选矿厂工艺流程设计.docx
《选矿厂工艺流程设计.docx》由会员分享,可在线阅读,更多相关《选矿厂工艺流程设计.docx(16页珍藏版)》请在冰豆网上搜索。
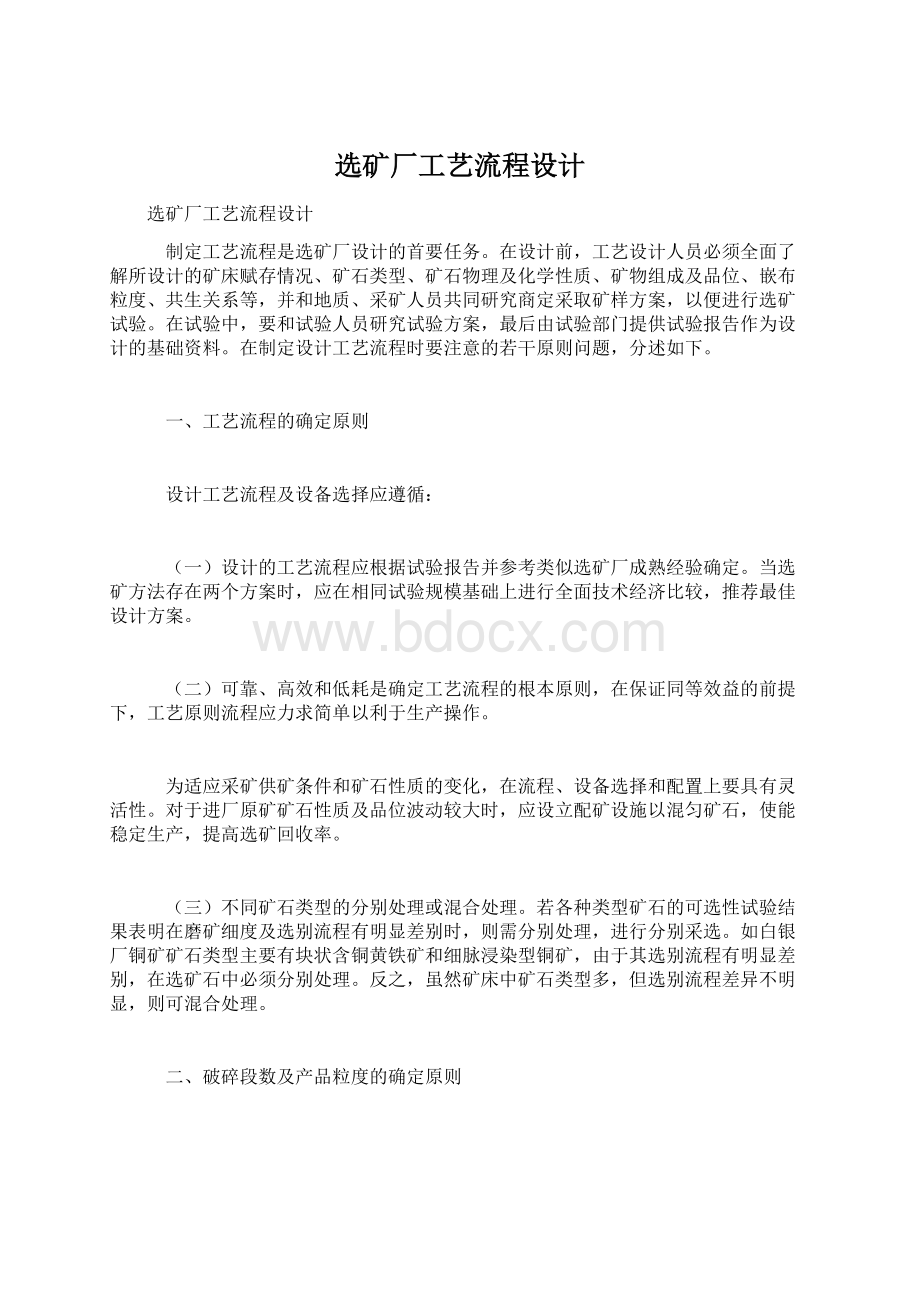
选矿厂工艺流程设计
选矿厂工艺流程设计
制定工艺流程是选矿厂设计的首要任务。
在设计前,工艺设计人员必须全面了解所设计的矿床赋存情况、矿石类型、矿石物理及化学性质、矿物组成及品位、嵌布粒度、共生关系等,并和地质、采矿人员共同研究商定采取矿样方案,以便进行选矿试验。
在试验中,要和试验人员研究试验方案,最后由试验部门提供试验报告作为设计的基础资料。
在制定设计工艺流程时要注意的若干原则问题,分述如下。
一、工艺流程的确定原则
设计工艺流程及设备选择应遵循:
(一)设计的工艺流程应根据试验报告并参考类似选矿厂成熟经验确定。
当选矿方法存在两个方案时,应在相同试验规模基础上进行全面技术经济比较,推荐最佳设计方案。
(二)可靠、高效和低耗是确定工艺流程的根本原则,在保证同等效益的前提下,工艺原则流程应力求简单以利于生产操作。
为适应采矿供矿条件和矿石性质的变化,在流程、设备选择和配置上要具有灵活性。
对于进厂原矿矿石性质及品位波动较大时,应设立配矿设施以混匀矿石,使能稳定生产,提高选矿回收率。
(三)不同矿石类型的分别处理或混合处理。
若各种类型矿石的可选性试验结果表明在磨矿细度及选别流程有明显差别时,则需分别处理,进行分别采选。
如白银厂铜矿矿石类型主要有块状含铜黄铁矿和细脉浸染型铜矿,由于其选别流程有明显差别,在选矿石中必须分别处理。
反之,虽然矿床中矿石类型多,但选别流程差异不明显,则可混合处理。
二、破碎段数及产品粒度的确定原则
破碎段数主要取决于采矿场来矿的最大块度和选矿厂破碎产品最终粒度。
它与矿床赋存条件、矿山规模、采矿方法及装运设备等有关。
最终产品粒度视选矿厂磨矿流程而定。
采用常规碎磨流程时,露天开采和大型坑内矿山的来矿块度大,一般为三段破碎;小型坑内矿山常采用两段破碎。
如果矿石硬度大,根据最终破碎粒度要求也可以考虑四段破碎。
常规碎磨流程的破碎产品粒度的确定,由于破碎较磨矿效率高、费用低、能耗低、因此应遵循“多碎少磨”的原则,尽可能降低破碎产品粒度。
一般为-10~-15毫米。
最终一段破碎即细碎以闭距破碎为宜。
使用棒磨机为开路作业时,破碎产品粒度一般控制在15~20毫米;当破碎含泥量多的矿石时,产品粒度可适当放大到20~25毫米。
砾磨机一般用作研磨棒磨产品或球磨机、半自磨机的产品。
所需磨矿介质,一般从破碎流程分出40~100毫米粒级矿石供砾磨机使用。
