Standard Guide for Specification.docx
《Standard Guide for Specification.docx》由会员分享,可在线阅读,更多相关《Standard Guide for Specification.docx(10页珍藏版)》请在冰豆网上搜索。
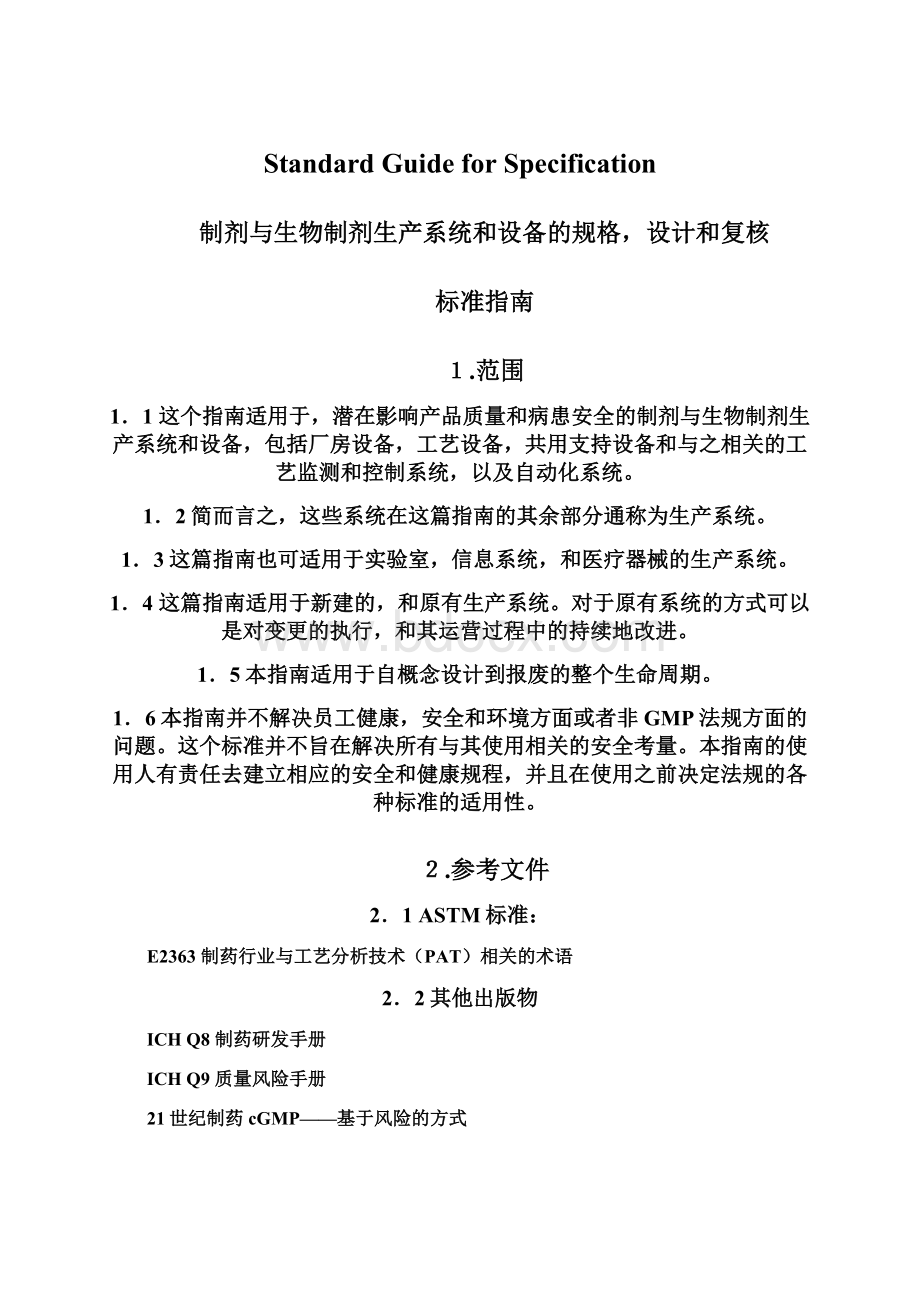
StandardGuideforSpecification
制剂与生物制剂生产系统和设备的规格,设计和复核
标准指南
1.范围
1.1这个指南适用于,潜在影响产品质量和病患安全的制剂与生物制剂生产系统和设备,包括厂房设备,工艺设备,共用支持设备和与之相关的工艺监测和控制系统,以及自动化系统。
1.2简而言之,这些系统在这篇指南的其余部分通称为生产系统。
1.3这篇指南也可适用于实验室,信息系统,和医疗器械的生产系统。
1.4这篇指南适用于新建的,和原有生产系统。
对于原有系统的方式可以是对变更的执行,和其运营过程中的持续地改进。
1.5本指南适用于自概念设计到报废的整个生命周期。
1.6本指南并不解决员工健康,安全和环境方面或者非GMP法规方面的问题。
这个标准并不旨在解决所有与其使用相关的安全考量。
本指南的使用人有责任去建立相应的安全和健康规程,并且在使用之前决定法规的各种标准的适用性。
2.参考文件
2.1ASTM标准:
E2363制药行业与工艺分析技术(PAT)相关的术语
2.2其他出版物
ICHQ8制药研发手册
ICHQ9质量风险手册
21世纪制药cGMP——基于风险的方式
3.术语
3.1定义——本片指南中所用到的定义条件,请参照E2363专门用语。
3.1.1接受标准——被用户或其他授权实体所接受的,一个系统或者部件必须符合的标准。
3.1.2设计复核——计划性地和系统划地对规格,设计,和设计过程与生产系统在生命周期内进行持续改进地变更,所进行的复核。
对应于标准和用户要求,’设计复核’对交工的文件进行评估,发现问题,并提出需要的改正措施。
3.1.3生产系统——与制剂与生物制剂生产能力有关的所有因素,包括生产系统,厂房设施,工艺设备,公用工程,和具有潜在影响产品质量和病患安全的工艺监测,控制系统,和自动化系统。
3.1.4专业问题专家(SME)——具有专业特长,和在一个特定领域或部门负有责任(比方说,质量,工程部,自动化,研发,运营,等等)。
3.1.5复核——一种系统性的方式来复核单个或组合的生产系统是否适用于指定用途、已经正确地安装、并且能够正常进行操作。
这是一个概括性的概念包括了所有确保系统适合使用的途径,比如说确认,调试与确认,复核,系统验证,或其他。
4.指南综述
4.1这篇指南描述了一个基于风险和基于科学的,对于能够潜产品质量和病患安全的生产系统和设备的规格,设计,和复核。
4.2这篇指南描述了一个系统性地,高效地,和有效地保证生产系统和设备适于目标用途的各种方式,并且保证关于产品质量,有效地管理各种导致病患安全的风险被,延伸到管理影响这些系统和设备的风险。
