偏心齿轮传动的快速优化设计要点.docx
《偏心齿轮传动的快速优化设计要点.docx》由会员分享,可在线阅读,更多相关《偏心齿轮传动的快速优化设计要点.docx(9页珍藏版)》请在冰豆网上搜索。
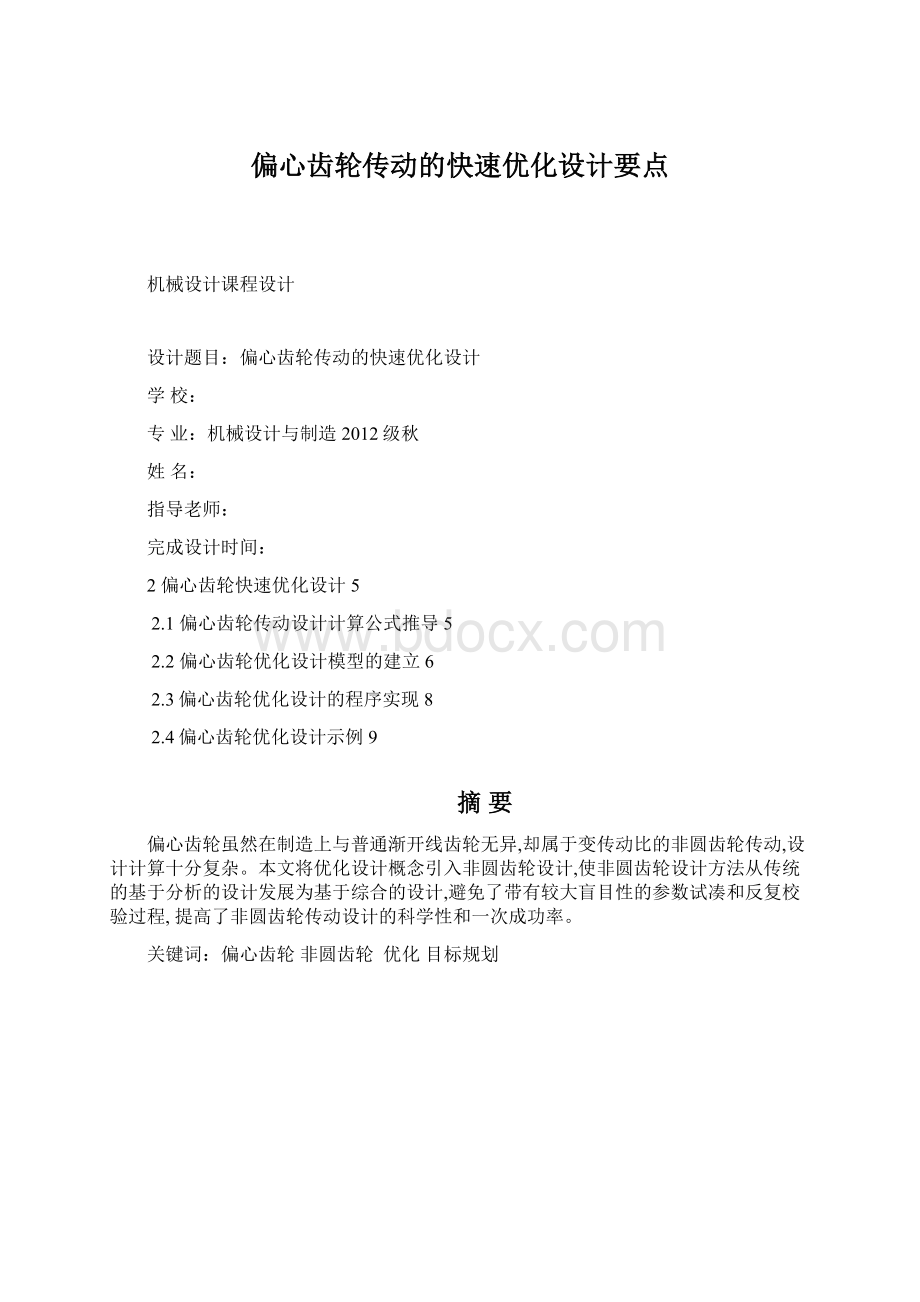
偏心齿轮传动的快速优化设计要点
机械设计课程设计
设计题目:
偏心齿轮传动的快速优化设计
学校:
专业:
机械设计与制造2012级秋
姓名:
指导老师:
完成设计时间:
2偏心齿轮快速优化设计5
2.1偏心齿轮传动设计计算公式推导5
2.2偏心齿轮优化设计模型的建立6
2.3偏心齿轮优化设计的程序实现8
2.4偏心齿轮优化设计示例9
摘要
偏心齿轮虽然在制造上与普通渐开线齿轮无异,却属于变传动比的非圆齿轮传动,设计计算十分复杂。
本文将优化设计概念引入非圆齿轮设计,使非圆齿轮设计方法从传统的基于分析的设计发展为基于综合的设计,避免了带有较大盲目性的参数试凑和反复校验过程,提高了非圆齿轮传动设计的科学性和一次成功率。
关键词:
偏心齿轮非圆齿轮优化目标规划
绪论
齿轮机构是应用最为广泛的机械传动机构,具有传递功率大、效率高、传动准确可靠、寿命长、结构紧凑等优点。
通常所说的齿轮传动是指传动比为常数的齿轮传动,其主要功能是传递匀速运动和恒定的动力(功率),而非圆齿轮则更多地作为运动控制元件使用,广泛应用于轻工、纺织、烟草、食品等机械中[1~5],在机构创新设计中具有重要作用。
非圆齿轮传动20世纪30年代就已出现,20世纪50年代原苏联学者李特文在文献[1]中首次建立了非圆齿轮传动的系统理论,20世纪70年代起这项技术被介绍到国内,并开始进行系统研究,但至今应用有限,甚至在我国机械专业的本科生教材中都未包含这部分内容。
其重要原因在于,非圆齿轮设计计算复杂,制造也很困难。
进入20世纪70年代以后,由于计算机技术和数控技术的发展和广泛应用,使制约非圆齿轮应用的两大难点都有了得以克服的可能,因而掀起了新的一轮非圆齿轮研究及应用热潮,国外甚至有人将其称为非圆齿轮的“再发明(Rediscovering)”,不仅开展非圆齿轮传动的研究,而且开展了非圆带、链传动的研究,形成一个内容丰富的非匀速比传动研究领域[4]。
由于齿轮数控技术的发展,非圆齿轮的制造已不再困难,但是,非圆齿轮设计计算复杂这一难点尚未得到根本克服,具体表现在以下两点。
1)现有文献中给出的某些计算公式作为分析计算工具无疑是正确的,但是如果将其用于设计计算,则缺乏可操作性,例如,文献[4]中给出的偏心齿轮计算公式以瞬时啮合角作为基本变量,要求计算时首先设定α值,其“缺点是α角的设定范围不易掌握,而且几何中心距的变化情况、特别是它的最小值lmin不能直接求出”。
