常压岗位操作法.docx
《常压岗位操作法.docx》由会员分享,可在线阅读,更多相关《常压岗位操作法.docx(91页珍藏版)》请在冰豆网上搜索。
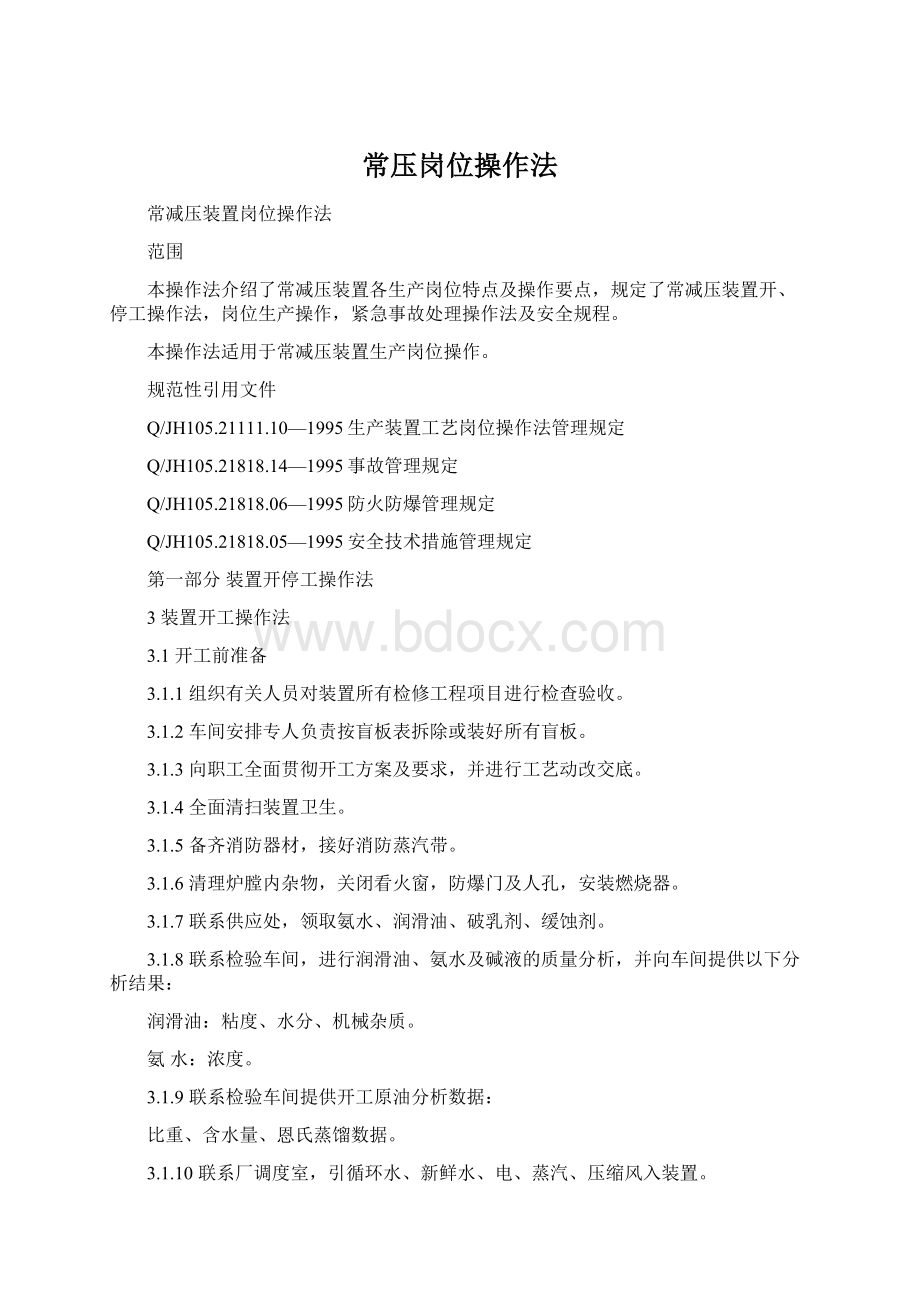
常压岗位操作法
常减压装置岗位操作法
范围
本操作法介绍了常减压装置各生产岗位特点及操作要点,规定了常减压装置开、停工操作法,岗位生产操作,紧急事故处理操作法及安全规程。
本操作法适用于常减压装置生产岗位操作。
规范性引用文件
Q/JH105.21111.10—1995生产装置工艺岗位操作法管理规定
Q/JH105.21818.14—1995事故管理规定
Q/JH105.21818.06—1995防火防爆管理规定
Q/JH105.21818.05—1995安全技术措施管理规定
第一部分装置开停工操作法
3装置开工操作法
3.1开工前准备
3.1.1组织有关人员对装置所有检修工程项目进行检查验收。
3.1.2车间安排专人负责按盲板表拆除或装好所有盲板。
3.1.3向职工全面贯彻开工方案及要求,并进行工艺动改交底。
3.1.4全面清扫装置卫生。
3.1.5备齐消防器材,接好消防蒸汽带。
3.1.6清理炉膛内杂物,关闭看火窗,防爆门及人孔,安装燃烧器。
3.1.7联系供应处,领取氨水、润滑油、破乳剂、缓蚀剂。
3.1.8联系检验车间,进行润滑油、氨水及碱液的质量分析,并向车间提供以下分析结果:
润滑油:
粘度、水分、机械杂质。
氨水:
浓度。
3.1.9联系检验车间提供开工原油分析数据:
比重、含水量、恩氏蒸馏数据。
3.1.10联系厂调度室,引循环水、新鲜水、电、蒸汽、压缩风入装置。
3.1.11按工艺要求安装经校验合格的压力表、温度计。
3.1.12开工前一天,各机泵、风机油箱装好润滑油。
3.1.13准备好加热炉点火棒。
3.1.14配制浓度为2%的破乳剂溶液。
3.1.15准备好岗位记录及交接班日记。
3.2开工前的检查
3.2.1塔
3.2.1.1检查塔盘、受液盘、抽出或返塔线、塔底及抽出口确无杂物。
3.2.1.2检查塔盘及加固件是否牢固,塔盘水平度是否合格,浮阀是否齐全灵活。
3.2.1.3检查回流分布管、蒸汽分布管开孔是否畅通,方向准确。
3.2.1.4检查压力表、液面计导管是否畅通,浮球是否灵活好用。
3.2.2加热炉
3.2.2.1检查炉管、回弯头、挡火墙是否完好。
3.2.2.2检查吊挂钩、支承架、加固件是否牢固。
3.2.2.3确保炉膛及火盆内无杂物。
3.2.2.4检查防爆门、通风门、看火窗、烟道档板是否安装合理好用。
3.2.2.5检查送风蝶阀调节是否灵活,将蝶阀开至1/3,烟道档板开至2/3。
3.2.2.6检查压力表、负压表是否备齐好用。
3.2.2.7检查消防蒸汽、炉膛灭火蒸汽是否好用。
3.2.2.8检查油、气火嘴是否安装无误,并用蒸汽吹扫火嘴,检查其是否畅通无泄漏。
3.2.2.9检查吹灰系统是否好用。
3.2.2.10按盲板表检查盲板拆装是否准确无误。
3.2.3容器
3.2.3.1检查容器内及各出入口管线内有无杂物。
3.2.3.2检查压力表、液位计等导管是否畅通,内部测量表是否安装准确。
