车身装配输送自行小车.docx
《车身装配输送自行小车.docx》由会员分享,可在线阅读,更多相关《车身装配输送自行小车.docx(21页珍藏版)》请在冰豆网上搜索。
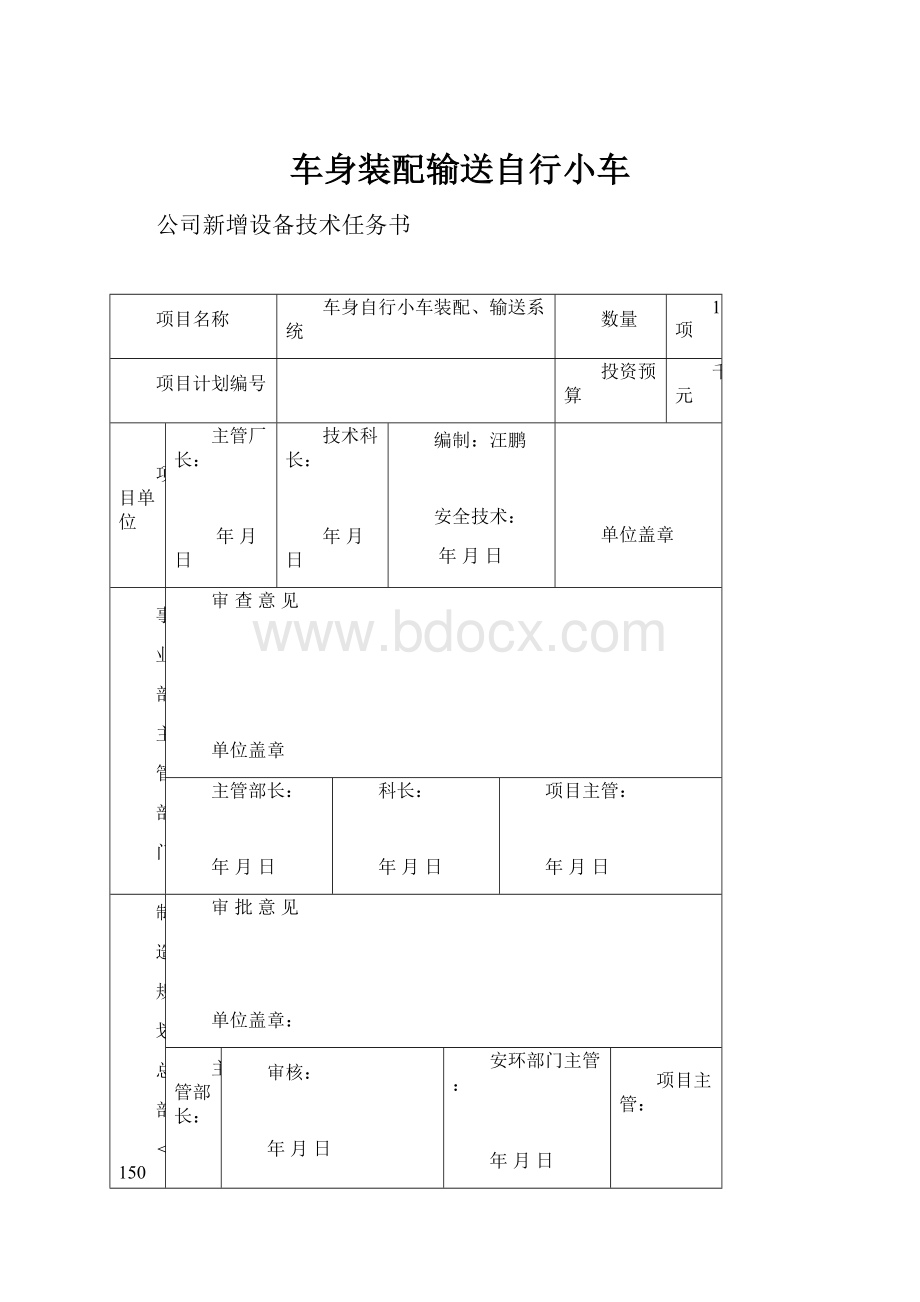
车身装配输送自行小车
公司新增设备技术任务书
项目名称
车身自行小车装配、输送系统
数量
1项
项目计划编号
投资预算
千元
项目单位
主管厂长:
年月日
技术科长:
年月日
编制:
汪鹏
安全技术:
年月日
单位盖章
事
业
部
主
管
部
门
审查意见
单位盖章
主管部长:
年月日
科长:
年月日
项目主管:
年月日
制
造
规
划
总
部
<150万元的项目由项目单位填报,事业部审批,报制造规划总部备案。
≥150万元的项目由项目单位填报,事业部审查,报制造规划总部审批。
审批意见
单位盖章:
主管部长:
年月日
审核:
年月日
安环部门主管:
年月日
项目主管:
年月日
车身自行小车装配、输送系统技术任务书
1主题和适用范围:
1.1设备名称:
车身自行小车装配、输送系统
1.2设备数量:
车身底部装配自行小车线I1条
车身底部装配自行小车线II1条
1.3设备用途:
1.3.1自行小车线I实现车身从存储系统发车转挂工位至内饰滑板线接车工位的输送,并具备在车身输送过程中进行底部装配作业的功能。
1.3.2自行小车线II实现车身从内饰滑板线发车工位至整车装配线车身落装工位的输送,并具备在车身输送过程中进行底部装配作业和在整车装配线上进行车身落装的功能。
1.3.3自行小车I、II具备连线功能,即具备使车身不通过内饰滑板线,直接完成车身从存储系统发车转挂工位至整车装配落装工位的输送,并在输送过程中能够进行底部装配作业和车身落装的功能。
1.3.4电控、监控系统用于对自行小车线的整体控制和监控。
1.4设备主要参数:
1.4.1设备的组成:
自行小车线(2条,含连线),电控系统,车身
吊具,维修轨道、维修平台、维修通廊及辅助钢结构,护网
1.4.2设备主要参数:
小车行走速度:
0-30m/min,可变频调速;
葫芦升降速度:
快速8m/min,慢速2m/min;
装配低位:
车身0Z坐标点离地高100mm
装配高位:
车身0Z坐标点离地高1100mm
工位间距:
3500mm
额定载重量:
2000kg。
1.5项目实施进度:
见商务合同
1.6货物需求表:
(见表1)
2工艺技术要求:
2.1车身品种及外型尺寸描述:
车型系列
品种
尺寸(长×宽×高)mm
D310系列
标准型
2030×2490×1995
加长型
2230×2490×1995
高顶加长
2460(2230+230)含扰流板×2490×2750
(含气喇叭200)
D530系列
一排半标准
1968×2267.5×1976
一排半薄顶
1968×2267.5×1896
单排
1688×2200×1896
D760系列
标准型
2260×2480×1800
高顶双卧
2260×2480×2310
2.2工艺流程或工序内容:
2.2.1存储系统发车转挂工位
1)车身存储系统发出挂车信号
2)自行小车由等待位到达挂车工位上方
3)空吊具落下一定高度停止(电气实现)
