锅炉内胆水温控制系统设计.docx
《锅炉内胆水温控制系统设计.docx》由会员分享,可在线阅读,更多相关《锅炉内胆水温控制系统设计.docx(18页珍藏版)》请在冰豆网上搜索。
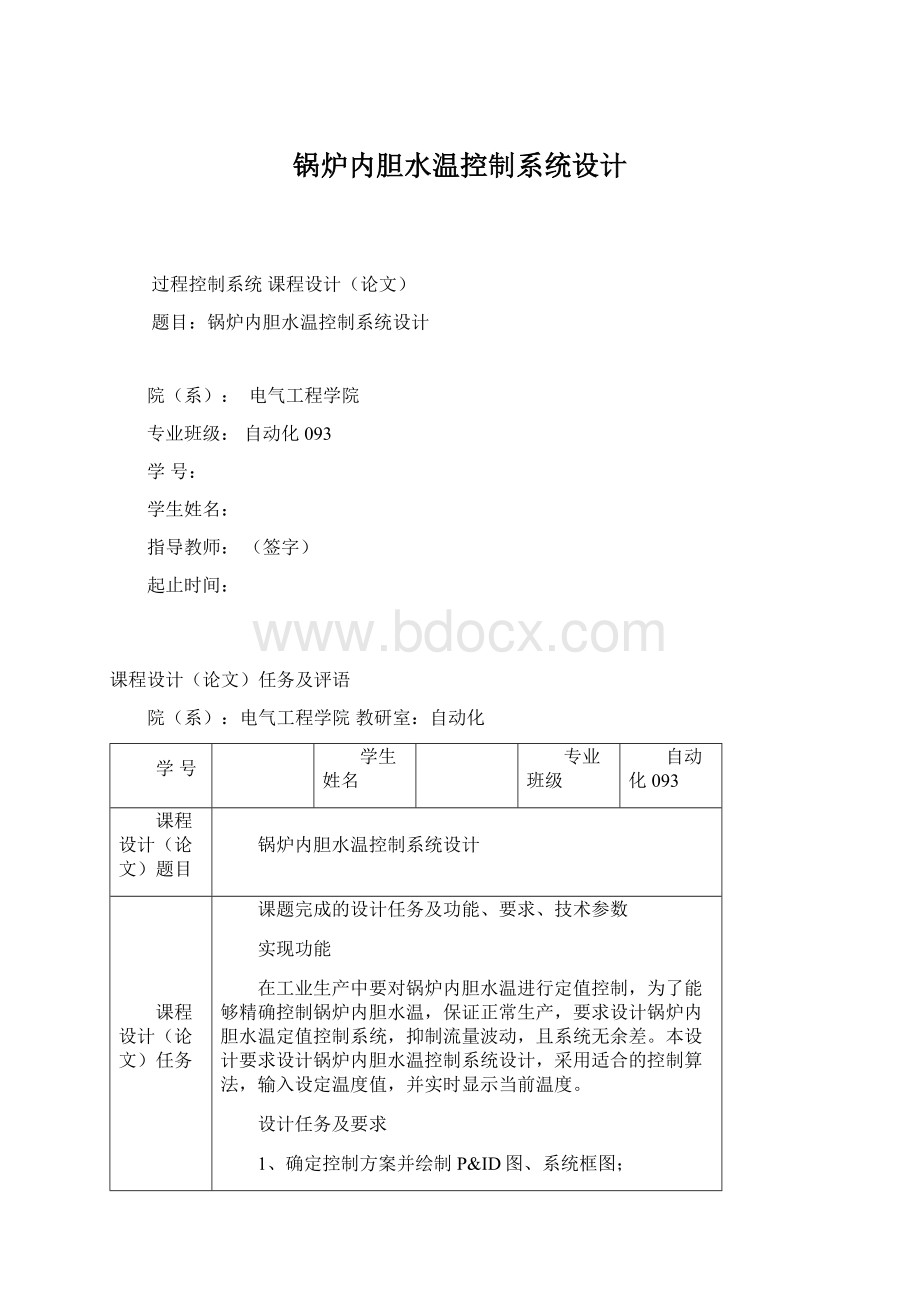
锅炉内胆水温控制系统设计
过程控制系统课程设计(论文)
题目:
锅炉内胆水温控制系统设计
院(系):
电气工程学院
专业班级:
自动化093
学号:
学生姓名:
指导教师:
(签字)
起止时间:
课程设计(论文)任务及评语
院(系):
电气工程学院教研室:
自动化
学号
学生姓名
专业班级
自动化093
课程设计(论文)题目
锅炉内胆水温控制系统设计
课程设计(论文)任务
课题完成的设计任务及功能、要求、技术参数
实现功能
在工业生产中要对锅炉内胆水温进行定值控制,为了能够精确控制锅炉内胆水温,保证正常生产,要求设计锅炉内胆水温定值控制系统,抑制流量波动,且系统无余差。
本设计要求设计锅炉内胆水温控制系统设计,采用适合的控制算法,输入设定温度值,并实时显示当前温度。
设计任务及要求
1、确定控制方案并绘制P&ID图、系统框图;
2、选择传感器、变送器、控制器、执行器,给出具体型号和参数;
3、确定控制器的控制规律以及控制器正反作用方式;
4、若设计由计算机实现的数字控制系统,应给出系统硬件电气连接图及程序流程图;
5、在实验室进行计算机软件仿真,并给出仿真结果;
6、按规定的书写格式,撰写、打印设计说明书一份;设计说明书应在4000字以上。
技术参数
测量范围:
-40~100℃;
控制温度:
70±0.5℃;
最大偏差:
2℃。
进度计划
1、布置任务,查阅资料,理解掌握系统的控制要求。
(2天,分散完成)
2、确定系统的控制方案,绘制P&ID图、系统框图。
(1天,实验室完成)
3、选择传感器、变送器、控制器、执行器,给出具体型号和参数。
(2天,分散完成)
4、确定控制器的控制规律、控制器正反作用方式以及保证系统无余差。
(实验室1天)
5、仿真分析或实验测试、答辩。
(3天,实验室完成)
6、撰写、打印设计说明书(1天,分散完成)
指导教师评语及成绩
平时:
论文质量:
答辩:
总成绩:
指导教师签字:
年月日
注:
成绩:
平时20%论文质量60%答辩20%以百分制计算
摘要
本文以锅炉内胆水温作为被控变量,着重讨论关于锅炉内胆水温的控制方案,使得系统在安全稳定运行的前提下能够更高效率的工作。
系统在工作过程中,由于受到的扰动不同,所需采取的控制方案也不同,需根据扰动的的大小程度和类型来选择控制方案。
锅炉水温具有非线性、时变性、大滞后和不对称性等特点,常规的方法难以达到理想的控制效果。
因此,针对锅炉内胆水温的控制,常用的控制方案有串级控制系统,前馈-反馈控制系统等。
