UT探伤工艺.docx
《UT探伤工艺.docx》由会员分享,可在线阅读,更多相关《UT探伤工艺.docx(13页珍藏版)》请在冰豆网上搜索。
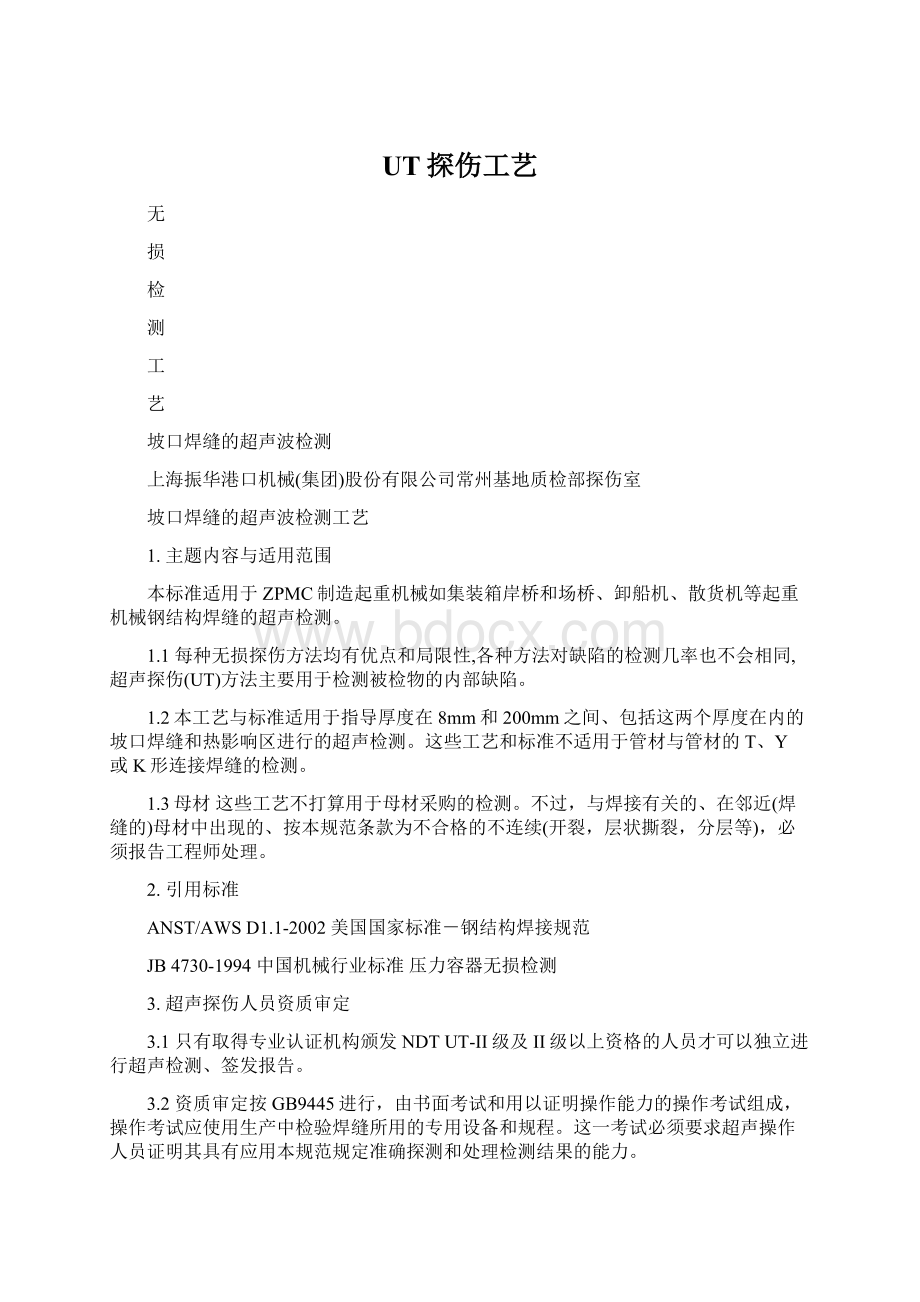
UT探伤工艺
无
损
检
测
工
艺
坡口焊缝的超声波检测
上海振华港口机械(集团)股份有限公司常州基地质检部探伤室
坡口焊缝的超声波检测工艺
1.主题内容与适用范围
本标准适用于ZPMC制造起重机械如集装箱岸桥和场桥、卸船机、散货机等起重机械钢结构焊缝的超声检测。
1.1每种无损探伤方法均有优点和局限性,各种方法对缺陷的检测几率也不会相同,超声探伤(UT)方法主要用于检测被检物的内部缺陷。
1.2本工艺与标准适用于指导厚度在8mm和200mm之间、包括这两个厚度在内的坡口焊缝和热影响区进行的超声检测。
这些工艺和标准不适用于管材与管材的T、Y或K形连接焊缝的检测。
1.3母材这些工艺不打算用于母材采购的检测。
不过,与焊接有关的、在邻近(焊缝的)母材中出现的、按本规范条款为不合格的不连续(开裂,层状撕裂,分层等),必须报告工程师处理。
2.引用标准
ANST/AWSD1.1-2002美国国家标准-钢结构焊接规范
JB4730-1994中国机械行业标准压力容器无损检测
3.超声探伤人员资质审定
3.1只有取得专业认证机构颁发NDTUT-II级及II级以上资格的人员才可以独立进行超声检测、签发报告。
3.2资质审定按GB9445进行,由书面考试和用以证明操作能力的操作考试组成,操作考试应使用生产中检验焊缝所用的专用设备和规程。
这一考试必须要求超声操作人员证明其具有应用本规范规定准确探测和处理检测结果的能力。
4.超声设备
4.1设备要求
超声仪器必须为脉冲反射式探伤仪,配用振荡频率为1~6MHz的换能器。
显示必须为整流的视频扫描的A型显示。
4.2水平线性
检测仪器的水平必须按“AWSD1.1:
2002版钢结构焊接规范”6.30.1在检测所用的全声程距离内进行鉴定。
4.3检测仪器要求
检测仪器必须带有内部稳压装置,使得温升后当额定供电电压变化15%、或在使用电池情况下整个充电使用寿命时间内,响应变化不大于±1dB。
必须装一警报器或仪表,以便在电池耗尽而仪器切断之前,发出电池电压下降信号。
4.4检测仪器的校准
检测仪器必须有校准用增益(衰减)控制器,它应至少在60dB的整个范围内每档1dB或2dB间断可调。
衰减装置必须具有±1dB以内的精度。
鉴定程序必须按6.2和“AWSD1.1:
2002版钢结构焊接规范”6.30.2所述。
4.5显示范围
仪器显示的动态范围必须做到1dB幅度的变化容易察觉并显示。
4.6直射波束(纵波)探头
直射波束(纵波)探头换能器必须有一不小于323㎜2又不大645mm2的工作面积。
换能器必须为圆形或方形。
