第七章金属磨损和接触疲劳.docx
《第七章金属磨损和接触疲劳.docx》由会员分享,可在线阅读,更多相关《第七章金属磨损和接触疲劳.docx(8页珍藏版)》请在冰豆网上搜索。
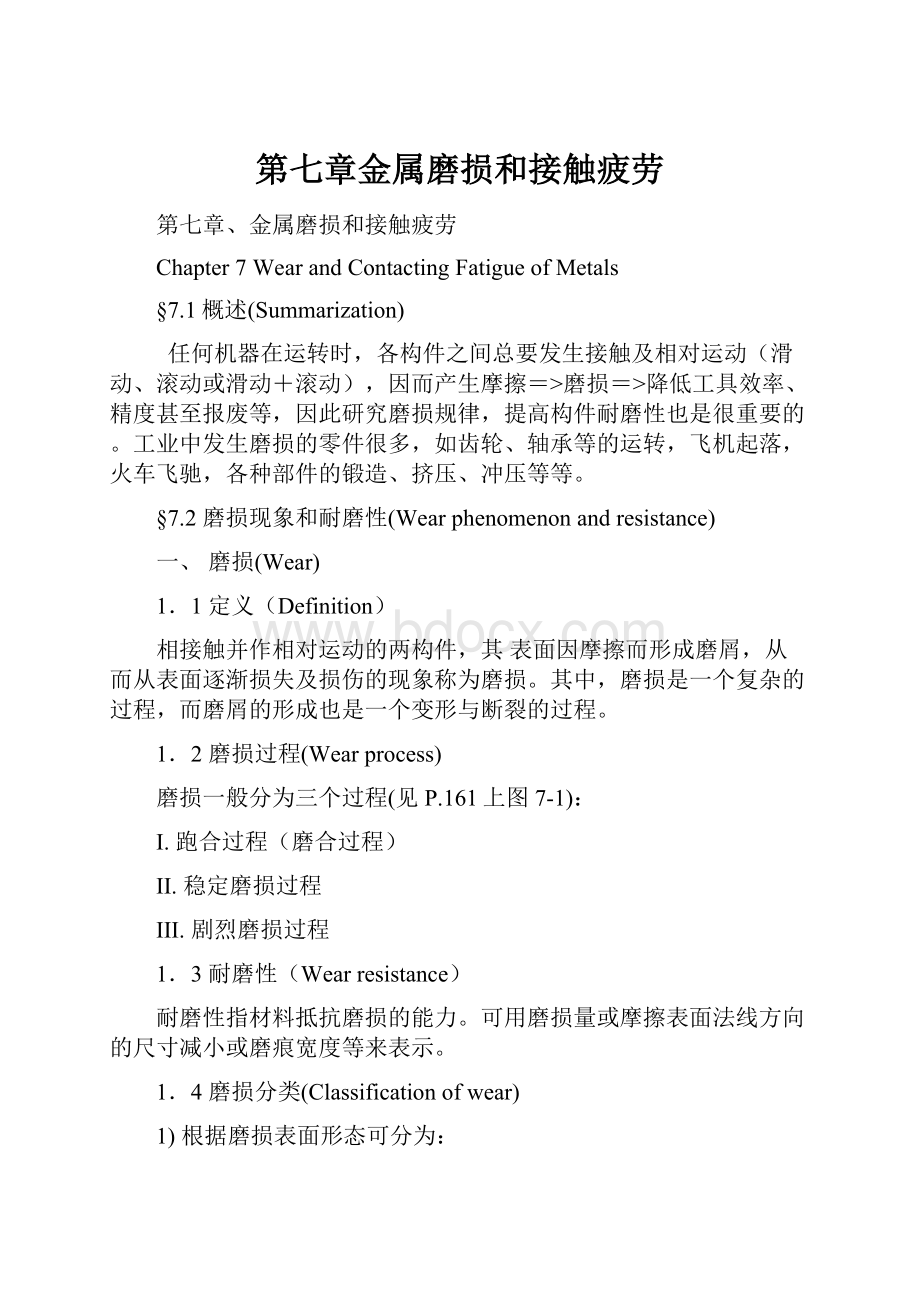
第七章金属磨损和接触疲劳
第七章、金属磨损和接触疲劳
Chapter7WearandContactingFatigueofMetals
§7.1概述(Summarization)
任何机器在运转时,各构件之间总要发生接触及相对运动(滑动、滚动或滑动+滚动),因而产生摩擦=>磨损=>降低工具效率、精度甚至报废等,因此研究磨损规律,提高构件耐磨性也是很重要的。
工业中发生磨损的零件很多,如齿轮、轴承等的运转,飞机起落,火车飞驰,各种部件的锻造、挤压、冲压等等。
§7.2磨损现象和耐磨性(Wearphenomenonandresistance)
一、磨损(Wear)
1.1定义(Definition)
相接触并作相对运动的两构件,其表面因摩擦而形成磨屑,从而从表面逐渐损失及损伤的现象称为磨损。
其中,磨损是一个复杂的过程,而磨屑的形成也是一个变形与断裂的过程。
1.2磨损过程(Wearprocess)
磨损一般分为三个过程(见P.161上图7-1):
I.跑合过程(磨合过程)
II.稳定磨损过程
III.剧烈磨损过程
1.3耐磨性(Wearresistance)
耐磨性指材料抵抗磨损的能力。
可用磨损量或摩擦表面法线方向的尺寸减小或磨痕宽度等来表示。
1.4磨损分类(Classificationofwear)
1)根据磨损表面形态可分为:
a.粘着磨损
b.磨粒磨损
c.腐蚀磨损
2)根据磨损所受应力大小,磨粒磨损可分为:
a.凿削式磨粒磨损(如挖掘机齿轮)
b.高应力辗碎性磨粒磨损
c.低应力擦伤性磨粒磨损
3)根据磨粒硬度与材料的相对硬度,磨粒磨损可分为:
a.硬磨粒磨损(磨粒硬度大于被磨材料的硬度)
b.软磨粒磨损(磨粒硬度小于被磨材料的硬度)
通常磨粒磨损即指硬磨粒磨损
§7.3磨损机理(Wearingmechanism)
一、粘着磨损(Adhesionwear)
1.1定义(Definition)
粘着磨损又称咬合磨损,是指在滑动摩擦条件下,且摩擦副相对滑动速度较小(<1m/s)的磨损。
1.2特点(Features)
粘着实际上是摩擦副两表面原子间的键合作用,在随后的继续滑动时,粘着点被全部剪断。
并转移到另一方金属表面。
然后脱落形成磨屑。
1.3过程(Process)
粘着磨损又有如下三个过程:
a.接触面凸起部分因塑性变形被辗平,并在接触面之间形成剪断强度高的分界面。
b.在摩擦一方金属远离分界面处,发生断裂称碎屑=>转移到另一方。
c.形成磨屑脱落。
1.4磨损量的估算(Evaluationofwearingmass)
J·F·Archard经推导得:
V=K·F·Lt/(9σsc·δ)
式中,V:
磨损的体积;Lt:
滑动距离;K:
磨屑形成几率;F:
法向作用力;σsc:
压缩屈服强度δ:
伸长率
由上式可见:
σsc,δ升高,即H升高,V降低;
F,Lt升高,V升高。
二、磨粒磨损(Particlewear)
2.1定义(Definition)
磨粒磨损——指当摩擦副一方表面存在坚硬的细微凸起,或在摩擦副接触面之间存在着硬质粒子时所产生的一种磨损。
前者又称为两体磨粒磨损,后者称为三体磨粒磨损。
2.2磨粒特征(Characteristic)
磨粒磨损主要特征是摩擦面上有明显的犁皱形成的沟槽。
如p165,图7-5。
2.3磨粒磨损量的估算(Evaluationofwearingmass)