[4]
2)现有文献中给出的设计方法(包括计算机辅助设计方法)均属于基于分析的设计方法,即,给定一组参数,得到分析计算(校核计算)结果,如发现不妥,则修改给定参数,再作分析与校核,具有较大的盲目性。
本文将优化设计概念引入非圆齿轮设计,使非圆齿轮设计方法从传统的基于分析的设计发展为基于综合的设计,避免了带有较大盲目性的参数试凑和反复校验过程,提高了非圆齿轮传动设计的科学性和一次成功率,力求从根本上扭转由于非圆齿轮设计计算复杂困难而限制其广泛应用的局面。
第1章偏心齿轮简介化原理
非圆齿轮种类繁多,包括内、外啮合的直齿、斜齿偏心齿轮、椭圆齿轮,变性椭圆齿轮,以及多圈非圆齿轮等非封闭形非圆齿轮。
其中偏心齿轮是指一对普通渐开线直齿圆柱齿轮,但其回转中心与几何中心不重合,形成一偏心距,从而实现变速比传动,具有制造上与普通渐开线齿轮无异、可在一定范围内代替制造复杂的其它非圆齿轮的诱人特点。
吴序堂、王贵海于20世纪90年代出版的《非圆齿轮与特种齿轮传动设计》一书中[4]首先系统地提出偏心齿轮的设计方法(注:
在文献[1]、[2]中也曾提到偏心圆齿轮,但那是指瞬心线为偏心圆的齿轮,而不是文献[4]5~7节中所说的回转中心与几何中心不重合的普通渐开线圆柱齿轮,后者可以同一般齿轮一样加工,却能获得非圆齿轮的传动效果),并首次提出非圆齿轮的CAD/CAM。
虽然偏心齿轮在制造时与普通渐开线齿轮没有什么区别,但在设计时却与定传动比齿轮传动迥然不同,这是因为非圆齿轮传动中很多参数是瞬时变化的,例如,文献[1]中指出“非圆齿轮机构中的压力角,不仅数值可以改变,而且正负号也可以改变”。
为了避免自锁,对压力角的最大值应加以限制,文献[4]则进一步提出不应超过65°;又如,文献[3]、[4]均指出非圆齿轮“啮合过程中的重合度也是变化的”;文献[4]则指出,偏心齿轮的“几何中心距是变化的,......因而传动过程中,齿轮齿廓的侧隙和顶隙也是变化的”,当几何中心距小到一定程度时,会因轮齿“相互干涉(产生负间隙)而影响传动”,相反,当几何中心距大到一定程度时,也会使轮齿脱离啮合造成连续传动中断;此外,为了保证非圆齿轮的加工,文献[1]、[4]均提出控制根切的问题。
由于上述这些众多影响因素的存在,使得非圆齿轮的传动设计十分复杂,而且随着齿轮副几何参数的不同,影响传动质量的问题发生在啮合过程的不同位置;排除了这一因素的影响,又可能在另一因素上发生问题。
如果采用传统的基于分析的设计方法进行设计,则势必要反复进行校核验算,而非圆齿轮的计算又涉及大量代数方程式、甚至微分方程式的解算,计算工作量浩大,人工计算实在难以胜任,设计周期必然冗长,设计质量还不能得到保证。
第2章偏心齿轮快速优化设计