3.2.3.3检查电脱盐罐内电极板、吊挂、进油分配器等内部元件安装是否合格。
3.2.3.4检查设备接地线安装是否合格。
3.2.4冷换设备
3.2.4.1检查管线连接、阀门安装是否正确。
3.2.4.2检查压力表及仪表一次测量元件安装是否正确。
3.2.4.3检查设备接地线安装是否合格。
3.2.5机泵
3.2.5.1检查各电机及泵座地角螺栓是否紧固。
3.2.5.2检查对轮是否装好,附件是否齐全。
3.2.5.3检查润滑油、脂是否注好。
3.2.5.4检查压力表是否校正装好,放空阀、扫线阀、预热小管及阀门安装是否正确。
3.2.5.5检查盘车是否灵活。
3.2.6工艺管线
3.2.6.1按盲板表检查各盲板拆装是否准确。
3.2.6.2检查管线连接是否正确,法兰垫片是否对正,各部螺丝是否紧固。
3.2.6.3检查各阀门盘根是否压好,开关是否灵活好用。
3.2.6.4检查各压力表、温度计、热电偶是否校正装好。
3.3空载试运
3.3.1新安装或经检修的机泵试运
3.3.1.1空运时间要求:
新安装的机泵试运不低于4小时,经检修的机泵试运不低于2小时。
3.3.1.2检查内容
电流、压力指示是否稳定正常;
各部螺栓有无松动;
泵体震动是否合格;
阀门开关是否灵活好用;
冷却、润滑系统是否正常;
轴承是否过热、端封是否渗漏、泵体内有无异音。
3.3.2新安装或经检修的炉风机试运
3.3.2.1空运时间要求:
新安装的风机试运不低于4小时,经检修的风机试运不低于2小时。
3.3.2.2检查内容
a)电流、压力指示是否稳定正常;
b)机体震动是否合格;
c)排风量是否正常;
d)各部螺栓有无松动;
e)机体、风道有无漏点;
f)轴承是否过热、润滑系统是否正常、机体有无异音;
g)蝶阀、风门就地调节是否好用。
3.3.3新安装或经检修的空冷风机试运
3.3.3.1空运时间要求:
新安装的空冷风机试运不低于4小时,经检修的空冷风机试运不低于2小时。
3.3.3.2检查内容
电流指示是否稳定正常;
机械震动是否合格;
各部螺栓有无松动;
轴承是否过热、转动有无异音;
风翅角度调整是否灵活好用。
3.3.4电脱盐电气设备空运
3.3.4.1准备工作
a)罐内、外进行全面检查;
b)罐内进行通风置换,测爆合格;
c)各出、入罐阀门关严;
d)低液位报警开关切除。
3.3.4.2检查内容
a)空载电流、电压是否正常,空载电流不大于5A为合格。
b)罐内引线构件绝缘性能是否良好。
c)安全保护系统是否灵敏可靠。
d)接地线是否牢固可靠。
3.3.4.3注意事项
a)测爆合格,方可进行空载试验。
b)空运时专人监护
c)送电时,若一次送不上,不能连续送,待找到故障,处理后方可再次送电。
d)空运合格后,封闭人孔。
3.4贯通与试压
3.4.1贯通试压的目的
3.4.1.1用蒸汽贯通和吹扫管线内的杂物,确认流程是否正确,检查管线是否畅通,阀门开关是否好用,压力表指示是否正确。
3.4.1.2用蒸汽试压,检查设备管线的人孔、阀门、法兰、焊口有无泄漏。
3.4.1.3对于高温、高压或经检修未试压的设备及管线用水试压,检查人孔、法兰、焊点、焊缝等有无泄漏。
