对航空CAE自主创新发展的回顾与思考.docx
《对航空CAE自主创新发展的回顾与思考.docx》由会员分享,可在线阅读,更多相关《对航空CAE自主创新发展的回顾与思考.docx(10页珍藏版)》请在冰豆网上搜索。
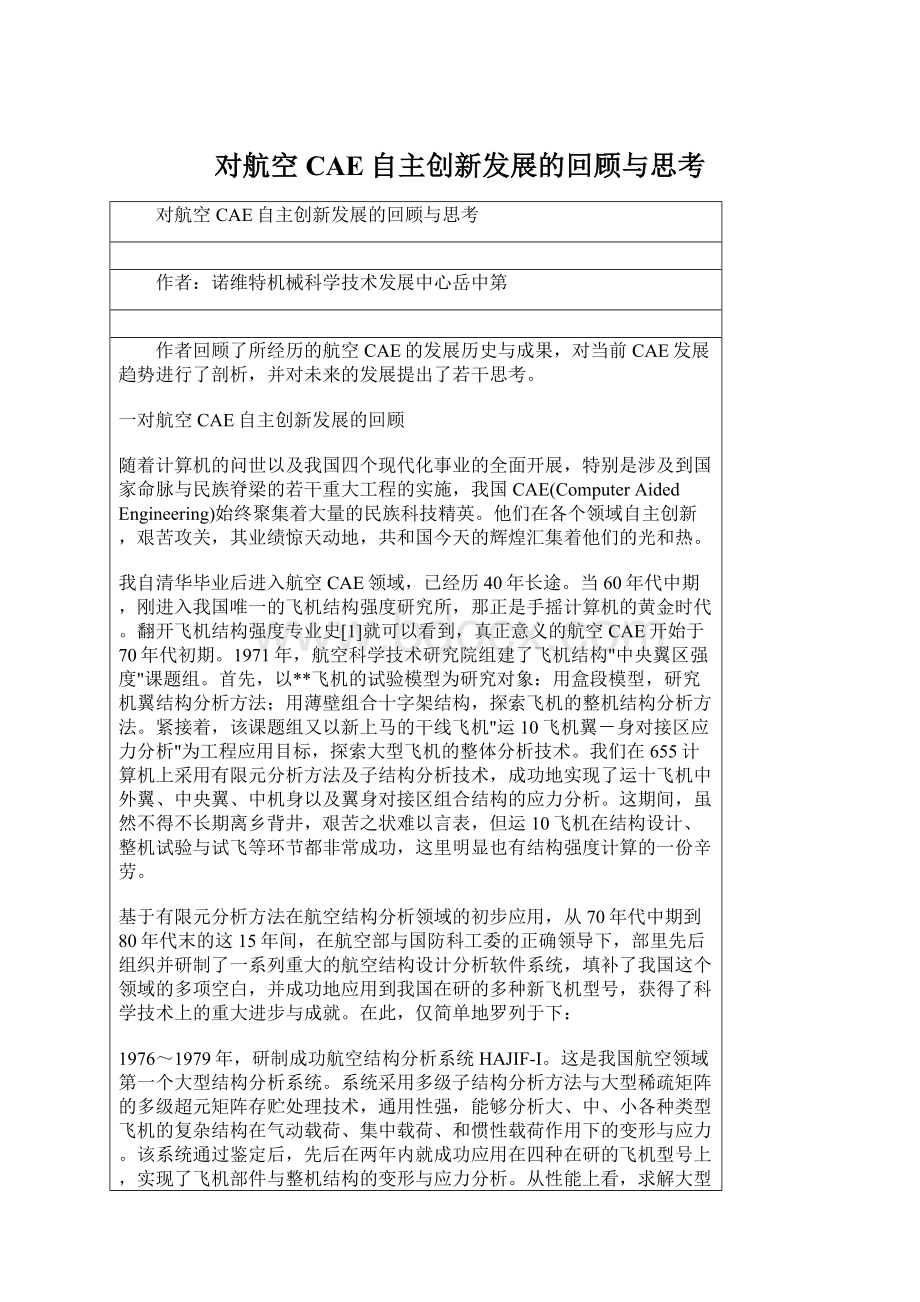
对航空CAE自主创新发展的回顾与思考
对航空CAE自主创新发展的回顾与思考
作者:
诺维特机械科学技术发展中心岳中第
作者回顾了所经历的航空CAE的发展历史与成果,对当前CAE发展趋势进行了剖析,并对未来的发展提出了若干思考。
一对航空CAE自主创新发展的回顾
随着计算机的问世以及我国四个现代化事业的全面开展,特别是涉及到国家命脉与民族脊梁的若干重大工程的实施,我国CAE(ComputerAidedEngineering)始终聚集着大量的民族科技精英。
他们在各个领域自主创新,艰苦攻关,其业绩惊天动地,共和国今天的辉煌汇集着他们的光和热。
我自清华毕业后进入航空CAE领域,已经历40年长途。
当60年代中期,刚进入我国唯一的飞机结构强度研究所,那正是手摇计算机的黄金时代。
翻开飞机结构强度专业史[1]就可以看到,真正意义的航空CAE开始于70年代初期。
1971年,航空科学技术研究院组建了飞机结构"中央翼区强度"课题组。
首先,以**飞机的试验模型为研究对象:
用盒段模型,研究机翼结构分析方法;用薄壁组合十字架结构,探索飞机的整机结构分析方法。
紧接着,该课题组又以新上马的干线飞机"运10飞机翼-身对接区应力分析"为工程应用目标,探索大型飞机的整体分析技术。
我们在655计算机上采用有限元分析方法及子结构分析技术,成功地实现了运十飞机中外翼、中央翼、中机身以及翼身对接区组合结构的应力分析。
这期间,虽然不得不长期离乡背井,艰苦之状难以言表,但运10飞机在结构设计、整机试验与试飞等环节都非常成功,这里明显也有结构强度计算的一份辛劳。
基于有限元分析方法在航空结构分析领域的初步应用,从70年代中期到80年代末的这15年间,在航空部与国防科工委的正确领导下,部里先后组织并研制了一系列重大的航空结构设计分析软件系统,填补了我国这个领域的多项空白,并成功地应用到我国在研的多种新飞机型号,获得了科学技术上的重大进步与成就。
在此,仅简单地罗列于下:
1976~1979年,研制成功航空结构分析系统HAJIF-I。
这是我国航空领域第一个大型结构分析系统。
系统采用多级子结构分析方法与大型稀疏矩阵的多级超元矩阵存贮处理技术,通用性强,能够分析大、中、小各种类型飞机的复杂结构在气动载荷、集中载荷、和惯性载荷作用下的变形与应力。
该系统通过鉴定后,先后在两年内就成功应用在四种在研的飞机型号上,实现了飞机部件与整机结构的变形与应力分析。
从性能上看,求解大型复杂结构的规模、效率、精度,都能与国外同类软件相比较。