换能器必须能分辨“AWSD1.1:
2002版钢结构焊接规范”6.29.1.3所述的三种反射波。
4.7斜射波束探头
斜射波束探头必须由换能器和一斜射楔块组成。
它可分列构成,也可为一个组合体。
4.7.1频率 换能器的频率必须在2~2.5MHz之间(包括2,2.5MHz)。
4.7.2换能器尺寸换能器晶体形状必须为正方形或矩形,宽度为15~25㎜,高度为15~20mm(见图6.20)。
最大宽高比为1.2:
1.0,最小宽高比为1.0:
1.0。
4.7.3角度探头必须在检测材料内产生一声束,其角度为70o、60o或45o中一个合适角度±2o。
4.7.4记号每一探头必须有清晰记号标明换能频率、额定折射角和入射点。
入射点定位方法如“AWSD1.1:
2002版钢结构焊接规范”所述。
4.7.5内部反射探头的最大容许内部反射必须如6.3所述。
4.7.6前沿距离探头的尺寸必须符合:
从探头的前沿到入射点的距离严禁超过25㎜。
4.7.7IIW试块用IIW对比试块进行鉴定的方法必须符合“AWSD1.1:
2002版钢结构焊接规范”和图6.21所示要求。
5.对比标准
5.1IIW标准
图6.22所示国际焊接学会(IIW)超声对比试块必须作为距离校准和灵敏度校准的标准。
如果检测仪/探头组合的对比灵敏度调节到IIW试块的等量值,则其他便携式试块也可应用。
5.2禁止使用的反射体
使用“端角”反射体来校准是禁止的。
5.3分辨力要求
探头与检测仪的组合必须分辨出RC分辨力对比试块上的三个孔,如图6.23所示。
探头位置见“AWSD1.1:
2002版钢结构焊接规范”6.29.2.5规定。
分辨力必须根据仪器控制处于正常试验状态下,以及孔的反射指示在萤光屏中等高度进行估算。
分辨能力必须至少能区分来自三个孔的指示峰值。
这RC分辨力对比试块不是用来进行校准的。
每一仪器探头(底板和换能器)的组合必须在其初次使用前就要进行检验。
每一探头和UT装置一经组合就必须进行校验。
如果保存的文件记录下述项目,则这一校验无需再次进行:
(1)UT机器的制造.型号和系列号。
(2)校验的制造商.类型.尺寸.角度和系列号。
(3)校验日期和技术员姓名。
注:
1.对比或校准时有关各表面之间的尺寸允许误差必须在标示值±0.13㎜的范围内。
2.所有材料必须为ASTMA36钢材或声学上等效的材料。
3.所有孔的内壁必须光滑,且必须对材料表面钻成90o。
4.所有刻度线与标记必须在材料表面上加工成凹槽,以使标定线持久耐用。
5.其他稍有不同尺寸或校准槽的校准块经认可也可使用。
6.上述所注各条适用于图6.22和6.23。
6.设备鉴定
6.1水平线性
在仪器每使用40小时后,必须对检测仪器需用的每一距离范围的水平线性重作鉴定。
鉴定方法必须按“AWSD1.1:
2002版钢结构焊接规范”6.30.1进行(见附录X,备用方法)。
