产品质量考核办法修改稿.docx
《产品质量考核办法修改稿.docx》由会员分享,可在线阅读,更多相关《产品质量考核办法修改稿.docx(14页珍藏版)》请在冰豆网上搜索。
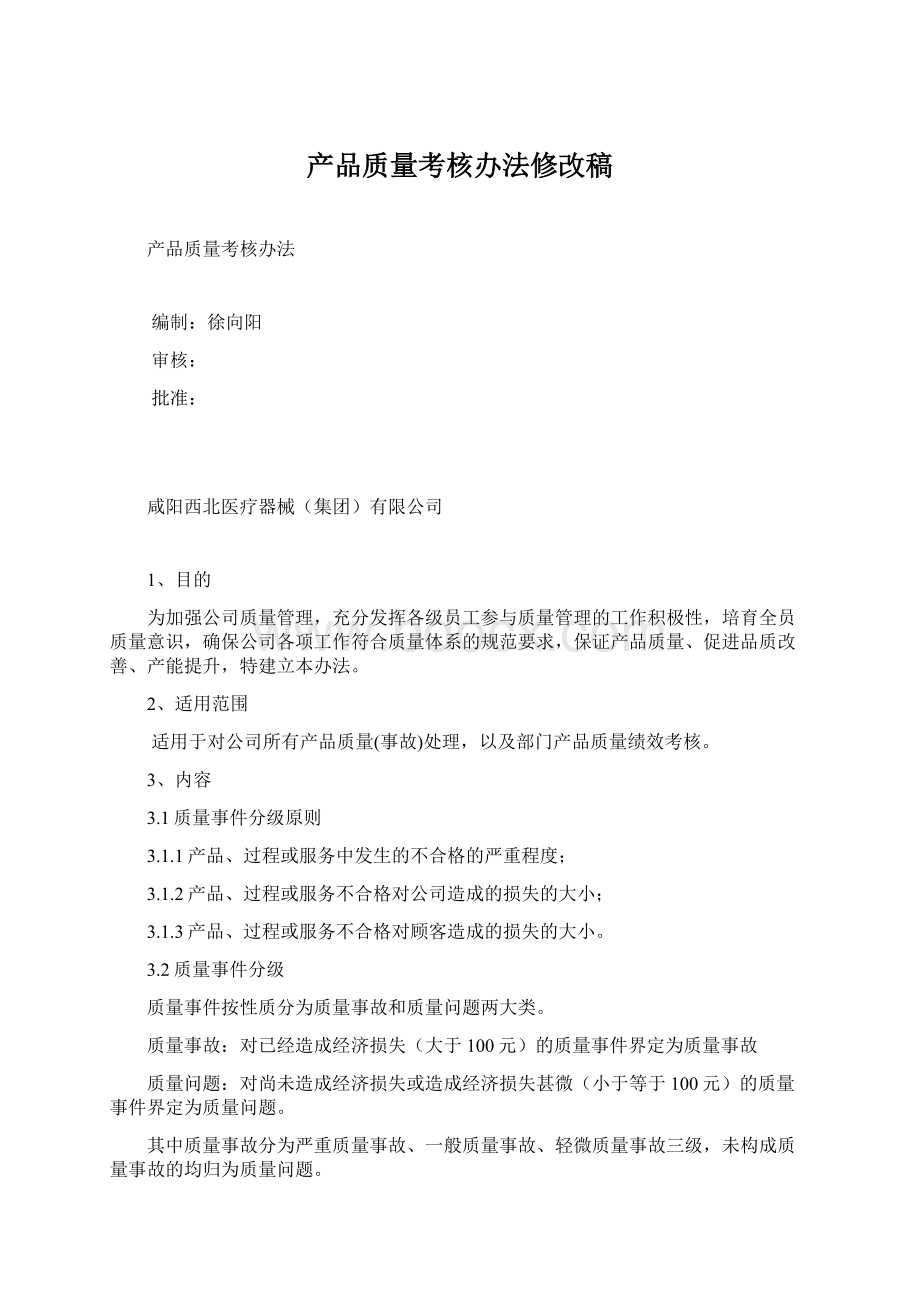
产品质量考核办法修改稿
产品质量考核办法
编制:
徐向阳
审核:
批准:
咸阳西北医疗器械(集团)有限公司
1、目的
为加强公司质量管理,充分发挥各级员工参与质量管理的工作积极性,培育全员质量意识,确保公司各项工作符合质量体系的规范要求,保证产品质量、促进品质改善、产能提升,特建立本办法。
2、适用范围
适用于对公司所有产品质量(事故)处理,以及部门产品质量绩效考核。
3、内容
3.1质量事件分级原则
3.1.1产品、过程或服务中发生的不合格的严重程度;
3.1.2产品、过程或服务不合格对公司造成的损失的大小;
3.1.3产品、过程或服务不合格对顾客造成的损失的大小。
3.2质量事件分级
质量事件按性质分为质量事故和质量问题两大类。
质量事故:
对已经造成经济损失(大于100元)的质量事件界定为质量事故
质量问题:
对尚未造成经济损失或造成经济损失甚微(小于等于100元)的质量事件界定为质量问题。
其中质量事故分为严重质量事故、一般质量事故、轻微质量事故三级,未构成质量事故的均归为质量问题。
3.2.1严重质量事故
经核实已造成批量不合格品(数量在200件以上的或价值超过3000元以上的),废品(数量在200件以上的或价值超过3000元以上的)
经核实已造成产品返工的;经核实已造成直接损失3000元以上;
经核实因质量异常造成重要客户投诉、客户索赔、退货的事件且经济损失3000元以上;
造成市场恶劣影响,公司品牌、形象、名誉受到破坏等等事件;
3.2.2一般质量事故
经核实已造成批量不合格品(数量在50~200件范围的)或废品的(数量在50~200件范围的或价值在500~3000元范围的);
经核实已造成产品返工的;经核实已造成直接损失500—3000元的;
经核实因质量异常造成客户投诉事件且经济损失在1000—3000元范围的;
造成市场影响,公司品牌、形象、名誉受到一般程度的影响的事件;
3.2.3轻微质量事故
经核实已造成批量不合格品(数量在50件以下的或价值在500元以下的)或废品(数量在50件以下的或价值在500元以下的);
经核实已造成产品返工的(数量在50件以下的或价值在500元以下的);
经核实因质量异常造成客户投诉的事件且经济损失在100—1000元范围的;
造成较小市场影响,公司品牌、形象、名誉受到轻微程度(潜在)的影响的事件;
3.2.4质量问题
造成的损失尚未构成质量事故;
核实存在质量不合格,但对产品适用性和顾客健康不会造成明显影响的;
阻碍或不利于企业质量管理工作的;
没有按照ISO9001质量体系文件相关规定执行的行为;
质量事件分类
不合格/废品数量(件)
不合格/废品价值(元)
返工损失(元)
客诉损失(元)
市场影响
质量问题
-
-
<100
<100
无
质量事故
轻微质量事故
<50
<500
<500
100~1000
轻微