该系统获航空部一等奖,国防科工委一等奖,国家科技进步二等奖。
1980~1981年,研制成功航空结构动力分析系统HAJIF-II。
这是航空领域第一个大型结构动力分析系统。
系统采用同时迭代法及多级子结构动力综合技术,具有结构固有振动特性计算、考虑主动控制系统的颤振计算和部分突风响应计算等功能,与美国1977年公布的NASTRAN版本的动力部分大体相当。
该系统先后在五种在研的飞机型号上应用获得成功。
该系统获航空部二等奖,并与HAJIF_I合并,获国家科技进步二等奖。
1979~1982年,研制成功飞机结构多约束优化设计系统YIDOYU。
在60年代,黄玉珊教授就提出了"小展弦比机翼薄壁结构的直接设计法"和"力法-应力设计法";在70年代初期,钱令希教授提出了"结构力学中的最优化设计理论与方法的近代发展"。
这些理论和方法都为飞机结构最佳设计指明了方向。
YIDOYU系统的应用对象是带操作面的翼面结构,考虑机身上的弹性支持和刚性外挂,其约束为静强度、位移、静气动弹性要求及一个给定情况下的颤振速度及结构最小尺寸。
该系统可以用于新机研制的方案论证和飞机翼面结构打样设计。
这是航空领域第一个飞机结构优化设计系统,相当于国外70年代中期的水平。
该系统获航空部一等奖,并获国家科技进步二等奖。
1982~1985年,研制成功航空结构非线性分析系统HAJIF-III。
这是继HAJIF_I、II后自行研制的第一个大型通用的结构非线性分析系统,主要为解决航空部门提出的日益增多的非线性结构分析问题。
它采用了大型线性与非线性方程组的多种有效算法、特征值问题的多种解法与子结构分析技术,可以解决航空、航天及其他工程结构的静力线性分析、热应力分析、弹塑性分析、稳定性分析、大位移或大变形及大位移情况下的弹塑性分析,也可用于新方法、新元素、新材料模式等方面的科学研究。
该系统填补了我国大型通用的结构非线性分析系统的空白,相当于国外80年代初期同类系统的先进水平。
该系统获航空部一等奖,国家科技进步一等奖。
1986~1995年,航空部组织全行业CAD\CAE\CAM\PDM方面的精兵强将,开发了一个初具规模且交互实用的飞机计算机辅助设计、辅助分析、辅助制造集成系统-CIEM系统工程。
该系统集成飞机设计各主要专业、主要研制阶段的应用程序,包括飞机数控加工程序,为飞机研制提供一个强有力的工具。
CIEM系统工程首先实现了在飞机设计领域中集成总体、气动力、结构强度、气动弹性、辅助制造几个专业的应用程序。
该系统工程获航空部一等奖,并获国家科技进步二等奖。
据我们了解,在国内的同一时期,也相继涌现出以大连理工大学JIEGFX为代表的一大批高水平的通用结构分析系统,在国内各个领域发挥出巨大的作用。
这是我国CAE技术高速发展的梦幻岁月,它是何等地光辉灿烂、百花齐放、百家争鸣!
