南京长江隧道重点工程右汊桥梁主索鞍鞍体制造基础工艺.docx
《南京长江隧道重点工程右汊桥梁主索鞍鞍体制造基础工艺.docx》由会员分享,可在线阅读,更多相关《南京长江隧道重点工程右汊桥梁主索鞍鞍体制造基础工艺.docx(10页珍藏版)》请在冰豆网上搜索。
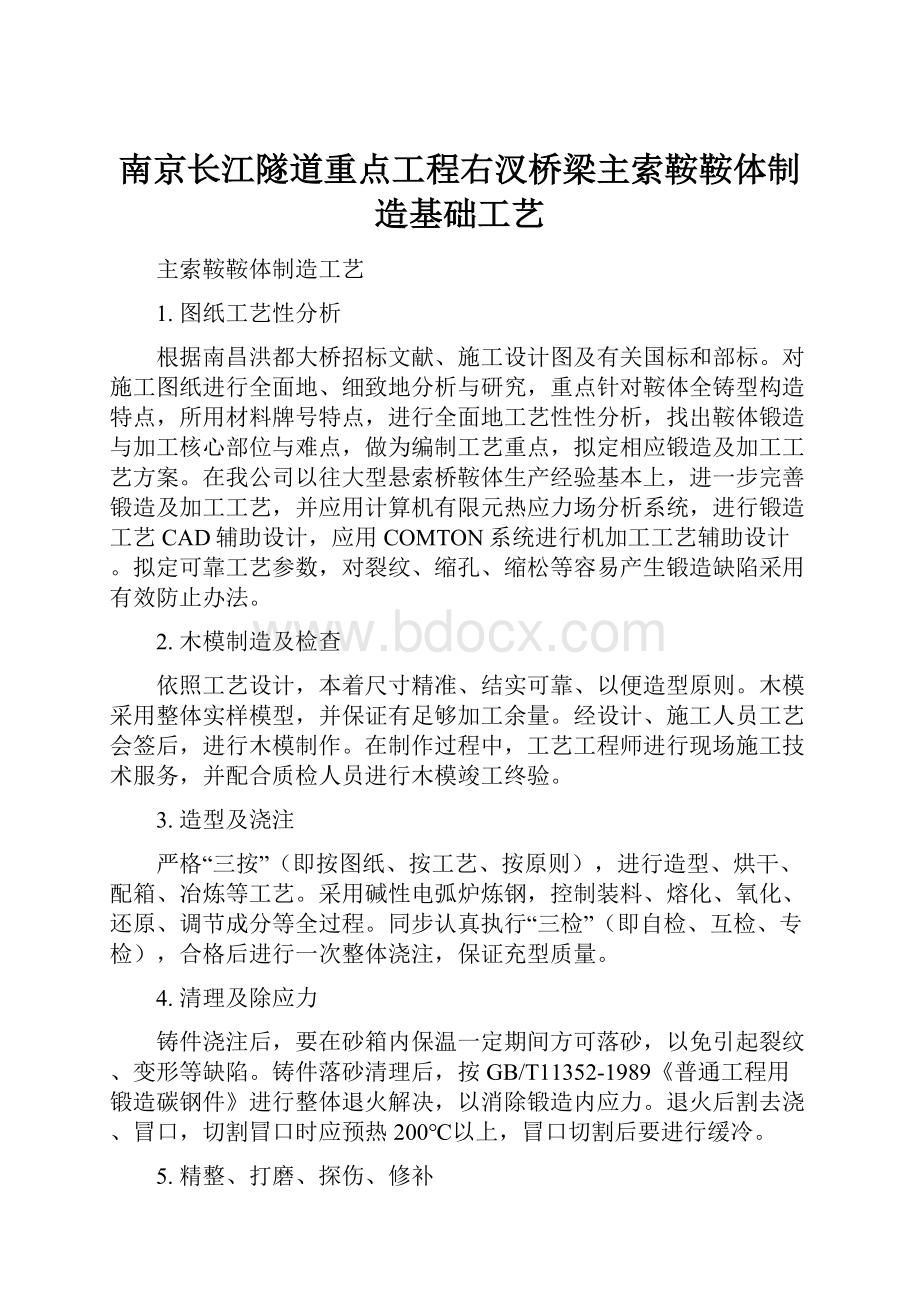
南京长江隧道重点工程右汊桥梁主索鞍鞍体制造基础工艺
主索鞍鞍体制造工艺
1.图纸工艺性分析
根据南昌洪都大桥招标文献、施工设计图及有关国标和部标。
对施工图纸进行全面地、细致地分析与研究,重点针对鞍体全铸型构造特点,所用材料牌号特点,进行全面地工艺性性分析,找出鞍体锻造与加工核心部位与难点,做为编制工艺重点,拟定相应锻造及加工工艺方案。
在我公司以往大型悬索桥鞍体生产经验基本上,进一步完善锻造及加工工艺,并应用计算机有限元热应力场分析系统,进行锻造工艺CAD辅助设计,应用COMTON系统进行机加工工艺辅助设计。
拟定可靠工艺参数,对裂纹、缩孔、缩松等容易产生锻造缺陷采用有效防止办法。
2.木模制造及检查
依照工艺设计,本着尺寸精准、结实可靠、以便造型原则。
木模采用整体实样模型,并保证有足够加工余量。
经设计、施工人员工艺会签后,进行木模制作。
在制作过程中,工艺工程师进行现场施工技术服务,并配合质检人员进行木模竣工终验。
3.造型及浇注
严格“三按”(即按图纸、按工艺、按原则),进行造型、烘干、配箱、冶炼等工艺。
采用碱性电弧炉炼钢,控制装料、熔化、氧化、还原、调节成分等全过程。
同步认真执行“三检”(即自检、互检、专检),合格后进行一次整体浇注,保证充型质量。
4.清理及除应力
铸件浇注后,要在砂箱内保温一定期间方可落砂,以免引起裂纹、变形等缺陷。
铸件落砂清理后,按GB/T11352-1989《普通工程用锻造碳钢件》进行整体退火解决,以消除锻造内应力。
退火后割去浇、冒口,切割冒口时应预热200℃以上,冒口切割后要进行缓冷。
5.精整、打磨、探伤、修补
喷砂、去氧化皮,并对铸件按GB6414-86《铸件尺寸公差与机械加工余量》进行尺寸形状检查,尺寸应符合CT13—CT15级公差。