一般质量事故
50~200
500~3000
500~3000
1000~3000
一般
严重质量事故
>200
>3000
>3000
>3000
恶劣
3.3、质量责任人
3.3.1直接责任人:
指因自己失职而直接导致事故的当事人;
3.3.2连带责任人:
指事故非由自身直接造成,但对事故的发生或扩大负有连带责任的人;
3.3.3分管责任人:
指班组长和检验员;
3.3.4主管责任人:
指各车间、部门主管。
以上责任人分类包括了一般情况下所有责任人范围,但在某具体质量事件中可能只有或只追究其中部分责任人责任,同时,直接责任人可能会是分管或主管责任人,视具体情况而定。
3.4、质量责任追究原则
3.4.1后一道工序过错或疏忽导致质量事故(含质量问题)且事故与前一道工序无关,则责任由后一道工序承担;
3.4.2若前一道工序造成事故(含质量问题)但未发觉,后一道工序及时发觉并采取措施避免了事故进一步扩大,则前道工序负全责,后一道工序不承担责任并可视情况给予嘉奖(属本岗位应尽职责的除外);
3.4.3若前一道工序造成事故(含质量问题)但未发觉,后一道工序未发觉而造成事故进一步扩大,直到其它工序发觉为止,则从事故发生工序直至事故发觉工序前的所有工序均要承担相应责任(后一道工序承担主要责任)。
3.5质量处罚内容
序号
事故
分级
责任人
处罚
经济处罚
行政处罚
1
严重质量事故
直接责任人
罚金损失金额×45%
辞退/记大过
2
连带责任人
罚金损失金额×15%
记大过/记过/警告
3
分管责任人
罚金200元
记过/警告
4
主管责任人
罚金200元
公司通报批评
5
一般质量事故
直接责任人
罚金200元
记过/警告
6
连带责任人
罚金50元
公司通报批评
7
分管责任人
罚金50元
记过/警告
8
主管责任人
罚金50元
公司通报批评
9
轻微质量事故
直接责任人
罚金100元
公司通报批评
10
连带责任人
罚金50元
内部通报批评
11
分管责任人
罚金50元
内部通报批评
12
质量问题
直接责任人
公司通报批评
13
连带责任人
内部通报批评
14
分管责任人
内部通报批评
备注
1)公司质量问题和轻微、一般质量事故由质管部进行评判,严重质量事故由相关部门进行讨论决定。
本表仅按事故严重程度确定了各类事件处罚范围,则按质量事故处罚条款实施处罚;
2)具体质量事故或质量问题中可视情况只追究直接责任人责任;
3)若属于顾客投诉引起的,处罚时可超过本表规定处罚范围。
3.6质量奖励内容
序
号
奖励事项
相关人员
奖励内容
备注
1
避免严重质量事故发生
当事人
嘉奖/奖金200元以上
详见本表说明
2
避免一般质量事故发生
当事人
通报表扬/奖金200元以下
3
班组质量考核(月度)
第一名
通报表扬/奖金50元
由部门主管提报、质管科审核核实,总经理批准
4
(全年/半年)无投诉及严重或一般质量事故的班组
车间(班组)
1000~2000元
由部门主管提报、质管科审核核实,总经理批准后实施。
5
(全年)无严重及一般质量事故
车间、科室主管
500元
总经理批准
6
其它应予以奖励的质量行为
当事人
100~500元
