整理重大危险源安全培训教育记录附件.docx
《整理重大危险源安全培训教育记录附件.docx》由会员分享,可在线阅读,更多相关《整理重大危险源安全培训教育记录附件.docx(17页珍藏版)》请在冰豆网上搜索。
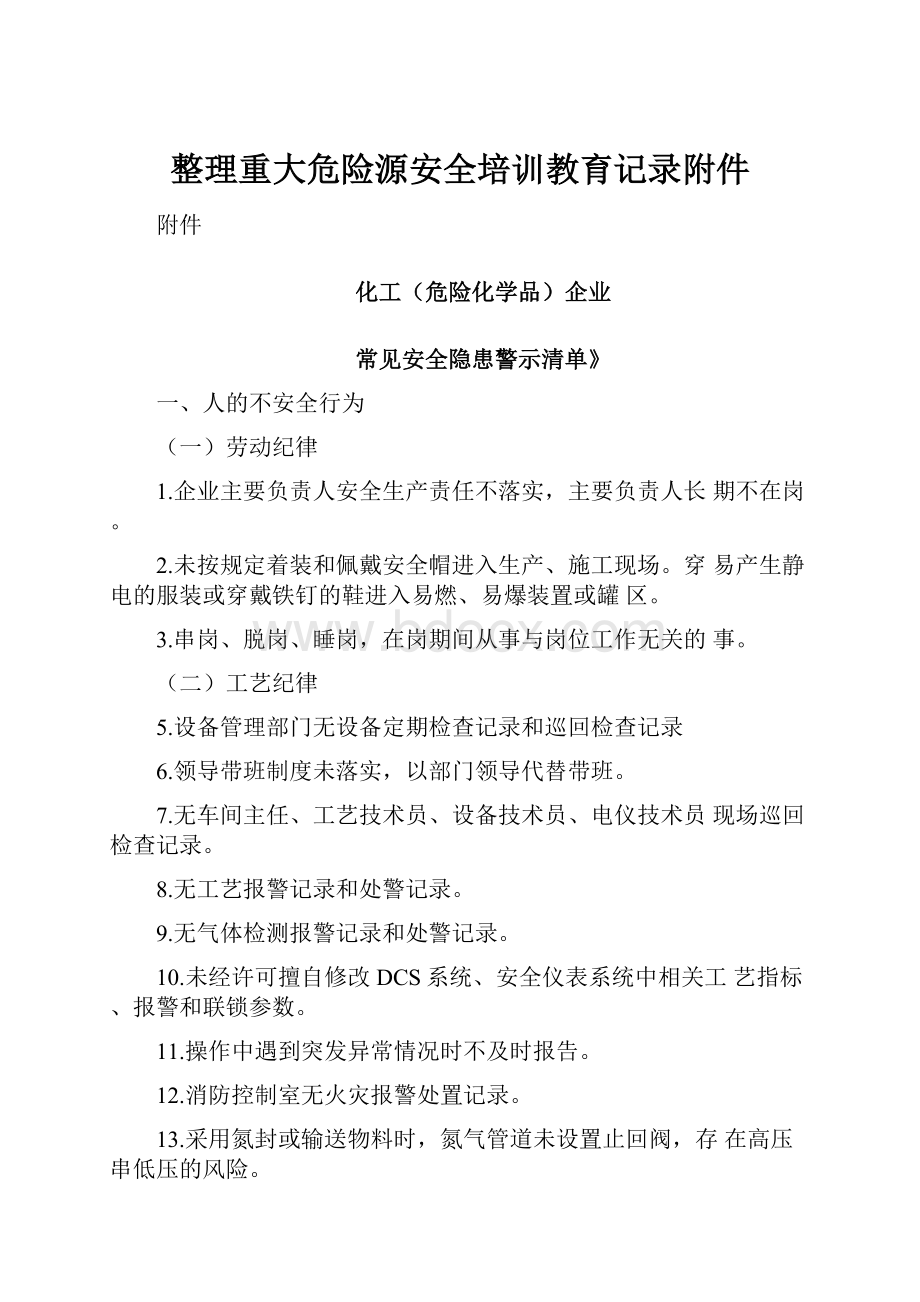
整理重大危险源安全培训教育记录附件
附件
化工(危险化学品)企业
常见安全隐患警示清单》
一、人的不安全行为
(一)劳动纪律
1.企业主要负责人安全生产责任不落实,主要负责人长期不在岗。
2.未按规定着装和佩戴安全帽进入生产、施工现场。
穿易产生静电的服装或穿戴铁钉的鞋进入易燃、易爆装置或罐区。
3.串岗、脱岗、睡岗,在岗期间从事与岗位工作无关的事。
(二)工艺纪律
5.设备管理部门无设备定期检查记录和巡回检查记录
6.领导带班制度未落实,以部门领导代替带班。
7.无车间主任、工艺技术员、设备技术员、电仪技术员现场巡回检查记录。
8.无工艺报警记录和处警记录。
9.无气体检测报警记录和处警记录。
10.未经许可擅自修改DCS系统、安全仪表系统中相关工艺指标、报警和联锁参数。
11.操作中遇到突发异常情况时不及时报告。
12.消防控制室无火灾报警处置记录。
13.采用氮封或输送物料时,氮气管道未设置止回阀,存在高压串低压的风险。
14.使用压缩空气进行易燃易爆物料的加料、压料操作。
16.现场盲板未编号和挂牌
(三)其他纪律
17.爆炸危险区使用非防爆工具、非防爆照明,使用手机等非防爆通讯设备等。
18.擅自停用可燃、有毒、火灾声光报警系统和安全联锁系统。
19.擅自关闭各类报警声音。
20.应急救援器材柜清单与柜内物品不符,没有固定检测日期,无检查标准。
21.消火栓、消防水炮无编号,消火栓保养、维护不够。
22.泡沫液储罐没有张贴泡沫液型号、批次等标签。
23.现场未设置或者缺少禁止、警告、指令、提示等安全标志。
24.未按国家标准分区分类储存危险化学品,超量、超品种储存危险化学品,相互禁配物质混放混存。
25.仓库现场没有危险化学品的出入库台账。
危险化学品仓库物品存放时,顶距、灯距、墙距、柱距、垛距“五距”不符合要求。
26.电气控制开关未挂标识牌;
27.未对所有岗位人员进行安全生产教育培训,安全教育考试卷未批改或批改不认真,随意给分。
28.管理人员违章指挥、强令冒险作业。
29.未为从业人员配备适用有效的个体防护用品。
30.未按照变更管理制度开展变更管理,变更后未对操作规程、图纸资料进行修改,未对制度、人员等进行变更管理;变更审批表缺少风险分析;变更审批单审批签字不全,工艺变更未对相关员工开展相应的培训。
31.现场操作人员不能正确熟练使用应急防护装备、器材
32.规章制度、岗位安全责任制、操作规程无企业负责人签发记录或签发文件,安全管理制度、操作规程未发放至岗位。
33.企业培训档案记录不全。
从业人员培训记录,培训时
间、内容、学时、参加人员等情况不全。
34.承包商管理存在疏漏,无承包商人员培训记录。
无外来人员入厂教育等方面的台账或记录。
35.人员变动未及时更新生产安全事故应急预案。
