卡圈零件冲压工艺及模具设计方案.docx
《卡圈零件冲压工艺及模具设计方案.docx》由会员分享,可在线阅读,更多相关《卡圈零件冲压工艺及模具设计方案.docx(21页珍藏版)》请在冰豆网上搜索。
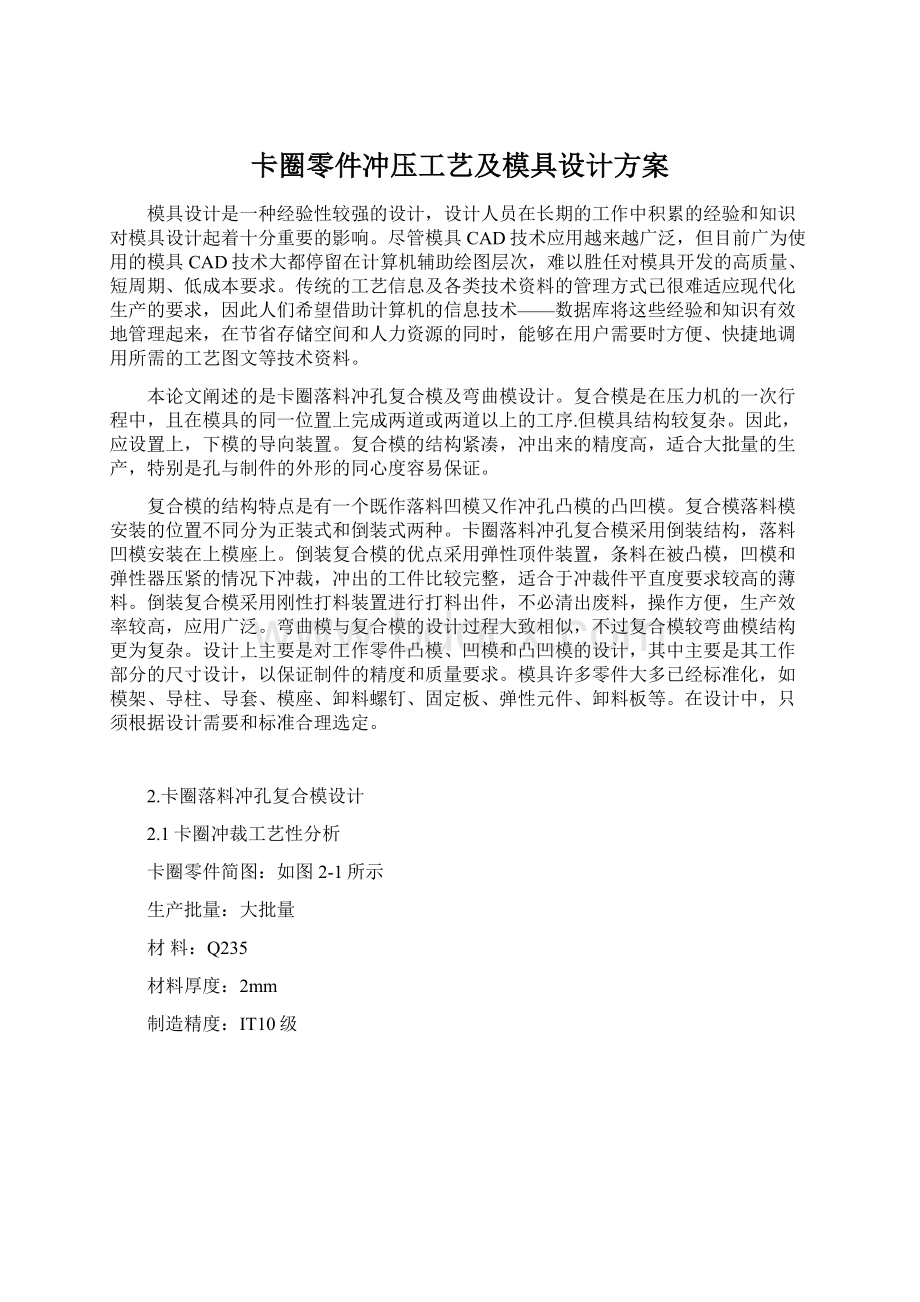
卡圈零件冲压工艺及模具设计方案
模具设计是一种经验性较强的设计,设计人员在长期的工作中积累的经验和知识对模具设计起着十分重要的影响。
尽管模具CAD技术应用越来越广泛,但目前广为使用的模具CAD技术大都停留在计算机辅助绘图层次,难以胜任对模具开发的高质量、短周期、低成本要求。
传统的工艺信息及各类技术资料的管理方式已很难适应现代化生产的要求,因此人们希望借助计算机的信息技术——数据库将这些经验和知识有效地管理起来,在节省存储空间和人力资源的同时,能够在用户需要时方便、快捷地调用所需的工艺图文等技术资料。
本论文阐述的是卡圈落料冲孔复合模及弯曲模设计。
复合模是在压力机的一次行程中,且在模具的同一位置上完成两道或两道以上的工序.但模具结构较复杂。
因此,应设置上,下模的导向装置。
复合模的结构紧凑,冲出来的精度高,适合大批量的生产,特别是孔与制件的外形的同心度容易保证。
复合模的结构特点是有一个既作落料凹模又作冲孔凸模的凸凹模。
复合模落料模安装的位置不同分为正装式和倒装式两种。
卡圈落料冲孔复合模采用倒装结构,落料凹模安装在上模座上。
倒装复合模的优点采用弹性顶件装置,条料在被凸模,凹模和弹性器压紧的情况下冲裁,冲出的工件比较完整,适合于冲裁件平直度要求较高的薄料。
倒装复合模采用刚性打料装置进行打料出件,不必清出废料,操作方便,生产效率较高,应用广泛。
弯曲模与复合模的设计过程大致相似,不过复合模较弯曲模结构更为复杂。
设计上主要是对工作零件凸模、凹模和凸凹模的设计,其中主要是其工作部分的尺寸设计,以保证制件的精度和质量要求。
模具许多零件大多已经标准化,如模架、导柱、导套、模座、卸料螺钉、固定板、弹性元件、卸料板等。
在设计中,只须根据设计需要和标准合理选定。
2.卡圈落料冲孔复合模设计
2.1卡圈冲裁工艺性分析
卡圈零件简图:
如图2-1所示
生产批量:
大批量
材料:
Q235
材料厚度:
2mm
制造精度:
IT10级
图2-1卡圈零件图
冲裁件的工艺性,就是冲裁件对冲压工艺的适应性能,即冲裁件结构形状、尺寸大小、工件精度等在冲裁时的难易程度。
好的冲裁工艺性能能保证材料消耗少、工序数目少、产品质量稳定且效率高、模具结构简单且寿命长等要求。
根据以上分析,该工件宜先冲孔落料,再弯曲达到图纸要求。
1)材料
Q235是普通碳素钢,有较好的冲压性能
2)结构形状
该零件外形简单、规则,仅有落料、冲孔、弯曲、三道工序特征,适合冲压加工。
3)尺寸精度
卡圈零件的加工精度要求为IT10,利用普通冲裁方式可以达到零件图纸要求。
