应用PROE设计塑料齿盘注射模具.docx
《应用PROE设计塑料齿盘注射模具.docx》由会员分享,可在线阅读,更多相关《应用PROE设计塑料齿盘注射模具.docx(38页珍藏版)》请在冰豆网上搜索。
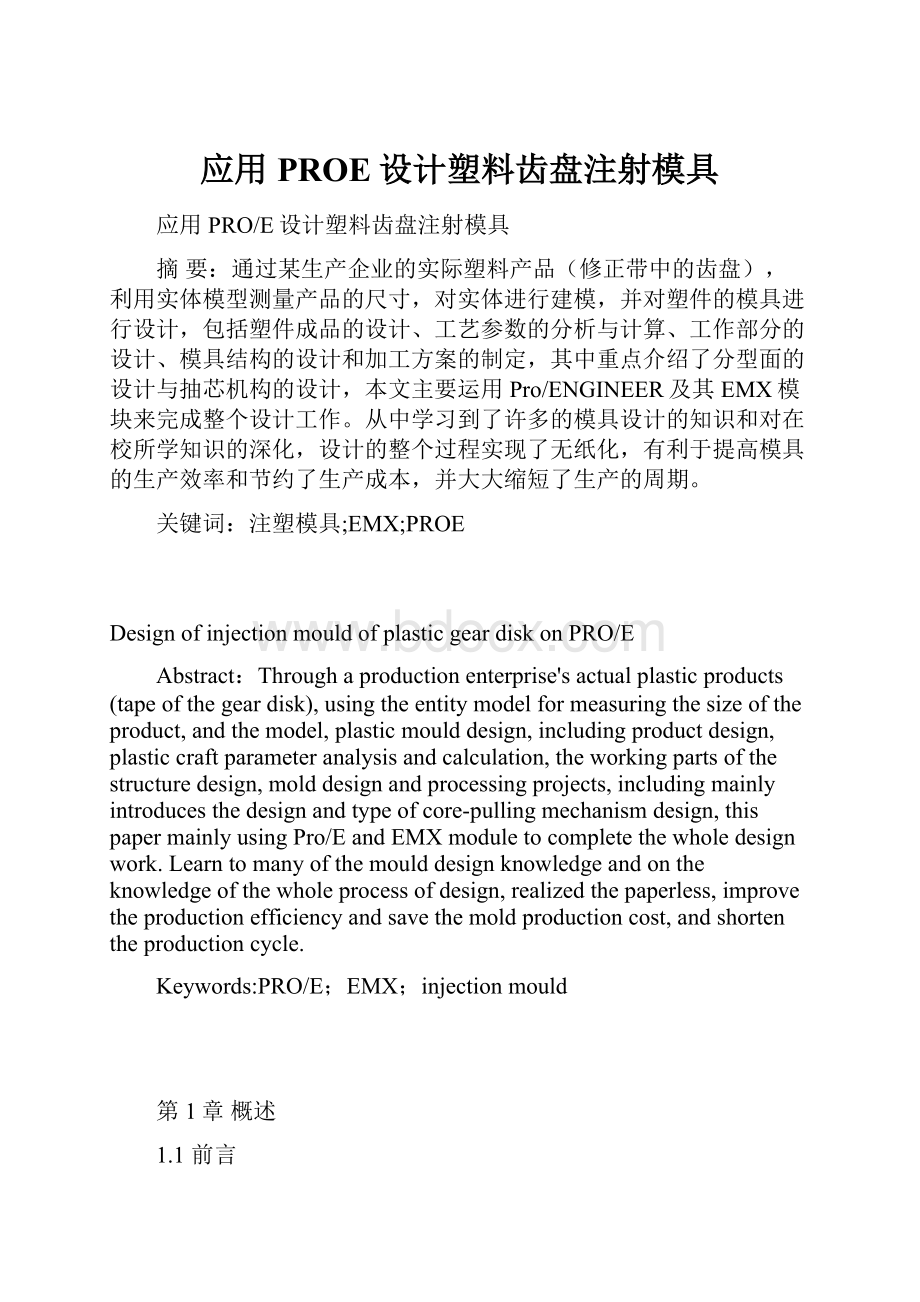
应用PROE设计塑料齿盘注射模具
应用PRO/E设计塑料齿盘注射模具
摘要:
通过某生产企业的实际塑料产品(修正带中的齿盘),利用实体模型测量产品的尺寸,对实体进行建模,并对塑件的模具进行设计,包括塑件成品的设计、工艺参数的分析与计算、工作部分的设计、模具结构的设计和加工方案的制定,其中重点介绍了分型面的设计与抽芯机构的设计,本文主要运用Pro/ENGINEER及其EMX模块来完成整个设计工作。
从中学习到了许多的模具设计的知识和对在校所学知识的深化,设计的整个过程实现了无纸化,有利于提高模具的生产效率和节约了生产成本,并大大缩短了生产的周期。
关键词:
注塑模具;EMX;PROE
DesignofinjectionmouldofplasticgeardiskonPRO/E
Abstract:
Throughaproductionenterprise'sactualplasticproducts(tapeofthegeardisk),usingtheentitymodelformeasuringthesizeoftheproduct,andthemodel,plasticmoulddesign,includingproductdesign,plasticcraftparameteranalysisandcalculation,theworkingpartsofthestructuredesign,molddesignandprocessingprojects,includingmainlyintroducesthedesignandtypeofcore-pullingmechanismdesign,thispapermainlyusingPro/EandEMXmoduletocompletethewholedesignwork.Learntomanyofthemoulddesignknowledgeandontheknowledgeofthewholeprocessofdesign,realizedthepaperless,improvetheproductionefficiencyandsavethemoldproductioncost,andshortentheproductioncycle.
Keywords:
PRO/E;EMX;injectionmould
第1章概述
1.1前言
作为工业生产基础工艺装备的模具,在国民经济中占有重要的地位,模具技术也已成为衡量一个国家产品制造水平的重要标志之一。
模具因其生产效率高、产品质量好、材料消耗低、生产成本低而获得广泛应用,与其他加工制造业所无法比拟的。
从工业产品生产行业看,模具是现代工业,特别是汽车、摩托车、航空、仪表、仪器、医疗器械、电子通讯、兵器、家用电器、五金工具、日用品等工业必不可少的工艺装备。
