共固化阻尼复合材料研究进展.docx
《共固化阻尼复合材料研究进展.docx》由会员分享,可在线阅读,更多相关《共固化阻尼复合材料研究进展.docx(11页珍藏版)》请在冰豆网上搜索。
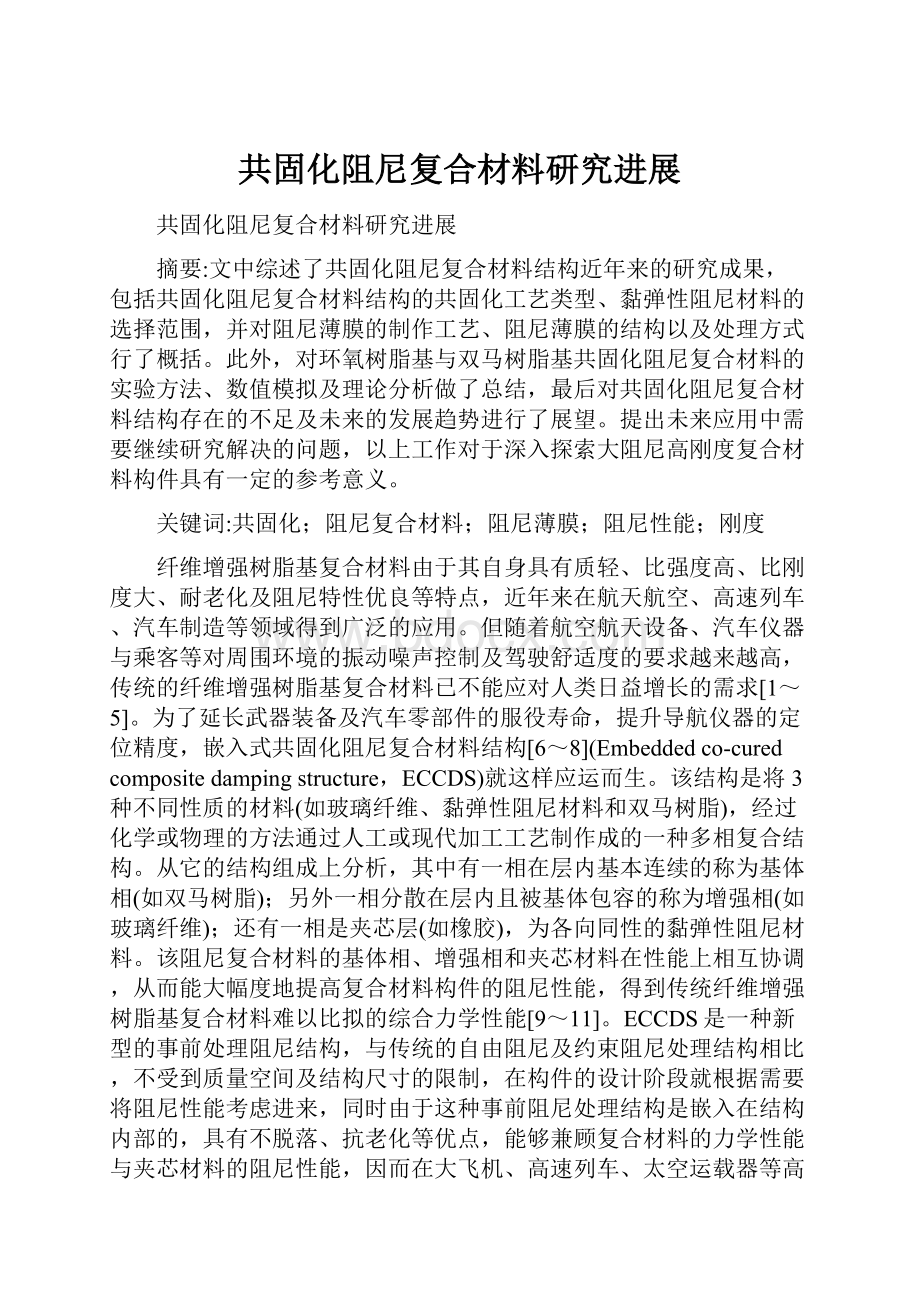
共固化阻尼复合材料研究进展
共固化阻尼复合材料研究进展
摘要:
文中综述了共固化阻尼复合材料结构近年来的研究成果,包括共固化阻尼复合材料结构的共固化工艺类型、黏弹性阻尼材料的选择范围,并对阻尼薄膜的制作工艺、阻尼薄膜的结构以及处理方式行了概括。
此外,对环氧树脂基与双马树脂基共固化阻尼复合材料的实验方法、数值模拟及理论分析做了总结,最后对共固化阻尼复合材料结构存在的不足及未来的发展趋势进行了展望。
提出未来应用中需要继续研究解决的问题,以上工作对于深入探索大阻尼高刚度复合材料构件具有一定的参考意义。
关键词:
共固化;阻尼复合材料;阻尼薄膜;阻尼性能;刚度
纤维增强树脂基复合材料由于其自身具有质轻、比强度高、比刚度大、耐老化及阻尼特性优良等特点,近年来在航天航空、高速列车、汽车制造等领域得到广泛的应用。
但随着航空航天设备、汽车仪器与乘客等对周围环境的振动噪声控制及驾驶舒适度的要求越来越高,传统的纤维增强树脂基复合材料已不能应对人类日益增长的需求[1~5]。
为了延长武器装备及汽车零部件的服役寿命,提升导航仪器的定位精度,嵌入式共固化阻尼复合材料结构[6~8](Embeddedco-curedcompositedampingstructure,ECCDS)就这样应运而生。
该结构是将3种不同性质的材料(如玻璃纤维、黏弹性阻尼材料和双马树脂),经过化学或物理的方法通过人工或现代加工工艺制作成的一种多相复合结构。
从它的结构组成上分析,其中有一相在层内基本连续的称为基体相(如双马树脂);另外一相分散在层内且被基体包容的称为增强相(如玻璃纤维);还有一相是夹芯层(如橡胶),为各向同性的黏弹性阻尼材料。
该阻尼复合材料的基体相、增强相和夹芯材料在性能上相互协调,从而能大幅度地提高复合材料构件的阻尼性能,得到传统纤维增强树脂基复合材料难以比拟的综合力学性能[9~11]。
ECCDS是一种新型的事前处理阻尼结构,与传统的自由阻尼及约束阻尼处理结构相比,不受到质量空间及结构尺寸的限制,在构件的设计阶段就根据需要将阻尼性能考虑进来,同时由于这种事前阻尼处理结构是嵌入在结构内部的,具有不脱落、抗老化等优点,能够兼顾复合材料的力学性能与夹芯材料的阻尼性能,因而在大飞机、高速列车、太空运载器等高科技领域有着广泛的应用前景。
一般来说,经典的复合材料结构本身的阻尼要比常用的金属的高10~100倍,部分地控制了结构的共振幅值、提高了其抗疲劳与耐冲击能力,但这在动载精密结构的工况中依旧偏低。
经典被动阻尼处理的方法有自由阻尼结构、约束阻尼结构和阻尼插入结构,但这3种办法都属于事后处理,使用中阻尼材料容易出现老化返原、剥离脱落等现象,严重地限制了阻尼复合材料的进一步应用[12~15]。
