小型单缸立式液压机课程设计.docx
《小型单缸立式液压机课程设计.docx》由会员分享,可在线阅读,更多相关《小型单缸立式液压机课程设计.docx(24页珍藏版)》请在冰豆网上搜索。
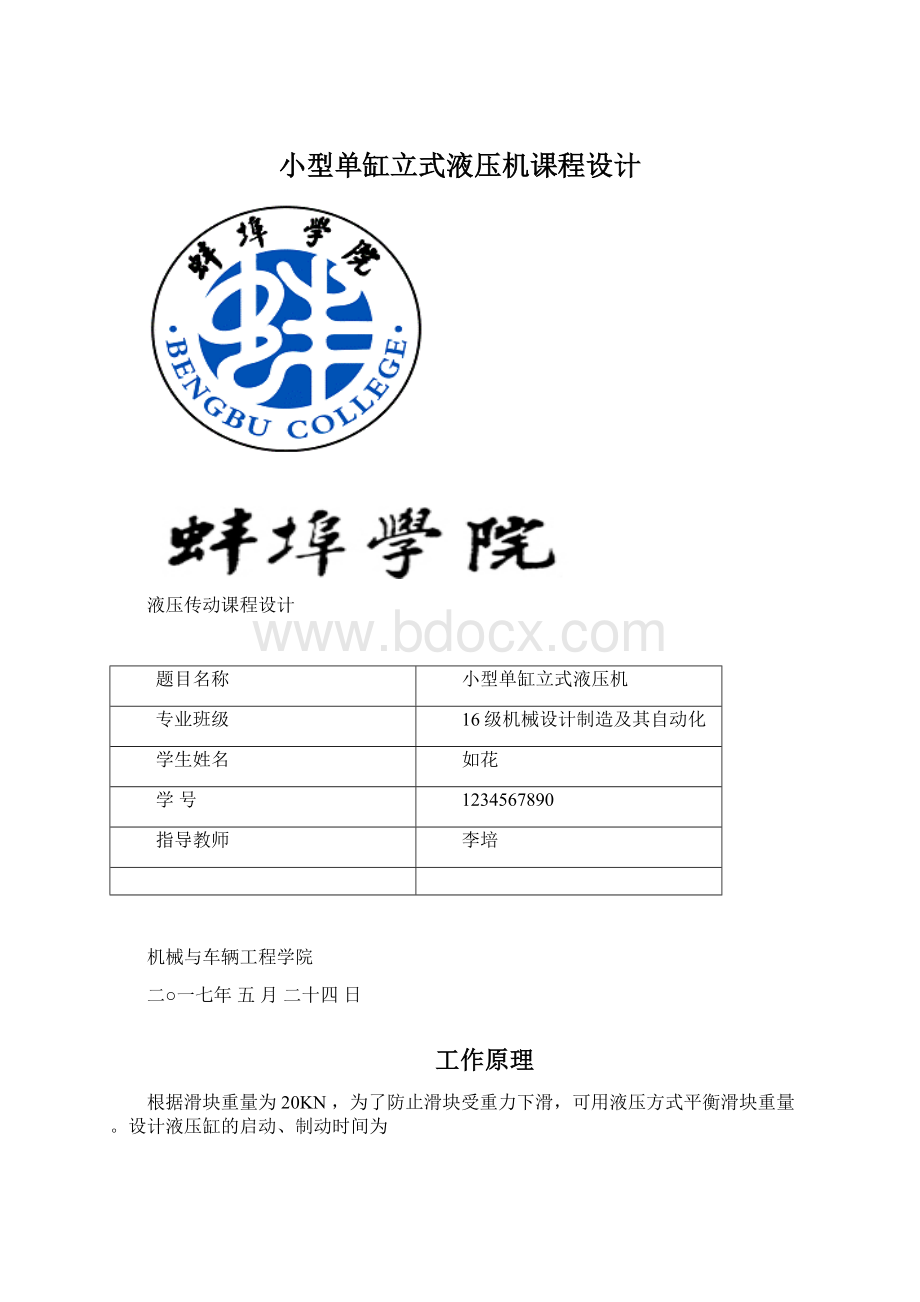
小型单缸立式液压机课程设计
液压传动课程设计
题目名称
小型单缸立式液压机
专业班级
16级机械设计制造及其自动化
学生姓名
如花
学号
1234567890
指导教师
李培
机械与车辆工程学院
二○一七年五月二十四日
工作原理
根据滑块重量为20KN,为了防止滑块受重力下滑,可用液压方式平衡滑块重量。
设计液压缸的启动、制动时间为
=0.02s。
液压机滑块上下为直线往复运动,且行程较小,故可选单杆液压缸作执行器,且液压缸的机械效率
1。
因为液压机的工作循环为快速下降、慢速加压、保压、快速回程四个阶段。
各个阶段的转换由一个三位四通的换向阀和一个二位二通的换向阀控制。
当三位四通换向阀工作在左位时实现快速回程。
中位时实现液压泵的卸荷,亦即液压机保压。
工作在右位时实现液压泵的快进和工进。
其工进速度由一个调速阀来控制。
快进和工进之间的转换由二位二通换向阀控制。
液压机快速下降时,要求其速度较快,减少空行程时间,液压泵采用全压式供油,且采用差动连接。
由于液压机压力比较大,所以此时进油腔的压力比较大,所以在由保压到快速回程阶段须要一个节流阀,以防在高压冲击液压元件,并可使油路卸荷平稳。
为了对油路压力进行监控,在液压泵出口安装一个溢流阀,同时也对系统起过载保护作用。
因为滑块受自身重力作用,滑块要产生下滑运动。
所以油路要设计一个单向阀,以构成一个平衡回路,产生一定大小的背压力,同时也使工进过程平稳。
在液压力泵的出油口设计一个单向阀,可防止油压对液压泵的冲击,对泵起到保护作用。
引言
液压机作为一种通用的无削成型加工设备,其工作原理是利用液体的压力传递能量以完成各种压力加工的。
其工作特点之一是动力传动为“柔性”传动,不象机械加工设备一样动力传动系统复杂,这种驱动原理避免了机器过载的情况。
一切工程领域,凡是有机械设备的场合,均可采用液压技术,它的发展如此之快,应用如此之广,其原因是液压技术有着优异的特点,归纳起来液压机的液压系统传动方式具有显著的优点:
液压机单位重量的输出的功率和单位尺寸的输出功率;液压传动装置体积小、结构紧凑、布置灵活,易实现无级调速,调速范围宽,便于与电气控制相配合实现自动化;易实现过载保护和保压,安全可靠;元件易于实现系列化、标准化、通用化;液压易与微机控制等新技术相结合,构成“机-电-液-光”一体化便于实现数字化。
第1章根据设计要求进行工况分析
1.1液压系统的工作要求
某小型单杠立式液压机的工作循环为快速空程下行—慢速加压—保压—快速回程—停止。
滑块的快速往返速度为3m/min,加压速度为40-250mm/min,压制力为200000N,运动部件总重为20000N,要求采用液压方式实现运动部件的平衡;不考虑各种损失。
下图为动作循环图。
图1-1工作循环图
1.2负载分析和运动分析
1.2.1确定执行元件的形式
液压机为立式布置,滑块做上下直线往复运动,往返速度相同,故可以选缸筒固定的单杆双作用活塞液压缸(取缸的机械效率ηm=0.9),作为执行元件驱动滑块进行压制作业。