总经理批准
说明
1.各级事故指尚未发生但若未经当事人发现则必然发生的;或是事故已在厂内造成但产品尚未出厂被发现而避免了出厂的产品质量隐患或不合格;
2.当事人所避免的事故须是与本岗位或工序职责无直接责任的,即非自身工作失职造成;
3.经公司质管部组织部门核实认可的;
说明
1.以上均是指对尚未构成质量事故的质量问题进行处罚,一旦构成质量事故则按第六条相关内容处罚;
2.少量产品质量问题由生产人员负责,品管员及带班主任只对1件以上产品质量问题负责(严重卫生问题如产品中蝇虫等除外);
3.质量问题由品管员在厂内部发现的则品管员不受处罚,上表所列对品管员进行的处罚是指在内部由其他部门人员发现或外部顾客投诉反馈的并达到上一条款数量要求的质量问题;
4.品管员及现场主任,生产、质量部经理隐瞒不报的,一经发现按直接责任人处理;
5.若包装组内无严格分工,责任不能具体落实到某人或某岗位时,则全体成员共同承担。
3.7质量奖惩实施程序
3.7.1人员职责:
质量问题、轻微质量事故相关人员质量奖惩由检验员提报、质管部经理批准;
一般及严重质量事故相关人员质量奖惩由质管部经理提报、总经理批准。
3.7.2考核形式:
个人质量奖惩记录作为年终个人绩效考核和各类先进评定的依据之一;
以现金形式考核的直接计入当月部门和个人工资。
3.7.3提报方式:
以月度报表方式,报管理者代表审核,送总经办,报总经理批准后,财务部实施。
3.7.4提报时间:
本月度报表在次月10日前,报批完毕。
3.8部门产品质量考核量化指标
质量考核以分值来计算,基础分为100分。
100分不奖不罚,以总得分超出或减少的分值计算,每分核算按100元计算;如110分奖励1000元、85分处罚1500元。
部门所得分值作为部门质量绩效考核的核算依据,按月度进行统计核算;并且部门所得分值还可以作为生产系统个人(班组长以上人员)绩效考核的依据。
3.8.1生产系统:
总装车间、零件车间、供应科、手机事业部、电子工段、设备动力科
总装车间:
1、成品一次交验合格率89%(治疗机与牙科椅加权平均数)
优秀>92%——加5~10分
92%≥超标≥89.9%——加1~4分
89.8%≥达标≥89%——0分
86%≤未达标<89%——减1~4分
严重不达标<86%——减5~10分
2、零件一次交验合格率99.1%(批次不合格≤2批)
优秀>99.8%——加3~6分
99.8%≥超标≥99.2%——加1~2分
99.1%≥达标≥98%——0分
97%≤未达标<98%——减1~4分
严重不达标<97%——减5~10分
3、质量事故≤3起
0质量事故——加(年度奖励)
1≤质量事故≤2——零分
5≥质量事故>2——减1~4分
质量事故>5——减5分
零件车间:
4、零件一次交验合格率99.1%(批次不合格≤5批)
优秀>99.8%——加3~6分
99.8%≥超标≥99.2%——加1~2分
99.1%≥达标≥98%——0分
97%≤未达标<98%——减1~4分
严重不达标<97%——减5~10分
5、质量事故≤3起
0质量事故——加1~5分(年度奖励)
1≤质量事故≤3——0分
5≥质量事故>3——减1~2分
