生胶的塑炼工艺.docx
《生胶的塑炼工艺.docx》由会员分享,可在线阅读,更多相关《生胶的塑炼工艺.docx(9页珍藏版)》请在冰豆网上搜索。
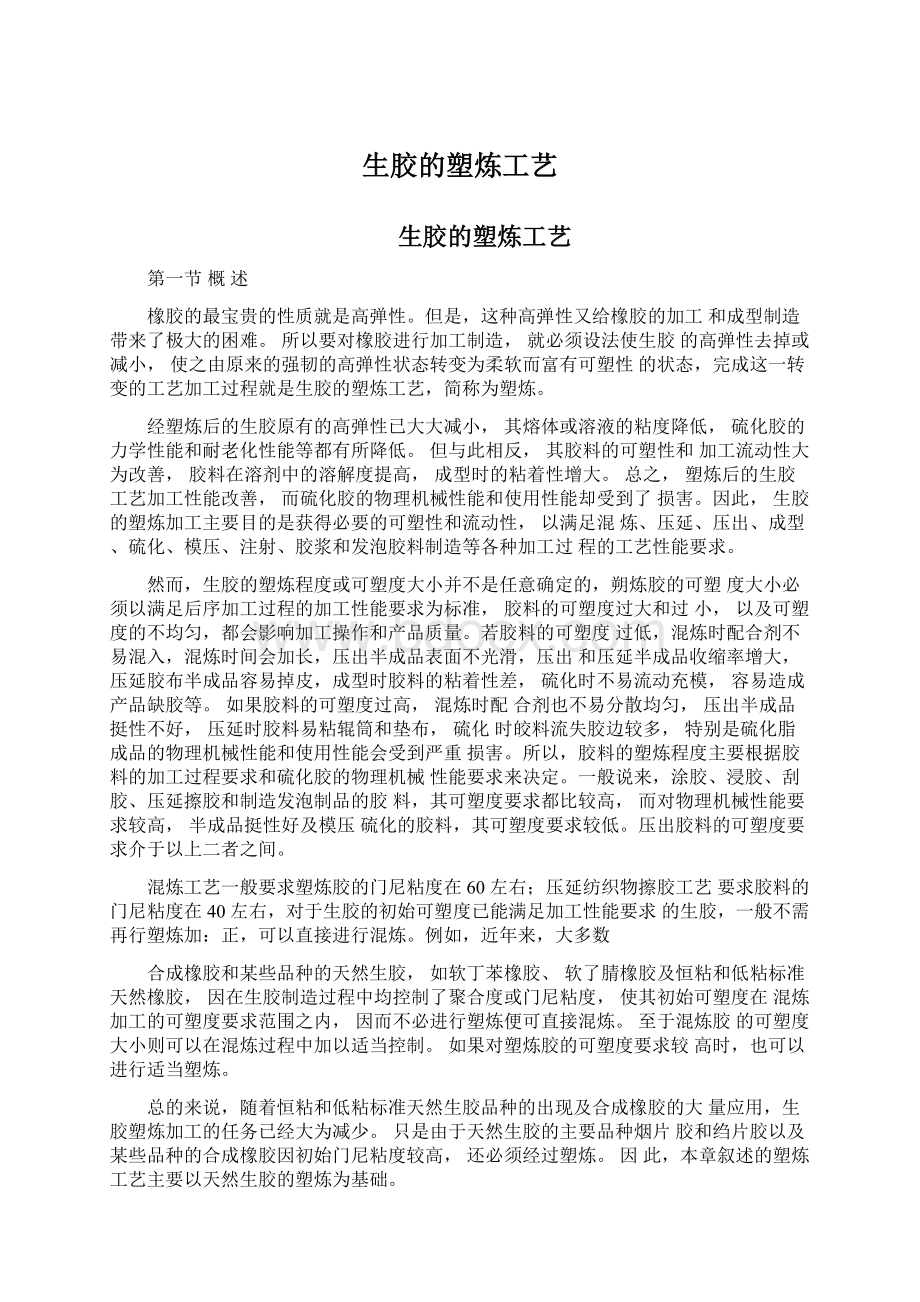
生胶的塑炼工艺
生胶的塑炼工艺
第一节概述
橡胶的最宝贵的性质就是高弹性。
但是,这种高弹性又给橡胶的加工和成型制造带来了极大的困难。
所以要对橡胶进行加工制造,就必须设法使生胶的高弹性去掉或减小,使之由原来的强韧的高弹性状态转变为柔软而富有可塑性的状态,完成这一转变的工艺加工过程就是生胶的塑炼工艺,简称为塑炼。
经塑炼后的生胶原有的高弹性已大大减小,其熔体或溶液的粘度降低,硫化胶的力学性能和耐老化性能等都有所降低。
但与此相反,其胶料的可塑性和加工流动性大为改善,胶料在溶剂中的溶解度提高,成型时的粘着性增大。
总之,塑炼后的生胶工艺加工性能改善,而硫化胶的物理机械性能和使用性能却受到了损害。
因此,生胶的塑炼加工主要目的是获得必要的可塑性和流动性,以满足混炼、压延、压出、成型、硫化、模压、注射、胶浆和发泡胶料制造等各种加工过程的工艺性能要求。
然而,生胶的塑炼程度或可塑度大小并不是任意确定的,朔炼胶的可塑度大小必须以满足后序加工过程的加工性能要求为标准,胶料的可塑度过大和过小,以及可塑度的不均匀,都会影响加工操作和产品质量。
若胶料的可塑度过低,混炼时配合剂不易混入,混炼时间会加长,压出半成品表面不光滑,压出和压延半成品收缩率增大,压延胶布半成品容易掉皮,成型时胶料的粘着性差,硫化时不易流动充模,容易造成产品缺胶等。
如果胶料的可塑度过高,混炼时配合剂也不易分散均匀,压出半成品挺性不好,压延时胶料易粘辊筒和垫布,硫化时皎料流失胶边较多,特别是硫化脂成品的物理机械性能和使用性能会受到严重损害。
所以,胶料的塑炼程度主要根据胶料的加工过程要求和硫化胶的物理机械性能要求来决定。
一般说来,涂胶、浸胶、刮胶、压延擦胶和制造发泡制品的胶料,其可塑度要求都比较高,而对物理机械性能要求较高,半成品挺性好及模压硫化的胶料,其可塑度要求较低。
压出胶料的可塑度要求介于以上二者之间。
混炼工艺一般要求塑炼胶的门尼粘度在60左右;压延纺织物擦胶工艺要求胶料的门尼粘度在40左右,对于生胶的初始可塑度已能满足加工性能要求的生胶,一般不需再行塑炼加:
正,可以直接进行混炼。
例如,近年来,大多数
合成橡胶和某些品种的天然生胶,如软丁苯橡胶、软了腈橡胶及恒粘和低粘标准天然橡胶,因在生胶制造过程中均控制了聚合度或门尼粘度,使其初始可塑度在混炼加工的可塑度要求范围之内,因而不必进行塑炼便可直接混炼。
至于混炼胶的可塑度大小则可以在混炼过程中加以适当控制。
如果对塑炼胶的可塑度要求较高时,也可以进行适当塑炼。
总的来说,随着恒粘和低粘标准天然生胶品种的出现及合成橡胶的大量应用,生胶塑炼加工的任务已经大为减少。