4.3总的目标是为提供已定的和受控的工艺生产能力,并稳定地生产出符合已确定质量要求的产品。
4.4本篇中描述的方式也支持持续的工艺能力改进,和试行的创新,比如工艺分析技术(PAT)。
4.5这篇指南中的主要元素是:
4.5.1将会应用到的基础核心概念。
4.5.2关于规格,设计,和复核过程的描述,与
4.5.3要求的支持性工艺的描述。
5.意义与用途
5.1本篇中描述的此种方式的使用,旨在满足国际上法规在保证生产系统和设备适于目标用途,并达到设计,安装,功能,和运行上的要求。
5.2这篇指南中描述的方式应用了FDA的创议中发起的理念和原则,21世纪制药cGMP——基于风险的方式。
5.3这篇指南支持、并与ICHQ8和ICHQ9的架构保持一致。
5.4这篇指南可以独立使用,或者借用到其他即将由ASTM国际出版的E55建议标准。
6.重要概念
6.1本指南应用到如下的重要概念:
基于风险的方式
基于科学的方式
生产系统的核心方面
质量源于设计
良好工程规程(GEP)
6.2基于风险的方式
6.2.1风险管理应该巩固其规格,设计和复核过程,并且在每一个阶段合理地使用。
6.2.2质量风险管理的两个最初原则在ICHQ9中定义到:
6.2.2.1质量的风险的评估应该建立在科学认知的基础上并且最终形成对病患的一种保护。
6.2.2.2质量风险管理过程的工作量,形式,和文件的水平应该和风险的水平相匹配。
6.2.3这些原则应该运用到生产系统的规格,设计和复核中。
6.2.4对于规格,设计和复核的质量风险管理的范围与其延伸,还有文件记录,应该建立在产品质量和病患安全的风险基础之上。
6.3基于科学的方式
6.3.1如果产品和工艺的信息与产品质量和病患安全相关,应该被当做制定基于科学和基于风险的决定的基础,以保证生产系统的设计与复核适用于其目标用途。
6.3.2考量产品和工艺的信息的例子有:
关键质量特性(CQAs),关键工艺参数(CPPs),工艺控制策略信息和先前的生产经验。
6.4生产系统的关键方面
6.4.1生产系统的关键方面典型的有功能,特征,能力和运行,或者能够保证稳定产品质量和病患安全的必要生产工艺和系统的各种特性。
这些应该被界定下来,在产品和工艺的科学理解的基础上做成文件。
6.4.2简而言之,这些特性在这篇指南的其余部分通称为关键方面。
6.4.3复核的实施应该集中在生产系统的这些方面,并且应该记录下来。
复核过程在7.4中详细描述。
6.5质量源于设计
6.5.1质量源于设计的概念应该用来确保在规格和设计过程中,关键方面被设计进系统。
设计和相关的接受标准的关键方面应该记录下来。
6.5.2保证生产系统适用于目标用途,不应该仅仅依靠于安装后的复核,而应该在整个系统生命周期中,通过计划了的,和组织好的复核应用方式来取得这一保证。
6.6GoodEngineeringPractice(GEP)良好工程规范
6.6.1GoodEngineeringPractice(GEP)良好工程规范应该加强并且支持规格,设计和复核活动。
6.6.2GoodEngineeringPractice(GEP)良好工程规范被定义为那些在生命周期内所应用的确定了的工程措施和标准,以提交合适的和有效的解决办法。