36.企业人员安全意识淡薄,人员不熟悉具体的岗位风险;不掌握防护知识,对近期发生生产安全事故不了解。
(四)特殊作业
37.同一作业涉及动火、进入受限空间、盲板抽堵、高处作业、吊装、临时用电、动土、断路中的两种或两种以上时,未按规定同时办理相应的作业审批手续。
38.特殊作业危险因素辨识不全。
39.特殊作业安全作业证有缺漏项,超过规定有效期,签批人不符合要求,签批时间未填写到分钟,提前审批作业许可证。
行安全分析。
41.动火和进入受限空间未按要求定期进行安全分析。
42.动火和进入受限空间作业票未注明检测危害物质种类和浓度。
43.未履行抽堵盲板作业票。
44.未按规定办理动火、进入受限空间等特殊作业许可证
45.动火、进入受限空间作业部位与生产系统采用关闭阀门实施隔离、隔绝,未采取加装盲板或断开一段管道的隔离措施。
46.采样分析部位与动火作业部位不一致,采样检测点没有代表性。
47.受限空间未设置安全警示或采取硬隔离措施。
48.动火、进入受限空间作业安全措施未确认落实或安全措施由同一人确认签字。
49.动火作业未做到“一点(处)一证一人”,未经许可,
擅自变更作业范围。
50.动火、进入受限空间作业现场未设专人监护。
51.动火、进入受限空间等特殊作业未进行完工验收签字
52.动火、进入受限空间等特殊作业安全作业证上填写的作业人员与现场实际作业人员不一致。
53.氧气、乙炔气瓶无防震圈、瓶帽等安全附件,乙炔气瓶未安装回火器。
氧气、乙炔气管道老化、皲裂。
54.使用未安装漏电保护器装置的电气设备、电动工具。
55.釜内检修时,没有切断电源并拴挂“有人检修、禁止合闸”的警示牌。
56.高处作业未系安全带,安全带未做到“高挂低用”。
57.火灾爆炸危险场所未使用相应防爆等级的电源及电气元件。
58.起重机械吊钩缺少防钢丝绳脱落装置
59.吊装现场未设置安全警戒标志或拉设警戒绳,没有专人监护。
60.特殊时段特殊作业审批未升级管理。
二、物的不安全状态
(一)工艺专业
60.操作规程设定参数、工艺卡片、工艺记录和控制参数不一致。
62.工艺控制联锁值、报警值设定错误,如报警值设定高于联锁值。
63.温度、压力、液位等超控制指标运行。
64内浮顶罐低液位报警或联锁设定值低于浮盘支撑的高度。
65.
重大危险源未配备温度、压力、液位、流量、组份等信息的不间断采集和监测系统,不具备信息远传、连续记
66.反应设备、储罐等未按规定要求设置温度、压力、液
位现场指示。
67.全压力式液化烃储罐未设置防泄漏注水措施,注水压力、注水方式不符合要求。
68.液体、低热值可燃气体、毒性为极度和高度危害的可燃气体、惰性气体、酸性气体及其他腐蚀性气体未设独立的排放系统或处理排放系统。
69.装置可能引起火灾、爆炸等严重事故的部位未设置超温、超压等检测仪表、声光报警、泄压设施和安全联锁装置等设施。
70.火炬系统没有可靠的点火系统及燃料气源,未设置可靠的防回火设施,火炬气的分液、排凝未投入使用。
71.控制室没有工艺卡片或工艺卡片未定期修订。
72.摘除和恢复联锁没有审批手续,未按工作票执行,摘除期间未采取安全措施。
