12MW汽轮发电机组规格书.docx
《12MW汽轮发电机组规格书.docx》由会员分享,可在线阅读,更多相关《12MW汽轮发电机组规格书.docx(45页珍藏版)》请在冰豆网上搜索。
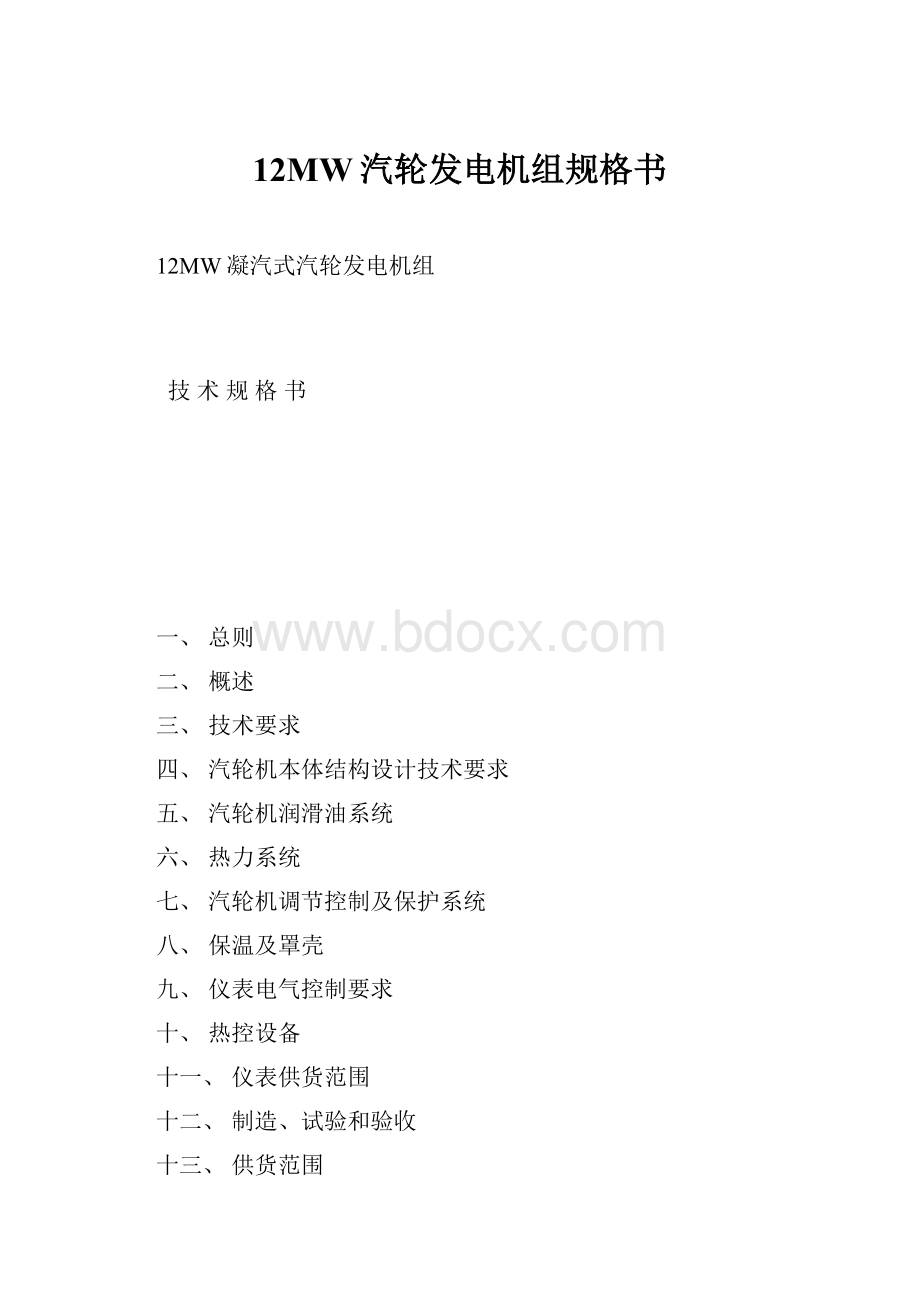
12MW汽轮发电机组规格书
12MW凝汽式汽轮发电机组
技术规格书
一、总则
二、概述
三、技术要求
四、汽轮机本体结构设计技术要求
五、汽轮机润滑油系统
六、热力系统
七、汽轮机调节控制及保护系统
八、保温及罩壳
九、仪表电气控制要求
十、热控设备
十一、仪表供货范围
十二、制造、试验和验收
十三、供货范围
十四、技术资料
十五、发电机
一、总则
1、本技术协议适用于1×12MW(发电机端最大输出功率为12MW)余热发电项目的汽轮机及其配套系统,提出了设备和系统的功能设计、结构、性能试验等方面的技术要求。
2、买方在技术协议中提出了最低限度的技术要求,并未规定所有的技术要求和适用的标准,卖方应提供满足本招标文件和所列标准要求的高质量产品及其相应服务。
对国家有关安全监察、环境保护等强制性标准,必须满足其要求。
3、本技术协议发出之后,如果买方有需要补充或说明的事项,将以书面形式提出,与本技术协议具有同等效力。
4、如未对本技术协议提出偏差,将认为卖方提供的设备符合技术协议中的要求,偏差(无论多少)都必须清楚地表示在附后的差异表中。
5、在签订合同之后,买方有权提出因规范标准和规程发生变化而产生的一些补充要求,具体项目由合同双方共同商定。
6、卖方须执行本技术协议中所列标准。
有矛盾时,按较高标准执行。
7、卖方中标并签定合同后,本技术协议将作为合同的附件,与合同正文具有同等效力。
二、概述
(一)、工程装设1台额定功率为12MW的凝汽式汽轮发电机组。
(二)、设备运行环境及厂址条件:
1、设备安装地点:
室内
2、室外历年平均气温:
27℃
(三)、设备使用条件
1、汽轮机运行方式:
定压、滑压运行
2、负荷性质:
基本负荷
3、汽轮机布置:
室内双层布置
4、汽轮机安装:
运转层标高m
5、冷却方式:
冷却塔开式循环水冷却
6、冷却水:
循环水
7、周波变化范围:
48.5~50.5Hz
(四)、主要技术规范
产品型号
额定功率
MW
12
额定转速
r/min
3000
旋转方向
额定进汽压力及变化范围
MPa
0.8±2(绝对)
温度
290±10℃
进汽量
t/h
25~50
排汽压力
Mpa
临界转速
r/min
额定转速时振动值
mm
≤0.03(全振幅)
临界转速时振动值
mm
≤0.15(全振幅)
发电机型号
(五)、供货范围
汽轮机供货范围包括从汽轮机主汽门入口开始,主要包括:
主汽门、调节汽门、主蒸汽管道、汽轮机本体(含垫铁等);冷凝器、排汽接管、射水抽气器、汽封加热器、疏水膨胀箱、汽封蒸汽调节装置、均压箱等;本体范围内的汽封管路、疏水管路及必需附件,润滑油系统(含交直流电动油泵)、调节油系统(含油管路及必需附件),DEH系统、ETS系统、TSI系统、汽轮机本体范围内的就地显示仪表等。
三、技术要求
(一)总技术要求
