参考焦炭塔本体的设计.docx
《参考焦炭塔本体的设计.docx》由会员分享,可在线阅读,更多相关《参考焦炭塔本体的设计.docx(38页珍藏版)》请在冰豆网上搜索。
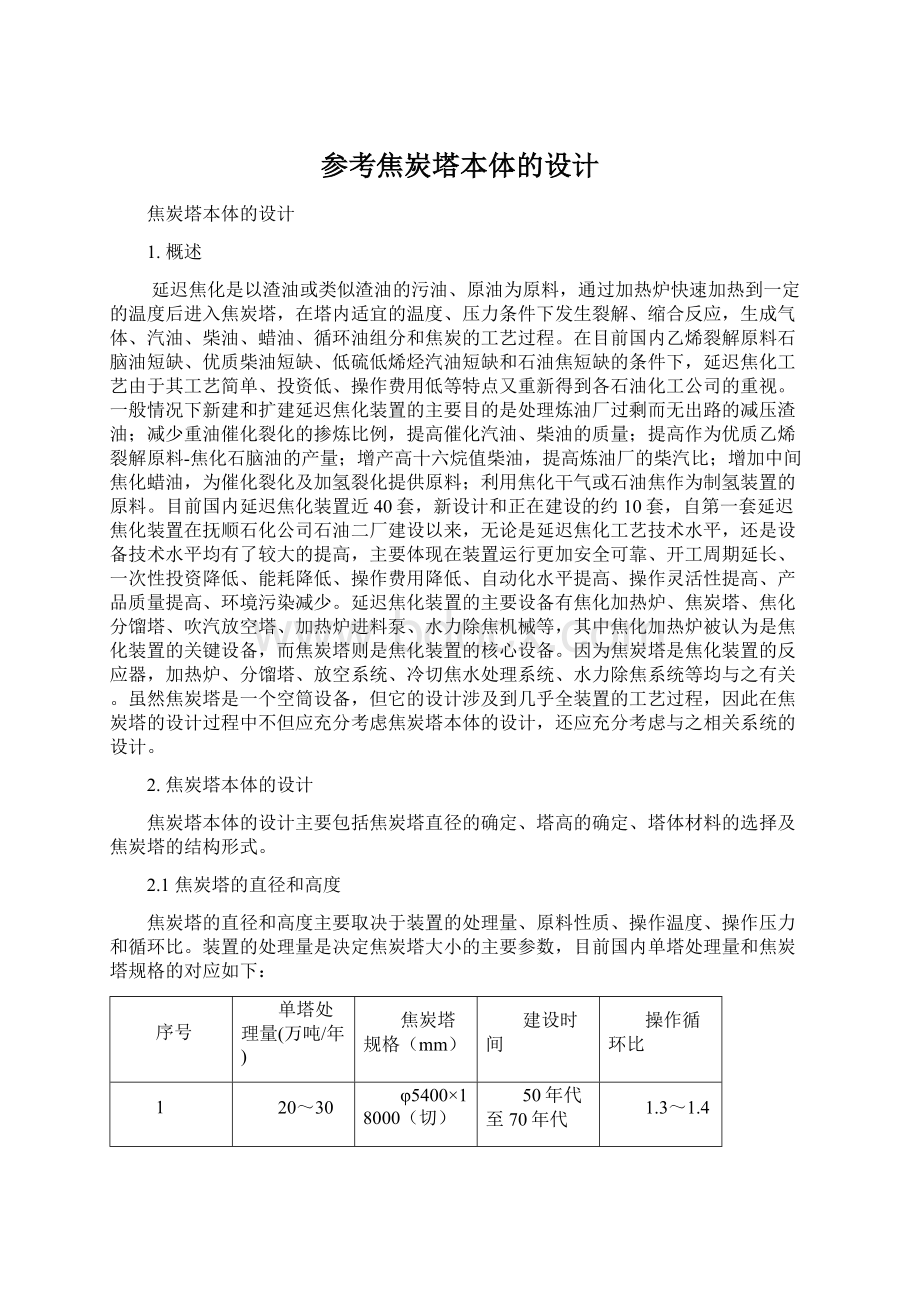
参考焦炭塔本体的设计
焦炭塔本体的设计
1.概述
延迟焦化是以渣油或类似渣油的污油、原油为原料,通过加热炉快速加热到一定的温度后进入焦炭塔,在塔内适宜的温度、压力条件下发生裂解、缩合反应,生成气体、汽油、柴油、蜡油、循环油组分和焦炭的工艺过程。
在目前国内乙烯裂解原料石脑油短缺、优质柴油短缺、低硫低烯烃汽油短缺和石油焦短缺的条件下,延迟焦化工艺由于其工艺简单、投资低、操作费用低等特点又重新得到各石油化工公司的重视。
一般情况下新建和扩建延迟焦化装置的主要目的是处理炼油厂过剩而无出路的减压渣油;减少重油催化裂化的掺炼比例,提高催化汽油、柴油的质量;提高作为优质乙烯裂解原料-焦化石脑油的产量;增产高十六烷值柴油,提高炼油厂的柴汽比;增加中间焦化蜡油,为催化裂化及加氢裂化提供原料;利用焦化干气或石油焦作为制氢装置的原料。
目前国内延迟焦化装置近40套,新设计和正在建设的约10套,自第一套延迟焦化装置在抚顺石化公司石油二厂建设以来,无论是延迟焦化工艺技术水平,还是设备技术水平均有了较大的提高,主要体现在装置运行更加安全可靠、开工周期延长、一次性投资降低、能耗降低、操作费用降低、自动化水平提高、操作灵活性提高、产品质量提高、环境污染减少。
延迟焦化装置的主要设备有焦化加热炉、焦炭塔、焦化分馏塔、吹汽放空塔、加热炉进料泵、水力除焦机械等,其中焦化加热炉被认为是焦化装置的关键设备,而焦炭塔则是焦化装置的核心设备。
因为焦炭塔是焦化装置的反应器,加热炉、分馏塔、放空系统、冷切焦水处理系统、水力除焦系统等均与之有关。
虽然焦炭塔是一个空筒设备,但它的设计涉及到几乎全装置的工艺过程,因此在焦炭塔的设计过程中不但应充分考虑焦炭塔本体的设计,还应充分考虑与之相关系统的设计。
2.焦炭塔本体的设计
焦炭塔本体的设计主要包括焦炭塔直径的确定、塔高的确定、塔体材料的选择及焦炭塔的结构形式。
2.1焦炭塔的直径和高度
焦炭塔的直径和高度主要取决于装置的处理量、原料性质、操作温度、操作压力和循环比。
装置的处理量是决定焦炭塔大小的主要参数,目前国内单塔处理量和焦炭塔规格的对应如下:
序号
单塔处理量(万吨/年)
焦炭塔规格(mm)
建设时间
操作循环比
1
20~30
φ5400×18000(切)
50年代至70年代
1.3~1.4
2
40~50
φ6100×21000(切)
80年代至90年代
1.3~1.4
3
100~120
φ8400×21000(切)
90年代末
1.15~1.35
4
130~140
φ8800×27000(切)
21世纪初
1.15~1.25
5
150~170
φ9400×26500(切)
21世纪初
1.15~1.25
