材料成型技术基础总复习.docx
《材料成型技术基础总复习.docx》由会员分享,可在线阅读,更多相关《材料成型技术基础总复习.docx(13页珍藏版)》请在冰豆网上搜索。
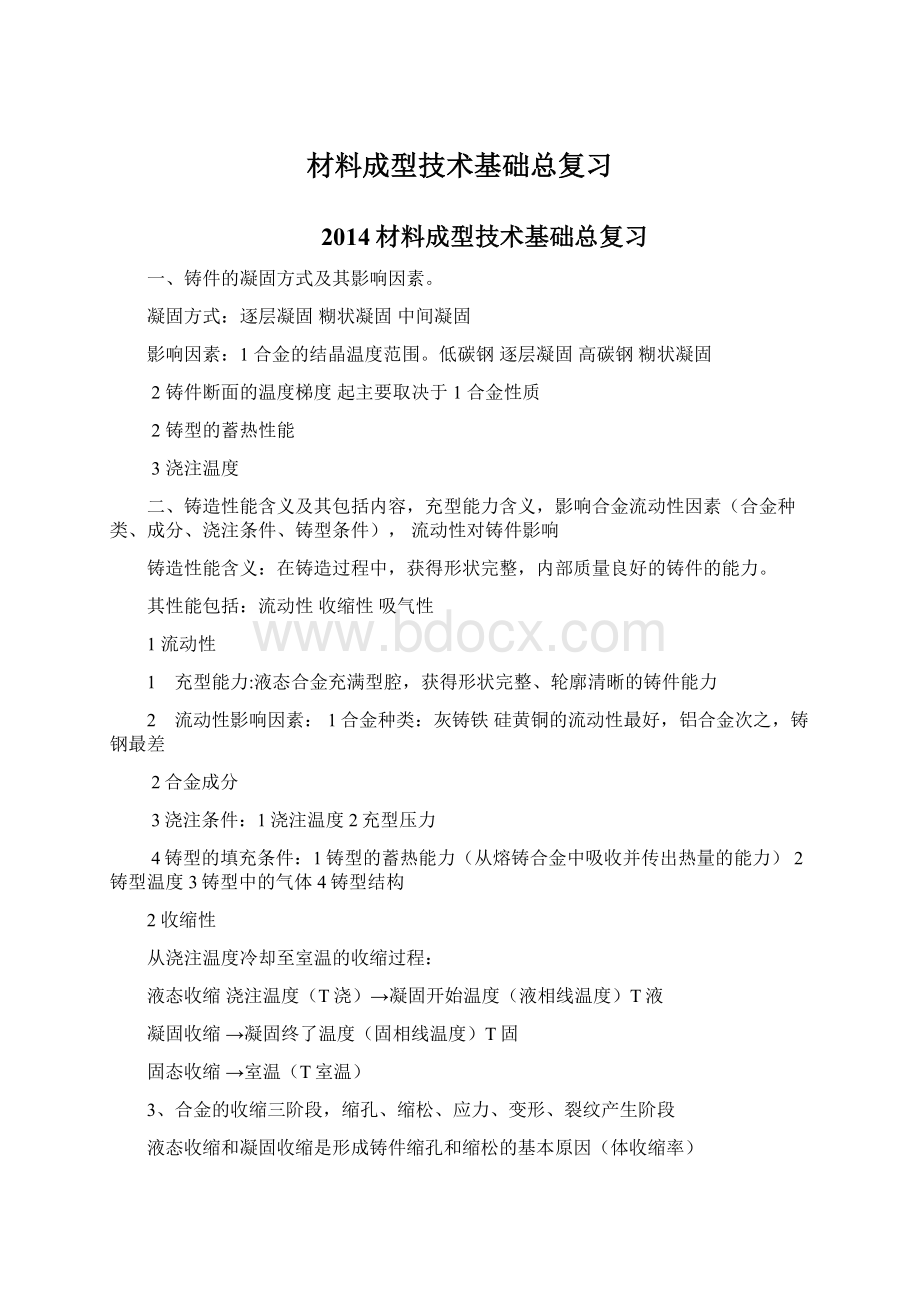
材料成型技术基础总复习
2014材料成型技术基础总复习
一、铸件的凝固方式及其影响因素。
凝固方式:
逐层凝固糊状凝固中间凝固
影响因素:
1合金的结晶温度范围。
低碳钢逐层凝固高碳钢糊状凝固
2铸件断面的温度梯度起主要取决于1合金性质
2铸型的蓄热性能
3浇注温度
二、铸造性能含义及其包括内容,充型能力含义,影响合金流动性因素(合金种类、成分、浇注条件、铸型条件),流动性对铸件影响
铸造性能含义:
在铸造过程中,获得形状完整,内部质量良好的铸件的能力。
其性能包括:
流动性收缩性吸气性
1流动性
1 充型能力:
液态合金充满型腔,获得形状完整、轮廓清晰的铸件能力
2 流动性影响因素:
1合金种类:
灰铸铁硅黄铜的流动性最好,铝合金次之,铸钢最差
2合金成分
3浇注条件:
1浇注温度2充型压力
4铸型的填充条件:
1铸型的蓄热能力(从熔铸合金中吸收并传出热量的能力)2铸型温度3铸型中的气体4铸型结构
2收缩性
从浇注温度冷却至室温的收缩过程:
液态收缩浇注温度(T浇)→凝固开始温度(液相线温度)T液
凝固收缩→凝固终了温度(固相线温度)T固
固态收缩→室温(T室温)
3、合金的收缩三阶段,缩孔、缩松、应力、变形、裂纹产生阶段
液态收缩和凝固收缩是形成铸件缩孔和缩松的基本原因(体收缩率)
固态收缩是产生变形,内应力和裂纹的基本原因(线收缩率)
缩孔是在铸件最后凝固的部位形成溶剂较大而且集中的空洞
缩松:
细小而分散的空洞
4、铸造内应力分类及其各自产生原因。
(厚壁心部与薄壁表面应力性质)
1、热应力:
由于冷却速度不同而引起不均衡收缩所产生的应力
2、收缩应力:
固态收缩时,因受到铸型、型心,浇冒口、砂箱等外力阻碍而产生的应力
3、相变应力:
固态下发生相变的合金,由于部分冷却速度不同,达到相变温度的时刻不同,而且发生相变的程度也不同,由此而产生的应力。
5、什么是定向凝固原则?
什么是同时凝固原则?
其目的是什么?
需要采取什么措施来实现?
定向凝固原则:
在铸件上可能出现缩孔的厚大部位安放冒口,在远离冒口的补位安放冷铁,使铸件上远离冒口的部位先凝固,靠近冒口的部位后凝固,冒口本身最后凝固。
同时凝固:
采取一定工艺措施,使铸件各部分无温差或温差尽量小,几乎同时进行凝固。
各部分温差小,不应产生热应力和热裂,铸件变形较小。
同时凝固不必设置冒口,工艺简单,节约金属。
但同时凝固的铸件中心容易出现缩松,影响铸件的致密性
6、防止或减少铸件应力与变形的措施?
1 合理的设计铸件结构
2 合理选用合金
3 采取同时凝固的工艺
4 减少收缩应力
5 对铸件进行时效处理