本文根据啮合基本定理(Willis定理),推导建立偏心齿轮传动的设计计算公式,深入研究偏心齿轮设计中必须考虑的影响因素和约束条件,在此基础上引入优化设计的概念,建立偏心齿轮优化设计模型,并编制了相应的软件工具,以利于工程技术人员方便使用。
2.1偏心齿轮传动设计计算公式推导
啮合基本定理(Willis定理)确定了按给定传动比变化规律传递平行轴之间回转运动的一对齿廓共轭的几何条件,瞬时啮合节点位于连心线上,并且把中心距分成与瞬时角速比成反比的两段线段。
这一定理不论对定传动比的平面啮合,还是对变传动比的平面啮合都是正确的[1]。
基于这一定理推导建立非圆齿轮传动的设计计算公式,理论依据更加明确,适用范围更宽,实践证明其表达形式也更加简洁明快[6][7][9]。
有关偏心齿轮设计计算公式的推导过程,在参考文献[6][7]两篇论文中给出,这里仅列出推导结果。
图1偏心齿轮传动示意图
2)啮合线斜率
k=[(x2-x1)(y1-y2)+(rb1+rb2)x(x2-x1)2+(y1-y2)2-(rb1+rb2)2]/
[(x2-x1)2-(rb1+rb2)2]
式中rbi——基圆半径
3)瞬时压力角
α1=arctan(-k)
4)基圆与啮合线切点坐标
5)瞬时传动比
经数值积分可求得φ2随φ1变化的规律。
6)重叠系数
7)几何中心距
2.2偏心齿轮优化设计模型的建立
非圆齿轮的设计过程可表述为,在给定传动比变化规律的前提下,选取一组几何参数,在保证轮齿正确啮合、连续传动的约束下,尽可能逼近给定的传动比变化规律,其本质是一个优化问题。
目标函数——尽可能逼近给定的传动比变化规律;
约束函数——瞬时压力角、重合度、几何中心距等均控制在一定的范围内;
设计变量——齿轮的几何参数(如齿数、模数、变位系数、刀具压力角、安装中心距、偏心率、变性椭圆齿轮的阶数、长半轴、轮齿分布等)
引入优化设计概念进行非圆齿轮的设计,是一种基于综合的设计方法,无须反复试凑参数和进行校验修正。
对于偏心齿轮传动设计,可以建立以下优化设计模型
min实际传动比变化规律与给定传动比变化规律之差的绝对值
s.t.瞬时压力角≤上限值
重合度≥1
下限值≤几何中心距≤上限值
............
设计变量为:
模数,齿数,变位系数,偏心距,刀具压力角,安装中心距等
其中,目标函数“实际传动比变化规律与给定传动比变化规律之差”可根据设计要求采用不同的表述方法。
如果设计仅要求满足特定啮合位置的传动比(如最大传动比、最小传动比),则取相应位置的实际值与给定值之差的绝对值作为目标函数;如果设计要求啮合过程中全程满足给定规律,则以全程各点际值与给定值误差绝对值的最大值作为目标函数。
由于瞬时传动比的变化规律通常要用多点数据加以描述和控制,因此这是一个多目标优化问题,本文选用非线性目标规划法进行优化。