10≥质量事故>5——减3~4分
质量事故>10——减5~8分
供应科:
6、采购物资交验合格率98%(含批量不合格退货)
优秀>99.7%——加3~6分
99.7%≥超标≥99.1%——加1~2分
99%≥达标≥98%——0分
97≤未达标<98%——减1~3分
严重不达标<97%——减4~8分
7、质量事故≤3起
0质量事故——加(年度奖励)
1≤质量事故≤2——零分
5≥质量事故>2——减1~4分
质量事故>5——减5分
8、采购物资占成品一次交验合格率中,不合格比率不超过40%
优秀<25%——加4~10分
35%≥超标≥25%——加1~3分
40%≥达标≥35%——0分
60%≥未达标>40%——减1~3分
严重不达标>60%——减4~6分
或:
采购物资漏报检≤2次(含报检不及时,外协现场检验)
优秀=0——加2分
2≥达标≥1——0分
4≥未达标≥3——减3~5分
严重不达标>5——减6分
手机事业部:
9、成品一次交验合格率95.6%
优秀>99.6%——加4~10分
99.6%≥超标≥99%——加1~3分
98.9%≥达标≥95.6%——0分
95%≤未达标<95.6%——减1~5分
严重不达标<95%——减6~15分
10、零件一次交验合格率99.1%(批次不合格≤3批)
优秀>99.9%——加3~6分
99.9%≥超标≥99.2%——加1~2分
99.1%≥达标≥98%——0分
97%≤未达标<98%——减1~4分
严重不达标<97%——减5~10分
11、质量事故≤3起
0质量事故——加(年度奖励)
1≤质量事故≤2——零分
5≥质量事故>2——减1~4分
质量事故>5——减5~8分
电子工段:
12、成品一次交验合格率89%
优秀>92%——加4~10分
92%≥超标≥89.9%——加1~3分
89.8%≥达标≥89%——0分
87%≤未达标<89%——减1~5分
严重不达标<87%——减6~10分
13、质量事故≤2起
0质量事故——加(年度奖励)
1≤质量事故≤2——零分
5≥质量事故>2——减1~4分
质量事故>5——减5分
设备动力科:
14、零件一次交验合格率98%
优秀>99.8%——加3~6分
99.8%≥超标≥99.2%——加1~2分
99.1%≥达标≥98%——0分
97%≤未达标<98%——减1~4分
严重不达标<97%——减5~10分
15、质量事故≤3起
0质量事故——加(年度奖励)
1≤质量事故≤2——零分
5≥质量事故>2——减1~4分
质量事故>5——减5分
3.8.2非生产系统:
技术部、质管科、售后服务部
技术部:
16、工艺、技术图纸差错≤5例(试制、工艺改进、小批量试制除外)
优秀=0例——加3~6分
2例≥超标≥1例——加1~2分
5例≥达标≥3例——0分
6例≤未达标≤8例——减1~5分
严重不达标≥9例——减6~8分
17、质量事故(设计问题)≤2起
0质量事故(设计问题)——加(年度奖励)
1≤质量事故(设计问题)≤2——零分
5≥质量事故(设计问题)≥3——减1~6分
质量事故(设计问题)>5——减7~8分
质管部:
18、错漏检率≤5例
