浅谈核设备缺陷自身高度超声波测量技术.docx
《浅谈核设备缺陷自身高度超声波测量技术.docx》由会员分享,可在线阅读,更多相关《浅谈核设备缺陷自身高度超声波测量技术.docx(17页珍藏版)》请在冰豆网上搜索。
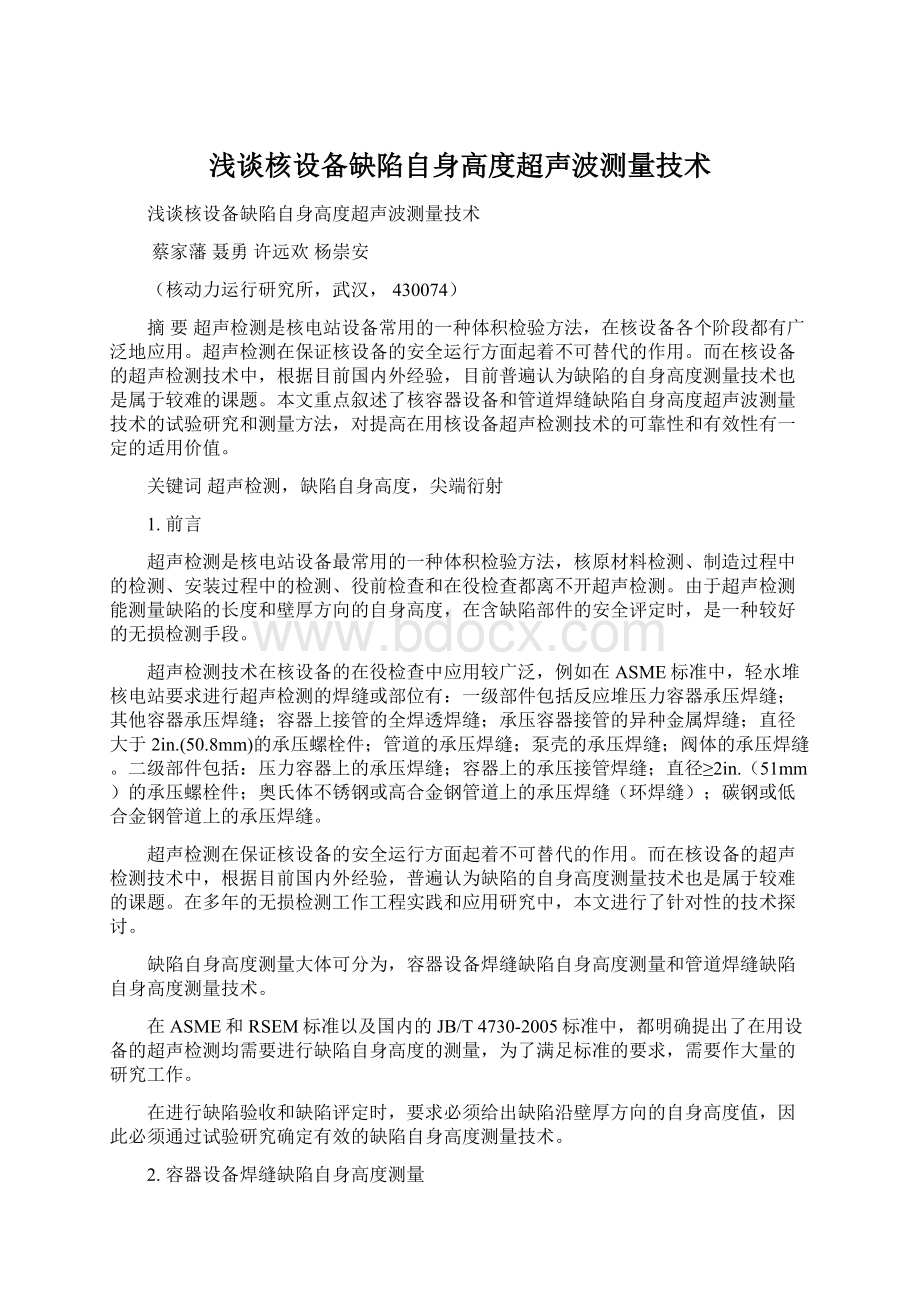
浅谈核设备缺陷自身高度超声波测量技术
浅谈核设备缺陷自身高度超声波测量技术
蔡家藩聂勇许远欢杨崇安
(核动力运行研究所,武汉,430074)
摘要超声检测是核电站设备常用的一种体积检验方法,在核设备各个阶段都有广泛地应用。
超声检测在保证核设备的安全运行方面起着不可替代的作用。
而在核设备的超声检测技术中,根据目前国内外经验,目前普遍认为缺陷的自身高度测量技术也是属于较难的课题。
本文重点叙述了核容器设备和管道焊缝缺陷自身高度超声波测量技术的试验研究和测量方法,对提高在用核设备超声检测技术的可靠性和有效性有一定的适用价值。
关键词超声检测,缺陷自身高度,尖端衍射
1.前言
超声检测是核电站设备最常用的一种体积检验方法,核原材料检测、制造过程中的检测、安装过程中的检测、役前检查和在役检查都离不开超声检测。
由于超声检测能测量缺陷的长度和壁厚方向的自身高度,在含缺陷部件的安全评定时,是一种较好的无损检测手段。
超声检测技术在核设备的在役检查中应用较广泛,例如在ASME标准中,轻水堆核电站要求进行超声检测的焊缝或部位有:
一级部件包括反应堆压力容器承压焊缝;其他容器承压焊缝;容器上接管的全焊透焊缝;承压容器接管的异种金属焊缝;直径大于2in.(50.8mm)的承压螺栓件;管道的承压焊缝;泵壳的承压焊缝;阀体的承压焊缝。
二级部件包括:
压力容器上的承压焊缝;容器上的承压接管焊缝;直径≥2in.(51mm)的承压螺栓件;奥氏体不锈钢或高合金钢管道上的承压焊缝(环焊缝);碳钢或低合金钢管道上的承压焊缝。
超声检测在保证核设备的安全运行方面起着不可替代的作用。
而在核设备的超声检测技术中,根据目前国内外经验,普遍认为缺陷的自身高度测量技术也是属于较难的课题。
在多年的无损检测工作工程实践和应用研究中,本文进行了针对性的技术探讨。
缺陷自身高度测量大体可分为,容器设备焊缝缺陷自身高度测量和管道焊缝缺陷自身高度测量技术。
在ASME和RSEM标准以及国内的JB/T4730-2005标准中,都明确提出了在用设备的超声检测均需要进行缺陷自身高度的测量,为了满足标准的要求,需要作大量的研究工作。
在进行缺陷验收和缺陷评定时,要求必须给出缺陷沿壁厚方向的自身高度值,因此必须通过试验研究确定有效的缺陷自身高度测量技术。
2.容器设备焊缝缺陷自身高度测量
从目前国内外的经验来看,尖端衍射信号测量法,是目前设备焊缝比较通用而有效的一种缺陷自身高度的测量方法。
尖端衍射信号:
根据惠更斯原理,超声波入射到缺陷(如裂纹)上时,在裂纹上下尖端会形成次波源而产生衍射(称为衍射波)。