据资料统计,利用模具制造的零件数量,在飞机、汽车、摩托车、拖拉机、电机、电器、仪器仪表等机电产品中占80%以上;在电脑、电视机、摄像机、照相机、录像机、传真机、电话及手机等电子产品中占85%以上;在电冰箱、洗衣机、空调、微波炉、吸尘器、电风扇、自行车、手表等轻工业产品中占90%以上;在了弹、枪支等兵器产品中占95%以上。
目前,美国、日本、德国等发达国家的模具总产值都已超过机床总产值。
模具技术的进步极大地促进了工业产品的生产发展,模具是“效益放大器”,用模具生产最终产品的价值将超过自身价格的几十倍乃至百倍及上千倍。
据各国报导,模具工业在欧美等工业发达国家被称之“点铁成金”的“磁力工业”,如今世界模具工业的发展速度超过了新兴的电子工业,已实现了模具专业化、标准化和商业化,因而深受赞誉。
美国工业界认为“模具工业是美国工业的基石”,日本称模具工业为“进入富裕社会的原动力”,在德国,被冠之以“金属加工业中的帝王”之称号,而欧盟一些国家称“模具就是黄金”,新加坡政府则把模具工业作为“磁力工业”,中国模具权威经理称为“模具是印钞机”。
可见模具工业在世界各国经济发展中具有重要的显著地位。
模具技术已成为衡量一个国家产品制造水平的重要标志之一。
1.2我国模具行业发展概述
近年来,我国模具行业一直保持着良好的发展势头,这种势头是否还会延续下去,这是业内人士十分关注的问题。
我国模具行业尽管面临着在中低端产品领域国内企业竞争日趋剧烈以及在中高端产品领域国外或外资企业压力日益增大的局面,但经过近年来的持续发展,实力已大大增强,完全有能力变压力为动力,继续保持平稳发展。
(1)有利因素
优惠政策为模具行业提供了良好的发展环境。
在国家产业政策和有关配套政策导向之下,近年来已有不少地方相继出台了一些支持当地模具工业发展的优惠政策,有的见诸于文件,有的见诸于行动,都已收到很好的效果。
同时,模具工业的快速发展也促进了当地经济的繁荣。
随着各地之间交流活动的日益频繁,相信对模具工业发展有利的政策,及因此而带来的良好的发展环境将有进一步发展。
模具行业内部体制改革和机制转换加速,产业结构渐趋合理,并且加强了管理,提高了水平。
为了适应形势,我国模具行业近几年来加快了体制改革和机制转换步伐,“三资”和民营企业已占行业主导地位,装备水平和产品水平有了较大的提升,管理有了很大进步。
许多企业已应用了CAD/CAM/CAE一体化技术、三维设计技术、ERP和IM3等信息管理技术以及高速加工、快速成型、虚拟仿真及网络技术等许多高新技术,不少企业已提出了“生产专业化、产品品牌化、企业现代化、市场国际化”等企业发展战略。
通过各种质量体系认证的企业一年比一年多。
规模经济产生效益,模具集群生产发展迅速。
在“小而精专”的专业化不断发展的同时,近年来,规模效应已被愈加重视。
除了把企业做强做大,使规模经济产生效益之外,模具集群生产也不断显示其优越性,因而“模具城”、“模具园区”、“模具生产基地”等各种集群生产形式在全国迅速发展。
据不少企业反映,集群生产与分散生产相比,至少有下列好处:
市场更广阔了,协作更方便了,生产成本降低了,相互交流多了,优惠政策享受到了。
目前全国年产1亿元以上模具的企业已有40多个,超过3000万元以上的企业已有200多个,具有一定规模的“模具城”已有近十个,正在建设或正在筹建的还有十多个。
这些模具集聚生产基地的建设,对我国模具工业的发展起到了积极的促进作用。