优秀=0例——加5分
2例≥超标≥1例——加1~2分
5例≥达标≥3例——0分
6例≤未达标≤7例——减1~3分
严重不达标≥8例——减4~8分
19、质量事故(错检)≤3起
0质量事故(错检)——加2分(年度奖励)
1≤质量事故(错检)≤3——零分
5≥质量事故(错检)>4——减1~5分
质量事故(错检)>5——减6~8分
售后服务部:
20、质量事故(客户服务投诉)≤2起
0质量事故(客户服务投诉)——加(年度奖励)
1≤质量事故(客户服务投诉)≤2——零分
5≥质量事故(客户服务投诉)>2——减1~5分
质量事故(客户服务投诉)>5——减6~8分
3.8.3质管科负责对所列项目进行统计,各个部门配合提供相关数据,报表经过每个部门负责人确认后,管理者代表审核、报总经办、总经理批准。
本制度从签发批准之日起执行。
质管部
2011-8-20
部门
考核指标
生产系统
成品一次交验合格率89%
零件一次交验合格率98%
质量事故<3起
标准值
≥92%
≥89%
<89%
≥99.6%
≥98%
<98%
0
1~2
≥3
加分
零分
减分
加分
零分
减分
加分
零分
减分
总装车间
>89.9%
89.9%≥
<89%
≥99.6%
99.1%≥
<98%
0
1~2
≥3
加1~10分
零分
减1~10分
加1~6分
零分
减1~10分
加(年度奖励)
零分
减1~5分
零件车间
/
/
/
≥99.2%
99.1%≥
<98%
0
1~2
≥3
/
/
/
加1~6分
零分
减1~10分
加1~5分
零分
减1~8分
供应科
采购物资漏报检≤2次
采购物资交验合格率98%
0
1~2
≥3
0
1~2
≥3
≥99.1%
99%≥
<98%
加2分
零分
减3~6分
加1~6分
零分
减1~8分
加(年度奖励)
零分
减1~5分
手机事业部
>98.9%
98.9%≥达标≥95.6%
<95.6%
≥99.6%
99.1%≥
<98%
0
1~2
≥3
加1~10分
零分
减1~10分
加1~6分
零分
减1~10分
加(年度奖励)
零分
减1~8分
电子工段
>89.9%
89.9%≥
<89%
≥99.6%
99.1%≥
<98%
0
1~2
≥3
加1~10分
零分
减1~10分
加1~6分
零分
减1~10分
加(年度奖励)
零分
减1~5分
设备动力科
/
/
/
≥99.6%
99.1%≥
<98%
0
1~2
≥3
/
/
/
加1~6分
零分
减1~10分
加(年度奖励)
零分
减1~5分
部门
考核指标
非生产系统
部门考核项目
质量事故
技术部
工艺、技术图纸差错≤5例
质量事故≤2起
2例≥超标
5例≥达标≥3例
未达标≥6例
0
1~2
≥3
加1~6分
零分
减1~8分
加(年度奖励)
零分
减1~8分
质管部
错漏检率≤5例
质量事故(错检)≤3起
2例≥超标
5例≥达标≥3例
未达标≥6例
0
1~3
≥4
加1~5分
零分
减1~8分
加2分
零分
减1~8分
售后服务部
/
质量事故(客户服务投诉)≤1起
/
/
/
0
1~2
≥1
/
/
/
加(年度奖励)
零分
减1~8分