汽轮机及辅助设备和附件使用的材料、制造工艺、检验测试及性能考核要求,均应符合原机械工业部及原水利电力部标准和相关的企业标准。
汽轮机的主要技术标准如下(但不局限于下列标准,如有更新版本,以最新版本为准):
1)JB/T9627-1999《汽轮机组成套供应范围》
2)JB/T2901-92《汽轮机防锈技术条件》
3)JB/T2900-92《汽轮机油漆技术条件》
4)JB/T2862-92《汽轮机包装技术条件》
5)JB/T1330-91《汽轮发电机组中心标高与连接尺寸》
6)JB/T1329-91《汽轮机与汽轮发电机组连接尺寸》
7)JB4058-85《汽轮机清洁度》
8)GB/T13399-92《汽轮机安全监视装置技术条件》
9)GB12145-89《火力发电机组及蒸汽动力设备水汽质量标准》
10)GB9782-88《汽轮机随机备品备件供应范围》
11)GB8117-87《电站汽轮机热力性能验收试验规程》
12)GB7520-87《汽轮机保温技术条件》
13)GB5578-85《固定式发电用汽轮机技术条件》
所有设备应设计和制造合理,能在规定的各种工况下安全、稳妥和连续运行,并能适应瞬时的事故工况,防止事故扩大或损坏设备。
(二)汽轮机寿命
1、汽轮机使用寿命不小于30年,汽轮机主要零部件寿命和汽轮机相同。
2、汽轮机年连续运行小时数应不小于8000小时,大修周期应不小于3年,小修周期应不小于1年。
3、提供汽轮机的强迫停机率和可用率(年可用率应大于97%)。
年可用率%=(8760小时-计划停机小时数-强迫停机小时数)/
(8760小时-计划停机小时数)×100
4、汽轮机的零部件(不包括易损件)的设计,在其寿命期内应能承受频繁冷热态启停工况。
(三)汽轮机性能要求
1、汽轮机可以在规定的参数范围内连续安全运行;
2、汽轮机可以在60℃排汽温度条件下安全连续运行;
3、汽轮机启动方式为定压启动或滑参数启动,提供汽轮汽轮机启动曲线;
4、汽轮机转子的临界转速应避开工作转速一定范围;
5、汽轮发电汽轮机能满足孤岛运行方式;
6、卖方提供汽轮机允许长期低负荷连续运行;
7、超速试验时,汽机应能在112%额定转速下作空负荷运行(汽轮机可长期空负荷运行),这时任何部件都不应超应力;
8、汽轮机发电机的轴系应能承受发电机突然发生短路,或者非同期合闸产生的扭矩;
9、汽轮机的出力应在发电机出线端测得;
10、叶片在允许的周波变化范围内不产生共振;
11、汽轮机的振动值应符合相关的标准;
12、距汽轮机化妆板及附属设备外1m处所测得的噪声值低于90dB(A);
13、制造厂对汽轮机的振动、临界转速、润滑油系统及靠背轮负责统一归口设计,保证汽轮机的稳定性。
四、汽轮机本体结构设计技术要求
1、汽轮机及所有附属设备应是成熟的、先进的,并具有制造相同容量机组且运行成功的实践经验。
不得使用试验性的设计和部件。
;
2、汽轮机转子为套装式,套装后的转子应彻底消除残余内应力。
转子出厂前进行动平衡试验,其不平衡重量符合相关的标准要求。
3、汽缸的设计考虑因温度梯度造成的变形,始终保持正确的同心度。
缸体有足够的刚度,保证各工况条件下汽轮机运行平稳,外型美观;
4、≥M64的汽缸螺栓设有热紧用加热孔;
5、设有开汽缸用顶开螺栓;