端点衍射波测量法是通过测量裂纹端点衍射回波的传播时间差值来求得裂纹自身高度的。
具体方法为,从焊缝两侧,分别探测缺陷的上端点和下端点衍射信号(有时也可用上下端点的反射信号进行测量,本文重点讨论尖端衍射信号测量技术),和/或角反射信号:
a)对于较近表面位置的缺陷,主要用60°横波探头进行缺陷自身高度测量,用45°横波探头进行核实。
b)对于较远区域位置的缺陷,主要用45°横波探头进行缺陷自身高度测量,用60°横波探头进行核实。
尖端衍射信号测量技术可以用来测量深埋和表面缺陷的自身高度。
用合适的探头,探测到缺陷的尖端衍射信号,调整增益,使信号幅度至50%~70%。
扫查探头找到上端点衍射信号(M1),记录探头位置和声程/或深度,移动探头,找到下端点衍射信号(M2)的最大回波,记录探头位置和声程/或深度。
对于表面缺陷,可以探测角反射信号(C1)和缺陷的尖端衍射信号。
深埋缺陷的高度测量
对于深埋缺陷见图2-1:
图2-1深埋缺陷探测示意图
-记录声程:
缺陷自身高度=(M2-M1)xCosθ
-记录深度:
缺陷自身高度=(D2-D1)
表面开口缺陷的高度测量
对于表面缺陷,如图2-2:
图2-2表面缺陷探测示意图
-记录声程:
缺陷自身高度=[(M2-M1)xCosθ]/2
=(M2-C1)xCosθ
=(C1-M1)xCosθ
-记录深度:
缺陷自身高度=(D2-D1)/2
=(D2-C1)
=(C1-D1)
3.管道焊缝缺陷自身高度测量技术
根据ASME标准的要求,管道焊缝的检测区域为内壁1/3壁厚的区域,在用设备的超声波检测主要考虑检测从内壁萌生的裂纹,针对这种情况,具体缺陷自身高度测量技术有别于设备焊缝的缺陷自身高度的测量技术。
目前通过试验研究,比较适合于管道焊缝缺陷自身高度的测量技术主要有:
绝对传播时间尖端衍射技术、相对传播时间尖端衍射技术和波型转换技术等。
探头波型选择:
主要使用横波,纵波或波型转换,包括探头在外表面形成爬波。
探头角度:
横波探头,角度为45°~70°之间;
纵波探头,角度为45°~70°之间,大角度探头可以形成外表面爬波或30/70/70波型转换方式。
绝对传播时间技术
如果能发现缺陷的尖端衍射信号,那么就可直接知道缺陷的尖端信号的深度,就可用壁厚直接减去尖端衍射信号的深度,计算缺陷的自身高度,见图3-1。
此技术适合于常规的45°~70°,横波或纵波斜探头检测。
应该还要用大角度外侧表面爬波探头进行核实。
图3-1(a)绝对传播时间测量
位置1:
缺陷根部反射信号
位置2:
探头往前移动时,缺陷面和尖端信号
图3-1(b)绝对传播时间测量技术示意图
相对传播时间技术
如果能探测到缺陷的内侧端角反射信号和缺陷尖端衍射信号,可以用端角反射信号和尖端衍射信号的深度差,计算出缺陷的自身高度。
通常此技术适合于45°~60°的常规横波或纵波探头,对较浅的缺陷效果更好。