许多企业开始认识到了“品牌”和“专利”的重要性,自主创新的资金投入力度和能力不断提高。
长期以来模具一直处于“后方”和“被动”的地位,因此也很少有“品牌”和“专利”。
随着市场经济的发展,近年来企业越来越重视“品牌”和“专利”。
有些企业已认识到了创新研发的重要性,投入力度提高很快。
据中国模具工业协会了解到的情况,近年不少企业在创新研发方面的投入与销售收入的比例达到5%左右,个别企业甚至达到8%至10%。
(2)不利因素
虽然我国模具行业已经驶入发展快车道,但由于在精度、寿命、制造周期及能力等方面,与国际水平和工业先进国家相比尚有较大差距,所以还不能满足我国制造业发展的需求。
特别是在精密、大型、复杂、长寿命模具方面,仍旧供不应求。
因此,每年尚需大量进口。
对外资的依存逐年增大。
我国加入世贸组织已过6年,外贸高速发展,我国经济对外贸的依存度从30%上升到70%。
同时,近年来,正是外资大量进入我国的时期,随着对外开放政策的不断扩大和深化,外资在我国模具行业的投资也越来越多,致使对外资的依存度也逐年增大。
例如广东省是我国模具第一大省,其产能约占全国的40%左右。
该省的模具产能中,外资企业已占60%左右,合资企业约占10%左右。
该省模具出口约占全国的50%左右,其中由外资、合资企业出口的也占其出口量的多数【7】。
对外资和外贸依存度大,会对行业安全,乃至整个国家的经济安全产生重大影响。
人才紧缺日益突出。
虽然近年来我国模具行业职工队伍发展迅速,估计目前已达近百万人,但仍然跟不上行业发展需求。
一是总量不足,二是素质不够,适应不了行业发展的需求。
根据有关资料,全国模具行业从业人员约缺口30万~50万人,其中工程技术人员约占20%。
目前尤其紧缺的是高素质和高水平的模具企业管理人员和中高层技术人员及高级技术工人。
虽然近几年模具出口增幅每年大于进口增幅,但所增加的绝对量仍是进口大于出口,致使模具外贸逆差一年比一年大。
模具外贸逆差增大主要有两方面原因:
一是国民经济持续高速发展,特别是汽车企业的高速发展带来了对模具旺盛需求,有些高档模具国内的确生产不了,只好进口,但也确实有一些国内可以生产的模具也在进口,这与我国现行的关税政策及项目审批制度有关。
二是对模具出口鼓励不够。
1.321世纪模具技术发展趋势
加入WTO后的中国,全球制造业正以垂直整合的模式向亚太地区转移,我国正成为世界制造业的重要基地,据权威报告,中国已成为世界第一制造大国。
目前,在参与世界产品市场的激烈竞争下,各行业产品的品种和数量不断增加,换型加快,对产品质量、样式和外观也不断提出新要求,使模具需求量增加,对模具质量要求也越来越高,模具技术直接影响制造业的发展、产品更新换代和产品竞争能力。
因此,迅速提高模具技术水平已成为当务之急。
例如:
日本汽车、计算机、电视机、手机等产品的品种,数量,质量在国际市场占有优势地位,其重要原因之一就是日本模具技术居于世界领先水平。
为了解决高精度、长寿命、高效的复杂型腔结构的现代模具,其发展趋势主要有如下三方面:
(1)模具材料及表面处理技术
模具工业要上水平,材料应用是关键。
因选材和用材不当,致使模具过早失效,大约占失效模具的45%以上。