焦炭塔的单塔处理量越大,要求的焦炭塔直径越大,这主要是由焦炭塔塔内的允许气速决定的。
焦化原料渣油在加热炉中被快速加热到500℃左右进入焦炭塔,为防止加热炉管结焦,炉出口的反应转化率一般不大于10%(气体和汽油的转化率),大部分的反应延迟到焦炭塔内进行,原料进入焦炭塔,在塔内适宜的压力、温度和停留时间的条件下发生裂解和缩合反应,裂解为吸热反应,缩合为放热反应,裂解的热量除了来自原料渣油本身外还有一部分由缩合反应提供,缩合反应生成的焦炭停留在塔内,并由塔壁向中心扩展,中心形成进料通道,在焦炭层以上为主要反应区,即泡沫层。
泡沫层分油相泡沫和气相泡沫,气相泡沫在上部,其密度约为30~100kg/m3,油相泡沫在焦层以上,其密度约为100~700kg/m3,焦化反应温度即为泡沫层温度,一般为460~480℃,并且生焦率越高,该反应温度越高。
焦炭层也存在焦化反应,裂化生成的气体自焦炭层益处,焦炭层的空隙率约为:
30%~50%。
使热态的焦炭层高度高于冷态的焦炭高度。
随着原料的不断进入,产生的焦炭量增加,焦炭层高度增加,泡沫层也随之连续升高。
塔内反应示意图如下:
由于泡沫层为反应区,一般不希望正在反应的泡沫被油气夹带到焦炭塔顶出口的大油气管线和分馏塔,导致管线结焦和分馏塔内结焦影响产品质量。
焦炭塔内油气的允许气速可用下式计算:
其中Uc为塔内允许气相线速,m/s;
ρL为轻相泡沫层密度,kg/m3;
ρLV为气相泡沫层密度,kg/m3。
K为物性校正系数
据资料报导,国外在焦炭塔内不注入消泡剂时,允许气速一般为0.11~0.17m/s。
在使用消泡剂时,正常的设计油气速度应低于0.12~0.21m/s。
根据允许的油气速度和焦炭塔内的油气流量即可确定焦炭塔的直径,为减少泡沫夹带,新设计焦炭塔建议采用低的油气速度,国内设计焦炭塔内的油气速度一般低于0.10~0.15m/s。
焦炭塔内的油气体积流量除和渣油进料量有关外,与原料性质、操作条件也有密切的关系。
在确定焦炭塔的直径以前应首先确定焦炭塔的操作条件和产品分布。
渣油是以碳、氢、硫、氮、氧等为主要元素的大分子烃类,通常分为饱和烃、芳烃、胶质和沥青质,沥青质含量高的渣油生焦率较高,轻油收率较低。
产品分布一般最终由试验确定,在没有实验数据时可参考下式估算:
(1)硫化氢收率,W%:
H2S=0.25*Sf
(2)干气收率,W%:
RG=3.5+0.1*CCR
(3)LPG收率,W%:
LPG=3.3+0.044*CCR
(4)焦炭收率,W%:
COK=1.6*CCR
(5)石脑油收率,W%:
Nao=11.38+0.335*CCR
(6)瓦斯油收率,W%:
TGO=100-(H2S+RG+LPG+COK+Nao)
(7)柴油收率/瓦斯油收率,R=0.38+0.011*CCR-0.00031*CCR
(8)柴油收率,W%:
LCGO=R*TGO
(9)蜡油收率,W%:
HCGO=TGO-LCGO
其中:
CCR为渣油的康氏残炭(W%),Sf为渣油的硫含量(W%)。
当原料性质确定后,对生焦率和产品分布影响较大的主要是循环比、反应温度和压力。
循环比减少10%,生焦率一般减少1%,同时焦化蜡油收率增加,气体、汽油、柴油收率下降。
当需要提高装置的液体收率时一般采用降低循环比(0.15~0.25)或零循环比操作;当需要多产焦化石脑油和柴油时一般采用较大循环比(0.25~0.45)操作;当焦化蜡油无出路或需要最大可能地生产乙烯原料时一般采用大循环比(0.4~1.0)操作。
循环比越大,焦炭塔内的油气体积流量越大。
提高焦化温度可增产液体产品收率,但基于焦化反应的特点,反应温度(炉出口温度控制)调整的幅度是很窄的,温度过高会导致提前结焦,堵塞炉管、转油线,影响开工周期,同时易生成硬质石油焦,使除焦困难;温度过低导致热量不足反应深度不够,轻油收率降低,焦炭挥发分增大或产生焦油。
一般情况下是根据原料性质确定最佳的操作温度,通常焦化炉出口温度为495~505℃,芳烃含量和沥青质含量的比值较大时宜采用较高的炉出口温度。
采用低压操作可改善焦化产品分布,在国内外已普遍认可,国内焦炭塔顶操作压力一般为0.15~0.20Mpa,国外最低的达到0.1~0.15Mpa。
压力降低一般是提高蜡油的收率,但是增大了焦炭塔的气体体积流量,势必使焦炭塔的塔径加大,装置的投资增加,因此应综合设备投资、操作费用和产品分布等因素确定适宜的操作压力。
另外焦化加热炉的注汽注水量、在线清焦时的加热炉吹汽量、四通阀及切断阀的汽封蒸汽量对焦炭塔的直径确定也有一定的影响,一般加热炉的注汽注水量按炉新鲜进料的1.0~1.5%考虑,在线清焦时应考虑减少渣油进料,增加蒸汽量,蒸汽量可按2~8t/h考虑。
焦炭塔底阀门的汽封量在采用连续注入时应考虑0.5~1.0t/h的蒸汽量。
在基本确定焦炭塔的直径后,根据原料性质、焦炭产率、生焦时间、泡沫层高度来确定焦炭塔的高度。
焦炭产率和原料性质、操作条件有关,泡沫层高度和原料性质、反应温度及压力有关。
当在焦炭塔内注入消泡剂后,泡沫层的高度一般减少50~70%。
当单塔处理能力、原料性质和操作条件确定后,塔内的焦层高度主要确定于生焦时间。
目前国内焦化装置设计的生焦时间均为24小时,国外焦化生焦时间一般为10~24小时,采用16小时的占大多数,采用短的生焦时间,可以提高焦炭塔的利用率,或者同等规模的焦炭塔的高度减少。
在确定焦炭塔高度时应留有一定的安全空高,安全空高一般为塔顶切线离泡沫层顶部的距离,国内设计的焦炭塔一般安全空高大于等于3米,国外焦炭塔的安全空高一般为2~3米。
空高越大,焦炭塔的利用率越低,但油气在塔内的停留时间延长,对减少油气线和分馏塔内结焦有利。
空高的计算公式如下:
其中:
H切-焦炭塔切线高度,m;
G焦-焦炭生焦速率,kg/h;
τ焦-生焦时间,hr;
ρ焦-塔内焦炭堆密度,kg/m3(800~900kg/m3);
V锥-焦炭塔锥体体积,m3;
D塔-焦炭塔直径,m;
H泡沫-泡沫层高度,m。