只是由于天然生胶的主要品种烟片胶和绉片胶以及某些品种的合成橡胶因初始门尼粘度较高,还必须经过塑炼。
因此,本章叙述的塑炼工艺主要以天然生胶的塑炼为基础。
第二节塑炼方法
一、生胶的增塑方法
增加生胶可塑性的方法依其塑化机理的不同可以分为以下几种:
1.物理增塑法利用低分子增塑剂加入生胶中增加生胶的可塑性的方法,称物理增塑法。
其基本原理就是利用低分子物质对橡胶的物理溶胀作用来减小大分子间的相互作用九从而降低了胶料的粘度,提高其可塑性和流动性。
但这种方法不能单独用来塑炼生胶,只能作为生胶塑炼过程中的一种辅助增塑方法,用于提高塑化效果。
2.化学增塑法利用某些化学物质对生胶大分子链的化学破坏作用来减小生胶的弹性和粘度,提高其可塑性和流动性,这种方法叫化学增塑法。
从生胶塑化机理看,化学增塑是比较有效的增塑方法,但与物理增塑法一样,也不能单独用来塑化生胶,只能作为其他机械塑化方法中的一种辅助增塑法使用。
3.机械增塑法利用机械的高剪切力作用使橡胶大分子链破坏降解而获得可塑性的方法叫机械增塑法或机械塑炼法。
这是目前生胶塑炼加工中使用最广泛而又行之有效的增塑方法,可以单独用于生胶塑炼加工,也可以与物理增塑法及化学增塑法配合使用,能进一步提高机械塑炼效果和生产效率。
机械塑炼法依据设备类型不同又分为三种,即开炼机塑炼法、密炼机塑炼法和螺杆式塑炼机塑炼法。
这都是生胶塑炼加工中最常用的塑炼方法。
由于设备结构与工作原理上的差别,在具体应用上又各有特点,应当依据具体情况适当选用。
另外,依据塑炼工艺条件的不同,机械塑炼方法又分为低温机械塑炼法和高温机械塑炼法。
密炼机塑炼法和螺杆塑炼机塑炼法的塑炼温度都在100℃以上,称为高温机械塑炼法;开炼机塑炼温度在100℃以下,故属于低温机械塑炼法。
第三节机械塑炼工艺
生胶在塑炼加工前需经一些准备加工,然后才能进行塑炼,塑炼后的胶料还要经过压片、冷却、停放和质量检查,质量合格后方能供下一步加工使用。
一、准备工艺
生胶塑炼前的准备加工包括烘胶、切胶、选胶和破胶等处理过程。
(一)烘胶
天然生胶经过长时间运输和贮存之后,常温下的粘度很高,容易硬化和产生结晶,尤其在气温较低的条件下,常会因结晶而硬化,使生胶难于切割和加工。
因此,应先进行加热软化,这就是烘胶。
烘胶的作用就是使硬度减小,结晶熔化,以便于进行切割和塑炼加工,同时还能使水分挥发掉。
烘胶一般在专用的烘胶房中进行。
烘胶房的下面和周边设有蒸汽加热器,生胶在烘房内按一定规则和顺序堆放在存放架上,但不得与加热器接触。
天然生胶室内的温度保持在50~60℃:
,加热时间依季节气候和地区的温度差异而不同。
在夏季高温季节,烘胶时间较短,一般为24—36h;在冬季低温条件下,加热时间一般为48~72h。
氯丁橡胶的烘胶温度要低些,一般为24~40℃,时间为4~6h。
