第三章起动系统.docx
《第三章起动系统.docx》由会员分享,可在线阅读,更多相关《第三章起动系统.docx(16页珍藏版)》请在冰豆网上搜索。
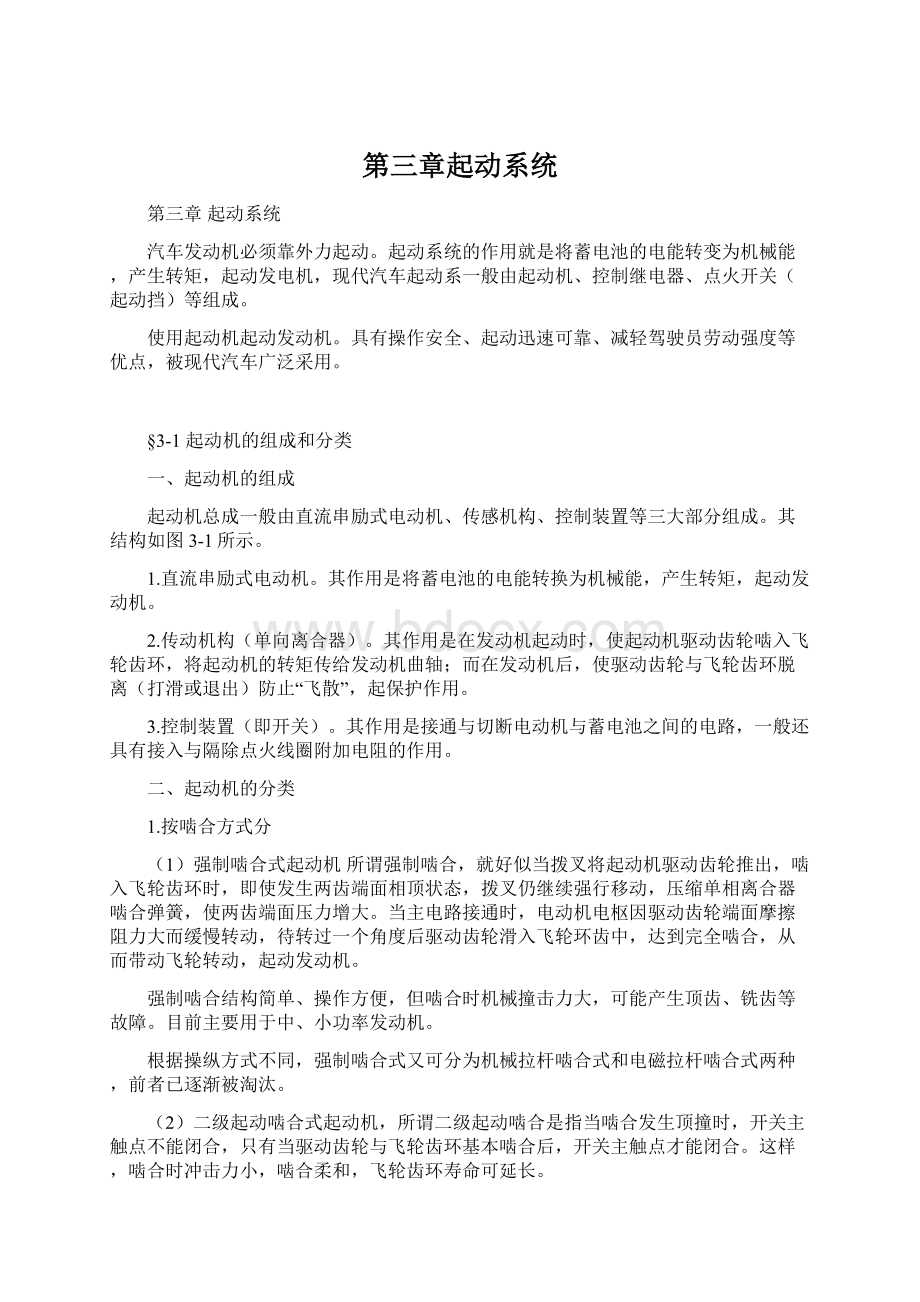
第三章起动系统
第三章起动系统
汽车发动机必须靠外力起动。
起动系统的作用就是将蓄电池的电能转变为机械能,产生转矩,起动发电机,现代汽车起动系一般由起动机、控制继电器、点火开关(起动挡)等组成。
使用起动机起动发动机。
具有操作安全、起动迅速可靠、减轻驾驶员劳动强度等优点,被现代汽车广泛采用。
§3-1起动机的组成和分类
一、起动机的组成
起动机总成一般由直流串励式电动机、传感机构、控制装置等三大部分组成。
其结构如图3-1所示。
1.直流串励式电动机。
其作用是将蓄电池的电能转换为机械能,产生转矩,起动发动机。
2.传动机构(单向离合器)。
其作用是在发动机起动时,使起动机驱动齿轮啮入飞轮齿环,将起动机的转矩传给发动机曲轴;而在发动机后,使驱动齿轮与飞轮齿环脱离(打滑或退出)防止“飞散”,起保护作用。
3.控制装置(即开关)。
其作用是接通与切断电动机与蓄电池之间的电路,一般还具有接入与隔除点火线圈附加电阻的作用。
二、起动机的分类
1.按啮合方式分
(1)强制啮合式起动机所谓强制啮合,就好似当拨叉将起动机驱动齿轮推出,啮入飞轮齿环时,即使发生两齿端面相顶状态,拨叉仍继续强行移动,压缩单相离合器啮合弹簧,使两齿端面压力增大。
当主电路接通时,电动机电枢因驱动齿轮端面摩擦阻力大而缓慢转动,待转过一个角度后驱动齿轮滑入飞轮环齿中,达到完全啮合,从而带动飞轮转动,起动发动机。
强制啮合结构简单、操作方便,但啮合时机械撞击力大,可能产生顶齿、铣齿等故障。
目前主要用于中、小功率发动机。
根据操纵方式不同,强制啮合式又可分为机械拉杆啮合式和电磁拉杆啮合式两种,前者已逐渐被淘汰。
(2)二级起动啮合式起动机,所谓二级起动啮合是指当啮合发生顶撞时,开关主触点不能闭合,只有当驱动齿轮与飞轮齿环基本啮合后,开关主触点才能闭合。
这样,啮合时冲击力小,啮合柔和,飞轮齿环寿命可延长。
二级起动啮合式起动机结构复杂,制造困难。
一般用在大功率发动机上。
我国引进的斯太尔91系列汽车发动机的起动机就采用二级起动啮合方式。
2.按起动机结构分
(1)机械啮合式起动机它是由驾驶员利用脚踏(或手动),通过杠杆联动机构,操纵机械式起动开关来接通与切断起动电流,属强制啮合式,现已逐步淘汰。
(2)电磁啮合式起动机它是由驾驶员转动点火开关至起动档(或按下起动按钮),通过起动继电器,使电磁开关工作,起动机运转,属强制性啮合式。
(3)减速式起动机它是在一般起动机的基础上加装了一个减速装置,属强制啮合式。
(4)活动磁极式起动机它的特点是4个磁极中有一个是活动的,这个活动磁极兼作电磁铁,其绕组(兼作吸引线圈)与保持线圈构成电磁开关,用以控制起动机运转,属强制啮合式。
