SPC稳异判别.docx
《SPC稳异判别.docx》由会员分享,可在线阅读,更多相关《SPC稳异判别.docx(10页珍藏版)》请在冰豆网上搜索。
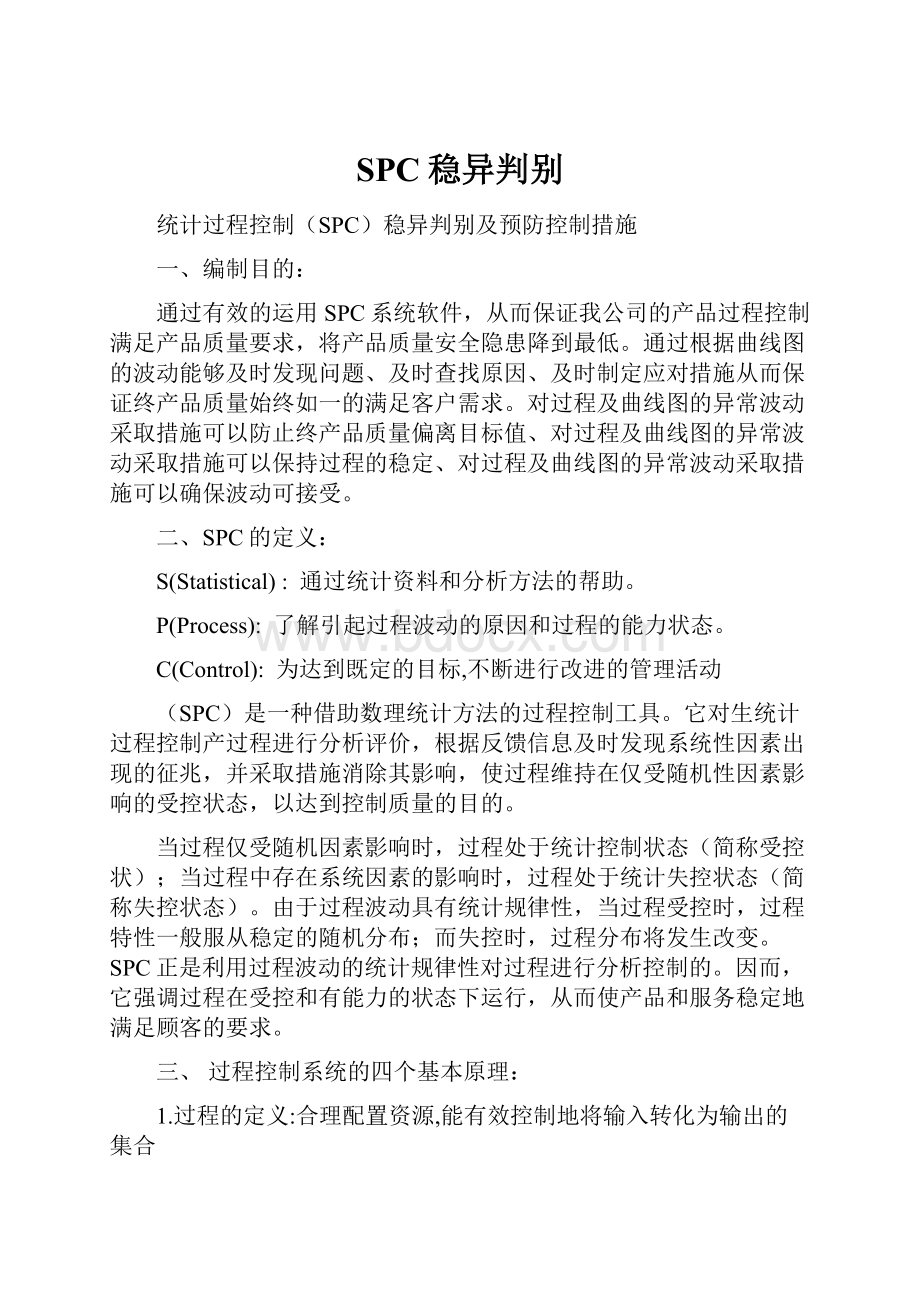
SPC稳异判别
统计过程控制(SPC)稳异判别及预防控制措施
一、编制目的:
通过有效的运用SPC系统软件,从而保证我公司的产品过程控制满足产品质量要求,将产品质量安全隐患降到最低。
通过根据曲线图的波动能够及时发现问题、及时查找原因、及时制定应对措施从而保证终产品质量始终如一的满足客户需求。
对过程及曲线图的异常波动采取措施可以防止终产品质量偏离目标值、对过程及曲线图的异常波动采取措施可以保持过程的稳定、对过程及曲线图的异常波动采取措施可以确保波动可接受。
二、SPC的定义:
S(Statistical):
通过统计资料和分析方法的帮助。
P(Process):
了解引起过程波动的原因和过程的能力状态。
C(Control):
为达到既定的目标,不断进行改进的管理活动
(SPC)是一种借助数理统计方法的过程控制工具。
它对生统计过程控制产过程进行分析评价,根据反馈信息及时发现系统性因素出现的征兆,并采取措施消除其影响,使过程维持在仅受随机性因素影响的受控状态,以达到控制质量的目的。
当过程仅受随机因素影响时,过程处于统计控制状态(简称受控状);当过程中存在系统因素的影响时,过程处于统计失控状态(简称失控状态)。
由于过程波动具有统计规律性,当过程受控时,过程特性一般服从稳定的随机分布;而失控时,过程分布将发生改变。
SPC正是利用过程波动的统计规律性对过程进行分析控制的。
因而,它强调过程在受控和有能力的状态下运行,从而使产品和服务稳定地满足顾客的要求。
三、过程控制系统的四个基本原理:
1.过程的定义:
合理配置资源,能有效控制地将输入转化为输出的集合
2.过程性能的体现:
取决于供需双方的沟通,过程的设计和实施方式
过程的运作和管理方式
原理二.性能的信息
过程的实时信息由过程输出直接获得,实时信息是揭示过程的客观运行实况,过程的有用信息由过程本质分析获得,有用信息是显示过程实际与目标差异,过程的特征信息由过程变化波动获得,特征信息是采取改善输出措施的依据。
四、对过程波动采取措施的重要性(包括原料气分析、产品过程控制分析、空车入厂分析、产品批次分析)
1、对过程及曲线图的异常波动采取措施可以防止偏离目标值
2、对过程及曲线图的异常波动采取措施可以保持过程的稳定
3、对过程及曲线图的异常波动采取措施可以确保波动可接受
五、只对终产品的波动采取措施的不足(成品出厂检验分析)
1、仅对终产品的波动采取措施只能是临时的管理方法
2、仅对终产品的波动采取措施不能改善产品质量特性
3、仅对终产品的波动采取措施不能改善过程的稳定性
六、波动形成的原因分析
1、波动的形成
过程波动:
即使是相同的研究对象之间,也都存在着差异.任何一个过程,都会受到外界客观条件的影响.对象或过程是动态的,对过程研究也是动态的,受影响有偶然的,短期的;也有必然的,长期的.
普通波动:
由于研究对象其存在固有的特征而产生的差异
特殊波动:
由于过程中不确定因素短期作用而产生的差异
系统波动:
过程中存在的有一定规律长期作用所致的差异
正常波动:
是由普通(偶然)原因造成的。
