拔丝相关技术管理小结编辑综述.docx
《拔丝相关技术管理小结编辑综述.docx》由会员分享,可在线阅读,更多相关《拔丝相关技术管理小结编辑综述.docx(25页珍藏版)》请在冰豆网上搜索。
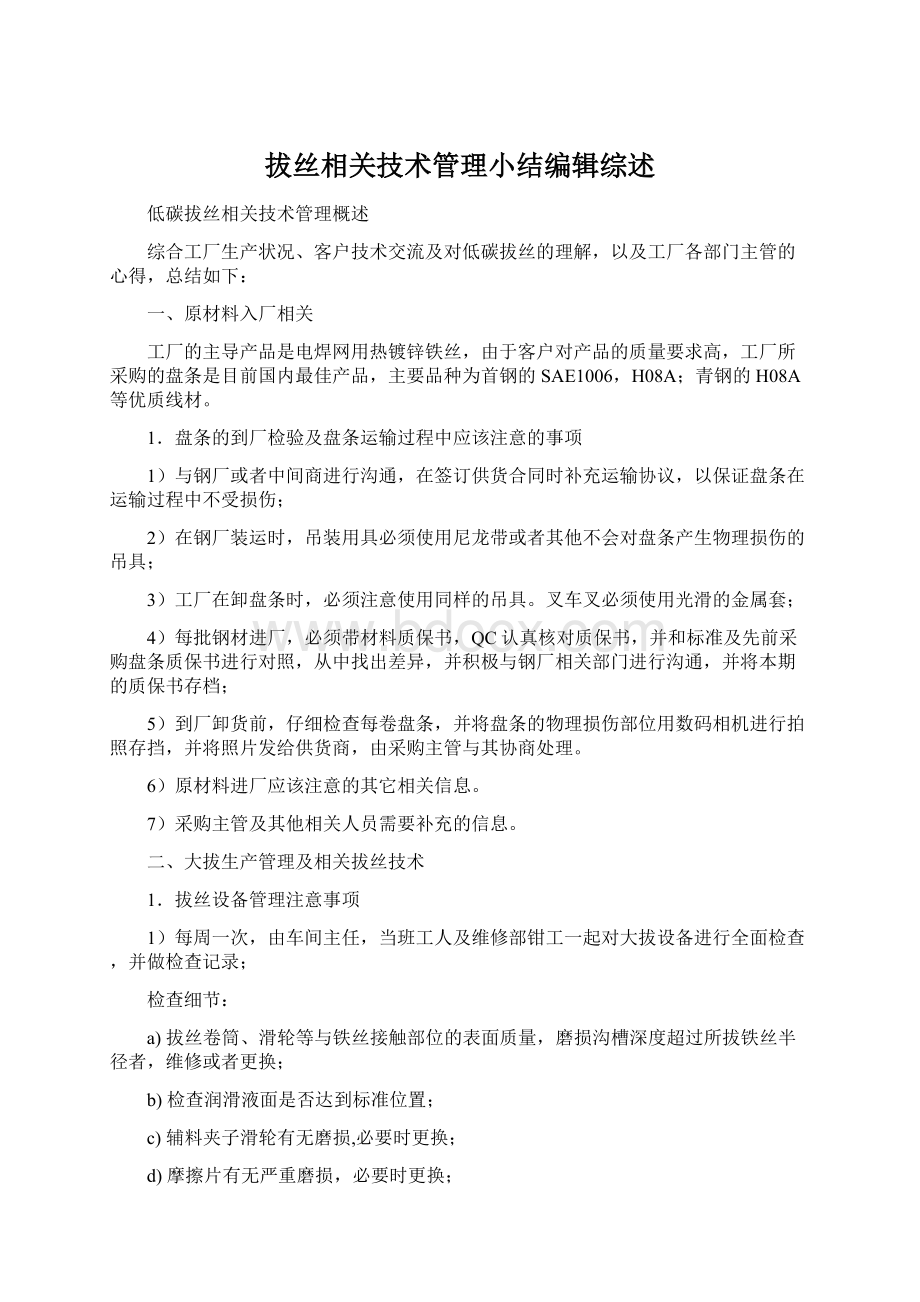
拔丝相关技术管理小结编辑综述
低碳拔丝相关技术管理概述
综合工厂生产状况、客户技术交流及对低碳拔丝的理解,以及工厂各部门主管的心得,总结如下:
一、原材料入厂相关
工厂的主导产品是电焊网用热镀锌铁丝,由于客户对产品的质量要求高,工厂所采购的盘条是目前国内最佳产品,主要品种为首钢的SAE1006,H08A;青钢的H08A等优质线材。
1.盘条的到厂检验及盘条运输过程中应该注意的事项
1)与钢厂或者中间商进行沟通,在签订供货合同时补充运输协议,以保证盘条在运输过程中不受损伤;
2)在钢厂装运时,吊装用具必须使用尼龙带或者其他不会对盘条产生物理损伤的吊具;
3)工厂在卸盘条时,必须注意使用同样的吊具。
叉车叉必须使用光滑的金属套;
4)每批钢材进厂,必须带材料质保书,QC认真核对质保书,并和标准及先前采购盘条质保书进行对照,从中找出差异,并积极与钢厂相关部门进行沟通,并将本期的质保书存档;
5)到厂卸货前,仔细检查每卷盘条,并将盘条的物理损伤部位用数码相机进行拍照存挡,并将照片发给供货商,由采购主管与其协商处理。
6)原材料进厂应该注意的其它相关信息。
7)采购主管及其他相关人员需要补充的信息。
二、大拔生产管理及相关拔丝技术
1.拔丝设备管理注意事项
1)每周一次,由车间主任,当班工人及维修部钳工一起对大拔设备进行全面检查,并做检查记录;
检查细节:
a)拔丝卷筒、滑轮等与铁丝接触部位的表面质量,磨损沟槽深度超过所拔铁丝半径者,维修或者更换;
b)检查润滑液面是否达到标准位置;
c)辅料夹子滑轮有无磨损,必要时更换;
d)摩擦片有无严重磨损,必要时更换;
e)检查机械去氧化皮装置的滑轮槽是否磨损,导轮是否松脱,各滚轮轴承是否损坏;
f)检查电机、电气控制系统是否正常;
g)检查设备水冷、风冷系统是否运转正常;
h)设备运转的声音是否异常,是否有异常的振动;
※机械去氧化皮装置的滑轮直径及延伸率的计算:
[(D+2d)-(D+d )]/(D+d)*100%=elongation%
通常延伸率的数据大约是8%;常用的盘条直径是6.5mm.
所以得出滑轮的基础直径是D=(100d-8d)/8=75mm.
5个滑轮相互交错,互成45°角焊接在牢固的钢管上。
加配机械去氧化皮装置的图纸;
2)工人每天上班前15分钟仔细检查大拔设备,将发现的问题及时反馈给车间主任,并对关键点进行润滑;
3)检查每只卷筒铁丝规格并和标准的配模比进行对照,看是否异常;
4)测量拔丝卷筒的温度,看是否异常并做记录;
5)检查铁丝的润滑状况是否良好,拔丝润滑剂挤出的形式。
