制动主缸补偿孔测量仪论文.docx
《制动主缸补偿孔测量仪论文.docx》由会员分享,可在线阅读,更多相关《制动主缸补偿孔测量仪论文.docx(38页珍藏版)》请在冰豆网上搜索。
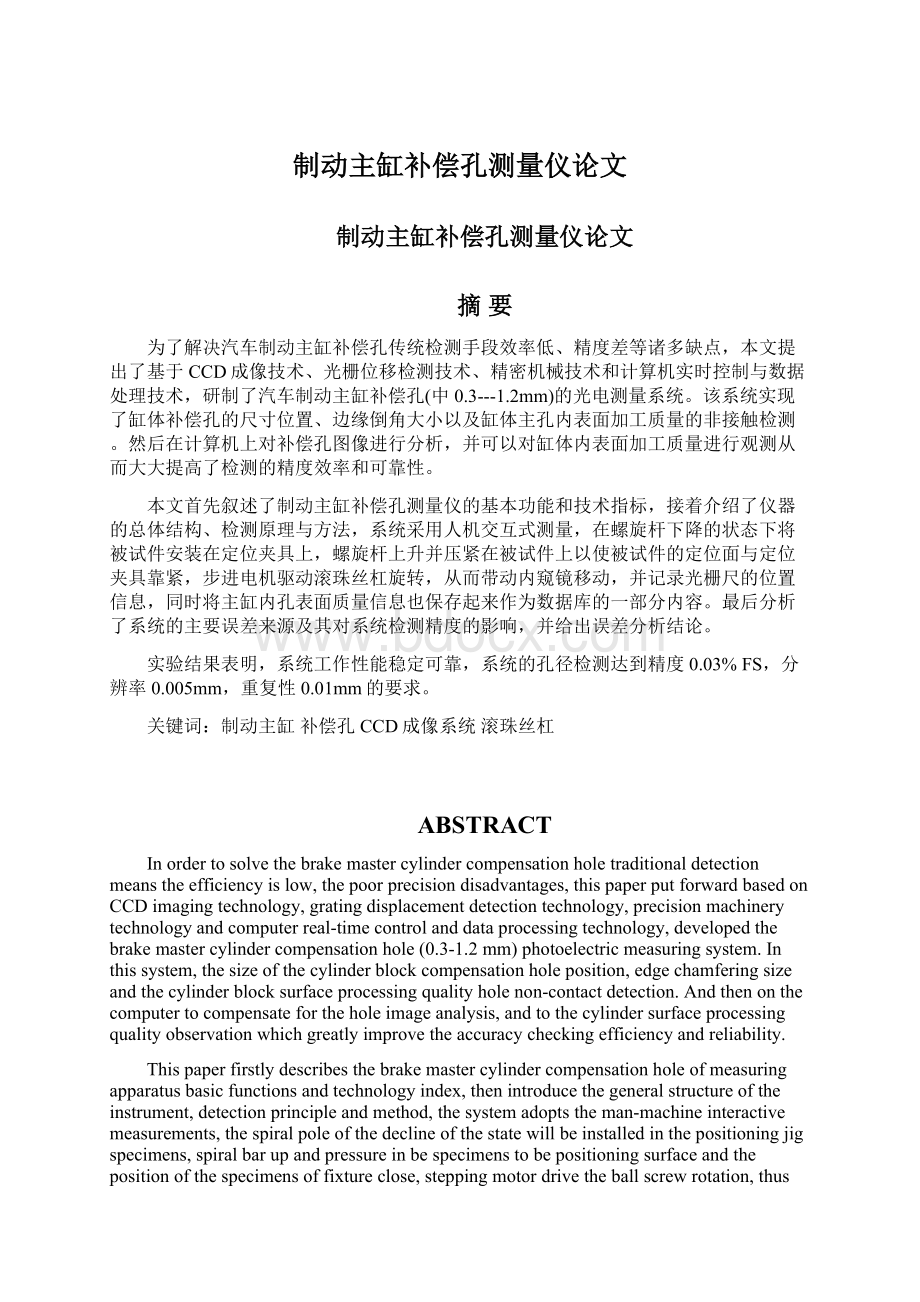
制动主缸补偿孔测量仪论文
制动主缸补偿孔测量仪论文
摘要
为了解决汽车制动主缸补偿孔传统检测手段效率低、精度差等诸多缺点,本文提出了基于CCD成像技术、光栅位移检测技术、精密机械技术和计算机实时控制与数据处理技术,研制了汽车制动主缸补偿孔(中0.3---1.2mm)的光电测量系统。
该系统实现了缸体补偿孔的尺寸位置、边缘倒角大小以及缸体主孔内表面加工质量的非接触检测。
然后在计算机上对补偿孔图像进行分析,并可以对缸体内表面加工质量进行观测从而大大提高了检测的精度效率和可靠性。
本文首先叙述了制动主缸补偿孔测量仪的基本功能和技术指标,接着介绍了仪器的总体结构、检测原理与方法,系统采用人机交互式测量,在螺旋杆下降的状态下将被试件安装在定位夹具上,螺旋杆上升并压紧在被试件上以使被试件的定位面与定位夹具靠紧,步进电机驱动滚珠丝杠旋转,从而带动内窥镜移动,并记录光栅尺的位置信息,同时将主缸内孔表面质量信息也保存起来作为数据库的一部分内容。
最后分析了系统的主要误差来源及其对系统检测精度的影响,并给出误差分析结论。
实验结果表明,系统工作性能稳定可靠,系统的孔径检测达到精度0.03%FS,分辨率0.005mm,重复性0.01mm的要求。
关键词:
制动主缸补偿孔CCD成像系统滚珠丝杠
ABSTRACT
Inordertosolvethebrakemastercylindercompensationholetraditionaldetectionmeanstheefficiencyislow,thepoorprecisiondisadvantages,thispaperputforwardbasedonCCDimagingtechnology,gratingdisplacementdetectiontechnology,precisionmachinerytechnologyandcomputerreal-timecontrolanddataprocessingtechnology,developedthebrakemastercylindercompensationhole(0.3-1.2mm)photoelectricmeasuringsystem.Inthissystem,thesizeofthecylinderblockcompensationholeposition,edgechamferingsizeandthecylinderblocksurfaceprocessingqualityholenon-contactdetection.Andthenonthecomputertocompensatefortheholeimageanalysis,andtothecylindersurfaceprocessingqualityobservationwhichgreatlyimprovetheaccuracycheckingefficiencyandreliability.
Thispaperfirstlydescribesthebrakemastercylindercompensationholeofmeasuringapparatusbasicfunctionsandtechnologyindex,thenintroducethegeneralstructureoftheinstrument,detectionprincipleandmethod,thesystemadoptstheman-machineinteractivemeasurements,thespiralpoleofthedeclineofthestatewillbeinstalledinthepositioningjigspecimens,spiralbarupandpressureinbespecimenstobepositioningsurfaceandthepositionofthespecimensoffixtureclose,steppingmotordrivetheballscrewrotation,thuspromoteendoscopemobile,andrecordthefeetofthegratingpositioninformation,andatthesametimewillbemaincylinderholesurfacequalityinformationalsosaveupaspartofthedatabasecontent.Atlast,analyzedthesystem'smainerrorsourcesandtheinfluenceoftheprecisionofthesystemisgiven,andtheerroranalysisconclusion.
Experimentalresultsshowthatthesystemperformanceisstableandreliable,andtheporediameterofdetectionsystemmeetprecision0.03%FS,resolution0.005mm,repeatability0.01mmrequirements.