如操作方法的微小变动,机床的微小振动,刀具的正常磨损,夹具的微小松动,材质上的微量差异等。
正常波动引起工序质量微小变化,难以查明或难以消除。
它不能被操作工人控制,只能由技术、管理人员控制在公差范围内。
异常波动(特殊波动及系统波动):
是由特殊(异常)原因造成的。
如原材料不合格,设备出现故障,工夹具不良,操作者不熟练等。
异常波动造成的波动较大,容易发现,应该由操作人员发现并纠正。
2、波动原因
普通原因:
指的是造成随着时间推移具有稳定的且可重复的分布过程中的许多波动的原因,我们称之为:
“处于统计控制状态”、“受统计控制”,或有时间称“受控”,普通原因表现为一个稳定系統的偶然原因。
只有波动的普通原因存在且不改变时,过程的输出才可以预测。
特殊原因:
指的是造成不是始终作用于过程的波动的原因,即当它们出现时将造成(整个)过程的分布改变。
除非所有的特殊原因都被查找出来并且采取了措施,否則它们将继续用不可预测的方式来影响过程的输出。
如果系统內存在波动的特殊原因,随时间的推移,过程的输出将不稳定。
七、过程波动原因分析及预防控制措施:
1、原因分析:
如果过程保持统计控制状态,并且其分布的位置,离散度、起始点都不发生变化则过程表现为服从可预测分布,那么其性能是可预测的.连续作业的工程规范符合的比例是可以估算的,过程控制是管理者所关注的焦点,旨在建立起一个稳定的作业体系
过程控制波动原因分析应遵循以下步骤进行:
本过程应做些什么(脱硫工序)→会出现什么错误→能否达到统计控制状态(实现SPC控制)→确定能力(分析仪器及人员)→维护过程(按要求取样分析化验)→监控过程性能(根据曲线图的波动情况进行分析)→查找偏差的特殊原因并采取措施达到先进管理水平→改进过程、改变过程从而更好
2、预防及控制措施:
→理解普通原因波动減少普通原因波动→Plan策划----根据管理中的问题或更高的质量要求,建立必要的目标(P)和达成目标的方法(P)→具体为五步骤:
找出所存在问题→调查问题现状→分析问题原因→找出主要原因→针对原因制定对策→Do实施-----按照制定的对策进行教育培训(Do)和实施(Do)过程的步骤→Check检查----对查核实施结果的步骤→Action处置-----采取措施处置异常情况,以持续改进过程业绩
具体为六步骤:
制定巩固成果的措施→防止问题再发生→提出遗留问题→提出下一步打算→列出新课题→调查问题现状进入新一轮PDCA这就是一个循环、四个阶段、十三个步骤。
八、SPC控制曲线图判异细则及预防控制措施
SPC控制软件的判异分为以下8类异常:
第1类异常:
1个点落于3σ区外第2类异常:
连续9个点在中心线同侧第3类异常:
连续6个点递增或递减第4类异常:
连续14个点上下交替第5类异常:
连续3个点中有2个点落于同侧2σ区外第6类异常:
连续5个点中有4个点落于同侧σ区外第7类异常:
连续15个点落于σ区内第8类异常:
连续8个点落于σ区外
控制措施:
当分析人员应用SPC软件进行控制时,软件提示有以上任意原因是分析人员应首先寻找并纠正特殊原因。
当从数据中已发现了失控的情況时,则必须研究操作过程以便确定其原因。
然后纠正该原因并尽可能防止其再发生。
由于特殊原因是通过控制图发现的,要求对操作进行分析,并且希望操作者或现场检验员有能力发现变差原因并纠正。
