视图及图面标准.docx
《视图及图面标准.docx》由会员分享,可在线阅读,更多相关《视图及图面标准.docx(19页珍藏版)》请在冰豆网上搜索。
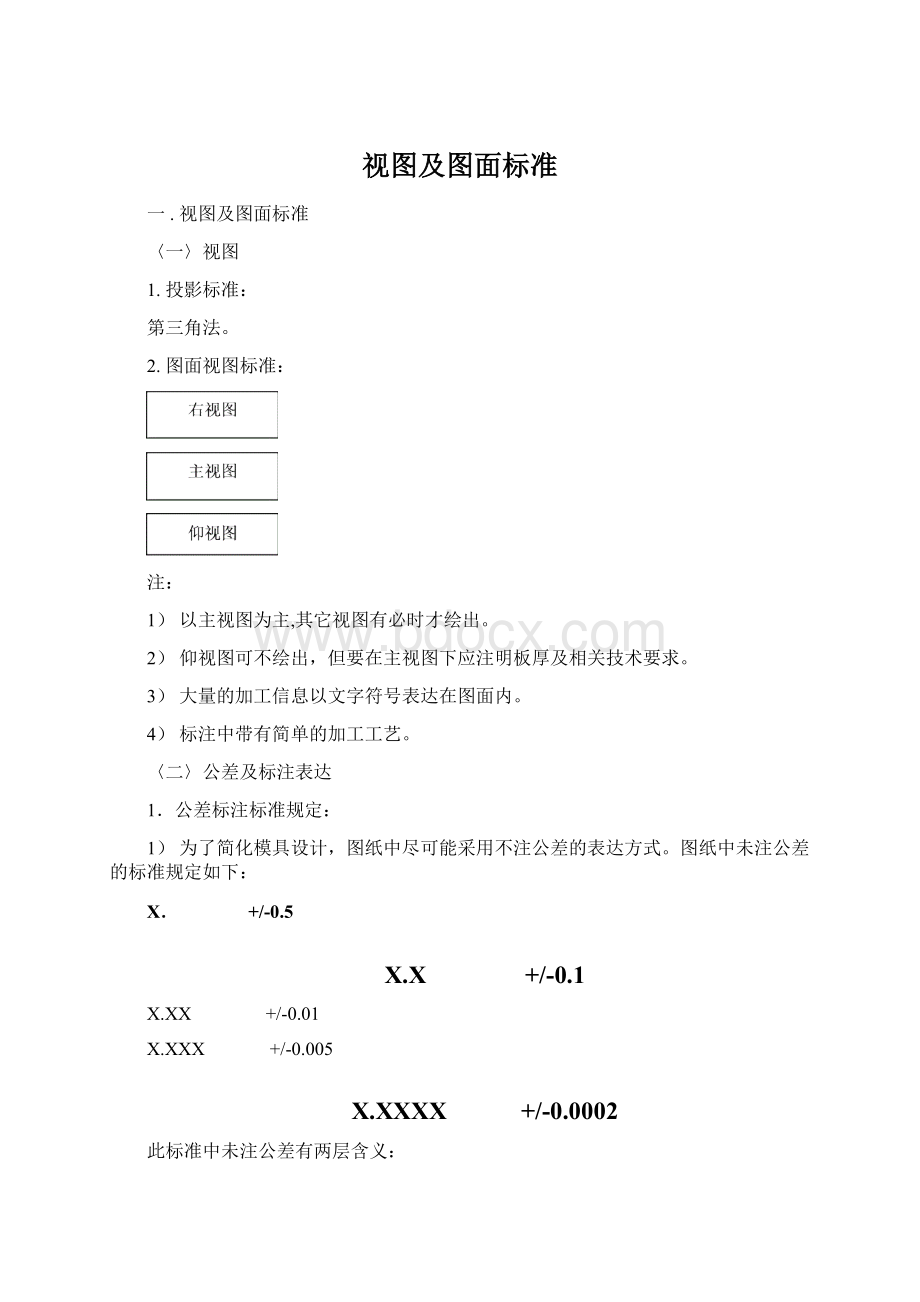
视图及图面标准
一.视图及图面标准
〈一〉视图
1.投影标准:
第三角法。
2.图面视图标准:
注:
1)以主视图为主,其它视图有必时才绘出。
2)仰视图可不绘出,但要在主视图下应注明板厚及相关技术要求。
3)大量的加工信息以文字符号表达在图面内。
4)标注中带有简单的加工工艺。
〈二〉公差及标注表达
1.公差标注标准规定:
1)为了简化模具设计,图纸中尽可能采用不注公差的表达方式。
图纸中未注公差的标准规定如下:
X. +/-0.5
X.X +/-0.1
X.XX +/-0.01
X.XXX +/-0.005
X.XXXX +/-0.0002
此标准中未注公差有两层含义:
A.表达要求公差,但模具加工单位要以高于此公差的标准来加工。
B.表达一种工艺,即X.X为铣削加工,X.XX、X.XXX为磨削加工或线切割加工。
2)对于有的公差不方便用以上标准表达时,可以直接标注需要的公差。
2.有关术语的中英文对照:
本标准的标注中,绝大部分加工信息由图面的文字符号表达出来,其符号规定如下:
钻:
DR 攻丝:
TAP 铰:
REAM
铣台阶孔:
CB 铣:
MILL 通孔:
THRU
深度:
DP 锥度:
TAPER 刃中高度:
LAND
正面:
FF 反面:
FS 线切割:
W/C
其中FF,TAP,THRU有时省略。
3.铣床、钻床加工的文本标注要求。
1)、铣床、钻床加工包括:
钻孔,攻丝,铰孔,钻台阶孔,铣型腔等。
2)、铣床、钻床加工一般尺寸标注为X.X,表明其公差为士0.1,但通常情况下X.X表明加工工艺为铣或钻,其公差为机床所能达到的公差。
铰孔标注为∮XH7,按国家标准执行。
3)为满足铣床工艺方面的要求,模板的尺寸标注应使用绝对坐标的形式。
4)用于安装大于或等于M10的螺塞的螺纹孔,应注明为细牙螺纹。
如M12*1.5THRU。
3)、标注文本时,需说明工艺要求,并需标注工艺尺寸,如穿丝孔等。
但攻丝和铰孔无需标明底孔直径。
如图1—1所示:
(a) DR8.0THRU-------钻8.0的通孔。
(b) TAPM8THRU----攻M8的螺纹,攻通。
(c) REAM∮8.0H7THRU------铰8.0的通孔。
(d) DR8.0THRU,CB12.0DP8.0------钻8.0的通孔,正面铣 ∮12.0深8.0的台阶孔。
(e) DR8.0THRU,CB12.0DP8.0FS------钻8.0的通孔,反面铣∮12.0 深8.0的台阶孔。
以上数值为有效值,如M8DP10指M8的有效深度为10,DR∮10DP20指钻∮10的孔,有效深度为20。
4.切割加工中文本标注要求和设计要求。
1)、基准孔的设置:
基准孔是加工、装配及模具反修的基准,有基准棒与其配合,通常SP,PP,DP板上的基准孔割成如图1—2所示的形式。
一般情况下基准孔应设置两个,且两孔连线应平行于X或Y轴线,尽可能保证其坐标与零件的基准的相对坐标为整数,且保证内导柱和销钉孔的座标为整数。
面积超过机床最大加工范围则需设置2个
以上的基准孔。
a.凹模板,卸料板,冲头固定板必须做成标准的基准孔。
上下模座只需铰出∮6H7的孔即可,不必割出,垫板的基准空做成∮6.4的通孔。
2)、销钉孔的设置
a.销钉的作用为定位,其图面的表达方式如图1-3所示:
b.同一模板上可设置四个销钉孔,且其与基准孔的相对位置的坐标都为整数,但使用时只用对角的两个,并且尽可能保证使用的两个销钉孔的距离最大。
c.DP,PP,SP板上的销钉孔用线割保证。
d.模座上的销钉孔应注意机加工工艺,如板太厚时,应设法减少铰孔深度。
如果条件许可,模座上的销钉孔用加工中心加工,否则设法配做。
3)、穿丝孔的设置
a.对于穿丝孔的设置,要注意线割的走丝轨迹,有的地方是可以割破,有的地方是不能割破,不能割破的部分采用INSERT结构,穿丝孔可以用钻或EDM保证,用钻床工艺尽可能用∮3~∮6的刀具。
b.线切割圆形时,穿丝孔设置在圆心。
c.线切割矩形时,且有一边长<10mm,穿丝孔设置在几何中心。
d.线切割矩形时,且有两边>10mm穿丝孔设置在矩行长边的中心
略5mm处。
如图1—4所不:
4)、异形、复杂的型孔,型腔的标注。
a.异形复杂的型孔,为保证图面的整齐,一般不标注线割的尺寸,但要标全铣削和磨削的加工尺寸,包括穿丝孔的大小和位置,线割的尺寸由机床保证,通常情况下在X和Y方向上各标一个检验尺寸。
当模板图纸附有磁盘时,不需将异形孔移出模板标注尺寸,仅需在磁盘和图纸上画出穿丝孔,然后标明线割部分的间隙为多少。
冲裁凹模要标注刃口高度和漏料孔的锥度。
如:
W/C(A.B.C.D.)+0.05/SIDE,3.0LAND TAPER1°
解释:
线切割割型孔A,B,C,D,实际尺寸按基准尺寸单边放大0.05mm,且刃口高度为3.0漏料锥度为1.0°。
b.所有的圆孔间隙都放好,保证标注尺寸与实际尺寸相一致。
所有异型孔的间隙不放,其间隙用文字表达在图面上。
c.它复杂型孔视情况而定。
基本的原则是加工信息表达清楚完整。
〈三〉图纸标准
1. 所有零件图纸必须使用本公司的标准图框形式。
既标准的A0,A1,A2,A3,A4图框
2.图纸的更改符合ISO9001的要求。
3.全套模具图纸应包含的内容:
a.产品图纸(产品展开图)
b.排料图或工序图
c.模具总装图
d.加工零件图
e.模具零件明细表
f.标准件清单
g.模具材料清单
4.模具图书写标准:
a.标注铣削图形座标时,须标注出铣刀的轨迹座标。
b.模具图中不标模板倒角,但制造时须制造出必要的倒角。
c.技术要求注明在主视图的下方.格式如下:
(编号) (名称)
1. MATL:
----
2. QTY:
----PCS
3. HAD:
----HRC
4. THICKNESS:
----mm
d.模具零件图的标注须体现加工类型和加工内容。
5.标注符号采用中兴的统一标准.即本章前面的标准。
(四)电子图档的要求
1.模具设计图层建立的规定
1) TCP 上盖板
2) TP 上模座
3) TBP 上垫板
4) PP 固定板
5) SBP 卸料垫板
6) SP 卸料板
7) DP 凹模板
8) DBP 凹模垫板
9) DS 下模座
10) PB 模脚
11) PUNCH 冲头
12) SP-INSERT1 卸料板中固定的INSERT
13) SP-INSERT2 卸料板中活动的INSERT
14) SP-INSERT3 卸料板中INSERT中的INSERT
15) DP-INSERT1 凹模板中固定的INSERT
16) DP-INSERT2 凹模板中活动的INSERT
17) DP-INSERT3 凹模板中INSERT中的INSERT
18) 0 产品的排样图
19) CUT 模具的切料形状
20) ARRY 装配图
21) DIM 尺寸标注
对于电子图档,装配图要求完整,其中模板的符号严格要求,其余的可以根据模具的难易程度作适当的增减。
2.模具图颜色的使用规定
1) 1 (RED) 放间隙的线割部分
2) 2 (YELLOW) W/C(FAST)快丝线切割
3) 5 (BLUE) 尺寸标注线
4) 6 (MAGENTA) 不放间隙的线割部分
5) 2 (YELLOW) PUNCH
6) 4 (CYAN) SP-INSERT1
7) 3 (GREEN) DP-INSERT1
8) 5 (BLUE) DP-INSERT2
我们对RED和MAGENTA两种颜色的使用严格限制,因为这关系道模具加工的线割编成,减少编成的失误。
3.模具的电子档要和图纸完全统一。
1)模具调试时有零件更改时,要及时更新图档。
保证图档是最新版本。
同时保证加工单位的图档是最新板本,
2)模具由于改模需要出图时,要在图面上指明图档路经。
3)对于改模的图面,要用色笔标出更改的部位,以方便加工。
二.模板标准
1.模具大小的定义。
模具的大小根据其长度来定义。
结合我们公司的模具结构,分类如下:
模具长度(mm)
模具大小
<400
小型
400---800
中小型
800---1,200
中型
>1,200
大型
2.模板厚度的设计标准。
模板厚度根据具体情况确定,为了节约资源,所有模板采用最小化原则,此板厚标准是基于此原则由经验丰富的设计师根据标准件及模具结构制定。
所以尽可能采用标准板厚。
1).冲压课连续模的基本结构如2-1(但具体结构会根据产品的结构确定),其模板厚度标准如下:
模板
中小型连续模
大型连续模
1.TCP
15
15
2.TP
50,60
60,65
3.TBP
15
15
4.PP
20
20
5.SBP
13,18
13,18
6.SP
20(25)
20(25)
7.DP
25(30)
25(30)
8.DBP
15