见图3-2。
图3-2相对传播时间测量技术示意图
步骤:
1.同时观察到根部反射和尖端衍射信号,见图3-3;
2.测量两个信号的声程差或深度差;
-如果标定时,按声程标定,缺陷自身高度按
公式A计算;
-如果标定时,按深度标定,缺陷自身高度按
公式B计算。
公式A
H=M/COS
公式B
H=d
H=缺陷自身高度图3-3根部反射和尖端衍射信号
=探头折射角
M=根部信号和尖端衍射信号的声程差
d=根部信号和尖端衍射信号的深度差
波型转换技术
波型转换技术的探头为大角度(大于或等于60°)纵波探头,缺陷自身高度的确定可以根据缺陷尖端衍射信号(绝对传播时间技术)或根据包括波型转换在内的其他回波信号的综合判断。
多种回波信号主要包括:
直接缺陷本身回波或尖端衍射波;如果缺陷高度大于6mm,波型转后在缺陷面的反射回波信号(通常的30/70/70),探头本身的35°横波,通过底面转换为发射70°纵波,在从缺陷面反射,被探头接受;内表面的爬波形成的回波。
见图3-5。
图3-4(a)波型转换测量技术示意图
较大缺陷
∙较强的内表面爬波信号
∙较强的缺陷面的波型转换反射信号(30/70/70)
∙较强的直接纵波尖端衍射信号
较小缺陷
∙较强的内表面爬波信号
∙较弱的缺陷面的波型转换反射信号
∙无直接纵波尖端衍射信号
30/70/70波型转换原理如下图:
图3-4(b)波型转换测量技术示意图
波型转换测量技术的探头主要形式有:
Ø左右分布的标准双晶纵波斜探头,主要可优化直接纵波;
Ø前后分布的标准双晶纵波探头,主要可优化波型转换波;
Ø单晶纵波探头(WSY70),主要可优化内表面爬波。
小结:
不是仅用一种测量技术就能很有效地对缺陷高度进行准确的测量,应该使用多种探头对缺陷进行自身高度测量,综合分析判断。
主要步骤如下:
Ø用较小角度(45-60)探头,尽量探测缺陷的内表面角反射信号,利用这个信号回波可以粗略测量壁厚;
Ø沿缺陷长度方向扫查,观察缺陷的特征,注意缺陷反射回波方向和位置,是否有分支等;
Ø扫查探头,探测角反射信号。
继续往前扫查探头直到探测到缺陷的尖端衍射信号;
Ø换用较大角度探头(60°-70°和外表面爬波);
Ø所有缺陷自身高度都需要用另一种探头或反方向扫查确认,假如不能确认,测量技术应该要进行改进,如:
换小探头,改变频率和焦距等。
4.试验研究
4.1试验方法
使用仪器设备:
CTS-2000数字超声仪和TOMOSCAN-III多通道超声检测仪
探头:
45°和60°横波斜探头
耦合剂:
CG-88
试块:
(1)在试块表面加工一定深度的EDM槽,材料为碳钢,槽宽0.2mm;
(2)在试块内部加工一定自身高度的人工裂纹,材料为碳钢;
(3)在试块上加工一定深度的疲劳裂纹,材料为碳钢,并在此表面上堆焊6mm左右的不锈堆焊层。
试验方法的基本要求:
CTS-2000数字超声仪配合探头在分别试块的两个探测面(裂纹开口侧和裂纹背面侧),或深埋缺陷的任意侧进行扫查;TOMOSCAN-III多通道超声检测仪配合探头在试块的探测面进行自动扫查。
从裂纹背面侧进行扫查
从裂纹背面侧进行检测时,就会出现缺陷端点衍射信号和缺陷根部形成的角反射两个信号,端点衍射信号的声程为M1,根部反射信号声程为M2。
见图4-1。
缺陷高度公式
或
(T为试块厚度)
图4-1表面开口缺陷自身高度衍射波测量法
从裂纹开口侧进行扫查
对于如图4-2的表面开口裂纹检测,从裂纹开口侧进行扫查:
图4-2表面开口缺陷自身高度衍射波测量法
如果用横波探头从裂纹开口侧检测时,会出现缺陷端点衍射信号(其声程为M1),以及如果入射波为横波,在端点处经波型转换成纵波(L),再在底面反射并沿原路返回探头的回波(其声程为M2)。
见图4-2,有两种方式计算出缺陷的自身高度,也就是说可以两种方式可以互相核实。
a.直接根据端点衍射信号声程计算自身高度H:
b.根据衍射波声程和波型转换回波声程计算自身高度H:
CL为纵波声速;CS为横波声速,T为壁厚。
深埋缺陷的高度测量
采用横波斜探头从试块一侧进行扫查,分别探测缺陷的上下端点衍射信号,并记录上下端点的信号回波波形图,记录信号的深度值。
其中试块三个试块分别预制了一个深埋的人工裂纹缺陷,试块示意图见图4-3(H为预制裂纹高度)。
图4-3深埋缺陷试块示意图
堆焊层下缺陷高度测量
如果从堆焊层侧检测堆焊层下缺陷,考虑到不锈钢堆焊层对超声波传播的影响,采用纵波双晶探头对堆焊层下裂纹高度测量有较好的效果。
例如,一块试块在碳钢上堆焊有6mm左右的不锈钢堆焊层见图4-4,并加工有两个高度分别为6mm和8mm的疲劳裂纹。
用Tomoscan-III多通道超声波探伤仪,配上纵波双晶斜探头在堆焊层表面上进行扫查,记录B-扫显示,并分析信号特征,测量裂纹的自身高度。
图4-4堆焊层下缺陷试块图
4.2试验结果
(1)表面开口裂纹自身高度测量结果见表4-1
注:
试块图同图4-1,试块TD009线槽d=5mm;TD007线槽d=15mm;TD008线槽d=25mm
(线槽宽度为0.2mm);下表中S代表横波,L代表纵波。
表4-1缺陷自身高度测量试验结果
编号
试块
探头
仪器
探测面
波型
缺陷自身高度(mm)
实际高度
(mm)
误差
(mm)
说明
备注
1
TD009
2MHz/45°/S
CTS-2000
裂纹背面侧
S
4.84
5
0.16
波形见图4-5
2
2MHz/45°/S
TOMOSCAN
裂纹背面侧
S
4.7
5
0.3
波形见图4-6
3
2MHz/45°/S
CTS-2000
裂纹开口侧
S
5.08
5
0.08
4
TD007
2MHz/45°/S
CTS-2000
裂纹背面侧
S
14.44
15
0.56
5
2MHz/45°/S
CTS-2000