前者有迅速克服进入副回路扰动的能力,而后者能够克服原料流量的波动,各有其特色。
通过选择对比,来达到一定的设计精度和要求。
关键词:
锅炉;水温;控制;精度
目录
第1章绪论…………………………………………………………….1
第2章设计方案……………………………………………………….3
2.1概述.…………..………………………………………………..3
2.2设计方案.……..………………………………………………...3
2.3分析…………..………………………………………………...6
第3章系统设计……………………………………………….……….7
3.1控制器…………………………………………………………..7
3.2变送器……………………………………….………………….8
3.3控制阀…………………………………………………………..9
第4章系统仿真………………….………………………………….10
4.1系统的参数整定………………………………………………..10
4.2整定方法………...……………………………………………..10
第5章总结…………………….…………………………………….14
参考文献…………………….……………………………………….15
第1章绪论
锅炉是将燃料中的可燃元素碳、氢等成分在高温条件下与氧结合发生化学反应,放出热量,进而又将此热量传递给水,使水升温变成热水或蒸汽,供用户使用的一种设备,因此,我们可以把锅炉称之为将燃料的化学能转化为热能的一种设备。
锅炉的发展可追溯到18世纪上半叶,蒸汽机的发明使得对蒸汽的需求量大大增加,这就要求锅炉有一定的的产生蒸汽的能力。
此时,所用的蒸汽压力等于大气压力。
19世纪,常用的蒸汽压力提高到0.8兆帕左右。
与此相适应,最早的蒸汽锅炉是一个盛水的大直径圆筒形立式锅壳,后来改用卧式锅壳,在锅壳下方砖砌炉体中烧火。
随着锅炉越做越大,为了增加受热面积,在锅壳中加装火筒,在火筒前端烧火,烟气从火筒后面出来,通过砖砌的烟道排向烟囱并对锅壳的外部加热,称为火筒锅炉。
1830年左右,在掌握了优质钢管的生产技术之后出现了火管锅炉。
一些火管装在锅壳中,构成锅炉的主要受热面,火(烟气)在管内流过。
在锅壳的存水线以下装上尽量多的火管,称为卧式外燃回火管锅炉。
它的金属耗量较低,但需要很大的砌体。
19世纪中叶,出现了水管锅炉。
锅炉受热面是锅壳外的水管,取代了锅壳本身和锅壳内的火筒、火管。
锅炉的受热面积和蒸汽压力的增加不再受到锅壳直径的限制,有利于提高锅炉蒸发量和蒸汽压力。
这种锅炉中的圆筒形锅壳遂改名为锅筒,或称为汽包。
初期的水管锅炉只用直水管,直水管锅炉的压力和容量都受到限制。
20世纪初期,汽轮机开始发展,它要求配以容量和蒸汽参数较高的锅炉。