3.4.2试压规定
3.4.2.1新建成或炉管经过检修后的加热炉用水试压,一般检修后用蒸汽试压。
3.4.2.2新增设或检修后的压力容器必须用水试压,一般容器装水试漏。
3.4.2.3新增设或检修后的冷换设备应进行单体水试压或气密试验。
3.4.2.4新增设或检修过的工艺设备,管线应试压。
3.4.3试压标准
3.4.3.1用蒸汽试压时,试验压力为最高操作压力的1.1倍。
3.4.3.2用水试压时,试验压力为最高操作压力的1.25~1.5倍。
3.4.3.3工艺管线用蒸汽试压为入装置主蒸汽的最高压力,即大于0.8Mpa。
3.4.4贯通与试压前的准备
3.4.4.1按规定线路,改好贯通试压流程。
3.4.4.2联系仪表,关闭各仪表引线。
3.4.4.3联系检修,装好有关泵入口过滤网。
3.4.4.4联系调度,保证动力供应,
3.4.4.5做好水试压所用机泵启运前的准备工作,
3.4.5注意事项
3.4.5.1贯通前,关闭各质量流量计保护阀,改走副线。
3.4.5.2联系仪表班,关闭各取压点阀,以免损坏仪表。
3.4.5.3贯通前,将加热炉火咀卸下,待管线吹扫干净后,再安装上,并用蒸汽贯通检查。
3.4.5.4关键设备和仪表调节阀改走副线,待管线吹扫干净后,再恢复流程,以免有杂物造成堵塞。
3.4.5.5冷换设备单程给汽时,另一程要打开排凝或放空,以免因水受热汽化,造成超压损坏设备。
3.4.5.6给汽前,必须排净蒸汽线内凝结水。
缓慢给汽,以免出现水击或给汽过快损坏设备。
3.4.5.7试压前,关闭各安全阀的保护阀。
试压后再打开,以免安全阀超压启跳。
3.4.5.8试压前,一定要排净系统内空气,以免漏点不易发现。
3.4.5.9水试压时,注意机泵电流,避免电机因超载造成跳闸或烧毁。
3.4.5.10暖塔或塔正压试验时,要缓慢给汽,避免因给汽过快损坏塔盘。
3.4.5.11塔和容器试压时,严禁超压。
3.4.5.12设备、管线憋压必须达到标准半小时后,经检查确认合格,方可泄压。
3.4.5.13试压结束后,排净系统内存水。
3.4.6贯通与试压流程:
3.4.7减压系统抽真空试验
3.4.7.1减压塔正压试验合格并放空结束后,可进行抽真空试验。
3.4.7.2引抽真空蒸汽至抽空器阀前,蒸汽压力0.8Mpa~0.9Mpa,低点少量放空。
3.4.7.3减顶水封罐加满水,溢流至减顶油罐后,关小给水阀,在减顶油脱水线少量放空。
3.4.7.4抽真空系统七台冷凝器引循环水,投入正常使用。
3.4.7.5按正压试验流程进行抽真空试验,但二级冷凝器瓦斯放空阀及减顶罐瓦斯放空阀打开。
3.4.7.6抽空器给汽要缓慢。
3.4.7.7抽空器的开启顺序为先开二级,再开一级,为考察各台、组抽空器的能力,需分组试验,再联合试验。
3.4.7.8抽空器系统试验结束合格后,关闭二级瓦斯放空阀及减顶罐瓦斯放空阀,关闭各抽空器给汽阀,再进行气密试验24小时,真空度下降0.2~0.5Mpa为气密合格。
3.4.7.9试验结束后,缓慢消除真空,水封罐停止加水,抽真空蒸汽在低点少量放空排凝,各冷却器继续给水,以便开工使用。
3.5开工操作
3.5.1进油前的准备
3.5.1.1班长岗位