7、影响铸铁石墨化因素、孕育铸铁、球墨铸铁、可锻铸铁各自含义,如何获得,组织与性能特点。
不同形态石墨的获得及对性能的影响(材控专业要求)
1影响铸铁石墨化的因素
1)铸铁成分的影响CSi促进SMnCrWuMo
2)冷却速度的影响(铸型的冷却条件,铸件壁厚)冷却速度慢,利于石墨形成并容易形成粗大片状石墨;冷却速度快,碳原子析出不充分,集聚较慢,只有部分碳原子以细石墨片析出
2灰铸铁:
由PP-FF的基体上分布着片状石墨所组成
1 力学性能:
脆性材料
2 工艺性能:
不能锻造冲压,可焊性差
3 减震性好
4 耐磨性好
5 缺口敏感性低
孕育处理:
得到细晶粒珠光体和分部均匀的细片状石墨组织
生产特点:
一般在冲天炉中铸炼,成本低廉。
凝固中有石墨化膨胀补偿收缩,故流动性好,收缩小,铸件的缩孔,缩松,浇不到、热裂、气孔倾向均较小。
3球墨铸铁:
向灰铸铁铁水中加入一定量球化剂进行球化处理,并加入少量孕育剂促进石墨化
具有优良的力学性能,切削加工性能和铸造性能,生产工艺简便,成本低廉,应用日益广泛。
凝固方式为糊状凝固,容易产生缩孔,缩松
1.增加铸型攻读,组织铸件向外膨胀,并利用石墨化向内膨胀,产生自缩补的效果,已达到防止或减少铸件缩孔或缩松的效果。
2.在热节点处安放冒口或冷铁
4可锻铸铁(玛钢玛铁)
将白口铸铁在退火炉中经过长时间高温石墨化退火,使白口组织中的渗碳体分解,而获得铁素体或珠光体基体加团絮状石墨的铸铁,改变其金相组织或成分,从而获得有较高韧性的铸铁。
铁水流动性差,收缩大,容易产生缩孔,缩松,裂纹等缺陷,浇注时铁水温度应较高,铸型与型心应有较好的退让性,并设置冒口,以获得完全的白口组织。
5铸钢
1.铸钢的力学性能高于各类铸铁
2.某些合金铸钢具有特殊的耐磨性、耐热性、耐蚀性等。
3.焊接性能好,便于采用铸-焊联合结构制造形状复杂的巨大铸件
熔炼采用炼钢炉,平炉,电弧炉,感应电炉。
能炼各种高级合金钢及含碳低的钢,其熔炼速度快,能源消耗小,且钢水质量高,适用于小型铸钢钢件生产
铸钢的熔点高,流动性差,收缩大,钢液易氧化,吸气,易产生黏砂,冷隔,浇不到,缩孔,气孔,变形,裂纹等缺陷,铸造性能差。
(退火正火)
8、灰铸铁、球铁与铸钢熔点、流动性、收缩率、铸造性能比较。
(材控专业要求)
9、熔模铸造工艺过程、特点和适用范围
液态金属在重力作用下浇入由蜡模溶失后形成的中空型壳中形成,从而获得精密铸件的方法。
工艺过程:
制造蜡模,制壳,脱蜡,焙烧,浇注
特点及应用:
1.铸件精度高,表面光洁
2.可铸出形状复杂的薄壁铸件
3.铸造合金种类不受限制
4.生产批量不受限制
10、金属型铸造应采取怎样的工艺措施来保证产品质量?
(预热、喷涂料、控开型、提高浇注温度)铸件特点、应用范围。
1.金属型应保持合理的工作温度。