4)人工操作完成空吊具下降、合拢工作并等待
5)人工操作控制吊具带车身起升到一定高度
6)收到接车等待工位空位信号
7)小车自动前进
2.2.2自行小车I线接车工位
1)小车带车身进入自行小车I线接车等待工位
2)吊具带车身自动下降到装配高位等待
3)收到第一工位允许前进信号
4)小车带车身向第一工位前进
5)向挂车工位发出前进信号
2.2.3自行小车I线第一、二工位
1)小车带车身进入工位后停止
2)安全机构自动闭合并等待,人工进行装配
3)装配完成后,由人工操作,发出装配完成信号,通过电气控制打开安全机构。
4)下工位发出空车位信号后,小车带车身向下一工位前进
5)向上一工位发出前进信号
2.2.4自行小车I线第三工位
1)小车带车身进入工位后停止
2)安全机构自动闭合并等待,人工进行装配
3)装配完成后,由人工操作,发出装配完成信号,选择空壳发送或总成发送
4)发车工位发出要车信号后,小车带车身向自行小车I发车工位前进,小车到位后吊具依据上工位人工选择的结果实现车身的高位等待或低位等待。
5)向上一工位发出前进信号
2.2.5自行小车I线发车工位
a)选择空壳发送时:
a1)小车带车身进入工位后高位停止
a2)接收到内饰滑板接车等待工位发出的要车信号后,小车带车身前进至滑板线接车等待工位
a3)向上一工位发出前进信号
a4)小车将车身放置在滑板接车工位后,空小车返回至存储系统发车转挂工位
b):
选择总成发送时
b1)小车带车身进入工位后低位停止
b2)在接收到本工位完工信号和自行小车II线接车工位发出的要车信号后,小车带车身前进至自行小车II接车等待工位
b3)向上一工位发出前进信号
2.2.6自行小车II线接车工位
1)小车带车身进入自行小车II线接车等待工位
2)吊具带车身自动下降到装配高位等待
3)收到第一工位允许前进信号
4)小车带车身向第一工位前进
5)依据系统指示向自行小车I线发车等待工位或滑板线发车工位发出要车信号
2.2.7自行小车II线第一至八工位
1)小车带车身进入工位后停止
2)安全机构自动闭合并等待,人工进行装配
3)装配完成后,由人工操作,发出装配完成信号,通过电气控制打开安全机构。
4)下工位发出空车位信号后,小车带车身向下一工位前进
2.2.8自行小车II线第九工位
1)小车带车身进入工位后停止
2)安全机构自动闭合并等待,人工进行装配
3)装配完成后,由人工操作,发出装配完成信号,选择正常发送或异常发送
4)发车工位发出要车信号后,小车带车身向自行小车I发车工位前进,小车到位后吊具依据上工位人工选择的结果实现车身的高位等待或低位等待。
5)向上一工位发出前进信号
2.2.9自行小车II线发车等待工位
a)选择正常发送时:
a1)小车带车身进入工位后高位停止
a2)接收到落装等待工位发出的要车信号后,小车带车身前进至落装等待工位
a3)向上一工位发出前进信号
b):
选择异常发送时
b1)小车带车身进入工位后低位停止
b2)在接收到本工位完工信号和落装等待工位发出的要车信号后,小车前进至落装等待工位
b3)向上一工位发出前进信号
2.2.10落装工位
1)落装等待工位的小车在得到前方落装信号后前进至落装工位
2)小车自动检测整车装配线链速
3)同步落装车身