!
。
回顾我们亲身经历的航空CAE(从HAJIF-I到CIEM工程)系统的自主创新发展的历史与成果,可以清楚地看到,我国工程技术人员完全具有自主创新、自强自立于世界民族之林的能力。
只要紧紧依靠他们、充分利用他们的聪明才智,用心规划,精心组织,刻苦攻关,全心全意地开发研制,几乎没有什么CAE技术不能自主创新发展。
二"拿来主义"与"踏着巨人的肩膀"
80年代初,开革开放的春风吹遍祖国大地。
祖国的大门从此洞开。
各行各业的大量科技精英走出国门:
有的参加国际学术交流,有的参加国际合作,有的当访问学者或留学生,有的移民他乡。
从80年代末到21世纪初,是我国CAE精英队伍经历国内外大规模地双向流动的阶段。
通过CAE技术这种双向交流与融合,其现状是:
国外的CAE技术(包括软硬件)象夏天强劲的台风刮向祖国大地,遍及国内的各个领域;他们的专家深入到各行各业的大学、院所、企业与工厂,展示他们的CAE技术、系统功能及使用技巧。
国内CAE技术市场的门大开着,精英队伍流向国外,几乎已经学遍全世界。
但是,客观地说,最近10多年CAE自主创新的步伐已经满了下来,有些甚至停了下来;国内CAE软件的工程化、产业化的发展,不令人满意;国内外CAE技术"你中有我,我中有你"的局面,并没有真正形成。
国内CAE精英流出多,国外CAE软硬件流进多,其趋势还在继续。
我们要回到80年代那样,完全独立自主地、封闭地开发与创新CAE软件系统,不吸收国外CAE的开发平台和先进技术,是既不现实也不明智了。
如同近代用枪炮取代古代长矛大刀,而现代又用飞机导弹取代落后的枪炮都是历史的必然一样,我们的CAE技术必须适应这样一种历史发展的总趋势。
这里,我仅以亲身的经历与感受,对新条件下CAE发展趋势进行评说。
1980年3月,我作为中国航空科学技术研究院的一名年轻代表,出席在英国举行的《第四界国际CAD学术会议及展览会》。
同时,我们代表团还参观了英国著名的高等学府牛津、剑桥大学,访问了英国皇家科学院及多个国家实验室及CAD/CAM研究中心。
第四界国际学术会议使我眼界大开,看到了我所在领域与世界的真实差距。
这也使我深深地思考,如何在已有的成果基础上继续前进,追赶国际的先进水平。
我们既没有理由盲目乐观,也没有理由枉自菲薄。
我们研制的HAJIF其功能并不差,对飞机这样的大型复杂结构的分析效率与精度也不差,但是我们软件的用户界面不友好,软件工程化与可移植性差,却是一个无法回避的事实。
这有点像大姑娘,穿着一件很破烂的衣服出席一场现代的服装晚会。
因此,90年代,我们的HAJIF系列软件在MSC与ANSYS这样的外来软件冲击面前,节节败退,被用户遗忘就成为必然了。
1984年,我作为中国西德航空技术合作项目专家工作队副队长,在异国它乡-德国的军用飞机分部MBB公司工作了三年半。
中方20多位专家与德国专家一道,在完全对等的合作领域,对所承担的工程CAD/CAE/CAM/APP.SUPPORT集成系统(简称CADEMAS工程)的繁重任务,进行了扎扎实实的技术攻关,取得了可喜的技术成果,并成功地移置和应用到国内外相关的工程项目上,得到了国内外同仁的广泛认可。
在与德国CAD/CAE专家深入接触后,感受最深的是如何以科学的态度选择与构建集成系统的开发平台。
在方案论证阶段,对可能构成未来系统框架的各个工程应用子系统进行评测是最重要的工作。
双方专家严肃认真地评测了世界上已有的商用CAD、CAE、CAM、DBMS及各种开发工具(包括语言及算法等),其目的就是要构建一个具有国际水平并与之接轨的工作平台。
那些通过商业途径能够购得的工程应用系统、组件与工具,决不列为项目组的开发任务,进行重复开发。