(5)永磁式起动机一般采用6个永久磁极,为增大转矩大多采用行星齿轮减速装置,属强制啮合式。
(6)电枢移动式起动机它是靠电动机内部辅助磁极的电磁力,使整个电枢作轴向移动,将驱动齿轮啮入飞轮齿环。
发动机启动后,由复位弹簧使电枢回位,齿轮退出。
这种起动机的接入分;两个阶段,属二级起动啮合式。
(7)齿轮移动式起动机它是在电枢移动式起动机的基础上发展起来的。
起动机的接入也分两个阶段,属二级起动啮合式。
目前,国产汽车多为强制性电磁啮合式起动机。
§3-2起动机用直流串励式电动机
一、直流串励式电动机主要由点数、磁极、机壳、端盖、电刷与电刷架等部件组成。
1.电枢
电枢是电动机的转子,用来产生电磁转矩。
它由铁心、绕组、换向器和电枢轴等组成,如图3-2所示、
(1)铁心铁心由硅钢片冲制叠压而成。
为减少涡流损失(磁极),硅钢片两侧涂有绝缘漆或经痒化处理。
铁心外圈冲有线槽,以便安放电枢绕组。
(2)绕组起动机要产生较大的转矩,而供电电压又很低,因此电枢绕组的电流都很大,电枢绕组都是用教粗的矩形裸铜线绕制而成。
为例防止裸体导线短路,在铁心与铜线之间、铜线与铜线之间用绝缘性能较好的复合肥绝缘纸隔开。
电枢绕组各线圈的端头都焊在换向器铜片的凸缘上,通过电刷将蓄电池的电流引入。
(3)换向器换向器的结构如图3-3所示。
它由一定数量的燕尾形铜片压装而成。
铜片与铜片之间、铜片与压环、轴套之间均用云母(或硬塑料)绝缘。
铜片的一端有焊接电枢绕组端头的凸缘。
为了避免电刷磨损的粉末落入铜片间形成短路,起动机的铜片间云母不割低。
(4)电枢轴电枢轴一般用优质钢材制成。
除了固装铁心和换向器外,还伸出一定长度的华健及阶梯光轴,用以套装传动机构和在端盖上作支撑用。
2.磁极
磁极的作用是建立磁场。
它由磁极铁心和励磁绕组组成。
为了增大起动机转矩,磁极数一般为4个,功率大于7.35kW的起动机有用6个磁极的。
(1)铁心用低碳钢制成,呈靴形,以便使磁场合理分布和便于绕组安装。
铁心用螺钉固定在起动机外壳上。
(2)绕组绕组用裸体扁铜线绕制,匝间用复合绝缘纸绝缘。
外部用无碱玻璃纤维带包扎,套装在铁心上。
外部绕组的线匝绕向,必须保证通电后产生N、S交叉排列的极性,如图3-4a所示。
并通过机壳形成通路,如图3-4b所示。
绕组的连接方式有两种,即串联和串并联,如图3-5所示。
采用串并联连接,电动机的总电阻较小,工作时可获得更大的电流,提高输出功率。
3.机壳
机壳是起动机的外壳,也是电动机的磁路部分(见图3-4)。
它由低碳钢板卷压焊成圆简铜形状或由无缝钢管加工而成,内部固定磁极,在它的一端开有检查电刷与换向器的窗口,平时用防尘箍密封。
机壳中部装有一个与之绝缘的电流输入接线柱,机壳两端止口上有组装定位销或缺口。
4.端盖