摘要I
ABSTRACTII
第1章绪论1
1.1引言1
1.2本课题研究的目的和意义2
1.3国内外发展现状3
1.3.1制动主缸补偿孔测量的发展现状4
1.3.2高精度高效率检测4
1.3.3数字化非接触检测5
1.4系统技术指标及要求5
第2章系统总体设计方案7
2.1精密机械传动机构及电控系统8
2.2精密机械传动机构9
2.3光栅位检测系统10
2.4计算机图像处理系统10
第3章精密机械传动机构及电控系统设计11
3.1机密机械传动机构及电控系统方案11
3.2精密机械传动机构设计12
3.2.1内窥镜直线传动设计13
3.2.2制动主缸旋转机构设计14
3.2.3定标装置设计15
3.3控制系统方案设计16
3.3.1上位控制模块17
3.3.2伺服电机17
3.3.3MSMD012G1V伺服电机驱动器18
第4章光学成像系统19
4.1光源设计19
4.2内窥镜的选用分析20
4.2.1内窥镜的技术分析20
4.2.2内窥镜的应用设计20
4.3CCD摄像机的选用分析21
4.3.1CCD摄像机的技术分析21
4.3.2CCD摄像机的应用选择21
第5章光栅位移检测技术研究23
5.1光栅位移测量的基本原理23
5.1光栅位移测量控制23
5.2光栅位移传感器与整机的连接原理24
第6章数据采集与图像处理系统设计25
6.1本章引论25
6.2补偿孔图像信息采集25
6.3补偿孔图像处理26
6.3.1图像处理软件开发分析26
6.3.2图像的灰度处理27
6.3.3图像的中值滤波处理27
6.3.4图像的锐化处理28
6.3.5图像的边缘检测28
第7章误差分析29
7.1机械检测装置的误差29
7.1.1工具误差29
7.1.2装配误差29
7.1.3工作台的几何误差30
7.1.4传动丝杠导程误差的影响30
7.2粗大误差30
7.2.1粗大误差的产生30
7.2.2粗大误防止31
结论32
致谢33
参考文献34
第1章绪论
1.1引言
现代测量技术是通过测量系统、被测系统和环境之间的相互作用,得到描述被测系统参数信息的过程。
测量作为一门应用技术,广泛地应用在工业和现代科学技术的各个领域,成为一门重要的研究学科。
伴随着现代科学技术的迅猛发展,复杂的自动化控制系统和信息处理技术得到了不断的提高,光电信号变换与检测技术的不断涌现使得综合性的自动化及智能化的光电系统得到了进一步的发展。
高精度与微型化是当前科技与工业发展的重要趋势。
除了“精密工程”以外,国际上还出现了微型工程与纳米技术的研究领域。
微型工程包括微电子学、微型光学与微型机械等,这就对微小尺寸的测量提出了越来越高的要求。
无论是尖端科学的热核反应,还是日常生活中的化学纤维,都有微小尺寸的测量问题。
微小尺寸的测量涉及到机械工业部门、电子工业部门、制药部门、医学部门及环保部门,涉及面很广,而要求进行微小尺寸测量的物体,从尺寸、几何形状和作用来划分,又各种各样。
例如,球状物体包括制导系统中毫米大小的轴承,激光核聚变中10um的玻璃小球,化学处理中1um左右的小滴,涂层和血液分析中微米级的聚合物。
平面形物体包括微米大小的集成电路,电子束刻划的亚微米级电子器件中的元件以及用电子束、激光或其他方法加工的直径小到1um的小孔等。
这些研究的进展迫切需要微小尺寸的精密测量取得长足的发展。
在一些缸体及深孔的内壁上经常会有补偿孔和功能小孔,这些小孔的位置、尺寸和形状直接影响缸体或深孔的功能,因此对这些功能小孔的测量就很有意义。