为了解决以上不足,国内外学者提出了一种新型的共固化阻尼复合材料,其结构如Fig.1,通过向复合材料内部嵌入黏弹性材料使整个结构获得大阻尼,同时使这种复合材料结构的树脂基体与黏弹性材料共同经受高温高压的固化过程,最终得到了这种新型的复合材料结构。
Fig.1 Damping composite structure[3]
1国内外研究现状
目前纤维增强树脂复合材料中基体材料主要为环氧树脂和双马来酰亚胺树脂等,根据固化温度的不同其固化工艺分为3种:
低温固化工艺(固化温度在120℃及以下)、中温固化工艺(固化温度在120~180℃之间)和高温固化工艺(固化温度在180℃及以上)[3]。
所谓的共固化是指嵌入黏弹性材料的硫化时间、温度与对应的基体树脂的固化反应时间、温度相同,而且共固化后的结构层间要有一定的结合力,最好是黏弹性材料与复合材料在结合面上形成微观的互穿网络结构,以此来保证结合面有足够的黏接强度和构件的整体刚度,以及较好的阻尼特性。
1.1共固化工艺
目前的ECCDS有2种共固化方式:
一种是通过胶黏剂把商用的阻尼材料与预浸料黏合在一起,再放入到热压罐中一同经历高温高压的考验,最终完成共固化;另一种是根据黏弹性材料的硫化特性与树脂基体的固化特点自制阻尼材料,直接将阻尼材料刷在预浸料上形成不同厚度的阻尼薄膜,然后再放入热压罐中完成ECCDS的共固化成型。
BIggerstaff[16]使用市售的商用阻尼材料黏接剂直接与预浸料黏结在一起在热压罐中实现共固化,研究发现阻尼材料的嵌入能大幅度提升复合材料层合板的阻尼性能,同时发现在共固化过程中处于黏流态的树脂渗入到阻尼层中会减小整体材料的阻尼损耗因子,此外研究表明共固化过程中的高温高压对复合材料的阻尼性能影响不大。
Pan等[17]使用市售的已硫化的橡胶片作为阻尼材料,并且通过胶黏剂与复合材料黏结固化成型,对其静态力学性能及动态力学性能分别做了研究,发现整体阻尼层的插入基本上不影响复合材料拉伸性能,而对复合材料弯曲刚度和强度以及层间剪切强度影响较大;黏弹阻尼层共固化复合材料动态力学性能的温度谱与黏弹性材料相似,且在黏弹性阻尼材料的玻璃化转变温度附近出现阻尼峰值。
共固化复合材料的损耗因子在所测试的温度范围内是纤维增强树脂基复合材料的2.5~13倍左右。
李瑞杰等[18]将阻尼胶膜插入到复合材料中,对共固化黏弹阻尼层树脂基复合材料I型梁的结构阻尼特性进行了理论分析和试验验证,表明共固化黏弹阻尼层树脂基复合材料的结构阻尼性能具有可设计性,黏弹阻尼层越靠近结构中性面,面板约束层厚度越大,阻尼层厚度越大,结构的模态损耗因子也越大;同时阻尼层的添加在明显提高了结构损耗因子的前提下,也降低了结构的静态刚度承载能力。
但由于以上共固化工艺使用的是已硫化的阻尼材料,容易导致阻尼材料老化以及阻尼层与复合材料脱落。