例如,航空CAD的几何算法,CAE的求解器,数据库管理系统(DBMS)等,都是通过双方技术专家评测后,以民主决策方式确定,"拿来"-采购就是了。
双方CAE专家把工作重点和最主要的精力放在与飞机结构紧密相关的CAD/CAE集成以及飞机结构有限元分析前后置处理软件的开发方面。
整个CADEMAS系统工程有两个法则是明白无误的:
一个就是鲁迅先生提倡过的"拿来主义",一个就是"踏着巨人的肩膀"攀登。
我认为,在改革开放的今天,正确把握这两点十分重要。
这可能也是我们CAE技术专家,面对改革开放后的巨大工程应用需求,对市场做出快速反应的一种有效途径。
三CAE技术在先进数字化制造中的应用
面对国外CAD/CAE软件洪水一般地席卷过来,工程部门的CAE精英应该努力学会游泳,争取站稳风头浪尖,继续前进。
自90年代以来,我和同事及所带学生基于国际通用的CAE开发平台,努力探索CAE技术在先进数字化制造中的应用,开发了飞机结构的有限元快速建模软件,实施了汽车起重机、矿用载重汽车及军用载重越野汽车的改装设计项目,探索了建立重型机械设计CAE数字化样机的方法,开发了金属胆复合材料全缠绕高压容器的设计分析软件,并成功应用到了国家的一些重大工程项目上,取得了较好的应用效果。
3.1飞机机体结构的FEA快速建模技术
采用通用CAD系统,就能实现CAD快速建模。
例如,采用CATIA系统就能很好地实现飞机机体结构的数字化建模和予装配。
但是,面对设计并行化、模型数字化与无纸化,实现飞机机体结构的有限元快速建模,并与数字化的CAD模型与气动载荷模型实现紧密集成,却一直是飞机总体设计师、结构设计师最关心的重要技术课题之一。
"十五"期间国力调查报告表明,对于某些军民机要建立整机机体结构的FEA模型,需要集中相当的技术人员,准备较长时间,而国外同行所用的人力与时间却要少得多。
CAD软件商向我们推荐的整体解决方案,即三维CAD实体模型自动转换为三维FEA模型,在零件实体一级也许可以使用,但在解决飞机机体结构的部件或整机一级,这种方案往往导致几十万、几百万、甚至上千万节点的FEA模型,而最终的分析结果却无法让专家们相信它的正确性。
在这种解决方案里,薄壁组合结构被视为三维连续实体结构,"结构组合"变成"结构铸合","薄壁"变成"实体",使飞机结构的力学特性受到扭曲。
实事上,机体结构的FEA建模应该有它固有的力学简化方法和途径。
我国工程技术人员利用自己创造的"板杆梁"理论,解决飞行器这类薄壁组合结构的实践,已经过大量部件结构与整机结构的试验所验证,也经过长期的安全飞行实践所证明,在航空航天领域得到广泛认同与应用。
我们基于CAE_X的开发平台,探索飞机结构FEA快速建模的特征设计技术[2]表明,它既能有效地缩短FEA建模周期,也能体现飞机结构力学、计算结构力学的理论与实践。
图1~4表示出一组飞机翼身特征结构的组合模型。
3.2重型机械结构分析的CAE样机技术
我国正在成为一个"世界制造工厂"。
但这并不意味着:
我国已是先进制造技术的专利大国。
我们制造了许多产品,但都是引进发达国家的图纸或生产线;我们甚至不惜花巨资引进全部专利技术,但没有来得及消化,产品已经换代或升级。
由于机械设计与制造过程的复杂性,如何对产品性能进行评定与优化,如何消化专利与制造工艺的"绝巧",已成为专业设计师最关注的事情。
产品的系列化、标准化,从数字化设计来说,最根本的就是建立支撑产品结构设计的CAE数字化样机-可对产品性能进行优化设计的参数化模型。
汽车起重机、矿用载重汽车、军用越野载重汽车,作为一类"大力神"产品,具有其特殊的作业环境,要求良好的力学性能,包括刚度、应力水平、变形、抗干扰性能等。
对于工程设计人员来说,零件、结构件及整机的力学性能如何?
