回转窑提产.docx
《回转窑提产.docx》由会员分享,可在线阅读,更多相关《回转窑提产.docx(52页珍藏版)》请在冰豆网上搜索。
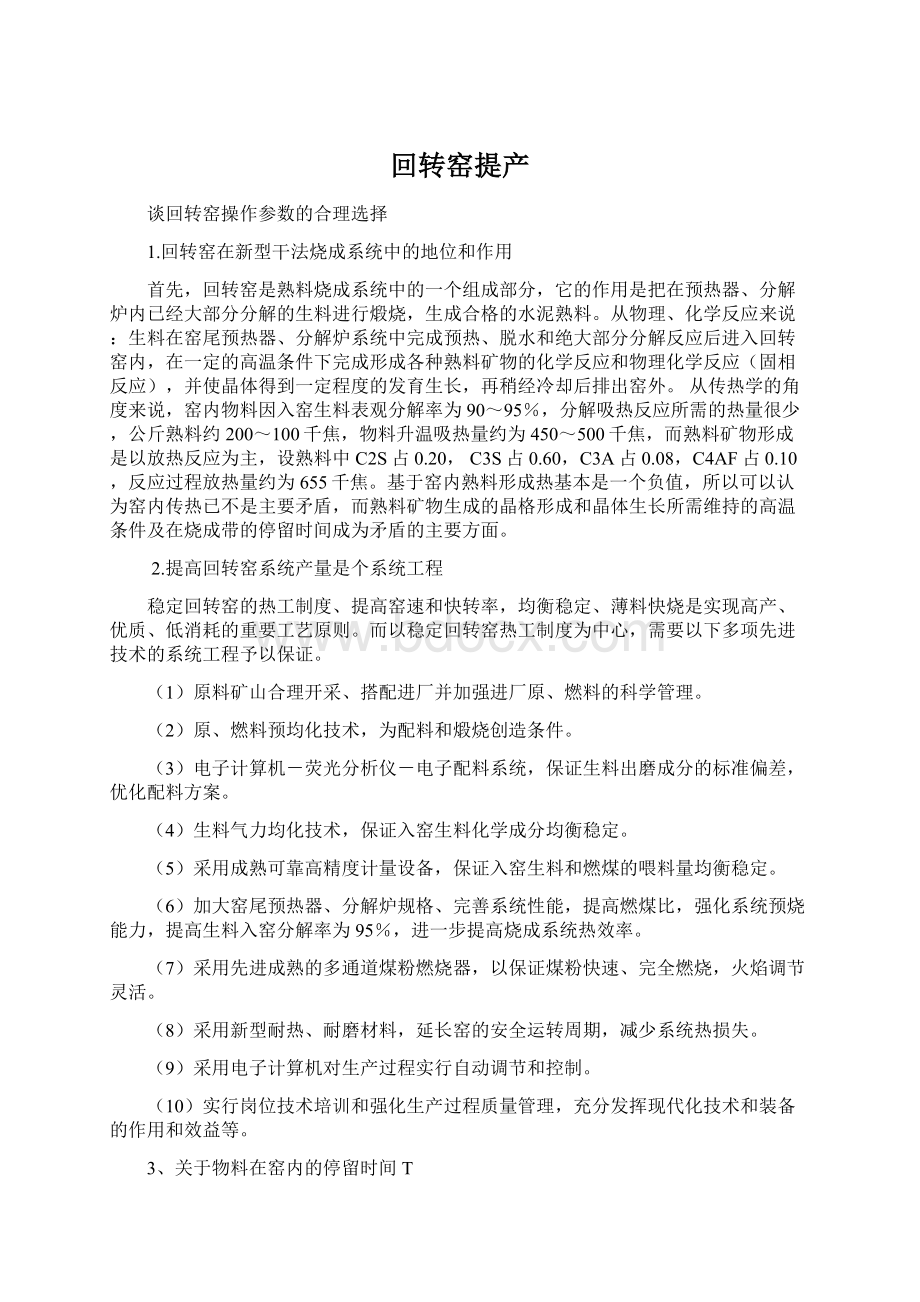
回转窑提产
谈回转窑操作参数的合理选择
1.回转窑在新型干法烧成系统中的地位和作用
首先,回转窑是熟料烧成系统中的一个组成部分,它的作用是把在预热器、分解炉内已经大部分分解的生料进行煅烧,生成合格的水泥熟料。
从物理、化学反应来说:
生料在窑尾预热器、分解炉系统中完成预热、脱水和绝大部分分解反应后进入回转窑内,在一定的高温条件下完成形成各种熟料矿物的化学反应和物理化学反应(固相反应),并使晶体得到一定程度的发育生长,再稍经冷却后排出窑外。
从传热学的角度来说,窑内物料因入窑生料表观分解率为90~95%,分解吸热反应所需的热量很少,公斤熟料约200~100千焦,物料升温吸热量约为450~500千焦,而熟料矿物形成是以放热反应为主,设熟料中C2S占0.20,C3S占0.60,C3A占0.08,C4AF占0.10,反应过程放热量约为655千焦。
基于窑内熟料形成热基本是一个负值,所以可以认为窑内传热已不是主要矛盾,而熟料矿物生成的晶格形成和晶体生长所需维持的高温条件及在烧成带的停留时间成为矛盾的主要方面。
2.提高回转窑系统产量是个系统工程
稳定回转窑的热工制度、提高窑速和快转率,均衡稳定、薄料快烧是实现高产、优质、低消耗的重要工艺原则。
而以稳定回转窑热工制度为中心,需要以下多项先进技术的系统工程予以保证。
(1)原料矿山合理开采、搭配进厂并加强进厂原、燃料的科学管理。
(2)原、燃料预均化技术,为配料和煅烧创造条件。
(3)电子计算机-荧光分析仪-电子配料系统,保证生料出磨成分的标准偏差,优化配料方案。
(4)生料气力均化技术,保证入窑生料化学成分均衡稳定。
(5)采用成熟可靠高精度计量设备,保证入窑生料和燃煤的喂料量均衡稳定。
(6)加大窑尾预热器、分解炉规格、完善系统性能,提高燃煤比,强化系统预烧能力,提高生料入窑分解率为95%,进一步提高烧成系统热效率。
(7)采用先进成熟的多通道煤粉燃烧器,以保证煤粉快速、完全燃烧,火焰调节灵活。
(8)采用新型耐热、耐磨材料,延长窑的安全运转周期,减少系统热损失。
(9)采用电子计算机对生产过程实行自动调节和控制。
(10)实行岗位技术培训和强化生产过程质量管理,充分发挥现代化技术和装备的作用和效益等。
3、关于物料在窑内的停留时间T
从操作上看,决定熟料产量和质量的二个重要条件就是窑内高温条件和物料在烧成带的停留足够时间。
物料在窑内所需停留时间与窑的类型有关,前期统计预分解窑为25~30min。
计算式如下:
式中:
T——物料停留时间(min)
D、L——分别为窑有效内径和长度(m)
P——窑斜度(度)3.5%(2.0º),4.0%(2.3º),4.5%(2.58º)
n――窑转速(r/min)
a――物料休止角(度),一般取35°
物料在窑内停留时间不足,使熟料“欠烧”影响产品质量性能;停留时间过长,熟料易“过烧”,使熟料矿物晶体过大且结构致密而影响熟料易磨性并使热耗增大。
在风、煤、料和窑速均衡稳定配合和稳定窑的热工制度下的薄料快烧,对缩短生料在窑内停留时间有利。
目前通过提高产量的生产实践证明:
φ4.0×60m、斜度3.5%NSP窑、最高窑速3.9r/min、负荷率7.0%、物料在窑内停留最短时间为22.4min均可保证优质熟料的烧成,窑内物料停留时间有缩短的趋势。
4.关于窑内负荷率
窑内物料负荷为窑内物料的容积与整个窑筒体有效容积的百分数,由于窑内各带物料运动速度不同,物料负荷率也不同,这里指的是平均负荷率的概念。
据资料介绍,一般
=5~13%。
窑内物料负荷率与窑直径、长径比、斜度、喂料量和转速相关,在生产中窑速要与喂料量同步增减调节,避免负荷率变化过大,这样有利稳定窑的热工制度。
预分解窑计算式如下:
式中:
——窑内物料平均负荷率(%)
t——物料在窑内停留时间(min)
G――窑小时熟料产量(t/h)
R——煅烧1Kg熟料所需窑内物料量(Kg生料/Kg熟料)
Ks——料耗(Kg生料/Kg熟料)
——―入窑料表观分解率(%)
D、L——分别为窑有效内径和长度(m)
——窑内物料平均容重(kg/m3)
=1/2(
s-
熟料)=1/2(0.9+1.27)=1.085kg/m3
薄料快烧是回转窑实现优质、高产的一个重要操作手段。
窑在最高产量时,窑的最高操作转速除需保证物料在窑内烧成所需最短停留时间外,物料负荷率必须在合理的薄料层范围内,以保证熟料烧成。
5.窑内物料负荷率、操作转速对窑传动功率的影响
新型干法窑正常运行中机械摩擦消耗功率约占额定功率的10%,不良情况可达30%,因此窑内物料翻转和输送的有用功率占额定功率的大部分,约占70~75%,窑内物料量和运动状态对回转窑消耗功率起决定作用。
窑内物料量大,窑的消耗功率大。
窑操作转速对传动功率的影响:
窑转速与窑需用功率成正比关系。
简易计算公式为:
N=kD2.5LN
式中:
N——窑需用功率(kw)
D、L——分别为窑有效内径和长度(m)
N——窑转速(r/min)
6.对目前NSP窑合理设计及操作参数的探讨
(1)关于物料在窑内停留时间T
当前由于新型干法烧成系统工艺技术装备趋于先进成熟,在窑尾预烧能力充分增强的条件下,生产实践充分证明实现“薄料快烧”后物料在窑内停留时间有明显的缩短趋势,窑内物料停留时间19~20分钟,完全能保证优质熟料的烧成。
(2)关于窑内物料平均负荷率
在保证物料窑内停留时间的前提下,采用高窑速和小负荷率的“薄料快烧”,有利于实现优质高产低消耗。
窑斜度与物料负荷率有直接关系:
斜度大,物料负荷率小;斜度小,物料负荷率大。
在生产操作中,产量一定时,窑速与负荷率成反比。
因此要求喂料量尽量与窑速同步增减以保证窑内物料负荷率不变,稳定窑的热工制度。
据统计计算国内部分φ3.0~φ6.0m,L/D=13.5~16.5的(三支承)NSP窑,窑内物料负荷率随窑直径加大而提高,=5.7~9%(见表二);而L/D<12的二支承短窑窑内物料负荷率偏高,=7.7~10.5%(见表二)。
(6)关于NSP窑提高生产能力的探索
提出NSP窑的熟料产量不是靠窑烧出来的,而是靠系统工程严格质量控制和管理出来的观点。
从系统工程着手,以稳定窑热工制度为中心、保证熟料烧成为前提,探索缩短物料在窑内的停留时间,实现“薄料快烧”。
探索高产条件下窑速与负荷率的优化配制是NSP窑系统优质、高产、节能的途径之一。