直水管锅炉已不能满足要求。
随着制造工艺和水处理技术的发展,出现了弯水管式锅炉。
开始是采用多锅筒式。
随着水冷壁、过热器和省煤器的应用,以及锅筒内部汽、水分离元件的改进,锅筒数目逐渐减少,既节约了金属,又有利于提高锅炉的压力、温度、容量和效率。
第二次世界大战以后,这两种型式的锅炉得到较快发展,因为当时发电机组要求高温高压和大容量。
发展这两种锅炉的目的是缩小或不用锅筒,可以采用小直径管子作受热面,可以比较自由地布置受热面。
随着自动控制和水处理技术的进步,它们渐趋成熟。
在超临界压力时,直流锅炉是唯一可以采用的一种锅炉,70年代最大的单台容量是27兆帕压力配1300兆瓦发电机组。
后来又发展了由辅助循环锅炉和直流锅炉复合而成的复合循环锅炉。
如今,锅炉的发展无论是在安全方面还是工艺效率都达到了前所未有的高度。
绝大多数锅炉采用了单片机、PLC、智能仪表等进行控制。
采用此类的控制方法使得系统运行稳定、反应快、精度高、安全系数高,满足工业的控制要求。
锅炉所产生的热水或蒸汽可以供给用户用以采暖、空调、通风、制冷,也可用以工业加热、烘干、蒸煮、消毒等。
除此之外,锅炉所产生的蒸汽还可用于拖动、发
电等。
锅炉除了可将固体燃料、液体燃料、气体燃料中的化学能转变为热能外,也可直接用电能、核能或废热能使水变成热水或蒸汽以供用户使用。
目前,我国制造和使用的锅炉是量大面广的供热锅炉,因此,对锅炉内胆的水温控制显得极其重要。
当其温度过高时,产生的蒸汽压力会过高,如果不对其进行控制,很可能发生工业事故。
而温度过低时,又不能满足用户或工业要求。
根据目前国家有关标准、规范、规定的限定,供热锅炉一般指额定蒸发量D≤65t/h,额定压力P≤3.9MPa的锅炉,这也是与建筑环境与设备专业密切相关的锅炉,是本专业重点研究和使用的对象。
要顺利完成化学能与热能之间的转换,或者说要顺利地产生用户所需的蒸汽或热水,光有锅炉本体设备还是不够的,还必须配以其他辅助系统,如燃料输送及出灰渣系统,引、送风系统,汽水系统,仪表附件及控制系统。
我国供热锅炉恒久以来不停存在所谓的“大马拉小车”现象,大多数锅炉处于低负荷运转状态,一方面是由于设计院和用户在选用锅炉时,考虑到今后的生长等因素,所选锅炉的容量及台数往往超过现实需求量很多,另一方面,锅炉现实运转中负荷常随用汽、用热负荷变革在较大范围内波动,形成很多锅炉恒久在低负荷下运转。
我国供热锅炉一样平常均匀负荷率在50%~70%,锅炉容量愈小,均匀负荷率愈低,反之则较高。
尽管供热锅炉在节能新技能、新产物应用方面获得了一些成果,但由于缺乏须要的政策支持,总体推行力度不大。
循环流化床锅炉、新型水火管锅炉、渣滓焚烧锅炉、燃生物质锅炉、真空锅炉等新产物都有不同程度的生长。