端盖有两个。
后端盖又称驱动端盖,用以安装起动机和容纳传动机构,用灰铸铁铸造,盖口有安装凸缘和螺孔,因轴较长,故在其中间加有一中间支承。
前端盖一般用钢板压制,端盖中心均压装着青铜石墨轴承或铁基含油轴承,外围有两个螺孔,起动机装配时,用两个长螺栓将前、后端盖及外壳联为一体。
5.电刷与电刷架
电刷与换向器配合,将电流引入电枢绕组。
它由铜粉与石墨压制而成,一般含镍80%~90%,呈棕红色,其顶部有软铜引线。
电刷架多制成框式,固定在前端盖上,正极电刷架与前端盖绝缘,负极电刷架直接搭铁,电刷架上装有弹力较强的盘形弹簧。
电刷及电刷架的组成,如图3-6所示。
二、直流串励式电动机的工作原理
1.工作原理
直流电动机是将直流电流电能转换为机械能,并产生转矩的设备。
它是根据载流导体在磁场中受力的原理设计而成的。
图3-7是直流电动机的工作原理图。
图为以永久磁铁作磁极,产生磁极,产生磁场,在磁场中放置一个能绕其轴旋转的线圈。
线圈的两端各连接一个随线圈转动的半圆形转换片,与换向片接触的电刷固定不动,它们经导线与蓄电池的两级连接。
接通电源在线圈中就有电流通过,电流方向如图所示。
根据左手定则可知,此时线圈将产生逆时针方向转矩。
当线圈转过180
后,虽然线圈在磁场中的位置发生了变化,但各边的电流方向,在换向片的作用下也随之改变,即在N极和S极下导线中电流的方向保持不变。
故电磁转矩的方向并不改变,线圈将继续旋转。
汽车上实际应用的电动机,为了获得较大的功率和转矩,获得比较平稳的转速,增加了线圈的数量与换向片数。
同时,为了提高磁感应强度,并获得理想的电机特性,采用由励磁绕组电流产生的电磁场。
2.转矩与电压平衡方程
(1)直流电动机的转矩由安培定律可知,作用在电枢每根导线上的平均电磁力为:
式中B——每一磁极下的平均磁感应强度;
I——导体内的电流;
L——导体的有效长度。
设电动机有2P个磁极(P为磁极对数),每个磁极的磁通为
,电枢的直径为D。
则每一磁极下的电枢表面积为DL/2P,每一磁极下的平均磁感应强度为:
而
式中
——电枢电流;
a——电枢绕组支路对数,当采用波绕组时,a=1,见图3-5。
将B,I代入
式得:
作用在电枢上的电磁转矩为:
式中Z——电枢的导体总数。
令
,它取决于电机的构造,对某一电机而言,为一常数,称为电机常数。
由此可见,电动机转矩的大小与电枢电流
和磁极磁通
的乘积成正比。
(2)电压平衡方程式电机接通电源时,绕组中有电源通过,产生转矩使电枢旋转,而电枢旋转时,其绕组又会切割磁力线。
根据电磁感应定律,将产生一个与电枢电流方向相反的反电动势
,其大小为:
式中n——电动机转速。
由此可知,外加电压U除一部分克服电枢绕组电阻
和励磁绕组电阻
上的电压降外,另一部分则用开平衡电动机的反电动势
,即:
上述公式是电动机运转时必须满足的一个基本条件,称为电压平衡方程式。