表二中所列多规格NSP窑的生产能力均达到国外同类窑型先进水平,也是我们通过努力可以达到的先进水平,它为我们今后的系统技改工作提出了努力的方向。
(7)NSP窑设计参数与节能
从以上技术方案比较结果的启示,窑的设计参数合理选择对节能有直接的影响,其中影响最大的是窑的斜度,其次是长径比。
斜度大,窑内物料负荷率和物料量减少,并带来操作窑速的降低,能显著降低窑的运行电耗。
窑长度缩短直接减轻了设备和窑内物料的重量,同样达到降低窑运行电耗的目的。
下面对不同斜度、长径比的窑型参数和节能进行比较(见表三)。
从表三可见,在保证窑内物料停留时间的前提下,采用“大斜度小长径比”的技术方案,如斜度4.5%、长径比14,可使窑的操作转速保持在中速状态2.9~3.2r/min,窑内物料负荷率维持在6.3%左右的薄料层范围,能有效减少窑内物料量约7.9t,有效降低窑内物料运动功耗,与方案1相比,达到节电46.2kwh/h或1109kwh/D,取得节电近26.6%的显著效果,单位熟料的物料运动功耗降到1.23kwh/t.cl的先进水平。
因此在当前节能是建材工业发展的重中之重的要求下,笔者进一步对NSP窑提出“大斜度小长径比”的节能新窑型技术方案,供行业专家、同仁共探讨。
本文在目前国内新型干法窑外分解水泥熟料生产工艺、技术装备趋于成熟、窑系统产量大幅度提高的情况下,采集一些最新实际生产数据,用物料窑内停留时间、“薄料快烧”以及系统工程的概念,重新对国内NSP窑型和通过技术改造成NSP窑的系统,在提高窑的生产能力、“经济产量”(节电)及在各种产量情况下的设计、操作参数等方面作一次反求的新探索,以求提高认识,再指导实践,并提出进一步节能的技术方案,希望能对新型干法烧成生产工艺、技术装备系统在不断追求技术进步的发展征途上起一定作用。
7.燃烧器及热工制度
水泥烧成系统由悬浮预热预分解系统、回转窑及篦冷机这三个设备构成的。
而预热单元由于多级粉体悬浮换热,传质换热效率很高,尤其是徐德龙院士提出的高固气比外循环式悬浮预热预分解系统,更是大大提高了预热单元的换热效率,因此再设法降低预热单元能耗的空间就很小。
新型干法水泥生产线采用的第四代篦式冷却机可以大幅度提高熟料热回收率及冷却效率。
因此降低水泥烧成系统能耗的总体瓶颈部分在于回转窑。
由于回转窑内的物料是处于堆积态,窑内气-固、固-固之间的换热效率就相对较低,研究高温热处理条件下回转窑内发生的物质与能量的转化与传递,并对煤粉燃烧器的操作参数进行优化,这对提高回转窑内换热效率、降低回转窑能耗具有重要的意义。
预热器、分解炉的采用使原本需要在回转窑内完成的生料预热和碳酸钙的分解任务现在转移到了在预热器内完成,缩短了煅烧时间,并大大缩短了回转窑的长度。
同时大大降低了水泥熟料生产热耗,很大程度上改善了水泥回转窑的热负荷和操作工况。
这在水泥工业的发展史上具有划时代的意义,同时标志着水泥工业开始向大型化方向发展。尤其近年来,随着人们对预热器和分解炉结构参数及其操作参数的不断优化,以及新型高效篦冷机的出现,再加上四通道煤粉燃烧器的推出和应用,这使得以预热预分解技术为特点的新型干法回转窑系统的出现成为必然。
回转窑在结构上不断的进行改进,但实质并未发生变化,窑内物料仍然是堆积态,换热效率较低,这与国家倡导的节能减排政策不符。
而寻求提高回转窑传质换热效率、优化回转窑的操作参数的途径,需要深入了解回转窑的结构参数、窑内物料运动、气固两相运动及物料化学反应等现象。