螺纹烟管技能在锅壳式锅炉上险些得到片面采用,并在其他换热设置装备摆设中得到应用。
燃煤分层安装、锅炉复合相变尾部换热器、锅炉计算机控制体系等产物在现有锅炉改造中也有不同程度的应用,其中燃煤分层安装应用相对广一些。
各地在供热锅炉改造中,还不同程度地采用了变频调速技能对供热锅炉配套的水泵和鼓、引风机进行控制改造。
第2章设计方案
2.1概述
本实验是以锅炉的内胆水温为被控变量,合理的设计方案。
考虑到锅炉的温度是整个锅炉工业控制系统的重要量,所以很好的控制温度意义重大。
控制锅炉内胆水温有多种控制方案,对温度的扰动量有进水流量﹑蒸汽的出口流量﹑蒸汽的压力以及燃料的流量等。
针对于进水的流量可测不可控扰动,可采用温度—流量的串级控制。
此控制方案只能针对单一的流量扰动,对于其他的扰动没有调节作用。
对于燃料流量的控制可采用温度—流量的串级控制。
对于蒸汽出口流量的调节,可采用前馈—串级控制系统。
串级控制系统是在工业中常用的系统,能够迅速克服进入复回路的扰动,使得控制更加精确。
考虑到在工业控制过程中,进水流量﹑燃料的流量及蒸汽的出口流量会对系统的影响较大,因此接下来着重对其进行设计。
2.2设计方案
闭环控制系统是指控制器与被控对象之间既有顺向控制又有反向联系的控制系统。
闭环控制系统优点----不管任何扰动引起被控变量偏离设定值,都会产生控制作用去克服被控变量与设定值的偏差.因此闭环控制系统有较高的控制精度和较好的适应能力,其应用范围非常广泛。
缺点---闭环控制系统的控制作用只有在偏差出现后才产生,当系统的惯性滞后和纯滞后较大时,控制作用对扰动的克服不及时,从而使其控制质量大大降低。
在闭环控制系统中,根据设定值的不同形式,又可分为定值控制系统,随动控制系统和程序控制系统。
主回路的设计:
串级控制系统的主回路是定值控制,其设计单回路控制系统的设计类似,设计过程可以按照简单控制系统设计原则进行。
这里主要解决串级控制系统中两个回路的协调工作问题。
主要包括如何选取副被控参数、确定主、副回路的原则等问题。
副回路的设计:
由于副回路是随动系统,对包含在其中的二次扰动具有很强的抑制能力和自适应能力,二次扰动通过主、副回路的调节对主被控量的影响很小,因此在选择副回路时应尽可能把被控过程中变化剧烈、频繁、幅度大的主要扰动包括在副回路中,此外要尽可能包含较多的扰动。
归纳如下:
(1)在设计中要将主要扰动包括在副回路中。
(2)将更多的扰动包括在副回路中。
(3)副被控过程的滞后不能太大,以保持副回路的快速相应特性。
(4)要将被控对象具有明显非线性或时变特性的一部分归于副对象中。
(5)在需要以流量实现精确跟踪时,可选流量为副被控量。
方案一:
此方案采取温度—流量的串级控制系统,其中主被控变量为锅炉内胆水温,副被控变量为燃料的流量,操纵变量为燃料的流量,扰动量为蒸汽的出口流量、压力等。