1.2.2负载分析
1、快速下降:
启动加速Fi1=
由于忽略滑块导轨摩擦力,故快速下滑时为负载为0。
2、慢速加压:
压制时压头上的工作负载可分为两个阶段:
初压阶段,负载力缓慢地增加,约达到最大压制力的5%,其行程为15mm;终压阶段,负载力急剧增加大最大压制力,上升规律近似于线性,其行程为5mm,则
初压:
Fε1=Fmax
5%=200000
5%=10000N
终压:
Fε2=Fmax=200000N
3、快速返回:
启动Fi2=
F=Fi2+G=500+20000=20500N
等速F=G=20000N
制动F=G-Fi2=20000-500=19500N
表1-1工况负载表
1.2.3运动分析
取快速下降行程为180mm,快速上升行程为200mm。
已知加压速度为40-250mm/min,取加压速度为4mm/s。
1、快速下行:
2、慢速加压:
慢速加压分两个阶段:
初压阶段行程为15mm;终压阶段行程为5mm。
初压:
终压:
3、快速回程:
表1-2运动时间表
1.2.4液压机液压缸负载循环图和速度循环图
图1-2负载循环图图1-3时间循环图
1.3确定系统主要参数
预选液压缸的工作压力P1=8MPa,将液压缸的无杆腔作为主工作腔,考虑到液压缸下行时用液压方式平衡,则可算出液压缸无杆腔的有效面积:
液压缸内径(活塞直径):
将液压缸内径圆整为标准值,取D=200mm
根据快速上升与快速下降的速度相等,采用液压缸差动连接来实现,从而确定活塞杆直径,由
,得
将活塞杆外径圆整为标准值,取d=140mm,从而算得液压缸有杆腔与无杆腔的实际有效面积为:
液压缸在工作循环中各阶段的压力流量计算:
快速下行:
启动
恒速P=0
慢速加压:
初压
终压
q由
到0
快速回程:
启动
恒速
制动
表1-3负载流量表
工作循环中各阶段的功率计算如表:
表1-4功率表
1.4制定基本方案,拟定液压系统图
1.4.1调速回路的选择
1、进油节流调速:
进油节流调速回路在停车后启动的时候,由于进油路上的节流阀控制流量,活塞前冲很小,甚至没有冲击;在实现压力控制方面,进油回油调速的进油腔的压力随负载而变化,当工作部件碰到死挡块而停止后,其压力将升到溢流阀的调定压力,利用这一压力变化来实现压力控制是很方便的。
但是进油回油调速回路中,经过节流阀发热后的液压由直接进入液压缸的进油腔,故发热和泄漏比较大;由于进油回油调速回路中的回油路油液没有节流阀阻尼作用,所以它的运动平稳性差。
2、回油节流调速回路:
由于回油回油调速回路中的回油路油液有节流阀阻尼作用,同时空气也不易进入,所以可以获得较好的的运动平稳性;回油回油调速回路中,经过节流阀发热后的液压由直接回油箱冷却,故发热和泄漏比较小。
但是由于回油节流调速回路的进油路上没有节流阀控制流量,在停车后启动的时候,即使回油路上节流阀关的很小,也会使活塞前冲;在回油节流调速回路中,只有回油腔的压力才会随负载变化,当工件碰到死挡块时,其压力降至为零,利用这一变化来实现压力控制比较麻烦。
综上,本设计采用进油节流调速,并在回油路上加背压阀的回路,这样可以综合进油回油调速回路和会有调速回路的优点,提高回路的综合性能。