采用自磨、半自磨流程时,矿石采用一段破碎到350毫米以下。
破碎产品直接供选别时,可根据矿石的解离度及不同工艺设备的入选粒度要求而定。
一般给入跳汰选矿为-20毫米;重介质选矿为-25,+3毫米,静态重介质选矿可到100毫米。
当要求破碎产品作为成品时,可根据用户要求来确定产品粒度。
三、洗矿作业的选定条件
选矿厂考虑洗矿作业有如下条件:
(一)矿石含泥量多、水分大时,必须考虑洗矿,以利破碎筛分作业的正常进行,防止破碎机及筛子的堵塞。
(二)矿石进行预选(如手选、光电选、重介质选矿)前需要洗矿。
手选、光电选是利用矿物和脉石、围岩颜色的不同进行选别的,所以必须预先洗除污泥,使矿石色泽清楚。
重介质选矿时,为降低矿浆粘度、提高选别效果,亦须预选洗矿。
(三)某些矿床,如沉积型铁锰矿床,洗矿是一种选别方法,通过洗矿脱泥使用有用矿物提高品位而获得合格产品。
又如天然硅砂,通常只需经洗矿、筛分(或分级)便可获得合格产品。
(四)有色金属、贵金属、稀有金属、金刚石的砂矿,大多数需要洗矿。
(五)有的太石含泥并有可溶性金属盐类,洗矿后可以回收溶解金属。
(六)特大型选矿厂,若采用洗矿作业导致工序复杂、难于管理,因此,往往在中碎前采用重型振动筛,筛出粉矿部分直接进入粉矿仓,以避免使用洗矿作业,从而简化了破碎流程。
如布干维尔(Bougainville)选矿厂用2.4×6米重型筛筛出泥矿直接运到粉矿仓,没有设置洗矿作业。
(七)对于难洗矿泥的矿石,可考虑采用半自磨(或自磨)流程来处理。
洗矿设置地点一般在粗碎后进行,但也有在粗碎前使用,少数设在细碎前。
设计时要根据具体情况来决定。
由于泥矿和砂矿性质不同,洗矿后的矿泥一般是单独进行处理,这样可以提高选别效果。
但对于规模较小的矿山且含泥量又不多时,也可考虑将泥矿保并到矿石中一起处理。
设计时应结合矿床赋存条件、矿物组成及矿石物理性质、含泥量多少、采矿方法、运输条件等因素,参考国内外有关实践合理选择洗矿方法和设备。
四、磨矿流程的选择原则
磨矿流程有多种,主要有:
(一)常规磨硫流程,主要有:
1、球磨流程;
2、棒磨-球磨流程;
3、棒磨-砾磨流程。
(二)自磨流程,包括有:
1、一段全自磨流程;
2、自磨-砾磨流程;
3、块磨磨矿流程;
4、自磨-球磨流程;
5、自磨-细破碎-球磨流程(A、B、C、流程);
6、单段半自磨流程;
7、半自磨-球磨流程;
8、半自磨-砾磨流程。
此外,尚有其他多种组合。
在这些流程中生产实践常用的有:
常规磨矿流程,块磨磨矿流程(北欧国家用),半自磨-球磨流程和自磨-细破碎-球磨流程。
我国目前普遍使用的是常规磨矿流程,少数矿山使用自磨流程。