15
9.DS
50,60
60,70
1.TCP 2.TP 3.TBP 4.PP 5.SBP 6.SP 7.DP 8.DBP 9.DS
2).冲压课落料复合模的基本结构如2-2(但具体结构会根据产品的结构确定),其模板厚度标准如下:
1.上模座 2.上模凹模固定垫板 3.上模凹模固定板 4.凹模板 5.导套 6.上模卸料板 7.导柱 8.下模卸料板 9.冲头 10.冲头固定板 11.下模座
模板
中小型落料模
大型落料模
1.上模座
30,40
40
2.上模凹模固定垫板
15
15
3.上模凹模固定板
20
20
4.凹模板
25
25
5.上模卸料板
20
20
8.下模卸料板
20
25
9.冲头
35
40
10.冲头固定板
20
25
11.下模座
40,50
50
3).冲压课弯曲模的基本结构如2-3(但具体结构会根据产品的结构确定),其模板厚度标准如下:
1.上模座 2.冲头固定板 3.弯曲冲头 4.压料板 5.弯曲块 6.固定板 7.键 8.下模座
模板
中小型弯曲模
大型弯曲模
1.上模座
30,40
40
2.冲头固定板
合模高度及产品高度决定
3.弯曲冲头
25
30
4.压料块
20
25
5.弯曲块
40,50
50
6.固定块
15
20
7.键
15*20*(60-100)
15*25*(60-100)
8.下模座
40,50
50
3.连续模模具材质及硬度标准
序
号
名称
代号
材质
厚度
(mm)
硬度
(HRC)
备注
1
上盖板
TCP
45#
15
***
2
上模座
TP
45#
40~60
***
3
上垫板
TBP
40Cr
(Cr12,45#)
15
40~45
4
固定板
PP
45#
(Cr12MoV)
20
***
(58~62)
5
卸料垫板
SBP
40Cr
(Cr12,45#)
18,13
40~45
6
卸料板
SP
Cr12MoV
20
55~57
7
凹模板
DP
Cr12MoV
25
58~62
8
下垫板
DBP
40Cr
(Cr12,45#)
15
40~45
9
下模座
DS
45#
45~70
***
10
模脚
PB
45#(A3)
***
***
11
冲头
PUNCH
DC53,SKD11,
Cr12MoV,ASP12
***
60~63
12
卸料INSERT
SP-INSERT
Cr12MoV,
DC53,SKD11
***
60~62
13
凹模INSERT
DP-INSERT
DC53,SKD11,
(Cr12MoV)
***
60~63)
另外,如果凹模上所有切料均采用镶块形式,则凹模板可用硬度为40---45HRC的40Cr钢,而镶块则采用60---62HRC的Cr12MoV、DC53或SKD11。
注:
为什么保证DP、SP、SBP、PP的厚度?
因为连续模开发周期比较短,模板和小件的加工是同时进行,最后再集中组装,如果模板的厚度出了问题,相应的小件的高度会发生改变,最后会引起大量的零件反修!