1.4.2三位四通电磁换向阀的选择
液压缸的运动方向采用三位四通M型中位机能电液换向阀控制,停机时换向阀处于中位,使液压泵卸荷,快速下降时换向阀处于右位,快速上升时换向阀处于左位。
1.4.3保压回路的选择
在三位四通电磁换向阀与液压缸之间设置一个液控单向阀,其控油口与液压缸的出油口管路相接,进油口与三位四通电磁换向阀相接,出油口与液压缸进油路相接,形成保压回路。
利用蓄能器的保压回路:
当液压缸工作压力不足时,通过释放蓄能器力的油液补充给液压缸来实现保压。
第一种保压回路可以自动的补充液压油,使液压缸的的压力能长期的保持在所需的范围内,而利用蓄能器的保压回路的保压时间取决于蓄能器的容量,没用第一种保压方案的保压时间长和稳定,故选用利用液控单向阀的自动补油保压回路。
在液压缸的进油路,液控单向阀出油路上连接一个电接点压力表,设置电接点压力表的上限、下限值,当液压缸的压力达到限值时,利用电接点压力发出的
电信号来实现切换四通三位电磁换向阀,以实现自动保压。
图1-4系统保压图
1.4.4快速回路的选择
1、差动连接快速路:
为实现压头的往返速度相等,需要有差动回路,在液压缸的进、出油口及液压缸出油口与换向阀之间分别连接两一个二位二通电磁阀。
液压缸快速下降时差动连接,快速上升时切断差动连接。
2、双泵供油快速回路:
双泵供油快速回路中,泵1为大流量泵,泵2是小流量泵,泵1与泵2之间放一个单向阀,快进时,油液由泵1经单向阀与泵2同时供油;工进时,控制泵1的液控顺序阀时其卸荷,只有泵2供油。
差动连接快速回路可以很好的控制其快进和快退的速度,使其符合题目中的快进和快退的速度相同;而双泵供油的泄漏大,效率低,结果复杂,成本高,故选择差动连接快速回路。
图1-5系统快速回路
1.4.5平衡回路的选择
防止压头在下降过程中由于自重而出现速度失控现象,在进如液压缸口处设置一个平衡回路来减轻这种现象。
1、减压平衡回路:
在回路中设置一个减压阀和一个溢流阀,形成减压平衡回路。
其中溢流阀的调定压力大于减压阀的调定压力。
2、顺序阀平衡回路:
在液压缸的出油口安装单向顺序阀来调定压力。
由于顺序阀的压力调定后,若工作负载变化小,则系统功率损失大,且活塞不可长时间停留在一个位置,不适合本设计保压要求,故选用减压平衡回路。
图1-6平衡回路
此外在泵的出口并联一个溢流阀,用于系统的安全保护;泵出口并联一个压力表及其开关,以实现测压;在液压泵的出口串联设置一个单向阀,以防止液压油倒灌。
综上,将各回路合并整理,检查以后绘制的液压机液压系统原理图如图所示:
图1-7系统回路图
1-油箱;2-过滤器;3-液压泵;4-溢流阀;5-压力表及其开关;6-节流阀;7-单向阀;8-背压阀;9-三位四通电磁换向阀;10-液控单向阀;11-减压阀;12-溢流阀;13-二位二通电磁换向阀;14-二位二通电磁换向阀;15-液压缸
系统图中个电磁阀的动作顺序见表:
表1-5磁阀的动作顺序表
第2章液压元件参数计算与选择
2.1确定液压缸的主要参数
2.1.1初选液压缸的工作压力
已知液压缸的最大工作负载为200000N,液压缸工作压力为:
2.1.2确定液压缸的主要结构参数
根据1章1.3节的内容,可知液压缸内径D=200mm,活塞杆外径d=140mm,液压缸无杆腔有效面积为A1=