2.2确定工艺方案
工艺方案的内容是确定冲裁件的工艺路线,主要包括确定工序数、工序的组合和工序顺序的安排,应在工艺分析的基础上制定几种可能的方案,在根据工件的批量、形状、尺寸等方面的因素,全面考虑、综合分析,选取一个较为合理的冲裁方案。
该零件冲裁工艺包括落料、冲孔两个工序,下表列有三种工艺方案选择
序号
工艺方案
结构特点
1
单工序模生产
模具结构简单,但需要两道工序,两套模具才能完成零件的加工,生产效率低,难以满足零件大批量生产的要求。
且两道工序中的定位误差,将导致孔中心距尺寸精度难以保证。
2
复合模生产
落料-冲孔复合
同一副模具完成两道不同的工序,大大减小了模具规模,提高生产效率,也能提高压力机等设备的使用效率,操作简单、方便,适合大批量的生产,能可靠地保证孔中心距尺寸精度。
3
级进模生产
冲孔-落料连续
同一副模具不同工位完成两道工序,生产效率高,模具成本要高,两工位之间的定位一要求非常高,否则无法保证孔中心距尺寸精度
经过比较,复合模生产最为恰当,既能保证精度,成本又低,效率高。
如果采用正装结构,落料废料均落在凹模表面,将导致清除困难而降低生产效率,增大劳动强度。
因此复合模采用倒装结构。
为保证制件较高的位置公差要求,上下模之间采用后侧导柱,条料采用手动送料,进入模具内依靠导料销保证送进导向,定位销保证定距精度。
冲裁完成后,冲孔完成后,冲孔废料由漏料孔从下模出,制件则由上模刚性顶件装置顶出,落在下模表面;落料废料则由安装于下模弹性卸料装置从凸凹模上剥落。
2.3冲裁间隙的确定
冲裁间隙是指冲裁凸模和凹模刃口部分尺寸之差,其值可正、可负,在一般的普通冲裁中均为正值。
凸凹模每侧间隙称为单边间隙,两侧间隙之和称为双边间隙。
若无特殊说明,冲裁间隙指双边间隙。
单边用间隙用C表示,双边用Z表示。
圆形冲裁模双边间隙为Z=D凹-D凸
式中D凹——冲裁模凹模直径尺寸(mm)
D凸——冲裁模凹模直径尺寸(mm)
2.3.1间隙的影响
冲裁间隙除了对冲裁件的质量起着决定性的作用以外,对模具寿命也有较大的影响。
间隙过小会使模具寿命降低,同时,小间隙还使模具制造的难度加大。
因此,冲裁间隙是保证合理冲裁过程的最主要的工艺的工艺参数。
影响合理冲裁间隙值的主要因素是板料厚度和材料性质。
板料愈厚,间隙数值也愈打。
反之板料愈薄,则间隙应愈小。
材料塑性愈好,间隙数值也应愈小。
而塑性差的硬材料,间隙数值就应大一些。
2.3.2合理冲裁间隙值的确定
冲裁间隙对冲裁件质量、模具寿命、冲裁力等都有很大的影响,但影响规律各不相同,不可能存在一个间隙值同时满足各项要求。
通常选择一个合适的间隙范围,在这个范围内能得到质量令人满意的冲裁件,并且满足冲裁力较小、模具有较高的使用寿命的要求。
我们称这个合适的间隙范围为合理间隙,它是一个范围值,其上限为最大合理间隙Zmax,下限为最小合理间隙Zmin。