6.2增益控制
仪器的增益(衰减器)控制必须满足4.4的要求,并必须每隔两个月按“AWSD1.1:
2002版钢结构焊接规范”6.30.2的要求校准一次。
如可证实至少等效于6.30.2要求,则选用的方法可用作校准的增益控制(衰减器)的鉴定。
6.3内部反射
仪器最多使用40小时,就必须对每一探头的最大内部反射进行校验。
6.4斜射波束探头校准
每一个斜射波束探头必须在每使用8小时后用认可的校准块进行检验,以确定接触面是否平整,声波入射点是否正确,以及波束角度是否在规定的±2°的公差范围内。
不符合这些要求的探头必须予以修正或更换。
7.检测时的校准
7.1衰减控制状态
所有的校准与检测必须在关闭衰减(限制或抑制)控制状态下进行。
衰减(限制或抑制)控制的使用可能改变仪器的波幅线性和导致检测结果无效。
7.2技术
灵敏度和水平扫描(距离)的校准必须由超声波检测人员就要在对每一焊缝检测之前,并在检测部位进行。
7.3重新校准
因检测人员变换,或仪器电路有下述任何一种形式的干扰,都必须重新校准:
(1)更换换能器;
(2)更换电池;
(3)更换电输出端;
(4)更换同轴电缆;
(5)电源中断(故障)。
7.4母材的直射波束检测
母材直射波束检测的校准必须将探头置于母材的A面并按下述要求进行:
7.4.1扫描线必须将距离校准的水平扫描线调节到显示至少等于两倍板厚的量值。
7.4.2灵敏度必须在无缺陷指示部位调节灵敏度,以使从钢板远边的第一底面回波达到全屏高度的50%~75%。
7.5斜射波束检测校准
斜射波束检测校准必须按如下要求进行。
7.5.1水平扫描线必须按5.1规定用IIW试块或代用试块进行调节,使其显示实际的声程距离。
距离校准必须采用显屏上125㎜刻度或250㎜刻度中较为适当的一种。
然而,如果这种设定中任何一种由于接头的轮廓形状或厚度妨碍了对焊缝的充分检验,则距离校准必须根据需要,使用400或500㎜的刻度。
探头位置如“AWSD1.1:
2002版钢结构焊接规范”所述。
注:
所有萤光屏指示的水平位置只取轨迹线左侧起点水平基线的位置。
7.5.2零对比基准用于伤评定(超声波检测报告的“b”项,见附录D的表格DII)零对比基准灵敏度,是由调节探伤仪的校准的增益控制(衰减器)来达到,调节应符合4的要求,使得最大水平轨迹偏移得到显示,符合“AWSD1.1:
2002版钢结构焊接规范”的要求。
8.检测工艺
8.1“X”轴
必须将伤定位用的“X”轴标记于焊件检测面上,方向与焊缝轴线平行。
其与焊缝轴线的垂直距离取决于详图的尺寸,且通常落在对接接头焊缝的中心线上;而对T形和角接接头焊缝而言,“X”轴总是落在这些焊缝的连接构件的靠近的面上(C面的相对面)。
8.2“Y”轴
“Y”轴连同焊缝标记号必须清晰地标注在经受超声波检测的焊缝旁的母材上。
这种标注的目的在于:
(1)焊缝标记;
(2)A面标记;