设计欲采用自磨(半自磨)的工艺时,必须根据半工业试验结果与常规碎磨流程进行技术经济方案比较,推荐最佳的碎磨设计方案。
设计常规碎磨注程时,由于破碎效率远比磨矿效率高,所以要遵循尽量降低破碎粒度,提高球磨生产能力的“多碎少磨”的原则。
“多碎少磨”具有下述优点:
1、提高磨矿生产能力降低单位能耗及成本;2、粉矿仓不会发生析离现象;3、磨矿给矿均匀,降低钢球消耗;4、降低噪音;5、减少维修工作量等。
在设计粗磨矿分级回路中使用水力旋流器时,为了减少砂泵及旋流器的磨损必须使用溢流型球磨机,球磨机排矿口需增加一定长度的轴颈筛(圆筒筛),砂泵槽也需采取隔离小球和大矿粒的措施。
在设计棒磨-砾磨流程时,对砾磨排出的顽石需有返回棒磨再磨的措施(如凤凰山选矿厂采用超声波自动控制气动返回棒磨措施)。
设计时注意吸收成熟的选进经验,对于新型磨机品种要进行试验后方可在设计中选用。
设计中研究采用新型衬板及材料如橡胶衬板、角螺旋衬板、磁性衬板等。
研究磨矿介质的形状、质量。
这些均需通过现场实践调查,或经过试验后采用。
选择采用合理先进的分析工艺及高效率分级设备。
一般采用水力旋流器或螺旋分级机分级。
生产实践中的两段分级,第一段磨矿使用直线筛,细磨使用高频细筛等以及其他高效率分级设备。
五、选别流程的确定
选别流程是根据矿石组分,矿石及矿物的物理、化学性质、矿物及脉石嵌布粒度、共生关系等的研究,经过选矿试验而确定的。
有单一选矿流程,如浮选、重选、磁选等;也有联合选矿流程。
如重选-浮选-重选,浮选-磁选、浮选-磁选-重选等。
还有的矿石,为回收其中有益矿物,需要采用机械选矿与化学选矿联合的流程。
(一)浮选流程
1、单金属矿浮选原则流程
单金属矿浮选原则流程的选择,主要取决于矿石中有用矿物的嵌布粒度特性。
一般多为不均嵌布,由于有益矿物和脉石硬度不同,易于泥化,影响回收率,制定选别流程的原则是尽量使用矿物经粗选、扫选得粗精矿或中矿,然后再磨再选,对于嵌布不均的有益矿物在粗磨的条件下能产出部分合格精矿,粗选尾矿进行再磨再选或得粗精矿再磨再选,而得第二种合格精矿。
处理复杂不均嵌布矿石时,由于该类矿石有用矿物嵌布不均,连生体解离范围较广,有时要用三段磨矿三段选别的流程。
处理含大量原生泥和可溶性盐类矿石时,由于矿泥和矿砂选别工艺不一样,一般用泥砂分选流程。
2、多金属矿浮选原则流程
金属矿浮选是指两种有益矿物以上的金属矿浮选,选别流程一般有优选浮选、混合浮选然后分离浮选和优先、混合浮选兼有的选别流程。
如铅锌矿一般有铅锌依次的优先浮选和铅锌混合浮选得混合精矿经再磨(或不再磨)后分离浮选得铅精矿和锌精矿。
又如铜、铅锌、硫化铁的多金属矿,其浮选流程一般为先优先浮选铜铅,进行铜铅分离,优先浮选铜铅的尾矿进行锌、硫混合浮选然后分离锌硫或依次优先浮选锌、硫得锌精矿、硫精矿。