73.电气线路的电缆或钢管在穿过墙或楼板处的孔洞,未采用非燃烧性材料封堵。
74.甲、乙、丙类液体仓库未设置防止液体流散的设施,
遇湿会发生燃烧爆炸的物品仓库未采取防止水浸渍的措施。
75.站内无缓冲罐时,在距汽车装卸车鹤位10m以外的装
卸管道上未设置便于操作的紧急切断阀。
76.关键设备报警值、联锁值等控制指标不全。
77.未对消防水池设置高低液位报警,现场未设置就地水位显示仪表。
78.有氮气保护设施的储罐,氮封系统不完好或未投用,没有事故泄压设备。
(二)设备专业
79.安全阀、爆破片等安全附件未正常投用,安全阀、爆破片等手阀未常开并铅封。
80.特种设备、安全阀、压力表、可燃气体报警器、雷电
防护装置、防静电设施等未在法定检测有效期内使用
81.可燃气体直接向大气排放的排气筒、放空管的高度不
符合规范要求。
82.可燃气体压缩机、液化烃、可燃液体泵使用皮带传动。
83.转动设备的转动部位没有可靠的安全防护装置。
84.配电室未落实防小动物进入的措施。
85.在设备和管线的排放口、采样口等排放部位,未采取加装盲板、丝堵、管帽、双阀等措施。
86.生产装置、储存设施存在跑冒滴漏现象。
87.储罐的进出管道未采用柔性连接,罐区防火堤有孔洞。
88.防爆电气设备设施固定螺栓未全部上齐。
89.操作、巡检等平台、护栏、楼梯等有缺损或腐蚀严重。
90.爆炸危险场所未按国家标准安装使用防爆电气设备。
91.可燃和有毒气体检测报警仪不具有就地声光报警功能。
92.手提式和推车式灭火器均是露天摆放,无相应的防雨
防晒等保护措施,部分灭火器永久性标志已腐蚀不清。
93.储罐水喷淋系统,部分喷嘴堵塞
94.爆炸危险区内电缆穿线管防爆封堵不严。
95.生产装置现场钢结构防火涂层多处脱落,不能满足防火要求。
96.可燃气体报警器探头设置不足,达不到全覆盖。
97.厂房、仓库无明显的安全出口标识。
98.灭火器未设置检查标签。
99.跨越道路的管廊缺少限高标识。
100.室外地下消火栓积水,应急时无法正常使用。
101.危险化学品重大危险源视频监控摄像没有全覆盖。
102.用电设备和电气线路的周围没有留有足够的安全通道和工作空间,或堆放易燃、易爆和腐蚀性物品。
103.火灾爆炸危险区域内电缆未采取阻燃措施,电缆沟防窜油汽、防腐蚀、防水措施不落实。
104.管道物料及流向、标识不清。
105.盛装甲、乙类液体的容器放在室外时未设防晒降温设施。
(三)仪表专业
106.未对需要配置安全仪表系统的化工装置开展功能安全评估。
107.未开展仪表检维修后投用前的回路测试。
108.仪表系统故障或异常工况没有及时解决。
109.工程师站控制系统、安全仪表系统修改权限低或不需修改权限。
110.涉及可燃和有毒气体泄漏场所未按国家标准安装泄漏检测报警仪。
111.可燃、有毒气体检测报警仪一级、二级报警值设定错误。
112.气体检测报警仪未采用UPS供电。
113.未对控制系统组态变更履行变更审批程序
114.未对远传仪表进行定期核对和校验。
115.无控制系统组态变更的详细信息记录,如缺少联锁逻辑、报警设定等信息。
116.未开展防爆电气设备专项检查,未配备防爆电工。