在模具材料方面,常用冷作模具钢有CrwMn、Cr12、Cr12MoV和W6Mo5Cr4V2,新型冷作模具钢有65N6、012A1、CG-2、LD、GD、GM等;常用新型热作模具钢有美国H13、瑞典QRO80M、QRO90SUPREME等;常用塑料模具钢有预硬钢(P20、SM1、B30)、时效硬化型钢(P21、PMS、SM2、日本NAKS5等)、热处理硬化型钢(MnCrWV、日本S-STAR、瑞典一胜百S-136等)、粉末模具钢(日本DEX40等)。
多工位精密冲模硬质合金(YG20、YG25等)及钢结硬质合金(TLW50、GW50等)。
在模具表面处理方面,其主要趋势是:
渗入单一元素向多元素共渗、复合渗(如TD法)发展;由一般扩散向CVD、PVD、PVCD、离子渗入、离子注入等方向发展;可采用的镀膜有:
T:
C、T:
N、T:
CN、T:
AN、CrN、Cr7C3、W2C等,同时热处理手段由大气热处理向真空热处理发展。
另外,目前对激光强化、辉光离子氮化技术也日益受到普遍重视。
(2)模具设计与制造技术
当代模具的设计与制造技术广泛采用计算机辅助设计与制造(CAD/CAM),设计过程程序化和自动化,使用程序、模拟成形过程、采用交互式设计方法,发挥人和计算机的各自特长。
数据库和计算机网络技术使设计人员拥有大量资料和信息。
设计与制造之间的直接传输便于设计中的反复修正改变。
先进设计和加工方法的日益普及,为高质量、短周期地开发模具并且保证模具有足够长的使用寿命,提供了技术保证,为模具工业发展奠定了坚实基础。
模具设计与加工方法的发展主要有以下三方面:
模具软件功能集成化,快速原型法和快速制模技术(RPM/RMT)和高速铣削技术。
(3)专业化生产及标准化
专业化生产是现代化工业生产的重要特征之一,国外工业先进的国家模具专业化生产已达75%以上。
美、日两国的模具厂,80%是10人以下的小工厂,90%是20人以下小而专的企业。
一般一个模具专业厂只生产1~2种模具。
这种专业化小模具厂易于管理,反应灵活,易于提高产品质量和经济效率,有较强的竞争力。
标准化是实现模具专业化生产的基本前提,能系统提高整个模具行业技术水平和经济效益,是机械制造业的深层次发展必由之路。
国外企业都极为重视模具的标准化,我国的模具标准化程度不足30%,而且标准品种少、质量低、交货期长,严重阻碍模具的合理流向和效能发挥,需大力制订标准化规范。
总之,随着模具技术的迅速发展及机械各类产品的多样化、复杂化,模具应用的广度和深度将不断向纵深发展,模具需求增长速度将继续高于国民经济总体发展的速度,供小于求的被动状态将大有改变。
因此,在模具设计与制造中,采用新技术、新工艺、新设备可持续发展模具工业,更将成为所有企业得以占据市场制高点的必由之路。
第2章 塑件设计结构分析
2.1塑件(齿盘)分析
此次设计的产品是修正带中的塑料齿盘(如下图2.1和2.2所示),该塑件是日常学习用品的重要组件,承受外力的几率不大,如冲击载荷,振动,摩擦等情况比较少;塑件的工作温度是室温,这使得在材料选择时对热变形温度,脆化温度,分解温度的要求降低;作为一种小件轻质日用品,生产批量应该是大批大量生产,这样,就必须考虑生产成本和模具寿命,在材料的选择时要综合各种因素;此外,还应注意塑料的老化。
在本次设计中齿数为27,先择模数为0.8。
图2.1齿盘三维视图图2.2齿盘工程图
2.2材料选择