,有杆腔有效面积为
。
2.1.3确定液压缸的工作压力、流量和功率
表2-1工作压力流量表
表2-2功率表
2.2液压泵及其驱动电动机的选择
液压缸的工作压力出现在终压后即保压阶段开始时,
。
此时缸的输入流量极小,且不考虑各种损失,故液压缸至泵间的进油路压力损失取值
。
算得泵的最高工作压力pp为:
。
所需的液压泵的最大供油量按液压缸的最大输入流量(
)进行估算。
取泄漏系数K=1.1,则:
根据系统所需流量,拟初选限压式变量液压泵的转速为n=1500r/min,暂取容积效率
,则可算得泵的排量参考值为:
根据以上计算结果查阅产品样本,选用规格相近YB—D200单联叶片泵,其额定压力Pn=6.3MPa,排量V=200ml/r,额定转速n=1500r/min,容积效率
。
其额定流量为:
符合系统对流量的要求。
不计任何损失,液压泵的最大理论功率即为液压缸工作时所需的最大功率Pp=1139.02W。
查手册,选用规格相近的Y100L2—4型封闭式三相异步电动机电机,其额定功率为3KW,同步转速1500r/min,满载转速1420r/min。
按所选电动机转速和液压泵的排量,液压泵的最大实际排量为:
满足使用要求。
2.3液压控制阀的选择
根据拟定的液压系统原理图,计算分析通过各液压阀的最高压力和最大流量,由设计手册,选择液压阀的规格,如下表:
2.4选择压力表
表1-3压力表型号
表1-4阀的规格表
2.5选择辅助元件
油管内径一般可参照所接元件接口尺寸确定,也可按管路允许流速进行计算。
管道内径及壁厚液压管道的两个主要参数,计算公式如下:
式中q—通过油管的最大流量,
;
—油管中允许流速,(取值见表1-5),m/s;
d—油管内径,m;
—油管厚度,m;
P—管内最高工作压力,MPa;
—管材抗拉强度,MPa;
油液流经油管
吸油管
高压管
回油管
短管及局部收缩处
允许流速
0.5~1.5
2.5~5
1.5~2.5
5~7
n—安全系数
表1-5油管流速表
管内最高工作压力/MPa
<17.5
7~17.5
17.5
安全系数
8
6
4
表1-6管内安全系数表
1、高压油管取内径d=25mm,则:
符合油管中的允许流速。
管材为45钢,其壁厚为:
取壁厚
=1mm。
2、对吸油管取内径d=60mm,则:
符合油管中的允许流速。
管材为45钢,其管内压力几乎为零,取其壁厚
=1mm。
3、对回油管取内径d=45mm,则:
符合油管中的允许流速。
管材为45钢,其管内压力最大时为0.41MPa,接近于零,取其壁厚
=1mm。
2.6过滤器的选择
表1-7过滤器型号表
2.7液压系统验算
前述液压系统的初步设计是在某些估计参数情况下进行的。
当系统原理图、组成原件及连接管路等设计完成以后,针对实际情况对设计进行各项性能分析计算。
其目的在于对系统的设计质量做出评价和评判,若出现问题,则应对液压系统某些不合理的设计进行修正或重新调整,或重新采取必要的措施。
性能验算内容一般包括压力损失、效率、发热和升温、液压冲击等,对于重要的系统,还应对其动态性能进行验算或计算机仿真。
计算时只采用一些简化的公式以求得概略的结果。
由于系统不考虑各种损失,且液压系统比较简单,因此不必进行液压系统性能验算。