117.固定式可燃和有毒气体检测报警仪检测报警信号没有发送至有操作人员常驻的控制室、现场操作室。
118.现场压力表、温度表、液位计等未标注上下限。
压力表量程选取错误。
(四)设计专业
119.企业现场布置与总平面布置图不一致。
120.未经正规设计或履行变更程序随意增加设备、设施、建构筑物。
121.企业生产及储存设施总平面布置防火间距不满足规范要求。
122.企业设施与相邻工厂或设施的防火间距不满足规范
要求。
123.控制室或机柜间面向具有火灾、爆炸危险性装置一侧不满足国家标准关于防火防爆的要求。
124.甲、乙类火灾危险性装置内设有办公室、操作室、固定操作岗位或休息室。
125.涉及“两重点一重大”的生产装置、储存设施外部安全防护距离不符合国家标准要求。
126.未按规范要求对承重钢结构采取耐火保护措施。
127.布置在爆炸危险区的在线分析仪表间设备为非防爆型时,在线分析仪表间未采取正压通风。
128.火灾危险性类别不同的储罐设在同一罐组,常压储罐与压力储罐布置在同一罐组。
三、管理缺陷
(一)合法合规性
129.新建、改建、扩建生产、储存危险化学品的建设项
目未通过安全审查进行建设。
130.危险化学品生产企业未取得安全生产许可证。
安全生产许可证超过有效期内,许可范围与企业现状不一致。
131.安全分管负责人和安全管理人员未取得合格证,专职安全管理人员不具备化工或安全工程类专业学历。
注册安全工程师配备数量不足。
132.特种作业人员、特种设备作业人员未持证上岗。
133.在用或新增压力容器未在规定的期限内取得使用证
134.未按规定编制危险化学品安全技术说明书,未在包装上粘贴、悬挂与化学品相符的安全标签。
135.工艺、设备等变更未进行风险评估和履行变更程序
136.未开展五懂五会五能、五个必须落实培训教育。
(二)制度、规程
137.安全管理规定的内容陈旧,其与企业实际情况不符
138.责任制与企业组织机构不匹配,主要负责人安全生
产责任制不符合法定职责要求。
139.特殊作业制度未规定审批权限。
140.变更管理制度中无变更后及时修订操作规程、进行变更验收的相关要求。
141.管理规定中未规定修改、废止程序和职责。
142.操作规程中缺少关键设备设施高高低低报警值、联锁值等工艺控制指标。
143.安全生产事故报告制度不符合《生产安全事故报告和调查处理条例》的规定。
144.未执行每年对操作规程适用性和有效性进行评审的规定。
145.未将涉险事故(如生产事故征兆、非计划停工、异常工况、泄漏等)安全事件纳入事故管理。
146.承包商管理缺失。
档案、台帐不全,企业内设机构
对承包商的安全管理职责界定不清,与部分承包商未签订安全生产协议,未存档部分承包商的单位和人员资质材料,向承包商技术交底无书面记录。
147.应急演练方案不完善。
演练计划和演练总结都没有体现应急救援的具体流程,忽略物料切断步骤。
应急演练脚本缺少对泄漏气体监测,个体防护用品配备等重要环节。
未对演练存在的问题制定针对性的整改措施并进行闭环管理。
148.装置开停工未编制开停工方案。
149.未建立设备检维修、巡回检查、防腐保温、设备润滑等设备管理制度。
