铝型材散热型挤压工艺与模具设计毕业设计.docx
《铝型材散热型挤压工艺与模具设计毕业设计.docx》由会员分享,可在线阅读,更多相关《铝型材散热型挤压工艺与模具设计毕业设计.docx(48页珍藏版)》请在冰豆网上搜索。
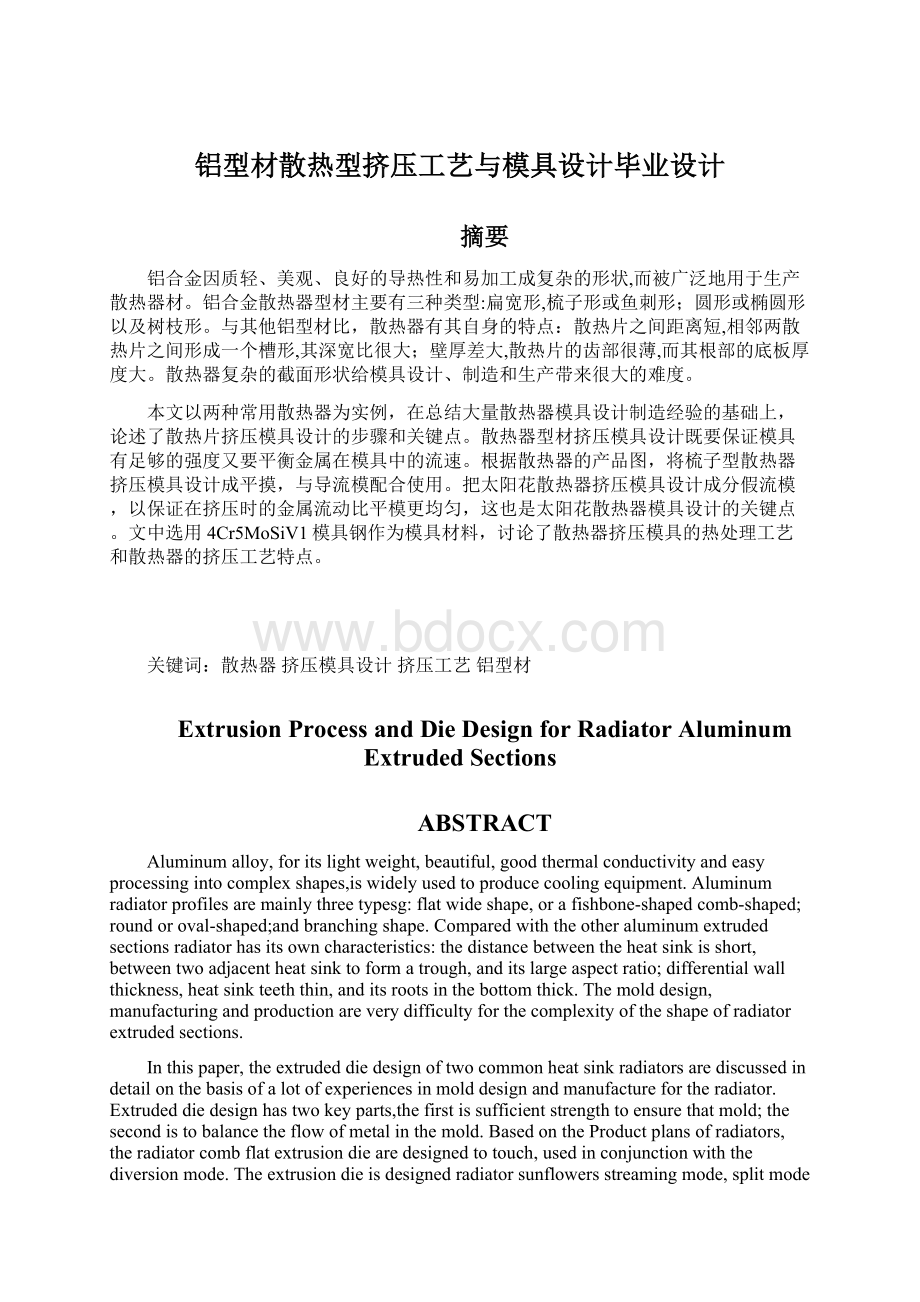
铝型材散热型挤压工艺与模具设计毕业设计
摘要
铝合金因质轻、美观、良好的导热性和易加工成复杂的形状,而被广泛地用于生产散热器材。
铝合金散热器型材主要有三种类型:
扁宽形,梳子形或鱼刺形;圆形或椭圆形以及树枝形。
与其他铝型材比,散热器有其自身的特点:
散热片之间距离短,相邻两散热片之间形成一个槽形,其深宽比很大;壁厚差大,散热片的齿部很薄,而其根部的底板厚度大。
散热器复杂的截面形状给模具设计、制造和生产带来很大的难度。
本文以两种常用散热器为实例,在总结大量散热器模具设计制造经验的基础上,论述了散热片挤压模具设计的步骤和关键点。
散热器型材挤压模具设计既要保证模具有足够的强度又要平衡金属在模具中的流速。
根据散热器的产品图,将梳子型散热器挤压模具设计成平摸,与导流模配合使用。
把太阳花散热器挤压模具设计成分假流模,以保证在挤压时的金属流动比平模更均匀,这也是太阳花散热器模具设计的关键点。
文中选用4Cr5MoSiV1模具钢作为模具材料,讨论了散热器挤压模具的热处理工艺和散热器的挤压工艺特点。
关键词:
散热器挤压模具设计挤压工艺铝型材
ExtrusionProcessandDieDesignforRadiatorAluminumExtrudedSections
ABSTRACT
Aluminumalloy,foritslightweight,beautiful,goodthermalconductivityandeasyprocessingintocomplexshapes,iswidelyusedtoproducecoolingequipment.Aluminumradiatorprofilesaremainlythreetypesg:
flatwideshape,orafishbone-shapedcomb-shaped;roundoroval-shaped;andbranchingshape.Comparedwiththeotheraluminumextrudedsectionsradiatorhasitsowncharacteristics:
thedistancebetweentheheatsinkisshort,betweentwoadjacentheatsinktoformatrough,anditslargeaspectratio;differentialwallthickness,heatsinkteeththin,anditsrootsinthebottomthick.Themolddesign,manufacturingandproductionareverydifficultyforthecomplexityoftheshapeofradiatorextrudedsections.
Inthispaper,theextrudeddiedesignoftwocommonheatsinkradiatorsarediscussedindetailonthebasisofalotofexperiencesinmolddesignandmanufacturefortheradiator.Extrudeddiedesignhastwokeyparts,thefirstissufficientstrengthtoensurethatmold;thesecondistobalancetheflowofmetalinthemold.BasedontheProductplansofradiators,theradiatorcombflatextrusiondiearedesignedtotouch,usedinconjunctionwiththediversionmode.Theextrusiondieisdesignedradiatorsunflowersstreamingmode,splitmodewhenthemetalflowintheextrusiondieismorecomplexthanflat,sohowtobalancetheflowrateofthemetalmoldiskeypointsforthedesignofradiatorsunflowers.4Cr5MoSiV1diesteelisusedandalsotheradiatorheattreatmentprocessandextrudedprocessarediscussed.
Keywords:
RadiatorExtrudemolddesignExtrusionprocessAluminumextrudedsections
第一章绪论
1.1引言
挤压工模具设计与制造是铝合金挤压材,特别是铝合金型材生产的关键技术,不仅影响产品的质量、生产效率和交货周期,而且也是决定产品成本的重要因素之一。
随着铝合金挤压材生产难度的增加和对产品个性化性要求的提高,这种作用更加明显。
2007年,我国铝合金挤压材产销量超过660万t,工模具消耗达80万套以上,价值高达20亿元以上,占挤压加工成本的25%~30%,大大制约了我国铝合金挤压工业的发展。
目前,我国铝合金挤压工模具的平均使用寿命为5~10t/模,一次上机合格率为50%左右,大大落后于国际上15~20t/模和一次上机合格率为67%的先进水平,大有潜力可挖。
因此,不断提高挤压工模具的质量和使用寿命不仅是企业的强烈愿望,也是我国从事挤压工作技术人员的责任[1]。
1.2挤压模具在铝型材挤压生产中的重要性
我国模具工业的发展,逐渐受到人们的重视和关注,在电子、汽车、电机、仪器、仪表、家电和通信等产品中,60%~80%的零部件都要依靠模具成形(型),可以说模具是工业生产的基础工艺装备。
在现代工业生产中,各类产品零件广泛采用冲压、锻压成形、压铸成形、挤压成形、塑料注射或其它成形加工方法,与成形模具相配套,使坯料成形加工成符合产品要求的零件。
与其它加工制造方法相比,用模具生产的产品具有高精度、高复杂程度、高一致性、高生产率和低消耗等特点,因此,模具在工业生产中具有相当重要的地位。
模具的质量和先进程度,直接影响产品的质量、产量、成本,影响新产品投产周期、企业产品结构调整速度与市场竞争力。
模具又是“效益放大器”,用模具生产的最终产品价值,往往是模具自身价值的几十倍以上。
目前,模具生产的工艺水平及科技含量的高低,己成为衡量一个国家科技与产品制造水平的重要标志之一,决定着一个国家制造业的国际竞争力。
现代模具行业是技术、资金密集型的行业,模具行业的发展,可以带动制造业的
蓬勃发展。
按照一般公认的标准,模具产值与其带动实现的工业产值之比为3:
100。
通过模具加工产品,可以大大提高生产效率,节约原材料、降低能耗和成本,产品的一致性好。
如今,模具因其生产效率高、产品质量好、材料消耗低、生产成本低,而在各行各业得到了广泛应用,并且直接为高新技术产业服务,特别是在制造业中,它起着其它行业无可取替代的支撑作用,对国民经济的发展有着辐射性的影响。
在现代化的大生产中,模具对实现整个挤压过程有着十分重要的意义。
模具使用寿命是评价某一挤压方法或挤压工艺经济可行的决定因素之一,工模具的设计与制造质量是实现挤压生产高产、优质、低耗、高效低成本的重要保证之一。
具体来说,其重要地位和作用表现在以下几方面[2]:
(1)合理的工模具结构是实现任何一种挤压工艺过程的基础,因为它是使金属产生挤压变形和传递挤压力的关键部件。
(2)模具是保证产品成形,具有正确形状、尺寸和精度的基本工具。
只有结构合理、精度和硬度合格的模具(包括针尖或模芯),才能实现产品的成形并具有精确的内外廓形状和断面尺寸。
同时,合理的模具和工具(包括模垫、支承环和导路等)设计能保证产品具有最小的翘曲和扭曲,最小的纵向弯曲和横向波浪度。
(3)模具是保证产品内外表面质量最重要的因素之一。
(4)合理的工模具结构、形状和尺寸,在一定程度上可控制产品的力学性能和内部组织,特别是在控制空心制品的焊缝组织和力学性能方面,分流孔的大小、数量和形状及分布位置,焊合腔的形状和尺寸,模芯的结构等起着决定性的作用。
挤压垫片、挤压筒和模子的结构形状与尺寸及表面质量,对控制产品的粗晶环和缩尾、成层等缺陷也有一定的作用。
(5)工模具的结构形状与尺寸对金属的流变、挤压温度-速度场、应力-应变场等有很大的影响,从而对提高生产效率、产品质量和减少能耗有重大作用。
(6)合理的工模具设计对提高其装卸与更换速度,减少辅助时间,改善劳动条件和保证生产安全等方面意义重大。
(7)新型的模具结构,对于开发新产品、新工艺,研制新材料和新设备,不断提高挤压技术起着很大的作用。
如扁挤压筒、舌型模、组合模、多层预紧应力模、变断面模等。
(8)高比压优质圆挤压筒和扁挤压筒及特种型材模和异形管材模的设计与制造技术是铝合金挤压生产的核心和关键技术,其技术含量在整个挤压技术中占有很大的比例。
(9)对于中等批量的挤压产品,工模具的成本占总成本的30%左右,如将其使用寿命提高5~10倍,则产品的成本可大幅度下降。
因此,在铝挤压界广泛流传的一句口号:
产品是生命,设备是基础,模具是关键,工艺是保证。
1.3铝型材挤压模具技术发展概况
在金属压力加工中,决定某一挤压方法是否经济可行,主要取决于下列三个方面,即产品质量、生产效率和工模具寿命,而工模具往往是工艺决策的关键因素。
因此,挤压用工模具的发展实际上伴随挤压技术的发展而发展。
铝合金挤压技术发展的初期,由于挤压机能力小,结构简单,产品形状单一而且尺寸较小,所变形合金较软,所以模具一般为结构形状极为简单,尺寸较小的圆状平面模,工具的结构形状也较为简单。
当时的模具多用普通工具钢,采用一般的机械加工方法制造。
随着铝合金挤压材向大型化、复杂化、精密、多规格、多用途方面发展,对挤压工模具提出了越来越高的要求。
不仅出现了像平面分流组合模、宽展模具、保护模、变断面模等多种新型结构的模具,成功地研制出多种σb达1500MPa以上的高级耐热高强度工模具材料,而且开发了多种大型的基本挤压工具,这些工具便于装卸,先进可靠,但结构形状复杂,尺寸规格大,难于设计制造。
如200MN卧式挤压机上的大型特种组合型材模具,模具组尺寸为φ1800×500mm,重达10t,需15t高强而热合金钢坯,其设计、制造、使用和维修都十分复杂。
我国模具开发制造水平与国外相比仍存在很大的差距,比国际先进水平至少落后10年,特别是在大型、精密、复杂、长寿命模具的制造上存在很大困难,这也成为制约我国制造业发展的瓶颈。
表1-1列出了国内外挤压模具设计制造的发展水平和主要差距[3]。
表1-1国内外挤压模具设计制造的发展水平和主要差距
国际先进水平
国内先进水平
设计理论和方法
普遍采用动态热分析与热模拟及有限元和电子计算机分析技术,研发了多种新结构模具及设计软件,建立了巨型数据库与专家库,正在研发零试模技术
基本采用传统方法,开始研究和开发新理论、新方法,开始重视新结构模具研发与软件开发
新结构大型工具
广泛采用高比压的优质圆、扁挤压筒,固定挤压垫,快速换模装置及高效反挤压工具
开始研发扁挤压工具和固定挤压垫及快速更换装置
模具材料
以H13钢及改进型钢为主,采用电渣重熔、炉外在线精炼