a)联系调度请示进油时间,产品方案。
b)负责各岗位之间的联系和协调工作。
c)对开工各步骤,各岗位改好的流程认真做好检查。
d)各消防蒸汽线给汽末端少量放空。
e)检查各排凝阀是否关死,以防跑油。
3.5.1.2常压司塔
a)改好如下流程并反复检查,确保准确无误,严禁跑油和串油。
原油罐区→自压入装置→原油泵→脱前换热器→电脱盐罐(V-10/1、2)→脱后换热器→初馏塔(T-1)→初底泵(P-4)→初底换热器→常压炉(F-1)→常压塔(T-2)→常底泵(P-13)→减压炉(F-2)
b)初、常顶瓦斯改放空,待正常开工后再改到加热炉。
c)其余各系统流程按照开工要求予以改通。
3.5.1.3司炉岗位
a)自罐区收燃料油至燃料油罐液面80%,开燃料油泵,建立燃料油系统循环,准备好点火柴油及点火棒。
b)雾化蒸汽引至炉前低点排凝,末端少许放空。
c)过热蒸汽引至炉前低点排凝,炉上放空。
3.5.1.4减压司塔
a)改好如下流程并反复检查,确保准确无误,严禁跑油和串油。
b)
常底泵(P-13)→减压炉(F-2)→减压塔(T-4)→减底泵(P-19)→减渣换热器→减渣水冷器→开路循环线→去原油罐区
→减渣出装置阀关
→闭路循环线关闭
c)其余各系统流程按照开工要求予以改通。
d)减顶油罐加水水封。
3.5.1.5一脱三注岗位
a)检查本岗位的流程是否正确。
b)准备各种化学药剂,配制一定浓度。
c)引新鲜水至注水泵前。
d)改好注氨、注破乳剂及注缓蚀剂流程。
3.5.1.6司泵岗位
a)各泵准备至备用状态。
b)做好原油泵及塔底泵的启动准备。
3.5.1.7各岗位都要注意各低点排凝阀,务必全部关死。
3.5.2装置进油循环操作
3.5.2.1班长岗位
a)与罐区联系,引原油进装置,按预定的进油时间,通知司泵工启动原油泵,进行开路循环。
b)原油泵启动后,检查管线有无问题。
c)塔底(T-1、T-2、T-4)液面升到2/3时,通知泵工启动P-4、P-13、P-19。
d)协调各岗位稳定操作。
e)进炉后,通知司炉工两炉各点一个火咀,保持循环温度80-90℃
f)改闭路循环前,指示三注岗位开始向电脱盐罐装油。
3.5.2.2常压司塔
根据指令,打开原油入装置阀,原油泵启动后,沿进油路线,全面检查原油系统。
原油入塔前,依次打开T-1、T-2塔底放空阀,专人脱水,见油即关闭。
初底泵启动后,全面检查初底油系统。
控制两塔液面80%,保持原油分支流量均匀稳定。
经常对照现场塔底浮球及室内指示,确认液面实际位置,以防满塔或抽空。
3.5.2.3司炉岗位
a)原油进入加热炉后,全面检查炉进料系统。
b)控制装置进油流量130t/h,平衡分支流量,保持入口分支压力平衡且稳定。
c)点炉前向炉膛吹汽15分钟,到烟囱冒汽为止,防止点火闪爆,提高烟囱抽力,烟道挡板开三分之二。
d)控制燃料油压力0.6Mpa,雾化蒸汽压力0.7Mpa。
e)根据班长指示,原油入炉后,常炉、减炉各点一个火咀,维持炉出口温度80~90℃。
f)点火时,燃烧器下严禁站人,免得回火伤人。
g)火焰突然熄灭时应关闭油咀,向炉内吹汽3-5分钟,再重新点火。
3.5.2.4减压司塔