两体磨粒磨损量的估算:
W=F·l·tgθ/3πσsc
或W=K·F·l·tgα/H
式中F:
法向作用力;H:
材料硬度;σsc:
材料抗压屈服强度;θ:
凸出圆锥面与软材料表面间的夹角;l:
摩擦副相对滑动的距离;K:
为系数。
可见提高材料的硬度H,或强度σ,均可提高磨粒磨损抗力。
2.4磨粒磨损影响因素
◆金属材料的磨粒磨损抗力随H/E(H:
材料硬度;E材料的弹性模量)的增大而提高,即材料硬度越高,则耐磨性越好(见P167上图7-7);
◆细化晶粒可以提高材料的耐磨性;
◆在较软基体中分布均匀、弥散的第二相,可以提高耐磨性;但在硬基体中分布均匀、弥散的第二相,反而会降低耐磨性;
2.5软磨粒磨损(一般应用较少,故略)(见P169)
§7.4磨损实验方法(Weartests)
磨损实验方法有实物的实验(与实际情况一致或接近)和实验室实验等两大类。
实验室试验方法有:
a.销盘式
b.销筒式
c.往复运动
d.MM型
e.砂纸磨损
f.快速磨损
具体装置简图见p172。
图7-11
磨损评定:
测量磨损重量或测量磨痕的长度。
§7.5提高耐磨性的方法(Methodsofincreasingwearresistance)
由于金属材料磨损主要发生在工件表面上的变形与断裂,因此提高材料表面强度(或硬度)及韧性,可以提高材料的耐磨性。
一、提高粘着磨损抗力的方法(Methodsofincreasingadhesionwearresistance)
方法有:
a.提高材料强韧性;
b.改善润滑条件(加润滑剂或表面渗S、P、N等);
c.提高氧化膜的稳定性及其与基体材料的结合力
d.降低工件表面粗糙度。
二、提高磨粒磨损抗力的方法(硬磨粒磨损)(Methodsofincreasingparticlewearresistance)
方法有:
a.提高材料的强韧性;
b.表面渗C、B、N;
c.保持表面清洁,即减少磨粒种类及数量。
§7.6金属接触疲劳(ContactingFatigueofMetals)
一、接触疲劳及接触应力(Contactingfatigueandstress)
1.1定义(Definition)
当两机件接触滚动或滚动加滑动摩擦时,在交变载荷(接触压应力)的作用下,表面因疲劳而损伤的现象称为接触疲劳,也成为表面疲劳磨损或疲劳磨损。
1.2分类(Classification)
接触疲劳磨损可分为:
i.麻点剥落(点蚀);
ii.浅层剥落;
iii.深层剥落(表面压碎)。
1.3特性(Characteristic)
接触疲劳破坏表面常有许多小针状或痘状凹坑或大凹坑。
二、接触应力(Contactingstress)
由于接触疲劳是在接触压应力长期作用下的结果,所以了解两物体接触应力及其分布是及其重要的。
2.1定义(Definition)
两物体相互接触时,在接触表面上产生局部压入应力称为接触应力,也称为赫兹应力,可以是面接触、线接触或点接触。
2.2两圆柱体作纯滚动时接触应力场(Contactingstressfieldofbothcylindersunderrollingcondition)
a.y=0处的应力场
如p175,图7-15所示,两接触圆柱体半径分别为R1、R2,长度为L0。
在未变形前时线接触。
施加法向力F后,则为面接触,接触面积为2bl。
根据弹性力学可推导出,σz沿y轴呈半椭圆形分布(在y=0处,σz达到最大(σzmax)
σz=σzmax(1-Y2/b2)1/2
式中b=F·(R1·R2)/【E·l·(R1+R2)】为接触面半宽;E=2E1·E2/(E1+E2)为综合杨氏模量。
