲,可把模具看成为热交换器。
压铸熔体凝固时释放出的热量中约有5%以辐射、对流的方式散发到大气中,其余95%由模具的冷却介质(一般为水)带走。
因此模具的生产效率主要取决于冷却介质的热交换效果。
冷却管道的设计主要遵循以下原则:
1.合理确定冷却管道的直径,中心距及型腔壁的距离。
2.降低进水与出水的温度差。
3.浇口处应加强冷却。
4.应避免将冷却管道开设在压铸件的熔合纹部位,并注意干涉及密封等问题。
5.冷却水道应便于加工和清理。
图2-9铸件冷却形式
水管(与机台连接冷却系统)
2.5抽芯结构设计
2.5.1行位的设计
侧向分型与抽芯机构简称行位,用来成型具有外侧凸起、凹槽和孔的塑件;成型壳体制品的局部凸起、凹槽和肓孔。
因为侧抽机构的压铸模,其可动零件多,动作复杂。
因此,侧抽机构的设计应尽量可靠、灵活和高效。
本产品图需要抽芯位置如图2-10红色面所示:
图2-10侧抽芯倒扣
A.行位及其组件的性能要求
行位有相对于其他零件的运动而且行位还是产品成型结构部分,因此行位及与其想配合的零件不仅满足一定的耐磨性要求还必须具有一定成型零件的性能。
行位及其组件的性能必须满足如下几点:
(1)高耐磨性:
滑块表面硬度必须大于HRC48,以保证其耐磨性能。
(2)硬度差:
行位与其配合的零件如下模镶件、行位驱动块、行位压紧块、耐磨片之间必须有HRC5~10的差值,因此不可以用同种材料以防止粘着磨损。
此次设计中行位采用8407,下模镶件采用预硬模具钢8407,其他与行位有接触的零件均采用TOOLOX44耐磨钢。
他们通过不同的热处理方式可以达到此项要求。
(3)加工性:
除行位以外的零件都是单一简单结构零件,热处理变形小,可加工性优异。
而行位的成型部分可以通过电火花加工,其余结构对于传统加工也容易保证其加工精度。
(4)配合要求:
行位与压板有相对运动,其配合采用H7/f7的间隙配合。
与下模镶件的的配合以保证不溢料尽量保证动作稳定灵活。
详细见模具总装的配合要求。
B.本设计采用斜导柱侧向分型机构
结构示意图如图所示。
其一般由以下五个部分组成:
1、动力零件:
采用油压缸;
2、锁紧零件:
束块;
3、定位零件:
挡板;
4、导滑零件:
滑块导向块;
5、成型零件:
滑块镶件、滑块等。
图2-11滑块示意图
C.侧向分型机构主要设计技术参数
1、滑块倾角:
15°<a<25°;滑块斜面倾角b=a+2~3°;
2、抽芯距S
S=胶件侧向凹凸深度+5~10㎜,
滑块1铸件需要抽芯距离为30㎜,加上安全距离则设计需要抽芯距离为40㎜;
滑块1铸件需要抽芯距离为40㎜,加上安全距离则设计需要抽芯距离为45㎜;
油缸行程计算:
S1=滑块行程+10~20㎜,
3、滑块抽芯力的计算
抽芯力的计算同脱模力计算相同。
对于侧向凸起较少的塑件,抽芯力往往是比较小的,仅仅是克服铸件与侧型腔的粘附力和侧型腔滑块移动时的摩擦阻力。
对于侧型芯的抽芯力,往往采用如下公式进行估算:
式中 FC—抽芯力,N;