人工打磨精整后按GB/T9444-1988《铸钢件磁粉探伤及质量评级办法》、GB/T7233-1987《铸钢件超声探伤及质量评级原则》、GB/T9443-1988《铸钢件渗入探伤及缺陷显示痕迹评级办法》、GB/T5677-1985《铸钢件射线照像及底片级别分类办法》等原则对规定部位作无损探伤检查。
对缺陷部位消缺修复后,焊后除应力再次探伤检查。
6.热解决
经消缺探伤合格铸件与同包浇注性能试材同炉进行正火+回火解决,严格控制热解决工艺规范,保证机械性能合格,毛坯无锻造缺陷。
7.探伤
对热解决后铸件喷砂,进行各部位人工打磨,进一步探伤,
8.划线
8.1将鞍体按图1方式直立放。
8.1.1以鞍体底平面为基准,找正鞍体。
8.1.2按设计图纸及制造工艺所给尺寸及规定,检测鞍体各处加工余量与否均匀。
8.1.3按设计图纸及制造工艺所给尺寸及规定,在鞍体上分别划出:
8.1.3.1主塔中心线。
8.1.3.2承缆槽圆弧中心线。
8.1.3.3底平面长度加工线。
8.1.3.4鞍体长度加工线。
8.2将鞍体按图2方式正立放。
8.2.1以鞍体底平面为基准,找正鞍体。
8.2.2按设计图纸及制造工艺所给尺寸及规定,检测鞍体各处加工余量与否均匀。
8.2.3按设计图纸及制造工艺所给尺寸及规定,在鞍体上分别划出:
8.2.3.1底平面厚度加工线。
8.2.3.2I.P点参照点并做永久标记。
注:
由于I.P点在鞍体之外,而I.P点又是一种非常重要基准点。
故在鞍体实体某些作出一种I.P点参照点,作为此后加工装配基准参照点。
8.3将鞍体按图3方式侧卧放。
8.3.1以鞍体底平面及已划出各线为基准,找正鞍体。
8.3.2按设计图纸及制造工艺所给尺寸和规定,检测鞍体各处各加工余量与否均匀。
8.3.3按设计图纸及制造工艺所给尺寸和规定,在鞍体上分别划出:
8.3.3.1鞍体中心线。
8.3.3.2鞍槽中心线。
8.3.3.3鞍槽宽度线。
8.3.3.4底平面宽度加工线。
9.加工底平面、钻孔
9.1用大型落地镗铣床进行加工,见图4。
9.2用Φ315和Φ250硬质合金端面铣刀。
9.3按图5方式放置鞍体。
9.4按已划出加工线找正鞍体并压牢。
9.5以鞍体鞍槽中心线为基准。
9.5.1按设计图纸所给尺寸,参照划线。
铣底平面。
9.5.2按设计图纸所给尺寸,参照划线。
铣底平面上上、下台阶面。
