连杆铣槽夹具设计说明书带cad图.docx
《连杆铣槽夹具设计说明书带cad图.docx》由会员分享,可在线阅读,更多相关《连杆铣槽夹具设计说明书带cad图.docx(12页珍藏版)》请在冰豆网上搜索。
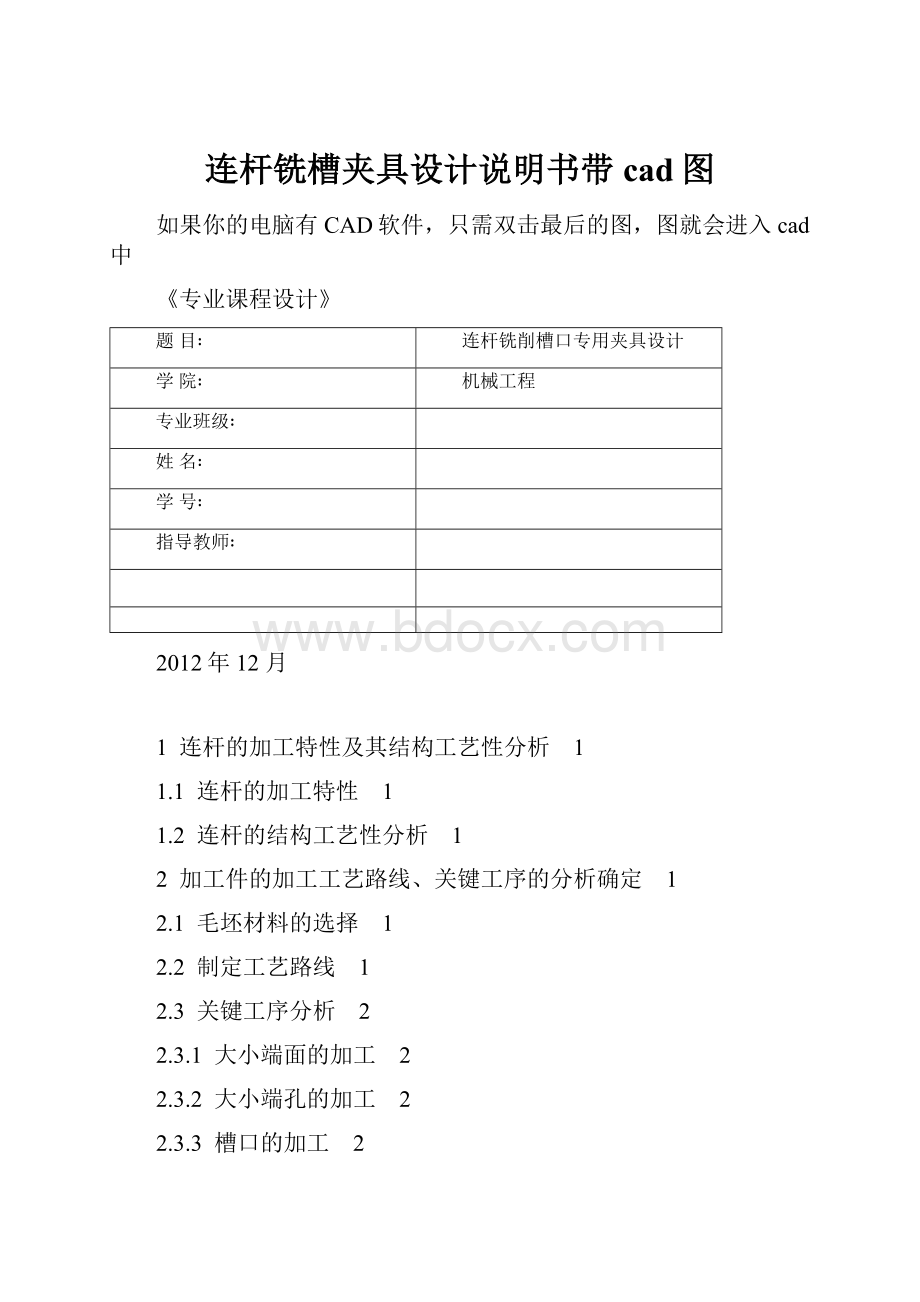
连杆铣槽夹具设计说明书带cad图
如果你的电脑有CAD软件,只需双击最后的图,图就会进入cad中
《专业课程设计》
题目∶
连杆铣削槽口专用夹具设计
学院∶
机械工程
专业班级∶
姓名∶
学号∶
指导教师∶
2012年12月
1 连杆的加工特性及其结构工艺性分析 1
1.1 连杆的加工特性 1
1.2 连杆的结构工艺性分析 1
2 加工件的加工工艺路线、关键工序的分析确定 1
2.1 毛坯材料的选择 1
2.2 制定工艺路线 1
2.3 关键工序分析 2
2.3.1 大小端面的加工 2
2.3.2 大小端孔的加工 2
2.3.3 槽口的加工 2
3 切削用量计算 3
3.1 选择刀具及切削用量 3
3.2工序卡 4
4铣削槽口专用夹具设计 5
4.1工件的加工工艺分析 5
4.2确定夹具的结构方案 6
4.2.1确定定位方案,设计定位元件 6
4.2.2夹紧方案选择及夹紧机构设计 7
4.2.3夹具对定位方案的确定 8
4.3夹紧力计算和定位误差分析 9
4.3.1夹紧力计算 9
4.3.2定位误差分析 10
4.4确定夹具的主要尺寸、公差和技术要求 10
4.4.1夹具总图应标尺寸,公差 10
参考文献 11
附录 11
1 连杆的加工特性及其结构工艺性分析
1.1 连杆的加工特性
连杆是发动机的五大件之一,是发动机重要的安全件。
其大头孔与曲轴连接,小头孔通过活塞销与活塞连接,其作用是将活塞的气体压力传给曲轴,又受曲轴驱动而带动活塞压缩气缸中的气体。
连杆受的是冲击动载荷,因此要求连杆质量小、强度高。
连杆杆身是工字型截面,而且从大头到小头逐步变小。
连杆的质量直接影响发动机的使用性能和安全性能。
从结构上看连杆并不复杂,但连杆属于典型的不规则件且精度要求高,所以加工工艺比较复杂:
磨削、钻、铰、镗、铣、衍磨等多种加工方法。
1.2 连杆的结构工艺性分析
连杆由连杆大头、杆身和连杆小头三部分组成。
连杆机械加工的主要内容有小端孔、大端孔和与其垂直的两端平面,以及连杆杆身和螺栓孔。
这些表面都要求达到一定的精度。
同时为了提高疲劳强度,要求有较小的表面粗糙度数值,不允许有细微的伤痕或裂纹。
高速机连杆杆身要求对全部非工作表面进行喷丸处理,圆角及过渡都应抛光。
连杆是一种杆类零件,外形细长、刚性差,因而在选择定位基准和夹压点时,应使其加工时的变形最小。
故大多数工序都是采用大、小端孔的端面作为定位基准,并使夹紧力作用在端面上。
这种定位方法简单,又避免因夹紧力和切削力的作用而使连杆发生变形。
2 加工件的加工工艺路线、关键工序的分析确定
2.1 毛坯材料的选择