1.2.2回转窑的结构
水泥回转窑的结构简单,外观:
·········(大同小异略)
水泥回转窑采用倾斜布置,其斜度约为2%-5%。水泥生料由高的一端(也称窑尾)送入,而燃料(一般为煤粉)与助燃空气由另一端(又称窑头)喷入。气固两相以逆流方式相对运动,进行热量、动量与能量传递并发生化学反应。整个回转窑的窑体转动用可调速电机经大小齿轮带动。物料从窑的高端送入后,随着窑体的转动被不断的扬起,又在一定的高度上滚落,同时向窑体的低端运动。
1.2.3回转窑内物料运动和化学反应
(1)回转窑内的物料运动
物料在回转窑内的运动状态影响着物料在窑内的加热时间,受热面积,料程温度的均匀程度,因此要研究回转窑内的传热传质过程,必须对物料在回转窑内的运动过程有一个清晰的认识。
回转窑内物料的运动方式包括横向运动和纵向运动。横向运动是指回转窑在转动时固体物料颗粒在窑横断面上被扬起,又在一定的高度上滚落。横向运动加强了窑内物料的传热和传质,有利于物料的加热。固体物料的纵向运动是物料由窑高的一端向低的一端运动,主要有利于物料的传输。
根据物料在回转窑横截面内的运动形式,固体物料颗粒在窑内的运动可分为3种:
滑移、滚动和抛落运动(理想状态以滚动为主)。
(2)回转窑内的化学反应
回转窑内的熟料烧成反应主要分为两个阶段:
预烧和烧成。
预烧以固相反应为主,主要是指硅酸二钙的生成。
烧成是液相反应,主要指硅酸三钙的生成。
随着温度的升高按下列方式转变为熟料相:
狭义上说,水泥熟料烧成反应是指硅酸二钙与氧化钙生成的液固相反应。
由于水泥熟料强度的主要组成来源是C3S,因此
C2S+CaO→C3S的烧成过程对整个煅烧过程具有至关重要的作用。
对C-S-A-F-MgO系统而言,该反应主要发生在熔融的液相中,液相出现的温度约为1550K(1277℃)。
烧结反应的机理可以这样描述:
固相反应生成的C2S和之前未被反应的CaO在液相中溶解、扩散并在液相中发生反应、经液相的过饱和及反扩散,最后经过再结晶形成新相C3S。
C3S形成速率取决于液相的数量和粘度、反应物的细度和温度,以及固体颗粒在液相中的扩散系数。
物料烧成包括了固相烧结与液相烧成两个过程。
固相烧结采用金斯特林格反应模型,此模型的动力学方程可以解决固相反应的速率问题,从而可知生成单位质量的硅酸二钙所用的时间。
反应模型示意图:
液相烧成采用溶解-沉淀传质中的Kingery液相烧结模型,通过此模型可以知道生成单位质量的硅酸三钙所需的时间。
反应模型示意图:
溶解-沉淀过程收缩率为:
1.3回转窑用燃烧器
1.3.1回转窑生产对燃烧器性能的要求
根据物料煅烧难易程度、窑的工况调节火焰形状。
因此回转窑对煤粉燃烧器的性能要求是必须易于调节。
煤粉燃烧形成的火焰形状应是肥瘦适宜的棒槌状,这样的火焰形状可使整个烧成带具有强而均匀的热辐射,从而在烧成带形成致密又稳定的窑皮,既可生成质量均匀且优质的水泥熟料,又延长了水泥回转窑耐火砖的使用寿命。
高温热处理过程包括回转窑内发生的物质与能量的转化与传递、回转窑内的气体、物料和窑内壁之间的辐射、对流和传导及物料运动与化学反应等过程。