此系统的仪表管道图如图2.1,系统结构框图如图2.2。
图2.1温度—流量的串级控制系统仪表管道图
图2.2温度—流量的串级控制系统结构框图
方案二:
此方案采取前馈—串级控制系统,其中主被控变量为锅炉内胆水温,副被控变量为燃料的流量,操纵变量为燃料的流量,扰动量为蒸汽的出口流量、压力等。
此系统的仪表管道图如图2.3,系统结构框图如图2.4。
图2.3前馈—串级控制系统仪表管道图
——
——
图2.4前馈—串级控制系统结构框图
备注:
TC:
温度控制器TT:
温度变送器FT:
流量变送器FC:
流量控制器FY:
运算器TY:
加法器
Gc(s):
控制器传递函数Gv(s):
执行器传递函数Gp(s):
控制对象传递函数
Gm(s):
检测变送环节传递函数GM:
检测变送环节传递函数GF:
扰动传递函数
2.3分析
结合以上两种设计方案仪表管道图和系统的结构框图可知。
方案一:
当扰动进入复回路后,首先,副被控变量检测到扰动的影响,并通过复回路的定值控制作用,及时调节操纵变量,使副被控变量回复到副设定值,也使扰动对主被控变量的影响减少。
即复回路对扰动进行粗调,主环回路对扰动进行细调。
因此,此串级控制系统能够迅速的克服进入副环的扰动,在扰动影响下,主控变量的最大动态偏差明显减小,对燃料流量的波动有很好的调节作用。
方案二:
此系统在方案一的基础上,又增加了以蒸汽流量作为前馈信号的前馈控制系统,前馈控制针对单一的蒸汽流量扰动,对其引起的动、静态偏差有及时矫正的作用。
除此之外,系统还具有串级控制系统的优势。
虽然增加了控制和检测变送器件,使得系统的成本相对于方案一增多,但在控制精度和快速性以及稳定性方面远远要比方案一好,综合起来,最终应选则方案二。
第3章系统设计
3.1控制器
设计过程中,要尽量降低系统的成本,根据现有的资源,控制器可采用辽宁工业大学工业过程控制实验室的“THSA-1型过控综合自动化控制系统实验平台”中的AI智能仪表,如图3.1所示。
此仪表是上海万讯仪表有限公司生产的AI系列全通用人工智能调节仪表,其中,SA-12智能调节仪控制挂件位AI-818型,SA-13智能位式调节仪为AI-708型。
AI-818型仪表为PID控制型,输出为4~20mA电流信号;而AI-708型仪表为位式控制型,输出为继电器触点型开关量信号。
AI仪表常用参数设置:
CtrL:
控制方式。
CtrL=0,采用位式控制;CtrL=1,采用AI人工智能调节∕PID调节;CtrL=2,启动自整定参数功能;CtrL=3,自整定结束。
Sn:
输入规格。
Sn=21,Pt100热电阻输入;Sn=32,0.2~1V电压输入;Sn=33,1~5V电压输入。
DIL:
输入下限显示值,一般DIL=0.