实际生产中,间隙值的选择主要考虑冲裁断面的质量和模具寿命这两个方面。
根据工件和生产上的具体要求可按如下原则选取间隙值。
1)工件的断面质量无严格要求时,选取较大的间隙值。
2)工件的断面质量及制造精度较高时,选取较小的间隙值。
3)在设计计算冲模刃口尺寸时,考虑模具在使用过程中的因磨损而导致隙值增大,应当按Zmin来计算。
确定间隙值的方法有理论计算法、经验确定法。
因为计算法在使用中不方便,实际生产中常用经验表或经验公式确定,其中经验数表法应用最广。
冲裁间隙经验数据表很多,在一般的冲压手册和模具设计资料上都可以查阅,应当注意的是有的数值相差比较大,在选择时应结合实际需要综合考虑。
计算间隙值的经验公式为
Z=mt
(2-1)
式中,t—材料厚度
m—系数,与材料厚度、性质有关,不同的行业也有差异
查表2-1选得间隙值为Zmin=0.246、Zmax=0.360(mm)。
表2-1冲裁模刃口始用间隙
材料名称
08F、10、35、09Mn、Q235
16Mn
40、50
65Mn
厚度t
初始间隙Z
Zmin
Zmax
Zmin
Zmax
Zmin
Zmax
Zmin
Zmax
<0.5
间隙很小或无间隙
1.0
0.100
0.140
0.100
0.140
0.100
0.140
0.100
0.140
1.5
0.132
0.240
0.170
0.240
0.170
0.230
2.0
0.246
0.360
0.260
0.380
0.260
0.380
2.5
0.360
0.500
0.380
0.280
0.380
0.540
为了使模具能在较长时间内冲制出合格的零件,提高模具的利用率,一般设计模具时取Zmin作为初始间隙。
2.4工件排样
在冲压生产中,节约和减小废料具有非常重要的意义。
据统计,零件的材料费用占制造成本的60%和80%,冲裁件在板料、条料或布料上的布置方式,称为冲裁件的排样法,简称排样。
在模具的设计中,排样的设计是一项极为重要的、技术性很强的设计工作。
排样合理与否,直接影响到材料利用率、制件质量、生产率与成本以及模具使用寿命等,所以排样工作的好坏是左右冲裁经济效益的重要因素之一。
2.4.1材料的利用率
排样的目的是为了合理利用原材料。
衡量排样经济性、合理性的指标是材料的利用率。
所谓材料利用率是指冲裁件的实际面积与所用板料面积的百分比。
材料利用率的计算公式如下:
一个进距的材料利用率η的计算如下:
η=(nA/Bh)×100%(2-2)
式中A——冲裁件面积(包括内形结构废料),(mm2);
n——一个进距内冲裁件数目。
b——条料宽度,(mm)。
h——进距,(mm)
一张板料上总的材料利用率η总的计算如下:
η总=(NA/LB)×100%(2-3)
式中N——冲裁件总数目;
A——板料宽度
L——板料长,(mm);
B——条料宽度
由公式可知,η总,η值越大,材料废料越少,材料利用率就越高。