6、汽轮机设有保护汽轮机用的排汽安全装置及防止排汽缸温度高的喷水冷却装置;
7、汽轮机设计应保证在启动和停机过程中其膨胀值、胀差和汽缸的变形都在允许的范围内,汽机本体必须设计上下缸温度测点,以保证机组启动和停机的灵活性。
汽轮机的滑销系统应保证长期运行灵活,运行中无需注入润滑剂。
8、卖方应对所有连接到汽缸上的管道,提出设备所能安全承受的作用力和力矩要求。
9、汽轮机本体设有性能试验时所需要测量装置的接口;
10、汽轮机转子及末级叶片具有抗应力腐蚀及抗湿汽侵蚀措施
11、盘车装置:
a、提供一套完整的电动盘车装置;该装置可就地手动盘车,盘车装置应能就地及远方操纵,盘车能在正常轴承润滑油压下从静止状态启动转子并连续运行。
b、该装置是手动啮合型的,停机转速到零时,可投入盘车装置能使汽轮发电汽轮机从静止状态转动起来,使汽轮机转子均匀冷却,避免热弯曲。
c、交流电动机驱动,盘车系统设压力联锁保护装置防在油压建立前投入盘车。
盘车装置运行中如发生供油中断或油压降低到不安全值时,及时报警,并停止运行。
d、一旦汽轮机启动,达一定转速时,盘车自动退出而不对汽轮机发生撞击,且不重新啮合。
12、汽轮机轴承:
a、汽轮机轴承采用椭圆形式,轴承设计应考虑失稳转速,具有良好抗干扰能力(不产生油膜振荡),轴承的失稳转速大于4000r/min.;
b、任何工况下,各轴承的回油温度不大于65℃,轴承金属温度不大于85℃,但轴承金属材料能长期承受110℃的温度。
;
c、各轴承金属温度测量使用埋入式铂热电阻,设计合理的推力瓦温和轴瓦测点走线,避免机组运行过程中线路出现磨损导致测点断线;
d、推力轴承能持续承受在任何工况下所产生的双向最大推力;
13、汽轮机前、后汽封结构可调整轴向间隙,汽封为新型的梳齿汽封;
14、主汽门和调节汽门
a、主汽门设有永久性蒸汽滤网;
b、主汽门、调节汽阀严密,采用具有高强度的耐热钢材,能承受在主蒸汽管道上做1.5倍设计压力的水压试验;
15、保安系统
a、危急遮断器动作转速:
3270~3330r/min(即:
额定转速的109-111%)
b、危急遮断器复位转速:
额定转速以下
c、电子超速停机转速:
额定转速的108%
16、机组长期、安全运行的最低负荷25t/h
17、机组允许负荷变化率
a.从100%-50%铭牌功率不小于5%/min
b.从50%-20%铭牌功率不小于3%/min
c.从20%以下铭牌功率不小于2%/min
18、其它
●制造厂应对汽轮机至发电机及励磁系统整个轴系的振动、临界转速、润滑油系统及联轴节负责统一归口设计,保证机组的稳定性。
●轴系的临界转速应能保证机组安全升速和进行超速试验。
卖方应提供最大的扭应力和安全系数、扭振频率及各个轴承失稳的转速和各阶临界转速值。
五、汽轮机油系统
汽轮发电机组油系统包含润滑油和DEH控制油系统,两系统配置有各自独立油箱、滤油、冷油和自循环清洁等功能,要求润滑油过滤精度20μ,控制油过滤精度10μ。
油系统设有可靠的主供油设备及辅助供油设备,在启动、停止、正常运行和事故工况下,满足汽轮发电机(汽轮机、发电机、励磁机、盘车装置)所有轴承用油和调节用油要求。
油系统应包括以下各设备:
1、汽轮机主油箱、控制油箱;
2、主油泵、控制油泵(一开一备);
3、交流辅助(启动)油泵;
4、交流润滑油泵;
5、直流润滑油泵
6、冷油器(包括润滑油,和控制油,均是一用一备,且都可在线切换)7、滤油器(包括润滑油,和控制油,均是一用一备,且都可在线切换)
(一)油箱
1、油箱配有就地液位液温计,并设液位指示器,可远传,并有高、低油位报警;
2、油箱容量考虑当厂用交流电失电时,冷油器断水的情况下保证安全惰走、停机,油箱中的油温不超过80℃;
3、主油箱上设置一台全容量排烟风机和除雾装置;
4、油箱所有接口可以防止外部水(如消防水)及其它杂物漏入;
5、油箱底部设有放油、排污门;油箱直接布置在油站上。
6、油箱内部设置回油滤油网;在油箱至电动油泵入口的出口处设置可拆式滤油器。
7、油箱设检修孔,油箱底部设有放油闸门。
(二)油泵
1、主油泵为离心油泵,直接安装在汽轮机轴上,工作可靠,运行平稳;系统设计须保证泵内不发生汽蚀现象。
2、全容量交流辅助(启动)油泵,用于汽轮机发电机组起动时供油;全容量交流辅助油泵应带有压力调节装置及自动启动装置。
不管油压是否降低,交流辅助油泵在汽轮机跳闸时应当立即启动。
交流油泵压力开关被用作附加信号,无论汽轮机跳闸与否,在系统油压低时,自动启动事故油泵。
3、交、直流事故油泵为事故状态下供润滑油,有足够容量满足机组停机要求。
事故油泵带有自启动装置,在润滑油压低时自动投入。
4、全容量控制油泵,用于DEH转速控制系统的调节用油,全容量控制油泵应带有压力调节装置及自动启动装置,实现出口油压调节及低油压备用泵自启。
(三)冷油器:
双联冷油器(管壳式,水走管程)
●设两台全容量100%的双联冷油器,一台工作,一台备用(冷却水温过高时可并联使用,设计最高冷却水温为35℃);油侧进口及出口为法兰连接,法兰规范按照中国标准。
●冷油器在设计冷却水量、入口冷却水温度达35°C、水侧清洁系数为0.85。
管子堵塞5%情况下,可满足机组的最大负荷供油温度要求。
●冷油器为浮头直管式结构,全部管束可以整体抽出,冷油器内管束采用45°错列布置,禁止使用鳍片管。
●润滑油冷油器垂直安装,便于拆卸,冷油器设置手动放水及排气阀。
●冷油器便于在汽轮机运行时将任一台冷油器投入工作而另一台冷油器脱离系统。
阀门的布置要合理,方便拆卸,且不使两个冷油器水管并联两只滤网,能互为切换与清洗。
冷油器的技术性能:
冷油器
型号
台数
台
2
冷却面积
m2
换热元件材质
0Cr18Ni9
(四)滤油器
1、润滑油管路设置100%双联滤油器,滤油精度:
15μm,滤油器配置前、后压差表,当滤芯堵塞,压差大于规定值时可在线进行切换,以便清洗或更换滤芯。
2、控制油管路设置100%双联滤油器,滤油精度:
10μm,滤油器配置前、后压差表,当滤芯堵塞,压差大于规定值时可在线进行切换,以便清洗或更换滤芯。
(五)油系统设备与管道
1、汽轮机在结构和系统设计上有防止汽水由于轴封漏气等进入油系统的措施。
2、油系统中各设备(如轴承箱、冷油器、油箱和管道等)在出厂前彻底清除残砂、焊渣、锈片等沾污物质,并经防腐蚀处理,妥善密封后出厂。