DIH:
输入上限显示值。
输入为液位信号是,DIH=50;输入为热电阻信号时,DIH=100;输入为流量信号时,DIH=100.
CF:
系统功能选择。
CF=0为内部给定,反作用调节;CF=1为内部给定,正作用调节
Addr:
通讯地址。
单回路实验Addr=1;串级实验主控为Addr=1,副控为Addr=2;
P、I、D参数可根据实验要求调整
主副控制器的控制规律
在串级控制系统中,主、副调节器所起的作用是不同的。
主调节器起定值控制作用,它的控制任务是使主参数等于给定值(无余差),故一般宜采用PI或PID调节器。
由于副回路是一个随动系统,它的输出要求能快速、准确地复现主调节器输出信号的变化规律,对副参数的动态性能和余差无特殊的要求,因而副调节器可采用P或PI调节器
图3.1AI智能仪表
3.2变送器
进水流量变送器:
用来检测流入锅炉的水的流量,可根据检测到的流量输出4至20毫安的电流信号。
图3.2.1供应LDE-25316L电极,内衬PTFE,一体式智能电磁流量计图片
采用“供应LDE-25316L电极,内衬PTFE,一体式智能电磁流量计”,首先最突出的一点是价格便宜,大约十几元钱左右。
其次,一体式电磁流量计结构简单,无转动部件,因而无摩擦,工作寿命长,计量精度高,性能可靠。
并且无机械惯性、反应灵敏、可测量瞬时脉动流量,也可与单元组合仪表、计算机配套组成各种自动检测、调节系统和程控系统。
输出方式:
4~20mA
蒸汽流量变送器:
用来检测蒸汽的流量,可根据检测的流量输出4至20毫安的电流信号。
图3.2.2LZB/ZS-15法兰流量计蒸汽流量计管道流量计内牙流量计图片
采用“LZB/ZS-15法兰流量计蒸汽流量计管道流量计内牙流量计”它无可动部件,准确度高测量快速,重复性好0.03~0.06%; 压损小仅孔板的1/2ΔP左右;无零漂;精度等级:
±0.5%、±1.0%、±1.5%测量范围宽:
1:
30倍;1:
10倍; 工况下:
饱和蒸汽、过热蒸汽都适用。
输出方式:
4~20mA,如图3.2.2所示。
3.3控制阀
因为燃料均为易燃物品,考虑到系统的安全准则,进口燃料阀门选择气开阀。
气开阀没外部信号输入时关闭,当输入到执行机构的信号增加时,流过控制阀的流量增加。
GEEVALVE阀门VA7010电动二通阀图片
采用GEEVALVE阀门VA7010电动二通阀,阀体黄铜锻造,不锈钢杆及弹簧,体积小,耐腐蚀。
阀芯结构优化,在不减少Kv值的情况下,允许压差大。
流量特性:
线性流量特性,满足dq=Kv2dl,增益Kv2是常数,与可调比R和最大流量Qmax有关,与流过控制阀的流量Q无关。
第4章系统仿真与分析
4.1系统的参数整定
串级控制系统中主副两个回路是彼此互相影响的,副控制器的整定对主控制器的影响一目了然,因为副回路的特性本身就是主回路广义对象的一个组成部分。
由于主控制器的输出本身就是副回路的设定值,所以对副回路的响应有影响。
如果主回路的工作频率相差很大,例如十倍以上,则对副回路而言在它的控制过程中可以近似认为主回路还没有来的及反应,可以忽略主回路对副回路的影响,则控制器的参数整定可以按由内而外的原则,分别独立按单回路系统控制器的参数整定方法整定。
4.2整定方法
逐次逼近法
这是一种主副回路反复调试以逐步接近最优的方法,其过程有以下4个步骤:
主回路开环,按单回路方法,整定副控制器。
主回路闭环,在已经整定的副控制器下整定主控制器。