第3章液压油缸的设计
3.1引言
液压缸有多种类型。
按结构特点可分为活塞式、柱塞式和组合式三大类;按作用方式又可分为单作用式和双作用式两种。
在双作用式液压缸中,压力油可供入液压缸的两腔,使缸实现双向运动。
由于该系统自身的特点,液压缸采用双作用式活塞式液压缸。
3.2液压缸的设计计算
3.2.1缸筒和缸盖组件
1、确定液压缸油口尺寸
液压缸的油口包括油口孔及连接螺纹。
油口可布置在缸筒或缸盖上,油口直径
应根据活塞最大速度
和油口最高流速
确定,计算公式如下:
式中D—液压缸内经,m;
—液压缸最大输出流速,m/min;
—油口流动速度,m/min,一般不大于5m/s。
对于无杆腔部位油口:
选取M22
1.5的链接螺纹尺寸。
对于有杆腔部位油口:
选取M22
1.5的螺纹连接尺寸。
2、确定缸筒和缸盖的连接形式
居于本设计,缸筒和缸盖的连接形式选用法兰连接。
3、选择缸筒和缸盖材料
缸筒选材:
铸钢45
前缸盖选材:
铸钢45
后缸盖选材:
铸钢45
4、计算缸筒和缸盖的结构参数
①缸筒壁厚
的计算
式中p—液压缸工作压力,MPa;
—试验压力,MPa,工作压力p≤16MPa时,
=1.5p;工作压力≥16MPa时,
=1.5p;
D—液压缸内径,m;
—缸体材料许用应力,MPa;
取铸钢
=120Pa;
②缸筒外径
的计算
标准液压缸的缸筒外径系列D1=220mm
③缸底厚度h的计算
对于平型缸底当缸底无油口时
当缸底有油口时
④液压缸头部法兰厚度h的计算
因为在缸筒头部有活塞杆导向孔,故其厚度的计算方法与缸底有所不同。
对于常用的法兰式缸头,其厚度的计算方法如下。
式中F—法兰受力总和这里取F=200000N
—螺钉孔分布圆直径,m;
—密封环平均直径,m;
[
]—法兰材料许用应力,Pa;
4、缸筒与缸盖的配合
缸盖与缸筒的配合采用H9/f9的间隙配合;缸筒与导向套采用H7/g9配合;缸底与缸筒采用H7/g6配合。
3.2.2排气装置
排气装置用于排除液压缸内的空气,使其工作稳定,一般把排气阀安装在液压缸两端的最高位置与压力腔相通,以便安装后、调试前排除液压缸内的空气,对于运动速度稳定性要求较高的机床和大型液压缸,则需要设置排气装置,如排气阀等。
排气阀的结构有多种形式常用排气阀为整体型排气阀,其阀体与阀芯合为一体,材料为不锈钢3Cr13,锥面热处理硬度HRC38~44。
3.3活塞及活塞杆组件
3.3.1确定活塞及活塞杆的连接形式
根据工作压力及活塞直径、机械振动的大小,选用螺纹连接。
3.3.2选择活塞及活塞杆的材料
活塞选择ZQSn6-6-3为材料;
活塞杆选择45钢;粗加工后调质到硬度为229~285HB,必要时高频淬火达到45~55HRC。
3.3.3活塞与缸筒的密封结构
活塞与缸筒之间既有相对运动,有需要使液压缸两腔之间不漏油。
根据液压缸的工作压力及作用选择Yx型密封圈进行密封。
根据公称直径进行选取沟槽的公差选取为h9或H9。
3.3.4活塞杆的结构
液压缸通常通过活塞杆的端部与其驱动机构相连接。
常用活塞杆端部结构形式,选用法兰结构形式。
3.3.5活塞杆的强度校核
活塞杆只承受轴向力的作用,因此只进行拉压强度校核,此时
3.3.6活塞杆的导向、密封和防尘