冲裁件所产生的废料分两种,一是工件的各种内孔产生的废料,它取决于工件的形状,一般不能改变,称设计废料;二是由于工件之间的搭边及工件与条料侧面的搭边、板料的料头、料尾而长产生的废料,它取决于冲压方式与排样方式,称为工艺废料。
提高材料利用率最主要的途径是合理排样使工艺废料尽量减少小,另外在满足工件使用要求的前提下,适当改善工件的结构形状也可以提高材料的利用率。
2.4.2排样方法
常用的冲裁件排样方法分为三类。
(1)有废料排样
(2)少废料排样
(3)无废料排样
少、无废料排样的缺点是工件质量较差,模具寿命不高。
但这两类排样可以节省材料,还具有简化模具结构、降低冲裁里和提高生产率等优点。
并且,工件必须具备一定的形状特征才能采用少、无废料排样。
对于形状复杂的工件,经常采用试排法。
上述采用的三类排样方法,按工件的外形特征有可分为直排、斜排、直对排、混合排、多行排及裁搭边等多种形式。
为满足尺寸精度的要求,设计的卡圈零件采用直排法。
2.4.3搭边
排样中相邻两制件之间的余料或制件与条料边缘间的余料称为搭边。
其作用是补偿定位误差和保持有一定的强度和刚度,防止由于条料的宽度误差、送进步距误差、送料歪斜等原因而冲裁出残缺的废品,保证冲出合格的工件,便于送料。
搭边值要合理确定。
搭边值过大,材料利用率低。
搭边值小,材料利用率虽高。
但过小的时就不能发挥搭边的作用,在冲裁过程中会被拉断,造成拉断,造成送料困难,使工件产生毛刺,有时还会被拉入凸模和凹模间隙,损坏模具刃口,降低模具寿命。
搭边值过小,会使作用在凸模侧面上的法向应力沿着落料毛坯周长的分布不均匀,引起模具刃口的损失。
为避免这一现象,搭边的最小宽度约为毛坯的厚度,使之大于塑变区的宽度。
搭边值的大小与下列因数有关:
1)材料的力学性能。
硬材料可小,软材料、脆性材料的搭边值要大一些
2)工件的形状与尺寸。
尺寸大或有突尖的复杂形状时,搭边值要取得大一些。
3)材料厚度。
厚材料的搭边值应取得大一些。
4)送料方式及挡料方式。
用手工送料、有侧压板导向的搭边值可以小一些。
搭边值一般由经验确定
由卡圈零件图和排样图2-2可得知:
因为经过卡圈毛坯经落料冲孔后,还须进行弯曲工序才能得到最后支承板零件,故在进行复合模的排样时,必须先进行弯曲展开计算。
卡圈弯曲展开长度为:
L=39×2+180°л(30+0.5×2)/180°=174mm
冲裁件面积:
A=174×130mm2=22620mm2
条料宽度:
b=174+3×2mm=180mm
进距:
h=130+2.5mm=132.5mm
一个进距的材料利用率:
η=(nA/bh)×100%=22620×1mm2/(132.5mm×180mm)×100%=94.8%
图2-2排样图
2.5冲压工艺力计算
冲裁力是设计模具、选择压力机的重要参数。
计算冲压力的目的是为了合理地选