通常,选择塑件的材料依据是它所处在的工作环境及使用性能的要求,以及原材料厂家提供的材料性能数据.对于常温工作状态下的结构件来说,要考虑的主要是材料的力学性能,如屈服应力,弹性模量,弯曲强度,表面硬度等.该塑件对材料的要求比较简单,主要是考虑该塑件成型难易和经济性问题,以下是对几种常用塑料的性能对比,如表2-1所示。
和机械加工一样要考虑到加工工艺问题,模具成型也要考虑到材料的注塑特性,在各特点都相差无几的情况下,好的成型特性是选择材料的主要标准,以下是三种材料的性能和成型特性比较,如表2-2所示。
表2-1材料的特性
塑料名称
PS
PC
ABS
拉伸强度/MPa
51.9
66~72
35~49
弯曲强度/MPa
110
95~113
80
洛氏硬度(M)
115
82
101
氧指数(OI)
18.1
24.9
17.3
热变形温度/℃
85
134
65~98
维卡软化点/℃
105
153
120
体积电阻率/
·cm
10
~10
2.1×10
1013
吸水率%
0.05
0.13
0.2%~0.45%
价格(元/吨)
11500~12300
33000~41000
9000~12000
表2-2材料的性能和成型特性比较
塑料品种
性能特点
成型特点
模具设计
注意事项
使用温度
主要用途
PS
透明性好,电性能好,抗拉强度高,耐磨性好,质脆,抗冲击强度差,化学稳定性教好
成型性能好,成型前可不干燥,但注射时应防止溢料,制品易产生内应力,易开裂
因流动性好,适宜用点浇口,但因热膨胀大,塑件中不宜有嵌件
30℃~80℃
装饰制品,仪表壳,绝缘零件,容器,泡沫塑料,日用品等
ABS
ABS有优良的力学性能,其冲击强度极好,耐磨性优良,尺寸稳定性好,又具有耐油性,力学性能受温度的影响较大
成型性能好,成型前可不干燥,但注射时应防止溢料,制品易产生气泡,易开裂
合理设计浇注系统,便于充型,脱模斜度尽可能大,严格控制料温与模温,以防分解
收缩率取0.35℅
-40℃~100℃
ABS树脂的最大应用领域是汽车、电子电器和建材。
PC
透光率较高,介电性能好,吸水性小,力学性能好,抗冲击,抗蠕变性能突出,但耐磨性差,不耐碱,酮,酯
耐寒性好,熔融温度高,黏性大,成型前需干燥,易产生残余应力,甚至裂纹,质硬,易损模具,使用性能好
尽可能使用直接浇口,减小流动阻力,塑料要干燥,不宜采用金属嵌件,脱模斜度〉2•
〈130℃脆化温度为60℃~100℃
在机械上做齿轮,凸轮,蜗轮,滑轮等,电机电子产品零件,光学零件等
以上的性能分析对比中看出,三种材料都可用来作为原料,由于是一般性民用品,所以价格上是需要重点考虑的,其它如拉伸强度,断裂伸长率等则是次要考虑的指标(这由塑件的工作环境决定),最终选定ABS为塑件材料。
因为从经济和实用两个方面来看,它所拥有的特性均符合我们的塑件要求,并且能减少成本。
2.3ABS的成型特性与工艺参数
ABS是由丙烯腈、丁二烯和苯乙烯三种化学单体合成。
每种单体都具有不同特性:
丙烯腈有高强度、热稳定性及化学稳定性;丁二烯具有坚韧性、抗冲击特性;苯乙烯具有易加工、高光洁度及高强度。
从形态上看,ABS是非结晶性材料。
中单体的聚合产生了具有两相的三元共聚物,一个是苯乙烯-丙烯腈的连续相,另一个是聚丁二烯橡胶分散相。