150.剧毒化学品、易制爆化学品未建立“双人验收、双人保管、双人发货、双把锁、双本账”等“五双”制度。
151.制度、规程不切实际,没有可操作性。
152.未制定实施动火、进入受限空间等特殊作业管理制
度。
153.未制定实施危险化学品重大危险源安全管理制度。
154.未制定实施变更管理制度。
155.未制定仪表自动化控制系统、安全仪表系统安全管
理制度。
156.入场教育制度不落实或不执行不严格。
157.安全承诺公告制度不执行或执行不严格。
(三)风险评估与隐患治理
158.风险管理不到位,企业风险辨识不充分,未建立风险管理清单,实施分级管理。
159.企业安全检查和隐患排查,检查结果全部为正常;
160.排查清单内容不具体,不切合本厂实际,隐患排查台账没有做到五落实。
安全检查无参加人员签字、无检查方案、检查内容、检查责任分工等。
161.主要负责人未每天实行风险研判和承诺公告。
162.未按规定要求开展危险与可操作性分析(HAZOP,
HAZOP分析提出的对策建议未落实整改。
163.精细化工企业未按规范性文件要求开展反应安全风
险评估。
164.工艺技术来源不可靠,没有合规的技术转让合同或安全可靠性论证。
(四)计划与台账
165.未制定实施年度安全生产教育培训计划。
166.未制定实施年度应急预案演练计划。
167.未制定实施年度设备检维修计划。
168.未建立安全生产教育和培训档案。
169.未建立班组安全活动记录。
170.未建立压力容器、压力管道台账和技术档案。
171.未建立安全附件台账、爆破片更换记录。
172.未建立仪表自动化控制系统、安全仪表系统有关安全联锁管理台账。
173.未建立承包商安全管理档案和年度评价记录。
附件
安全生产条件评价表
项目
评价内容
评价结果
规戈V
布局
符合国家产业政策
符合当地县级以上(含县级)人民政府的规划、布局
新设立企业在省级以上化工元'化工集中区
总体布局符合国冢相天标准、规范的要求
危险化学品生产装置或者储存危险化学品数量构成重大危险源的储存设施,与规定的八类场所、设施、区域的距离符合有关法律、法规、规章和国家标准或者行业标准的规
定建、改建、扩建和在役生产、储存装置的外部安全防护距离符合个人可接受风险标准和社会可接受风险标准
企业厂房、作业场所储存设施
和安全设施、设备、工艺
建设项目由具备国家规定资质的单位设计、制造和施工建设
设工生产装置由具备相应资质的专业设计单位设计经正规设计在役化工生产装置已进行安全设计诊断
无国家明令淘汰、禁止使用和危及安全生产的工艺、设备
生产工艺安全可靠,新开发的化工工艺经过风险评估,经过小试、中试、工业化试验,经过安全可靠性论证
涉及危险化工工艺、重点监管危险化学品的装置装设了自动化控制系统
涉及危险化工工艺的大型化工装置装设了紧急停车系统
涉及易燃易爆、有毒有害气体化学品的场所装设了易燃易爆、有毒有害介质泄漏报警等安全设施
在厂区内设置二道门并严格管理,做到生产区与非生产区分开设置,符合国家标准或者行业标准规定的距离
危险化学品生产装置和储存设施之间及其与建(构)筑物之间的距离符合有关标准规范的规定