非线性目标规划法是一种专门用来处理目标函数、约束函数均为非线性函数的多目标优化方法,具有以下一些特点[10]
1)目标规划法将多个目标函数按其重要性程度的不同分成若干个优先等级,同一优先等级中的数个目标还可按其重要性程度的细微差别赋予不同的非负加权因子。
2)目标规划法要求对各目标函数事先给定期望值,在优化过程中尽量争取达到这些期望值。
3)目标规划通过引入正负偏差变量将原优化模型中的“硬约束”变为“软约束”,一个约束优化问题在“软约束”下总是有解的,不过是目标规划意义下的最优解。
4)通常意义下的目标函数在目标规划中变成约束函数的一部分,称为目标约束,而目标规划数学模型中的目标函数由偏差变量构成,且总是线性的。
本文算例中以齿轮偏心距e1、e2,安装中心距α为设计变量,以最大、最小瞬时传动比实际值与许用值(期望值)之差的绝对值为目标函数,以将重合度、瞬时压力角和几何中心距控制在一定范围内为约束函数。
优化数学模型为
其中带有max或min下标的参数分别为传动周期中各自的最大、最小值,[]内为许用(期望)值。
采用优化设计方法进行非圆齿轮设计,设计人员唯一要做的是按上述形式建立数学模型(问题函数子程序),即:
选定设计变量(对于不同的设计任务,有些参数可能已事先给出定值),选择目标函数的表述方法,以及调整约束函数的上下限,并输入一些设计中不变化的几何常数,那么,只要这个优化问题是有解的(即设计任务本身是合理有解的),程序就会运用数学规划的方法找到最优解。
根据优化设计理论,这个最优解首先必定是可行解,即满足数学模型中的所有约束,并且是满足所有约束的可行解中使目标函数即实际传动比变化规律与给定传动比变化规律之差最小的解,一次性地成功完成非圆齿轮传动设计。
2.3偏心齿轮优化设计的程序实现
用Fortran语言编写的偏心齿轮优化设计程序由下列模块构成,相互间的调用关系为
输入数据为
模数、齿数、分度圆压力角;
最大、最小瞬时传动比许用(期望)值;
最大瞬时压力角、最大、最小几何中心距许用值;
数值积分步长;
以及其它一些与优化模型、精度控制有关的参数。
输出数据为
设计变量最优值;
目标函数最优值及其与许用(期望)值的正负偏差值;
约束函数值及其与许用值的正负偏差值。
最终优化结果数据可导入图形仿真程序,直观地显示啮合传动过程。
2.4偏心齿轮优化设计示例
设计一对偏心齿轮,模数2mm,齿数均为40,分度圆压力角15°,瞬时压力角不大于40°,重合度不小于1,几何中心距在80mm~83mm之间,偏心距(设计变量)初始值为0mm(无偏心),数值积分步长为15°(每隔15°计算一个点)
[第一类算例]
给定安装中心距、最大最小瞬时传动比,求偏心距