ABS的特性主要取决于三种单体的比率以及两相中的分子结构。
这就可以在产品设计上具有很大的灵活性,并且由此产生了市场上上百种不同品质的ABS材料。
这些不同品质的材料提供了不同的特性,例如从中等到高等的抗冲击性,从低到高的光洁度和高温扭曲特性等。
ABS材料具有超强的易加工性,外观特性,低蠕变性和优异的尺寸稳定性以及很高的抗冲击强度。
ABS在比较宽广的温度范围内具有较高的冲击强度,热变形温度比PA、PVC高,尺寸稳定性好,收缩率在0.4%~0.8%范围内,若经玻纤增强后可以减少到0.2%~0.4%,而且绝少出现塑后收缩。
ABS具有良好的成型加工性,制品表面光洁度高,且具有良好的涂装性和染色性,可电镀成多种色泽。
ABS尚具有良好的配混性,可与多种树脂配混成合金(共混物),如PC/ABS、ABS/PC、ABS/PVC、PA/ABS、PBT/ABS等,使之具有新的性能和新的应用领域,ABS若与MMA掺混可制成透明ABS,透光率可达80%。
ABS是吸水的塑料,于室温下,24小时可吸收0.2%~0.35%水分,虽然这种水分不至于对机械性能构成重大影响,但注塑时若湿度超过0.2%,塑料表面会受大的影响,所以对ABS进行成型加工时,一定要事先干燥,而且干燥后的水分含量应小于0.2%。
2.3.1ABS塑料主要的性能指标:
密度(Kg.dm-3)1.02~1.07
收缩率%0.4~0.8
熔点℃130~160
热变形温度45N/cm65~98
弯曲强度Mpa80
拉伸强度MPa35~49
拉伸弹性模量GPa1.8
弯曲弹性模量Gpa1.4
压缩强度Mpa18~39
缺口冲击强度kJ/㎡11~20
硬度HRR62~86
体积电阻系数Ωcm1013
介电常数3.7
2.3.2ABS的注射成型工艺参数:
注塑机类型:
螺杆式
喷嘴形式:
通用式
料筒一区150——170
料筒二区180——190
料筒三区200——210
喷嘴温度180——190
模具温度50——70
注塑压60——100
保压40——60
注塑时间2——5
保压时间5——10
冷却时间5——15
周期15——30
后处理红外线烘箱
温度(70)
时间(0.3——1)
更为重要的是因为目前原油价格的下降,导致ABS的市场价格大幅度的下跌。
第3章注塑成型的准备
3.1注塑成型工艺简介
注塑成型是利用塑料的可挤压性与可模塑性,首先将松散的粒状或粉状成型物料从注塑机的料斗送入高温的机筒内加热熔融塑化,使之成为粘流状态熔体,然后在柱塞或螺杆的高压推动下,以很大的流速通过机筒前端的喷嘴注射进入温度较低的闭合模具中,经过一段时间的保压冷却以后,开启模具便可以从模腔中脱出具有一定形状和尺寸的塑料制件。
一般分为三个阶段的工作。
图3-1注塑成型压力—时间曲线
(1)物料准备;成型前应对物料的外观色泽、颗粒情况,有无杂质等进行检验,并测试其热稳定性,流动性和收缩率等指标。
对于吸湿性强的塑料,应根据注射成型工艺允许的含水量进行适当的预热干燥,若有嵌件,还要知道嵌件的热膨胀系数,对模具进行适当的预热,以避免收缩应力和裂纹,有的塑料制品还需要选用脱模剂,以利于脱模。
(2)注塑过程;塑料在料筒内经过加热达到流动状态后,进入模腔内的流动可分为注射,保压,倒流和冷却四个阶段,注塑过程可以用如图所示3.1所示。