针对以上问题,梁森等[19]通过正交试验法研究黏弹性材料组分并用相关溶剂配制阻尼材料溶液直接与复合材料预浸料结合一起实现共固化,阻尼材料通过物理融合或化学交联与复合材料形成互穿网络结构,大大提高了黏弹性材料与复合材料间的层间结合性能,同时在几乎不损失层合板刚度的前提下大大提高了层合板的阻尼性能。
除此之外,很多国内外学者也对共固化阻尼复合材料进行了大量的科学研究。
1.2ECCDS的阻尼薄膜的制作方法
嵌入式共固化复合材料阻尼结构属于事前处理,使复合材料结构具有传统复合材料板结构不具备的可设计性,即可以在设计阶段将复合材料的铺层层数及顺序和黏弹性材料的厚度及其铺设位置,然后通过共固化工艺形成阻尼功能结构一体化的高阻尼材料结构。
目前嵌入的黏弹性材料主要有丙烯酸黏合剂、氯丁橡胶、丁腈橡胶、聚氨酯、腈化酚醛黏合剂等[20~23]。
阻尼材料的选择要根据树脂基体的固化温度及固化时间,同时还要考虑使用环境及其应用目的,进而对阻尼复合材料的力学性能、阻尼性能等多方面对比后最终确定合适的黏弹性材料。
目前黏弹性阻尼薄膜的制备方法主要有模压法及刷涂法。
阻尼薄膜固化处理方式有直接黏结法和层间隔离法。
阻尼薄膜的结构有穿孔阻尼薄膜、网格阻尼薄膜和混杂阻尼薄膜。
1.2.1 模压法:
模压法是最基本的制作黏弹性阻尼薄膜的方法。
张忠胜等[24]用模压法制作了一种符合高温固化的阻尼薄膜。
为了制造预硫化的阻尼膜,这里采用内部混合器、板式硫化压力机和一组专门设计的模具来将原料压缩成部分硫化的阻尼膜。
在压缩和成形过程中,为了获得高质量的黏弹性膜,必须将模腔加热并抽真空10min,以使阻尼材料预硫化。
文献[10]中Fig.2显示了预硫化的黏弹性阻尼膜,该薄膜的剩余硫化时间约为150min。
为了使黏弹性膜方便地铺设成复合材料,阻尼膜的预硫化程度既不能太高也不能太低,否则不利于整个生产过程的实现。
所用阻尼膜的硫化程度约占30%~50%。
阻尼膜的厚度根据研究的具体需要而定。
然后把制成的阻尼膜铺设在复合材料层中,根据树脂的固化工艺曲线和预浸料一起完成共固化。
Fig.2 Mold and damping layer[10]
Fig.3 Damping solution[26]
Fig.4 Composite prepreg with damping film[26]
1.2.2 刷涂法:
将阻尼材料制成可刷涂的溶液,然后将其均匀涂覆在复合材料预浸料表面上,形成带有阻尼薄膜的预浸料[25~27]。
与模压法相比,刷涂工艺具有简单易行的特点,此外,通过刷涂工艺可以直接在预浸料表面制成不同厚度的阻尼薄膜,阻尼材料可以渗透预浸料表面,来加强阻尼材料与基体树脂在界面的结合力。
为了得到黏度适中且易刷涂的阻尼材料溶液,必须将混炼胶按照一定比例溶解于有机溶剂中,刷涂溶液的制备过程要在通风良好的室内进行,Fig.3为阻尼材料溶液,Fig.4为刷涂了阻尼材料的复合材料预浸料。
1.2.3 直接黏接法:
直接黏接法最早由Biggerstaff[12]提出。