金属型铸造没有退让性和透气性,铸型导热快,合理的工作温度可减缓铸型冷却速度,减少熔融金属对铸型的“热击”作用,延长金属型使用寿命;提高熔融金属的充型能力,防止产生浇不到,冷隔,气孔,夹杂等缺陷。
对于铸铁件,合理的工作温度有利于促进铸铁的石墨化,防止产生白口
2.喷刷涂料。
浇筑前必须向金属型型腔和金属心表面喷刷涂料。
其目的是可以防止高温的熔融金属对型壁直接进行冲击,保护型腔。
3.控制开型时间。
尽早从铸型中取出。
但是开型过早,也会因铸件强度低而产生变形
4.提高浇注温度和防止铸铁件产生“白口”。
金属型铸造的特点及应用:
1 实线一型多铸,省去配砂、造型、落砂等工序,节约了大量造型材料、造型工时、场地,改善了劳动条件,提高了生产率。
便于实现机械化、自动化生产。
2 尺寸精度高,表面质量好,铸件的切削余量小,结余了机械加工的工时,节省了金属。
3 金属型冷却速度快,铸件组织细密,力学性能好。
4 铸件质量较稳定,废品率低
11、离心铸造特点及应用(不用型芯;双金属铸件)。
1.省去型心及浇注系统和冒口
2.补缩性能好,使铸件致密,机械性能好
3.便于浇注“双金属”轴套和轴瓦
12、压力铸造的特点及应用(薄壁、精密件,镶嵌件,不能热处理)
1.操作简便,易实现自动化或半自动化生产
2.合金充型能力强,能铸出结构复杂、轮廓清晰的薄壁,精密的铸件,可直接住处各种孔眼、螺纹、花纹和图案等,也可压铸镶嵌件
3.可实现少、无切削加工,省工、省料、成本低
4.在压力能顾,且冷却速度快,铸件组织细密,表层紧实,强度、硬度高,抗拉强度比砂型铸造提高20%~40%
13、铸件结构设计的要求(理解工艺要求、铸造性能要求)(图4-6,4-15,4-20,4-21)
对铸件结构和工艺设计:
1铸件外形应便于取出模型
1 避免外部侧凹
2 分型面尽量平直
3 凸台、筋条的设计
2合理设计铸件内腔
1.节省型心的设计
2.便于型心的固定、排气和铸件清理
3铸件筋的设计
1 增加铸件的刚度和强度,防止铸件变形
2 消除铸件厚大截面,防止铸件产生缩孔,裂纹(加强筋)
4铸件结构应尽量减少铸件收缩受阻,防止产生变形和裂纹
1.尽量使铸件能自由收缩
2.采用对称结构,防止铸件变形
14、浇注位置选择原则、分型面选择原则。
(理解图4-31,4-32)。
铸件浇注位置的选择:
1.铸件的重要加工面应朝下或位于侧面
2.铸件的宽大平面应朝下
3.面积大的薄壁部分应置于铸型下部或垂直、倾斜位置
4.易形成缩孔的部件,应将截面较厚的部分放在分型面附近的上部或侧面
5.减少型心数量,便于型心安放,固定,排气
铸型分型面的选择
1)便于起膜,使造型工艺简化
2)分型面应尽量平直
3)尽量减少分型面,特别是机械造型时,只能有一个分型面。
十五、下列铸件在大批量生产时最适宜采用哪种铸造方法:
铝合金活塞发动机钢背铜套铸铁水管车床床身汽轮机叶片
16、冷、热变形含义(再结晶温度),变形后组织性能特点。
冷变形:
金属在再结晶温度一下进行的塑形变形