4)落装完毕后向落装等待工位发出要车信号
5)空车返回,返回时遵循自行小车II线上料工位优先原则,即首先自行小车II线上料点等待空车2个,其余空车在自行小车I线上料点积放等待
2.3达到的质量指标:
2.3.1实现2.1所列全系列车身的转运,使自行小车线能达到混流作业
2.3.2实现2.1所列全系列车身与整车装配线的同步落装功能
2.3.3自行小车小车吊具、吊钩要通用于2.1所列全系列驾驶,且不能导致车身划伤和变形。
2.4生产率要求(生产纲领和节拍):
生产纲领:
40000台/年
生产节拍:
4.94分钟/台
生产班次:
244天双班15小时
2.5其它技术要求:
2.5.1要求自行小车下吊具牢靠,确保车身运行时同步、平稳。
(投标时详细说明)
2.5.2运行中车身晃动量不大于50mm。
2.5.3工位停止时的位置精度5mm。
2.5.4内饰底部装配自行小车线在存储系统接车和滑板上放车的定位精度5mm。
2.5.5在装配工位车身摆动量不大于30mm。
2.5.6自行小车落装车身时要求能够自动检测整车装配线线速,实现同步落装,落车身时必须保持车身前倾,满足落装装配需求。
2.5.7小车主吊钩挂在车身左、右车门门框上边缘,另外在车身后部设计辅钩,避免车身由于重心位置的变化而发生歪斜。
同时要求车身主钩、辅钩在吊挂、放置车身时可通过电气控制实现自动打开和闭合。
2.5.8吊具额定载荷2000kg,满足2.1所列全系列车身的通用性,吊具本体不得与车身非吊挂部位发生干涉。
2.5.9自行小车线沿线设置维护、排障钢通廊,用于滑触线、集电器组、小车电箱等维护以及故障小车的人工推移。
2.5.10要求设有专用的检修轨道及检修平台、梯子。
2.5.11自行小车线的设计必须要满足生产节拍的要求。
2.5.12车身底部作业区必须设计安全防护装置。
(投标时详细说明)
2.5.13自行小车装配、输送线在装配工位和车身底部装配等待工位(共4个)之外的所有区段均需设置安全护网,护网最低点距离地面高度4.5米,小车运行时车身本体、吊钩不得与护网发生干涉。
2.5.14设备运行噪音小于60分贝。
2.5.15自行小车具备积放功能。
2.5.16自行小车I线的发车等待工位和自行小车II线的接、发车等待工位(共3个)均可手动控制实现车身的临时上/下线功能。
满足异常情况时发生时车身临时下/上线的需求。
2.5.17自行小车I线第3工位和自行小车II线第9工位需要设置手动选择空壳放行和总成放行开关。
a)选择空壳放行后,小车在发车工位高位等待后自动前进;b)选择总成放行后,小车在发车工位低位等待后,通过完工信号控制小车前进。
2.5.18自行小车II线上的接车工位能够依据系统指示分别向内饰滑板线和自行小车I线的发车工位发出要车信号。
3工厂条件:
3.1电流种类及电压:
380V±15%交流;
3.2压缩空气压力:
0.5~0.7MPa;
3.3上水水质及压力:
压力0.1~0.15MPa;
3.4厂房温度与湿度:
温度-10~40℃,湿度40%~80%
3.5屋架下弦高度:
10.7m;
3.6照明条件:
150Lx~300Lx;
3.7地坪及承载能力:
道路区80KPa,其它50KPa。
4设备功能及结构技术要求:
4.1主要零部件的功能及技术要求
4.1.1自行小车:
采用双葫芦型,小车的电机减速机选用德国SEW产品,带有排障离合装置。
小车组承载能力为2t。
4.1.2车组数量:
12+22=34组。
(供应商可依据节拍计算进行建议)
4.1.3小车速度:
运行速度:
0-30m/min,可变频调速,小车随车带电气控制箱,设置手动控制选择按钮。
4.1.4电动环链葫芦:
数量:
68台
提升速度:
快速8m/min,慢速2m/min
提升行程:
9m
单台葫芦额定载重量:
T=1.6t
4.1.5吊具:
主钩吊挂左、右车门框上边缘,辅钩吊挂车身后围,可适用于2.1所列车型,不得造成车身本体变形、划伤。
4.1.6吊具的数量:
12+22=34套
4.1.7轨道:
采用高强度铝合金轨道(使用寿命10年)。
轨道长度:
自行小车I轨道长度约150m,
自行小车II轨道长度约280m,
自行小车I、II连线轨道产度约50m
4.1.8滑触线和集电器:
滑触线和集电器选用性价比高优质品牌。
4.1.9安全护网下底面标高4.5m,宽度不小于5m
4.2控制系统的功能及技术要求:
车身自行小车装配、输送电气控制系统的设计、制造、安装、选型必须依据内饰传输工艺、内饰装配设备、设备维护、设备管理、生产节拍、物流、及机械化传输设备等功能要求进行;并遵循国家相关电气标准、法规及环保等要求;同时必须保证工艺参数控制准确,调整方便,工艺设备及机械化传输设备运行安全、稳定、可靠。
能在现有环境下保证生产的连续和产品的质量。
4.2.1设计要求(各执行单元均采用自动控制方式+手动控制方式)
1)设备电气控制采用可编程序控制器(PLC)及现场总线控制。
2)电气控制系统的设计、控制元器件的选择必须保证节能要求,达到最好的节能效果。
3)各种仪器、仪表、检测装置,应选用规格合理、灵敏可靠、易于辨识的产品。
4)电气设备及元件应安全、可靠,便于操作、安装、维修及更换。
5)电气设备本身不允许存在火灾和安全隐患。
停电时不应发生任何危险,不会出现误动作、短路、控制程序紊乱、控制数据丢失等现象。
恢复供电时,机械设备不能自行起动,安全保护电路应通过复位操作才能再起动。
6)对存在发生伤害事故隐患的设备,应采取有效的防护措施,设警示标志,并确保在操作人员进入危险区时设备自动停止。
7)设备应设计可靠的限位装置。
对可能因超负荷发生损坏的部件应设计超负荷保护装置。
8)电气设计必须充分考虑电磁干扰等特殊环境的要求,保证控制系统软、硬件运行稳定。
9)继电器、接触器类产品在设备调试运行后,应至少还备用1个常闭(NO)、1个常开(NC)辅助触点。
10)控制电路采用隔离变压器与动力电路相隔离。
11)选用的电气设备及元件的噪音不能高于60分贝。
12)设备接地电阻应符合国标电工要求,接地可靠。
13)控制柜防护等级为:
IP54(不包括通风口),通风出入口防护等级为:
IP33。
14)在安有可编程序控制器(PLC)主机的控制柜中间易于编程操作的部位应安装编程操作支架,每组控制柜必须至少有1组单相及三相电源插座。
15)控制柜必须设置降温装置(考虑排水),确保控制柜内温度不大于35摄氏度。
通风口必须加过滤网。
16)控制线路采用线槽或桥架安装方式。