连杆复杂的工作条件(承受拉力、压力和扭曲的多变负荷)及高的疲劳强度要求,决定了它的材料的选取和毛坯的制造方法。
这里选择的材料为牌号是QT40—17,它能够满足上述要求,由于连杆的强度要求,故其毛胚的制造选择了铸造的方法。
2.2 制定工艺路线
连杆加工工艺过程见表1所列。
表1 连杆加工工艺过程
工序号
工序名称
1
铸造毛坯
2
粗铣大小、头两端面
3
粗镗大、小端孔
4
热处理
5
半精铣大、小两端面
6
精镗大、小端孔
7
划加工线
8
粗铣大头端槽口
9
半精铣大头端槽口
10
钻φ6孔
11
攻丝
12
去毛刺
13
发蓝处理
14
检查
2.3 关键工序分析
2.3.1 大小端面的加工
大小端孔常常先加工好,使其作为后续工序的定位基准。
大小端面常用铣、磨以及拉削方法加工。
加工时先以其中的一边端面为基准加工另一边端面,然后将连杆翻转180°,以加工过的端面作为基准加工另一端面。
2.3.2 大小端孔的加工
大小端孔常常为孔本身加工和其他表面的定位基准。
大小端孔的加工精度和表面粗糙度要求都较高,通常分为粗、半精二次进行。
对于这种尺寸较小的连杆,模精度要求很高,一般只经过粗镗、半精镗、精镗。
小端孔的粗加工一般安排在大端孔粗加工前,这是由于小端孔在后续加工中将作为主要定位基准。
镗孔时以杆身装夹,按孔的划线痕找正定位。
2.3.3 槽口的加工
槽口的定位以两端孔的的中心线为基准。
以槽口的加工要求和精度,分为粗铣和半精铣两次进行。
在槽口的深度方面的工序基准是工件的相应端面。
从基准重合的要求出发,定位基准选择此端面,但由于要在次端面上开槽,开槽时此面必须朝上,相应的夹具定位势必要设计朝下,这对定位、夹紧等操作和加工都不方便。
因此,定位基准选在与槽相对的那个端面比较合适。
由于槽深的尺寸公差为(0.2mm),而基准不重合造成的误差仅为0.1mm,所以这样选择定位基准是可以的。
在保证夹角45°±10′方面,工序基准是双孔中心线所在平面,所以定位件采用圆柱销和菱形销。
以大端孔为主要定位基准,小端孔为次要基准。
3 切削用量计算
3.1 选择刀具及切削用量
选择高速钢圆柱铣刀,根据槽口要求,选铣刀直径
=12mm,齿数为8
1.选择切削用量
1)
=5mm
=3.2mm af=0.1mm
2)决定进给量
根据查表取
=0.10mm/z
(1)选择车刀后到面最大磨损量为0.4mm,刀具寿命为T=120min。
(2)查切削用量简明手册表3.10,
当
,查切削用量简明手册表3.9修正系数为0.87,所以
(3)实际切削速度和每齿进给量
根据铣床X61W型万能铣床说明书,选择
(4)计算基本工时
式中L=l+η+Δ,其中l=4×70mm=280mm,根据切削用量简明手册表3.25,η+Δ=17mm
故
tm=(280+17)/85=3.49min
3.2工序卡
连杆加工工艺工序卡见表2所列。
表2 连杆加工工艺工序卡
佳木斯大学
机械加工工艺过程卡
产品型号
产品名称
连杆
共1页
第1页
材料编号
QT40—17
毛坯种类
铸造
毛坯外
形尺寸
每毛坯
可制件数
1
备注
工
序
号
工序名称
工序内容
刀具
工艺
装备
工时/h
准终
单件
1
铸造毛坯
2
粗铣
大小端面以加工面的对面为基准
立式铣刀
铣床
3
粗镗
粗镗大小头端孔以端面为基准
镗刀
镗床
4
热处理
热处理检查
5
划线
划加槽口工线以大小端孔为基准
6
半精铣
大小端面以加工面的对面为基准
立式铣刀
铣床
7
精镗
精镗大小头端孔以端面为基准
镗刀
镗床
8
粗铣
铣大头端槽口以加工面的对面为基准
立式铣刀
铣床
9
精铣
半精铣大头端槽口以加工面的对面为基准
立式铣刀
铣床
10
钻孔
钻φ6孔
钻头
钻床
11
攻丝
12
去毛刺
去毛刺
13
表面处理
表面发蓝处理
14
检验
全面检查
4铣削槽口专用夹具设计
4.1工件的加工工艺分析
工件已加工过的大小头孔径分别为
mm和
mm,两孔中心距为80±0.05mm
,大、小头厚度均为
mm。
如图1。
图1
在加工槽口时。
槽口的宽度由刀具直接保证,而槽口的深度和位置则和设计的夹具有关。
槽口的位置包括两方面的要求:
(1)槽口的中心面应通过
mm的中心线,但没有在工序图上提出,说明此项要求精度较低,因此可以不作重点考虑。
(2)要求槽口的中心面和两孔中心线所在的平面的夹角为45°±10′。
为保证槽口的深度
mm和夹角45°±10′,需要分析与这两个要求有关的夹具精度。
4.2确定夹具的结构方案
4.2.1确定定位方案,设计定位元件
在槽口深度方面的工序基准是工件的相应端面。
从基准重合的要求出发,定位基准最好选择此端面。
但由于要在此端面上开槽,开槽时,此面必须朝上,相应的夹具定位势必要设计成朝下,这对定位、夹紧等操作和加工都不方便。
因此,定位基准选在与槽相对的那个端面比较合适。
由于槽深的尺寸公差较大(0.2mm),而基准不重合造成的误差仅为0.1mm,所以这样选择定位基准是可以的。
在保证夹角45°±10′方面,工序基准是双孔中心线所在的平面,所以定位工件采用一圆柱销和一菱形销最为简便。
由于槽开在大头端面上,槽的中心面应通过孔
的
mm中心线,这说明大头孔还是槽口的对称中心面的工序基准。
因此,应选择大头孔
mm
作主要定位基准,定位元件选择短圆柱销(限制两个自由度)。
而小头孔
mm
作次要定位基准,定位元件选择菱形销(限制一个自由度),如图2.
图2
在每个工件上铣八个槽,除正反两面分别装卸加工外,在同一面的四个槽的加工也可采用两种方案:
一是采用分度机构在一次装夹中加工,由于不能夹紧大头端,夹具结构比较复杂,但可获得较高的槽与槽间的位置精度;另一方案是采用两次装夹工件,通过两个菱形定位销分别定位(如图2),由于受两次装夹定位误差的影响,获得的槽与槽间的位置精度较低。
鉴于本夹具设计中槽与槽间的位置精度要求不高(夹角45°±10′),故可采用第二种方案。