在主回路闭环的条件下,重新整定副控制器的参数。
在副控制器的基础上,再重新整定主控制器。
按照逐次逼近法,先主回路开环,按单回路方法整定副控制器,建立的Simulink模型如图4.1所示。
图4.1系统开环Simulink模型
不断试验,当kc2=45时,副回路阶跃响应如图4.2所示。
图4.2副回路阶跃响应曲线
由图可以看出,调节时间大约为1秒,超调量为10%,基本符合要求,因此可以进入主控制器的参数整定。
即主回路闭环,此时的Simulink模型如图4.3所示。
图4.3系统闭环Simulink模型
不断试验,调节主控制器,当Kc1=18时,主回路的阶跃响应如图4.4所示,由图可知,此时Ts1=5s,调节时间过长,因此在主回路闭环条件下重新整定副控制器的参数,根据衰减曲线法,取Kc1=15,Kc2=30,此时系统主回路阶跃响应曲线如图4.5所示。
图4.4主回路的阶跃响应曲线
图4.5系统的阶跃响应
由图可知,系统的阶跃响应效果不是很理想,超调量太大,需要精调。
反复试验,最终得到的阶跃响应曲线如图4.6。
图4.6系统最终的的阶跃响应曲线
由曲线可知,超调量变短,调节时间基本符合要求。
此时主副控制器的PID参数如下:
主控制器:
P:
13I:
5D:
6
副控制器:
P:
40I:
6D:
5
第5章总结
本设计完成了题目要求的基本部分的全部要求。
由于时间的短缺而没有更好地完善,在今后条件允许的情况下再扩展。
基本部分各单元工作稳定。
通过这次设计使我学会如何去培养我们的创新精神,从而不断地战胜自己,超越自己。
创新,是要我们学会将理论很好地联系实际,并不断地去开动自己的大脑,从为人类造福的意愿出发,做自己力所能及的,别人却没想到的事。
使之不断地战胜别人,超越前人。
同时,更重要的是,我在这一设计过程中,学会了坚持不懈,不轻言放弃,设计过程,也好比是我们人类成长的历程,常有一些不如意,也许这就是在对我们提出了挑战,勇敢过,也战胜了,胜利的钟声也就一定会为我们而敲响。
通过合作,我们的合作意识得到加强。
合作能力得到提高。
上大学后,很多同学都没有过深入的交流,在设计的过程中,我们用了分工与合作的方式,每个人互责一定的部分,同时在一定的阶段共同讨论,以解决分工中个人不能解决的问题,在交流中大家积极发言,和提出意见,同时我们还向别的同学请教。
在此过程中,每个人都想自己的方案得到实现,积极向同学说明自己的想法。
能过比较选出最好的方案。
在这过程也提高了我们的表达能力。
在设计的过程中我们还得到了老师的帮助与意见。
在学习的过程中,不是每一个问题都能自己解决,向老师请教或向同学讨论是一个很好的方法,不是有句话叫做思而不学者殆。
做事要学思结合。
总之一周的课设,让我觉得很累,但从中收获了很多,最终的成功让我觉得累也是值得的。
在此,感谢同学们的帮助以及老师在此次实验中的指导。
参考文献
[1]何衍庆,黎冰,黄海燕.工业生产过程控制.第二版.北京:
化学工业出版社,2009.8
[2]吴中俊,黄永红.可编程控制器原理及应用[M].北京:
机械工业出版社,2004
[3]邓则名,程良伦.电器与可编程控制器应用技术[M].北京:
机械工业出版社,1997.1
[4]林小峰.可编程序控制器及应用.北京:
高等教育出社[M],1991
[5]方承远.工厂电气控制技术.第二版.北京:
北京机械工业出版社[M],2000
[6]汪道辉.逻辑与可编程控制系统.北京:
机械工业出版[M],2001