控制电缆留有5%的备用线。
17)行线槽内动力电缆和控制电缆(如:
光电开关、接近开关等)分开,保证控制的稳定性和安全性。
18)对现场所有的开关(如:
行程开关、光电开关、光幕等)及执行元件(如:
电机、阀组等)应有铝制标牌,内容包括:
元件号、输入或输出地址号。
19)随车控制箱面板部分应布置在检修通廊侧。
4.2.2电器元件
电器元件的选择必须考虑电磁干扰等特殊环境的要求;电器元件,必须采用灵敏可靠,质量优异,性价比高的产品。
4.2.3可编程序控制器(PLC)
采用PLC控制+变频调速,指定AB品牌的PLC和AB品牌的变频器,符合以下要求:
1)通信接口要求:
每个可编程序控制器(PLC)控制系统必须提供1个编程口,1个工业以太网通讯口和1个人机界面接口。
2)每个可编程序控制器(PLC)控制系统在验收时必须保证以下预留量:
a)I/O点输入、输出各按实际使用配置I/O总点数的20%以上。
且预留I/O点为独立的组(有公共端)。
b)机板至少有2个及以上空槽。
c)存储器剩余可编程空间不少于总存储容量的30%。
d)所有可编程序控制器(PLC)内部资源(如:
定时器、计数器、过程标志位、数据存储区等)剩余可编程空间不少于总存储容量的20%,且剩余空间必须为连续地址空间或分段连续的地址空间。
e)PLC系统包括相关附件:
备用电池、存储器、专用适配器、编程电缆、通信电缆、编程软件及授权盘等。
3)可编程序控制器(PLC)软件设计规定:
可编程序控制器(PLC)编程软件必须为最高版本,控制程序为结构化程序设计,通过子程序或功能块间的调用来实现控制系统功能,严禁全程线性编程。
4)控制程序注释要求:
a)所有I/O地址、过程标志位等必须加地址注释以说明该地址的作用。
b)所有I/O地址必须加符号地址,符号地址必须对应原理图中元件号。
c)控制程序应加注各种注释。
验收时交付的控制程序文件中注释语言必须为汉语
4.2.4控制系统需具备状态监测的功能,能对自行小车装配、输送线进行动态监控;控制柜采用AB触摸屏(14英寸)的人机操作界面(提供编程电缆和软件)进行实时监测和相关参数修改。
能显示设备运行状态和该线体各小车上是否有车及车型、颜色的实时信息,同时可实时显示各类故障信息(出现故障时要求声光提示,方便维修)。
电控柜设置编程用插座,供编程电脑使用,同时电柜设置照明灯;控制柜低压电气元件选用施耐德产品;具有以太网络通讯接口和信息采集功能,遵守OPC协议,能将采集的信息送入OPC接口,并与MES系统联合调试。
控制柜考虑在装配线边靠柱放置(具体位置现场定)。
4.3小车控制方式:
4.3.1自行小车在行走启动和停止时要求平稳,分为低速启动、高速行走、低速缓冲、停止四个阶段。
在装配轨段自行小车平均速度约为15米/分钟,空车返回轨段平均速度约为25米/分钟。
4.3.2小车进入弯道前应减速,进入直线端后应加速。
4.3.3检修段:
1)进入检修段的道岔设手动控制和自动控制两种,在检修段内小车可进行前进、后退、上升、下降、吊具开合。
2)当线上出现故障小车组后,可用自行小车上的按钮盒将该车组导入检修段;若该车组已不能行走,可用拨杆松开行走电机尾端的离合器手柄,将该车组在线体停电状态下拉入检修段进行维修。