其中一种是使用商用的阻尼材料直接作为插层铺设在复合材料结构中,与碳纤维增强环氧树脂基预浸料一同完成共固化;另一种是先将复合材料上下层分开分别固化,固化完成后用阻尼黏合剂作为中性层把上下层复合材料黏接起来,最终发现这2种工艺都能提高复合材料层合板的阻尼性能,但是第2种相对于第1种阻尼效果更好。
潘利剑[21]利用胶黏剂将商用阻尼层与预浸料黏接在一起,然后再一同实现阻尼复合材料的共固化。
但是这种复合材料具有致命的缺点就是容易分层剥落。
Fig.5 Embedded co-cured composite damping structure with intermediate transition layer and its shear deformation[16]
1.2.4 层间隔离法:
由于直接黏接法中阻尼材料在共固化过程中会丧失部分阻尼性能,于是Biggerstaff等[12,16]就采取措施将阻尼层与环氧树脂直接隔离,在预浸料与黏弹性材料中加一层50μm厚的聚酰亚胺薄膜,为了提高聚酰亚胺薄膜与阻尼层和环氧树脂的结合力,在使用之前将其磨光并用异丙醇擦拭干净。
如Fig.5所示,目前这种方法使用的阻尼材料为AveryFT1125HL、AveryFT1191UHA、3MAF32、3MISD-112和3MISD130,其隔离层主要为Upilex、Kapton等聚酰亚胺薄膜。
实验结果证明,由于隔离层的加入,在很大程度上消除了共固化过程中阻尼层与基体树脂之间的相互作用,与直接黏接法相比,该方法大幅度地提升了复合材料层合板的阻尼损耗因子。
1.2.5 穿孔阻尼薄膜:
穿孔阻尼复合材料结构是在单层复合材料预浸料上预浸阻尼层,然后将带有阻尼层的单层复合材料预浸料在圆锥形凸模上扎出所需要的孔洞阵列,再与不带阻尼层的复合材料预浸料一起按照设计要求铺层,然后进行共固化处理。
在共固化过程中,预浸料中的树脂处于黏流态时会流动并将阻尼薄膜上的孔洞填充满。
最后阻尼层上的孔洞中的树脂完成固化,形成连接上下层预浸料的树脂钉。
该工艺制成的嵌入式共固化穿孔阻尼薄膜复合材料试件,在略微损伤纤维结构的前提下大幅度提高了层间结合力,增加了整体结构的阻尼性能,如Fig.6所示。
最早提出这种方法的是Robinson和Kosmatka[15],Pan、梁森等[17,19]也对穿孔阻尼薄膜进行了理论分析及数值模拟,研究了穿孔面积与阻尼层面积比与整体刚度、阻尼损耗因子之间的关系,并用相关的实验进行了验证。
Fig.6 Perforated damping composite structure
1.2.6 网格阻尼薄膜:
网格阻尼复合材料结构包括上复合材料预浸料层、下复合材料预浸料层以及在上、下复合材料预浸料层之间铺设的形状大小相同并按照一定间距分布的阻尼片阵列[20]。
阻尼片之间的间隔区域在共固化时逐渐被树脂填充并固化,最后便制得嵌入式共固化网格阻尼复合材料结构。