a)原油入T-4前,打开塔底放空阀,专人脱水,见油即关闭。
b)启动塔底泵后,全面检查减底油系统。
c)控制减渣水冷器出口温度60~70℃。
3.5.2.5一脱三注岗位
a)引原油入装置后,待改闭路循环前,开电脱盐罐入口阀,按装油步骤装油。
b)装油时罐顶放空专人看管,免得冒油污染环境,见油后立即关放空阀。
c)装油后检查整个系统,有无问题,及时汇报并处理。
d)装油检查无问题,请示班长送电,并检查各部位运行情况。
无问题后,并入系统。
3.5.2.6司泵岗位
原油引入装置后,打开原油泵出口阀,待原油自压流经泵体后,再启动原油泵,同样方法依次启动初底泵、常底泵、减底泵。
加强四台循环泵及燃料油泵的检查与维护。
冷循环后期,循环泵切换运行,以免升温后抽空。
3.5.3闭路升温热循环
3.5.3.1闭路升温应具备的条件
a)系统循环已经建立,各部流量、压力平稳。
b)三塔液面控制平衡,并保持在80%左右。
c)设备、管线无泄漏,机泵及仪表运行状态完好。
d)渣油水冷器采样分析含水量小于2.5%。
3.5.3.2闭路升温的目的
进一步脱除系统内的存水。
进一步考验设备、仪表,并进行设备热紧。
为再升温,切换原油开侧线做准备。
3.5.3.3闭路循环流程
原油入装置阀关闭→原油泵→脱前换热器→电脱盐→脱后换热器→初馏塔→初底泵→初底换热器→
→常压炉→常压塔→常底泵→减压炉→减压塔→减底泵→减渣换热器→减渣水冷器→闭路循环线→原油泵
→减渣出装置阀关
→开路循环线关闭
3.5.3.4班长岗位
a)指挥常压司塔岗位改闭路循环。
b)指挥司炉岗位升温。
c)联系调度开路循环线给汽扫线,原油线给汽伴热。
3.5.3.5常压司塔
a)根据指令缓慢打开闭路循环线阀门,同时缓慢关闭开路循环阀和原油入装置阀,即开路循环改为闭路循环。
b)根据塔顶压力上升情况,增开空冷风机,增开冷却器给水,控制塔顶压力<0.06Mpa,塔顶冷后温度35~40℃。
c)平稳控制三塔液面。
d)经常检查对照塔顶压力及V-1、2、3界面的一、二次表指示,确保准确。
3.5.3.6司炉岗位
a)常压炉增点火咀,开始升温。
b)常压炉增点火咀时,点燃对称火咀,利于炉膛温度均衡,减压炉仍然维持一个火咀。
c)升温速度:
200℃以前升温速度为30℃/h,200℃以上升温速度为40℃/h。
d)保持进炉分支流量均匀,炉出口温度均匀上升。
3.5.3.7减压司塔
a)控制渣油水冷器出口温度80~90℃。
b)检查减顶抽真空系统流程及减顶罐水封情况。
c)抽真空蒸汽加强低点排凝,做好抽真空前的一切准备工作。
3.5.3.8一脱三注岗位
a)详细检查电脱盐系统情况。
b)配合其他岗位开工。
3.5.3.9司泵岗位
a)检查塔底泵运行情况及备用泵预热情况,备用泵盘车。
b)炉出口温度达到120℃时,塔底备用泵切换一次。
c)升温过程中,塔底泵易抽空,及时发现处理。
3.5.4恒温脱水及恒温热紧
3.5.4.1班长岗位
a)常压炉出口温度达到200℃,进行恒温脱水2小时。
b)常炉出口温度达到250℃后,联系有关单位进行恒温热紧2小时,组织有关岗位人员检查设备管线泄漏情况。