4.3.4内饰底部装配自行小车线每个装配工位应设置自锁式急停按钮、完工按钮、撤消完工按钮、求援按钮、完工/求援信号灯、手动/自动选择开关。
自行小车I、II线装配等待工位除上述按钮外另外具备手动控制小车前进、后退、上升、下降、吊具开合的功能按钮。
小车的前进需要前一车位的空车信号和本工位的完工信号共同控制。
4.3.5自行小车装配工位要有保护装置在手动控制方式下的动作操作按钮。
4.3.6自行小车I线发车工位
a)在车身低位等待时的前进动作需要由本工位的完工按钮和自行小车II线接车工位的空位信号共同控制;
b)在车身高位等待时的前进动作由滑板线接车工位的空位信号进行控制。
4.3.7每台小车上都有一套相对独立的电气控制箱,包含以下内容:
1)面板上有电源开关
2)左右及下侧面装有:
(具有防错插的措施)
a)集电器用插座接头
b)行走电机控制用插座接头
c)升降电机控制用插座接头
d)磁簧开关用插座接头
e)积放保护开关用插座接头
f)二个定位检测开关用插座接头
g)手动控制按钮盒用插座接头
h)夹持终点开关,光电开关,插座接头
i)夹持电机控制用插座接头
j)小车在各工位的位置识别传感器用插座接头
3)车体装有的信号:
k)升极限开关
l)前进积放开关
m)小车行走加减速开关(磁性控制)
n)小车定位开关
o)小车升降位置控制开关组件
p)检测有/无工件的光电传感器
q)小车在各工位的位置识别传感器
4.3.8检修段装有操作按钮站,有如下操作功能:
自锁式紧停按钮叫车
1)自锁式紧停按钮
2)检修/正常(二位置旋钮)
3)前进/后退(按钮)
4)上/下(按钮)
5)快慢转换(二位置旋钮)
6)夹持松开/合拢(按钮)
4.3.9配有小车手动控制按钮盒可随时安装连接到小车上,能手动执行:
前进/后退
升/降
夹持松开/合拢
选择自动/手动行走方式
4.3.10装配线在开始运行前,发声光信号提示,并延时5秒钟后启动。
4.3.11电控柜四周设置安全防护栏。
4.4环保、安全与防护技术要求:
4.4.1一般性要求:
对人的安全、防护、辐射等劳动保护条款符合非标制造国家和行业相关标准。
4.4.2设备的设计要符合中国国家或ISO标准。
4.4.3主要设备按国际通用标准,且各种防护保护要有连锁保护开关。
4.4.4全线设计达到国家相关安全和环境标准,并设置固定防护栏。
同时要求有防止滑撬冲出设备的安全装置。
4.4.5防护装置、安全部件的布置、规格符合中国国家标准。
4.4.6控制柜油漆和颜色为珍珠白,设备本体颜色见《联合工厂色彩管理方案》;
4.4.7对施工完毕后发现的安全问题,施工方按要求限期整改。
4.4.8设计、改造达到国家相关安全和环境标准:
1)国家电气设备安全技术规范(GB19517-2009)
2)电气设备安全设计导则GB4064-1983
3)生产设备安全卫生设计导则(GB5083-1999)
4)机械防护安全距离(GB12265-1990)
5)固定式钢梯及平台安全要求第3部分:
工业防护栏杆及钢平台(GB4053.3-2009)
6)起重机械吊具与索具安全规程LD48-1993
7)机械安全防止上下肢触及危险区的安全距离(GB23821-2009)