活塞杆导向套装在液压缸的有杆侧端盖内,用以对活塞杆进行导向,内装有密封装置以保证缸筒有杆腔的密封。
外侧装有防尘圈,以防止活塞杆在后退时时把杂质、灰尘和水分带到密封装置处,损坏密封装置。
1、导向套的尺寸配置与最小导向长度
导向套的主要尺寸时支承长度,通常按活塞杆直径、导向套的形式、导向套材料承受能力、可能遇到的最大侧向负载等因素来考虑。
导向套过短将使缸应配合间隙引起初始挠度增大,影响液压缸工作性能和稳定性,因此,设计时必须保证有一定的导向长度,一般液压缸的最小导向长度应满足:
L—液压缸最大行程,mm;
D—缸筒内经,mm;
导向套外圆与端盖内孔的配合采用H7/g6。
导向套内径的配合一般多为H8/f9(或H9/f9),其表面粗糙度为
0.63~1.25
。
外圆与内孔的同轴度不大于0.03mm,圆度与同柱度公差不大于直径公差之半,内孔中的环形油槽要浅而宽,以保证良好润滑。
2、活塞杆的密封和防尘
活塞杆常用密封与防尘结构,选用J型防尘圈。
3.3.7活塞
活塞在液体压力的作用下沿缸筒往复滑动,因此它于缸筒的配合应适当,即不能过紧,也不能间隙过大。
设计活塞时,主要任务就是确定活塞的结构形式,其次还有活塞与活塞杆的连接、活塞材料、活塞尺寸及加工公差等。
活塞的结构形式分为整体活塞和组合活塞,根据密封装置形式来选用活塞结构形式,该系统液压缸中可采用Yx形圈密封。
所以,活塞的结构形式可选用组合活塞。
3.3.8缓冲装置
液压缸的行程终端缓冲装置可使带着负载的活塞,在到达行程终端减速到零,目的是消除因活塞的惯性力和液压力所造成的活塞与端盖的机械撞击,同时也为了降低活塞在改变运动方向时液体发出的噪声,使液压系统速度换接平稳,速度稳定。
缓冲装置的工作原理时使缸筒低压油腔内油液(全部或部分)通过节流把动能转化为热能,热能则由循环的油液带到液压缸外。
液压缸的活塞速度在0.1m/s时,一般不采用缓冲装置;在0.2m/s时,则必须采用缓冲装置。
本设计的液压系统最大速度为3m/min,即0.05m/s小于0.1m/s,但是活塞较大,所以不设置缓冲装置。
3.4缸体长度的确定
液压缸的缸体内部长度应等于活塞的行程与活塞的宽度之和,缸体外形长度还要考虑到两端端盖的厚度,导向套宽度,一般液压缸缸体长度不大于内径的20~30倍,即在本系统中缸体长度不大于4000~6000mm。
本系统中:
活塞行程L=200mm;
活塞宽度B=(0.6~1)D=120~200mm,其中D为液压缸内经;
导向套滑动面的长度A=(0.6~1)D=120~200mm;
取活塞宽度B=120mm,导向套滑动面的长度A=120mm,液压缸缸底厚度H=20mm,液压缸缸盖厚度H=20mm。
液压缸缸体内部长度为液压缸行程长度、中隔圈宽度与活塞宽度之和,即:
液压缸缸体外形长度为液压缸内部长度、导向套宽度与缸盖厚度之和,即:
第4章液压油箱设计
4.1引言
液压油箱简称油箱,它往往时一个功能组件,在液压系统中主要用于储存液压油、散发油液热量、溢出空气及消除泡沫和安装元件等。
按新近的液压系统污染控制理论的要求,油箱不应该时一个容纳污垢的场合,而要求在油箱中油液本身时达到一定清洁度等级的油液,并以这样清洁的油液提供给液压泵及整个液压系统的工作油路。