移项,得电枢电流为:
可见,当电动机负载增加时,由于电枢阻力矩增大,电枢转速降低,反电动势减小,而使电枢电流增大,电动机的转矩也随之增大,直至与阻力矩达到新的平衡,电动机在较低转速下平稳运转,反之亦然。
所以,当直流串励式电动机的负载变化时,其转速、电流、转矩会随之变化,以满足不同工况的要求。
三、直流串励式电动机的工作特性
直流串励式电动机的工作特性主要是指电动机的转矩、转速、功率与电流之间的关系。
它包括转矩特性、转速特性和功率特性。
其特性曲线如图3-8所示。
1.转矩特性
所谓转矩特性是指直流串励式电动机的电磁转矩随电枢电流的变化关系,即:
图3-9为直流串励式电动机的工作原理。
由于直流串励式电动机的励磁绕组与电枢绕组与电枢绕组串联,电枢电流与励磁电流相同。
即:
式中:
由上式可知,串励式电动机的电磁转矩在磁路未饱和时,与电枢电流的平方成正比。
只有在磁路饱和,
几乎不变时,电能转矩才与电枢电流成直线关系,如图3-10所示,这是直流串励式电动机的一个重要特点。
在相同情况下,串励式电动机的转矩要比励式电动机的转矩大得多。
特别是在发动机起动瞬间,由于阻力矩很大,起动机处于完全制动状态,n=0,反电动势
,电枢电流达最大值,产生特别大的转矩
,称为制动转矩,从而使发动机易于起动。
这是汽车起动机采用直流串励式电动机的首要原因。
2.转速等性
直流串励式电动机的转速随电枢电流的变化关系称之为转速特性。
即:
由电压平衡方程,
可得
在磁路未饱和时
。
当负载较小时,由于阻力距小,电枢电流(也就是励磁电流)小,磁通
与绕组压降
(
)也较小,故电动机的转速膏。
反之,当负载较大时转速低,即轻载时转速高,重在时转速低。
这种特性通常称为软机械特性,如图3-11所示,这种特性对起动发动机十分有利。
因为重载时转速低,可使起动安全可靠,这是汽车起动机采用直流串励式电动机的又一重要原因。
功率特性
所谓功率特性是指直流串励式电动机输出功率随电枢电流的变化关系。
即:
发动机的功率可由测量电枢轴上的转矩M和转速n确定。
即:
式中M——电枢轴上的转矩;
N——电枢的转速。
由、上式可知,完全制动(n=0)和空载(M=0)时,电动机的输出功率都等于零。
只有在电枢电流接近制动电流的1/2时,功率才达到最大值,如图3-8中的曲线所示。
由于起动机运行时间很短(t<5s),允许以最大功率运转,通常起动机的功率就是指最大功率。
生产中长通过起动机的空转和全制动试验开检查起动机是否正常。
§3-3起动机的传动机构与控制装置
一、传动机构
1.单向离合器
单向离合器的作用是在起动发动机时,将电动机的转矩传给发动机曲轴,,起动发动机;而当发动机起动后,能制动打滑,保护起动机不至飞散。
常用的单向离合器有以下几种:
(1)滚柱式单向离合器
1)构造滚柱式单向离合器的构造如图3-12所示。