8)机械安全避免人体各部位挤压的最小间距(GB12265.3-1997)
9)机械安全进入机器和工业设备的固定设施第2部分:
工作平台和通道(GB17888.2-2008)
4.4.9安全装置(投标时详细说明)
1)线体要求设置车身安全防脱落装置及吊具框架防脱落装置
2)自行小车是悬挂运动件,各运动件应有防坠落安全保障及安全防护措施
3)线体在通过非装配区域及通道均设置安全网,确保安全。
4)底部装配高位在车身正下方必须有底部防护,确保车身脱落后不砸到人。
5备件和易损件技术要求:
5.1备件按投标总价3%考虑,并在投标时提交明细(附在标书里)。
最终选用的备件和易损件明细,必须要用户认可
5.2所有提供的备件和易损件必须为原厂生产的产品,型号规格要与设备上的型号规格一致。
5.3提供完整的外购设备随机易损件。
5.4设备交付时提供备件、易损件清单和易损件一套,并确保能长期提供备件。
6技术资料:
6.1在技术协议签订后一周内,提供设备基础图;
6.2需提供技术资料的明细:
提供竣工图纸资料,设备技术规格、安全操作规程、操作说明书、设备结构图(完整的结构图、零部件图和明细表)、电控图纸及相应软件资料、易损件清单等;
6.3技术资料的语言、格式及份数要求:
要求中文版,电子资料一份,纸质资料四套;
6.4设备外购件的有关要求:
提供使用说明书和外购件采购途径;
6.5其它特殊要求:
无
7设计认可(图纸会签):
7.1明确需设计认可的项目:
结构总图及电气控制图会签,评标前提供达到施工图标准的设计图纸;
7.2明确设计认可的时间、人员、费用:
双方技术人员;
7.3设计认可后的相关资料交付时间:
设计认可会签后十天之内;
7.4其它要求:
评审图纸中含易损件清单;
8人员培训及服务
8.1明确培训时间、地点、对象、费用和次数:
设备安装调试后、正式使用之前,在设备安装现场免费对使用方技术人员、操作人员及设备维护人员分别进行培训,并提供培训资料;
8.2培训内容规定:
供应商技术人员分别对使用方技术人员、操作人员及设备维护人员进行设备操作及设备维修技术方面的培训;
8.3培训效果:
被培训人员应基本掌握上述各项技能基本使用和维护能力,如不能有效掌握时应增加培训次数。
9设备包装、发运:
9.1包装规定:
供应商负责包装
9.2运输规定:
运输规定:
供应商负责运输、卸货至安装地点及保管;
10设备安装调试:
10.1设备出厂之前,使用方代表到制造厂家参与出厂验收;
10.2设备到达后,应由供应商代表和使用方代表在现场共同开箱,并确认设备、附件及备件(配件)是否与清单相符,双方确认签字后方可进行设备安装;
10.3供应商技术人员在使用方相关人员的配合下,进行设备基础及设备安装(设备安装位置详见工艺设备安装图);
10.4安装应达到“平、稳、正、全、牢、灵、通”。
1)平。
设备底座与基准面、设备的导轨面、其他测量平面与设备基准面不平度必须达到设备安装要求的标准。
2)稳。
设备与基础、设备各部件之间的连接要稳固,试车时不能出现移动、摆动、跳动和颤动等现象。
3)正。
设备各测量部位与基准面、基准线或各测量部位之间的形位公差及其他配合尺寸,应严格按原设计中所规定的安装标准安装。
4)全。