※判断润滑粉的质量好坏根据:
a)生产每吨铁丝的润滑粉的消耗量;
b)使用前后,模具的使用寿命变化如何。
※正确记录模具的使用寿命。
※机械去氧化皮装置的图纸;
※压力模的图纸。
※摩擦机构的图纸。
※敷料夹子是和压力模一起使用才起作用,压力模前模不能拉拔铁丝,必须比进线铁丝的直径大10-30丝左右,盘条进线处压力模可以再大些,因为盘条的直径变化较大,工人在更换盘条时必须测量盘条的进线直径,以保证前模必须大于盘条进线直径20丝以上,否则不但润滑不好,而且要损伤铁丝。
※另外,选用润滑粉必须和工厂的实际拔丝工况相适应,目前工厂拔丝为机械去氧化皮,拔丝速度在6.8m/s以下。
目前选用的是天津东亚公司生产的50号润滑粉。
再选择别家工厂时,必须将上述事实告知该厂。
※模盒采取溢流式水冷,提高模具使用寿命;
※大拔配模比有大拔设备的减速比来决定,两者之间只能存在1-2%的差异,变频调速设备,范围差别可以适当大一些;
2.每天记录进料重量,出料重量,考核大拔生产的成材率,大拔生产的成材率必须控制在98.5%以上;
3.每天将大拔所出的废铁丝及盘条腰扣称重入库;
4.每天不定时检查设备的运转速度是否在限定的范围之内,并对违反操作规定的工人进行处罚;
5.每2小时检查工人的出丝直径及拔丝的质量,润滑是否良好,铁丝是否有损伤,损伤的铁丝必须小于10圈,大于10圈的处以扣产处罚;直径超差的扣产处罚;
6.每月根据财务统一安排将本月的成材率及工人产量报表等相关报财务,由财务进行核算,执行财务管理程序;
7.其他由大拔主管及其他相关人员的补充。
三、水箱拔丝相关技术及管理相关
1.水箱设备管理相关
1)每周一次,由车间主任,当班工人及维修部钳工一起对水箱拔丝设备进行全面检查,并做检查记录;
检查细节:
a)卷筒及塔轮磨损程度检查,磨损沟槽的深度必须小于或者等于该槽所挂铁丝的半径;
b)调直轮的磨损情况;
c)传动链及传动带的工作状况是否良好,主要检查链是否松动,皮带磨损情况;
d)水箱驱动轴及从动轴的工况是否正常;
e)电动机及控制系统工作是否正常;
f)水箱拔丝系统的润滑系统是否正常。
g)调速系统是否准确;
h)其它应该关注的细节。
2)工人每天上班前15分钟仔细检查水箱拔丝设备并对关键点进行润滑,并将发现的问题及时反馈给车间主任;
3)检查每只模具铁丝规格并和标准的配模比进行对照,看是否异常;
4)检查模具的安装位置是否和铁丝垂直,是否处于平滑过渡;
5)铁丝滑动率及配模比相关:
a)测量塔轮每个沟槽的直径计算其相对应的减速比,再和该规格的配模比相对照,计算出的滑动率控制在5%之内,此状况下对设备、模具及铁丝的表面质量最有益。
b)滑动速率越大,塔轮沟槽的磨损速度越快,带来的维护成本相应增加越多,对铁丝的表面质量影响最大;
c)改善的方法:
为了更好的充分利用塔轮,采取配模比调整与塔轮沟槽直径修磨同时协调进行,每次加工完成塔轮后,对新的直径进行记录,计算减速比,按此及所拔规格进行配模,以获得滑动速率控制在5%以内。
d)计算方法描述:
假设:
水箱拔丝主动轴与从动轴的转速相同为n转/分,主动轴塔轮为a,其上沟槽直径分别为a1,a2,a3……an;从动轴塔轮为b,其上沟槽直径分别为b1,b2,b3……bn;沟槽直径的排列均为由小到大,相对应模具的规格为d1,d2,d3……dn;每个沟槽的实际线速度分别为Va1,Va2,Va3……Van,Vb1,Vb2,Vb3……Vbn
滑动速率理想值为5%于滑轮的实际速度。
计算过程如下:
单位时间内通过的铁丝体积相等
(πd12/4)L1=(πd22/4)L2……L1,L2单位时间内通过的铁丝的实际长度
∴L1/L2=d22/d12
单位时间内塔轮相应沟槽转动的长度L1',L2'
L1'=nπa1t;L2'=nπa2t
∴L1'/L2'=a1/a2
∴如果a1/a2=d22/d12,收线机的收线速度和塔轮最后一沟槽的速度相等,那么塔轮上铁丝的滑动率为0,
我们允许滑动速率为±5%,
∴我们计算时按照a1/a2=1.05d22/d12,或者1.05a1/a2=d22/d12,
水箱拔丝的配模比δ=(1-d22/d12);
e)塔轮出线沟槽的速度为Vbn=nπbn即为象鼻子收线机的设定线速度。
f)通过检查断点的形状来判断工人操作时是否设定的收线速度太高而拉断铁丝。
由此我们可以进行相应的调整计算,从而延长水箱塔轮的使用寿命,减少塔轮对铁丝的磨损。
2.每天记录进料重量,出料重量,考核水箱拔丝生产的成材率,水箱拔丝生产的成材率必须控制在99.6%以上;
3.每天将水箱拔丝所出的废铁丝称重入库;
4.每天不定时检查设备的运转速度是否在限定的范围之内,并对违反操作规定的工人进行处罚;
5.每2小时检查工人的出丝直径及拔丝的质量,铁丝是否有损伤,损伤的铁丝必须小于10圈,大于10圈的进行扣产处罚;直径超差的扣产处罚。
6.测量每个工人的下线的抗拉强度,抗拉强度的与相应标准之间的误差必须控制在+/-3kg/mm2之内,对与超差者查出原因,分别追究责任;
7.水箱拔丝的撒线尺寸必须控制在390-420mm之间,通过调整机器上的调直轮来达到此撒线尺寸;
※客户提供调直轮图纸存档;
8.水箱模具的配模比基本相同,必须基本维持在10%±1%的水平,并参照塔轮沟槽的直径;标准配比推荐如下:
2.05,1.87,1.73,1.64,1.54,1.45,1.37,1.30;或者
2.00,1.87,1.73,1.64,1.54,1.45,1.37,1.30;
9.每月根据财务统一安排将本月的成材率及工人产量报表,处罚相关报财务,由财务进行核算,执行财务管理程序;
10.其他由水箱拔丝主管及其他相关人员的补充。
四、镀锌生产相关技术管理
1.镀锌设备设施的管理