一方面,该结构中的阻尼片起到增加整体结构阻尼的作用;另一方面,阻尼片之间的树脂连接条起到增加层间结合力和提高整体结构刚度的作用,从而使结构具有良好的整体力学性能。
具体网格阻尼结构如Fig.7所示。
Fig.7 Grid damping composite structure
1.2.7 混杂阻尼薄膜:
混杂阻尼复合材料结构是将穿孔阻尼结构与网格阻尼结构复合起来的一种新型阻尼结构,通过调整树脂钉(共固化时阻尼薄膜上的孔逐渐被树脂填充并固化形成的连接钉)和树脂连接条位置实现整体结构的面外力学性能和阻尼各向异性性能可控制[3]。
具体阻尼薄膜的结构形状如Fig.8所示。
Fig.8 Hybrid damping film
1.3环氧树脂基ECCDS的研究现状
Biggerstaff[16]最早对环氧树脂基碳纤维共固化阻尼复合材料做了研究,分别探索了112℃、149℃、177℃共固化时不同阻尼材料ECCDS的阻尼性能,研究发现除了SoundcoatDyad606外,其余的的阻尼材料损耗因子随固化温度的变化影响不大。
潘利剑等[17,21]研究了在150℃时共固化带丁腈橡胶黏弹层的T700/TT85环氧树脂基ECCDS,并对其拉伸性能、弯曲刚度及层间剪切强度做了测试,结果表明整体阻尼层的插入基本上不影响复合材料拉伸性能,而对复合材料弯曲刚度和强度以及层间剪切强度影响较大。
李瑞杰[18]自制了一种带阻尼胶膜的环氧树脂基ECCDS,发现黏弹阻尼层越靠近结构中性面,面板约束层厚度越大,阻尼层厚度越大,结构的模态损耗因子也越大;同时阻尼层的添加在明显提高了结构损耗因子的前提下,也降低了结构的静态刚度承载能力。
李
[22]通过自行设计黏弹性阻尼材料,制作了一种160℃时共固化玻璃纤维/5231环氧树脂基ECCDS,并对其进行了阻尼测试,实验结果表明加入较薄的阻尼层会在构件刚度改变不大的情况下提高构件的阻尼,但若加入阻尼层较厚时,对构件阻尼的增加效果逐渐降低。
Mi等[23]对160℃共固化玻璃纤维/环氧树脂基ECCDS的冲击性能进行了数值分析及实验探究,与同质的复合材料结构相比,ECCDS凭借其呈现出的塑性变形具有更优的冲击性能。
张忠胜[24]在前人的基础上对160℃共固化的玻璃纤维/5231环氧树脂基ECCDS进行了更深一步的研究,首次提出用刷涂工艺制备阻尼薄膜,并探究了刷涂法制备的ECCDS的层间结合性能及阻尼性能,结果表明相对于模压工艺制备的ECCDS,其层间剪切强度和相对阻尼系数都大幅度地提升。
雒磊、梁森和付小静[25~27]分别对160℃共固化环氧树脂基ECCDS的湿热性能、弯曲性能、模态性能和酸碱处理后性能做了研究,并在此基础上研制了一种大阻尼高刚度复合材料仪表板。
史盼等[28]制备了以丁腈橡胶为阻尼层的玻璃纤维/环氧树脂基阻尼复合材料,研究了温度、约束层刚度和阻尼层结构对约束阻尼复合结构减振效果的影响。