驱动齿轮与外壳制成一体,外壳内装有十字块和4套滚柱、压帽和弹簧。
。
十字块与华健套固连,壳底与外壳相互扣合密封。
花健套简的外面装有啮合弹簧及衬圈,末端安装着拨环与卡圈。
整个离合器总成套装在电动机轴上的花键部位上,可作轴向移动和随轴转动。
2)工作原理
①结构特点在外壳与十字块之间,形成4个宽窄不等的楔形槽,槽内分别装有一套滚柱、压帽和弹簧。
滚住的直径略大于楔形槽窄端,略小于楔形槽的宽端,因此,当十字块主转时,滚柱滚入窄端,将十字块与外壳卡紧,似乎成为一体,能传递转矩;当外壳主转时;滚柱滚入宽端,则放松打滑,不能传递转矩。
②工作过程起动时,拨叉动作,将离合器推出,驱动齿轮啮入飞轮齿环后电动机通电,常动十字块旋转。
由于十字块处于主动状态,迫使4套滚柱滚入窄端(受力分析见图3-13a),将十字块与外壳卡紧,传递转矩,驱动曲轴旋转,起动发动机。
起动后,飞轮齿环带动驱动齿轮与外壳高速旋转,当转速超过十字块时,就迫使滚柱滚入宽端打滑(见图3-13b),各自自由转动,起“飞散”保护作用。
(2)摩擦片式离合器中等功率和大功率的起动机多采用摩擦式单向离合器。
它是通过摩擦片的压紧(传递转矩)和放松(防止“飞散”)来实现离合的。
其结构和工作原理如图3-14所示。
2)工作原理起动时,当驱动齿轮啮入飞轮齿环后,电动机通电旋转,内结合毂由于螺旋花键的作用向移动,摩擦片被压紧而将起动机的转矩传给驱动齿轮。
当发动机阻力距较大时,内结合毂会继续向右移动,增大摩擦片之间的压力,直到摩擦片之间的摩擦力足够传递所需的起动转矩,带动曲轴旋转,起动发动机。
起动后,驱动齿轮齿轮被飞轮齿环带动,其转速超过电枢转速时,内结合毂沿螺旋花键向左退出,摩擦片之间的压力消除。
这时驱动齿轮虽然高速旋转但不会带动电枢,起“飞散”保护作用。
(3)弹簧式单向离合器
1)构造弹簧式单向离合器的构造如图3-15所示,连接套筒装在电枢轴的螺旋花键上,驱动齿轮1则套在电枢轴的光滑部分上,两者之间由两个月形键3连接。
月形键可使驱动齿轮与连接套筒之间不能轴向移动,但可相对转动。
在驱动齿轮柄与连接套筒外面包有扭力弹簧4,其两端内径较小(每端内径较小部分的长度占弹簧总长度的1/4),并分别箍紧在齿轮柄和连接套筒上。
扭力弹簧有圆形和扭矩两种截面,外部有护圈封闭。
2)工作原理起动时,电枢轴带动连接套筒旋转,扭力弹簧顺其螺旋方向扭转,圈数增加,内径变小,将齿轮柄与连接套筒包紧,成为整体。
于是,电动机的转矩传给驱动齿轮,带动曲轴旋转,起动发动机。
起动后,驱动齿轮转速高于电枢转速,扭力弹簧被反向扭转,内径变大,齿轮柄与连接套筒松脱,各自转动(齿轮柄被飞轮齿环带动高速旋转),使发动机转矩不能传给电枢,起“飞散”保护作用。
(4)棘轮式单向离合器
1)构造棘轮式单向离合器的传递转矩大,多用于大功率的起动机上。