所以应当严格控制模板的厚度。
三.模具设计中的计算
1、冲模设计中力的计算
1)、冲压力
Po=LTδ
Po——冲切力(Kg)
L——冲切长度(mm)
T——材料厚度(mm)
δ——材料抗拉强度(Kg/mm)
2)、卸料力
P=KPo
P——卸料力(Kg)
K——卸料力系数(一般取K=0.04---0.07)
Po——冲切力(Kg)
3)、弯曲力
自由弯曲的弯曲力
0.6KBt2δb
V形弯曲 P1=--------------------
R+t
0.7KBt2δb
U形弯曲 P1=--------------------
R+t
式中:
P1——材料在冲压行程结束时,不受校正的弯曲力(N);
B——弯曲件的宽度(mm)
t——弯曲件材料厚度(mm)
R——弯曲内半径(mm)
δ、b——弯曲件材料抗拉强度(N/mm2)
K——安全系数,一般取1.3
4).顶件力和压料力
顶件力或压料力P3值可近似取自由弯曲力的30~80%,
即P3=(0.3~0.8)P1
2、弯曲件的尺寸展开
1)、R>0.5t的弯曲件(按中性层不变计算)
L=L1+L2+π/2(r+kt)
T——材料厚度
K——补偿系数(见下表)
序号
1
2
3
4
5
6
7
8
9
R/T
0.1
0.2
0.25
0.3
0.4
0.5
0.6
0.8
1
K
0.3
0.33
0.35
0.36
0.37
0.38
0.39
0.41
0.42
序号
10
11
12
13
14
15
16
17
18
R/T
1.2
1.5
1.8
2
3
4
5
6
8
K
0.43
0.45
0.46
0.46
0.47
0.48
0.49
0.5
0.5
2).R<0.5t的弯曲件,根据经验计算:
L=L1+L2+Kt
K=0.35~0.45(一般公司取0.4)
3)根据我们的经验,无论内R为多少,都可以按中心层不变原理展开,其公式同上,即:
L=L1+L2+π/2(r+kt)
当内r=0mm时,模具设计时取:
r=0.3t
再用电脑展开,其展开参数同上表。
4)出现“Z”形弯曲时,要根据模具结构、材料的厚度和材料的硬度,由模具设计工程师根据经验适当的增加偿值。
5)对于有些情况无法展开准确,而产品要求又特别的高的情况下,在模具设计时应做适当的处理,尽可能在更改切料尺寸时不用再加工模板。
3. 翻孔的计算:
1).翻孔的参数参考下表取值
THREADSIZE
DETAIL
MATERIALTHICKNESS
0.5
0.8
1.0
1.2
1.55
2.0
M2.5
A
2.28
2.31
2.31
B
3.30
3.5
3.76
H
0.8
0.90
0.85
D
1.3
1.20
1.20
M3
A
2.76
2.76
2.79
2.79
2.76
B
3.50
3.80
4.00
4.26
4.56
H
0.80
0.80
1.00
1.00
1.00
D
1.50
1.80
1.60
1.60
1.61
M3.5
A
3.21
3.21
3.21
3.21
B
4.16
4.50
4.70
5.10
H
0.80
1.00
1.00
1.05
D
2.40
2.00
2.00
2.00
M4
A
3.69
3.66
3.66
3.66
3.66
B
4.67
4.90
5.16
5.50
6.10
H
1.0
1.00
1.00
1.05
1.20
D
2.20
2.30
2.40
2.50
2.50
M5
A
4.56
4.56
4.56
B
6.00
6.45
7.05
H
1.40
1.40
1.40
D
3.00
3.00
3.00
2)、对于表中没有的,按体积不变计算
即:
π(B2-A2)/4(T+H)=π(B2-d2)/4TK
因为由于整个孔不规则,所以实际上计算的体积前后不等,在计算时乘以补偿系数K,K值从上面的参数推出。
(K值一般为0.82~0.85)。
四、工件排样