裂纹开口侧
S
15.52
15
0.52
S/L转换
S/L
14.92
0.08
6
2MHz/45°/S
TOMOSCAN
裂纹开口侧
S
14.9
15
0.1
S/L转换
S/L
15.9
0.9
7
2MHz/60°/S
CTS-2000
裂纹背面侧
S
15.70
15
0.70
8
4MHz/45°/S
CTS-2000
裂纹开口侧
S
15.20
15
0.20
波形见图4-7
S/L
14.90
0.10
S/L转换
9
TD008
4MHz/45°/S
CTS-2000
裂纹背面侧
S
25.70
25
0.70
10
4MHz/45°/S
CTS-2000
裂纹开口侧
S
25.35
25
0.35
11
2MHz/60°/S
CTS-2000
裂纹开口侧
S
25.11
25
0.11
12
2MHz/45°/S
CTS-2000
裂纹开口侧
S
24.55
25
0.45
13
2MHz/45°/S
TOMOSCAN
裂纹开口侧
S
25.1
25
0.1
注:
测量高度值与实际高度值偏差最大为0.90mm。
表4-1中的选取了几组试验的波形图及其测高计算:
从表面开口槽的背面进行扫查:
试验编号1
试验波形图见图4-5:
根部信号
图4-5
●运用公式
=30.08-25.24得出缺陷自身高度4.84mm。
●S1、S2均为槽的尖端衍射信号,其声波传播路径图见图2-2。
从表面开口槽的背面进行扫查:
试验编号2
使用TOMOSCAN-III仪器和2MHz/45°/S探头对TD009试块A面补充扫查图如下,结果类似。
试验波形图见图4-6。
图4-6
●运用公式
得出缺陷自身高度4.7mm。
●S1为槽的尖端衍射信号
从表面开口缺陷的同侧进行扫查:
试验编号8
图4-7
●有两种方式计算出缺陷的自身高度。
a.直接根据端点衍射信号声程计算自身高度H:
运用公式
得出缺陷自身高度15.20mm。
b.根据衍射波声程和波型转换回波声程计算自身高度H:
运用公式
=30-8.19×5.9/3.2=14.90mm。
●S1为线槽尖端衍射信号,S2波是横波入射至线槽尖端衍射出纵波,纵波至底面返回线槽尖端,在线槽尖端转换成横波返回,被探头接收的信号
(2)对深埋缺陷自身高度测量结果
采用KK公司横波450,频率4MHz的探头从试块上表面进行扫查分别探测缺陷的上下端点衍射信号,并记录上下端点的信号回波波形图,记录信号的深度值。
其中试块TD05-3-02上下端点回波图分别见图4-8和4-9。
试块图见4-3。
图4-8TD05-3-02上端点回波图4-9TD05-3-02下端点回波
●运用公式:
H=d=12.73-9.67=3.06mm
试块中深埋缺陷的自身高度测量值见表4-2。
表4-2深埋缺陷自身高度测量值
试块编号
深埋缺陷实际高度值(mm)
下端点深度值(D2mm)