烘胶温度不宜过高,否则会影响橡胶的物理机械性能。
烘胶必须达到胶块内外温均匀,否则影响塑炼质量和效率。
(二)切胶和选胶
烟片胶的包装方式都是ll0kg左右的大胶包。
为便于使用,必须首先切成小块。
生胶经加温后自烘胶房取出,在切胶前应先剥除胶包的外包皮或刷洗除去表面的砂粒其他杂物,然后才能进行切割。
切胶用单刃立式切胶机或多刃立式及卧式切胶机,具体依生产规模和生产条件而定。
生胶切割后,须经外观检查,并注明胶种。
若胶包中有不符等级品种质量规定的生,或有杂质、霉烂等现象,应加以挑选和分级处理,以便按质量等级适当选用。
(三)破胶
用开炼机进行塑炼时,为了提高生产效率和保证质量及设备安全,在塑炼前有的还要切好的胶块用破胶机进行破胶。
破胶时辊温在45C以下,辊距保持在2—3mm,让胶料逼辊距几次即可,一般2~3次:
破胶操作应注意避免被弹出的胶块打伤。
二、开炼机塑炼工艺
开炼机塑炼是应用最早的机械塑炼方法,至今还在使用。
与其他机械塑炼方法相比,炼机塑炼法自动化程度低、生产效率低、劳动强度大、操作危险性大,所以不适于现代化规模生产。
但由于开炼机塑炼温度低,塑炼胶可塑度均匀,胶料的耐老化性能和耐疲劳性较好,动态下生热性较小,机台容易清洗,变换胶种灵活,另外设备投资较节省,所以适塑炼胶质量要求高,胶料品种变化多和生产批量较小的加工。
(一)开炼机塑炼工艺方法
开炼机塑炼的操作方法主要有包辊塑炼法、薄通塑炼法和化学增塑塑炼法。
1.包辊塑炼法胶料通过辊距后,胶片包在前辊筒表面上,随着辊筒一起转动重新回到辊距的上方并再一次进入辊距,这样反复通过辊距受到捏炼,直至达到规定的可塑度要求为止,然后下片、冷却。
这就是一次完成的包辊
塑炼法,又叫一段塑炼法。
一段塑炼法的塑炼操作和胶料的停放管理比较简单方便,但塑炼时间长,效率低,最终能获得的可塑度也较低,不适用于塑炼胶可塑度要求较高的生咬塑炼。
分段塑炼法是先将胶料包辊塑炼一定时间,通常10~15min,然后下片、冷却和停放4一8h,再将停放后的胶料重新放到炼胶机上进行第二次包辊塑炼一定时间,并下片、冷却和停放。
这样反复塑炼数次,直至达到要求的可塑度为止。
通常分两段塑炼法和三段塑炼法即可。
具体依可塑度要求而定。
分段塑炼法胶料管理比较麻烦,所需胶料停放面积较大,但塑炼温度较低,塑炼效果较好,能达到任意的可塑度要求,适用于可塑度要求较高的生胶塑炼。
2.薄通塑炼法薄通塑炼的辊距在imm以下,胶料通过辊距后不包辊而直接落在接料盘上,等胶料全都通过辊距后,再将胶料返回到辊距上方重新通过辊距,这样反复数次,直至达到要求的可塑度为止。
具体依可塑度要求而定。
胶料的可塑度要求越高,需要通过辊距的次数也就越多。
薄通塑炼法胶料散热快,冷却效果较好,机械塑炼效果大,塑炼胶可塑度均匀,质量高,能达到任意的塑炼程度,是开炼机塑炼中最普遍采用的和行之有效的塑炼方法。