(3)距离测量和离开“X”轴的方向(+或-)。
(4)从焊缝的端部或边缘的定位测量。
8.3清洁处理
所有探头接触的表面必须无焊接飞溅、污物、脂类、油类(用作耦合剂的油除外)、油漆和松散氧化皮,且必须有一容许紧密耦合形。
8.4耦合剂
在探头和待检测材料之间必须使用耦合剂。
耦合剂必须是甘油或具有适当稠度的纤维素胶与水的混合物。
如需要可以加增湿剂。
在校准块上可用轻机油作耦合剂。
8.5检测范围
检测焊缝时,超声波必须扫经母材,必须对整个母材进行有无层状缺陷反射的检验,检验用直射波束探头,它需符合4.6的要求进行,校准按4.6的要求进行。
如在任何区域发现底面回波消失,或者在某一位置有一等于或大于原底面回波高度的指示,且其影响正常的焊缝扫查过程,则必须确定其尺寸、部位和离A面的深度,并记录在超声波检测报告上,同时,必须使用另一种焊缝扫查方法进行检测。
8.5.1反射体尺寸反射体尺寸的评估方法必须按“AWSD1.1:
2002版钢结构焊接规范”6.31进行。
8.5.2不可达性如果按照表6.7的要求进行检测、而由于如8.5所述有层状缺陷、部分焊缝不可达时,为得到全部焊缝的检测结果,必须使用下述一种或几种选用方法进行检测:
(1)必须将焊缝表面打磨平齐;
(2)必须从A面和B面进行检测;
(3)必须使用其他探头角度。
8.6焊缝检测
必须使用符合4.7要求的斜射波束探头、按7.5要求校准的仪器、使用表6.6所示的角度检测焊缝。
随后的校准以及检测过程中,唯一允许进行的仪器调节是使用校准的增益控制(衰减器)进行灵敏度调节。
衰减(抑制或限幅)控制必须关闭。
按表6.2或6.3进行焊缝扫查时,灵敏度必须比基准水平有所提高。
8.6.1扫查检测角度和扫查方法必须符合表6.7所示要求。
8.6.2对接接头所有对接焊缝必须从焊缝轴线的两侧检测。
角接接头和T形接头必须基本上仅从焊缝轴线的一侧检测。
所有焊缝的检测必须使用适当的扫查方式,或在必要时使用图6.24所示的方式,纵向和横向的伤都要探测。
无论什么地方的实际情况如何,最低限度要有意做到:
检测焊缝的声波在两相交方向上通过所有受检焊缝与热影响区的整个体积。
表6.7
工艺卡
材料厚度
焊缝
类型
8
~
≤35
>38
~
≤45
>45
~
≤60
>60
~
≤90
>90
~
≤110
>110
~
≤130
>130
~
≤160
>160
~
≤180
>180
~
≤200
对接
1
0
1
F
1G或 4
F
1G或5
F
6 或 7
F
8 或10
F
9 或11
F
12或13
F
12
F
T型
1
0
1
F或XF
4
F或XF
5
F或XF
7
F或XF
10
F或XF
11
F或XF
13
F或XF
-
-
角接
1
0
1
F或XF
1G或4
F或XF
1G或5
F或XF
6或7
F或XF
8或10
F或XF