4.2油箱的类型
按油箱的结构和用途分,通常分为整体式油箱、两用油箱和独立邮箱三种类型。
整体式邮箱是指在液压系统或机器内部的构件内形成的油箱;两用油箱是指液压油与机器中的其他目的的用油的公用油箱,独立油箱是应用最应用最广泛的一类油箱,其热量主要通过油箱壁靠辐射和对流作用散发,因此油箱是尽可能窄而高的形状。
根据油箱液面与大气是否相通,又可分为开式油箱和闭式油箱。
因此本系统选用开式油箱。
4.3油箱的容量
油箱的容量是油箱的基本参数。
油箱的容量包括油液的容量和空气的容量。
油箱的容量可用经验法或根据散热加以确定,本符合JB/T7938—1999《液压泵站油箱公称容量系列》的规定。
用经验法确定油箱的容量注意一下三种情况:
1油箱的容量通常为液压泵每分钟排出体积额定值的3~5倍;
2采用定量泵或非压力补偿变量泵的液压系统,油箱容量的要大于泵流量的3倍以上;
3采用压力补偿压力油泵时,应尽量提供至少为系统每分钟所需油液体积的平均值(以升记)3倍的油箱容积。
本系统液压泵为单联叶片泵,其每分钟输出油液的流量为300L/min,根据情况
,选用公称油箱容积为1000L的油箱。
油箱的外形长、宽、高分别为2340mm,860mm,815mm。
此油箱为不带支脚油箱,取油箱的壁厚为8mm。
4.4油箱设计
4.4.1箱顶、通气器、注油口
油箱的顶部结构取决于它上面安装的元件。
当箱顶上安装泵组时,顶板厚度为侧板的四倍,以免产生振动。
箱顶上一般要设置通气器、注油口,通气器常为附带注油口的结构。
取下通气帽可以注油,放回通气帽即成通气过滤器。
通气过滤器的网眼应小于250
,过流量应大于20L/min,过滤精度不小于40
,其容量应为液压泵容量两倍。
油箱箱顶上的螺纹孔应该用盲孔(不通孔),以防止污染物落入油箱内。
4.4.2箱壁、清洗孔、吊耳(环)、液位计
当箱顶与箱壁之间不可拆连接时,应在箱壁上至少设置一个清洗孔。
清洗孔的数量与位置应便于用手清洗油箱所有内表面。
清洗口盖板应能由一个人拆装。
清洗孔盖板应配有可重复使用的弹性密封圈。
为了便于油箱搬运,应在油箱四角上方焊接吊耳,对于无支脚油箱应设置起吊用孔。
液位计一般设置在油箱外壁上,并靠近注油口,以便于注油时观测液面。
液位计的下刻线至少比吸油过滤器或吸油管上缘高出75mm,以防止吸入空气。
4.4.3箱底、放油塞、支脚
应在箱底设置放油塞(≥M18×1.5),以便于油箱清洗和油液更换。
为此箱底应朝清洗孔和放油塞倾斜,倾斜坡度通常为1/25~1/20,这样就可以使沉积物(油泥和水)聚集到油箱中的最低点。
为了便于放油和搬运,应把油箱架起来,油箱至少离地150mm。
但本设计选用无支脚油箱,因此不设置支脚。
4.4.4隔板和除气网
油箱中,尤其是在油液容量超过100L的油箱中应设置隔板。
隔板要把系统吸油区和回油区隔开,并尽可能使油液在油箱内沿油箱壁环流。
隔板缺口处要有足够大的过流面积,使环流速度为0.3~0.6m/s。
溢流式隔板的高度不应低于液面高度的2/3;隔板下应有缺口,使吸油侧的沉淀物经此缺口以至回油侧,并经放油口排出。
为了有助于油液中的气泡浮出液面,可在油箱设置除气网。
除气网用网眼直径为0.5mm的金属网制作,并倾斜
~
布置。
如