上端点深度值(D1mm)
缺陷高度测量值(D2-D1mm)
误差
(mm)
TD05-3-02
3
12.73
9.67
3.06
+0.06
TD05-3-04
4
13.93
10.02
3.91
-0.09
TD05-3-05
7
17.61
10.09
7.52
+0.52
注:
测量高度值与实际高度值偏差最大为0.52mm。
(3)对堆焊层下缺陷测量结果
用70°双晶纵波斜探头进行扫查时,其B-扫图如图4-10。
试块图见图4-4。
图4-10B-扫图
●根据尖端衍射信号测量高度值为C1#=8.6mm,和C2#=6.7mm。
非常接近8mm(C1#)和6mm(C2#)的实际高度。
误差小于+/-1mm。
4.3试验结果分析
上述试验中,可以发现根据缺陷尖端信号测量技术测量的缺陷自身高度误差小于+/-1mm以内。
由于加工的是模拟自然裂纹缺陷,和真实的裂纹缺陷有一定的差异,在某些情况下很难发现真实缺陷的尖端衍射和端点反射信号,裂纹缺陷的形状决定了能否发现尖端信号的主要因素。
为了更好的发现缺陷尖端信号,往往必须将扫查灵敏度提高到足够高,才能发现尖端信号,一般将灵敏度提高,但须保持本底噪声低于屏幕的20%以下,观察缺陷的动态回波波形。
在不能发现尖端信号时,应该采用当量法或-6dB法测量
缺陷的自身高度测量不能单靠一种方法就能解决问题,必须用不同的测量技术,不同的探头,不同的扫查方向和动态回波综合判断,才能较好地对缺陷自身高度进行测量。
而自动扫查更容易对缺陷自身高度进行测量。
5应用
通过对表面开口缺陷、深埋缺陷和堆焊层下缺陷的自身高度测量试验研究发现,只要缺陷形状和取向适当,探头选择合适,缺陷自身高度测量精度较高。
为了提高对较小缺陷自身高度测量精度,在信噪比满足要求的条件下,尽量选用较高频率探头,如4~5MHz频率;并选用宽带窄脉冲。
根据研究成果,目前国内用于反应堆压力容器检查的堆焊层下缺陷自身高度测量技术采用70°纵波双晶斜探头探测和测量,再用45°纵波双晶斜探头进行高度核实,测量技术采用尖端衍射技术。
能够测量大于或等于~5mm的缺陷自身高度。
对于筒体焊缝的其他区域采用45°和60°横波单晶探头,并用尖端衍射技术进行缺陷自身高度测量。
6.结论
缺陷自身高度的测量技术是在役设备在运行期间必须使用的超声检测手段,这对设备中缺陷的评定和寿期评估有着重要意义。
尖端衍射缺陷自身高度测量技术、相对传播时间尖端衍射缺陷自身高度测量技术、绝对传播时间尖端衍射缺陷自身高度测量技术和波型转换缺陷自身高度测量技术,根据不同的应用对象,有较高的测量精度。
缺陷自身高度测量与缺陷形状和缺陷取向有密切的关系,并且决定了高度的测量准确度
参考文献
1.无损检测手册李家维陈积懋主编
2.无损检测(高级教程)上海锅炉厂上海无损检测技术服务部
3.JB/T47302005
4.ASMEXI2004年版
5.RSEM1997年版