通常所说的缩短生焦时间可以提高处理量,是提高了焦炭塔的利用率。
焦炭塔直径和切线高度的关系
焦炭塔直径和高度相互补充,当装置处理量、操作条件确定后,直径增大可以降低高度,高度增加也可以适当减少塔径。
国内在过去建设的焦炭塔的直径一般为5.4~6.4米,其高径比一般为3~4。
最近建设的大直径焦炭塔的高径比一般为2~3。
美国焦炭塔的高径比一般为2~3。
焦炭塔的直径和高度受到水力除焦机械,设备设计、制造、运输、吊装等的限制,不宜太大和太高,美国目前运行的最大焦炭塔的直径为9.14米。
建议在装置处理量较大,采用一炉二塔使焦炭塔的直径和高度特别庞大时,采用缩短生焦时间或二炉四塔或三炉六塔更为适宜,不能盲目的追求设备大型化。
2.2塔体材料的选择
焦炭塔的材质选择应考虑焦化原料性质、塔内操作条件、焦炭塔的结构尺寸、装置的建设投资。
90年代以前,国内设计的焦炭塔的材质大部分为20g,因原料中硫含量不高,设计的温度及压力较低,焦炭塔的直径较小。
通过近三十年的使用经验表明,该材质基本满足生产要求,但也出现了不少的问题,主要表现在由于其耐热性能差,使用一段时间出现塔体裂纹、鼓包和变形,给生产带来不安全因素。
根据最新材料选择标准,焦炭塔的材质应选用20R。
目前针对小直径焦炭塔,并且原料油中含硫量低,建设投资不高的情况下,仍可采用20R作为焦炭塔的材料。
采用碳钢材料,设计温度不能高于375℃,实际上焦化原料进焦炭塔的温度为485~495℃,由于生成的焦炭积聚于塔壁,起到了隔热作用,实际测量焦炭塔塔体的最高温度不高于475℃;设计压力一般低于0.3Mpa,设计腐蚀裕度不小于3mm,否则焦炭塔的壁厚太大,给焦炭塔的制造、热处理、施工安装带来一定的困难。
当焦炭塔的直径较大和原料中硫含量较高时,焦炭塔若采用碳钢材质,其塔体的厚度就会很厚,无论从使用性能、设备制造、施工安装、设备费用等方面均不利。
因此目前设计的大型化焦炭塔的材质均采用Cr-Mo钢。
国内近几年设计的焦炭塔的材质大都为15CrMoR。
美国自1980~1997年大量使用Cr-Mo钢,CrMo钢中经常用的是1Cr-1/2Mo,11/4Cr-1/2Mo和21/4Cr-1.0Mo,11/4Cr-1/2Mo钢和1Cr-1/2Mo钢相比,许用应力高、对缺口敏感性小、耐热性更好,但国内应用的还比较少。
美国Foster-wheeler公司为印度设计的直径29英尺的焦炭塔下部锥体采用21/2Cr-1.0Mo钢,上部采用11/4Cr-1/2Mo钢。
为提高焦炭塔的耐热腐蚀性,焦炭塔上部经常采用不锈钢复合板,复合层的厚度一般为3mm,复合层的材质为0Cr13Al或0Cr13,国内焦炭塔大部分采用0Cr13Al,据资料报导,0Cr13Al应限制在343℃以下使用,长期处于371~538℃会使其变脆,焦炭塔上部的温度为460℃左右,应采用0Cr13为好。
美国1980~1997年安装的焦炭塔大部分采用0Cr13作为复合层。
国内新设