实际上,在F作用下,接触处应力为三向压应力,σx、σy、σz为主应力,相应的最大切应力为:
τzy45o=(σz-σy)/2
τzx45o=(σz-σx)/2
τyx45o=(σy-σx)/2
其中τzy45o最大。
它的分布见P175上图7-16和P176图7-17。
由图7-17或计算可得:
在接触深度为0.786b处,τzy45o达到最大值。
τzy45omax≈(0.3~0.33)σzmax
因此该处将作0~τzy45omax之间的循环应力作用。
振幅为1/2τzy45omax。
b.其他区域的应力分布
以上是沿z轴方向的应力分布,在接触区的其他区域应力分布与此不同。
即切应力不等于零。
也即σx、σy、σz不是主应力了。
最大切应力τ0max也平行于接触表面。
τ0max=0.25bσzmax。
切应力平行于接触表面。
且在z=0.5b处,y=0.85b处为最大。
现两圆柱体作纯滚动接触,有两处接触应力,即z=0.786b,y=0和z=0.5b,y=±0.85b处。
这两处最大切应力将是疲劳裂纹形成的源区。
c.其他接触体的应力场。
见p176-177。
2.3有滑动+滚动两圆柱体接触应力场(ContactingstressfieldofbothcylindersunderSlidingandrollingcondition)
在这种情况下,接触应力场会更加复杂。
即是摩擦力的应力场和接触应力的应力场相互叠加的结果。
由p186图7-22可见,在有滑动时,接触切应力τ0由脉动应力变成交变应力τ0·最大切应力深度将从z=0.786b移向表面。
实验证明,当摩擦系数>0.2时,则τ0·max移向工件的表面。
三、接触疲劳破坏机理
接触疲劳裂纹也是切应力作用下塑性变形形成的。
因此根据切应力分布特点可以决定裂纹产生的位置和接触疲劳的类型。
3.1麻点剥落(FormationofSpots)
当τ0max在表面处,会形成麻点剥落,具体过程见p177图7-19。
产生条件:
表面摩擦力大,或表面缺陷(脱碳夹杂)
3.2浅层剥落(Fallingofresiduelayers)
浅层剥落产生了亚表层,其深度与τzy45omax最大位置相当,即0.786b或0.5b。
残层剥落多出现在机件表面粗糙度低,即光滑,相对滑动小,即摩擦力小的场合。
3.3深层
剥落(压碎性剥落)(Formationofdeepspots)
对于表面硬化处理良好的机件,若在0.786b处产生裂纹会向内部过渡区扩展,形成压碎性剥落。
产生条件:
机件心部强度过低,硬化层深不合理,梯度太陡或过渡区存在不利的应力分布是造成深层剥落的原因。
四、接触疲劳实验方法(不讲)
材料的接触疲劳性能也可以用σmax-N来描述,σmax赫芝公式算出的最大接触压应力。
N为断裂周次。
专用实验机,精度不高,(如嘉定齿轮厂齿轮台架寿命实验机)
五、影响接触疲劳抗力的因素(Factorsofaffectingcontactingfatigueresistance)
从上面分析可知,接触疲劳破损主要是决定于接触件中最大综合切应力与材料屈服强度的相对大小,并考虑局部缺陷造成的应力集中,因此其影响因素有:
5.1内部因素(Internalfactors)
i.工件内部存在金属夹杂=>疲劳抗力降低
ii.表面硬度升高=>疲劳抗力升高
iii.表面压应力升高=>疲劳抗力升高
iv.硬化层要有一定的深度。
5.2外因(Externalfactors)
a.表面粗糙度降低=>疲劳抗力升高
b.接触体硬度要匹配
c.接触体之间的装配间隙、润滑等
作业:
(P181)1[
(1)、(7)、(8)];3;4;7;8。