3、机组的油系统应确保机组的启动,停机以及正常运行和事故状态的供油要求,并包括主油箱、控制油箱、主油泵、辅助油泵、事故油泵、控制油泵、全容量的冷油器(一用一备)、全容量的滤油器(一用一备)、仪表以及供给每个用油点所必须的辅助设备和管道。
4、油系统设有低压力开关,并设有低压报警装置,油压进入控制系统监视,油系统包括整套的管道、阀门、滤油器、相关的仪表及其它辅助设备等;所有油管路采用不锈钢。
5、油管道采用强度足够的厚壁管,至少按两倍工作压力进行设计,并且管道最低设计压力等级不低于2.5MPa。
管道附件也按相同压力等级进行设计。
尽量减少法兰及管接头数量,法兰采用对焊法兰,油系统中的附件不使用铸铁件。
6、油系统的设计及布置考虑防火措施。
蒸汽管道或其它热的表面不能布置在油动机或其它盛油设备的下方或附近。
对靠近高温蒸汽管道的油管道应采用隔离措施。
7、所有的油管道布置尽可能避免被撞击、踩踏。
其它设备或管道不允许悬挂在油管上。
六、热力系统
热力系统的主要设备有:
凝汽器、汽封管路、疏水管路、射水抽气器、抽空气管路以及主蒸汽的汽水分离器等组成。
(一)凝汽器
1、凝汽器的设计应满足《汽轮机凝汽器技术条件》标准;
2、每台汽轮机配置一台凝汽器,凝汽器的设计对循环水温度38℃时,凝汽器的压力在允许的范围内进行校核。
在低负荷工况和满负荷工况运行时,凝结水的含氧量符合水汽质量标准;
3、凝汽器的管子和管板材料应充分考虑循环水的腐蚀,选用合适的材料或采取相应的防腐措施;
4、凝汽器采用焊接结构,其强度和刚度能承受管道的附加荷载,防止汽轮机传递来的冲击和共振;有合适的设施允许凝汽器膨胀自如,凝汽器采用弹性支承,凝汽器内的水重量不作用在汽缸上;
5、凝汽器冷却水双进双出,以开式冷却塔作为冷却水源,可以满足在最高冷却水温时,汽轮机发铭牌功率时的背压要求。
6、凝汽器的设计和制造按国内有关标准执行,设计水流速不大于2m/s,清洁系数按0.9设计,循环水进出口温升应小于9°C。
冷凝器的堵管率应小于5%,在TRL工况运行时,凝汽器出口凝结水的过冷度不大于0.5℃
7、凝汽器应有足够的抽真空设备(射水抽气器),满足汽轮机正常运行的要求,从大气压状态下抽气到机组冲转时间应≤30分钟。
8、凝汽器的每个水室设人孔门,并有适当的放气和放水接头。
凝结系统严密不漏汽,真空下降速度不大于666Pa/min,凝汽器水室和冷却水管束应能承受的压力为0.34MPa(a);
9、凝汽器热井设就地水位计并输出4~20mA信号;
10、凝汽器的技术性能:
凝汽器
型式
二流程表面式
冷却面积
m2
冷却水温
℃
额定27℃,夏季最高38℃
冷却水设计压力
MPa
冷却水水阻
m
管子材料
HSn70-1
管子规格
mm
(二)汽封系统
汽封系统具备完善的汽封蒸汽系统和设备,包括汽封自立式压力调节阀、轴封冷却器及其辅助设备等,防止运行中,高压蒸汽从轴端漏入大气或串入轴承箱,防止空气从低压轴端漏入真空部分。
1、轴封用汽可来源于抽汽、厂内辅助蒸汽或主蒸汽减温减压。
2、在轴封系统的入口设永久性滤网,系统中设置1台100%容量轴封冷却器,设100%容量轴流抽风机。
3、汽封系统包括均压箱、自动调节阀、旁路阀、管道等有关附属设备。