会不会因强度不够造成破坏事故?
汽车起重机的主要承力结构件是吊臂、转台、车架。
矿用载重汽车、军用越野载重汽车的主要承力骨架是整体车架,它们又是许多结构件的组合,包括支撑架、前车架、中车架、尾架及若干子构件。
结构件有限元分析往往只是产品设计的基础分析,整体分析才是工程师面临的最直接、最重要的问题。
汽车起重机整体分析的对象包括若干个主承力结构件和机构(回转、变幅、伸缩、起升等)。
矿用载重汽车与军用越野载重汽车的整体车架分析对象包括了整车的各种严重工况(静满载、转弯、爬坡、刹车等)。
参数化模型使设计人员在设计过程中能较快地预测到整体结构在不同严重工况(路况与作业)下结构的应力与变形,以便完善与优化总体设计,解决自己最急迫关心的技术问题。
我们基于通用的ANSYS/APDL开发平台,探索了建立重型机械结构设计的CAE数字化样机的方法与实施途径[3]。
图5~8所示的正是相应三类重型机械结构简化后CAE数字化样机的FEA整体应力与变形分析的云图与用户界面。
这里,结构件参数的提取是参数化设计的基础,关键是选取能表述结构件几何特征的主要参数。
一般地说,结构件的主要参数包括长、宽、高、关键点、连接条件、板厚、型材截面积、材料与物理特性、载荷工况等。
我们将对这些参数规范化地命名,设置有关的参数名,定义结构件的APDL参数模块;集成所有结构件的参数模块,便构成了产品结构的FEA参数库文件。
这些参数模块的任何参数值的改变,都会引起有关结构件的有限元模型的改变,也就引起整体结构的改变。
系列化的产品便是这些参数的系列变化。
产品结构性能的优化设计便是这些参数的合理匹配及优化。
产品结构件与整体结构的FEA模型产生程序,就是利用ANSYS/APDL语言,引用参数库中相应参数模块,进行CAE二次开发得到的。
3.3先进的航空数字化制造工艺的CAE仿真
飞机的高新性能是与新材料、新工艺的大量使用密不可分的。
特别是,具有高强性能比的复合材料机体结构的制造工艺,高强合金钣金构件的整体超塑成型工艺,高强易脆材料的大型整体构件的高速数控切铣工艺,大型整体壁板的低应力无变形的焊接工艺与其他连接工艺等,都代表着我国航空航天的先进制造能力。
但是,这些先进的制造工艺都是通过先进的数字化CAE模型,进行制造过程的数值仿真,并辅之以少量必需的实物验证试验,才能稳定地应用于航空航天制造工程。
我们仅以航空航天工程使用的高压容器-金属胆复合材料气瓶的设计与制造为例,说明数字化制造的特点和要求[4]。
根据ISO11439设计规范的要求:
建立可用的材料非线性分析方法与流程;建立正确的材料非线性的弹-塑性、应力-应变模型;建立多纤维缠绕层或不同纤维材料构成的材料本构方程与平衡方程;分析纤维缠绕张力作用下的预应力;不同压力工况应包括:
紧缩压力、零压力、工作压力、水压试验压力、最小爆炸压力和平均爆炸压力等;最大的缺陷尺寸,应能确保在循环压力工况下的安全可靠性,同时可保证LBB性能(爆炸前先泄露)等。
这就要求正确地建立各复合材料层的本构关系;对于金属内胆,要采用金属材料双线性各向同性强化模式;必须正确地应用预应力技术,在内壁预先建立一种切向压应力-预应力,并和拉伸的工作切向应力叠加,以大大减少甚至于完全消除切向拉应力,在合成状态建立起切向压应力或压应变。
这样,就能带来一系列静强度和疲劳强度上的优点。
研制某产品的实践表明,我们基于ANSYS平台开发的CAD/CAE软件与美国知名专业技术资询公司(HEI)相比较,针对同一产品的几种不同设计与制造参数,进行七种载荷工况的非线性分析,能够得到相同工程精度的数值结果。