并且,缸体主孔内表面的加工质量、铸造质量也是人们所关心的,在检测小孔的同时,对主孔的加工质量也要能以图像的形式提供给计算机进行图像处理。
因此,本课题基于汽车工业孔类零件内膛难以检测的问题,提出了一种精密测量内膛小孔直径的系统,即制动主缸补偿孔测量仪。
制动主缸补偿孔测量仪是一种涉及光学、精密机械、电子学、现代传感技术、自动控制和计算机等多学科领域的高性能精密仪器,主要用于测量汽车液压制动主缸缸体补偿孔位置、尺寸和形状,同时对主缸缸体主孔内表面加工质量、铸造质量进行图像检测。
该仪器采用高分辨率CCD成像技术,利用高精度的传动机构完成上述测量任务。
与传统的测量仪相比,具有操作简单、精度高、自动化程度高等特点,实现人机交互,减少了主观因素的影响。
本课题利用CCD成像技术、光栅位移检测技术、精密机械技术和计算机实时控制与数据处理技术,研制了制动主缸补偿孔的光电测量系统,实现了对汽车制动主缸的补偿孔(中0.3mm一中1.2mm)尺寸、位置以及边缘倒角大小的非接触检测,同时还可以进行孔表面质量的观测。
1.2本课题研究的目的和意义
汽车是重要的交通工具,是科学技术发展水平的标志,世界各工业发达国家几乎无一例外地把汽车工业作为本国国民经济的支柱产业。
从1886年第一辆汽车问世至今的一百余年里,汽车工业从无到有,迅猛发展,产量大幅度增加,技术日新月异。
汽车的制动性是汽车的主要性能之指标之一,它直接关系到交通安全。
重大交通事故往往与制动距离过长、紧急制动时发生侧滑等情况有关。
故汽车的制动性能是汽车行驶的重要安全保障。
改善汽车的制动性能即改进作为制动系统最主要部分的制动器的结构性能,始终是汽车设计制造和使用部门的重要任务。
汽车制动系统在车辆行驶安全方面担负着非常重要的作用,随着技术应用的发展,汽车的制动方式也演变成很多种形式,但是考虑到其基本制动功能量和综合效率,压制动系统依旧是最可靠、最经济的方法,应用也最为广泛,而其中的制动主缸便是其核心的部件,所以液压制动主缸的补偿孔及其主缸内表面的加工质量就显的尤为重要,汽车制动主缸对其寿命和工作效率都要求较高,而常规的补偿孔检测方法比如接触式测量、简单光学式测量、投影仪式测量、人工测量等在检测性能精度都上不能满足实际的技术要求,再加上工件的形状特点、生产环境、人的因素等,所以对制动主缸的检测带来了很大的难度和不确定因素,一方面是对汽车安全性能的重视,对制动主缸加工精度的要求越来越高,另一方面是制动主缸检测手段的低精度、低效率,已经完全不能适应制动主缸工业化检测的需要。
因此研究出一种非接触、高效率、高精度的汽车制动主补偿孔及其主缸内表面的检测设备就显得迫在眉睫,非常的必要。
由于制动主缸的重要性,行业标准ZBT/T24008一90《汽车液压制动主缸》规定:
产品出厂前应进行“残留阀性能、输出功能、液压密封性”等项目的测试,其检测结果符合要求方可出厂。
但其试验方法规定:
(l)残留阀性能—用压缩空气来检测;
(2)输出功能和密封性—用制动液来检测。
这一方法在大批量生产中明显存在着下列缺点:
(1)使用的介质是两种介质,试验中存在变换介质的问题;
(2)试验中,需给主缸内腔充满制动液,这意味着在试验时存在排
气问题,导致检验的辅助时间太长;
(3)在更换制动主缸时,充满在主缸及管路中的制动液要释放溢
出,造成对制动液的浪费及环境污染;