其结构如图3-16所示,主要由主动棘轮、被动棘轮、花键套筒、有键槽的轴套、弹簧、橡胶垫等组成。
2)工作原理起动时,离合器在拨叉的作用下作轴向移动,使驱动齿轮啮入飞轮齿环。
电动机电枢轴上的转矩通过有键槽的轴套2、主动棘轮8、被动棘轮12传到发动机曲轴上,起动发动机。
起动后,当驱动齿轮转速超过电动机电枢转速时,被动棘轮变为主动,迫使主动棘轮8压缩弹簧7,摆脱同主动棘轮的啮合而打滑,起“飞散”保护作用。
2.拨叉
拨叉的作用是使离合器作轴向移动,将驱动齿轮啮入和脱离飞轮齿环。
现代汽车上一般采用电磁式拨叉。
图3-17为电磁式拨叉。
它用外壳封装于起动机壳体上,由可动和静止两部分组成。
可动部分包括拨叉和电磁铁心,两者之间用螺杆活络地连接。
静止部分有绕在电磁铁心套筒外的线圈、拨叉轴和复位弹簧。
发动机起动时,驾驶员只需将点火开关旋至起动(Ⅱ)挡,线圈通电产生电磁力,将铁心吸入,于是带动拨叉转动,由拨叉推出离合器,使驱动齿轮啮入飞轮齿环。
发动机起动后,松开点火开关,点火开关便自动回位一个角度(回至点火开关Ⅰ挡),二、控制装置
1.电磁开关
电磁开关的作用是接通与切断起动机的主电路和起动时短路点火线圈附加电阻。
(1)构造电磁开关的结构如图3-18所示。
电磁开关装在起动机外壳上,吸引线圈和保持线圈绕在黄铜套管上,套管内有固定铁心6和活动铁心9.吸引线圈与电动机的励磁和电枢绕组串联。
保持线圈一端搭铁,另一端与吸引线圈用时接在起动机接线柱上(见下节图3-20)。
活动铁心通过调节器螺钉11与拨叉12连接,并可以通过推杆8推动主接触盘,接通与切断主电路。
(2)工作过程见下节QD124型起动机控制电路。
2.继电器
现代汽车起动系多装用组合继电器,如图3-19所示(有的用单联起动继电器,如QD124型起动机控制电路)。
(1)组合继电器的作用
1)与点火开关配合,控制起动机电磁开关吸引线圈与保持线圈电流的通、断。
避免了因两线圈电流大,而烧损点火开关(或起动按钮)。
2)使起动机具有自锁保护作用,即在发动机起动后能自动停止工作,还能防止起动机误投入工作。
3)兼作控制充电指示灯。
(2)组合继电器的构造组合继电器由起动继电器和保护继电器两部分组成。
起动继电器用来控制电磁开关工作。
L1线圈承受蓄电池的端电压,K1触点常开。
保护继电器在发电机中性点电压
作用下,使起动机具有自锁功能,其K2触点为肠壁式,在“L”柱与点火开关之间接一指示灯,可进行充电指示控制(见图2-37)。
(3)工作过程见下节CA1092型汽车起动系统控制电路。
§3-4起动系统实例
一、东风EQ1090型汽车起动系统
早期的东风EQ1090型汽车起动系统,由QD124型电磁开关强制啮合式起动机、起动继电器、点火开关(起动挡)等组成,其控制电路如图3-20所示。
工作过程如下:
1.起动时,将点火开关3旋至起动挡(Ⅱ),起动继电器线圈通电,其电路为:
蓄电池“+”极→主接线柱→电流表→点火开关Ⅱ→起动继电器点火开关接线柱→继电器线圈2→搭铁接线柱→搭铁→蓄电池负极。
由于线圈通电,产生电磁力吸下衔铁,触点1闭合,接通了电磁开关吸引线圈与保持线圈电路,其电流路线为:
蓄电池“+”→主接线柱4→起动继电器电磁接线柱→磁扼及衔铁→触点1→继电器起动机接线柱→磁扼及衔铁→触点1→继电器起动机接线柱→起动机接线柱9→
→搭铁→蓄电池“—”极。
由于两线圈电流同向,磁场叠加,产生较大的电磁力,将活动铁心15吸入,通过拨叉19,将单向离合器20推出。
在起动机缓慢转动下,驱动齿轮21柔和地啮入飞轮齿环。
当齿轮啮合1/2时,活动铁心15就顶动推杆11,使接线柱6和主接线柱4、5相继接通。
在点火线圈附加电阻被短路后起动机通入大电流,产生强大转矩,起动发动机。
2.起动中,由于接触盘把主接线柱4和5接通,将吸引线圈13短路,靠保持线圈14的电磁力维持在工作位置。
3.起动后,松开点火开关,点火开关即自动回转一个角度(到点火挡),起动继电器线圈断电,衔铁被释放,触点1打开,电磁开关保持线圈中的电流改经起动机开关与吸引线圈,形成通路,其电路为:
蓄电池“+”极→主接线柱4→接触盘10→主接线柱5→导电片7→接线柱8→吸引线圈13→接线柱9→保持线圈14→搭铁→蓄电池“—”极。
此时,两线圈电流反向,磁场互相抵消,电磁力迅速消失,在复位弹簧的作用下,拨叉回位,驱动齿轮退出。
同时活动铁心15放松了对推杆11的顶压,主、辅电路相继断开。
起动机停止工作,附加电阻又串入点火电路。
驱动齿轮未退出前,单向离合器起“飞散”保护作用。
二、解放CA1090型汽车起动系统
解放CA1092型汽车起动系统由电磁开关强制啮合式起动机、组合继电器和点火开关(起动挡)等组成,其控制电路如图3-21所示。
工作过程如下:
1.起动时,将点火开关旋至起动挡(Ⅱ),组合继电器线圈L1通电,其电路为:
蓄电池“+”极→电磁开关主接线柱1→30A熔断器→电流表→点火开关Ⅱ挡(1—4)→组合继电器接线柱SW→起动继电器线圈L1→保护继电器常闭触点K2→接线柱E→搭铁→蓄电池“—”极。
由于L1线圈通电,K1闭合,接通了起动机电磁开关中吸引线圈与保持线圈电路:
蓄电池“+”极→电磁开关主接线柱1→组合继电器接线柱B→触点K1→接线柱S→起动机接线柱3→
→搭铁→蓄电池“—”极。
以后起动机投入工作的过程与QD124相同,故不重述。
2.起动后,松开点火开关,它自动返回点火(Ⅰ)挡,起动继电器L1线圈断电,K1打开,起动机停止工作(过程与QD124相同).
3.自停:
发动机发动后,若点火开关仍处于起动挡,起动机也会自动停止运转.这是因为发动机起动后,发动机已正常发电,中性点电压
加在保护继电器线圈L2个使K2打开,起动继电器线圈L1断电,K1打开,切断了电磁开关电路,起动机停止工作.