工件排样是冲压工件及模具设计的重要环节,它直接影响到材料的利用率,工件的质量,生产率,模具制造难易程度,模具寿命等,在排样时,应注意以下几点:
1、排样时,要特别注意材料的纹向,避免纹向与弯曲线平行,尽可能使其与弯曲线垂直。
(不过,一般情况下,主要考虑材料的利用率,只有产品对纹向有特别要求时才主要考虑材料的纹向,这种情况下材料的利用率一般不是最高)。
2、排样时,应充分考虑精确可靠的定位。
特别注意导正钉的分布和直径。
直径尽可能大一些,同时有利于产品的定位;对于有成型的部位,可能会引起导正钉孔的变形,这种情况一定要考虑更换导正钉孔的位置;对于拉深件,拉深后产品位置可能发生变化,所以拉伸后要考虑用产品的形状定位。
3、一般情况下第一步冲导正钉孔,下一步才冲产品的其他部位,但当步距很大时,可以在第一步同时冲产品。
4、相对位置精度要求较高的型孔,应尽可能在同一工步冲出;型孔与外形的位置精度要求较高时,应尽可能在相邻工步冲出。
5、弯曲成型部位需安排得容易送料和不易变形,同时还应当考虑模具尽可能简单,加工方便。
6、弯曲达不到工件要求时,可采用两次弯曲或增加整形工位;对于直角的弯曲,为了避免材料的拉伸,可采用先弯45度,再弯90度;弯曲时一定要考虑压料,特别是材料较厚时,压料力要求特别的大,这时候就应当冲工艺上考虑,如采用对称弯曲;弯曲的工艺对产品尺寸的展开有影响。
7、当刃口距离太近时,应设置空步,以提高DP,SP,PP的强度。
有时侯当预感到某一步可能会有问题时,后面要留有改模空间。
8、排样时应考虑模具的制造简单,模具调试的方便性。
尽可能保证调模时不要动太多的零件。
9、对于复杂的型孔,应分解成若干个简单的型孔进行分步冲裁。
但在分解时应注意前后冲次的良好衔接,即采用适当的工艺接口,一般情况下工艺接口的位置、大小、形状要经过客户的书面确认。
在型孔分开时,还应当同时考虑PUNCH、DP-INS的固定方法,加工方法。
10、为了使材料在冲压过程中稳定进给,必须在排样中设置载体,并在连接处把工件和材料连接起来。
载体一般设置在材料的两侧,中间部位或单侧,载体的大小要有足够的强度,又要节省材料。
带有导正孔的载体,能校正高速冲压过程中的窜动。
连接处的位置应选择恰当,既要稳定可靠,又要有利于其他工位和最后工位的切断,与载体分离。
11、在满足冲压条件下,尽可能使材料利用率最高。
材料的步距,材料的宽度应取整数。
12、料的成型的基本步骤为:
大成型、冲切、小成型、弯曲、落料。
但这些工序并非一成不便,而是根据不同的产品合理的排列工序。
任何一道工序都不是单独存在,而是相互联系,相互制约。
所以应当根据产品的具体情况合理安排。
12.成型时,应充分的考虑材料的流动量,一般情况下应当保证成型过程中条料不变形或少变形。
所以有时会适当增加工艺切口。
切断相互影响的部位,特别是切断各个产品的相互影响。
13.冲头形状的设计应当考虑凹模的强度,冲头的强度,冲头的固定,冲头的加工等各种因素。
14.弯曲应考虑后道工序的让位,各种弯曲的先后关系,模具的强度,送料是否顺畅。
15.最后一步产品取出的可靠性。
16.当产品的成型简单,成型部分高出主平面不太多是,应考虑采用导板导向,这样材料的利用率会增加。
17.当产品对毛刺有要求是,要考虑毛刺方向和是否采用去毛刺工艺。
18.在排样时,一定要选对主平面,主平面的选取时从各方面考虑,当产品样件时,应充分分析样品,如毛刺方向,工艺接口,产品弯曲擦伤等,从中可以看出别人的成型工艺。
19.对于产品工序排完时,应检验工序是否有遗漏。
五、开发评审项目
1.产品图
1)图纸是否受控
2)公差是否合理
3)电子档与图纸上所有尺寸是否一致
4)是否经过自检和互检
2.展开图
1)展开方法是否正确
2)是否考虑了补偿值
3)是否经过自检和互检
3.排料图或工序图
1)排料图或工序图的工序安排是否合理
2)毛刺方向与产品要求是否一致
3)切口问题是否经客户确认
4)是否经过评审
4.装配图
1)整体体结构是否合理
2)冲床吨位及合模高度是否正