图9、10分别是产品封头及过渡段结构的局部应力云图,它们精细地表明了具有不同缠绕厚度和方向的各个结构层的不同应力状态。
总之,在先进的数字化制造中,基于国际通用的CAE_X开发平台,快速建立CAE数字化样机,往往是各行各业实现自主创新发展的核心技术。
先进的数字化制造是建立在先进的数字化设计与数字化制造工艺上的,必需对设计、材料、环境与制造过程进行精细的、难度极高的CAE数字化仿真。
在航空航天的众多高精尖领域,产品模型化,模型参数化,制造工艺数字化,已是一种常规,需要CAE解决的问题极多。
CAE是大有作为的。
四对我国CAE自主创新发展的若干思考
回顾亲身经历的CAE发展历史,我有如下思考:
(1)我国CAE技术的发展水平与阶段
我国CAE技术的发展获得了历史性的重大进步,它在推动我国四个现代化与建设创新型国家中起到了核心柱石的作用。
没有CAE技术的发展,就没有今天"两弹一星"及航空航天技术等重大工程的诞生与跨越式的发展。
但是,据我观察,我国CAE的发展与应用水平,不管是高精尖技术领域,还是一般民用技术领域,与国外相比,在诸多方面还是处在初级发展阶段。
我国是"制造大国"不是"专利大国"就表明,CAE在建立创新型国家的伟大工程中还有长足的发展空间。
(2)要有发展CAE技术的大措施
国家正在实施的科教兴国战略应该包括CAE的发展战略。
要像重视"两弹一星"及航空航天技术那样,重视发展CAE技术。
实际上,促进CAE发展的措施,就是增强、提高国家核心竞争力的措施,就是促进富国富民强兵的措施。
要以改革开放的大视野、大思维认识CAE自主创新发展。
它与洋为中用、拿来主义、"踏着巨人的肩膀攀登"等,是既对立又统一,对CAE发展是相辅相成、相互促进的。
要建立中长期的国家CAE发展战略和应用研究规划。
要从基础理论、计算机技术与方法、开发平台、行业应用等几个方面着手,做出规划,定好纲要,制定出发展措施。
(3)要建立几个国家级的CAE发展研究中心
我国应该有CAE基础理论创新发展研究中心,若干知名高校具有充分的条件。
我国应该有CAE技术创新发展研究中心,科学院和军工及民用行业的若干技术发展院所都是有实力的。
发展CAE技术,要运用市场经济的杠杆与手段,引进竞争机制。
(4)建立地区、行业或企业级的CAE应用研究中心
实施地区、行业或企业级的CAE技术的ASP服务。
建立若干个CAE技术示范、培训与认证基地。
应用研究中心对国内外先进的CAE技术,按市场经济法则实行拿来主义、"踏着巨人的肩膀攀登",大力促进应用技术开发。
CAE专家应该相对多地聚集于应用研究中心。
(5)建立CAE专家的虚拟联盟与交流平台
我国从事CAE基础理论与实用技术研究与开发的队伍人数不少。
但是,孤军不成合力,缺乏技术交流与培训;许多学非所用;不少CAE精英流失国外。
建立CAE专家的虚拟联盟与CAE发展论坛,形成若干个国家级的CAE学术交流平台,广聚英才,为CAE专家真正提供一个可以施展抱负、发表学术见解的天地。
总之,认真落实科教兴国战略,就应该促进我国CAE在理论创新、技术创新及工程应用创新等方面的健康发展。
我希望,这是本次CAE自主创新发展战略论坛的最高宗旨。
[参考文献]
(1)中国航空工业史丛书,飞机结构强度专业史,1991年。
(2)岳中第,航空组合结构的有限特征建模技术,计算力学学报,第14卷增刊,1997。
(3)岳中第,先进数字化制造中的工程分析及其应用,航空制造技术,2006/06。
(4)岳中第,马宁,基于ISO11439标准及ANSYS平台的CNG气瓶有限元应力分析,航空制造技术,2003/11。
(end)