(4)由于近来为了改善制动性能,大量的制动主缸在出厂检测后,残留于缸体内部的制动液对铸铁缸体内壁有严重的腐蚀作用,致使产品存放一段时间后,主缸内壁锈蚀,主缸出现卡死或皮碗拉伤而不能使用;
(5)在检测时,使用的液压达9MPa,难以实现效率较高的快速密封结构。
综上所述,行业标准ZBT/T24008一89《汽车液压制动主缸》中规定的出厂检测项目,已明显不适应大批量的生产,本文提出了一种全新的方法可达到“方便简捷”的效果。
补偿孔式液压制动主缸的寿命必须有严格的使用规定,即常温下工作50万次,70℃时不少于12万次。
为保证这一技术要求,主缸的补偿孔与主孔相贯部应尽可能平滑,因此,制动液补偿孔的加工是一项关键技术。
如果补偿孔与主孔相贯周边毛刺去不干净,势必造成主缸工作中的主皮碗过早破损,远达不到使用要求,甚至造成行车事故。
因此,汽车液压制动主缸缸体补偿孔位置、尺寸、形状的检测,以及对主缸缸体主孔内表面的加工质量和铸造质量进行图像检测尤为重要。
制动主缸的主体由制动腔和补偿孔组成。
制动腔是指通过残留阀或排液孔与制动回路相通的腔。
在制动过程中制动腔内建立起的液压与同其相连接的回路内的液压相同。
补偿孔是指缸体上制动腔与储液室连通的孔,在制动解除状态下向制动腔补偿制动液或把多余的制动液返回储液室。
本文针对目前我国汽车制动主缸补偿孔测量技术落后这一现状,提出了一种集光、机、电、算于一体的高性能精密测量的新方法,该仪器采用高精度的传动机构配合,利用高分辨CCD摄像技术获取补偿孔图像通过图像处理技术于精密光栅检测技术实现对制动主缸补偿孔检测的目的,该仪器消除了主观因素的影响,具有无接触、简单操作、精度高、自动化程度高、可靠性高的特点,适合于生产企业和计量部门对主缸补偿孔进行抽样或100%检测,以保证制动主缸的加工质量。
该产品一旦研制成功,必将在汽车制动主缸质量检测中获得广泛的应用,因此有着广阔的发展前景。
1.3国内外发展现状
伴随着制造业特别是汽车产业的高速发展,机械零部件产品的效率和质量日渐受到人们的重视,精密检测技术的发展也使零部件制造业向高、精、尖的技术方向发展,零部件的制造和检测彼此依存,互为基础,近年来,深孔类零件精密检测设备的研发投入和产出均有较大的增长。
物体几何尺寸的精密检测在检测技术中是一个应用十分普遍且具有实际应用价值的问题。
在外形尺寸和平面尺寸测量方面,已达到1nm,甚至0.1nm的分辨力。
相对而言,内尺寸的测量还远远落后。
对于盲孔和小孔的测量,特别是要测量出小孔任意截面处的尺寸及形状误差,目前还没有十分完美的测量手段。
英国在20世纪70年代曾经生产过一种用微小玻璃球作为探针,接触测量小孔形貌的小孔测量仪。
但是由于操作繁琐,特别是探针极易损坏,这种仪器很快就停止了生产。
目前,小孔测量方法基本上可分为接触式和非接触式测量两种。
1.3.1制动主缸补偿孔测量的发展现状
制动器是生产阻碍机器的运动或运动趋势的一种装置,是保证机器安全可靠运转的重要部件。
随着汽车工业的飞速发展和高速公路的迅速延伸,汽车的行驶速度越来越快,对汽车行驶的安全性要求也越来越高。
汽车行业是对制动器技术性能要求最高的部门之一,制动器是影响现代汽车行驶安全的重要制约因素之一。
补偿孔式液压制动主缸是汽车行驶安全的重要装置,是汽车制动系统中的关键部件。
汽车在运行过程中,制动主缸使用频繁,因而它的寿命必须有严格的使用规定,即常温下工作50万次,70度时不少于12万次。
为保证这一技术要求,主缸的补偿孔与主孔相贯部应尽可能平滑,因此,制动液补偿孔的加工是一项关键技术。