某些矿石可利用矿物的可浮性使用选择性捕收剂优先选出已解离的部分矿物,然后再进行混合浮选、分离浮选。
流程中有否再磨工序,视矿物解离情况而定。
优先浮选和混合浮选的优缺点如下:
(1)混合浮选磨矿细度较直接优先浮选为粗,可节省磨矿费用。
(2)混合浮选的浮选机用量少于优选浮选,浮选药剂也节省些。
(3)优先浮选生产操作较易,容易达到精矿品位,而混合浮选的分离浮选,生产操作较优先浮选困难些。
上述是一般的优缺点比较,多金属矿选别流程要进行试验,对优先、混合浮选的设计方案进行比较选定。
(二)重选流程
重力选矿在国内外仍广为应用,我国钨、锡选矿广泛使用重选流程,铁矿石的选别也有采用。
制定重选流程应注意矿物性脆,易于过粉碎的特点,因此要尽量做到“早收多收、早丢多丢、细粒归队、阶段磨矿、分级选别”。
使用重选法进行洗矿、预先丢废,可以提高选矿厂的生产能力,从而降低磨选成本。
在磨矿方面一般采用棒磨,最好与筛子闭路。
进行多段磨矿、多段选别。
由于重选选别设备,对不同粒级适应性和分选效果不同,应注意严格分级,矿砂按粒度归队再分别给入不同选别设备。
应进行粗细分选、贫富分选、难易分选。
矿石用重选处理,一般都是泥砂分选,分别用不同设备处理。
泥矿重选处理是较复杂的。
钨锡矿的矿泥处理,现阶段仍以重选为主,必要时根据矿泥情况辅以浮选、磁选等方法。
细泥重选处于是使用离心选矿机、矿泥摇床、皮带溜槽、横流皮带溜槽等等。
有的联合使用。
(三)磁选流程
磁选是一种有效的选矿方法,根据各种矿物的比磁化系数的差异,用不同磁场强度的磁选机进行磁选,一般大致分为三类:
1、强磁性矿物,比磁化系数大3000×10-6厘米3/克,如磁铁矿、磁黄铁矿等,用弱磁选设备即能有效与脉石矿物分离。
2、中磁性矿物,比磁化系数为500~3000×10-6厘米3/克,如半假象赤铁矿及某些钛铁矿、铬铁矿等,用中磁场磁选设备进行分选。
3、弱磁性矿物,比磁化系数为15~500×10-6厘米3/克,如赤铁矿、褐铁矿、碳酸铁矿、铁锰矿、硬锰矿、菱锰矿、金红石及某些钛铁矿等,用强磁选及其他方法回收。
比磁化系数小于15×10-6厘米3/克为非磁性矿物,如石英、长石、荧石等。
磁选流程要通过试验来选定,对磁选矿石来说,一般大中型磁选厂,当磨矿粒度大于0.2毫米时,常用一段磨矿磁选;小于0.2毫米时,则采用两段磨矿磁选,若在粗磨条件能选出部分合格精矿,则采用阶段磨矿阶段选别的流程。
若在粗磨条件经粗选可以丢弃尾矿,则可用粗磨粗选,粗精矿再磨再选的流程。
矿石中含有弱磁性矿物和强磁性矿物时,可用弱磁-强磁联合流程。
当矿石在块度较大