1)安装中心距80mm,希望最大瞬时传动比1.25,最小瞬时传动比0.8
求得偏心距3.515625mm、3.5625mm
实际最大瞬时传动比1.19,最小瞬时传动比0.84
最小重合系数1.002715,最小几何中心距79.676mm(第四优先等级)
2)安装中心距80.2mm,最大瞬时传动比1.1,最小瞬时传动比0.9
求得偏心距1.96875mm、1.875mm
实际最大瞬时传动比1.1007,最小瞬时传动比0.909
最小重合系数1.279458,最小几何中心距80.08mm(第二优先等级)
[第二类算例]
给定最大最小瞬时传动比,求偏心距、安装中心距
希望最大瞬时传动比1.1,最小瞬时传动比0.9
求得偏心距1.875mm、2mm,安装中心距80.625mm
实际最大瞬时传动比1.101,最小瞬时传动比0.908
最小重合系数1.014588,最小几何中心距80.488mm
[第三类算例]
求最大最小瞬时传动比
求得偏心距2.916016mm、2.933594mm,安装中心距80.21875mm时
最大瞬时传动比1.157,最小瞬时传动比0.864
最小重合系数0.999936(第二优先等级),最小几何中心距80mm(第一优先等级)
结论
本文依据啮合基本定理(Willis定理)推导出的计算公式,理论上更加严密,形式上更加简洁,更具有一般适用性,不仅可用于分析计算,更可用于设计计算。
将优化设计概念引入非圆齿轮设计,使非圆齿轮设计方法从传统的基于分析的设计发展为基于综合的设计,避免了带有较大盲目性的参数试凑和反复校验过程,提高了非圆齿轮传动设计的科学性和一次成功率。
本文的研究成果直接以软件工具的形式提供,便于工程技术人员现场应用,并在软件中充分应用数值积分、数值模拟、图形仿真等先进技术手段,使设计结果具有可视性。
参考文献
[1][前苏联]φ..李特文.齿轮啮合原理.上海:
上海科学技术出版社,1984
[2]李福生等.非圆齿轮.北京:
机械工业出版社,1975
[3]李福生等.非圆齿轮与特种齿轮传动设计.北京:
机械工业出版社,1983
[4]吴序堂,王贵海.非圆齿轮及非匀速比传动.北京:
机械工业出版社,1997
[5]韩继光.偏心渐开线齿轮在高速包装机上的应用.林业机械及木工设备,
1996(6)
[6]高洪,吕新生.偏心齿轮机构传动比函数的研究.机械传动,2002(4):
15~16
[7]高洪,吕新生,用偏心齿轮连杆组合机构实现两行程等速运动,安徽机电学院学报,2002(3):
52~55
[8]高洪,吕新生.变性椭圆齿轮节曲线设计及图形仿真,中国机械工程,2003(19),1645~1648
[9]宣家骥,方爱群.目标规划及其应用.合肥:
安徽教育出版社,1987