6.6.3GoodEngineeringPractice(GEP)良好工程规包括:
6.6.3.1规格,设计和安装活动应该全面地将各种适用的要求加进来,包括GxP,安全,健康,环境,劳动强度,操作性,维护,承认的行业标准,和其他的法律要求。
6.6.3.2与质量相关的规定应该包含在规格,设计和其他的合同文件里面。
6.6.3.3生命周期的文件记录涵盖了应该提供的计划,规格,设计,复核,安装,接受和维护。
6.6.3.4对实施,建造和安装活动的进行合适的复核可以达到一定水平的监管和控制。
图一 规格,设计和复核
6.7专业问题专家(SME):
6.7.1专业问题专家(SME)定义为,具有专业特长,和在一个特定领域或部门负有责任(比方说,质量,工程部,自动化,研发,运营,等等)。
6.7.2在自己的本专业和责任范围内,专业问题专家(SME)在生产系统的复核活动中应当充当合适的领导角色。
6.7.3专业问题专家(SME)的责任包括计划和定义复核的策略,定义接受标准,选择恰当的测试方法,复核测试的执行和结果审核。
6.8供应商材料的使用
6.8.1供应商文件,包括测试文件可以当做复核文件的一部分,作为一个合格的公司对它的供应商的进行的评估作为证据,这些证据是:
6.8.1.1合格的供应商质量系统。
6.8.1.2供应商技术能力,和
6.8.1.3供应商的GEP的应用,比如供应商提供的信息需要准确并且可以满足复核的目的。
6.8.2若在供应商的质量体系,技术能力,GEP的应用中有不恰当的因素存在,那么合格的用户可以选择通过使用特定的,目的性的,额外的复核检查或者其他控制,去消除这些潜在的风险,而不是简单地重复供应商的测试,和复制供应商的文件。
6.8.3是否使用供应商文件来支持生产元素中的关键方面的决定与判断,应当建立在生产系统的未来用途上,应当文件记录下来,并且由包括质量部门在内的专业问题专家(SME)来批准。
6.9持续性的改进
6.9.1随着在商业生产中经验不停增加,通过阶段性的复核和评估,操作和运行数据,和差错的原因分析等等,会发现越来越多的改进机会。
6.9.2在这篇指南中描述的规格,设计,和复核方式之后,变更管理应该提供一个非独立的机理,能够推广技术性改进的实施。
7.过程
7.1概述——生产系统的规格,设计和复核的过程,应该包括如下的活动:
要求定义
规格和设计
复核
接受和放行
7.1.1在整个过程中应该应用良好工程规程(GEP)的概念。
7.1.2风险管理应当恰当地执行,以评价对于与产品质量和病患安全相关的生产系统与相应的设计方法的风险。
风险管理是一个支持性的过程,在8.2中进行了定义。
7.1.3设计回顾应该在生产系统的整个生命周期中进行。
设计回顾过程是一个支持性的过程,在8.3中进行了定义。
7.1.4在整个过程中应该应用变更管理.变更管理是设计回顾过程是一个支持性的过程,在8.4中进行了定义。
7.2用户要求的界定:
7.2.1详细的用户要求应当确定下来,并应当做为接下来生产系统的规格,设计,和复核工作的基础.