c)指挥常压司塔岗位,减压司塔岗位每两小时活动一次换热器副线,每次15分钟。
d)指挥司泵岗位,常炉出口温度达到200℃时,再切换一次备用泵。
3.5.4.2常压司塔
a)平稳控制三塔液面,如液面低于40%时,联系厂调,开原油泵入口阀,向装置内补油至三塔液面80~90%。
b)初、常顶温度达到90℃时,启动回流泵,及时向塔顶打回流,控制好塔顶温度。
c)当初、常顶温度上升,塔顶压力平稳,塔底无响声,塔底泵不抽空,V-1、2、3界面稳定,切水量显著减少,原油含水分析小于1%,说明水分已脱净可以继续升温。
d)换热器副线每两小时活动一次,每次15分钟。
e)全面复查侧线流程及回流流程,打开各侧线馏出口上线阀,各侧线水冷器给水。
f)排净各回流线内存水。
3.5.4.3司炉岗位
a)常压炉出口温度达到200℃,恒温脱水2小时。
b)恒温脱水结束后,常炉出口以40℃/h的速度升温至250℃,恒温热紧2小时。
c)自罐区收燃料油至燃料油罐液面80%。
3.5.4.4减压司塔
b)控制减渣水冷器出口温度80-90℃。
c)换热器副线每两小时活动一次,每次15分钟。
d)全面复查侧线流程及回流流程。
e)排净各回流线内存水。
f)联系厂调度室,引外援回流入减一线集油箱,恒温热紧结束后,启动减一线泵,建立减一线回流循环。
3.5.4.5一脱三注岗位:
电脱盐罐继续送电运行。
3.5.4.6司泵岗位
a)排净各塔顶,侧线回流泵内的存水及空气。
b)做好各塔顶,侧线回流泵的启运准备工作。
3.5.5再升温,切换原油开侧线。
3.5.5.1班长岗位
a)250℃恒温热紧结束后,指挥司炉岗位继续升温。
b)常压炉出口温度达到300℃时,开始常底给吹汽。
c)减炉升温后,减压塔开始抽真空。
d)当常压炉出口温度达到320℃时,回流建立正常,通知常压、减压司塔岗位改开路。
e)联系调度,污油线扫线。
f)根据侧线来油情况,指挥常压、减压司塔岗位改开侧线。
g)及时与厂调联系油品外送工作,防止憋压。
h)联系化验进行质量分析。
3.5.5.2常压司塔
a)密切注视蒸、常顶压力、温度,严格控制塔顶压力在0.08Mpa以下,平稳控制塔顶温度在指标范围内。
b)严格控制蒸、常顶水冷器出口温度40℃以下,防止温度过高瓦斯量过大,油水分离器放空线喷油。
c)常压炉出口温度达到300℃时,常压塔开始吹入少量蒸汽。
随炉出口温度及原油量的逐步提高,逐步增加吹汽量,直到工艺卡片要求的指标,过热蒸汽入炉压力平稳控制在0.25~0.3Mpa以内。
d)分别启动常一中、常二中泵建立正常中段回流。
e)常压炉出口温度达到320℃时,改开路,缓慢打开原油入装置阀同时关闭闭路循环线阀,开关阀要与减压岗位开渣油出装置阀同步进行,以防憋压。
f)根据汽提塔来油情况,自上而下逐一启动侧线泵,开侧线出装置。
g)开侧线后,及时检查油品颜色,做好质量分析,本着宁轻忽重的原则控制好产品质量。
h)按工艺卡片的要求,控制好产品冷后温度。
3.5.5.3司炉岗位
a)恒温热紧结束后,常炉以50℃/h的速度升温至365℃
b)塔底给吹汽后及时关闭过热蒸汽放空阀。
c)切换原油正常开路后,减炉增点火咀,以50℃/h的速度升温至400℃。