4、汽封系统设置自动的汽封蒸汽调压装置,用以调节汽封蒸汽的压力,以满足各汽封的供汽参数要求;卖方提供完整的汽封系统所要求的其它组件。
5、提供汽封系统用管路和阀门,包括均压箱、轴封冷却器。
6、轴封冷却器的技术性能:
轴封冷却器
型式
表面式
台数
台
1
传热面积
m2
水侧压力(max.)
MPa
冷却水量
t/h
管子材质
HSn70-1A
(三)疏水系统
1、汽轮机本体疏水系统须能排出所有汽轮机本体设备包括管道和阀门内的凝结水。
系统能使随时可能投入运行的设备经常处于热备用状态。
2、汽轮机汽缸提供足够数量的疏水点以能彻底疏水及预热。
(四)凝汽系统
主要由凝汽器、凝结水泵、射水抽气器、抽空气管路及管路内的阀门和相关的附件。
射水抽气器的技术性能:
射水
抽气器
型号
台数
台
2
工作水压力
Mpa
工作水量
T/h
抽气量
Kg/h
(五)主蒸汽管道系统
●卖方提供自主汽门与汽机进汽室间的管道,其设计满足运行条件。
●主蒸汽关断阀及应严密不漏,使主蒸汽管道能够进行水压试验。
●主蒸汽过滤器为固定式,能承受外来杂质的冲击。
七、汽轮机调节控制及保护系统
(一)汽轮机调速控制系统
1、汽轮机调速系统采用DEH,卖方提供远方控制汽轮机负荷的手段,并在故障时有危急保安措施,提供汽轮机安全监视仪表(汽缸热膨胀,监视段压力表。
轴向位移,轴承振动,转速和凝汽器真空)等。
2、汽轮机甩额定负荷时危急遮断器不动作,并能维持转速为3210r/min左右。
3、启动升速及转速控制和保护:
控制系统根据预先给定的升速率、暖机速率和暖机时间自动改变转速调节的给定值,使汽轮机由盘车状态以设定升速率平衡地升速至额定转速。
升速率、暖机转速和暖机时间可以由运行人员选定或由控制系统根据汽轮机的状态自动确定亦可自动或手动启动。
4、超速保护试验:
在DEH控制下可进行电超速保护试验,机械超速保护试验。
具有超速保护(109%)功能。
5、同步及自动初负荷控制:
机组定速后,可由运行人员通过手动或“自动准同期”装置发出的转速增减信号调整机组转速以便并网。
机组并网后,DEH立即自动使机组带上一定的初负荷以防止机组逆功率运行。
6、负荷控制:
DEH系统能在汽轮发电机并入电网后可根据运行情况或电厂运行规程,运行人员通过操作控制器转速设定控制汽轮发电机从带初始负荷直到带满负荷,并应能根据电网要求,参与一次调频。
系统具有开环和闭环两种控制方式去改变或维持汽轮发电机的负荷。
开环控制根据转速给定值及频差信号确定阀门的开度指令。
该种方式即为阀位控制方式。
闭环控制则以汽轮发电机的实发功率作为反馈信号进行负荷自动调节。
该种方式即为功频控制方式。
功频调节采用不等率控制,不等率的设定值为3-6%,可调。
7、甩负荷控制:
当机组甩负荷时控制器切换到转速控制方式并切除功率和抽汽控制。
维持汽轮机在同步转速(2950r/min)下空转,以便汽机能迅速重新并网。
8、辅助控制和串级控制:
辅助PID控制器和串级PID控制可以组态为控制汽轮机的进汽压力、排汽压力等参数。
9、操作及通讯:
所有控制指令可以通过控制器本身键盘、触点、遥控或通讯方式。
控制器配备有RS-232、RS422、RS485三种通讯接口供用户选择与DCS通讯。