适用于各种生胶的塑炼加工,也可采用分段方法。
3.化学增塑塑炼法开炼机塑炼时,可采用化学塑解剂增加机械塑炼效果,提高塑炼生产效率并节约能耗。
适用的化学塑解剂类型为游离基接受体型及混合型化学塑解剂,如国产的化学塑解剂SJ—103及进口的RenacitV等,化学塑解剂应以母胶形式使用,并应适当提高开炼机的辊温。
(二)开炼机塑炼的影响因素
影响开炼机塑炼的因素主要有容量、辊距、辊速与速比、辊温、塑炼时间、化学塑解剂等。
1.容量容量就是一次炼胶的胶料容积。
塑炼容量的大小取决于设备规格与生胶种类,容量过大,辊距上方的积存胶数量过多,不仅使散热困难,胶温升高,降低塑炼效果,而且使单位时间内胶料通过辊距的次数减少,生产效率下降,同时还会加大操作的劳动强度;容量过小也会降低塑炼的生产效率。
合理的容量应根据以下经验公式计算:
Q=K·D·L
式中Q—塑炼容量,L;
K—经验系数,一般取值范围为0.0065~0.0085,L/cm2;
D——前辊简直径,cm;
L——辊筒工作部分长度,cm。
合成胶塑炼时生热量多,升温快,应适当减小容量,如丁腈橡胶塑炼容量一般比天然橡胶低20%~25%。
2.辊距辊速和速比一定时,辊距越小,机械塑炼效果越大,同时因胶片减薄,冷却效果改善又进一步提高了机械塑炼效果。
例如,天然生胶开炼机塑炼时的辊距从4mm减至0.5mm时,胶料的门尼粘度在同样薄通次数内迅速降低。
由此可见,采用薄通塑炼法是比较合理的。
这种方法对合成橡胶塑炼也很有效。
例如难以塑炼的丁腈橡胶等只有采用薄通塑炼法才能获得较好的塑炼效果。
3.辊速和速比辊距一定,提高开炼机辊筒的转速或速比都会增大胶料的机械剪切作用,从而提高机械塑炼效果,因此,开炼机塑炼时的速比较大,一般在1.15~1.27范围内。
但速比过大又会使生胶升温过快,反过来又会降低机械的塑炼效果,并加大塑炼过程的能耗;速比过小也会降低机械塑炼效果和生产效率。
4.辊温开炼机塑炼温度用辊筒的表面温度表示。
辊温低,塑炼效果好。
实验证明,塑炼胶的可塑度与辊温的平方根成反比关系。
由于胶料塑炼时的摩擦生热会使辊温升高而降低机械塑炼效果,所以在塑炼过程中必须不断向辊筒内腔通入冷却水冷却辊筒,使辊温保持在较低的温度范围内。
但若辊温过低又容易造成设备超负荷而受到损害天然橡胶通常控制前辊温度在45~55℃,后辊
温度在40~50℃为宜,采用分段塑炼法和薄通塑炼法有利于辊温的控制
5.塑炼时间在塑炼过程的最初10—15min,胶料的门尼粘度迅速降低,此后则渐趋缓慢。
这是由于塑炼过程中胶料因生热软化,分子链之间易产生相对滑移,降低了机械作用为的效果所致。
所以要获得较大的可塑度,最好的办法就是分段进行塑炼。
每次塑炼的时间在20min以内,不仅塑炼效率高,最终达到的可塑