结果表明,复合材料结构的最大阻尼范围落在黏弹性材料的玻璃化转变区;玻璃纤维约束阻尼结构能将复合材料结构的阻尼温域扩宽到阻尼材料的橡胶态区域,增加阻尼层厚度可以提高复合材料整体结构的阻尼性能。
王东山等[8]调配了一种与玻璃纤维/BA9913环氧树脂预浸料120℃共固化的氢化丁腈橡胶阻尼材料,并研究了这种ECCDS层合板的模态性能及层间剪切性能,验证了这种共固化阻尼材料组分的有效性。
倪楠楠等[29,30]制备了分别负载PVDF的尼龙无纺布及芳纶无纺布中性层的180℃共固化碳纤维增强环氧树脂基ECCDS层合板,并研究了其拉伸强度、弯曲强度、断裂韧性、动态力学性能及阻尼性能。
结果表明,在复合材料层间插入负载PVDF的中性层能在不引起力学性能明显下降的前提下,显著提高复合材料的阻尼性能和断裂韧性。
其基本阻尼机理是在共固化过程中热塑性插层材料在复合材料的层间形成了具有较高损耗因子的富树脂区。
林国兴等[6]通过嵌入一种丁腈橡胶阻尼层制成了145℃共固化碳纤维/环氧树脂基ECCDS,并采用180°剥离强度测试、振动性能测试对结构界面结合强度、减振性能进行测试。
结果表明,所制备碳纤复合约束阻尼结构中约束层与阻尼层界面结合紧密,剥离强度接近5kN/m,减振量超过19dB,结构减重50%以上,具备较高的应用价值。
1.4双马树脂基ECCDS的研究现状
张忠胜等[13]最早对185℃共固化碳纤维增强双马树脂基ECCDS做了研究,层间剪切测试获得了薄膜厚度与层间最大剪切应力的变化关系,刷涂工艺能提高嵌入式高温共固化复合材料阻尼结构层间结合性能10%以上,而且阻尼层越薄,提高幅度越大。
后来王东山等[8]基于正交试验研制了一种能与双马树脂碳纤维预浸料180℃共固化的黏弹性材料,并获得了层间剪切应力与损耗因子随阻尼层厚度的变化规律。
倪楠楠等[30]开发了一种新型插层材料,利用尼龙无纺布和芳纶无纺布作为插层材料,制备了180℃共固化碳纤维增强双马树脂基ECCDS。
利用动态力学分析仪测试并分析了复合材料的损耗因子和储能模量等动态力学指标;通过弯曲实验和短梁剪切实验评价其静态力学性能。
此外,通过单悬臂梁强迫共振实验和自由振动衰减实验研究了复合材料层合板的共振频率和损耗因子。
1.5ECCDS的理论研究
Barrett等[31]在1991年最早提出了这种复合材料阻尼结构。
Finegan等[32]对如何提升这种复合材料阻尼做了进一步的研究,并在宏观力学和微观力学层面上总结了聚合物基复合材料的阻尼优化及提升方法。
Saravanos[33]利用半解析方法预测了简支特种复合材料板的模态阻尼,开发了离散层阻尼力学。
由Rao等[34]开发了一种全面而简单且研究多阻尼层复合材料梁的各向异性层合约束动力学行为的模型。
Liao等[35]基于RKU模型和NA方法的简单组合进行了理论研究,以研究高阻尼夹层对复合梁阻尼性能的影响。
Yim等[36]研究了插入黏弹性层的叠层夹层复合梁的阻尼性能,并同时考虑了夹芯层合板的面内应力和横向剪切应力对其的影响。