7.2.2这些与产品质量和病患安全相关的详细要求应当建立在如下的基础之上:
7.2.2.1产品认识和理解
7.2.2.2工艺认识和理解
7.2.2.3法规要求和
7.2.2.4公司质量的要求
7.2.3产品和工艺认识与理解,包括在产品和工艺中变量的来源的认识,关键质量特性的识别,和工艺控制策略信息,应该建立在实验性和研发工作和生产经验中积累的科学数据的基础上。
产品和工艺的认识组成了在ICHQ8中描述的科学理解的基础,和工艺控制策略。
7.3规格与设计
7.3.1企业应当建立恰当的机制以充分沟通用户的要求,包括产品质量考量,对进行设计的相关人员,这样才能根据相关的产品、工艺以及其他要求的相关知识正确地设计出生产系统。
7.3.2规格编写和设计活动应该着重包括那些被鉴别为对产品质量和病患安全有影响的关键方面。
7.4复核——应该界定一种系统性的方法来复核单独或者组合的生产系统,看是否适合计划的用途,已被正确地安装,正常地运行。
这种复核的方式应该被界定并且文件记录下来。
复核的外延和文件详细的程度应该取决于包括那些与——产品质量,病患安全,复杂程度和生产系统的创新程度等相联系的各种风险。
7.4.1接受标准
7.4.1.1接受标准是一个生产系统为了适于使用,而必须要满足的标准并且被用户或其他授权实体所接受。
7.4.1.2接受标准应该由专业问题专家(SME)来界定。
7.4.1.3关键方面(即对于产品质量和病患安全的关键方面)的接受标准应该被质量部门批准。
7.4.2复核策略
7.4.2.1接受标准和复核策略应该在合适的复核计划中记录下来。
7.4.2.2复核计划应该界定包含了哪些附属复核活动的可接受的文件记录。
7.4.2.3复核计划应该由专业问题专家(SME)来编写并且批准。
含有关键方面的系统的计划应由质量部门来批准。
7.4.3复核活动:
7.4.3.1专业问题专家(SME)应该执行或者主持复核活动,并且按照复核计划中的规定,记录复核结果。
7.4.3.2供应商复核文件可以被启用,按照6.8中所述。
7.4.4复核的检查
7.4.4.1所有结束的复核文件记录应该由具有适合资格的,与独立的,并且没有参与复核活动的专业问题专家(SME)来检查。
7.4.4.2检查者应该保证所有的测试已经结束并正确地记录。
7.4.4.3与复核计划的脱离与偏差,应当被正确地处理并由检查者和/或其他合适的专业问题专家(SME)来妥善解决。
7.5接受与放行
7.5.1专业问题专家(SME)应当确定生产系统适合指定用途。
该确定应该正确地记录下来。
7.5.2这份记录应该包括一次检查或对结果的总结,对注明了的关键方面的接受标准出现不合格情况时的检查。
7.5.3文件记录需要包括,一份建立在检查基础上的,关于该生产系统是够适合指定用途的明确的陈述。
参与制定此项决定的人员应确定并记录下来。
7.5.4这样的文件记录应该由专业问题专家(SME)来准备并且批准。
该系统的关键方面的文件应该由质量部门来批准。
7.5.5在批准之后,此生产系统可被放行,用于生产运行。
8.支持性过程
8.1上面描述的规格,设计和复核过程应该由风险评估,设计回顾,和变更管理来支持,正如下面的章节所述。
8.2质量风险管理:
8.2.1对于药品质量和病患安全,质量风险管理是一个系统的风险评估、控制、沟通和回顾的过程。
8.2.2风险管理应该在适当的阶段进行,以评估相关于生产系统与相应设计方案的产品质量和病患安全的风险。
8.2.3与提交的供应商和建筑施工相关的风险,和因为技术革新或者复杂性相关的风险应该被联系于他们对产品质量和病患安全的影响进行考虑。
8.2.4风险评估应该由专业问题专家(SME)进行。
8.2.5依靠风险评估,应该选择适当的控制手段和复核技巧,着重于生产系统的关键方面,将风险管理到一个可接受的水平。
8.2.6控制和复核的程度应该与和产品质量与病患安全相关的风险水平相一致。
8.2.7如果风险不能够通过设计手段来降低,应该应用其他的恰当的风险控制机制。
8.2.8在ICHQ9上可以找到有关于风险管理上的更多的细节。
8.3设计回顾
8.3.1设计回顾是计划性地和系统性地对规格、设计、设计过程和在生产系统生命周期中进行的不断改进的变更的各种回顾。
8.3.2设计回顾对照标准和用户要求,评估递交的文件,发现问题,和提出必要的纠正行为。
8.3.3设计回顾应当用来确保:
8.3.3.1设计满足产品和工艺的要求。
8.3.3.2恰当处理生产系统的关键方面。
8.3.3.3确定产品质量和病患安全的风险。
8.3.3.4不可接受的风险通过设计、和其他手段来降低或消除。
8.3.4设计回顾应该由合适的专业问题专家(SME)来进行。
8.3.5设计回顾应该被文件记录。
执行回顾的每个人应该被确定。
8.3.6设计回顾的文件记录应包括一个陈述:
若有疑问的事项被接受的话,提出的纠正建议应已被执行完成。
8.4变更管理
8.4.1应该建立变更管理,并将其过程应用于整个生命周期中。
8.4.2在接受之前,变更管理就应该开始应用。
专业问题专家(SME)应该掌管这个过程并批准这些变更。
8.4.3在接受之后,在商业生产之前,应该启用运行变更管理。
在运行变更管理中,所有与产品质量和病患安全相关的规格要求的变更,都需要质量部门的预先批准,除非对特定变更或特定情况有预先的约定。