可利用诸如排列图和因果分析图等解決定问题数据。
然后重新计算控制限,当进行初始过程研究或对过程能力重新评价时,应重新计算试验控制限,以更排除某些控制时期的影响,这些时期中控制状态受到特殊原因的影响,但已被纠正。
一旦历史数据表明一致性均在试验的控制限內,则可将控制限延伸到将来的时期。
它们便变成了操作控制限,当将来的数据收集记录了后,就对照它来评价。
最后绘制图分析修改后的过程控制图,当对过程采取了系统的措施后,其效果应在控制图上明显地反应出来;控制图成为验证措施有效性的一种途径。
对过程进行改变時,应小心地监视控制。
这个变化时期对系统操作会是破坏性,可能造成新的控制问题,掩盖系统变化后的真实效果。
在过程改变期间出现的特殊原因变差被识別并纠正后,过程将按一个新的过程均值处于统计控制状态。
这个新的均值反映了受控制状态下的性能。
可作为现行控制的基础。
但是还应对继续系统进行调查和改进。
九.判稳判异准则
1、判稳准则:
☉控制图中的点子符合以下三种情况即可判稳:
☉a.连续25个点,界外点数d=0(Pa=0.0654)
☉b.连续35个点,界外点数d≤1(Pb=0.0041)
☉c.连续100个点,界外点数d≤2(Pc=0.0026)
2、八种判异准则
判别1.任一点落于控制限外P1=0.0027判别1.一点超出A区
常见原因:
•新工人,方法,原材料改变或仪器出现故障。
•检验方法或检验标准的改变。
•操作者技能和积极性方面的转变
判别2.连续9点位于中心线同一侧(P2=0.0038)
常见原因:
•操作者控制过严。
•用同一图控制两个过程。
•两个不同的班,取样设备或取样方法不同或者两位不同的操作者
判别3.连续6点稳步上升或下降(P3=0.00273)
•
常见原因:
•新工人,方法,原材料或分析仪器出现故障
•检验方法或检验标准的改变
•操作者技能和积极性方面的转变。
判别4.连续14点交替升降P4由统计模拟验证
•
常见原因:
•操作者控制过严。
•用同一图控制两个过程。
•两个不同的班,取样设备、方法、取样点不同或者两位不同的操作者
判别5.连续3点中有2点位于或超出A区(单边)(P5=0.0006585
常见原因:
新工人,方法,原材料或分析仪器出现故障。
•检验方法或检验标准的改变。
•操作者技能和积极性方面的转变。
•判别6.连续5点中有4点位于或超出B区(单边)(P6=0.0021)
常见原因:
•新工人,方法,原材料或分析仪器出现故障
•检验方法或检验标准的改变
•操作者技能和积极性方面的转变
判别7.连续15点位于C区(中心线CL上下)(P7=0.0032
常见原因:
•控制限的计算不正确
•(对过程的变动性估计过大)
•持续改进获得成功
判别8.连续8点位于中心线CL两侧而无一居C区(P8=0.000096
常见原因:
•系统性的环境变化。
•(温度,操作者疲劳,操作者轮换,机器设定的上下波动)
•维护计划所排。
•工器具磨损。
十、应对方法:
•验证数据的正确性及数据输入的正确性。
•看看有否关于特殊原因的简单解释(例如取样、仪器自身故障、分析人员对仪器操作的掌握)。
•当失控情况信号发生后,应对失控情况信号和由此产生的影响加以评价从而决定下一步的行动路线。
(最好写进文件中):
停线;寻找根本原因。
十一、产品统计过程控制(SPC)波动对策表