如果补偿孔与主孔相贯周边毛刺去不干净,势必造成主缸工作中的主皮碗过早破损,远达不到使用要求,甚至造成行车事故。
因此,汽车液压制动主缸缸体补偿孔位置、尺寸、形状的检测,以及对主缸缸体主孔内表面的加工质量和铸造质量经行图像检测尤为重要。
制动主缸的主体由制动腔和补偿孔组成。
制动腔是指通过残留阀或排液孔与制动回路相通的腔。
在制动过程中制动腔内建立起的液压与同其相连接的回路内的液压相同。
补偿孔是指缸体上制动腔与储液室连通的孔,在制动解除状态下向制动腔补偿制动液或把多余的制动液返回储液室。
目前,汽车液压制动主缸补偿孔的测量方法有很多种,如由上海汽车制动器公司和上海光学仪器厂合作研制的主缸中0.7补偿孔孔位测量仪和气动测量法等。
但限于检验条件及实际工况,本文提出一种集光、机、电、算于一体的高性能的精密测量方法,以此弥补各种检测方法的不足。
1.3.2高精度高效率检测
深孔类零件的精密测量技术是集光学、机械、电子及计算机技术为一体的综合性交叉学科,其检测设备具有精密化、集成化的发展趋势,世界各国在测量技术的微/纳米级别上展开了广泛的应用研究。
制造业生产现场对深孔类零件精密检测设备的技术要求如下:
(l)高检测精度、高可靠性。
(2)高检测效率,适应大批量检测的要求。
(3)能够适应各种工业生产环境。
(4)容易操作,性价比高。
有专家预测,为了进一步提高检测精度和效率,21世纪的深孔类零件检测技术的发展方向应该是:
由位置测量过渡到综合的形状检测阶段,提高整体检测精度由微米级向纳米级发展。
随着深孔类零件检测需求的增加,各公司也争相的开发新产品来满足不断提高的高精度高效率检测。
如三丰公司的CS一5000CNC能一次将表面粗糙度和位置信息检测出来。
东京精密公司的SURFCOMZoo0DX测量仪可实现低振动精确定位,检测精度和效率有了很大的改善。
美国OGP公司利用直接录像显微镜(VDM)来显示大深度小孔和不可视的检测区域,延长了人的视觉,更加的稳定可靠。
三坐标测量机在机械零件的检测中亦有使用,但其对环境的要求较高。
目前外国公司掌握着该检测领域的关键技术,三丰公司、德国卡尔蔡司、东京精密及海克斯康集团等都具有相当的技术和资金优势,使国内企业在竞争上面临很大的压力,所以我们必须要开发出适应自己市场需求的产品。
1.3.3数字化非接触检测
随着检测技术的发展,市场需求不仅对深孔类零件的形位、表面质量、圆度等的检测提出了更高精度要求,还要求能实现数字化、在线检测。
在现代化的生产环境下,对零件进行检测的同时还要将检测数据实时的传递给各个工序流程,也可以利用网络进行远端控制和管理,随着计算机技术的发展应用,深孔类零件检测领域也不断的开发出可以适应数字化特点的检测设备,自动化水平也有很大的提高。
虽然接触式测量可以适应不同的零件尺寸,但它对零件表面和检测环境要求较高,如果在频繁变更零件类型的情况下,很难保证检测的高精度。
目前,业界开始利用光学技术开发非接触深孔类零件的检测设备,意大利MARPOSS公司的Mid瓦Laser测量系统就是利用激光测头来辅助实现全数化非接触式检测,日本索尼精密工程公司的YP20121是采用半导体激光传感器实现非接触检测的,日本YKT公司的非接触三坐标测量系统乙p250也可以实现高精度的数字化检测。