生产作业场所配备了相应的职业危害防护设施,为从业人员配备了符合国家标准或行业标准的劳动防护用品
建设项目安全审查按规定程序和审查权限经安监部门审查通过,新建企业或有建设项目的企业,建设项目验收的组织及验收过程符合苏安监[2015]12号文要求
安全教育
和
培训
主要负责人、分管安全负责人和安全生产管理人员取得了安监部门颁发的安全合格证,按照《江苏安全生产条例》和苏政办发[2015]81号文要求,设立安全总监
主要负责人、分管安全负责人、分管技术负责人、专职安全管理人员符合规定的专业、学历要求
特种作业人员经相关部门培训合格并取得特种作业操作
证。
新招的危险工艺操作冈位人员,独立上冈的已满头习
项目
评价内容
评价结果
其他从业人贝按规疋进行了女全教育和培训并考核合格
项目
评价内容
评价结果
安全
管理
设置了安全生产管理机构并配备了规疋数量的专职安全生产管理人员
建立了全员安全生产责任制,并与职务、岗位相匹配
以文件形式发布了至少包括《实施办法》第十四条规定的十九项制度
有针对性地编制了岗位操作安全规程
按规定提取和使用安全生产费用
按规定为从业人员缴纳了工伤保险费和安全生产责任保险费
费时进行危险化学品登记,并为用户提供了化学品安全技术说明书和化学品安全标签
按照《化学品生产单位特殊作业安全规范》和苏安监
〔2016〕132号文要求修订并严格执行动火、受限空间作
重大
危险源
业审《制险化学品重大危险源辨识》对重大危险源进行了辨识和安全评估、分级
按规定建立了重大危险源安全监测监控体系和控制措施
定期对重大危险源的安全设施和安全监测监控系统进行了检测、检验
重大危险源中关键装置、重点部位明确了责任人或责任机构,并定期进行安全检查
重大危险源所在场所设置了明显的安全警示标志
重大危险源的应急管理、登记建档和备案符合规定要求
重大危险源配备温度、压力、液位、流量、组份等信息的不间断采集和监测系统以及可燃气体和有毒有害气体泄漏检测报警装置,并具备信息远传、连续记录、事故预警、信息存储等功能;一级或者二级重大危险源,具备紧急停车功能;储存剧毒物质的场所或者设施,设置视频监控系
统重大危险源中的毒性气体、剧毒液体和易燃气体等重点设施,设置紧急切断装置;毒性气体的设施,设置泄漏物紧急处置装置。
涉及毒性气体、液化气体、剧毒液体的一级或者一级重大危险源配备独立的安全仪表系统
应急
管理
按照国家有关规定编制、修订了危险化学品事故应急救援预案并报安监部门备案
建立了应急救援组织或者明确了应急救援人员
配备必要的应急救援器材、设备设施,并定期进行检测、检验和维护保养
生产、储存和使用有毒有害气体的企业,配备了符合规定要求的防护装备和设施
定期组织从业人员开展事故应急救援演练
安全
评价
按照《危险化学品安全管理条例》(国务院令第591号)
规疋委托具备国豕规疋资质的安全评价机构疋期进行了安全评价,并对安全评价报告进行了确认
对安全评价报告中提出的整改意见完成了整改并经评价机构复查确认
整理丨尼克
本文档信息来自于网络,如您发现内容不准确或不完善,欢迎您联系我修正;如您发现内容涉嫌侵权,请与我们联系,我们将按照相关法律规定及时处理。