空气过剩系数、二次风温度、内外风量比等操作参数对窑内传热过程的影响,并对操作参数进行优化,从而求得烟气、物料、窑内外壁沿窑长方向的温度变化规律,借此了解煅烧窑内温度分布及炉窑热工特性,可为优化窑的操作参数提供理论依据,并为降低回转窑能耗寻求一种有效的途径。
2.2煤粉燃烧模型
根据煤粉与氧化剂混合时间点的不同把煤粉燃烧模型分为三种,分别为非预混燃烧模型、预混燃烧模型和部分预混燃烧。
非预混燃烧,顾名思义就是燃料与氧化剂在燃烧前没有进行过混合,此种燃烧类型适用于燃料和氧化剂分别从不同入口喷入的情况。在非预混燃烧计算中用统一的混合物浓度作为未知变量进行求解,而不采用有限速率化学反应模型,由于计算中不用计算代表组元生成或消失的源项,因此这种方法的计算速度比采用有限速率化学反应模型的计算速度要快。但是采用非预混燃烧进行计算对流场有要求,例如要满足流场必须为湍流。非预混燃烧可以存在三个入口,一个是燃料入口,一个是氧化剂入口,这两个入口是必须存在的,而第三个入口根据需要可有可无,且通过这个流动入口的流体可以是燃料或氧化剂,也可以是不参与任何燃烧反应的第三种流体。
适合非预混燃烧计算的化学反应模型有三种,分别为火焰层近似模型、平衡流计算模型和层流火苗模型。火焰层近似模型假设燃料和氧化剂的反应速度为无穷大,即燃料和氧化剂一相遇就立刻燃烧完毕,此模型的好处是计算速度非常快,缺点是计算误差会比较大,特别是计算局部热量时,计算结果与实际值出入比较大。平衡流计算模型是用来求解气体组分的浓度场,其解算方法是吉布斯自由能极小化,这种方法的好处是能够精确地得到气体组分浓度场,同时又不用解算有限速率化学反应模型。层流火苗模型是先将湍流火焰燃烧划分成多个层流区,每个层流区中可以采用真实的反应模型,然后再把这些层流区组合起来,得到最后的结果,这种方法的计算精度很高。在非预混燃烧计算中湍流计算采用时均化NS方程,用概率密度函数PDF来表征湍流与化学反应的相干过程。计算处理燃烧计算过程中反应物的化学性质。计算处理后,保存为PDF格式,FLUENT在计算非预混燃烧时可随时进行调用数据。
预混燃烧是指在燃烧前燃料和氧化剂已经充分混合了的燃烧。其火焰传播速度取决于两方面,一是层流火焰传播速度,二是湍流对层流火焰的相干作用。在预混燃烧中,在火焰区可明显区分正在燃烧反应的反应物和燃烧之后的生成物。
煤粒燃烧过程是一个非常复杂的气固两相流动与煤粉燃烧共同存在的过程,具体包括了预热、挥发份析出、挥发份燃烧及焦炭的燃烧。
煤粒反应过程:
碳粒耗尽所需要的时间是煤反应过程的重要组成部分,其范围短可为30ms,长可达到1h以上。碳粒非均相反应过程受到煤结构的多变、反应物的扩散、反应物的反应和煤粒尺寸等多种反应变量的影响,因此对它的模拟是非常困难的。
对于热解碳的氧化反应,氧化剂为O2,比反应速率RpO可看成一级非均相反应,其反应式可表示为:
Rpo=ρog/[(1/km)+(1/kr)]
Rpo是以外表面积为基础的比反应速率(g/m2s);
ρog是气体容积中氧化剂的浓度(g/m3);
km是氧化剂向煤粒的传质系数(m/s);
kr是氧与焦炭的反应速率系数(m/s)。
1、火焰粗短的调节:
增大旋流风出风面积和角度,火焰变粗,同时增大外轴流风的风速,保证外轴流风包裹火焰形状,即减小外轴风的出风面积,提高外轴风的风速和风压。
标尺直观判断:
旋流风标尺数字变大,外轴风标尺数字变小。
2、火焰细长的调节:
减小旋流风出风面积和角度,火焰变细,同时减小外轴流风的风速,保证外轴流风包裹火焰形状,即增大外轴风的出风面积,减小外轴风的风速和风压。
标尺直观判断:
旋流风标尺数字变小,外轴风标尺数字变大。
3.1回转窑内煤粉燃烧数学模型的建立
3.1.1假设条件
回转窑内煤粉燃烧数学模型包括烟气的紊流、气体燃烧和辐射现象。
这里用到两个假设:
一是烟气流动为稳态条件,且窑内压力恒定;二是烟气按不可压缩流对待。
3.1.2物理模型及网格划分
回转窑的原型规格为ф4×60m。去除燃烧带内衬及窑皮的厚度之后,有效内径为ф3.4m。
考虑到回转窑内煤粉燃烧主要在燃烧器附近20m以内的燃烧带内进行,为减少计算工作量和提高计算效率,计算区域取为20m,包括了从窑头开始至烧成带结束的连续区域。
采用了目前较为先进的体网格结构及结构化的非均匀网格技术对上述回转窑实体模型进行网格划分。
考虑到燃烧器前方存在强烈的射流运动与湍流作用,该部分网格划分得比较密。
为减小运算负荷,其它计算区域划分得相对稀疏。
回转窑实体模型共划分了145158个计算单元。
网格化的回转窑数值模型:
基于四通道煤粉燃烧器已在新型干法水泥生产线上得以广泛应用,本文也选取四通道煤粉燃烧器进行计算。
四风道煤粉燃烧器的结构见图,选取的计算区域见图
3.1.3采用的数学模型
(1)湍流模型
回转窑内气体流动为复杂的湍流流动。
由于standardk−ε模型具有良好的稳定性、经济性,计算精度也很高,因此采用standardk−ε模型计算窑内气体流动与煤粉的射流运动。
(2)煤燃烧模型
煤粉由四通道煤粉燃烧器送入,煤粉与高温空气在进入窑内后进行混合,其燃烧特征符合非预混燃烧模型,因此煤粉的气相燃烧模型采用非预混燃烧模型。
煤粉的流动用离散相模型来模拟,此模型可以预测出单个煤粒的运动轨迹。离散项的轨迹与气相连续方程交替计算也包含了煤粒与气体间的热量、动量和质量的传递。
(3)辐射模型
由于回转窑内的辐射换热主要体现在气体与颗粒之间,P1辐射模型对计算气体与颗粒之间的辐射换热的效果较好,因此本课题选取P1辐射模型用于求解气体和颗粒间的辐射传热。
应用FLUENT软件进行计算时,各个模型之间能够进行很好的耦合。
首先在气体与煤粉湍流运动的基础上,引入非预混燃烧模型计算煤粉的燃烧,与此同时耦合计算气体与煤粉颗粒之间的辐射换热。
3.1.4求解的初始条件及边界条件
二次风、煤风和内净风进口采用风速边界条件,根据实测工况参数范围直接设定入窑速度。燃烧器的中心风、外净风出口速度很大,为可压缩流,进口采用质量边界条件,直接设定入窑质量流率。出口采用压力边界条件,出口压力设定为-70Pa。
对于近壁面,以及气固界面,沿烟气流动方向采用壁面函数。
计算选取的各种初始条件及边界条件见表:
风道
入口温度/K
入口速度/m/s
质量流率/kg/s
二次风
1373.0
8.4
22.65
一
次
风
中心风
361.0
116.0
0.047
内净风
321.0
71.0
0.69
煤风
385.0
25.0
1.086
外净风
334.0
310.0
1.48
煤粉低位发热量(DAF)为25.27MJ/kg,热值为1000J/(kg·K),密度为1.01kg/m3。
一次风和二次风为净空气,由21%的氧气和79%的氮气组成。
3.1.5数值模型求解方法