通讯协议采用MODBUS协议。
硬接线开关量采用干接点,模拟量采用4-20mA。
所有控制指令可以通过控制器本身键盘,遥控或通讯方式输入。
10、技术规范:
转速控制范围:
40~3390r/min(根据机组安全,上界定为3390r/min)
转速控制精度:
±1.5r/min
负荷控制范围:
0~120%
负荷控制精度:
≤1%额定负载
速度不等率:
3~6%连续可调
系统迟缓率:
≤0.2%
转速超调量:
≤7%
系统响应时间:
≤50ms
系统可用率:
99.99%
11、DEH系统的一些重要参数需要进入控制系统监视:
例如二次油压、505输出监视等
(二)保护装置
1、汽轮机必须设有成熟可靠的危急保安系统,防止超速;汽轮机危急保安系统的跳闸系统有联锁保护,防止汽轮机突然再进汽。
2、汽机自动保护装置应能在下列条件下(但不限于)关闭主汽门和调节汽门,紧急停机。
●汽轮机的转速超过设定转速(电子跳闸转速为额定转速的1.08倍,由505发出)
●TSI系统发出电超速信号跳机(发出三个开关量至控制系统,控制系统三取二)
●汽机的转速超过危急保安器动作转速(危急保安器动作转速为额定转速的1.09-1.11倍)
●润滑油压下降超过极限值(压力开关三取二),控制油压下降超过极限值
●轴承温度超过极限值
●转子轴向位移超过极限值
●汽机振动达到危险值
●DEH故障
●发电机主保护动作
●手动停机
●冷凝器真空低(压力开关三取二)
3、不单独配置ETS保护装置,由控制系统实现ETS保护
4、当汽轮机具备再次启动条件时,只有按照启动前的规定操作程序才能使跳闸系统重新复位。
5、从危急保安器动作到主汽阀完全关闭的时间0.5秒。
6、汽轮机组可分别在主控制室操作盘及就地手动实现紧急停机操作。
7、TSI系统需要跳机和报警的信号,如:
转速、振动、胀差、轴位移等信号都必须由TSI产生一个开关量输出至控制系统。
八、保温及罩壳
1、卖方负责汽轮机本体及主蒸汽管道的保温设计说明,在正常运行情况下,在环境温度27℃时,汽轮机保温层表面温度不超过50℃;
2、卖方提供在平台以上的汽轮机部分壳体装饰罩壳,一直延伸至楼板抹面。
卖方完成保温罩达到生根(铁板,凹槽),以使护罩连接于抹面后的楼板上。
九、仪表要求
仪表设备选型:
本着技术、装备的成熟性、可靠性、先进性、实用性原则,仪表设备主要选型要求如下:
1、智能变送器
智能变送器采用罗斯蒙特、横河川仪EJA、霍尼韦尔并带现场数字显示表装置,配置2台智能终端手操器,具体要求:
HART协议数字通迅
.智能性、两线制,4~20mA,DC。
.零点可迁移,易于量程调整。
.差压变送器应具有单向耐全压的能力。
2、执行器
.电动执行器采用一体化智能电子式;
.电机过热保护功能(设定值大于120℃);
.电机过流保护功能;
.电子式动态制动功能;
.就地手动操作功能;
.防电磁干扰;
.控制信号/阀位信号为4~20MA,电源220VAC,50HZ,首先湖南力升LSDZ系列产品。
3、电动调节阀
.汽水系统上的调节阀全部采用原装进口HORA、FISHER调节阀,
.电动执行机构配用drehmo智能一体化电动执行机构,动作频次1200