随着光机电一体化技术更为成熟的发展,在高精度的生产和质量管理体系中,可以利用光学系统采集被测零件的图像,利用计算机图像识别技术对其中感兴趣的信息进行提取和处理,通过这些技术手段,零件的检测精度和效率都获得大大的提高,而且可以与计算机网络相连接便于管理和更加的人性化操作,因此,深孔类零件的数字化非接触检测也就必然成为未来精密检测技术的重要发展趋势,是我们所必须关注的重要技术领域。
1.4系统技术指标及要求
本课题针对目前我国汽车制动主缸补偿孔测量技术落后这一现状,提出了设计制造制动主缸补偿孔测量仪这一新思路。
该仪器采用高分辨率CCD成像技术完成测量任务,具有操作简单、精度高、自动化程度高、可靠性高等特点,消除了主观因素的影响,是一种集光、机、电、算于一体的高性能精密测量仪器。
本课题主要研究以下几方面内容:
1.完成汽车液压制动主缸缸体补偿孔位置、形状的精密检测。
(1)补偿孔位置检测:
补偿孔中心到缸体法兰面轴向绝对距离的测量;
(2)补偿孔倒角检测:
补偿孔(主缸主孔端)边缘倒角大小和倒角与补偿孔同心度的检测。
2.要达到的技术指标:
(1)测量范围:
主缸缸体主孔直径:
。
15~中45Inln;
补偿孔位置范围:
一30~150二;
补偿孔直径范围:
0.3~1.Zlnln。
(2)尺寸测量:
精度:
0.O3%FS;
分辨率:
0.o05Inln;
重复性:
0.ollnln。
(3)测量时间:
每件主缸从装夹到生成报告所用时间不得超过2分钟(不包括报表名头和参数输入时间)。
本课题的研究目的和意义是:
设计实用合理的制动主缸补偿孔测量仪,并通过试验研究,得出影响补偿孔测量精度的主要因素,从而为早日开发出能投入实际应用的、结构简单、性能优异的制动主缸补偿孔测量仪提供有价值的理论分析和试验依据。
第2章系统总体设计方案
本课题研制的制动主缸补偿孔测量仪主要由计算机数据采集处理系统、控制系统、CCD成像系统、光栅位移传感器和精密机械传动系统组成。
制动主缸补偿孔测量仪的工作原理是:
系统采用人机交互式测量,在螺旋杆下降的状态下将被试件安装在定位夹具上,螺旋杆上升并压紧在被试件上以使被试件的定位面与定位夹具靠紧,步进电机驱动滚珠丝杠旋转,从而带动内窥镜移动,同时蜗轮蜗杆带动刚性导光臂旋转,根据CCD所成图像的处理结果用鼠标确定采样点位置,并记录光栅尺的位置信息,同时将主缸内孔表面质量信息也保存起来作为数据库的一部分内容。
制动主缸补偿孔测量仪采用光、机、电、算技术完成制动主缸缸体补偿孔位置和形状的精密检测,计算机控制试验的整个过程。
在方案的设计过程中,考虑了仪器的可扩展性、高可靠性和稳定性,同时也考虑了先进技术的应用,使得仪器功能在同行业中处于较高的水平。
根据实际工况,提出了两套整体设计方案,即主缸上置和主缸下置。
制动主缸上置总体结构简图如图2-1所示:
图2-1制动主缸补偿孔测量仪总体结构见图
如图2-1所示,系统由精密机械传动机构及电控系统、光栅位移传感检测系统、光学成像系统及计算机数据采集处理系统组成。
其中:
机密机械传动机构包括内窥镜直线传动机构和被测制动主缸旋转机构、被测制动主缸夹紧机构;光栅位移传感检测系统采用绝对式封闭光栅传感器;光学成像系统采用远心内窥光路,由小型CCD成像模块和照明系统组成。
整个系统采用人机交互式测量,被测件安装在定位夹具上,并使被测件的定位面与定位夹具靠紧,伺服电机驱动滚珠丝杠旋转,从而带动内窥镜移动,同时同步齿形带带动刚性导光臂旋转,根据CCD所成图像的处理结果确定采样位置,同时记录光栅尺的位置信息,并将主缸内表面质量信息保存。
具体工作时,首先将标校