水泥熟料窑内气体流动为复杂的旋流流动,本课题使用的四风道煤粉燃烧器的旋流角为15度,为弱旋流。熟料窑内传热传质数学模型糅合了气体流动、煤粉燃烧、传热、传质等多个模型,而且对工程实物进行数值模拟计算需要的时间较长,收敛比较困难。为了加快迭代的收敛速度,减少计算时间,并能获得较高的计算精度,采用修正的速度-压力耦合算法和混合差分格式,湍流模型每计算100次进行一次辐射计算。
另外,煤粉颗粒传输模型在求解程序中构成了关于流动计算的外循环,为保证由颗粒到流体的反向耦合收敛,外循环次数应设置为较大的值,在本计算中取10,颗粒的粒径分布选择RossinRallunler分布。如果迭代发散是由迭代过程中差分方程的系数和源项值随参数的改变而变化过大造成的,这种情况可以采用欠松弛因子来解决。虽然欠松驰因子在求解过程中有多种调节作用,但对不同的问题存在相应的一个最佳欠松弛因子。欠松弛因子过大或过小,都会降低收敛的速率。如果欠松弛因子取得太高,会导致迭代中各点数值的震荡,这种不稳定性会降低收敛的速度,严重时会导致迅速发散。如果欠松弛因子选得太小,会降低不收敛的可能性,但收敛速率也将减慢。在本课题中针对不同的参数使用不同的欠松弛因子。
在计算初期,为了获得一个较好的初始场,实现煤粉着火燃烧,优先采用较小的欠松弛因子。为了减少计算时间,加快收敛速度,在得到了初步的速度流场和温度场后,使用较大的欠松弛因子。网格划分的处理与划分网格的数目对数值计算的精度和收敛影响较大。划分网格的数目过少会大大下降低计算的精度,甚至会导致发散,但网格数目过多,会占用计算机的大量内存并大大增加计算的时间。本计算中采用结构化的非均匀网格,对气体流动情况比较复杂和变量变化梯度较大的喷口附近区域,网格划分较密集,而变量变化梯度较小的其它位置,网格划分稀疏。在模拟计算的求解过程中,即便掌握了这些方法,还会出现很多其它的问题,仍需要观察计算的收敛情况,以便按需随时进行调整,得到计算精度较高又收敛的模拟值。
3.1.6模拟计算结果及分析
本文采用同规格生产线的热工标定实测参数作为初始参数进行计算。
着重研究了空气过剩系数、内外风量比及二次风温度对窑内温度分布的影响。
测试工况下内外风量比为0.47,二次风量为24.38kg/s,窑头过剩空气系数为1.12,二次风温度为1373K。窑内温度分布模拟计算结果见图。
窑内温度分布的主要影响因素内外风量比R、空气过剩系数n、二次风温度T(K)和旋流角a(°)的值列在图下方。
由图3.5可以看出,火焰形状呈向外波动的棒槌形,这与从工程经验所知的实际火焰形状相符。
表3.4为通过模拟计算得出的窑内壁温度推算出的窑外壁温度与热工标定测得的窑外壁温度,通过对比可知两者的值基本相符。
由此可知,计算选用的模型是可靠的,同时也保证了数值模拟计算方法的准确度。
如图3.5指示,煤粉在离燃烧器喷嘴较远的一个窄而短的区域内高温燃烧,喷嘴附近的烟气温度均比较低,黑火头较长,这使得实际的烧成带较短,而使冷却带延长,预热分解带也相应缩短,这种窑内温度分布会降低窑的有效传热面积,因此不能满足水泥烧结所需的温度要求。同时由于高温区域较小,煤粉极易燃烧不完全,未来得及燃烧的煤粒或在物料内燃烧,或被物料带出,还有的甚至被烟气带出窑外,造成较大的机械损失及化学不完全燃烧热损失,甚至出现结皮、烧损衬料与窑壁等事故。回转