组织性能:
1.晶粒沿变形方向被拉长
2.晶粒破碎“冷变形强化或加工硬化”随变形程度的增加,金属材料的所有强度指标和硬度都有所提高,但塑形下降
3.晶粒择优取向,形成变形织构
4.残余内应力
冷变形后金属在加热时组织和性能变化:
组织性能:
1)金属致密度提高
2)组织细化,力学性能提高
3)出现锻造流线
17、加工硬化
在冷变形时,随着变形程度的增加,金属材料的所有强度指标和硬度都有所提高,但塑性和韧性有所下降
十八、回复与再结晶含义,回复与再结晶后组织与性能变化。
1回复消除晶粒的晶格扭曲,显著降低金属内应力
2再结晶以大量的碎晶或杂质为结晶核心,原子在金属内部重新排列,形成新的晶粒而取代冷变形后破碎和被拉长的已变形晶粒。
“随性变形后金属被拉长,破碎的晶粒重新生核,结晶,形成新的等轴晶粒现象”
热变形:
金属在再结晶温度以上的塑形变形
19、锻造流线对性能影响,如何利用?
充分利用锻造流线的方向性,遵守两原则:
1式锻造流线分部与零件的轮廓相符合而不是被切断
2使零件所受的最大拉应力与锻造流线平行,最大切应力与锻造流线垂直
二十、什么是金属的可锻性,影响可锻性的因素有哪些?
各自如何起作用?
金属在受压应力加工产生塑性变形的工艺性能
金属可锻性取决于材料的性质(内因)和加工条件(外因)
材料性质的影响:
1.化学成分的影响纯铁低碳钢高合金钢
2.金属组织和结构的影响
加工条件的影响:
1 变形温度的影响:
过热:
加热温度过高,晶粒急剧长大,材料力学性能降低。
过烧:
加热温度接近熔点,晶界氧化破坏了晶粒间的结合,使金属失去塑形,胚料报废
2 变形速度的影响
3 应力状态的影响
4 胚料表面的影响
二十一、自由锻工序,特点,制定自由锻工艺规程的主要内容?
工艺余块含义?
锻件图内容。
用简单的通用性工具,或在锻造设备上、下砧间直接使胚料变形而获得所需的几何形状及内部质量的锻件的加工方法
特点:
手工自由锻和机械自由锻手工自由锻只能生产小型锻件,生产率低。
工艺规程:
1)绘制锻件图加工余量、锻造公差、工艺余块:
为了简化锻件形状而加上去的部分金属
2)确定所用工序夹具
3)加热设备
4)加热规范
5)加热火次
6)冷却规范
7)锻造设备
8)锻件的后续处理
二十二、与自由锻相比,模锻有什么特点?
模膛分类?
模锻模膛?
飞边槽、冲孔连皮含义?
拔长、滚压模膛作用?
胎模锻、
与自由锻相比特点:
优点:
1.锻件形状,尺寸比较精确,表面粗糙度低,机械加工余量小,能锻出形状复杂的锻件。
材料利用率高,节省加工工时
2.金属胚料的锻造流线分部更加合理。
力学性能提高
3.生产率高,大批量生产时,锻件成本低
缺点:
胚料整体变形,变形抗力大。
磨具材料昂贵,只能加工一种锻件,成本高
模膛分类:
预锻模膛:
使胚料变形到接近于锻件的形状与尺寸
终锻模膛:
使胚料最后变形到锻件所要求的形状与尺寸
飞