d)切换原油正常开路后,以50t/h的速度提原油加工量到正常处理量。
e)升温过程中,及时均匀增点火咀,保持各路分支出口温度均匀,尤其是切换原油开路后,由于炉进料温度的降低及原油量的提高,被加热介质需要热量急剧增加,一定要控制好炉温稳定上升,防止炉温下降,影响开工速度。
3.5.5.4减压司塔
a)减压炉升温后,随减炉出口温度的升高,减压塔开始抽真空。
减炉出口温度与减顶真空度对应关系:
减炉出口温度℃280320380400
减顶真空度Mpa0.0260.040.0530.09
b)减压塔开始抽真空后,通过调节减一线回流量控制减顶温度不高于70℃,用减一线回流水冷器水量控制回流温度55~60℃。
c)常压炉出口温度达到320℃时,与常压岗位密切配合,缓慢打开渣油出装置阀,改正常开路。
d)减炉出口达到360℃,减压塔底开始少量给吹汽。
e)减压塔各部温度上升后,减三线集油箱有液面时,开启减一中、减二中泵,建立中段回流。
f)根据回流建立情况,依次送减一、二、三线经冷蜡线出装置,控制好出装置温度70~80℃。
g)严格控制渣油出装置温度85~95℃。
h)减顶罐来油后,及时启动减顶泵,送减顶油出装置。
3.5.5.5司泵岗位
a)根据班长指令,依次启动各回流泵及各侧线出装置泵。
b)作好各运行泵的检查维护及备用泵的预热盘车工作。
3.5.6调整操作
3.5.6.1班长岗位
a)指挥并协调各岗位调整操作。
b)通知三注岗位,投注破乳剂,新鲜水,塔顶注氨,注缓蚀剂。
c)通知常压岗位开初馏塔侧线。
3.5.6.2常压司塔
a)根据负荷情况及初侧产品质量分析情况,投用初馏塔侧线。
b)调节各回流量、侧线泵、控制好产品质量在规定指标内。
c)打开各后冷器冷却水,控制各油品冷后温度在正常指标内。
d)操作正常后,初、常顶低压瓦斯改去常炉烧火。
3.5.6.3司炉岗位
a)稳定控制常炉、减炉出口温度在规定指标内。
b)进行火焰调节。
c)保证炉膛温度均匀,炉出口分支温度平衡。
d)增点低压瓦斯火咀。
3.5.6.4减压司塔
a)调整抽真空系统,保证减顶的高真空度。
b)调整各回流及侧线量,平稳控制塔顶、各侧线温度在工艺卡片要求范围。
c)调整出装置水冷器水量,控制蜡油、渣油冷后温度在工艺卡片要求范围。
3.5.6.5电脱盐岗位
a)装置开工基本正常后,开始注新鲜水和破乳剂。
b)一、二级脱盐罐注水正常,两罐油水界面建立,切水平稳后改二级切水回注一级。
c)初顶注氨水和成膜型缓蚀剂,常顶注中和型缓蚀剂和成膜型缓蚀剂,减顶注氨水。
d)整个电脱盐系统正常后,调节混合阀压降。
e)根据原油分析结果,调节注水量和注破乳剂量。
3.6正常生产
3.6.1经调整各项工艺参数基本达到正常控制指标时,即转入正常生产。
3.6.2正常生产中,严格按工艺卡片要求控制各项工艺参数。
3.6.3严格按《岗位操作法》进行正常操作和设备管理。
3.6.4严格按《生产作业计划》控制原油加工量和各项产品质量。
3.7开工升温曲线(附图1)
见附图一
4装置停工
4.1停工前准备
4.1.1组织准备
4.1.1.1由车间根据厂生产计划的安排,制定《停工方案》,并上报有关部门审批。
4.1.1.2组织操作员