图中T0代表螺杆或柱塞开始注射熔体的时刻;当模腔充满熔体(T=T1)时,熔体压力迅速上升,达到最大值P0。
从时间T1到T2,塑料仍处于螺杆(或柱塞)的压力下,熔体会继续流入模腔内以弥补因冷却收缩而产生的空隙。
由于塑料仍在流动,而温度又在不断下降,定向分子(分子链的一端在模腔壁固化,另一端沿流动方向排列)容易被凝结,所以这一阶段是大分子定向形成的主要阶段。
这一阶段的时间越长,分子定向的程度越高。
从螺杆开始后退到结束(时间从T2到T3),由于模腔内的压力比流道内高,会发生熔体倒流,从而使模腔内的压力迅速下降。
倒流一直进行到浇口处熔体凝结时为止。
其中,塑料凝结时的压力和温度是决定塑料制件平均收缩率的重要因素。
(3)制件后处理;由于成型过程中塑料熔体在温度和压力下的变形流动非常复杂,再加上流动前塑化不均匀以及充模后冷却速度不同,制件内经常出现不均匀的结晶、取向和收缩,导致制件内产生相应的结晶、取向和收缩应力,脱模后除引起时效变形外,还会使制件的力学性能,光学性能及表观质量变坏,严重时会开裂。
故有的塑件需要进行后处理,常用的后处理方法有退火和调湿两种。
3.2注塑成型工艺条件
(1)温度;注塑成型过程中需要控制的温度有料筒温度,喷嘴温度和模具温度等。
喷嘴温度通常略微低于料筒的最高温度,以防止熔料在直通式喷嘴口发生“流涎现象”;模具温度一般通过冷却系统来控制;为了保证制件有较高的形状和尺寸精度,应避免制件脱模后发生较大的翘曲变形,模具温度必须低于塑料的热变形温度。
ABS属无定形塑料,无明显熔点,熔融流动温度不太高,t6OC以上即有充分的流动性,但温度过高并不会使流动性增加。
ABS的品种较多,不同品种的料筒温度有所不同,通用ABS的料筒温度为180-230C;耐热ABS为190-240C;阻燃ABS为170-220C。
喷嘴温度较料筒温度前部温度低20-30摄氏度。
(2)压力;注射成型过程中的压力包括注射压力,保压力和背压力。
注射压力用以克服熔体从料筒向型腔流动的阻力,提供充模速度及对熔料进行压实等。
保压力的大小取决于模具对熔体的静水压力,与制件的形状,壁厚及材料有关。
通常,耐热ABS的注射压力为60-85MPa;阻燃ABS的注射压力为60-1OOMPa。
如充模时的流动阻力大,则选用较高的注射压力;反之,选用较低的注射压力。
ABS成型时常采用较高的注射压力以降低熔体粘度,提高充模性能。
(3)时间;完成一次注塑成型过程所需要的时间称为成型周期。
包括注射时间,保压时间,冷却时间,其他时间(开模,脱模,涂脱磨剂,安放嵌件和闭模等),在保证塑件质量的前提下尽量减小成型周期的各段时间,以提高生产率,其中,最重要的是注射时间和冷却时间,在实际生产中注射时间一般为3-5秒,保压时间一般为20-120秒,冷却时间一般为30-120秒(这三个时间都是根据塑件的质量来决定的,质量越大则相应的时间越长)。
经过上面的经验数据和推荐值,可以初步确定成型工艺参数,因为各个推荐值有差别,而且有的与实际注塑成型时的参数设置也不一致,结合两者的合理因素,初定制品成型工艺参数如表3-1所示。
表3-1制品成型工艺参数初步确定
特性内容
特性内容
注塑机类型螺杆式
喷嘴形式直通式
喷嘴温度(℃)200
中段温度(℃)165~180
注射压力MPa100
注射时间s1
冷却时间s20
成型周期s