1)每周一次,由车间主任,当班工人及维修部钳工一起对镀锌相关设备设施进行全面检查,并做检查记录
检查细节:
后机/Payoff/上线处:
a)上线处地面是否平整;
b)上线处每套调直轮的运转情况,螺丝是否松脱,调直轮是否磨损,c)调直轮转动是否灵活,转动处是否缺润滑油;
d)助动装置的工作状况,调速装置工作是否正常,调速电机温升是否正常,是否用的防尘调速电机,助动卷筒转速的设定是否在镀锌铁丝的1.05-1.10倍之间;
助动卷筒的槽磨损是否严重等,沟槽的深度有无超过所镀铁丝直径的1/2,视为是否维修的分界点;
※助动卷筒的图纸是否打印存档;
退火炉/平炉/Annealingfurnace:
a)平炉眼砖有无堵塞,上期吹平炉眼砖的日期;
b)炉温设定是否和所镀铁丝的规格相一致;
c)炉排工作是否正常,是否有裂纹,脱节,磨损严重的链环;
d)电气控制系统工作是否正常,是否清洁,是否存在安全隐患,有无虚焊,脱焊,连接线松动的位置等;
f)炉灰炉渣清理是否及时,彻底;
g)减速电机工作温度测量,减速箱润滑状况是否良好;
h)测温计测温是否准确;
i)炉膛有无炼熘结渣堵塞情况。
j)未来工厂彻底取消水箱拔丝后,退火炉因为润滑剂太多而堵塞的问题,必须有妥善的有效的解决方法。
酸洗/Acidcleaning/酸池相关:
a)上次池内氯化铁等杂物清理情况;
b)酸液有无漏出,外墙是否需要维修;
c)烟囱张紧绳是否有破损,移动,松脱等状况;
d)内外酸罐有无漏酸,缺少防护盖等情况。
水池/Watertank:
a)加热炉工作是否正常;
b)有无准备备用水池;
氨池Flux:
a)加热炉是否正常,氨池的最佳工作温度在80-90℃之间;
b)加氨的比率是100kg水+20kg氯化铵;
c)有无备用氨池;
d)氨池内是否放置锌锭;
锌锅/ZincTank:
a)铅液面是否适当;
b)锌锅擦拭器安装位置是否与铁丝的出丝位置平行;
c)温度传感器显示温度是否正确;
d)炉膛距锌锅底部的距离是否适当;
蜡池/Waxtank:
a)蜡池的位置放置是否水平;
b)分布在四周的出蜡口是否能够有效地将表面的油状物溢流出去;
c)蜡池循环系统工作是否正常,有无滴漏现象;蜡的浓度是否控制在1.2-1.5%的水平,蜡池的温度是否控制在60-65℃;
前机/Takeup/下线处:
a)各下线机减速系统工作是否正常;
b)铁丝导轮滑轮是否磨损,螺丝是否有松脱现象;
c)各小轴有无磨损切断现象;
d)各调直轮转动是否灵活,沟槽是否磨损;
e)各调直轮轴承是否采用密封轴承,密封功能有无失效;
f)撒线盘的使用情况,是否磨损,磨损的沟槽深度是否超过铁丝半径;
g)各润滑加油点是否缺油;
h)下线机加油润滑后,润滑油有没有滴落到下线架上,特别是镀锌铁丝上,特别注意当夏天到来的时候,润滑油容易液化,滴落加注润滑油及润滑油脂不易过多;
i)下线架有无损坏,弯曲,变形。
包装/Packa