9.6钻底平面上各孔。
9.6.1按设计图纸及制造工艺所给尺寸和规定,以鞍槽中心线和主塔中心线为基准。
运用机床坐标系统定位每一种位置。
10.粗加工鞍槽内各台阶面以备超声波探
10.1用数控龙门镗铣床进行加工,见图6。
10.2加工刀具:
Φ500硬质合金三面刃铣刀。
10.3使用专用数控加长直角铣头。
10.4按图7方式放置鞍体。
10.5按设计图纸及制造工艺所给尺寸和规定,以已加工过底平面及鞍体上I.P点参照点为基准。
数控编程三轴联动加工鞍槽:
10.5.1粗铣鞍槽及鞍槽内各个台阶。
11.探伤
对粗加工后鞍槽内表面进行超声波探伤及规定部位射线探伤,检查有无内在裂纹及其他缺陷;如发现缺陷应按技术规范中关于规定进行解决。
12.精加工鞍槽内各个台阶及顶面圆弧
12.1设备、刀具、装夹方式同上。
12.2按设计图纸及制造工艺所给尺寸和规定,以已加工过底平面及鞍体上I.P点参照点为基准。
数控编程三轴联动加工鞍槽:
12.2.1精铣鞍槽及鞍槽内各个台阶,见图8。
12.2.2精铣鞍体顶弧面,见图8。
13.加工鞍体底平面四边、鞍槽处拉杆螺栓孔及盖板螺纹孔
13.1用大型落地镗铣床进行加工,见图9。
13.2按设计图纸所给尺寸,以鞍槽中心线和主塔中心线为基准:
13.2.1铣准鞍体底平面宽度。
13.2.2铣准鞍体底平面长度。
13.2钻栏杆螺栓孔。
13.2.1按设计图纸所给尺寸,以鞍体底平面和主塔中心线为基准:
运用机床坐标系统定位每一种位置。
14.打磨槽道以备焊接隔板
按设计图纸规定,打磨槽道以备焊接隔板。
15.装焊隔板
装焊前应加工特种工装,将各级隔片均装好后进行一次焊接。
焊接时,应控制焊接参数,消除焊接变形。
16.打磨焊道
磨平焊道,焊缝,清除焊渣,内外喷砂解决,见图10。
17.喷砂
按设计图纸及有关原则规定,鞍体整体进行喷砂解决。
注1:
喷砂前,将安装盖板螺纹孔保护好。
注2:
喷砂中,注意保护好底平面上加工面及不锈钢表面。
18.槽内喷锌,外部上漆
对槽内及隔片进行喷锌解决。
锌层厚度不不大于200μm,非加工表面涂防锈漆两道,加工表面涂脂防锈,各孔内涂油防锈。
192.装配并检查
按成对标记进行总成装配,以检查各个零、部件之间互相配合性。
20.包装发运