Suzuki等[37]基于多层理论和高阶理论开发了一种有限元模型,用于对带有黏弹性夹层的金属板自由振动和阻尼分析。
Zhang等[7]同时考虑了黏弹性阻尼材料的频率依赖性和纤维增强复合材料引起的能量耗散的贡献,并预测了具有整体黏弹性层的层合复合梁的模态损耗因子。
潘利剑[17]基于模态叠加法与模态应变法提出了一种新的复合材料阻尼结构的阻尼预测方法,并认为计算的阻尼值不是模态损耗因子,而是来自贡献模式的阻尼的组合,通过实验与理论分析获得了阻尼损耗因子预测的一致性。
Mohan等[38]研究了预浸料储存湿度对共固化复合材料接头混合型断裂韧性的影响,发现水分作为游离水或结合水存储在预浸料中。
还显示预浸料将来自高湿度环境的水分作为游离水储存,而结合水的水平保持不受影响。
显示过量的水分使黏合剂增塑,降低了玻璃化转变温度。
随着湿度水平的增加,在模式I和模式II负载下,断裂韧性降低。
在低湿度条件下混合模式韧性显著增加。
虽然混合模式的韧性随着湿度的增加而降低,但是这些值从未低于使用原始材料制造的接头的值。
Sargianis等[39]研究了夹芯材料对碳纤维夹芯复合材料波数和振动阻尼特性的影响,确定了低剪切模量芯具有与结构阻尼值类似的材料阻尼值,随着芯的剪切模量增加,发现这些值之间的百分比差异线性增加,还观察到高结构阻尼值与低波数幅度相关,其对应于来自结构的噪声辐射水平的降低。
Zhai等[40,41]通过汉密尔顿原理、变分原理获得ECCDS的复合材料层合板壳的弯曲变形方程及本构关系,并对其与数值模拟结果进行对比,发现理论推导与数值分析具有很好的一致性,对嵌入式共固化复合材料的理论方面作了杰出的贡献。
2展望
尽管已经对环氧树脂基与双马树脂基共固化阻尼复合材料做了大量的研究工作,但离实际应用还有很多的障碍,具体表现在:
(1)共固化复合材料层合板间的脱层剥离现象仍然存在,如何进一步地提高复合材料层合板间的层间结合性能仍是本研究的重中之重。
(2)由于黏弹性阻尼材料的动态力学性能与温度以及频率有关,但是在应用温度范围内的阻尼损耗因子仍然偏低,如何提高阻尼材料的损耗因子、拓宽其阻尼温域也是接下来需要深入研究的问题。
(3)由于黏弹性材料随着时间环境变化会出现老化现象,所以对于共固化复合材料在极寒、极热环境下的应用仍是一种挑战。
(4)对于复杂结构的共固化复合材料的研究,例如穿孔阻尼复合材料、缝合阻尼复合材料以及加阻尼筋复合材料的理论研究仍然不足,是今后研究的重要方向。
3结束语
本文综述了共固化阻尼复合材料结构的发展进程,包括共固化阻尼复合材料结构的共固化工艺类型、黏弹性阻尼材料的可选种类,并对阻尼薄膜的制作方法、阻尼薄膜的结构以及处理方法进行了总结。
此外,对环氧树脂基与双马树脂基共固化阻尼复合材料的实验方法、数值模拟及理论分析做了汇总工作,最后对共固化阻尼复合材料结构存在的不足及未来的发展趋势进行了展望。
以上工作对于深入探索轻质大阻尼复合材料构件具有参考意义。