4.防止误动作:
发动机正常运行时,发电机中性点电压
一直加在保护继电器的线圈L2上,K2一直打开,这时,即使驾驶员误将点火开关旋至起动挡,因起动继电器线圈L1的电路不通,K1不会闭合,电磁开关也就不会动作,起到了锁止作用。
三、QD04型起动机
某些柴油汽车,电系电压为12V,而起动机额定电压却为24V,为了满足正常和起动两种电压的要求,在起动机控制电路中,装设了电压转换开关,QD04型起动机就是这种控制电路,如图3-22所示。
工作工程如下:
1.不工作时,触点3和5常闭,蓄电池Ⅰ和Ⅱ处于并联状态,输出电压12V,其并联电路为:
蓄电池Ⅱ“+”极→接线柱+DⅡ→熔断丝14→接线柱D2→触点3→接线柱+D1→蓄电池Ⅰ“+”极。
蓄电池Ⅱ“—”极→接线柱-D2→触点5→熔断丝13→搭铁。
即蓄电池Ⅰ和Ⅱ的正极联通,负极都搭铁,形成并联电池组。
2.起动时,接通点火开关12,按下起动按钮11,转换开关线圈9通电,其电路为:
电池组“+”极→接线柱+D1→点火开关12→按钮11→接线柱X2→转换开关线圈9→接线柱X1→搭铁→电池组“—”极。
线圈9通电后
,产生电磁力,将活动铁心10吸入,通过推杆8,使接触盘和夹布胶木圈4左移,顶开触点3和5,同时大接触盘6接通-D2和+D1,小接触盘7接通J与+D2,使蓄电池Ⅰ和Ⅱ串联,其电路为:
蓄电池Ⅰ“+”极→接线柱+D1→大接触盘6→接线柱→D2→蓄电池Ⅱ“—”极。
将蓄电池Ⅰ的正极与蓄电池Ⅱ的负极接通,串联成电池组,输出电压24V。
其中蓄电池Ⅱ的正极为电池组的正极,蓄电池Ⅰ的负极为电池组的负极,蓄电池组对电磁开关供电,其电路为:
蓄电池组“+”极→接线柱+DⅡ→熔断丝14→接线柱+D2→小接触盘7→接线柱J→起动机接线柱→
搭铁→蓄电池组“—”极。
于是电磁开关工作,主电路接通,其电路为:
蓄电池组“+”极→接线柱+DⅡ→电磁开关主接触盘→主接线柱→起动机励磁、电枢绕组→搭铁→蓄电池“—”极。
起动机子啊24V电压下工作,产生强大转矩,起动发动机。
3.起动后,松开起动按钮,转换开关线圈9断电,在复位弹簧弹力的作用下,接触盘等复位。
+D1与-D2,+D2与J断开,触点3和5闭合,蓄电池恢复并联。
汽车电系以12V供电。
§3-5汽车用其他形式的起动机
一、活动磁极式起动机
活动磁极式起动机与一般起动机的主要区别是它的4个磁极中有一个是活动的。
这个活动磁极兼作电磁铁,其绕组(兼作吸引线圈)与保持线圈构成电磁开关。
这种饿其动机的结构与控制电路如图3-23所示。
工作过程如下:
1.打开点火开关S,起动继电器线圈电,触点K1闭合,接通了起动机电路,一方面电流经励磁绕组(吸引线圈)D、搭铁触点K2和保持线圈E并联接地,产生电磁力,吸引活动磁极向下运动,拨叉逆时针摆动,推动右端离合器向右运动,使驱动齿轮与飞轮迟缓啮合。
另一方面,励磁绕组A、B几电枢绕组(励磁绕组C与电枢绕组并联)通电,使起动机驱动齿轮在电枢缓慢转动下柔和地嗫嚅飞轮齿环。
2.驱动齿轮与飞轮齿环啮合后,拨叉左端将电磁开关触点K2打开。
于是励磁绕组A、B、C、D和电枢绕组形成4级串励式直流电动机标准电路,产生强大转矩,起动发动机。
3.发动机起动后,断开点火开关,起动继电器线圈断电,触点K1打开,起动机断电,拨叉复位,起动机停止工作。
1.结构特点
电枢在复位弹簧14的弹力作用下与磁极错开一定位置,而且换向器也较长。
起动机有3个(也有